射出成型原理
射出成型简介

射出成型简介1 射出成形之基本知识。
1.1 射出成形的特征以及组成。
射出成形是将溶融的成形材料以高压的方式填充到封闭的模具内,射出成形的模腔内承受的压力约400KGF/CM2,大约为400个大气压,以这样高的压力来制作产品是它的特征,这是它的优点也是它的缺点。
也就是说模具必须制作得相当坚固,因而模具价格也相当昂贵,因此必须大量生产以便与高价的模具费用互相扣抵,例如每批之生产量必须10000PCS以上才合理,换句话说;射出成形的工作必须以大量生产才行。
成型过程所说几个步骤:1.1.1关门安全门上才开始成型。
1.1.2 锁模将移动侧的移动板前进,使得模具关闭,模具关闭以后确实地把模具锁紧。
1.1.3 射出(包括保压)螺杆快速地往前推进,把熔融之成形材料注入模腔内填充成形,填充之后压力要必须继续保持,这个动作特别取名为“保压”。
在刚充填时模具承受的压力,一般叫做射出压或者叫做“一次压”。
1.1.4 冷却(以及下个动作的可塑化工程)模腔内之成形材料等待冷却凝固之过程叫“冷却”。
在这时候射出装置也准备下次工作,这个过程叫做“可塑化过程”。
放在料斗里的成形材料,流入加热的料管内加热,是依据螺杆旋转把原料变成熔融状态,螺杆像拨取螺丝的原理一样,一面转一面后退,螺杆前端会储存熔融之成形材料,螺杆旋转时,抵抗螺杆向后退的压力称之为螺杆的“背压”。
1.1.5 打开模具将移动侧的移动板向后退,模具跟着打开。
1.1.6 打开安全门安全门打开,这时成形机处于待机中之状能。
1.1.7 取件将成品取出,然后检视确认模具内未残留任何物件再关门.以上整个成形作业叫做一个CYCLE成型。
成品是由模具的形状成形出来。
模具是由母模及公模组合成,公母模模仁之间留有空隙,材料在此流入压缩形成产品。
成型材料要流入公母模之前的通路有主流道(SPRUE)流道(RUNNER)闸门(GA TE)等。
1.2 射出成形机射出成形机以较大项目来区分,可分为两项,锁模装置和射出装置。
塑料射出成形的原理

塑料射出成形的原理1.塑料熔融:将固体塑料颗粒加热至熔融状态,通常通过加热器加热塑料料筒中的原料。
在料筒中,螺杆将塑料推送到加热区域,并通过加热带将其熔化。
在被熔化的状态下,塑料经过混炼,确保其均匀性,以及与其他添加剂和颜料的混合。
2.射出注塑:将熔融态的塑料材料通过射出筒传送到射出嘴端,然后注射到模具的射出系统中。
射出系统通常由一个射出筒和一个射出嘴组成。
当塑料材料被注入到模具中时,射出嘴的阀门关闭以防止漏料。
3.压力和冷却:一旦塑料进入模具中,会施加一定压力以保持模具的形状。
这种压力通常由射出机的液压系统提供。
此外,模具内的冷却系统会通过冷却介质(如水)迅速降低塑料温度,促使其固化。
4.分离和排出:在塑料冷却和固化之后,模具会打开以分离成型件和废料。
成型件通常有一个喷嘴可以用来排出气体,是为了减少模具中的空气气体。
废料可以回收再利用,以减少浪费并提高效率。
1.高效生产:塑料射出成形是一种快速且连续的生产方法,可以在短时间内生产大量的塑料制品。
这是因为塑料射出成形每次只需要几秒钟至几分钟的周期时间。
2.复杂形状:塑料射出成形可以制造复杂的三维形状,具有细节丰富的内部空间和壁厚变化。
这是因为模具的设计可以根据需要进行定制,以实现所需的形状。
3.高精度:塑料射出成形具有高精度和重复性,可在0.001英寸的尺寸范围内制造产品。
这是因为模具的精确度高,并且注射过程经过精确控制。
4.多材料应用:塑料射出成形可以使用多种塑料材料进行生产,如聚丙烯、聚氨酯、聚碳酸酯等。
这使得塑料射出成形具有广泛的应用领域,在汽车、电子、医疗器械等行业得到广泛应用。
总结起来,塑料射出成形是一种通过将加热熔融态的塑料注入到模具中,通过压力冷却和固化成型的塑料加工方法。
它具有高效生产、制造复杂形状、高精度和适用于多材料的优势。
这种加工方法已经成为现代塑料制造业中不可或缺的一种技术。
射出成型简介

射出成型简介1 射出成形之基本知识。
1.1 射出成形的特征以及组成。
射出成形是将溶融的成形材料以高压的方式填充到封闭的模具内,射出成形的模腔内承受的压力约400KGF/CM2,大约为400个大气压,以这样高的压力来制作产品是它的特征,这是它的优点也是它的缺点。
也就是说模具必须制作得相当坚固,因而模具价格也相当昂贵,因此必须大量生产以便与高价的模具费用互相扣抵,例如每批之生产量必须10000PCS以上才合理,换句话说;射出成形的工作必须以大量生产才行。
成型过程所说几个步骤:1.1.1关门安全门上才开始成型。
1.1.2 锁模将移动侧的移动板前进,使得模具关闭,模具关闭以后确实地把模具锁紧。
1.1.3 射出(包括保压)螺杆快速地往前推进,把熔融之成形材料注入模腔内填充成形,填充之后压力要必须继续保持,这个动作特别取名为“保压”。
在刚充填时模具承受的压力,一般叫做射出压或者叫做“一次压”。
1.1.4 冷却(以及下个动作的可塑化工程)模腔内之成形材料等待冷却凝固之过程叫“冷却”。
在这时候射出装置也准备下次工作,这个过程叫做“可塑化过程”。
放在料斗里的成形材料,流入加热的料管内加热,是依据螺杆旋转把原料变成熔融状态,螺杆像拨取螺丝的原理一样,一面转一面后退,螺杆前端会储存熔融之成形材料,螺杆旋转时,抵抗螺杆向后退的压力称之为螺杆的“背压”。
1.1.5 打开模具将移动侧的移动板向后退,模具跟着打开。
1.1.6 打开安全门安全门打开,这时成形机处于待机中之状能。
1.1.7 取件将成品取出,然后检视确认模具内未残留任何对象再关门.以上整个成形作业叫做一个CYCLE成型。
成品是由模具的形状成形出来。
模具是由母模及公模块合成,公母模模仁之间留有空隙,材料在此流入压缩形成产品。
成型材料要流入公母模之前的通路有主流道(SPRUE)流道(RUNNER)闸门(GATE)等。
1.2 射出成形机射出成形机以较大项目来区分,可分为两项,锁模装置和射出装置。
塑胶射出成型原理

内 压
2
3
4 1
时间
时间
比 容 积
1 2充填 2 3压缩 3 4保压 5开模 6收缩至常温
6
5 4
塑料射出成型进阶教程 第一章:射出成型原理探讨
保持(Holding) 当模穴内塑料被适当压缩后,应立将注射的压力降低,以防过量,但如降 得太低,则因模穴内塑料沿处高温高压状态,将发生逆流,所以必需仍以适当 的压力加以对抗,直到入浇口冷凝封住的过程. 在保持的过程,热料不再(或极微量)进入模穴,所以料温较快的冷却,模穴 内压大致依据下式所代表的原理,逐步下降低: (P+A)(V-W)=R’T 式中P:表模穴内压. V:表塑料比容积. T:表塑料温度. A,W及R:是和塑料分子结构有关的系数
第一章:射出成型原理探討
塑膠射出成型進階教程
目 錄 第一章:射出成型原理探討
第二章:安定成型的參數設定
第三章:低壓成型技術概述
塑膠射出成型進階教程 第一章:射出成型原理探討
1.前言 熱可性塑膠加熱熔解后 在塑形過程中及完了後又漸漸冷卻至定形, 這幾 乎是所有塑膠成型加工法的必要程序. 受熱熔解 ,冷卻固化, 意味著塑膠分子鏈團的被解開與再集合, 但射出成型 加工的過程,絕非如此而已,它必需在模腔被充滿後, 為補嘗冷卻後的容積收縮, 而在塑料尚在高溫時, 适時適量地補充注入. 一定容積的模腔,要擠入較多的塑料, 必定對熔融的塑料形成壓縮, 壓縮使 塑料產生抵抗(模腔內壓), 在抵抗仍然存在的時間內适當的保持壓力的對抗(避 免模腔內塑料逆流)是不可避免的. 模腔的充填速度如果太慢 , 則因塑料溫度的降低(流動阻抗增加), 有可能 使充填無法完全(短射), 或充滿後的壓縮變成困難, 但充填速度太快,則又容易形 成外觀上不良的等問題. 綜上所述,溫度, 壓力, 速度, 時間和量等五大參數, 對射出成型工程的影響是 我們所必需探討的.
精密射出成型

精密射出成型乃是传统射出成型但是要求产品之高精密度。
一、射出成型各阶段之基本原理与物理现象:﹝1﹞射出成型以模具的机械动作可分为锁模阶段、充填阶段、保压阶段、冷却阶段及开模顶出五个阶段,如图1-1所示;但以熔胶在模具的流动至开模为止,则可分为充填、保压及冷却三个过程。
图1-1模具机械动作阶段图﹝2﹞在充填过程中时射出成形机的螺杆向前运动将熔胶经由浇口,流道压入模穴内。
由于熔融树脂具有高度黏性,为,同时熔胶也必须维持有压力梯度。
熔胶的黏度随时间、剪变率而改变,因此在模腔内各点的压力随着时间位置在变化。
在整个过程中,模穴壁上的压力随时间的变化大致如图1-2所示。
图1-2模穴压力在射出成周期的变化。
﹝1﹞充填阶段﹝2﹞压料(packing) ﹝3﹞冷却阶段在充填阶段﹝1﹞压力主要是来克服熔胶在模穴内流动的阻力,当模穴充填完后由于熔胶的可压缩性以及其后冷却的收缩,为了补偿这个收缩效应,在保压阶段﹝2﹞保压压力将熔胶继续压挤入模穴直浇口凝固。
尔后熔胶一直冷却至表面固化到某一程度成品才被顶出。
充填阶段时,当熔胶流入模穴时与冷的腔壁接触,会形成薄的凝层,靠近壁上的熔胶温度会降低,在熔胶流动的峰前,由于喷流效应( Fountain Flow Effect ) 熔胶从中心往两模腔壁流动造成等速的熔胶流动,同时热熔胶从中心带至前缘及两边模腔壁。
在熔峰后端之熔胶则是层状流动,在中心的流动速度最大,而凝固层边的流速为零。
如图1-3所示。
图1-3充填过程中熔胶流动方向剖面流速分布图。
熔胶流峰显示喷流效应(Fountain FlowEffect)同理靠近模穴处温度较低而肉厚中央熔胶仍然保持高温,有时由于黏度生热﹝Viscous Heating﹞的效应﹝与射速有关﹞在较近模穴的地方会产生高温,这种现象在浇口尤其显着( 图1-4 )。
由于熔胶是非牛顿流体,黏度呈现剪薄(Shear Thinning ﹞效应随着温度、剪切率而改变,因此在充填过程中,压力、速度、温度,以及扮随的黏度、剪切率在流动方向以及肉厚方向均有很大的变化,对于成型及成品品质会有很大的影响。
塑胶射出成形的原理

6.射出成形用材料---加熱則軟化的塑膠
成形收縮率
成形品的尺寸(常溫)通常都稍微小於模具尺寸(常溫),這縮小的比例叫做成 形收縮率.
各种塑膠的成形收縮率不同,例如聚苯乙烯是0.4%,而聚丙烯是1.6%(表1).
成形收縮率比較小的一群是結晶性小(非晶質)的材料,通常其粘度受成形時
的溫度的影響小,不會因溫度上升
射出成型現場實用技術手冊
使用塑膠材料應注意點
1.精密度稍差:膨脹係數大,通常比金屬類多一位數.此外,有些塑膠會因 濕度或經久變形或發生尺寸變化.
2.耐熱性通常不佳:耐高溫性較差,通常不超過100oC. 3.可燃性:大部分屬於可燃性,有些塑膠燃燒時產生有毒氣體.焚化時,容
易產生黑煙或腐蝕性氣體,或發熱量過大,容易損傷焚化爐. 4.強度不夠:除通常提到的破裂強度外,實際上則因剛性不足發生的困
熱硬化性塑膠:thermosets plastics
加熱則硬化的塑膠.成形後加熱固化. 酚樹脂,美拉明樹脂,尿素樹脂,聚酯,環氧樹脂,聚醯亞胺等. 成形: Molding,製成形狀物. 成形品: Moldings,經成形的塑膠製品. 模具: Mold,成形用的模(注進塑膠用). 射出成形: Injection molding 成形粒: Pellet,米粒狀的熱可塑性塑膠成形材料. Mpa : mega pascal : M=106(100萬倍) 1Pa = 1 N/m2 1N (牛頓) = 0.102kgf 1MPa = 10.2 kgf/cm2
流動狀,即變為可塑化狀態. • 3.這可塑化塑膠被柱塞擠向前方,由缸尖端的注嘴注入密封模具內,即射出. • 4.等模具內塑膠冷卻硬化後,打開模具,拿出成形品. • 5.一般使用的成形機都採用如圖2的螺桿式.
射出成型基本原理.ppt

a.昇高料管溫度 b.昇高模具溫度 c.降低射出速度 d.加寬進澆口(如扇形) e.在豎澆道與橫澆道的接 縫或橫澆道分岐點.設材料 滯流區(冷料區).
九.銀條(起瘡)
原因
解決對策
原料中水份或揮發分.附 著模面的水分等氣化所 致成形機螺桿卷入空氣
a.原料必須依特性及作業 標準卻實除濕乾燥. b.增高模具溫度. c.降低料管溫度. d.減低射出速度. e.降低射出壓力. f.昇高螺桿背壓.
持在和初期粘度幾乎一
壓力降低太多時,就
樣的低粘度之流路設計 (流逆、澆口設計)及 成形條件是最理想的狀
會產生射出不足、縮 孔、焊線等成形不良。
況。
(四)、保壓工程
• •
•
•
模加若會封壓就少施 膛壓澆從前封是必加 而力口澆停人澆須的 造則密口止模口利壓 成壓封部保膛部用力 浪力後消壓內的澆保 費不仍失的。固口持 。會然,話在化密時
程
(三)、射出工程
• 1、適當的前端流動速度
• 通常,被射出的熔融樹脂,會流經澆道、流
道、澆口等流路進入模腔內。此時,為了使澆 道、流道部份之樹脂的前端流動速度對模具溫 度產生最小的影響,且提高剪斷發熱效果,基 本上應該是愈快愈好,但有些澆口方式會使成 形品發生射流,或在模腔部份速度太快或太慢 時,都會發生各式各樣的外觀不良。為了解決 這個問題,每一個流路都要進行射出速度的控 制,所以通常都會使用可以讓前端流動速度維 持在適當速度的多段射出速度控制成型機。
..
•
!
不 惜 賜 教 , 謝 謝
講 解 完 畢 , 請 大
20 04 07 14
家
等所 進以
1
行必 1
充須 分以
等
響成直使中 燥 的,未果 射 均 埃
射出成型基础030614
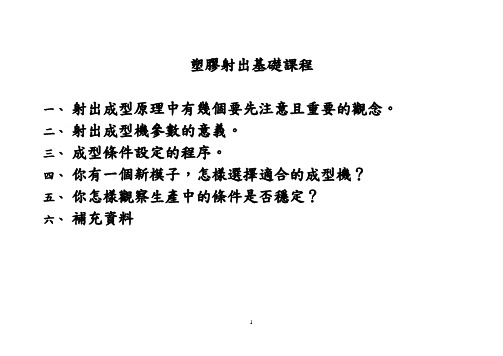
塑膠射出基礎課程一、射出成型原理中有幾個要先注意且重要的觀念。
二、射出成型機參數的意義。
三、成型條件設定的程序。
四、你有一個新模子,怎樣選擇適合的成型機?五、你怎樣觀察生產中的條件是否穩定?1六、補充資料一.射出成型原理中有幾個特別注意且重要的觀念。
材料在模具中流動的2●像岩漿一樣的流動●硬化層●越小越薄的通道越難進入●射出機壓力與模內壓力分開思考3二.射出成型的參數意義1.射出壓:又稱“一次壓”,指成品充填時所需之壓力,操作時是指開始射出到產品的充填至95%時所用之壓力。
2.保壓:又稱“二次壓”,指充填完畢後,持續之壓力。
操作上是指成品最後5%~10%充填完畢後一直維持到澆口凝固後所需之壓力。
3.充填時間(一次壓時間):開始射出到切換保壓間的時間。
位置切換設4定時,壓力、速度、材料流動性、模具構造等所匹配自然產生的時間,一般可從射出機查出。
也可以直接設定。
4.保壓時間(二次壓時間):依材料凝固速度、成品、澆口大小、冷卻速率而決定,由操作者輸入。
理論上可用澆口凝固測量(GATE SEAL)得知,但一般都用經驗值。
5.最大射出壓力:射出機在射膠時泵可出之最大壓力。
6.理論射出容量:一次最多可射出之容積。
57.可塑化能力:單位時間內可熔融多少材料的能力。
8.射出率:單位時間內最多可射出容積的能力。
9.背壓:射出機螺桿計量時,油壓缸對應於螺桿自動後退的阻力,當背壓愈大時,塑料密度愈高,不容易有氣泡,但太大則螺桿不能後退,無法完成計量程序。
反之,螺桿後退快,但塑料密度鬆,易產生氣泡。
6三.成形條件的設定程序1了解材料之限制條件(料溫、流動性、壓力、速度之需求…)2了解模具之限制條件(作動、耐壓強度…)3了解成品之限制條件(不飽模是否會黏模、重量大小…)4確認材料乾燥條件(溫度、時間)是否達到。
5預估成品料量、設定計量。
6依材料特性及模具成品的狀況,設定一次壓、速度。
7保壓設定為零(或極低值)。
78開始射出、觀察充填狀況。
- 1、下载文档前请自行甄别文档内容的完整性,平台不提供额外的编辑、内容补充、找答案等附加服务。
- 2、"仅部分预览"的文档,不可在线预览部分如存在完整性等问题,可反馈申请退款(可完整预览的文档不适用该条件!)。
- 3、如文档侵犯您的权益,请联系客服反馈,我们会尽快为您处理(人工客服工作时间:9:00-18:30)。
厚度對壓力差之探討
• 厚度對壓力差之探討
厚度分布 Thickness Distribution
– 厚度厚,壓力差較小 流動阻力較小區域 流動阻力較大區域 – 厚度薄,壓力差較大 縫合線 Welding Line • 會有黏滯加熱現象產生,造成 溫度上昇,黏度下降 • 流動行為實為流動和熱傳競爭
• 射出時間和壓力關係圖
壓 力 區域1 區域1:粘滯流動控制區
2 1
時間
區域3 區域3:熱傳流動控制區 區域2 區域2:最佳成型控制區
3
保壓過程原理
保壓過程說明 流率
壓力
time
• 更多塑料進入模穴以防止產品收縮變形。 更多塑料進入模穴以防止產品收縮變形。
• 此一階段稱為壓力控制階段。 此一階段稱為壓力控制階段。
水管直徑 D (mm) 5 8 10 12 15 20 25 30 水流量 Q (cc/sec) 40 64 80 96 120 160 200 240 油流量 Q (ss/sec) 115 184 230 276 345 460 575 690
Q in cc/sec, D in mm
2500πDη 8 D for water Q≥ ≈ for oil ρ 23 D
速度分布 剪切率分布 分子鏈配向性 配向性遞減 decrease in molecular chain orientation orientation
速度差造成配向說明
velocity profile
shear rate profile
遲滯效應
• 遲滯效應
– 因厚度差,而造成流動趨勢不一現象
• 厚度薄,阻力增加,造成塑料冷卻,先到 先冷卻 • 厚度差異大,造成流動趨勢改變
成型週期 35 模溫 20 射出 開模 最高模溫
平均模溫 最低模溫 時間
(佔成型週期最長)
– 脫模時間
(熱變形溫度下頂出)
影響冷卻速率因素
• 塑件厚度設計
– 約和厚度成平方比
tc ∝ h 2
• 冷卻方式
– – – – 模材選擇 冷卻管配置 冷卻液性質 冷卻液流速
• 塑料種類 • 加工參數
冷卻時間粗估
C r y s t a llin e P o ly m e r 181 P O M /A c e t a l 225 PET 225 P E T -G F 225 PETG 225 PBT 225 P B T -G F 220 PA 6 220 P A 6 -G F 265 P A 6 /6 265 P A 6 /6 - G F 265 P A 6 /6 - C F 227 P A 6 /1 0 1 9 4 /1 7 9 P A 1 1 /P A 1 2 290 PPS 275 F E P /T e f lo n 334 PEEK 330 LCP S e m ic r y s t a llin e P o ly m e r 110 LDPE 90 LLDPE 125 MDPE 130 HDPE 176 PP 176 P P /G F 120 P P O /P P E 120 P P O -G F
熱傳較佳 熱傳較差
速度分布 剪切率分布 速度分布 剪切率分布
成型參數對壓力差之探討
• 成型參數對壓力差之探討
– 充填速度
• 高速充填,其行為往往取決於充填體積大小 • 慢速充填,其行為往往取決於產品厚度
– 模具溫度 高速充填 – 塑料溫度
慢速充填
噴泉流動
• 噴泉流動
冷卻水管
流動波前
遠離流動波前之速 度分布,全展流, 以剪切流動為主
• 螺桿儲料以進行下一週期成型準備。 螺桿儲料以進行下一週期成型準備。
Back
頂出階段說明
•當產品固化到足以頂出強度時,射出成型機台之頂出單元便行頂出。 當產品固化到足以頂出強度時,射出成型機台之頂出單元便行頂出。 •頂出後便進行閉模動作,為下一週期準備。 頂出後便進行閉模動作,為下一週期準備。
塑件冷卻過程
常見塑料溫度設定
P la s t ic s T m e lt ( o C ) T p ro c . ( o C )
1 8 0 -2 0 0 1 7 0 -2 7 0 2 6 0 -3 1 0 1 9 0 -2 7 5 2 2 0 -2 8 0 2 4 5 -2 7 0 2 3 0 -2 6 0 2 7 0 -2 9 0 2 6 0 -2 9 0 2 8 0 -3 0 0 2 8 0 -3 0 5 250 2 1 0 -2 5 0 3 0 0 -3 6 0 315 3 6 0 -4 0 0 4 0 0 -4 3 0 1 7 0 -2 4 0 1 7 0 -2 0 0 1 9 0 -2 6 0 2 0 0 -2 8 0 1 8 0 -2 8 0 2 6 0 -2 8 0 2 2 0 -3 2 0 2 5 0 -3 4 5
air-trap
流動平衡
• 流動平衡
– 具流動平衡設計模具,一般而言可具較均一品質
• 在多模穴設計中,可使各模穴產品品質均一 • 在單模穴中可減少產品局部過度充填現象,避 免撐模及毛邊現象產生
不平衡之澆道系統 不平衡之澆道系統
可能發生充填不飽的模穴
過度保壓的模穴
由於遲現象造成充填不飽的模穴
最佳化成型時間
冷卻分析目的
• 冷卻分析目的
– 預估冷卻時間及成型週期長短 – 冷卻系統設計的最佳化
• 使塑件各部的冷卻效果均勻而有效 率 • 因冷卻不均造成塑件的翹曲變形
冷卻分析所需物性資料
• 塑膠材料熱物性質
– 密度(density) – 比熱(specific heat)或熱容量(heat capacity) – 熱傳導係數(thermal conductivity)
• 平板型塑件
W L
4 Tm − Tw tc = ln 2 απ π Te − Tw h
2
h
Tm = 冷卻初塑料溫度℃ Tw = 模具溫度℃ Te = 塑料頂出溫度℃
d=2R L
• 圓型塑件
Tm − Tw tc = 0.173 ln 1.6023 T − T α e w R2
Back
充填基本流動方式
熔膠波前 Melt Front
• 充填基本流動方式
– 圓管流動 – 平板流動 – 徑向流動
圓管流動 Tube Flow 針點進澆
平板間流動 Flow between Plates
徑向(輻射型)流動 Radial Flow 熔膠波前 Melt Front
充填基本流動模式
• 充填基本流動模式
T degr (oC )
222 320 320 280 288 288 310 310 310 310 310 310 310 508
T e je c ( o C )
110 150 150 60 125 125 130 130 160 160 160 130 135 120 170
T m o ld ( o C )
• 塑件冷卻過程
模具本體 Mold Base 冷卻水管
熱傳導
Heat Conduction
Cooling Lines
熱對流 Heat Convection
模穴(塑件) 模穴(塑件)
Cavity(Part) 熱傳導Heat Conduction
模溫週期變化
• 模溫週期變化
– – – – 合模時間 充填時間 保壓時間 冷卻時間
• 冷卻液性質
– 黏度(viscosity), 密度,[g/cc] – 比熱,[erg/g-K],熱傳導係數,[erg/sec-cm2-K]
• 模材熱物性質
– 密度,[g/cc],熱傳導係數 ,[erg/sec- cm2 -K]
Back
冷卻水管參數的設定
• 冷卻液流量的設定應該儘可能達到紊流 (turbulent flow)狀態,使熱傳效果較佳
• 平行流動方向,收縮率較大 • 垂直流動方向,收縮率較小
– 對加玻纖塑務料影響更大
局部流場 分子鏈局部受力情形 速度梯度較低 lower velocity gradient 速度梯度較高 higher velocity gradient local flow field forces acting on molecular chain molecular chain orientation 配向情形
– 壓力差為主要動力 – 塑料流動趨勢
• 往阻力小區域流動 • 單位時間內流動距 離大,表阻力小 • 單位時間內流動距 離小,表阻力大
流動阻力較大區域,流 動波前等位線較為密集 流動阻力較小區域,流 動波前等位線較為稀疏 厚度分布 Thickness Distribution
影響壓力差主要因素
• 影響壓力差主要因素
335 335 335 335 328 330 350 350
80 80 90 100 90 90 120 120
常見塑料溫度設定
Plastics T m elt ( C)
o
T proc . ( C)
180-280 170-260 220-270 190-280 170-270 170-235 180-215 190-230 260-320 300-330 230-300 250-280 170-190 190-215 190-220 310-400 330-380 305-370 340-425 230-260
保壓過程流動探討
• 保壓過程流動探討
– 防止收縮變形 – 降低收縮差 – 殘留應力產生
保壓流動將沿局部阻力較小 路徑前進並向兩側傳遞壓力
熔膠溫度對模穴壓力探討
• 熔膠溫度對模穴壓力探討