22324轴承内圈滚道面开裂原因分析
滚动轴承内圈故障特征

滚动轴承内圈故障特征
滚动轴承内圈的故障特征可能包括:
1. 轴承内圈出现裂纹,这可能是由于装配过盈量太大,配合不当,受到较大的冲击载荷,或者制造质量不良,轴承材料内部有缺陷。
2. 轴承内圈的金属剥落,这可能是由于冲击力或交变载荷使滚道和滚动体产生疲劳剥落,内外圈安装歪斜造成过载,间隙调整过紧,配合面间有铁屑或硬质杂物,或者选型不当。
3. 轴承内圈的表面出现点蚀麻坑,这可能是由于油液黏度过低,抗极压能力低,或者超载。
4. 轴承内圈咬死,这可能是由于严重发热造成局部高温。
5. 轴承内圈磨损,这可能是由于润滑不良,超载、超速,装配不良、间隙调整过紧,或者轴承制造质量不高。
以上信息仅供参考,具体故障特征及可能的原因和解决方案需要根据实际情况进行判断。
如遇到相关问题,建议寻求专业人员的帮助。
滚动轴承零件常见的淬火裂纹分析与预防
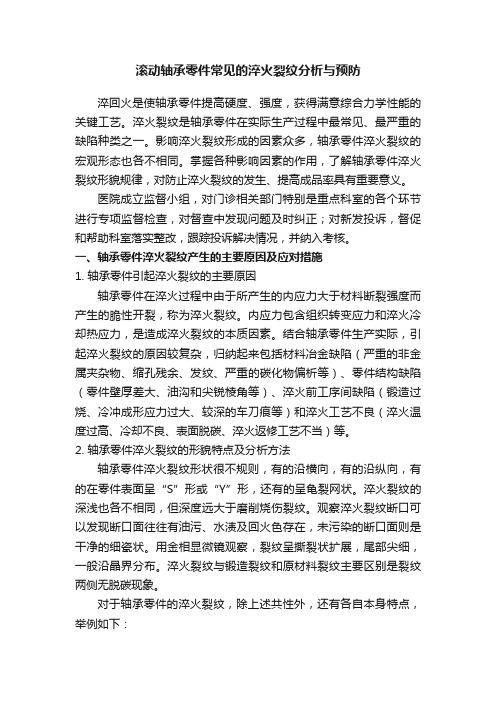
滚动轴承零件常见的淬火裂纹分析与预防淬回火是使轴承零件提高硬度、强度,获得满意综合力学性能的关键工艺。
淬火裂纹是轴承零件在实际生产过程中最常见、最严重的缺陷种类之一。
影响淬火裂纹形成的因素众多,轴承零件淬火裂纹的宏观形态也各不相同。
掌握各种影响因素的作用,了解轴承零件淬火裂纹形貌规律,对防止淬火裂纹的发生、提高成品率具有重要意义。
医院成立监督小组,对门诊相关部门特别是重点科室的各个环节进行专项监督检查,对督查中发现问题及时纠正;对新发投诉,督促和帮助科室落实整改,跟踪投诉解决情况,并纳入考核。
一、轴承零件淬火裂纹产生的主要原因及应对措施1. 轴承零件引起淬火裂纹的主要原因轴承零件在淬火过程中由于所产生的内应力大于材料断裂强度而产生的脆性开裂,称为淬火裂纹。
内应力包含组织转变应力和淬火冷却热应力,是造成淬火裂纹的本质因素。
结合轴承零件生产实际,引起淬火裂纹的原因较复杂,归纳起来包括材料冶金缺陷(严重的非金属夹杂物、缩孔残余、发纹、严重的碳化物偏析等)、零件结构缺陷(零件壁厚差大、油沟和尖锐棱角等)、淬火前工序间缺陷(锻造过烧、冷冲成形应力过大、较深的车刀痕等)和淬火工艺不良(淬火温度过高、冷却不良、表面脱碳、淬火返修工艺不当)等。
2. 轴承零件淬火裂纹的形貌特点及分析方法轴承零件淬火裂纹形状很不规则,有的沿横向,有的沿纵向,有的在零件表面呈“S”形或“Y”形,还有的呈龟裂网状。
淬火裂纹的深浅也各不相同,但深度远大于磨削烧伤裂纹。
观察淬火裂纹断口可以发现断口面往往有油污、水渍及回火色存在,未污染的断口面则是干净的细瓷状。
用金相显微镜观察,裂纹呈撕裂状扩展,尾部尖细,一般沿晶界分布。
淬火裂纹与锻造裂纹和原材料裂纹主要区别是裂纹两侧无脱碳现象。
对于轴承零件的淬火裂纹,除上述共性外,还有各自本身特点,举例如下:(1)材料冶金缺陷沿轧制方向分布,因此,由于组织疏松和显微孔隙造成的淬火裂纹热酸洗后在套圈、滚子端面和钢球两级呈点状或短线状分布,发纹和严重的碳化物偏析多在零件表面沿轴向分布。
大型轴承表面裂纹原因分析

大型轴承表面裂纹原因分析李立军,龚桂仙,吴立新,张友登(武汉钢铁集团公司技术中心,湖北武汉430080)摘要:对进口大型轴承内套圈表面裂纹进行分析。
结果表明,裂纹产生的原因与磨削工艺不当有关,在磨削过程中发生高温回火烧伤,使材料表面断裂强度降低而产生裂纹。
关键词:轴承;裂纹;分析某冷轧厂冷轧机组进口支承辊轴承,内套圈外径<990mm,内径<900mm,宽度420mm。
轴承内套圈与支承辊装配采用热装工艺,在油箱中将轴承内套圈加热到166℃,保温25min,取出后迅速装到支承辊上。
热装后,对轴承内套圈表面进行最后的磨削,保证内套圈与支承辊的同心度。
在轴承使用之前,发现多个轴承内套圈外表面有很多细小裂纹。
通过对轴承内套圈进行取样分析,探明了裂纹产生的原因,本文介绍分析过程及结果。
1 检验与结果1.1 裂纹特征1.1.1裂纹表面特征检查多个轴承内套圈外表面,肉眼很难发现裂纹。
采用磁粉探伤、着色和荧光显示,在内套圈外表面上发现许多细小裂纹,裂纹位置的分布无规律,在内套圈外表面的边部、中部及整个圆周方向均发现了裂纹。
裂纹大多数呈放射状,其中有的呈“人”字形,有的呈“T”形,有的呈“×”形,另外还有少数裂纹呈分散条状。
在放射状裂纹密集的区域,裂纹交织成网状。
对内套圈外表面进行热酸蚀检查,发现表面裂纹更加明显[图1(a)]。
浅磨内套圈外表面试样(保留磨削加工过程中的磨痕),在金相显微镜下观察,裂纹与磨痕方向呈一定角度或垂直[图1(b)]。
进一步磨去试样表面磨痕并抛光,在金相显微镜下观察,发现裂纹由断续分布的线条组成,线条呈弯曲状[图1(c)]。
(a)热酸蚀后; (b)浅磨后; (c)抛光后图1 裂纹表面特征1.1.2裂纹截面特征选取内套圈截面试样进行观察,发现裂纹仅分布于外表层,未出现在内部和内表层。
在金相显微镜下观察有裂纹截面试样,裂纹垂直于表面而向内扩展,并从表面至内部由粗到细而逐渐消逝[图2(a)]。
轴承损坏状态分析

轴承剥皮损伤分析
卡伤损伤状态
• 所谓卡伤是由于在滑动面伤产生的部分的 微小烧伤汇总而产生的表面损伤。滑道面、 滚动面圆周方向的线状伤痕。滚子端面的 摆线状伤痕靠近滚子端面的轴环面的卡伤。 原 因:过大载荷、过大预压。润滑不良。 异物咬入。内圈外圈的倾斜、轴的挠度。 轴、轴承箱的精度不良。措 施:检查载荷 的大小。预压要适当。改善润滑剂和润滑 方法。检查轴、轴承箱的精度
轴承压痕分析
轴承梨皮状点蚀状态分析
• 在滚道面上产生的弱光泽的暗色梨皮状点 蚀。原 因:润滑过程中出现异物咬入。由 于空气中的水分而结露。润滑不良。措 施:改善密封装置。充分过滤润滑油。使用 合适的润滑剂。
轴承梨皮状点蚀分析
轴承磨损状态分析
• 所谓磨损蚀由于摩擦而造成滚道面或滚动 面,滚子端面,轴环面及保持架的凹面等 磨损。原 因:异物侵入,生锈电蚀引起的 发展。润滑不良。由于滚动体的不规则运 动而造成的打滑。措 施:改善密封装置。 清洗轴承箱。充分过滤润滑油。检查润滑 剂及润滑方法。防止非直线性。
轴承磨损分析
轴承微振磨损状态分析
• 由于两个接触面间相对反复微小粉末, 因而页称微振磨损腐蚀。原 因:润滑不良。 小振幅的摇摆运动。过盈量不足。措 施: 使用适当的润滑剂,加预压,检查过盈量, 向配合面上涂润滑剂。
轴承微振磨损状态分析
轴承损坏状态分析
技术培训
轴承损伤状态分析
• 轴承再承受载荷旋转时,内圈、外圈的滚 道面或滚动体面由于滚动疲劳而呈现鱼鳞 状的剥离现象。原 因:载荷过大。安装不 良(非直线性)力矩载荷异物侵入、进水。 润滑不良、润滑剂不合适轴承游隙不适当。 轴承箱精度不好,轴承箱的刚性不均轴的 挠度大生锈、侵蚀点、擦伤和压痕(表面 变形现象)引起的发展。措 施:检查载荷 的大小及再次研究所使用的轴承改善安装 方法改善密封装置、停机时防锈轴承再承
轴承断裂原因

二、生产与设备
1.锻造:锻造过程中若产生过烧、过热、内裂成网状碳化物等都会降低套圈的韧性和强度。所以必须始终严格控制加工温度、循环加热和锻后散热条件(如喷冷却)等,特别是地较大品种套圈终锻后,温度在700℃以上的,不得堆积摆放。
2.热处理:对热处理设备密切监控是车间一项重要工作。
淬火冷却条件。为解决中大型品种轴承套圈软点等缺陷,应测定淬火油的成分和性能,不合要求的要预以更换,以快速淬火油替代,以增强淬为介质淬透能力,改善淬火冷却条件。
严格回火工艺。针对断裂现象发生较多的品种,在其套圈粗磨后进行二次回火,这样既可进一步稳定套圈的组织和尺寸,又可减沁磨削应力,改善磨削变质层性能。近期已对22328/02及22236/02两个品种实行二次回火工艺,有待售后跟踪反馈验证。
套圈断裂是困扰轴承质量的问题之一,而缺陷断裂是套圈断裂的主要存在形式,其产生原因主要是原材料自身问题或生产操作不当,设备不能正常运行造成。现结合实际浅析如下。
一、原材料
原材料夹杂、疏松、脆性元素偏析或碳化物液析、网状、带状、不幸免匀偏聚等缺陷在加工工中不被消除或改善时,都会造成应力集中,削弱套圈基本强度,成为裂纹源。预防措施是坚持主渠道供货,尽量采购质量稳定可靠的钢材,加强对购进钢材的入库检查,从源头把好关。
三、套圈过载断裂和疲劳断裂的可能性同时存在,特别是服役条件差的轴承(如22328等)。对套圈断裂现象的研究,不仅要从材料和生产过程中产生的缺陷这些角度去考虑,还要对轴承零件的结构尺寸、加工测量手段、加工工艺、轴承服役条件等因素进行研究分析。
1.轴承结构和服役条件。不同的结构适合不同的服役条件;轴承零件结构不同其加工工艺就不尽相同,也就影响到其质量。因此我们应开发新结构产品,以适应不同的服役条件,并可在轴承使用说明上注明其适合的服役条件或性能,以方便客户的选择。
轴承钢棒料内部裂纹原因

轴承钢棒料内部裂纹原因一、材料组织原因轴承钢棒料的内部裂纹往往与材料的组织有关。
首先,轴承钢棒料中的非金属夹杂物如硫化物、氧化物等会降低材料的韧性,使其易于产生裂纹。
其次,轴承钢棒料的晶粒尺寸如果过大,会增加材料的内部应力,从而导致裂纹的生成和扩展。
此外,轴承钢棒料的冷处理过程中,如果温度和时间控制不当,也会导致材料的组织不均匀,从而引发内部裂纹的形成。
二、制造工艺原因轴承钢棒料的制造工艺也是导致内部裂纹的一个重要原因。
首先,轴承钢棒料的热处理工艺如果控制不当,会导致材料的组织不均匀,从而引发内部裂纹。
其次,制造过程中的机械加工操作如果过于粗糙或不符合要求,也会在材料表面产生划痕和裂纹,进而影响到材料的内部完整性。
此外,轴承钢棒料在冷却过程中如果受到不均匀的应力作用,也会导致内部裂纹的生成。
三、使用环境原因轴承钢棒料的使用环境也会对其内部裂纹的形成起到一定影响。
首先,轴承钢棒料在高温或低温环境下,由于温度的变化会引起材料的热胀冷缩,从而导致内部应力的积累,进而产生裂纹。
其次,轴承钢棒料在潮湿或腐蚀性环境中,会加速材料的腐蚀和氧化,从而削弱材料的强度和韧性,导致内部裂纹的生成和扩展。
此外,轴承钢棒料在使用过程中如果受到过大的载荷或振动,也会引起材料的应力集中,进而导致内部裂纹的形成。
针对轴承钢棒料内部裂纹的原因,我们可以采取一些措施来预防和控制。
首先,在材料的选型过程中,应选择具有良好韧性和均匀组织的轴承钢棒料,以减少内部裂纹的发生。
其次,在制造过程中,应严格控制材料的热处理工艺和机械加工操作,确保材料表面的完整性和内部的均匀性。
此外,对于使用环境的要求,应选择适当的轴承钢棒料,并采取防腐蚀和防振动措施,以延长材料的使用寿命。
轴承钢棒料内部裂纹的原因主要包括材料组织、制造工艺和使用环境等方面。
了解并控制这些原因,可以有效预防和减少轴承钢棒料的内部裂纹问题的发生,提高材料的质量和可靠性。
轴承内圈滚道剥落原因

轴承内圈滚道剥落原因
轴承内圈滚道剥落的原因可能有以下几点:
1.轴承在制造过程中,滚道表面粗糙度差,在制造、装配或使用过程中有杂质进入滚道,造成滚动体在运行中滚动阻力增大,从而产生滚道表面早期磨损或剥落。
2.轴承在安装时,如果安装过紧或使用过程中发生轴的弯曲变形,会使得轴承保持架承受额外的径向力,造成轴承保持架断裂或轴承外圈与安装轴承孔脱离。
3.轴承的润滑不良,如润滑油中含有杂质或不足,也会造成轴承滚道表面早期磨损或剥落。
4.轴承长期超速运转,也会导致轴承保持架断裂或轴承外圈与安装轴承孔脱离。
5.轴承的安装不正确,如安装倾斜或轴弯曲,也会导致轴承滚道表面早期磨损或剥落。
为了防止轴承内圈滚道剥落,应选用合格的润滑油进行润滑,避免使用不清洁的润滑油;保持适当的轴承转速,避免超速运转;正确安装轴承,避免倾斜或轴弯曲。
同时,应定期检查轴承的运行状况,发现异常应及时处理。
轴承内圈滚道剥落原因

轴承内圈滚道剥落原因
1. 过载:当轴承承受的负荷超过其设计承载能力时,内圈滚道表面的材料可能会因过度应力而剥落。
2. 润滑不良:轴承在缺乏足够的润滑剂或润滑剂失效的情况下运行,会导致摩擦和磨损增加,从而使内圈滚道表面的材料剥落。
3. 污染:进入轴承的杂质、颗粒或污染物可能会导致内圈滚道表面的磨损和剥落。
4. 安装不当:不正确的安装方法,如过紧的安装或不均匀的负荷分布,可能会导致内圈滚道表面的应力集中,从而引发剥落。
5. 材料缺陷:轴承内圈滚道材料本身存在缺陷,如裂纹、夹杂或材料不均匀,可能会导致剥落问题。
6. 疲劳:在长期的交变载荷作用下,轴承内圈滚道表面可能会出现疲劳裂纹,最终导致材料剥落。
为了避免轴承内圈滚道剥落问题,应确保正确的安装和维护,定期检查和更换润滑剂,并避免过度负载和污染。
如果发现轴承内圈滚道剥落,应及时更换轴承以确保设备的正常运行。
- 1、下载文档前请自行甄别文档内容的完整性,平台不提供额外的编辑、内容补充、找答案等附加服务。
- 2、"仅部分预览"的文档,不可在线预览部分如存在完整性等问题,可反馈申请退款(可完整预览的文档不适用该条件!)。
- 3、如文档侵犯您的权益,请联系客服反馈,我们会尽快为您处理(人工客服工作时间:9:00-18:30)。
!墨型!鲤Q二!!鲤CN41一1148/TH轴承2叭0年8期Bearing2010,No.839—4022324轴承内圈滚道面开裂原因分析王学平,邓有云(六安滚动轴承有限公司,安徽六安237161)摘要:GCrl5钢制22324内圈采用常规淬、回火热处理工艺后,经粗磨后滚道面局部发生开裂及翘皮现象。
采用金相及热酸洗的方法对该现象进行了分析,结果表明,内圈滚道面上的开裂及翘皮现象是由于磨削裂纹引起的。
通过调整磨削工艺,规范磨削操作,杜绝了磨削烧伤和裂纹。
关键词:滚动轴承;内圈;金相分析;磨削裂纹中图分类号:THl33.33;TGll5.21文献标志码:B文章编号:1000-3762(2010)08—0039—021存在的问题2检验某一22324轴承内圈,系由GCrl5钢制造,采用常规淬、回火工艺进行热处理。
在粗磨内圈滚道面后,经磁粉探伤发现滚道的两侧,尤其是靠近油沟处出现许多细小裂纹,个别套圈还出现了多道较深的、垂直于砂轮磨削方向的开裂及翘皮现象,其开裂形貌如图1所示。
经线切割后,还出现整块材料从滚道面脱落现象。
图1裂纹形貌收稿日期:2009—12—28;修回日期:2010—03—262.1金相检验从出现开裂的轴承套圈上切取一块试样(将裂纹沿纵向解剖),制备成金相试样后,放置在光学显微镜下观察并按照JB/T1255—2001标准进行评定,结果如下:(1)滚道表面存在严重的二次淬火层和高温回火层,二次淬火层深度约0.2mm,高温回火层深度约1.0mm。
金相组织见图2。
(2)裂纹起源于滚道表面的高温回火层,深度图2二次淬火层+高温回火层金相组织步地完善。
参考文献:【1]梁波,葛世东,席颖佳.宇航固体润滑轴承技术[J].轴承,2001(5):8—12.[2]刘继奎,高星.太阳帆板驱动机构固体润滑轴承的跑合技术实践[J].控制工程,2003(2):1-5.[3]郭青.二硫化钼固体润滑性能及其应用[J].精密[4][5]制造与自动化,2007(3):26—29.叶军.卫星用固体润滑轴承的研究[D].合肥:合肥工业大学硕士论文,2004.HawthorneHM.TribomaterialFactorsinSpaceMecha-nismBrakePerformance[c]∥ProceedingsofSym-posiumSponsoredbytheNationalAeronauticsandSpaceAdministration.1990(4):18—20.(编辑:赵金库)·40·《轴承))2010.№.8约2.5mm,其形貌见图1和图3‘11。
(3)裂纹两侧未发现有脱贫碳现象(图3)。
(4)内圈的淬回火马氏体组织为4级,符合标准要求。
图3裂纹两侧无脱碳2.2热酸洗检验将线切割过程中表面发生脱落的试样按照JB/T1255—2001标准附录c进行热酸洗,结果发现:两侧滚道面均有裂纹,裂纹的形状多为网状,也有垂直于磨削方向的直线裂纹,见图4。
图4热酸洗后滚道面裂纹形貌3结果分析在热处理过程中,内圈滚道面往往会因为较深的车刀痕、热处理组织过热或因返修致使表面严重脱碳而产生裂纹【2J。
在磨削过程中,也会因为磨削热而产生磨削裂纹。
磨削热与砂轮磨削力和磨削速度成正比。
由于磨削力和磨削速度很大,因此,磨削热会很大,瞬间温度可达800—1500cc。
在磨削过程中,如果散热措施不好,很容易造成工件表面烧伤,而GCrl5轴承钢是导热性较差的材料,操作不当很容易烧伤。
此外,工件表面高温也容易造成工件表面发生二次淬火,产生较大的应力而引起裂纹[3】。
热处理裂纹的特点是裂纹一般较深且细,裂纹两侧没有脱碳;而磨削裂纹一般较浅,裂纹两侧无脱碳,烧伤层金相组织会因二次淬火及高温回火而发生明显的变化。
根据受检内圈金相组织和裂纹形貌初步判断如下:(1)裂纹两侧无脱碳,裂纹产生于热处理或磨削工序;(2)滚道表面存在严重的二次淬火和高温回火层,酸洗后裂纹分布呈网状或与磨削方向垂直,而淬火马氏体在合格范围内,因此,内圈滚道面上的裂纹是磨削裂纹。
内圈一侧滚道面上的裂纹较深,说明该侧滚道面在磨削过程中所承受的磨削应力和热应力均较大,因而造成金属脱落的面积及厚度也较大。
由以上分析可以确定,送检的22324轴承内圈滚道面裂纹为磨削裂纹,其是造成滚道面开裂及翘皮的主要原因。
4预防措施为避免磨削裂纹的产生就要减少磨削热的产生和加速热量的散发。
可以采取的预防措施有:(1)选择恰当的切削液,进行充分而均匀的冷却。
(2)选择合适的砂轮。
在磨料确定的前提下,可选用硬度较低、组织号大的砂轮并及时修整,因为大气孔砂轮自锐性好,散热性佳,可有效避免烧伤和磨削裂纹。
(3)合理选择磨削进给量旧J,减小进刀量,提高工件圆周速度也可降低磨削温度,减少烧伤,从而避免磨削裂纹。
因此,采取的措施是:(1)精心调整设备,杜绝大进给量磨削,采用均匀进给,小火花磨削,2s无火花光磨加缓慢退刀的操作规程。
(2)确保冷却液对试件进行充分而均匀的冷却。
(3)选用硬度级别为J,组织号为6的橡胶砂轮。
通过采取上述措施后,再未出现类似的滚道面磨削开裂及翘皮现象。
参考文献:[1]雷建中.轴承钢纯洁度对轴承疲劳寿命的影响[C].轴承用材料“十五”发展战略研讨会论文集,2003.[2]技工学校机械类通用教材编审委员会.热处理工艺学[M].北京:机械工业出版社,1980.[3]轴承行业教材编审委员会.轴承磨工工艺学[M].北京:机械工业出版社,1986.(编辑:赵金库)22324轴承内圈滚道面开裂原因分析作者:王学平, 邓有云, WANG Xue-ping, DENG You-yun作者单位:六安滚动轴承有限公司,安徽,六安,237161刊名:轴承英文刊名:BEARING年,卷(期):2010,(8)被引用次数:0次1.雷建中轴承钢纯洁度对轴承疲劳寿命的影响 20032.《技工学校机械类通用教材》编审委员会热处理工艺学 19803.《轴承行业教材》编审委员会轴承磨工工艺学 19861.期刊论文周爱华.郑永伟.ZHOU Ai-hua.ZHENG Yong-wei基于小波变换的滚动轴承内圈故障诊断-机械与电子2010(6)利用小波变换将滚动轴承故障振动加速度信号分解到不同尺度,对包含有故障特征频率的小波系数进行Hirbert变换解调,最后对解调后的信号进行频谱分析获取轴承故障特征信息.实例分析表明,利用小波变换进行滚动轴承内圈故障诊断具有良好的诊断效果.2.期刊论文裴礼清.张峰.Pei Liqing.Zhang Feng滚动轴承的滚动体与内圈接触部分的相对滑动分析-机械设计与研究2000(2)本文作为滚动轴承微动磨损研究的一个部分,对滚动体与内圈滚道接触部分的微小滑动进行了研究,其分析有助于揭示滚动轴承微动磨损的机理.本文以中国轴承厂生产的深沟球轴承为模型,对接触部分进行有限元分析,结果表明,切向力的作用与滑动区域的形状无关,差动滑动的滑动量要大于或等于切向力产生的滑动量.3.学位论文田英滚动轴承内圈故障劣化状态辨识的研究2008随着工业生产现代化的发展,设备维修方式正在逐步转向预知维修,设备故障诊断技术是实现预知维修技术的保证。
滚动轴承是现代工矿企业中常用的机械零件,在整个生产设备中起着关键的作用。
为了对滚动轴承实现预知维修,保证其正常运行,需要准确地发现故障类型,更需要及早地发现故障劣化程度,所以对滚动轴承内圈故障劣化状态辨识的研究具有重要的理论和应用价值。
本文在广泛收集相关资料的基础上,提出将希尔伯特-黄变换(Hilbert-huang Transform简称HHT)和球结构支持向量机相结合应用于滚动轴承内圈故障劣化状态的识别方面,并且对辨识结果进行可视化,充分验证了这种方法是可行的。
本文主要做了以下几方面的研究工作:分析了滚动轴承的特征频率、正常状态的振动信号特征和内圈故障的振动信号特征。
搭建了滚动轴承故障诊断系统模型,采集了滚动轴承从正常、内圈轻微故障、中度故障、重度故障逐步劣化的振动信号。
阐述了目前先进的时频信号处理方法Hilbert-huang的原理。
采用EMD分解和小波分解对相同的仿真信号进行了分析和比较。
使用Hilbert边际谱和功率谱对滚动轴承内圈故障的劣化状态信号进行了分析,结果表明Hilbert谱分析有更高的分辨率,但是单靠谱分析还不能很好地识别滚动轴承内圈故障劣化的程度,需要提取特征向量,并将其映射到高维空间进行模式识别。
EMD方法是一种自适应的时频分析方法,可以更准确地把握信号的特征信息。
本文采用内禀模态能量熵和内禀模态奇异值方法来提取滚动轴承内圈故障劣化程度的特征。
通过比较结果,内禀模态奇异值方法可以更有效地提取出滚动轴承内圈故障的劣化程度特征,随着滚动轴承内圈故障逐步劣化时,奇异熵值逐步变小。
在此基础上,研究了用球结构支持向量机作分类器,对滚动轴承内圈故障的劣化程度进行识别的理论和方法。
同时对核函数问题进行了探讨,表明径向基核函数比较适合球结构支持向量机。
求出了不同故障程度下的类中心(即球心)及类半径,研究了它们的变化规律。
此外,本文还利用主成份分析和基于色度图的高维数据可视化技术研究了球结构支持向量机辨识结果(高维)的二维空间显示,使球结构支持向量机的辨识结果直观化。
本文的研究结果表明,HHT和球结构支持向量机相结合的这种方法能够准确地识别滚动轴承内圈故障的劣化状态,为滚动轴承的故障诊断提供了一种有效的方法。
4.期刊论文袁立福.赵金辉.Yuan Lifu.Zhao Jinhui铁路货车滚动轴承内圈滚道检查仪的设计与应用-铁道机车车辆工人2010(6)在以往对货车滚动轴承内圈滚道面的实际检查中,操作人员都是通过带有光源的放大镜对被测面进行检查,这样容易造成视觉疲劳,且工作时间长还会发生漏栓等情况,因此研制了"铁路货车轴承内圈滚道检查仪系统".提高了工作效率和检查质量,降低了劳动强度.5.期刊论文宋延辉.李吉.刘鹏虎.王珍.SONG Yan-hui.LI Ji.LIU Peng-hu.WANG Zhen滚动轴承内圈圆、粗糙、波纹度的综合检测-辽宁工程技术大学学报(自然科学版)2005,24(z1)阐述了滚动轴承误差检测的基本理论,并设计开发了一种检测系统,该系统采用了高精度差动式磁芯型电感位移传感器和小波包分解与重构技术.通过对轴承内圈表面特征数据一次采样,实现表面圆度、粗糙度、波纹度误差的综合检测和分析评定.通过对406型轴承的实测数据进行处理,成功实现了三种误差信号的分离,实验证明了该系统的可靠性和实用性.6.期刊论文蔡海潮.李孟源.靳颜博.张小瑞.CAI Hai-chao.LI Meng-yuan.JIN Yan-bo.ZHANG Xiao-rui铁路货车轮对轴颈轴承内圈松动故障检测-轴承2007(2)采用声发射和振动加速度传感器对铁路货车轮对轴承内圈松动故障进行检测,并用小波包分析方法提取故障信号的能量特征向量,通过对内圈不松动和松动两种情况下能量分布的比较,提取高频带内能量与总能量之比作为特征参数,可有效诊断内圈松动故障.车辆2010,30(5)针对轴承滚道面视觉检查现状,研制开发了铁路货车轴承内圈滚道检查仪系统,介绍了检查仪的设计原理、特点及软件结构,并对现场应用情况进行了阐述.8.期刊论文方乾杰.马万明.原继红.FANG Qian-jie.MA Wan-ming.YUAN Ji-hong轻窄系列轴承内圈Sd的工序间检测-轴承2009(11)针对d/B≥4轻窄系列轴承内圈Sd在工序间检测中存在的问题,根据GB/T307.2中测量Sd的规定,提出了基于D902内径检测仪的Sd测量方案,分析了检测系统误差的影响因素,通过D902仪器的重新构建,实现了轻窄系列轴承内圈Sd的工序间检测.9.期刊论文李莉萍.钱晓光.邓伟宾6213轴承内圈裂纹的原因分析-轴承2008(4)采用理化分析的方法,对6213轴承内圈产生裂纹的原因进行分析,结果表明,由于淬火温度过高或保温时间过长,导致针状马氏体组织粗大,造成轴承内圈产生裂纹.10.期刊论文卢福宝滚动轴承内圈疲劳失效的故障诊断-有色设备2002(5)介绍一种滚动轴承故障的诊断方法,可以缩小故障部位范围,缩短设备检修时间.本文链接:/Periodical_zc201008012.aspx授权使用:大连理工大学图书馆(dllg),授权号:bcac78f5-a03e-4baa-a2de-9ea1004596b0下载时间:2011年3月9日。