CAE仿真与分析
cae仿真的基本流程

cae仿真的基本流程以CAE仿真的基本流程为标题,本文将介绍CAE仿真的基本流程,包括前处理、求解和后处理三个主要步骤。
一、前处理前处理是CAE仿真的第一步,主要包括几何建模、网格划分和边界条件设置。
几何建模是将待仿真的物体或结构通过CAD软件进行建模,以获取其几何形状和尺寸等信息。
网格划分是将几何模型划分成离散的小单元,如三角形或四边形,在每个单元上建立数值计算模型。
边界条件设置是根据仿真目的和实际情况,为几何模型的边界面设置初值或边界条件。
二、求解求解是CAE仿真的核心步骤,主要包括材料属性定义、加载条件设置和数值计算。
材料属性定义是为待仿真的物体或结构选择合适的材料参数,如弹性模量、泊松比等。
加载条件设置是根据仿真目的和实际情况,为待仿真的物体或结构施加合适的加载条件,如力、压力、温度等。
数值计算是根据已定义的几何模型、材料属性和加载条件,利用数值计算方法求解结构的力学响应,如位移、应力、应变等。
三、后处理后处理是CAE仿真的最后一步,主要包括结果输出和分析。
结果输出是将数值计算得到的仿真结果以图形或表格的形式输出,如位移云图、应力分布图等。
分析是根据输出的仿真结果,对待仿真的物体或结构进行分析和评估,如强度分析、疲劳分析等。
总结:CAE仿真的基本流程包括前处理、求解和后处理三个主要步骤。
前处理阶段主要是对几何模型进行建模、网格划分和边界条件设置;求解阶段主要是对材料属性进行定义、加载条件进行设置,并利用数值计算方法求解结构的力学响应;后处理阶段主要是将仿真结果进行输出和分析。
通过CAE仿真的基本流程,可以更加准确和全面地了解待仿真物体或结构的性能和行为,为设计和优化提供科学依据。
CAE仿真分析流程

CAE仿真分析流程CAE(计算机辅助工程)仿真分析是一种利用计算机实现的工程分析方法,以模拟和预测工程产品和系统的性能。
它通过数值计算和模型来代替传统的试验方法,可以快速、准确地评估产品的设计和性能。
下面是CAE仿真分析的流程及其步骤。
第一步:准备工作在进行CAE仿真分析之前,需要建立分析目标和所需的输入数据、边界条件以及使用的CAD模型。
这包括收集和整理相关数据,制定分析方案和目标。
第二步:建立数值模型在这一步,需要将CAD模型转化为数值模型,以便进行数值计算。
这可以通过网格划分和离散化来实现。
划分网格时,需要考虑模型的几何和结构特征。
第三步:设定物理和数学模型在这一步中,需要选择适当的物理模型(如流体动力学、热传导等)和数学模型(如有限元法、有限差分法等)。
物理模型会影响模拟的准确性和计算效率。
第四步:设定边界条件在这一步中,需要指定问题的边界条件,如约束、加速度和载荷等。
这些条件会直接影响计算结果和仿真分析的准确性。
第五步:进行数值计算在这一步中,使用所选的数值方法和模型进行数值计算。
这包括解方程组、求解数值逼近方程以及处理非线性和非定常问题等。
第六步:分析结果在这一步中,需要对数值计算的结果进行分析和解释。
这可能涉及到图形绘制、数据处理和统计分析等。
通过分析结果,可以评估产品的性能和优化设计。
第七步:验证和验证在这一步中,需要对模拟结果进行验证和验证。
这可以通过将仿真结果与真实试验数据进行比较来实现。
如果两者之间有良好的一致性,那么该模拟可以用于预测实际情况。
第八步:优化设计根据仿真结果和分析,可以对设计进行优化。
可以通过调整材料、几何形状和边界条件等来改善产品的性能。
第九步:迭代在这一步中,如果发现仿真结果与实际情况不一致,可以对模型和分析方法进行调整和迭代。
这可以提高仿真的准确性和可靠性。
总结CAE仿真分析是一种快速、准确和经济实用的工程分析方法。
通过建立数值模型、设定物理和数学模型、进行数值计算和分析结果,可以预测产品性能和优化设计。
CAE仿真分析报告
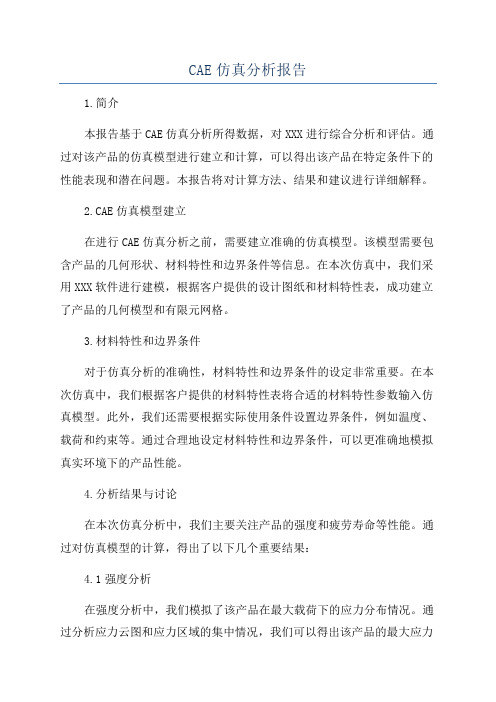
CAE仿真分析报告1.简介本报告基于CAE仿真分析所得数据,对XXX进行综合分析和评估。
通过对该产品的仿真模型进行建立和计算,可以得出该产品在特定条件下的性能表现和潜在问题。
本报告将对计算方法、结果和建议进行详细解释。
2.CAE仿真模型建立在进行CAE仿真分析之前,需要建立准确的仿真模型。
该模型需要包含产品的几何形状、材料特性和边界条件等信息。
在本次仿真中,我们采用XXX软件进行建模,根据客户提供的设计图纸和材料特性表,成功建立了产品的几何模型和有限元网格。
3.材料特性和边界条件对于仿真分析的准确性,材料特性和边界条件的设定非常重要。
在本次仿真中,我们根据客户提供的材料特性表将合适的材料特性参数输入仿真模型。
此外,我们还需要根据实际使用条件设置边界条件,例如温度、载荷和约束等。
通过合理地设定材料特性和边界条件,可以更准确地模拟真实环境下的产品性能。
4.分析结果与讨论在本次仿真分析中,我们主要关注产品的强度和疲劳寿命等性能。
通过对仿真模型的计算,得出了以下几个重要结果:4.1强度分析在强度分析中,我们模拟了该产品在最大载荷下的应力分布情况。
通过分析应力云图和应力区域的集中情况,我们可以得出该产品的最大应力点和应力集中区域。
根据计算结果,我们发现产品的强度较高,没有明显的应力集中区域。
4.2疲劳分析在疲劳分析中,我们模拟了该产品在长期使用条件下的疲劳寿命。
通过设定适当的载荷条件和循环次数,我们可以计算出产品的寿命曲线和疲劳寿命。
根据计算结果,我们发现产品在设计寿命内可以正常工作,并且没有出现严重的疲劳损伤。
5.问题与建议通过对仿真结果的分析,我们发现该产品在设计条件下表现良好,没有明显的问题。
5.1强度优化虽然该产品的强度较高,但我们建议客户在设计上进一步考虑一些强度优化的手段,例如增加壁厚或者加强一些关键部位的结构,以进一步提高产品的强度和可靠性。
5.2疲劳寿命提升尽管该产品疲劳性能良好,但我们建议客户在设计上考虑一些疲劳寿命提升的措施,例如使用更高强度的材料或者改变产品的形状,以延长产品的使用寿命。
CAE仿真分析流程

CAE仿真分析流程CAE仿真分析是一种基于计算机数值方法的工程分析方法,可以帮助工程师在设计开发过程中评估和优化产品的性能,包括结构强度、疲劳寿命、动态响应、流体力学、热传导等方面。
本文将介绍CAE仿真分析的流程,并以汽车碰撞仿真为例进行说明。
1.问题定义首先,需要明确模拟分析的目的和范围,明确需要分析的问题和关键因素。
例如,在汽车碰撞仿真中,需要评估车辆在不同碰撞条件下的结构强度和安全性能。
2.建立数值模型根据问题定义,建立数值计算模型。
对于复杂的结构,可以进行三维建模,并确定材料属性、载荷和边界条件等。
例如,在汽车碰撞仿真中,需要根据车辆CAD模型建立有限元模型,并确定材料模型和碰撞速度、角度等载荷条件。
3.网格划分对于建立的数值模型,需要进行网格划分,将结构划分成小的三角形、四面体或六面体等形状,以便进行数值计算。
网格划分需要根据结构复杂度和计算精度进行调整。
利用数值方法对建立和网格划分后的数值模型进行求解,得到模型在受力、变形等情况下的应力、位移、速度等结果。
在汽车碰撞仿真中,可以通过求解非线性动力学方程组,获得车辆碰撞前后的位移、速度、加速度等参数。
5.结果后处理对求解后得到的数值结果进行后处理,包括数据展示、可视化、统计分析等。
例如,在汽车碰撞仿真中,可以通过捕捉每个节点的受力和变形情况,评估车辆的结构强度和安全性能,并进行可视化展示。
6.评估和优化根据模拟结果,评估设计方案的性能,并进行优化改进。
此时可以调整材料选择、几何形状、结构布局等方面,以提高产品性能和降低成本等。
总结CAE仿真分析流程涵盖了问题定义、数值模型建立、网格划分、数值求解、结果后处理和评估、优化等步骤。
在工程设计中,CAE仿真分析已经成为必不可少的工具,它可以减少实验成本,提高产品性能和设计效率,为科技创新和可持续发展提供支持。
CAE-轿车设计中CAE仿真分析

六 轿车开发中CAE的应用
轿车产品的四个阶段, 筹划阶段; 概念设计和可行性研究; 产品设计和原型车确认; 定型生产等四个阶段。
需18-32个月时间。CAE 技术在开发工作的后三个阶段 都有十分重要的应用。
轿车更侧重时代流行潮流和舒适性,现代轿 车市场生命时间越来越短,一般变型车设计变化最 大的是车身。所以车身是轿车开发的重点
六 轿车开发中CAE的应用
产品设计重点是白车身
白车身设计的一个重点是交叉节结构的 连接方法。它对车身刚度、强度都有
较大的 影响。 必要时 应该进 行重点 分析研 究。
六 轿车开发中CAE的应用
确认设计:解决问题并进行投产准备:
l 针对实验产生的问题(疲劳、NVH、轻 量化、碰撞安全、噪声等问题)进行有目的 分析,提出问题点的焦点,改进的对策。
l 消除汽车的卡嗒声(Rattle)
l 有产品图纸、资料、试验结果。对产品 进行详细分析,结果保存为技术档案。进行 技术总结。这是验证分析条件,建立CAE规范 的大好时机。
六 轿车开发中CAE的应用
确认设计--解决问题、进行投产准备:
l 变形车开发中应用 CAE l 工艺设计和生产准用
# CAE软件的现代进展
• CAE总体发展趋势向专业化方向发 展
• CAE分析功能大幅度提高
– 分析对象: – 分析项目: – 应用科目: – 分析内容: – 分析类别:
• 分析周期与CAD设计同步
• 使用方法简化,应用和结果明确直 观
二 CAE 在汽车技术上的应用
要求对分析入口文件、模型化方法、加 载、分析结果处理、评价标准等建立本企 业的标准化的统一方法。 分析不因人 而异,分析结果纵横对比,评价客观。提 升CAE结果应用价值。不满足于 个案的对 比分析。
CAE结构仿真分析及技术培训

CAE结构仿真分析及技术培训CAE(计算机辅助工程)结构仿真分析是一种通过计算机模拟和计算来预测和评估结构行为的技术。
随着计算机技术的不断进步和发展,CAE结构仿真分析在工程领域中得到了广泛的应用。
它能够帮助工程师快速准确地评估和优化产品设计、优化材料和工艺选用,提高产品的性能和质量,缩短产品研发周期和开发成本。
CAE结构仿真分析主要包括有限元分析(FEA)、计算流体力学分析(CFD)、多体系统动力学分析(MBD)等。
其中,有限元分析是最常用的一种技术,它通过将结构离散为有限数量的有限元单元来近似连续结构,利用数学方程求解方法对结构进行模拟和计算。
有限元分析可以用来预测结构的强度、刚度、振动响应、疲劳寿命等性能,帮助设计师评估和改善产品设计。
CAE结构仿真分析的优势在于可以全面、详细地观察和分析结构的应力、应变、变形等行为,比传统的试验方法更加灵活、高效、经济。
同时,CAE还可以进行多种不同工况的模拟和比较分析,帮助设计师进行全面的优化,提供更合理的设计方案。
对于工程师来说,掌握和运用CAE结构仿真分析技术是非常重要的。
因此,进行CAE结构仿真分析技术培训是必要的。
在培训中,首先需要学习计算力学、结构力学的基础知识,了解有限元分析的基本原理和方法。
然后,学习和熟悉常用的CAE软件,掌握软件的使用和操作技巧。
在培训中最好能有一些实际案例和工程应用,通过实践来提高学员的能力和技巧。
在CAE结构仿真分析技术培训中,可以设置以下几个主要内容:1.理论知识教学:包括计算力学、结构力学的基本原理和方程,有限元分析的基本概念和方法等。
2.软件操作培训:介绍常用的CAE软件,如ANSYS、ABAQUS等,讲解软件的功能和特点,讲解软件的界面和操作方法,以及如何建立结构模型、设置边界条件、求解和分析结果等。
3.实例分析:通过一些实际工程案例的仿真分析,让学员了解和熟悉实际工程中的问题和解决方法,通过实践来提高分析能力和技巧。
CAE结构仿真分析及技术培训
CAE结构仿真分析及技术培训----强度、振动与优化中国科学院深圳先进技术研究院产品与工程仿真实验室1、题目:电子机械产品结构强度与振动性能分析报告人:吴忠鸣工程师个人简介吴忠鸣硕士,工程师,2005年获华中科技大学材料加工硕士学位。
2005年7月至2009年5月在富士康科技集团华南检测中心机构仿真实验室任职,2009年5月加入深圳先进技术研究院产品与工程仿真实验室。
研究领域主要包括:结构方向的强度及疲劳分析、显式动力学、振动与噪声等,从事结构相关的产品设计优化与结合仿真手段的新产品的设计研发。
主持或参与项目:1、NOKIA及MOTOROLA多款手机跌落、球落仿真及相关零组件强度与疲劳分析:通过校验手机整机在跌落、球落工况下的强度,以及对转轴抗扭强度及工作状况和FPC的应力及疲劳分析(压延铜),为设计方案提供改进建议;2、多款知名品牌电脑机箱整机模态、响应及随机振动分析:机箱在随机振动测试中部件会出现开裂现象,通过整机模态、频率响应及随机振动一系列分析找出关键频率,通过优化结构设计及改良连接方式消除开裂现象;3、电脑PCB板组件级静力分析:针对DELL某型号机箱组件级PCB板进行了细致的建模及静力分析,在一定载荷条件下,控制PCB板上的芯片引脚周围应变在一定范围内;4、温控开关弹片强度分析及灵敏性优化:通过对温控开关的工作过程仿真,寻找影响温控开关灵敏性的因子,改善尺寸、工艺参数提高了温控开关的灵敏性;5、带包装微波炉的跌落仿真及产品结构与包装设计的优化。
校验带包装微波炉整机跌落工况下的强度,优化EPS包装结构,降低了跌落冲击加速度。
题目:电子机械产品结构强度与振动性能分析报告内容:一、力学及材料学基本概念二、有限元方法基础及其基本实现过程三、有限元方法在行业中的应用1、静载强度问题2、跌落、冲击与碰撞问题3、模态、振动问题材料破坏现象:工程结构正常工作应满足以下要求:1、强度要求应有足够的抵抗破坏的能力;2、刚度要求应有足够的抵抗变形的能力;3、稳定性要求应有足够的保持原有平衡形态的能力。
CAE-整车碰撞仿真分析
整车碰撞仿真分析完成整车建模、设置好相应的测试单元,并核对模型整车情况与试验完全一致后即可将模型提交计算,完成计算后即可对结果进行分析。
正面刚性壁碰撞仿真分析内容主要包括:仿真计算可信性分析;整车和关键部件变形分析;B柱速度/加速度分析;A柱折弯分析;前侵入分析;假人伤害情况分析。
1 仿真计算可行性分析在整车碰撞仿真中虽然顺利完成计算,但由于有以下三个原因的存在并不能保证该计算结果完全准确可靠。
(1)在有限元仿真计算中涉及多种积分算法和不同的接触算法,系统为保证计算正常进行有时会自动增加某些部件的质量,如果该质量增加太多则会导致后期计算结果不可信。
(2)为节约计算时间计算中更多时候采用了非全积分的积分算法,这时将有可能在计算中发生沙漏,导致系统总体能力不守恒。
(3)在接触计算中如果接触设置不合理,将有可能产生较大的界面滑移能,这也是导致系统总能量不守恒的重要因素。
所以在顺利完成仿真计算后,需要对计算结果进行分析。
只有由于上述因素导致的质量增加和能量变化在可接受的范围内,再能认为该模型仿真计算结果是可信的,值得分析的。
打开计算输出的glstat文件或binout文件的glstat选项(见图1. 1),可以方便查看模型计算中涉及的以上因素变化曲线。
图1.1binout文件glstat选项菜单质量增加和能量变化查看内容为added_mass、energy_ratio,一般要求最终质量增加和能量变化不得超过5%,通常计算中初始质量增加在10kg以内,随着计算的进行整车质量还将有所增加。
关于能量变化曲线一般查看hourglass_energy、internal_energ y、kinetic_energy、interface_energy、total_energy这五项。
通常情况这五条曲线形状大致如图1.2。
图1.2仿真过程中能量变化曲线如图1.2可以观察到系统动能逐步转换为内能的过程,图中几条曲线一般应该为光滑过渡,如果在某位置发生突变则有可能是这个位置发生了较大的沙漏或质量增加。
汽车工业虚拟仿真及CAE分析解决方案
汽车工业虚拟仿真及CAE分析解决方案汽车工业是一个技术密集型的行业,虚拟仿真和计算机辅助工程(CAE)分析是其发展的重要方向之一、虚拟仿真和CAE分析解决方案可以提供全面的工程设计和性能分析,帮助汽车制造商和供应商提高产品质量、降低成本和缩短开发周期。
虚拟仿真是一种使用计算机模型和数值方法来模拟和预测汽车产品性能的技术。
虚拟仿真可以通过建立车辆结构的三维数学模型,计算和分析各种力学、热力学、流体力学等物理过程,预测车辆在各种条件下的运动、应力和变形等性能指标。
通过虚拟仿真,汽车制造商可以在产品实际制造前,进行全面的性能评估和优化设计,提高产品质量,减少实验试验和原型制造,降低研发成本。
虚拟仿真解决方案可以应用于各个汽车部件和系统的设计和分析。
例如,对于车身结构设计,虚拟仿真可以通过优化钢板厚度分布和梁的布置,实现轻量化设计,提高强度和刚度,同时降低整车质量和燃料消耗。
对于悬挂系统设计,虚拟仿真可以模拟车辆在不同路况下的动力学行为,评估悬挂系统的舒适性和稳定性。
对于发动机设计,虚拟仿真可以预测燃烧过程、热传导和流体力学,评估发动机的性能和排放。
CAE分析解决方案主要包括有限元分析(FEA)、计算流体力学(CFD)、多体动力学分析(MBD)、可靠性和优化等。
有限元分析可以对复杂结构和部件进行强度、刚度和模态等分析,为制造商提供准确的应力和应变分布数据。
计算流体力学可以对流体介质中的流动、传热和传质等过程进行数值计算,评估汽车系统的热管理和气动性能。
多体动力学分析可以模拟汽车在不同路况下的运动和悬挂系统的工作特性,评估车辆的舒适性和稳定性。
可靠性和优化分析可以通过数学模型和算法,实现汽车设计的最优方案选择和参数优化。
总之,汽车工业虚拟仿真和CAE分析解决方案是现代汽车工程设计的重要工具。
它可以帮助汽车制造商和供应商进行全面的工程设计和性能分析,提高产品质量、降低成本和缩短开发周期。
随着计算机技术和仿真算法的不断发展,虚拟仿真和CAE分析将在汽车行业中发挥越来越重要的作用。
cae分析报告
cae分析报告CAE(计算机辅助工程)是一种通过计算机模拟和仿真技术来分析物体性能和行为的方法。
它在各个领域都得到了广泛的应用,例如汽车工程、航空航天、建筑结构等。
本篇文章将对CAE分析报告进行探讨,介绍其意义、内容和编写要点。
一、概述CAE分析报告是基于对实际物体进行仿真和模拟后得到的结果,用于评估物体的性能、强度、对环境的响应等。
它提供了全面的分析结果和可行的改进方案,为工程师和设计师在产品开发和优化过程中提供指导意见。
因此,编写一份准确、详细的CAE分析报告对于工程项目的成功和效率至关重要。
二、内容1. 建模与网格划分CAE分析的第一步是建立物体的数学模型,并进行网格划分。
模型的精确度和网格质量将对计算结果的准确性产生重要影响。
因此,在报告中需要详细描述建模过程,包括采用的软件和方法、模型的几何特征、所选网格类型和质量等。
2. 载荷和约束条件在进行CAE分析前,需要确定物体所受的外部载荷和内部约束条件。
比如,在汽车工程中,载荷可以是行驶在不同路况下的动态载荷,约束条件可以是车轮在地面上的接触条件。
在报告中,需清晰地描述这些载荷和约束条件,并给出计算依据和分析原理。
3. 结果分析CAE分析的核心是得到准确的结果,并进行深入的分析与解释。
在报告中,应包括物体的应力分布、变形情况、疲劳寿命、流体流动轨迹等相关结果。
同时,需要对结果进行分析,解释其原因和影响,并与实验数据进行对比,以验证模型的准确性。
4. 优化方案根据CAE分析的结果,可以提出改进和优化方案,以提高产品的性能和可靠性。
在报告中,需要详细描述这些方案的设计思路和实施步骤。
同时,对于每个方案,应进行CAE分析以评估其效果,并给出具体的指导建议。
三、编写要点1. 语言简洁明了:CAE分析报告通常是给工程师和设计师阅读的,因此要避免使用过于专业或晦涩的术语和定量方法。
尽可能使用简单明了的语言,使读者能够轻松理解和掌握分析结果。
2. 图表展示清晰:在CAE分析报告中,经常使用图表来展示结果和数据。
- 1、下载文档前请自行甄别文档内容的完整性,平台不提供额外的编辑、内容补充、找答案等附加服务。
- 2、"仅部分预览"的文档,不可在线预览部分如存在完整性等问题,可反馈申请退款(可完整预览的文档不适用该条件!)。
- 3、如文档侵犯您的权益,请联系客服反馈,我们会尽快为您处理(人工客服工作时间:9:00-18:30)。
流体分析 空调系统
热-结构耦合场应力分析 发动机内场
被动安全性CMVDR294
被动安全性CMVDR294
初始车速50km/h
车速变化
被动安全性CMVDR294
A柱变形
门框变形量
被动安全性仿真
被动安全性 车门静挤压强度
冲压分析 板金件成形
动力学、运动学分析
整车动态受力分析主要包括整车的操纵稳定性分析,整车的平顺性分析 操纵稳定性分析包括稳态转向,角阶跃,角脉冲等虚拟试验分析。
CAD&CAE建模能力
CAD&CAE建模能力
分析基本流程
求解器
三维CAD
3
传递计算结果
建立三维几
何模olid格
1
式文件
前、后处理
可视化计算
结果输出
4
弯曲刚度
热-结构耦合分析 振动与噪声分析
被动安全性
扭转刚度
模态分析
流体分析
应力和疲 劳寿命分 析 冲压成形
动力学、运动学分析
某变速器操纵机构运动分析
动力学、运动学分析
车门玻璃升降分析
玻璃与车门内的其它 零件干涉校核
动力学、运动学分析
某后备行李厢弹簧刚度及其预载分析
动力学、运动学分析
滑移门开启过程运动分析
汽车设计过程中的CAE
上海同济同捷科技股份有限公司 同济同捷汽车设计工程研究院
CAE 推动产品与技术创新的动力源泉 CAE 是实现汽车自主开发的必须手段
CAE工作内容
• 概念设计阶段
– 建立设计标准,确定性能目标 – 基于设计要求以及布置结构研究汽车的结构性能
• 样车试制阶段
– 根据设计结果评估和分析汽车性能 – 根据分析结果提出建议改进设计中存在的缺陷和不足 – 将样车的试验结果与CAE分析结果进行对比
• 产品开发阶段
– 结构分析、检查与计算校核 – 结构优化
CAE技术优点
• 实现优化设计 • 缩短产品设计周期,增强了竞争力 • 提高产品质量 • 减少设计过程中人力、物力的消耗 • 促进设计的标准化、系统化
CAE技术在汽车设计过程中应用
• 分析和设计紧密结合、设计和分析同步 • 向大规模集成方向发展 • 大幅度提高分析能力 • 基于显式分析的高度非线性求解为工艺分析提供可能 • 整车安全性分析用于实际汽车安全性设计 • 计算机图形化显示水平不断提高 • 软件提供二次开发语言用于开发满足客户需求的软件
根据某大型汽车厂要求,在其原有的车型基础上进行前悬架改制,改进并优化该车前桥,使其满 足车厢地板离地高度为340mm的要求,并且其它各项性能也符合设计要求
动力学、运动学分析
车轮定位参数和悬架杆系的布置直接影响到整车的操纵稳定性,因此合理的 车轮定位参数变化值及变化趋势对整车行驶性能尤为重要。
动力学、运动学分析
动力学、运动学分析
通过各种试验分析已经成功解决了几个车的操纵稳定性问题并且得到了相关的验证。除了一 般性能的分析,其它的性能也得到了相应的印证。
动力学、运动学分析
平顺性随机输入分析
动力学、运动学分析
某发动机在高速旋转 时曲柄轴径受力状况
某汽车雨刮器 人机工程学设计
某客车前桥改制
动力学、运动学分析
在底盘设计过程中,一般情况下会涉及到大量的运 动部件,这些部件相互间的关系,往往会影响车轮定位参数 变化趋势,更进一步影响到悬架及整车的性能。
动力学、运动学分析
在分析过程中往往会涉及到大量的参数,例如弹性铰链的 特性,弹簧的刚度,关键点的位置等等。这些数据有的可以从数 学模型中得出,有的需要做相关试验测量。
多刚体运动学&动力学分析
弯曲刚度 轿车白车身
弯曲刚度 客车骨架&蒙皮
扭转刚度 轿车白车身
扭转刚度
6 5 4 3 2 1
客车骨架&蒙皮
模态分析 弯曲、扭转振型
应力分析 零部件
应力分析 桁架结构
疲劳寿命分析 疲劳寿命
振动与噪声分析
模态分析 频率响应分析 排气系挂点优化 乘坐室声场分析
流体分析 外流场