组装工艺及常见异常原因与措施
电子产品组装过程常见失效机理及预防措施

电子产品组装过程常见失效机理及预防措施摘要:随着微电子电路集成度的大幅度提高,组装密度越来越高,承担机械与电气连接的焊点尺寸越来越小,而任意焊点的失效就有可能造成器件甚至系统整体的失效。
微波组件组装中,经常出现内引线键合系统的缺陷。
一些缺陷在某种条件下可导致产品失效。
本文分析了内引线键合的缺陷和失效问题,提出了改进设计和制造工艺,采取有效质量管理措施。
关键词:电子组装;失效分析;预防措施随着现代电子技术的发展,微波组件的工作频率越来越高,其在武器装备中的应用范围越来越广。
微波组件的有源部分通常由单个或多个管芯、封装器件、单片电路以及它们的组合组成,无源部分通常由电阻、电容、电感、环行器、隔离器、分布式传输线、接插件等各种元器件以及做成传输线的电路基板组成。
通过分析研制过程中的缺陷和失效问题,分辩其失效模式和失效机理,确定其最终的失效原因,提出改进设计和制造工艺的建议,采取有效质量管理措施,消除故障隐患,使产品质量稳定可靠。
一、失效模式1、金带开路失效。
组件中元器件的种类繁多,金带常需键合在性能差异较大的板材上。
根据不同的材料应选取相应的键合参数,键合参数选用不当,键合部位将存在缺陷,在机械应力作用下可产生失效。
金带键合颈部的断裂,使电气连接呈现时断时续的状态,而导致组件失效。
2、金丝短路失效。
芯片安装方向偏差导致键合金线过长、交叉,介质板上的键合点与芯片上的键合区位置没有做到按顺序一一对应,相邻金丝短路失效。
3、金丝损伤。
生产过程中,常出现金丝倒伏、变形、扭曲、裂口及擦痕等机械损伤。
在200~500倍显微镜下观察,发现金丝拱弧表面有损伤,不光滑,比较毛糙。
在某种状态下,微带线连接点金丝将开路失效。
二、故障原因分析1、金带键合根部失效。
观察发生故障的部位,发现介质板表面低于陶瓷板表面,导致金带的两键合点不在同一水平面内,且落差较大。
金带在陶瓷板端无向上的弧度,而贴近陶瓷片表面,在其边沿处折弯通向介质板,且故障部位的键合点颈部变形较大。
在生产工艺中出现的问题、原因及解决办法

4、调整磷化液及磷化处理的各项指标
磷化后工件有挂灰现象
1、磷化液中促进剂含量过高
2、磷化液中反应生成的沉淀物过多
1、停止加入促进剂,让其反应或自然消耗
2、清除磷化液中底部残渣
磷化液呈深褐色(不含高温磷化)磷化效果不佳
1、磷化中亚离子含量过高
2、磷化液长时间使用没有及时添加补充,过分疲劳
2、加强除锈后的水洗
3、调整或更换表调剂
4、适当提高磷化温度
5、适当延长磷化时间
6、按要求添加促进剂
7、把工件单体摆放
8、改变工件放置角度
磷化膜不均匀有“泛彩”现象
1、除油不净
2、工件表面有硬化状态
3、工件因热处理方法不同
4、促进剂溶解不均
5、磷化的各项技术指标中有未在范围内的情况
1、加强脱脂
2、加强除锈使工件表面状况接近一致或进行磷化前的表面调整
脱脂、除锈、磷化系列产品在生产工艺中
出现的问题、原因及解决办法
一、脱脂部分
问 题
原 因
解 决 方 法
脱脂不彻底
1、脱脂液浓度低
2、脱脂时间短
3、脱脂液温度太低
4、局部油脂太厚
1、增加脱脂剂的含量
2、延长脱脂处理时间
3、脱脂液升温
4、利用搽拭等方法进行预处理
喷淋处理
泡沫溢出药液槽
1、消泡剂加入量太少
2、消泡剂失效
表面准备不当,底漆或底层不相容,基体受层间污染,层间固化时间太长
干喷
表面呈粗糙多孔结构,呈砂纸状外观,这常与无机富锌涂层有关
雾化差,喷枪距表面太远,空气温度过高,温度低,溶剂蒸发过快,接近表面竞价的涂料微粒干了
组装工艺及常见异常原因与措施

• 措施
03
定期对设备进行维护和保养,确保设备处于良好状态;加强员
工操作培训,提高员工的操作技能和设备维护意识。
常见异常案例分析
案例三
产品质量不达标
• 原因
组装过程中的工艺参数不合理、质检环节失控等。
• 措施
优化组装工艺参数,确保产品质量稳定;加强对质检环节的管理,采用先进的质检设备和 方法,确保产品100%合格。
稳定性。
维护不到位
设备维护不及时或不规范,可能导 致设备在组装过程中出现故障。
设备不匹配
使用不合适的设备进行组装,可能 无法达到预期的组装效果。
物料问题
物料质量问题
物料本身存在缺陷,如裂纹、变 形等,影响组装效果。
物料不匹配
使用的物料与设计要求不符,可 能导致组装异常。
物料存储不当
物料在存储过程中受潮、受损等 ,影响物料的性能和可靠性。
定期维护
制定设备维护计划,定期对组装设备进行检查、保养,确保设备 处于良好运行状态。
更新升级
及时关注新技术、新设备的发展,对组装设备进行更新升级,提高 组装效率和质量。
故障排查
设备出现故障时,应迅速组织专业人员进行排查和修复,减少故障 对组装线的影响。
物料质量控制和管理
严格筛选供应商
选择具有良好信誉和稳定质量 的供应商,确保物料来源可靠
组装工艺及常见异常 原因与措施
汇报人: 日期:
目 录
• 组装工艺概述 • 常见的组装异常原因 • 解决组装异常的措施 • 案例分析和预防措施
CHAPTER 01
组装工艺概述
组装工艺定义和流程
定义
组装工艺是指将多个零部件按照 规定的技术要求组装在一起,形 成一个完整产品的过程。
太阳能电池组件封装常见问题与对策
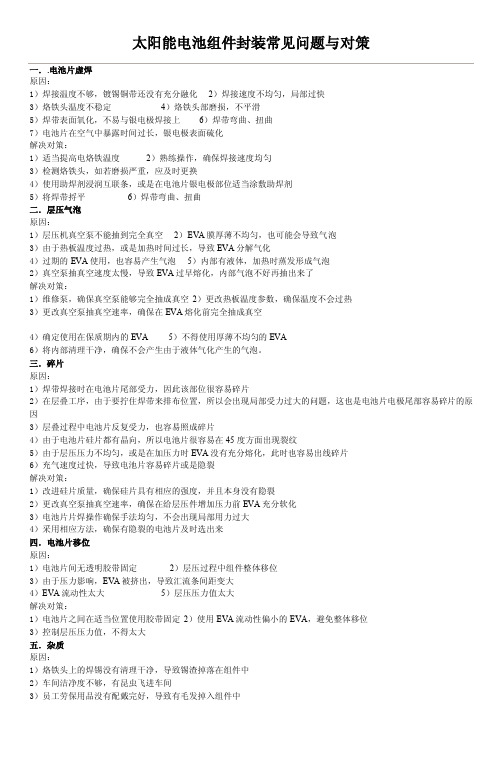
太阳能电池组件封装常见问题与对策一..电池片虚焊原因:1)焊接温度不够,镀锡铜带还没有充分融化2)焊接速度不均匀,局部过快3)烙铁头温度不稳定4)烙铁头部磨损,不平滑5)焊带表面氧化,不易与银电极焊接上6)焊带弯曲、扭曲7)电池片在空气中暴露时间过长,银电极表面硫化解决对策:1)适当提高电烙铁温度2)熟练操作,确保焊接速度均匀3)检测烙铁头,如若磨损严重,应及时更换4)使用助焊剂浸润互联条,或是在电池片银电极部位适当涂敷助焊剂5)将焊带捋平6)焊带弯曲、扭曲二.层压气泡原因:1)层压机真空泵不能抽到完全真空2)EVA膜厚薄不均匀,也可能会导致气泡3)由于热板温度过热,或是加热时间过长,导致EVA分解气化4)过期的EVA使用,也容易产生气泡5)内部有液体,加热时蒸发形成气泡2)真空泵抽真空速度太慢,导致EVA过早熔化,内部气泡不好再抽出来了解决对策:1)维修泵,确保真空泵能够完全抽成真空2)更改热板温度参数,确保温度不会过热3)更改真空泵抽真空速率,确保在EVA熔化前完全抽成真空4)确定使用在保质期内的EVA 5)不得使用厚薄不均匀的EVA6)将内部清理干净,确保不会产生由于液体气化产生的气泡。
三.碎片原因:1)焊带焊接时在电池片尾部受力,因此该部位很容易碎片2)在层叠工序,由于要拧住焊带来排布位置,所以会出现局部受力过大的问题,这也是电池片电极尾部容易碎片的原因3)层叠过程中电池片反复受力,也容易照成碎片4)由于电池片硅片都有晶向,所以电池片很容易在45度方面出现裂纹5)由于层压压力不均匀,或是在加压力时EVA没有充分熔化,此时也容易出线碎片6)充气速度过快,导致电池片容易碎片或是隐裂解决对策:1)改进硅片质量,确保硅片具有相应的强度,并且本身没有隐裂2)更改真空泵抽真空速率,确保在给层压件增加压力前EVA充分软化3)电池片片焊操作确保手法均匀,不会出现局部用力过大4)采用相应方法,确保有隐裂的电池片及时选出来四.电池片移位原因:1)电池片间无透明胶带固定2)层压过程中组件整体移位3)由于压力影响,EVA被挤出,导致汇流条间距变大4)EVA流动性太大5)层压压力值太大解决对策:1)电池片之间在适当位置使用胶带固定2)使用EVA流动性偏小的EVA,避免整体移位3)控制层压压力值,不得太大五.杂质原因:1)烙铁头上的焊锡没有清理干净,导致锡渣掉落在组件中2)车间洁净度不够,有昆虫飞进车间3)员工劳保用品没有配戴完好,导致有毛发掉入组件中解决对策:1)定时清理烙铁头,确保没有锡渣堆积2)车间内保持正风压,保证飞虫等不会进入车间3)员工劳保用品应配戴完整六.焊接不良原因:1)员工焊接手法不准,导致焊带和银电极没能完全的对应上2)如若是自动焊接设备焊接的话,那就是因为设备没有调试好3)焊花是由于在背面电极焊接的过程中,对正面焊带也造成了热冲击,导致正面焊带粘贴在串焊模板上产生焊花解决对策:1)熟练操作,确保焊带与银电极完全对齐2)如若是自动焊接机,则应调试好后再投产3)在串焊模板上,电池片银电极对应的位置开一定深度的槽,避免焊带与串焊模板接触产生焊花七.背板问题原因:1)背板凹坑是因为层压机内部有异物,层压过程中压下来导致背板凹坑2)背板鼓包是由于组件内部EVA受热分解气化,导致产生鼓包解决对策:1)清理层压机,特别是气囊和高温布2)调整层压的参数,包括降低温度和减少层压时间3)如若还是有鼓包,则应检测EVA是否在保证期以内,以及这批EVA原材料的性能八.型材问题原因:1)型材在运输过程中收到碰伤2)型材表面没有塑料保护膜3)型材鼓包、起皮是由于表面处理不好导致的4)型材颜色不均匀是由于边框在不同批次的氧化池里面表面处理,而其颜色又不太一致所导致的解决对策:1)在工厂内减少搬运环节,避免缺陷的产生2)表面鼓包、起皮的边框不能使用3)对于颜色不一致的边框要求供应商做挑选,确保一个批次的边框颜色基本保持一致组件在封装加工过程中,可能会出线各种各样的问题。
设备装配现场改善措施方案

设备装配现场改善措施方案引言设备装配现场是制造业中非常重要的一个环节,负责将零部件组装成完整的设备。
一个高效、稳定的装配现场能够提高生产效率、降低成本并且保证产品质量。
然而,由于各种原因,设备装配现场在实践中常常会面临各种挑战,比如工艺不稳定、设备故障、人员管理等问题。
本文将提出一些设备装配现场改善措施方案,以期提高装配效率和产品质量。
分析与改进1. 工艺改进在设备装配现场中,工艺流程的合理性与稳定性直接影响装配效率和质量。
因此,我们需要对工艺进行全面的分析和改进。
首先,我们可以采用价值流图的方法,对装配过程中的各个环节进行细致的剖析,找出存在的瓶颈和浪费,以期消除不必要的等待和运输时间。
其次,我们需要在工艺流程中引入标准化工具,如标准作业指导书(SOP)和工艺文件。
这样可以确保每个工序的执行标准一致,减少误操作和重新加工的发生。
最后,我们可以采用先进的装配技术和设备,例如自动化装配线和机器人装配系统。
这些技术和设备可以提高装配效率和质量,并减少人为因素对装配过程的影响。
2. 设备维护与保养设备的故障和损坏常常会导致装配现场的停工和生产延误,严重影响生产效率和产品质量。
因此,做好设备的维护与保养工作至关重要。
首先,我们需要建立设备维护的标准和流程,并进行定期的维护检查。
同时,设备操作人员需要接受相应的培训,熟悉设备的使用方法和常见故障处理方法。
其次,我们可以采用智能化的设备监控系统,实时监测设备的运行状态。
一旦发现异常情况,系统可以及时发出警报并通知相关人员处理。
最后,我们需要建立设备保养的档案和记录,对设备的使用寿命、故障维修情况等进行统计和分析。
这样可以及时发现设备的问题,并做出相应的改进和决策。
3. 人员管理与培训人员是设备装配现场不可或缺的关键要素,正确的人员管理和培训对提高装配效率和质量至关重要。
首先,我们需要建立科学的岗位职责和工作规范,明确每个人的职责和权限。
同时,我们可以采用绩效考核制度,对人员的工作业绩进行评估和奖惩,激发员工的积极性和责任心。
工艺操作常见故障及解决及解决方法

工艺操作常见故障及解决及解决方法主厂房区域1、泵不上量或上量不好原因:空压机工作不正常,风压达不到所要求,鼓风管有堵塞现象,三角带有短缺、打滑现象,盘根有漏气,桶内介质沉淀时间过长,桶位低等原因,固液比失调。
处理方法:(1)尤其在开介质泵之前,提前鼓风或打小循环,将桶内介质和水搅拌均匀。
(2)用泵前稀释水将介质稀释减轻起泵时的负荷。
(3)关闭入料阀门,将稀释水打开,待水达一定高度将阀门打开,靠水的压力冲顶桶内介质。
(4)大循环时必须确保鼓风阀、给料阀、小循环阀门关闭。
2、扫地泵堵或上量不好原因:停车时地沟末处理干净,扫地泵长时不开,导致煤和介质沉淀在泵坑内将吸料口糊死。
机修在维修时将布条等杂物掉入泵坑将吸料口及叶轮堵死。
处理方法:及时清理地沟,扫地泵工作要既不常开也不常停,尤其在停车放料时,一定要将地沟冲洗干净,将泵坑水抽干净。
如遇上量不好泵坑内积货太多,可用扫地水管对泵坑内冲刷,将吸料口沉淀物冲散。
看上量情况,如不上量将泵吊起清理坑内吸料口杂物,而后检查管道有无堵塞,用手锤敲打管道,听其声音判断堵塞情况,在堵管前方割口用水冲刷管道。
3、皮带跑水跑货现象原因:几个系统扫地泵同时开,导致清扫筛处理不过来,进入皮带。
起车时未将皮带上的水拉空就带煤,离心机脱水效果不好,振动筛脱水效果不好,絮凝剂流失,导致清扫系统振动筛筛缝透筛不好。
处理方法在开扫地泵时,要每个系统扫地泵间隔开,向以上各层的操作工询问扫地筛处理情况。
起车时,就地开起二层皮带将水泄入地沟,再带煤生产。
生产当中,及时观察下料溜槽带水情况,如发现异常,及时通知集控室停煤,检查相关关联设备。
4、产品粒度超限情况原因:破碎机间隙过大,破碎齿磨损严重,块煤振动筛上层筛板有破损情况,下料翻板走向是否在旁路状态。
处理方法:在巡视检查当中,密切注意产品皮带机粒度情况,发现有超粒度现象,马上通知集控室停煤检查。
5、压皮带现象原因:比重不合适,矸石量太大。
紧急停车、带煤前未将离心机、筛子上煤拉空就带煤。
ZD6电动转辙机入所修工艺流程及常见问题处理
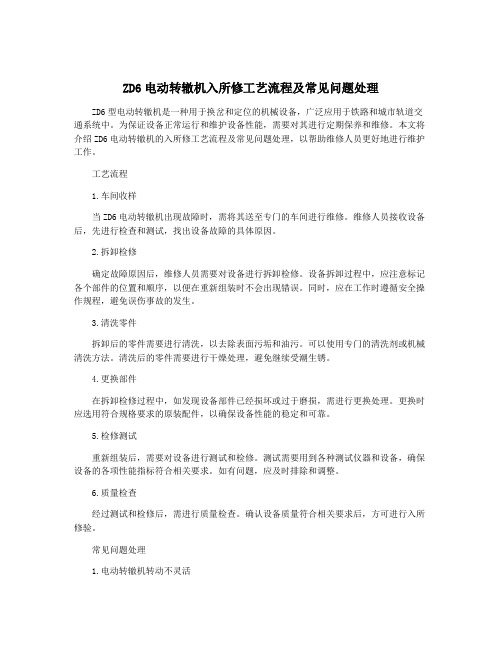
ZD6电动转辙机入所修工艺流程及常见问题处理ZD6型电动转辙机是一种用于换岔和定位的机械设备,广泛应用于铁路和城市轨道交通系统中。
为保证设备正常运行和维护设备性能,需要对其进行定期保养和维修。
本文将介绍ZD6电动转辙机的入所修工艺流程及常见问题处理,以帮助维修人员更好地进行维护工作。
工艺流程1.车间收样当ZD6电动转辙机出现故障时,需将其送至专门的车间进行维修。
维修人员接收设备后,先进行检查和测试,找出设备故障的具体原因。
2.拆卸检修确定故障原因后,维修人员需要对设备进行拆卸检修。
设备拆卸过程中,应注意标记各个部件的位置和顺序,以便在重新组装时不会出现错误。
同时,应在工作时遵循安全操作规程,避免误伤事故的发生。
3.清洗零件拆卸后的零件需要进行清洗,以去除表面污垢和油污。
可以使用专门的清洗剂或机械清洗方法。
清洗后的零件需要进行干燥处理,避免继续受潮生锈。
4.更换部件在拆卸检修过程中,如发现设备部件已经损坏或过于磨损,需进行更换处理。
更换时应选用符合规格要求的原装配件,以确保设备性能的稳定和可靠。
5.检修测试重新组装后,需要对设备进行测试和检修。
测试需要用到各种测试仪器和设备,确保设备的各项性能指标符合相关要求。
如有问题,应及时排除和调整。
6.质量检查经过测试和检修后,需进行质量检查。
确认设备质量符合相关要求后,方可进行入所修验。
常见问题处理1.电动转辙机转动不灵活原因:转辙机内部机械部件磨损或过于紧缩。
处理方法:拆卸检修,更换或调整相关部件。
2.电动转辙机电机启动困难或异常停机原因:电机本身技术问题或供电问题。
处理方法:检查电机线路和电源供应,排查问题所在。
3.电动转辙机换向不到位或反应迟钝原因:控制装置或传感器故障。
4.电动转辙机开关误动或停机不利原因:电气连接不良或连线出现问题。
总之,针对不同的问题,应有所区别地进行检查、排查和处理。
有效地维修和保养电动转辙机,将有助于其稳定高效地工作,同时也能延长其使用寿命。
注塑异常原因及处理
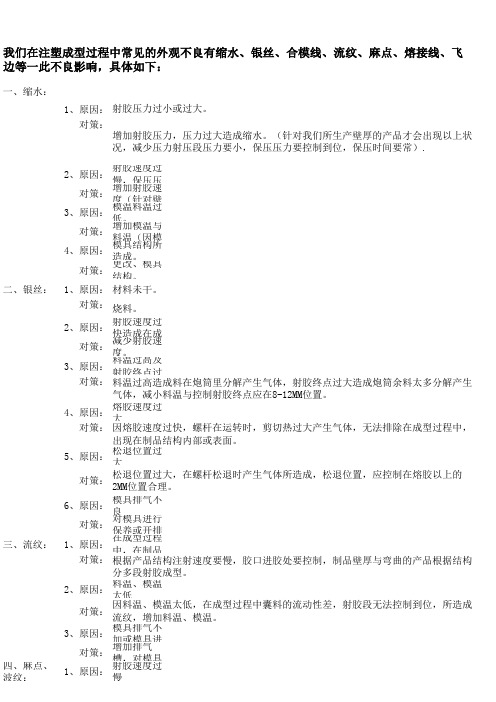
一、缩水:1、原因:对策:2、原因:射胶速度过慢,保压压力时间过小。
对策:增加射胶速度(针对壁薄产品因为射胶速度过慢造成制品筋条处缩水)。
3、原因:模温料温过低。
对策:增加模温与料温(因模温料温太低,制品在成型过程中压胶流动性差)。
4、原因:模具结构所造成。
对策:更改、模具结构。
二、银丝:1、原因:材料未干。
对策:烧料。
2、原因:射胶速度过快造成在成型过程中剪切热过大造成气体无法排除。
对策:减少射胶速度。
3、原因:料温过高及射胶终点过大。
对策:4、原因:熔胶速度过大对策:5、原因:松退位置过大对策:6、原因:模具排气不良对策:对模具进行保养或开排气槽。
三、流纹:1、原因:在成型过程中,在制品的胶口进胶处,及产品在制品弯曲处。
对策:2、原因:料温、模温太低对策:3、原因:模具排气不加或模具进胶口位置设计不合理。
对策:增加排气槽,对模具进行A级保养,对模具进胶口位置更改。
四、麻点、波纹:1、原因:射胶速度过慢我们在注塑成型过程中常见的外观不良有缩水、银丝、合模线、流纹、麻点、熔接线、飞边等一此不良影响,具体如下:增加射胶压力,压力过大造成缩水。
(针对我们所生产壁厚的产品才会出现以上状况,减少压力射压段压力要小,保压压力要控制到位,保压时间要常).射胶压力过小或过大。
料温过高造成料在炮筒里分解产生气体,射胶终点过大造成炮筒余料太多分解产生气体,减小料温与控制射胶终点应在8-12MM位置。
因熔胶速度过快,螺杆在运转时,剪切热过大产生气体,无法排除在成型过程中,出现在制品结构内部或表面。
松退位置过大,在螺杆松退时产生气体所造成,松退位置,应控制在熔胶以上的2MM位置合理。
根据产品结构注射速度要慢,胶口进胶处要控制,制品壁厚与弯曲的产品根据结构分多段射胶成型。
因料温、模温太低,在成型过程中囊料的流动性差,射胶段无法控制到位,所造成流纹,增加料温、模温。
对策:增加射胶速度。
2、原因:料温、模具太低。
对策:增加料温、模具。
- 1、下载文档前请自行甄别文档内容的完整性,平台不提供额外的编辑、内容补充、找答案等附加服务。
- 2、"仅部分预览"的文档,不可在线预览部分如存在完整性等问题,可反馈申请退款(可完整预览的文档不适用该条件!)。
- 3、如文档侵犯您的权益,请联系客服反馈,我们会尽快为您处理(人工客服工作时间:9:00-18:30)。
塑 件 BOSS 固 定 鐵 件
銅 釘 埋 入 塑 件 BOSS
光 鉻 與 塑 件 結 合
超 音 波 機
單 段 式
三 段 式
兩 段 式
三 段 式
二. 熱熔技術---熱熔機各零部件簡介
熱熔機零組件介紹
定時器 氣壓表 緩沖調節閥
電流表
溫控器 機箱 氣缸主軸 鎖模桿
發熱管
熱熔機頂板
絕熱塊 導向軸
熱熔機中板
加熱板 壓塊及鎖 模螺絲 起動開關
治具底座
緊急停 止開關
二. 熱熔技術---熱熔機各零部件簡介
熱熔機零組件功能介紹
氣 岡 主動力 產生器 控制動力大小 感應/控制氣岡活塞活動界 當接到紅外線感應器信號后觸動,供電給電磁閥 電磁閥工作后,從而控制氣路開啟/關閉
氣 壓 調 節器 紅外線感應器 繼 電 電 磁 器 閥
時 間 調 節器
溫 度 調 節器 溫 控 器
控制總行程時間(運行時間衡定,故,直接控制熱時間)
設定熱熔之最高溫度 控制發熱板溫度(即:衡溫控制)
發
熱
板
熱能產生器
通過調節各鈕,控制各種狀態
控 制 面 板
熱熔技術---熱熔機各零部件簡介
定時器:設定自動開關時間.
電流表:顯示電流值,直觀判定發熱管有無損壞.
溫控器:設定溫度及控制溫差.
氣壓表:顯示當前實際氣壓值.
緩沖調節閥:調節緩沖氣流大小.
發熱管:加熱使用.
二. 熱熔技術---熱熔參數
3.熱熔各種參數對比表
埋釘參數設置
傳杆材質 塑膠材質 ABS ABS+PC ABS+纖 銅傳杆 220± 20℃ 240± 20℃ 260± 20℃ 鐵傳杆 240± 20℃ 260± 20℃ 280± 20℃ 熱熔時間 韋錸機械 8± 3s 8± 3s 8± 3s 廣德機械 5± 3s 5± 3s 5± 3s 特殊情 況例外
組裝工藝介紹及組裝常見異常
原因分析與改善措施
制作﹕馬維青 2005.11.15
目錄
組裝工藝介紹
組裝常見異常原因改善措施
組裝工藝介紹---四種工藝介紹
一. 印刷技術
二. 熱熔技術 三. 鐳雕技術 四. 燙金技術
一. 印刷技術 分以下四個部分介紹:
1.印刷設備的類型
2.印刷機台結構原理
3.印刷油墨的組成
二.熱熔技術
分四部分介紹:
1.熱熔的功能及熱熔機的類型 2.熱熔機各零部件簡介
3.熱熔參數
4.熱熔常見不良現象及原因分析對策
二. 熱熔技術---熱熔的功能及熱熔機的類型
1.熱熔的功能和熱熔機的類型對照表
熱
熔
熱 熔 功 能 熱 熔 機 類 型
塑 件 與 塑 件 結 合
塑 件 BOSS 固 定 塑 件
耐抗性以及其他調整劑
一. 印刷技術
4.印刷常見不良現象及原因分析對策
易見問題 原因 1.網架太高或太低 2.印刷角/力度不當 3.新油墨幹網 1.產品變形 2.制具對位不當 3.作業手勢 油墨使用過久或新油墨 處理措施 1.調整網架至合適高度 2.調整作業員手勢之角/力度 3.充分攪油墨(正常情況新油墨需使 用半天後才正常. 此時間段一般印1PCS洗1次網) 1.短:用美紋膠粘貼法;長:知會責任單位改善 2.技術員調機 3.技術指導 首件比對SAMPLE,首件留樣逐日比對;印刷色板,首件 測試(根據色差值而確定加何顏色) 1.更換新油墨 2.調整烘烤時間(一般流水線為60攝氏度/60秒) 3.加硬化劑 1.充分攪拌後再使用 2.重新調整油墨成分的比例 1.調試油墨濃度 2.勤洗網或換網板 3.指導作業手勢 1.指導作業手勢與方法 2.客戶要求變更->加底油 3.調網板的高低 4.調油墨濃度->加開油水
整體粗細不均
印刷偏移
色差
1.油墨特性不符 附著力NG 2.烘烤時間不夠 3.幹燥時間太慢 1.未充分攪拌 銀粉脫落但不見底 2.銀粉太多 1.油墨濃度(濃->細,稀->粗) 字體細或粗 2.作業手法 3.網板本身原因 1.手勢 2.塑件表面粗糙度 絲刷字體針孔,斷線,毛邊 3.洗網不透 4.油墨濃度
熱熔塑膠參數設置
塑膠材質 ABS ABS+PC ABS+纖 傳杆材質 熱熔時間
銅傳杆
140± 20℃ 170± 20℃ 210± 20℃
鐵傳杆
160± 20℃ 200± 20℃ 230± 20℃
Байду номын сангаас
韋錸機械
曲 印 機
移 印 機
一. 印刷技術---手印台/自動网印機/移印機結構及原理
2. 手印台/自動网印機/移印機結構及原理
网 板 定位架 平 衡 調整器 印刷底模平台 平面位置調整 网板平行調節 三 控 网 平 停 油 底 刮 控 調 點 組合 制 面板 框 架組 台 組 止 塊 盤 組 模 平台 刀 組 制 面板 節 面板 固定网板 控制网板抬起角度及力度 固定制品受台 通過調節旋鈕,調節印刷位置 調整网板與產品間隙 控制進氣壓力.過濾.潤滑 控制機器動作 固定网板 調整平面印刷被印刷物之位置 控制左右行程距離 固定鋼板及放置油墨 固定印刷物及調整印刷之位置 通過油刷添加油墨至鋼板,利用刮刀除去多余油墨 控制所有動力臂動作 調節動力大小
一. 印刷技術---印刷油墨的組成
印刷油墨的組成圖
.
印 刷 油 墨
主劑
色 料 媒 質
顏料 染料
有機顏料
無機顏料
干性油/天然樹脂/瀝青質 臘/纖維素/可塑劑/溶劑 粘性/塑性/搖變性/彈性/拉絲性 便於作業調整劑
助劑
便於干燥調整劑
提高效率調整劑
親和性等調整劑如:凡立水 干燥劑
干燥抑制劑 色濃度調整劑
手 印 台 自 動 网 印 機
移 印 機
一. 印刷技術---手印台/自動网印機/移印機結構及原理
自動网印機/移印機/手印台實體展示
自動网印機
移印機
手印台
一. 印刷技術---印刷油墨的組成
3.先簡單敘述印刷油墨,用途,成分,特性:
用途﹕使用於印刷物上之著色材料. 成分﹕以色料媒質為主,於必要時添加/混合其他助劑攪拌而成 特性﹕色調. 光澤性.耐抗性( 耐光性.耐熱性.耐折曲性.耐摩擦性)耐藥品性 (耐酸.耐堿性).耐肥皂性.耐溶劑性.
4.印刷常見不良現象及原因分析對策
一. 印刷技術---印刷設備類型
1.印刷產品面不同,所選用的印刷設備也不同.印刷設備類型如下圖
對照表﹕
印 刷
被 印 制 品 種 類
平 面 制 品
斜 面 制 品
曲 面 制 品
圓 筒 形 制 品
凸 面 制 品
設 備 類 型
自 動 网 印 機
手 印 台 移 印 機
移 印 機 手 印 台