基础工业工程课程设计
基础工业工程课程设计报告

基础工业工程课程设计报告1. 引言本次课程设计旨在通过实际案例的研究,帮助学生深入了解基础工业工程的核心概念和方法。
在本次设计中,我们选择了一个实际的生产流程进行分析和优化,以提高生产效率和降低成本。
2. 问题陈述在现有的生产流程中,我们面临以下问题:1.生产效率较低:由于某些环节存在瓶颈,导致整个生产流程的效率不高。
2.资源利用不足:部分设备和人力资源的利用率较低,造成资源浪费。
3.质量控制不稳定:在生产过程中存在一些误差和变异,导致产品质量不稳定。
3. 方法和过程针对以上问题,我们使用了以下方法进行优化:1.流程分析:通过详细的流程分析,找出流程中的瓶颈和不必要的环节。
2.设备优化:对部分设备进行改进和升级,以提高生产效率和资源利用率。
3.人力调整:根据实际需求,合理安排人力资源,以提高工作效率和降低成本。
4.质量控制:引入更严格的质量控制措施,减少产品误差和变异。
在具体的设计过程中,我们采用了以下步骤:步骤1:流程分析首先,我们对现有生产流程进行了详细的分析。
通过对每个环节的时间、资源和人力成本的评估,我们找出存在问题的环节,并确定优化的方向。
步骤2:设备优化针对流程中的瓶颈环节,我们对相关设备进行了优化。
通过改进设备的性能和功能,减少故障和停机时间,提高生产效率。
步骤3:人力调整在分析了生产流程后,我们发现有些环节的人力利用率较低。
因此,我们对人力资源进行了调整。
将工作时间和任务分配进行优化,以提高工作效率。
步骤4:质量控制为了确保产品的质量稳定,我们引入了更严格的质量控制措施。
通过提高检测频率和质量标准,降低产品误差和变异。
4. 结果和讨论通过对生产流程的优化,我们取得了一些显著的改善:1.生产效率提高:流程中的瓶颈环节被消除或减少,导致整个流程的生产效率得到提高。
2.资源利用率提升:设备和人力资源的利用率得到了提高,减少了资源的浪费。
3.质量控制稳定:引入更严格的质量控制措施后,产品质量的稳定性得到了提高。
基础工业工程课程设计
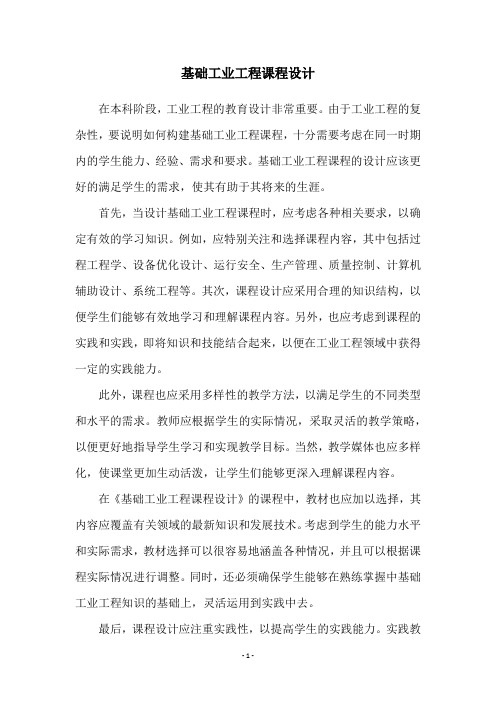
基础工业工程课程设计在本科阶段,工业工程的教育设计非常重要。
由于工业工程的复杂性,要说明如何构建基础工业工程课程,十分需要考虑在同一时期内的学生能力、经验、需求和要求。
基础工业工程课程的设计应该更好的满足学生的需求,使其有助于其将来的生涯。
首先,当设计基础工业工程课程时,应考虑各种相关要求,以确定有效的学习知识。
例如,应特别关注和选择课程内容,其中包括过程工程学、设备优化设计、运行安全、生产管理、质量控制、计算机辅助设计、系统工程等。
其次,课程设计应采用合理的知识结构,以便学生们能够有效地学习和理解课程内容。
另外,也应考虑到课程的实践和实践,即将知识和技能结合起来,以便在工业工程领域中获得一定的实践能力。
此外,课程也应采用多样性的教学方法,以满足学生的不同类型和水平的需求。
教师应根据学生的实际情况,采取灵活的教学策略,以便更好地指导学生学习和实现教学目标。
当然,教学媒体也应多样化,使课堂更加生动活泼,让学生们能够更深入理解课程内容。
在《基础工业工程课程设计》的课程中,教材也应加以选择,其内容应覆盖有关领域的最新知识和发展技术。
考虑到学生的能力水平和实际需求,教材选择可以很容易地涵盖各种情况,并且可以根据课程实际情况进行调整。
同时,还必须确保学生能够在熟练掌握中基础工业工程知识的基础上,灵活运用到实践中去。
最后,课程设计应注重实践性,以提高学生的实践能力。
实践教学应以学生的参与和实践为核心,以提高学生的分析问题和解决问题的能力为目标。
教师应带领学生参与有关实践项目,共同调研和探索,以便学生能够以正确的方式运用工业工程知识。
以上就是对基础工业工程课程设计的一般性介绍。
在设计过程中,教师应考虑知识结构、实践性和实践要求,以保证基础工业工程课程的有效性与实用性。
只有这样,学生才能在未来的工作中产生最大的价值,在工业工程领域取得成功。
基础工业工程课程设计

根底工业工程课程设计题目: 云南农业大学回族食堂效劳效率的评析与改善学院: 工程技术学院专业班级: 10 级工业工程学生姓名: 学号:名目1. 食堂简介2.选题背景3.课程设计及其目的4.农大回族食堂场景描述4.1.农大回族食堂平面布置线路图4.2.对目前食堂就餐流程进展记录、分析4.3.模特排时法对改进前的动作分析4.4.改进前流程程序图〔物料型〕4.5.改进前人员流程程序图5.作业分析5.1双手作业分析5.2人—机作业分析6.现场治理7.食堂就餐存在问题及改善方案7.1 存在的问题7.2就餐要点改进7.3改进后食堂就餐要点7.4改进后人员流程程序图7.5模特排时法对改进后的动作分析7.6 改进后流程程序图〔物料型〕7.7改善后分析及结论8.总结一、食堂简介温饱是人类生存最根本的需求,不管你是在哪里,你首先要考虑的就是先解决温饱问题,而食堂就是帮你解决温饱问题的一个场所。
由于每个地方的风俗以及外界环境不同,每个食堂的治理制度也是不一样的,因此,不同地方的食堂都有不同的现状。
回族食堂位于集中片区食堂中的一个,是效劳全校回族以及局部非回族学生及教师的食堂。
二、选题背景大学食堂的状况与大学生有着亲热的联系。
对于回族食堂来说,由于回族食堂的地理位置比较好,处在东校区众多宿舍的中心,且处在塑胶篮球场和足球场之间,运动的学生比较多,价格实惠,因此回族食堂已经成为东校区这边的多数大学生就餐的首要选择。
回族食堂的经营方式是以私营为主,它的规模不大。
回族食堂以学生为主要消费人群,价格较低,通过向大学生供给经济快捷的餐饮效劳来赚取利润。
三、课程设计及其目的本课程设计的主要选择大学生在回族食堂就餐过程进展流程程序分析。
此次课程设计主要通过自己寻常对生活的观看。
作为一名工业工程的学生,养成敏锐的观看力是格外重要的,同时也是理论联系实际的一个过程。
通过观看生活,把工业工程方面的学问运用到生活中去,进一步的理解、消化、把握课堂上所学习的专业根底学问。
基础工业工程课程设计

基础工业工程课程设计
机械制造与自动化是机械工程专业必修的一门基础工业工程课程,本课程的设计侧重
于培养学生的工业工程理念,理论知识和实践能力,帮助他们了解工厂流程的整体规划。
第一部分,让学生了解和掌握基本的机械原理,重点讲解机械结构、几何形状、刚度,振动、材料加工和表面抛光等重要知识,有助于开发和设计机械系统。
第二部分,介绍工业自动化技术,以及其在机械零件产生、装配、运输、检测或测试
等工序中的应用,有助于降低生产成本,提高产品质量等。
第三部分,让学生进行机械模型设计和分析,同时要求学生了解和掌握机械设计原理、结构分析、力学性能和加工参数等理论,包括CAD和CAE(计算机辅助分析和设计)软件的
运用。
最后部分,加强学生的实践能力,让学生对机械系统的整体组装、拆装和调试有深刻
的了解,并结合上述4种方法,运用计算机技术,制作模拟试验设计、装配拆卸工艺及零
件特性测试等系统工艺设计,实现实践技能的全面落实和提高。
本课程的一个关键目标是让学生充分了解机械设计、制造和技术,以便能够提高生产
效率,有效地优化机械系统以及机械系统中的制造工艺。
基础工业工程教学设计

基础工业工程教学设计1. 概述基础工业工程是一门重要的专业,它与各种制造行业有着密不可分的联系。
在教学中,如何设计恰当的课程结构和实验方案至关重要。
本文将介绍如何设计一份高质量的基础工业工程教学方案。
2. 课程结构设计在设计基础工业工程的课程结构时,首先需要根据学生的专业背景和知识水平进行划分。
下面是一个典型的基础工业工程课程结构:•课程介绍•工程设计基础•工程图样和标准符号•工程测量学•材料学基础•机械加工工艺学•制造工艺学基础•工装设计基础•物流与供应链管理在每个阶段,教学应该注重对学生理论知识的讲解,并结合实践,让学生在实验过程中逐渐掌握基础工业工程的核心技能。
其中,工程测量学和工装设计是非常重要的环节,因为它们关乎到制造流程中的精度和效率。
3. 实验设计实验设计是基础工业工程中最为重要的环节之一。
下面列举了一些基础工业工程实验的范例:3.1 工程测量这是一种重要的实验,它可以帮助学生了解仪器的运作原理,让他们能够使用各种工具和标准来测量不同类型的零件。
这些实验可以包括:•精密测量器的使用和规格•轮廓仪、投影仪和影像扫描仪的使用•水平仪和望远镜的使用3.2 工程图样和标准符号工程图样和标准符号非常重要,他们是制造流程中正确交流的关键。
这些实验可以包括:•使用不同类型的绘图工具和掌握相关的标准符号•熟悉ISO和ANSI的标准•学习如何使用自动CAD和其他图形软件3.3 机械加工工艺学机械加工是基础工业工程中重要的一环。
在这个部分,学生将学会如何使用各种切削工具和其他机械工具。
下面列举了一些具体的实验:•研究高速钻头、卡盘和其他机械工具•车床和铣床的使用和操作•切削气体和金属热处理4. 课程教学方法与其他领域不同,基础工业工程的教学需要结合到实践环节。
因此,在教学过程中,教师应该注重课堂与实验的平衡。
下面列举一些可能有效的教学方法:•制定详细的教学计划,确保教学过程能够顺利进行。
•组织小组研究,让学生分工,相互配合,完成实验和项目。
基础工业工程课程设计

基础工业工程课程设计前言基础工业工程课程作为一门重要的工程学科,主要研究工业系统的设计和优化,提高生产效率和经济效益。
在这门课程中,学生需要学习各种工具和技术,包括系统分析、生产线设计、物流管理等,以及如何将这些知识应用于实际生产中。
在课程结束时,通过一次课程设计,学生将能够将所学到的知识应用到实际情境中,提高综合应用能力、创新思维和解决问题的能力。
课程设计要求项目背景某高科技公司的生产线分为A、B两个部分,现在需要重新设计生产线,使得成本和生产效率得到提高。
需要将原有的生产线进行分析、优化并提出改进方案。
项目目的通过本次课程设计,学生应该能够:1.进行生产线设计和优化2.使用系统分析方法进行业务过程分析3.运用物流管理知识提高生产效率4.提高团队协作和沟通能力项目要求团队人数为3-5人,完成以下任务:1.分析原有A、B两个生产线的生产效率和成本,制定优化计划2.设计新的生产线方案,并进行成本、效率分析3.提出改进方案及操作手册时间安排•第1周:组队,确定课题•第2-3周:初步了解业务流程,形成流程图•第4-5周:进行业务过程分析,确定优化方案•第6-7周:设计新的生产线方案,并进行成本、效率分析•第8周:撰写课程设计报告报告要求1.报告应该包括以下内容:项目背景、目的、任务、时间安排和参考文献。
2.课程设计报告应以Word或PDF文档形式提交,不超过10页。
3.报告中应包括生产线设计图、流程图、成本和效率分析表格等。
总结基础工业工程课程设计旨在通过实际项目,提高学生的实践能力和团队协作能力,以及深入了解生产线设计、物流管理等工业工程的知识。
学生将会通过分析业务流程、制定优化方案、设计新的生产线方案等环节,掌握实际工作的技能和方法,为将来的就业和职业规划打下坚实的基础。
工业工程基础课程设计
工业工程基础课程设计一、课程目标知识目标:1. 让学生理解工业工程的基本概念,掌握其核心原理和应用领域;2. 使学生掌握工业工程中常用的数据分析方法,并能运用到实际问题的解决中;3. 帮助学生了解我国工业发展现状,认识到工业工程在提高企业竞争力中的作用。
技能目标:1. 培养学生运用工业工程原理和方法分析、解决实际问题的能力;2. 提高学生在团队协作中运用工业工程知识进行项目设计的能力;3. 培养学生运用信息技术工具进行数据收集、处理和分析的能力。
情感态度价值观目标:1. 激发学生对工业工程的兴趣,培养其探究精神和创新意识;2. 培养学生关注我国工业发展,增强国家意识和社会责任感;3. 引导学生树立正确的人才观,认识到工业工程师在社会主义现代化建设中的重要作用。
课程性质:本课程为工业工程专业基础课程,旨在帮助学生建立工业工程的基本概念,培养实际操作能力,提高学生的综合素质。
学生特点:学生具备一定的数学、物理和计算机基础,具有较强的逻辑思维能力和动手能力,但对工业工程的实际应用了解有限。
教学要求:结合学生特点,注重理论联系实际,采用案例教学、分组讨论、实践操作等多种教学方法,提高学生的知识水平和实践能力。
在教学过程中,关注学生的学习进度和反馈,及时调整教学策略,确保课程目标的实现。
通过本课程的学习,使学生能够将所学知识运用到实际工作中,为我国工业发展做出贡献。
二、教学内容1. 工业工程基本概念与原理:包括工业工程的定义、发展历程、核心原理和应用领域,以课本第一章内容为基础,使学生建立对工业工程的初步认识。
2. 数据分析方法:教授工业工程中常用的数据分析方法,如统计过程控制、方差分析等,结合课本第二章内容,培养学生分析数据、解决问题的能力。
3. 工业工程应用案例:分析国内外典型工业工程应用案例,以课本第三章内容为参考,使学生了解工业工程在实际生产中的重要作用。
4. 企业竞争力与工业工程:探讨工业工程在提高企业竞争力方面的作用,结合课本第四章内容,引导学生关注我国工业发展现状。
基础工业工程课程设计
项目内容与要求
01
项目要求
• 完成现场调研,收集相关数据和资料;
02
• 对生产系统或作业现场进行详细分析,识别存在的问题和改
03
进空间;
项目内容与要求
01
• 设计改进方案,并进行优化;
02
• 撰写课程设计报告,包括问题分析、方案设计和 实施效果预测等部分;
03
• 进行项目汇报和答辩。
项目实施计划
效果。
提升就业竞争力
通过课程设计,学生可以积累实际 工作经验,提高解决问题的能力, 增强就业竞争力。
个人能力全面发展
课程设计不仅培养学生的专业能力, 还注重学生的非专业能力的培养, 如团队协作、沟通协调等,有助于 学生的全面发展。
02
工业工程概述
工业工程的定义与特点
定义
工业工程是一种对人员、物料、 设备、能源和信息所组成的集成 系统进行设计、改善和设置的工 程学科。
培养实际操作和创新能力
02
课程设计将注重学生的实际操作和创新能力的培养,通过解决
实际问题,提高学生的实践能力和创新思维。
提升团队协作和沟通能力
03
在课程设计中,学生将分组进行项目实践,培养团队协作精神,
提升沟通协调能力。
课程设计的重要性
理论与实践相结合
课程设计将工业工程的理论知识 与实践相结合,帮助学生更好地 理解和应用所学知识,提高学习
流程分析概述
流程分析的步骤
流程分析的工具
流程分析的应用
流程分析是对工作流程的系 统分析和优化,目的是提高 工作效率、降低成本并改善 工作质量。
流程分析主要包括对工作流 程的识别、分析和改进三个 步骤,识别是对工作流程的 全面了解和梳理,分析是对 工作流程的评估和优化,改 进则是根据分析结果提出改 进措施并实施。
《基础工业工程》课程设计指导书
《基础工业工程》课程设计指导书一、课程设计的目的及要求1、巩固和加深学生在《基础工业工程》课程中所学的程序分析技术、操作分析技术、作业测定技术、标准时间定额以及基础工业工程各项实验,使学生熟练掌握工业工程的基本分析方法,培养学生计算、设计、绘图、文献查阅、报告撰写等基本技能;2、培养学生独立分析和解决工程实际问题的能力;3、培养学生的团队协作精神、创新意识、严肃认真的治学态度和严谨求实的工作作风。
二、课程设计内容及要求1、针对某一制造过程中某项作业所经过的工作程序,运用所学程序分析技术(工艺程序分析、流程程序分析、搬运分析、管理事务流程分析等)、“5W1H”提问技术和“ECRS”优化原则分析现有工作程序,并提出相应的改进方案。
要求:程序分析的目的是改善生产过程中不经济、不合理、不科学的作业方法、作业内容以及现场布置,是工序管理、搬运管理、布局管理、作业编制等获取基础资料的必要手段,在进行程序分析时可以从以下几个方面入手:1)从流程上入手。
可以发现工艺流程中是否存在不经济、不合理、停滞和等待等现象。
2)从工序上入手。
可以发现加工顺序是否合理、流程是否畅通、设备配备是否恰当、搬运方法是否合理。
3)从作业入手。
可以发现工序中的某项作业是否一定必要、是否可以取消、是否有更好的方法。
程序分析的步骤大致分为:①选择,选择所需研究的工作;②记录,针对不同的研究对象采用相应的研究图表进行全面记录;③分析,用5W1H、ECRS四大原则进行分析、改进;④建立,建立最经济、最科学、最合理、最实用的新方法;⑤实施,实施新方法;⑥维持,对新方法经常性的检查,不断改善,直至完善等6大步骤。
2、针对某一制造过程中某项以操作为主体的工序操作过程,运用所学操作分析技术(人-机操作分析、工组联合操作分析、双手操作分析等)、“5W1H”提问技术和“ECRS”优化原则分析现有工作操作程序,并提出相应的改进方案。
要求:通过对以人为主的工序的详细研究,使作业者、作业对象、作业工具三者科学合理地布置和安排,以达到工序结构合理,减轻劳动强度、减少作业工时消耗、缩短整个作业的时间,以提高产品的质量和产量,其基本要求包括:1)通过删减、合并、简化,使操作总数减至最低、工序排列最佳,并使每一操作简单易行。
基础工业工程课程设计
目录一、绪论 (1)1.1 课程设计目的 (1)1.2企业背景 (1)1.3 实验背景简介 (2)二、现场动作调查及现行问题分析 (2)2.1试验仪器简介 (2)2.2 现场工作区域模拟图 (3)2.3 下导柱加工全过程的动素分析和问题分析: (4)2.3.1工件在车床上的安装过程 (4)2.3.2工件加工前的位置校对过程 (4)2.3.3工件的加工过程 (8)2.3.4 工件加工一次后进行测量核对过程 (8)2.3.5 原方案的动素分析和问题分析小结 (10)三、改善方案的制定与评价 (10)3.1 动作改善 (10)3.1.1 工件加工前的位置校对过程的动素改善方案 (10)3.1.2 工件每加工一次后进行测量核对过程的动素改善方案 (12)3.2 改善方案与原方案对比 (13)3.2.1工件加工前的位置校对过程的动素原方案与改善方案的对比分析 (13)3.2.2工件每加工一次后进行测量核对过程的动素原方案与改善方案的对比分析 (14)四、改善方案的标准化及实施 (15)五、课程设计总结 (15)5.1 面临的问题与问题的解决 (15)5.2 个人收获总结 (16)参考文献 (17)西安电力机械厂下导柱车加工过程动素分析一、绪论1.1 课程设计目的工业工程在中国是一门新兴的专业,还不是十分受到各个企业部门及工厂的重视,但是在国外工业工程倍受各个行业的高度重视和认可,有着十分深远的与美好的发展前景。
我们知道提高生产率、缩短工作时间、减小成本是每个企业行业的目标和愿望。
我们工业工程就是对这一方面进行优化改进。
虽然我们在学校学习的相关知识远远不足,所以通过查阅相关资料书籍、结合在学校已经学习了工业工程的相关知识进行合理的解决方案的设计需要实地调研考察才能得以实现。
因此我们迫切的希望能够有一次亲身实践的经历,通过实践增长知识掌握技能考察检验自己的实际应用能力。
也希望通过实践利用自己的实际能力为现实需解决的问题做一份贡献。
- 1、下载文档前请自行甄别文档内容的完整性,平台不提供额外的编辑、内容补充、找答案等附加服务。
- 2、"仅部分预览"的文档,不可在线预览部分如存在完整性等问题,可反馈申请退款(可完整预览的文档不适用该条件!)。
- 3、如文档侵犯您的权益,请联系客服反馈,我们会尽快为您处理(人工客服工作时间:9:00-18:30)。
《基础工业工程》
课程设计
学院:机械工程学院
专业:工业工程
班级:114120301
学号:
姓名:
指导教师:
提交时间:2016.11.28
一、装配线概况
本课程设计研究的是一级蜗轮蜗杆减速器的装配过程。
在这条装配线上,计划月产量为4800件,每月工作28天,每天工作8小时。
一级蜗轮蜗杆减速器的装配结构图如图1所示,BOM(Bill of Materials)表如表1所示。
图1减速器装配结构图
表1减速器BOM表
各操作工人的生产负荷尽量均衡,减少工人忙闲不均现象,使之按生产节拍运转和高效率生产,是极具现实意义的。
一级蜗轮蜗杆减速器的装配主要包括右端盖的安装、左端盖的安装、轴的安装、箱盖的安装、后箱盖的安装、注油塞安装等工序组成。
在该装配线上共
有6个工位,实际生产流程及各工位操作内容如图2所示.
图2 减速器装配流程
二、生产线现状及问题
1、生产线的作业测定
作业时间是核算生产线平衡率的基础数据,也是找出瓶颈工位的依据。
本研究采用秒表测时方法对生产线6个在线工位进行测定,结果如图3所示。
图3 各工位的标准时间
从以上搜集到的时间数据可以看出,除工位1、工位2和工位3基本符合生产节拍以外,其余各工位均远小于生产节拍,其中,工位4、工位5和工位6的标准时间分别为53s、56s、30s远小于其他各个工位,能力过剩,造成资源浪费,操作工人一直十分空闲,多数时间处于等待状态。
如果能将过剩的生产能力有效利用起来,生产效率必定会有大幅度提高。
2、生产线平衡分析
生产不平衡最大时间损失:
%100m ⨯⨯=
)
节拍()实际工位数目()
任务时间总和(平衡率CT T P
生产不平衡损失率=1-平衡率=1-61.52%=38.48%
由以上计算可知,在生产过程中,有38.48%的时间由于产线配置不平衡而损失了。
生产线生产不平衡最大时间损失为106s ,不平衡最大时间损失非常大,该生产线存在很大的改进空间。
1.3生产线的第一次优化分析 1、作业分解与重排
由于该生产线各工位时间差相当大,各操作工人的生产负荷不均,我们希望对各工位的生产作业进行重新分配,以优化生产线平衡现状。
首先,我们对各工位进行作业分解,如表2所示:
表2 各工位作业分解
结合产品特征及各基本作业的实际装配顺序,作出工作网络图,如图4所示。
图4 工作网络图
2、工位分析
通过对各工位进行作业分解,结合工作网络图,我们对部分工位进行了重点分析:
工位4、5、6操作分析
工位4、5、6所用时间相对很短,能力过剩。
工人的任务量相对其他工序小很多。
工序总用时中等待时间过长,即这3个工位的操作工人大部分时间是在等待。
通过以上分析,结合生产的实际情况,运用动作经济原则和整个生产线工作量平衡理论,利用ECRS原则,充分利用现有资源提高生产能力,将工位4、工位5、工位6的作业合并为新的工位4的基本作业,从而形成新的工位作业分配表,如表3所示。
表3改善后的作业分配
3、第一次优化效果
经过对各工位作业进行合理的调整,整个生产线的生产率已经得到明显的提高,具体表现在:
①生产成本方面
将生产能力明显过剩的原工位4、5、6合并在一起,从而,取消了原工位5和原工位6,减少两个工位,从而减少两名工人,节约了人工成本。
②时间研究方面
对改善后的各工位再次进行秒表时间研究,测得各工位的标准时间如图5所示。
图5 改善后的工位负载
由上图我们发现,经过改善后各工位操作时间渐趋平衡,大部分工位操作时间相差不大。
工位4的操作时间相对较长,有待进行进一步优化。
③生产线平衡方面
生产不平衡最大时间损失:
T Max-T M1in=139-106=33(s)
%100m ⨯⨯=
)
节拍()实际工位数目()
任务时间总和(平衡率CT T P
生产不平衡损失率=1-平衡率=1-90.29%=9.71%
由以上计算可知,经过第一次优化,生产线不平衡最大时间损失由106s 降低到33s ,生产线平衡率由61.52%提高到90.29%,生产节拍由136s 略增到139s ,但减少了两个工位,节省了人工成本。
可见第一次优化效果相当明显,但是生产不平衡最大时间损失仍然较大,依然有进一步优化的空间。
四、第二次优化
经过第一次优化,整条生产线的生产效率得到了显著的提高,但是部分工位——工位4的操作时间较其他工位明显较长,制约了该生产线生产率的提高,成为了新的瓶颈环节。
因此,我们采用MOD 排时法对工位4进行动作时间分析。
1、操作分析
我们利用工位4的影像资料进行分析,发现在扭紧后端盖对应的3颗小螺栓的操作时,操作者一直保持一只手操作,另一只手持住箱底的操作状态(如图6所示),明显不符合动作经济原则的双手动作原则,在操作时间上存在较大的改善空间。
因而我们运用MOD 排时法对扭紧小螺母的操作进行动作因素分析,如表4所示。
图6 扭紧小螺母操作
表4 工位4的动作因素分析
由表4不难看出,在整个螺栓的操作中,时间浪费相当严重。
左手一直保持持住箱座等待的状态,右手一直在重复取物和安装动作。
解决双手分工极不
均衡,节奏性差的问题是降低整个工位操作时间的关键。
2、第二次优化方案
我们采用“5W1H”提问方法发现,之所以左手要一直保持持住箱座的状态,是由于箱座没有固定,必须要左手进行人工固定,便于右手在箱座上进行安装操作。
所以我们选用一个支架,来代替左手固定箱座,从而使左手解脱出来帮助右手进行组装操作,改善后的动作因素分析见表5。
表5改善后的动作因素分析
改善后,MOD 值由213减少为174,操作时间由27.477s 降低到22.446s,减少了5.031 s 。
双手同时进行相同的操作,协调性强,操作效率高。
工位4的整体操作时间也从139s 减少为133.969s,不再是瓶颈环节,任务时间总和由502s 变为496.969s 。
生产不平衡最大时间损失:
T=T Max -T Min =136-106=30
%100m ⨯⨯=
)
节拍()实际工位数目()
任务时间总和(平衡率CT T P
生产不平衡损失率=1-平衡率=1-91.35%=8.65%
经过第二次优化,生产线不平衡最大时间损失由33s 降低到30s ,生产线平衡率由90.29%提高到91.35%,生产节拍由139s 降低到136s 。
与第一次优化相比,生产效率再次得到提高,生产不平衡状况得到极大改善,日产量也相对提高。
五、优化效果对比
运用秒表时间研究法以及MOD 排时法,先后对原生产线进行了两次优化,两次优化效果对比如表6所示。
表6 改善前后工艺评价比教
为了更清晰得展现改善效果,我们做出了各工艺评价指标的柱状图,如图8所示。
图8 改善效果柱状图
由以上图表我们可以清晰的看见,进过两次改善之后,原生产线的不平衡最大时间损失由106s减少到30s,生产平衡率由61.52%提高到91.35%,增长了29.83%,日产量得到显著提高。
同时依据动作经济原则对操作人员的操作进行了合理的改善,使操作方法更加科学合理,各工位任务分配合理,工人的疲劳程度降低,工段生产能力平衡。
六、结论
通过对实际生产线工艺进行评价及优化,说明运用作业测定技术能够充分利用现有资源有效地提高生产线的生产能力,减少无效时间,节约人工成本。
这一实例也给企业提供了解决同类问题的方法和措施。
.。