氰特产品资料
高亚氨基甲醚化三聚氰胺树脂的合成研究
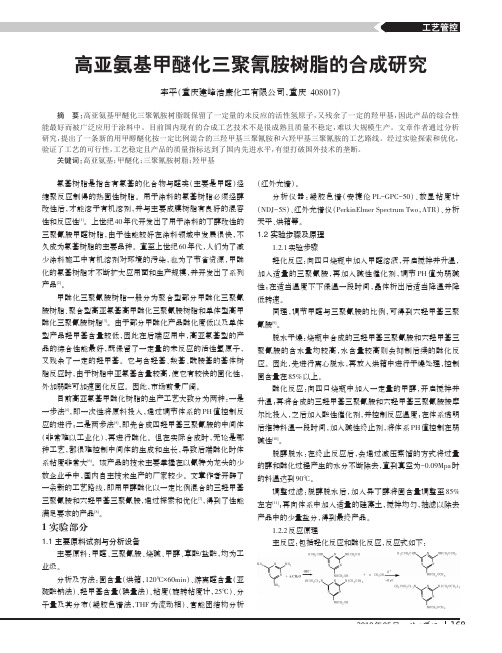
李平(重庆建峰浩康化工有限公司,重庆 408017)
摘 要:高亚氨基甲醚化三聚氰胺树脂既保留了一定量的未反应的活性氢原子,又残余了一定的羟甲基,因此产品的综合性 能最好而被广泛应用于涂料中。目前国内现有的合成工艺技术不是很成熟且质量不稳定,难以大规模生产。文章作者通过分析 研究,提出了一条新的用甲醇醚化按一定比例混合的三羟甲基三聚氰胺和六羟甲基三聚氰胺的工艺路线。经过实验探索和优化, 验证了工艺的可行性,工艺稳定且产品的质量指标达到了国内先进水平,有望打破国外技术的垄断。
表 1 三羟甲基三聚氰胺数据表
序号 1 2 3
均值
固含量/% 90.8 91.0 88.6 90.1
羟甲基含量/% 43.08 43.10 43.05 43.07
游离醛含量/% 0.30 0.25 0.26 0.27
三羟甲基三聚氰胺理论上的羟甲基含量为 43.06%,合成的 三羟甲基含量与理论值基本吻合,说明合成工艺正确且稳定, 同时也说明该产品保留了较多的亚氨基;固含量为 90.1%,说明 脱水干燥手段有效;游离醛含量较低,不超过 0.3%。 2.2 六羟甲基三聚氰胺的结果分析
表1三羟甲基三聚氰胺数据表序号123均值固含量908910886901羟甲基含量4308431043054307游离醛含量030025026027三羟甲基三聚氰胺理论上的羟甲基含量为4306合成的三羟甲基含量与理论值基本吻合说明合成工艺正确且稳定同时也说明该产品保留了较多的亚氨基
工艺管控
高亚氨基甲醚化三聚氰胺树脂的合成研究
子量及其分布(凝胶色谱法,THF 为流动相)、官能团结构分析
2019 年 05 月
169
下:
2 结果与分析
2.1 三羟甲基三聚氰胺的结果分析 通过探索和数据分析,最终确定三羟甲基三聚氰胺的合成
氰特亚太区粉末涂料用树脂(中文版)

粉末涂料用树脂和助剂产品范围亚太区34568910111314151617181920212223242526272830关于我们粉末涂料树脂和助剂的介绍产品综述产品命名方法粉末涂料混合型聚酯树脂混合型树脂的典型性能粉末涂料Primid 1聚酯树脂Primid 1树脂的典型性能粉末涂料TGIC 聚酯树脂TGIC 树脂的典型性能粉末涂料用PT910聚酯树脂PT910树脂的典型性能粉末涂料用聚氨酯聚酯树脂聚氨酯树脂的典型性能UV 固化粉末涂料用聚酯树脂和添加剂UV 固化树脂的典型性能母粒和添加剂母粒和添加剂的典型性能用于不同领域的其他树脂粉末涂料用超耐候树脂粉末涂料光泽可控体系健康,安全和产品的处置术语表产品索引联系我们1 EMS-Chemie 公司的商标从帮助采矿业的客户了解更高效的矿物处理流程到研发用于木器和金属的新型聚合物添加剂,氰特特种化工的各产品部门都一起致力于为客户的利益而不断创新。
我们和客户密切合作,研发能帮助他们提高产品性能和生产效率的革新技术,从而开辟新的市场并优化新的应用。
在环境问题广受关注的情况下如何提高产品的性能或涂料的功效?怎样开发能在紫外光线下仍然具有良好性能的聚合物?如何用磷化氢为农业创造出更好、更安全的杀虫剂和熏蒸剂?我们的技术和销售团队每天都在客户身边和他们一起面对现今的业务挑战同时解决未来可能遇到的问题。
应用领域不同,但使命却一致:通过持续地研发,精诚地合作和创新的热情来为客户找到更好的解决方案。
广泛的产品部门氰特特种化工可以为许多行业中要求高价值表面技术的客户提供完整的解决方案,包括工业涂料、汽车、建筑、木器和纸张、油墨、黏合剂和光电子行业。
我们用环保的产品如UV/EB(紫外光/电子束)固化树脂和助剂、粉末涂料树脂和助剂、以及水性和溶剂型液体涂料树脂和助剂为客户提供先进和多样的用于表面的产品和技术。
我们致力于和客户共同研发环境优化的方案并且乐于公开关于我们产品的安全操作、分销、使用和废弃处理的各项信息。
全球磁性材料顶级企业

全球磁性材料顶尖企业德国VAC公司VACUUMSCHMELZE (VAC)公司是全球高性能磁性材料及器件生产商的领导者。
产品涵盖半成品材料及其零部件,元器件及其集成系统,产品被广泛应用于电力电子及电子工程领域。
从软磁产品到世界上磁性最强的永磁产品,VACUUMSCHMELZE是全球屈指可数的可以给客户提供整套磁性技术方案的跨国公司之一。
今天的 VAC 已经拥有超过3000 名员工,分支结构(包括生产和销售)遍布在全世界40 多个国家,其年均销售额约为3亿欧元。
正不断发展壮大成为一家国际化的企业。
美国莱尔德电子材料集团美国莱尔德电子材料集团是设计和制造电磁屏蔽材料、导热界面材料和无线天线产品的世界著名公司,产品广泛应用于电信、数字通讯、手机, 计算机、通用电子装置、网络设备、航空、国防、汽车以及医疗设备等领域。
美国莱尔德电子材料集团的客户均为世界著名厂商。
美国莱尔德集团的母公司为英国莱尔德集团公众有限公司(其为英国伦敦股票交易所上市公司具有140多年历史)。
美国莱尔德电子材料集团注册于美国的特拉华州,通过并购一系列世界著名的电磁屏蔽产品、导热产品和无线天线产品的制造厂家(包括诸如Instrument Specialties, APM, Bavaria Elektronik, Altoflex, R&F Products, BMI, Warth, Thermagon, Centurion, Melcor等著名公司)而形成今天的规模美国莱尔德电子材料集团总部设于美国圣路易斯市,其制造基地和技术支援公司分布在美国,中国(北京, 天津, 上海, 昆山, 苏州, 泉州, 深圳),法国,德国,匈牙利,瑞典,日本,英国,捷克共和国,新加坡,马来西亚,韩国和中国台湾。
美国莱尔德电子材料集团的战略发展是向客户提供全球技术解决方案及当地制造就近供货。
自2000年美国莱尔德电子材料集团开始进入中国的市场, 现已拥有八家大型生产制造企业分布在北京,上海,天津,深圳,苏州,昆山和泉州, 为国内外客户生产具世界领先水平的电子元件及提供当地便捷、周到的各项服务。
氰特产品在塑料上的应用技术

5 4 3 2 1 0
0 168 336 504 672 840 1008 hours 1176 1344 1512 1680 1848 2016
b value-2706 b value-2704 b value-2708 b value-2810 b value-2816
5
Offering Cytec Products On Plastic
Macrynal SM 548/50X
Fast drying Hardness Adhesion Sanding Chemical Resistant
Application
Primer
Application
Primer
10
Offering Cytec Products On Plastic
Macrynal SM 2810/75BAC
Hardness High Gloss Flexibility Leveling Weather resistant Pot life Film building
Application
2K Clear coat 2k Pigment Topcoat
Adhesion High gloss Leveling Pot life High Film building High solid
Application
2K Clear coat 2k Pigment Topcoat
Application
2K Clear coat 2K Pigment Topcoat
20 deg-VSM 1007/70LG
200 gloss
20 deg-VSM 1001/60XBAC
20 deg-VSM 2800/70BAC
5-7主体树脂和氨基树脂的官能团——主体树脂官能点的类型
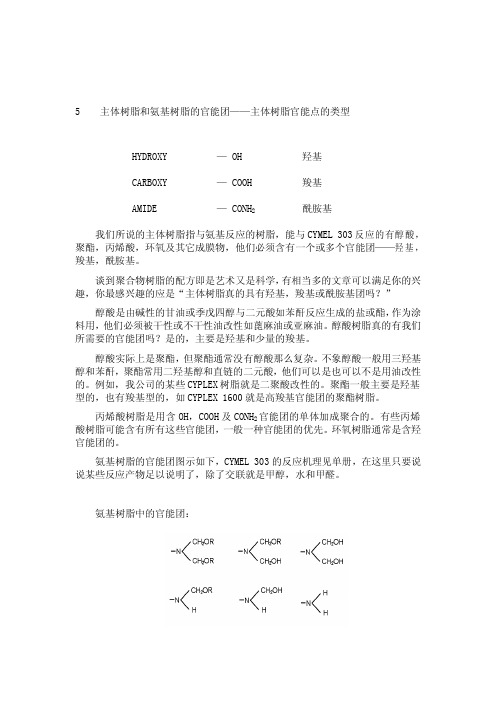
5主体树脂和氨基树脂的官能团——主体树脂官能点的类型CYMEL303反应的有醇酸,聚酯,丙烯酸,环氧及其它成膜物,他们必须含有一个或多个官能团——羟基,羧基,酰胺基。
谈到聚合物树脂的配方即是艺术又是科学,有相当多的文章可以满足你的兴趣,你最感兴趣的应是“主体树脂真的具有羟基,羧基或酰胺基团吗?”醇酸是由碱性的甘油或季戊四醇与二元酸如苯酐反应生成的盐或酯,作为涂料用,他们必须被干性或不干性油改性如蓖麻油或亚麻油。
醇酸树脂真的有我们所需要的官能团吗?是的,主要是羟基和少量的羧基。
醇酸实际上是聚酯,但聚酯通常没有醇酸那么复杂。
不象醇酸一般用三羟基醇和苯酐,聚酯常用二羟基醇和直链的二元酸,他们可以是也可以不是用油改性的。
例如,我公司的某些CYPLEX树脂就是二聚酸改性的。
聚酯一般主要是羟基型的,也有羧基型的,如CYPLEX1600就是高羧基官能团的聚酯树脂。
丙烯酸树脂是用含OH,COOH及CONH2官能团的单体加成聚合的。
有些丙烯酸树脂可能含有所有这些官能团,一般一种官能团的优先。
环氧树脂通常是含羟官能团的。
氨基树脂的官能团图示如下,CYMEL303的反应机理见单册,在这里只要说说某些反应产物足以说明了,除了交联就是甲醇,水和甲醛。
氨基树脂中的官能团:HYDROXY—OH羟基—COOH羧基—CONH2酰胺基注意,可能的反应从这开始:先羟甲基化然后烷氧基化CH2OH羟甲基CH2OR烷氧基=CH3甲基=C2H5乙基=C4H9丁基羟甲基化烷基醚化先是在碱或酸的存在下,甲醛的CH2OH(羟甲基)取代三聚氰氨上的H(氢),即羟甲基化反应,然后是在酸性条件下用醇进行烷氧基化反应,如果ROH上的R 是CH3,即甲氧甲基。
甲氧甲基三聚氰氨甲醛树脂的结构:部分烷氧基化的聚合体全部烷氧基化的单体全部烷氧基化的单体就是HMMM,或叫CYMEL303,所有的H(6个)都被甲氧甲基取代。
部分烷氧基化的聚合体树脂具有甲氧甲基,羟甲基和—NH亚胺基。
氰特公司的氨基树脂资料(翻译版)

目录1涂料及其市场2本公司对涂料工业的贡献3丁醇醚化氨基树脂4高固体份氨基交联剂5主体树脂和氨基树脂的官能团——主体树脂官能点的类型氨基树脂的官能团三聚氰氨——甲醛树脂的生产技术甲醚化三聚氰氨——甲醛树脂的结构标准的丁醚化三聚氰氨——甲醛树脂6高固体份三聚氰氨——甲醛树脂交联剂7反应官能团和与性能的关系氨基树脂的反应官能团氨基树脂性能趋势8高固体份氨基树脂CYMEL1158CYMEL324CYMEL370、373、380CYMEL385CYMEL300系列CYMEL1100系列CYMEL1123羧基改性混合醚化体系甘脲树脂BEETLE甲醚化脲素——甲醛树脂POWDERLINK1174粉末涂料交联剂9催化剂氨基交联剂实用催化剂低温交联剂用催化剂的选择催化剂分类氨基树脂对交联效果的影响胺封闭型催化剂10水性体系水溶解型高固体份三聚氰氨——甲醛氨基树脂水稀释型氨基树脂水分散型树脂的中和水性涂料用甲氧甲基三聚氰氨树脂的特性CYMEL303和其它甲醚化氨基树脂作为乳液的改进剂11CYPLEX树脂卷材涂料12高固体份涂料和VOCsVOC的计算VOC计算的验证及实践氨基树脂在高固体份涂料中的VOCs13氨基树脂中的甲醛溢出14氨基树脂在汽车面漆中的应用——耐腐蚀和耐候性15高固体份汽车再涂漆的附着力16高固体份涂料的其它问题反应活性聚合度与性能的关系挥发物的溢出与漆膜收缩氨基树脂醚化用醇的选择对高固体份涂料交联作用的影响塑料用高固体份涂料中CYMEL303对耐划伤性能的多种作用纸张用高固体份涂料1718FDA认可19氰特公司树脂的毒理及安全处理程序20附注有关高固特性及催化剂分问题与答案棱型图表例索引图例索引。
氰特湛新氨基树脂资料 AllnexAminosProductGuide

AMINO CROSSLINKERSPRODUCT GUIDE • CYMEL® Resins •WorldwideAll About Resins FACTS & FIGURESAbout usdimately3Amino ResinsAllnex's expertise in crosslinking technology is part of our corporate heritage and the foundation to our leadership in supplying the market for amino resins. This brochureprovides product characteristics, compositional information and brief general comments on CYMEL ® amino crosslinkers used in industrial coatings applications includingautomotive, Original Equipment Manufacturers (OEM),kitchen cabinets, metal food and beverage packaging, metal building products and general metal finishing.Our new CYMEL formaldehyde-free crosslinkers are ideal for applications where formaldehyde emissions are a concern.Amino crosslinkers are used with epoxy, polyester, acrylic and alkyd resins and provide the desired balance offlexibility, exterior durability, chemical resistance and film toughness.Allnex's Goals in Research and DevelopmentSeveral factors drive Allnex's research and development efforts. Allnex focuses on gaining a fundamentalunderstanding of the technical challenges encountered by our customers as they work towards improving their formulations. Allnex also focuses on offering solutions quickly and cost-effectively. Equally important is ourcommitment to developing new products that fulfill long-standing needs of the industries we serve. Our technical specialists routinely visit customer locations, worldwide, to assist them in resolving problems and accelerating development of better products.True Customer CommitmentWith our extensive portfolio of liquid resin & additive, radiation cured and powder coating resin & additive, and crosslinker technologies, we are ideally positioned to help customers find the solutions to all of their coating challenges. We are dedicated to delivering value through the development of innovative, market-leading, high quality products that offer enhanced performance, increased ease-of-use, environmental compliance and reduced cost.IntroductionHigh Solids Methylated Melamine Resins ...............4Highly Methylated Melamine Resins ....................... 4Methylated High Imino Melamine Resins ................5Partially Methylated Melamine Resins .. (5)High Solids Mixed Ether Melamine Resins ............. 6 Highly Alkylated Melamine Resins ........................... 6High Imino Melamine Resins (7)Butylated Melamine Resins ....................................... 8n-Butlyated Melamine Resins ................................... 8Highly n-Butylated Melamine Resins ........................8n-Butylated High Imino Melamine Resins .............. 9iso-Butylated Melamine Resins (9)High Solids Urea Resins ........................................... 10Methylated Resins .................................................... 10Butylated Resins . (10)Butylated Urea Resins .............................................. 12n-Butylated Urea Resins ........................................... 12iso-Butylated Urea Resins . (13)Benzoguanamine and Glycoluril Resins ............... 14Benzoguanamine Resins ......................................... 14Glycoluril Resins .. (15)Formaldehyde Free Resins ...................................... 16CYMEL NF 2000 ........................................................ 16CYMEL NF 3041 .. (16)Table of ContentsHighly Methylated Melamine ResinsHighly methylated melamine resins consist of commercial versions of hexamethoxymethylmelamine (HMMM). They differ primarily in their degree of alkylation and monomer content. All are efficient crosslinking agentsfor hydroxyl, carboxyl and amide functional polymers. The practical equivalent weight for most of the resins is 130-180. Advantages are low VOCs; high film flexibility and toughness when used with inherently flexible backbone resins; excellent formulation stability, especially in waterborne systems formulated at a pH of 8-9; good mar resistance; and good intercoat adhesion properties. As typical with melamine resins, all are low in color and color development, have excellent exterior durability and good heat resistance. Because of their high extent of alkylation, the resins in this series require the addition of a strong acid catalyst for acceptable cure response when bakedat 125-150°C. Typically, 0.2- 0.4% p-toluene sulfonic acid based on total binder solids is recommended. The optimum concentration of acid catalyst depends on the basicity of the other components in the formulation and should be determined experimentally. Using a blocking amine forthe acid catalyst and adding a stabilizing alcohol to the formulation can enhance formulation stability.High Solids Methylated Melamine Resins4Methylated High Imino Melamine ResinsMethylated high imino melamine resins are partially methylolated and highly alkylated. These characteristics result in resins containing a significant concentration of alkoxy/imino or high NH functionality. The advantagesare fast cure response at 120-150°C without the need for strong acid catalysts, fast cure response in waterborne formulations, high film hardness, and low formaldehyde release on cure. In addition to reacting with hydroxyl, carboxyl and amide functionality on polymers, these resins also self-condense readily. Therefore, their practical equivalent weight is typically 180-240. They too, can be stabilized by adding tertiary amine and stabilizing primary alcohol to the formulation. Compared to their highly alkylated counterparts, the imino resins usually result in slightly less flexible coatings and slightly higher VOCs when used in solvent-based systems.Partially Methylated Melamine ResinsPartially methylated melamine resins are highly methylolated and partially alkylated. They cure well at 125-150°C without the need to add a strong acid catalyst. The acidity of most polymers used in thermoset coatings is sufficient to catalyze their reaction. Their film performance properties are similar to those of the high imino resinsin the previous category. In addition to reacting with the hydroxyl, carboxyl and amide functionality of polymers they, too, can self-condense readily. Their practical equivalent weight is also 180-240. As with all melamine resins, they can be stabilized by adding amine and stabilizing alcohol to the formulation. The major limitation of these products is high formaldehyde release on baking, primarily due to their high free methylol content.Product availability can vary by usage location. Please contact your local Allnex representative regarding availability in specific countries and regions.5Highly Alkylated Melamine ResinsThe highly alkylated melamine resins in thiscategory are similar to the commercial versions of hexamethoxymethylmelamine (HMMM) except for the type of alkylation alcohol. The resins contain combinations of methoxy sites and longer chain length alkoxy sites (ethoxy, n-butoxy or iso-butoxy). They also differ from each other in their degree of alkylation and monomer content. Longer chain length alkoxy sites impart lower viscosity, improved flow and leveling, and intercoat adhesion. All of the resins in the series are efficient crosslinking agents for hydroxyl, carboxyl and amide functional polymers. The practical equivalent weight for most is 140-200. Other advantages are low VOCs; high film flexibility and toughness when used with inherently flexible backbone resins; excellent formulation stability, especially in waterborne systems at a pH of 8-9 and good mar resistance properties. Because of their high extent of alkylation, the resins in this series require the addition of a strong acid catalyst for acceptable cure response when baked at 125-150°C. Typically, 0.2-0.4% p-toluene sulfonic acid based on total binder solids is recommended. The optimum concentration of acid catalyst depends on the basicity of the other components in the formulation and should be determined experimentally. The use of a blocking amine for the acid catalyst and the addition of a stabilizing alcohol to the formulation should enhance formulation stability.High Solids Mixed Ether Melamine Resins6High Imino Melamine ResinsThe high imino melamine resins in this category are similar to those in the high imino methylated melamine series in that they are partially methylated and highly alkylated. They differ from methylated melamine resins in the type of alkylation alcohol, and they contain combinationsof methoxy sites and n-butoxy sites. The butoxy sites impart improved flow and leveling and intercoat adhesion properties. As in the methylated series, their composition contains primarily alkoxy/imino or alkoxy/NH functionality. The advantages are fast cure response at 120-150°C without the need for strong acid catalyst addition; fast cure response in waterborne formulations; high film hardness; and low formaldehyde release on cure. In addition to reacting with hydroxyl, carboxyl and amide functional polymers, the resins also self-condense readily. Therefore, their practical equivalent weight is typically 200-250. They, too, can be stabilized by amine and stabilizing alcohol addition to the formulation.Product availability can vary by usage location. Please contact your local Allnex representative regarding availability in specific countries and regions.7n-Butylated Melamine Resinsn-butylated resins in this category are very polymeric in nature. They differ in extent of methylolation, butylation and polymerization. In general, higher extents of methylolation and butylation result in more hydrophobic resins with lower viscosities, higher stability, slightly higher film flexibility, film gloss and adhesion but slower cure response. Higher extents of polymerization result in faster film property development but also in higher viscosities, and therefore higher VOCs. None of the resins in this category require the addition of a strong acid catalyst for adequate cure at 125-150°C. Usually, the acidity of the other resin components in the formulation results in sufficient catalysis. In addition to reacting with hydroxyl, carboxyl and amide functionalities on polymers, these resinsself-condense readily. Their practical equivalent weight is typically 220-280 on a solids basis, High concentrations of the melamine resins in the formulation result in high film hardness and improved exterior durability but, possibly, lower film flexibility and lower adhesion properties. They, too, can be stabilized by adding amines and stabilizing alcohol to the formulation.Highly n-Butylated Melamine ResinsHighly butylated melamine resins are similar to the commercial versions of hexamethoxymethylmelamine (HMMM), except they are n-butylated. They also are slightly more oligomeric than their methylated counterparts.The butylation or butoxy sites impart improved flow and leveling and intercoat adhesion properties. However,cure response is slower than that of the resins in the methylated category. Yet, highly butylated melamine resins, are efficient crosslinking agents for hydroxyl, carboxyl and amide functional polymers. The practical equivalent weight is 160-220. Other advantages are high film flexibility and toughness when used with inherently flexible backbone resins; excellent formulation stability; and good mar resistance properties. Because of their high extent of alkylation, the resins require the addition of a strong acid catalyst for acceptable cure response when baked at 125-150°C. Typically 0.2-0.4% p-toluene sulfonic acid based on total binder solids is necessary. The optimum concentration of acid catalyst depends on the basicity of the other components in the formulation and should be determined experimentally. The use of a blocking amine for the acid catalyst and the addition of a stabilizing alcohol to the formulation should enhance formulation stability.Butylated Melamine Resins(1) = Foil solids 45 min at 45°C (2) = Pan solids 60 min at 100°C (3) = Pan solids 120 min at 105°C (4) = Pan solids 120 min at 120°C8n-Butylated High Imino Melamine ResinsButylated high imino melamine resins are similar to those in the high imino methylated melamine series; they are partially methylolated and highly alkylated. They differ from the high imino methylated melamine resins in that they are n-butylated. The butoxy sites impart improved flow and leveling and intercoat adhesion properties.As in the methylated series, their composition contains primarily alkoxy/imino or alkoxy/NH functionality. The advantages are fast cure response at 120- 150°C without the need to add a strong acid catalyst; high film hardness; and low formaldehyde release on cure. In addition to reacting with hydroxyl, carboxyl and amide functionality on polymers, the resins self-condense readily. Therefore, their practical equivalent weight is typically 160-220. They can be stabilized by the addition of an amine and a stabilizing alcohol to the formulation. iso-Butylated Melamine ResinsThe iso-butylated melamine resins in this category are similar to polymeric n-butylated resins and differ only in that they are "iso" rather than "n"-butylated. It is generally believed that iso-butylated melamine resins cure faster than n-butylated resins, although differences in extentof methylolation, alkylation and polymerization are believed to be more significant factors with respect to cure response. The comments made previously concerning the n-butylated resins also apply to the iso-butylated resins.Product availability can vary by usage location. Please contact your local Allnex representative regarding availability in specific countries and regions.910Methylated ResinsMethylated urea resins were designed for waterborne and solvent-based formulations for interior and non-UV resistant applications. They differ from each otherprimarily in their extent of methylolation and methylation. As with other amino resins for coatings, higher extents of alkylation result in improved compatibility with most binders, improved stability; and better flow and leveling, but slower cure response. None of these resins require the addition of a strong acid catalyst for acceptable cure response at 125°C. The acidity of the other components in a formulation usually is sufficient for catalysis. For very low temperature cure systems, those for wood finishes, for example, a 2-component formulation is necessary. In such formulations, the acid catalyst is added to the fully-formulated system just prior to use. If the bake temperature is around 70°C, a concentration of 1-2% on total binder solids of a strong or weak acid is recommended. In general, urea resins react with thehydroxyl, carboxyl and amide functional sites on polymers, but they also have a high tendency for self-condensation. Their practical equivalent weight is in the range of 180- 260. The use of a blocking amine for the acid catalyst and the addition of a stabilizing alcohol to the formulation enhances formulation stability. The latter approach is recommended for 2-component formulations.Butylated resinsThe one resin in this category, CYMEL U-80 resin, issimilar in composition to several of the methylated resins, except that its alkylation alcohol is n-butanol. This resin is also recommended for interior and non-UV resistant coatings; it is used primarily in solvent-based systems. It is very hydrophobic and stable but slower curing than its methylated counterparts. A strong acid catalyst is recommended for acceptable cure response at 125°C. Other formulation details are the same as those given for methylated resins.High Solids Urea ResinsHigh Solids Urea ResinsProduct availability can vary by usage location. Please contact your local Allnex representative regarding availability in specific countries and regions.11n-Butylated Urea ResinsThe urea resins in this category are all partially n-butylated and very polymeric in nature. They differ in extent of methylolation, butylation, and polymerization. In general, higher extents of methylolation and butylation result in more hydrophobic resins with lower viscosities, higher stability, and slightly higher film toughness, film gloss and adhesion but slower cure response. Higher extents of polymerization result in faster film property development but also in higher viscosities and, therefore, higher VOCs. None of the resins require the addition of a strong acid catalyst for adequate cure at 125°C. Usually, the acidity of the other resin components in the formulation is sufficient for catalysis. In addition to reacting with hydroxyl, carboxyl and amide functional polymers, the resins also selfcondense readily. Their practical equivalent weight is typically 220-300 on a solids basis. High concentrations of the urea resins in the formulation result inhigh film hardness, but, possibly, lower film toughness and lower adhesion properties. They can be stabilized by amine and stabilizing alcohol addition to the formulation. As with other urea resins,they are recommended for interior, non-UV resistant applications. The most typical applications are interior container coatings andButylated Urea Resins(1) = Pan solids 90 min at 105°C (2) = Pan solids 120 min at 105°C (3) = Pan solids 120 min at 120°C(4) = Pan solids 60 min at 100°C122-component solvent-based wood finishes, In the latter application, the acid catalyst is added to the fully-formulated system just prior to use. A concentration of 1-2% on total binder solids of a strongor weak acid is recommended for systems that require low bake temperatures - typically less than 70°C.iso-Butylated Urea ResinsThe iso-butylated urea resins in this category are similar tothe polymeric n-butylated resins, except that they are iso-butylated rather than n-butylated. It is generally believed that iso-butylated urea resins cure faster than n-butylated resins, although differences in extent of methylolation, alkylation and polymerization are believed to be more significant factors with respect to cure response. iso-butylated urea resins performin much the same way as n-butylated urea resins. That is, high concentrations of these resins in the formulation result in high film hardness, but, possibly, lower film toughness and lower adhesion properties. iso-butylated resins can be stabilized by adding amine and stabilizing alcohol to the formulation. They are recommended for interior and non·UV resistant applications, as well.Product availability can vary by usage location. Please contact your local Allnex representative regarding availability in specific countries and regions.1314Benzoguanamlne ResinsBenzoguanamine resins are similar to melamine-based resins in that they, too, are triazine based, but in this instance, the triazine has a benzene group substitution. Therefore, they are less functional than melamine-based resins, and are not UV resistant. Benzoguanamine resins are noted for their enhanced film flexibility, or toughness, and for their chemical resistance. They are typically used in primers, container coatings, and appliance finishes. Usually, highly alkylated, monomeric benzoguanamine resins result in higher film flexibility than that which can be achieved with other types of resins, but they alsorequire the addition of a strong acid catalyst for adequate cure at temperatures greater than 125°C. Their practical equivalent weights are slightly higher than the practicalweights of their melamine counterparts and range from 160-220. The less alkylated polymeric resins only require the acidity of the other components in the formulation to cure adequately at greater than 125°C, but they have higher VOCs in a solvent-based formulation. Their practical equivalent weights are also slightly higher than those of their melamine counterparts and range from 200-260 on a solids basis. The use of a blocking amine and the addition of a stabilizing alcohol to the formulation should enhance formulation stability.(1) = Pan solids 120 min at 120°CBenzoguanamine and Glycoluril Resins(2) = Foil solids 45 min at 45°C(3) = Pan solids 120 min at 105°CGlycoluril ResinsGlycoluril resins are similar to their melamine resinscounterparts in that they, too, are based on a ring structure,glycoluril. Similar to benzoguanamine resins, they areless functional than melamine resins but are UV resistantand can be used in exterior coatings. Their advantagesare film toughness and flexibility, ability to adhere tometals, and low formaldehyde release on curing. There aretwo categories in the product line, unalkylated methylolglycoluril resins, and those which are highly alkylated.CYMEL 1172 is unalkylated, and was designed for water-based coatings with low temperature cure performanceproperties. The highly alkylated resin, CYMEL 1170, wasdesigned to replace HMMM where there is a desire toimprove film flexibility. The same comments concerninghighly alkylated monomeric melamine resins also apply tothe alkylated glycoluril resins.Product availability can vary by usage location. Please contact your local Allnex representative regarding availability in specific countries and regions.15CYMEL® NF 2000CYMEL NF 2000 crosslinking agent is a unique trifunctional melamine-based crosslinker containing reactive carbamate functionality. It can be used to crosslink hydroxy- and epoxy containing polymers to give highly durable, acid-resistant films that exhibit a favorable balance of hardness and flexibility. An important feature of CYMEL NF 2000is that it does not contain or emit formaldehyde on cure.It can be employed as the sole crosslinker in a coatingor ink formulation, or it may be used at lower levels in combination with other crosslinkers, such as conventional amino resins or isocyanates, in order to obtain a balance of properties. CYMEL NF 2000 is recommended for high quality durable finishes such as automotive topcoats, exterior can varnishes and coil coatings. CYMEL NF 2000 reacts with hydroxy functional backbone resins at >125°C bake schedules to form urethane linkages. Cure can typically be accomplished without use of a catalyst to yield films that exhibit excellent hardness, chemical resistance, exterior durability and environmental etch resistance. Addition of low levels of acid catalyst (e.g. 0.5% dodecyl benzene sulfonic acid on binder solids) has been found to improve humidity resistance properties in some systems. Both catalyzed and uncatalyzed formulations show good 1K package stability at 23°C. CYMEL NF 2000 will react with carboxy functional backbone resins, but require bake temperatures >150°C. CYMEL NF 3041CYMEL NF 3041 is a partially n-butylated crosslinker agent designed for 2 pack ambient and heat cured formulations for industrial wood and plastic applications. These systems have excellent early hardness, resistance properties, appearance and hot/cold cycle flexibility. CYMEL NF 3041 is a very effective crosslinking agent for alkyd, polyester and acrylic polymers containing primary hydroxyl functionality. CYMEL NF 3041 resin requires the addition of an acid catalyst to the formulation in order to obtain effective cure for both ambient and heat cured applications. It is recommended to use 2.0% CYCAT 500 based on weightof total binder solids. However, the acidity of other formulation components may affect the reaction rate and should be evaluated in combination with the catalyst. Catalyzed potlife can be extended by the addition of 10 to 20% primary alcohol on total binder solids. Methanol or ethanol is preferred to ensure early hardness development and sandability. The coatings demonstrate very good flow, gloss, early film hardness, early print resistance and chemical resistance.Formaldehyde Free Resins(1) = Foil solids 45 min at 45°C(2) = Pan solids 120 min at 105°C16Product availability can vary by usage location. Please contact your local Allnex representative regarding availability in specific countries and regions.1718All About ResinsNotice: Trademarks indicated with the ® or ™ are registered, unregistered or pending trademarks of Allnex Belgium SA or its directly orindirectly affiliated Allnex Group companies.Disclaimer: Allnex Group companies (“Allnex”) decline any liability with respect to the use made by anyone of the information containedherein. The information contained herein represents Allnex's best knowledge thereon without constituting any express or implied guaranteeor warranty of any kind (including, but not limited to, regarding the accuracy, the completeness or relevance of the data set out herein).Nothing contained herein shall be construed as conferring any license or right under any patent or other intellectual property rights of Allnexor of any third party. The information relating to the products is given for information purposes only. No guarantee or warranty is providedthat the product and/or information is adapted for any specific use, performance or result and that product and/or information do notinfringe any Allnex and/or third party intellectual property rights. The user should perform its own tests to determine the suitability for aparticular purpose. The final choice of use of a product and/or information as well as the investigation of any possible violation of intellectualproperty rights of Allnex and/or third parties remains the sole responsibility of the user.©2014 Allnex Group. All Rights Reserved.19XLR3001-EN-WW-0314 AFRICAASIAAUSTRALIAEUROPENORTH AMERICASOUTH AMERICAAllnex Global Operational HeadquartersSquare Marie Curie 111070 Anderlecht – BrusselsBELGIUM。
六羟甲基三聚氰胺和高度甲醚化的三聚氰胺甲醛树脂物理性能及用途

六羟甲基三聚氰胺和高度甲醚化的三聚氰胺甲醛树脂物理性能及用途一、产品性能:中文名为:六羟甲基三聚氰胺,英文名为:hexamethylol melamine,简称:HMM.分子式为:C3N6(CH2OH)6或C9H18N6O6。
熔点164℃~174℃,沸点669℃,分子量,相对密度为1.821 g/cm3(20℃),羟甲基含量﹥50%且低羟物少;水份:8%-10%(105℃,2小时);游离甲醛含量﹤1%。
根据用户要求,游离甲醛含量可控制在%以下。
其特点是羟甲基含量高、水份稳定、游离甲醛含量极低;投料时,粉尘少。
CAS no.:531-18-0结构式:二、产品用途1、橡胶粘合剂行业此产品与醇类醚化可生产橡胶粘合剂A从而制成RA。
即美国氰特CYREZ® 964产品。
[CYREZ® 964 浓缩粉末树脂(六甲氧基甲基三聚氰胺)或者HMMM在“HRH”橡胶粘合体系中作为亚甲基给予体来增强橡胶与帘线的粘合方面有着广泛的应用。
]2、涂料行业此产品与甲醇醚化可生产涂料用高甲醚化型氨基树脂[如氰特Cymel 303 树脂,首诺(孟山都)SOLUTIA 747,德国巴斯夫(BASF)的Luwipal 系列的高甲醚化氨基树脂以及韩国P&ID公司美螺丝(Melcross 03)树脂等],是制水性涂料、高固体份涂料、粉末涂料所必需的涂料助剂,广泛用于卷材涂料、汽车涂料助剂。
3、由于我公司产品游离甲醛含量可控制在%以下,是服装整理剂助剂的最好选择。
三、选择我公司产品的好处1、由于产品游离甲醛含量极低,用户选择我公司产品以代替甲醛和三聚氰胺可解决现场生产职工职业卫生及环保问题。
2、用户选择我公司产品来代替甲醛和三聚氰胺同样的生产设备可提高产能50%以上。
3、由于我公司产品水份非常稳定,加之用我公司比用甲醛和三聚氰胺工艺流程缩短,用户选择我公司产品直接与甲醇醚化,醚化的产品质量很容易控制,且产品收率也较高,从而降低了用户的生产成本。