循环流化床燃烧技术旋风分离器
循环流化床锅炉中旋风分离器的设计与探讨

粒, 旋风分离器都可以完全捕集 , 而后者对 d。 5 的颗粒
粒径 刚好 有 5 %被 捕 集 , 程上 常 采 用 d 。 进 行 设 0 工 来
Vo | I 3 No. 4
Oc . 2 07 t 0
循 环 流 化 床 锅 炉 中 旋 风 分 离 器 的 设 计 与 探 讨
黄新章 王永波 郑传 贵 徐 有宁 , , ,
( . 阳工程 学院 动力 工程 系 , 阳 1 0 3 ; . 宁科 林环保 工程 有限 责任公 司 , 阳 10 3 ; 1沈 沈 116 2 辽 沈 10 4
计l. 2 临界 分 离 粒 径 的 大 小 决 定 于 分 离 器 的结 构 尺 ] 寸 , 以应在满 足一 定分离 效率 的条件 下 , 算临 界分 所 计
离粒 径 , 临界分 离粒径 确定 后 , 根据 经验公 式来确 定 再
是 用分离器 的效 率和 压 损来 衡 量 、 中分离 效 率 高 低 其
关键 词 :旋 风 分 离 器 ; 离效 率 ; 分 临界 分 离粒 径 中 图分 类 号 :TO 5 0 文 献 标 识 码 :A 文 章 编 号 :17 —1 0 (0 7 0 6 3 6 3 2 0 )4—0 3 3 3—0 2
旋 风分离 器是 结构 简 单 、 易 制造 和 安装 的 常见 容 的化工设 备 , 在食 品 、 医药 、 日用化 工 以及 冶金 电力 等
为衡 量其好 坏 的最 主要 指标 , 即旋 风 分 离 器处 理 后 的
循环流化床锅炉高温绝热旋风分离器超温分析及技术改造浅谈
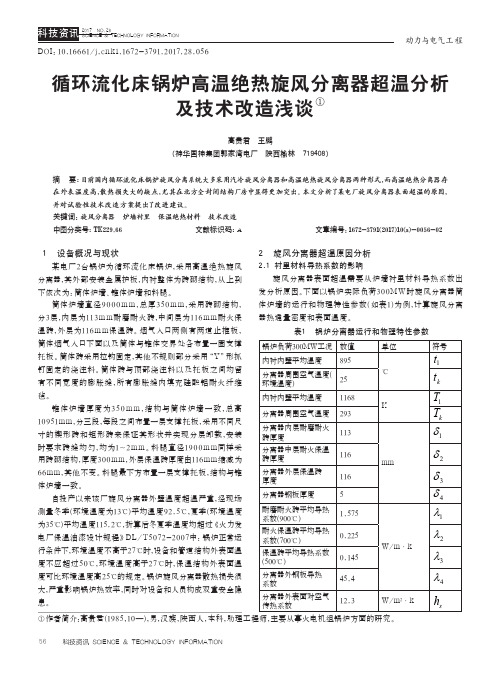
动力与电气工程56科技资讯 SCIENCE & TECHNOLOGY INFORMATIONDOI:10.16661/ki.1672-3791.2017.28.056循环流化床锅炉高温绝热旋风分离器超温分析及技术改造浅谈①高贵君 王鹏(神华国神集团郭家湾电厂 陕西榆林 719408)摘 要:目前国内循环流化床锅炉旋风分离系统大多采用汽冷旋风分离器和高温绝热旋风分离器两种形式,而高温绝热分离器存在外表温度高,散热损失大的缺点,尤其在北方全封闭结构厂房中显得更加突出。
本文分析了某电厂旋风分离器表面超温的原因,并对试验性技术改造方案提出了改进建议。
关键词:旋风分离器 炉墙衬里 保温绝热材料 技术改造中图分类号:TK229.66文献标识码:A文章编号:1672-3791(2017)10(a)-0056-021 设备概况与现状某电厂2台锅炉为循环流化床锅炉,采用高温绝热旋风分离器,其外部安装金属护板,内衬整体为砖砌结构,从上到下依次为:筒体炉墙、锥体炉墙和料腿。
筒体炉墙直径9000m m,总厚350m m,采用砖砌结构,分3层,内层为113m m 耐磨耐火砖,中间层为116m m 耐火保温砖,外层为116m m保温砖。
烟气入口两侧有两道止推板,筒体烟气入口下面以及筒体与锥体交界处各布置一圈支撑托板。
筒体砖采用拉钩固定,其他不规则部分采用“Y”形抓钉固定的浇注料。
筒体砖与顶部浇注料以及托板之间均留有不同宽度的膨胀缝,所有膨胀缝内填充硅酸铝耐火纤维毡。
锥体炉墙厚度为350m m,结构与筒体炉墙一致,总高10951mm,分三段,每段之间布置一层支撑托板,采用不同尺寸的楔形砖和矩形砖来保证其形状并实现分层卸载,安装时要求砖缝均匀,均为1~2m m。
料腿直径1900m m同样采用砖砌结构,厚度300mm,外层保温砖厚度由116mm缩减为66mm,其他不变。
料腿最下方布置一层支撑托板,结构与锥体炉墙一致。
自投产以来该厂旋风分离器外壁温度超温严重,经现场测量冬季(环境温度为13℃)平均温度92.5℃,夏季(环境温度为35℃)平均温度115.2℃,折算后冬夏季温度均超过《火力发电厂保温油漆设计规程》DL/T5072-2007中:锅炉正常运行条件下,环境温度不高于27℃时,设备和管道结构外表面温度不应超过50℃,环境温度高于27℃时,保温结构外表面温度可比环境温度高25℃的规定。
旋风分离器发展及工作原理

旋风分离器发展及工作原理摘要:综述了旋风分离器的发展概况,并从气体、粉尘运动的工作原理以及分类等方面介绍了。
一、旋风分离器的发展旋风分离器的应用已有近百年的历史,因其结构简单,造价低廉,没有活动部件,可用多种材料制造,操作条件范围宽广,分离效牢较高,所以至今仍是化工、采矿、冶金、机械、轻工等工业部门里最常用的一种除尘、分离设备。
随着工业发展的需要,为使旋风分离器达到高效低阻的目的,自1886年Morse的第一台圆锥形旋风分离器问世以来百余年里,由于分离器的结构、尺寸、流场特性的不同,出现了许多不同用途的旋风分离器,现从两个方面来进行概述。
1.气体、粉尘运动的研究旋风分离器内颗粒流体的流动属于稀浓度颗粒流体力学,故可先分析纯气体流场,再计及颗粒在其中的运动。
在1949年,TerLinden研究得出切向速度轴对称分布,在同一断面随其与轴心的距离减小而增大,达到最大值后又逐渐减小;径向速度在中心区方向朝外,在外围区方向朝内,形成源汇流;轴向速度在外部区域气流向下,在轴心区域气流向上;压力分布是壁面处大于中心处。
1962年,Lewellen把不可压缩流体的连续性方程和Navier-stokes方程在圆柱坐标系和轴对称定常流动下进行了简化,通过引入流函数和环量,得到了强旋转简化层流模型。
1975年Bloor、Ingham运用普朗特提出的混合长理论确定湍流表观粘度,并对水力旋流器流场进行了分析,建立了适合于工程应用的初级湍流模型。
1982年Boysan等人利用Rodi推得的关于雷诺应力的近似代数关系式,得到了高级湍流模型。
用这些模型计算得到的切向速度数值解与实验测定结果较吻合。
2.旋风分离器内气固流况的剖析通过对旋风分离器内气固流况的剖析,针对影响旋风分离器效率的顶部上涡流和下部的二次带尘,影响动力消耗的进口膨胀损失和出口旋转摩擦等因素,人们进行改进。
为了消除因上涡流而引起粉尘从出口管短路逃逸的现象,Cardiff 大学的Biffin等人研制的新型带集涡室的旋风分离器、德国西门子公司顶端带导向叶片的旋流分离器、日本专利多头切向进口的多管分离器,以及国内的倾斜螺旋形进口的CLT/A、CLG、DⅠ型等也都是为了削弱上涡流的带尘。
循环流化床锅炉燃烧改性高硫煤的污染物排放特性

循环流化床锅炉燃烧改性高硫煤的污染物排放特性摘要:随着煤炭资源开采的不断延长和开采年限的增加,晚下石炭统煤层逐步开采时,高硫煤将逐渐增多。
当上部煤被充分开采时,该矿只能生产高硫煤。
另一方面,高硫煤是我国部分地区的主要煤炭资源。
强制使用低硫煤的,必须从其他地方运来。
这不仅会浪费当地资源,还会造成能源消耗和交通污染。
显然,高硫煤是我国重要的能源资源。
如何高效、清洁利用高硫煤是关系到能源安全、环境保护和国民经济可持续发展的重大问题,也是洁净煤技术面临的技术挑战。
关键词:循环流化床锅炉燃烧改性高硫煤;污染物排放特性;前言:锅炉排气损失是锅炉运行中最重要的热损失,占锅炉热损失的60% - 70%。
目前,为了减少烟气的温度,减少烟气的热损失,提高电厂的经济,低温保温材料,来提高烟气余热利用的效率,火电行业得到了广泛的关注。
然而,对于高硫燃煤电厂,由于烟气腐蚀问题尚未得到解决,很少有项目采用烟气余热回收利用。
1 燃用高硫煤造成的危害1.1 对锅炉自身的危害锅炉燃烧时最常见的问题是高温加热器腐蚀、高温加热表面腐蚀、热源尾部氧化、污渍、设备和系统的消毒不能安全工作,锅炉的总体经济效率也在下降。
1.2 对环境的危害锅炉燃烧高硫煤燃烧和脱硫效率,不含硫化物烟气太高,而二氧化硫(SO2),进入大气层,溶于少量水蒸汽冷凝液滴入并不断与氧化剂反应进入云,导致pH降低,氧化失云、云的表面上。
酸雨的形成损害了农作物的生长,导致了作物和纪念碑的侵蚀。
在低温和潮湿的大气中,含硫酸和硫酸盐的气溶胶形成,这些气溶胶聚集在地下以污染烟雾,危害人类健康,特别是对呼吸系统造成严重损害。
二氧化硫、灰尘、氮氧化物和各种重金属颗粒聚集在云层和云层之间,污染混合大气,吸入肺部,刺激人类的气道,引起肺气肿、气管、哮喘等。
2 循环流化床锅炉燃烧改性高硫煤的污染物排放特性2.1 原料改良过的高硫化煤,由清洁煤炭研究生产。
它有复合的化学添加剂和高硫化煤炭,其中包括碱性和碱性金属,具有可在不同温度范围内抵抗污染的反应性,这与传统的混合方法不同,这与传统的混合方法不同。
130t/h循环流化床锅炉旋风分离器进口烟道制造工艺要点

尺 寸控 制 和焊接 变形 的预 防和控 制等进 行 了详细 的介绍 。
1 前 言 循环 流化 床锅炉 是采 用新 型燃烧 技术 的 锅 炉 ,该 技术 具有高 效 、低污染 、燃 料选用 性 强 、负荷调 节 比大等优 点 ,在我 国有广 泛 的市场 。而旋 风筒是 循环 流化 床锅炉 的关键
经验 ,对 影 响产 品质 量和进 度 等方 面的 问题
2 2 进 口烟 道制造 工艺要 点 .
进 口烟道 传统 的制造 方法 是 :按 图整 根 弯制 管子 ,然 后放 样定位 上 、下集箱 ,用 整 根 管子 连接上 、下 集箱 ,再全 部手工 装焊 管
子 间 的扁钢 。 由于大多 数管子 都包括 好 几个
也方便管子部分焊接和焊后变形 的校正。 ()所有 管 子间 的密封 件 采 用 数控 或 靠 4
l 天 ,工 效 为 原 来 的 两倍 。 同时 提 高 了 产 7
品质量 ,在 焊接变 形等 方面也 得到 了很 好 的 控制 。 该 工 艺 有 效 地 指 导 着 我 公 司 10/ 3 th
图 2 进 1烟 道 制 造 主 要 工 艺 流 程 : 7
元 片成排 弯制 成形 ,对样 校正后 单元 片 手工 拼装 成 整片 ;与集箱 连接 的弯 管部分 采用 弯 管机单 独 弯 制 后 再 与膜 式 壁 管 片 和 集 箱 对
接 。膜 式壁 自动焊 机设 备 的有 效利用 ,不 仅 大大减 少 了焊 接和装 配 的工作 量 ,而且 有 效
图 1 进 口烟道 尺寸 结构 简 图
2 1 进 口烟道 制造工 艺流程 .
维普资讯
余 热 锅 炉
2 0 . 061
进 口烟 道 制 造 主要 工 艺 流 程 如 图 2所
循环流化床锅炉旋风分离器内胆的改造

2 旋 风 分 离 器 的 .
循环 流化床 的分 离机构 是循 环流化 床锅炉 的关键 部件 之一 ,其 主要作用是将 大量的固体物料从气体 中分离 出来 ,
送 回燃 烧 室 , 以 维 持 燃 烧 室 的快 速 流 态 化 状 态 ,保 证 物 料 和 脱 硫 剂 多 次 循 环 、反 复燃 烧 和 反 应 。这 样 ,才 有 可 能 达
2 48 5.
备注
为此 ,对循环流化床锅炉旋风分离器内胆进行 了改造 。
一
、
锅 炉 简 述
1 窑街煤 电集 团公 司 电厂 的 四台上 述锅 炉 为单汽 包 、 . 自然循 环 、集 中下 降管 ,兀形布置 的燃煤 循环流化 床锅炉 ,
全 钢 构 架 。炉 膛 为 膜 式 水 冷 壁 悬 吊 的 封 闭 结 构 ,上 部 的 横
5 6
工质出 口温度 材 质
21 8. 9 2G 0
的 性 能 ,将 直 接 影 响 整 个 循 环 流 化 床 锅 炉 的 总 体 设 计 、系 统 布 置及 锅 炉 运 行 性 能 。
截面尺寸为 45 3 6 9 m。左右两个 高温 汽冷旋风筒位于 .1 mx . 3 9 炉膛 出 口和尾部 竖井烟道 之间 ,旋 风筒采 用膜式 汽冷管 结 构 ,管内 的流 动介质为 汽包 出来 的饱和蒸 汽 ,旋 风筒采 用 支撑结 构 。旋 风筒 出 口水平 烟道 ,尾部包 覆过热 器采用 悬
气 动 流动 。旋 风 分 离 器是 利 用 旋 转 的含 尘 气体所产 生的离 心力 ,
将 颗 粒 从 气 流 中 分 离
图 1 旋风分离器结 构示意 图
到理 想的燃烧效率 和脱硫效 率 。因此循环 流化床 分离机 构
循环流化床锅炉运行的五个调整
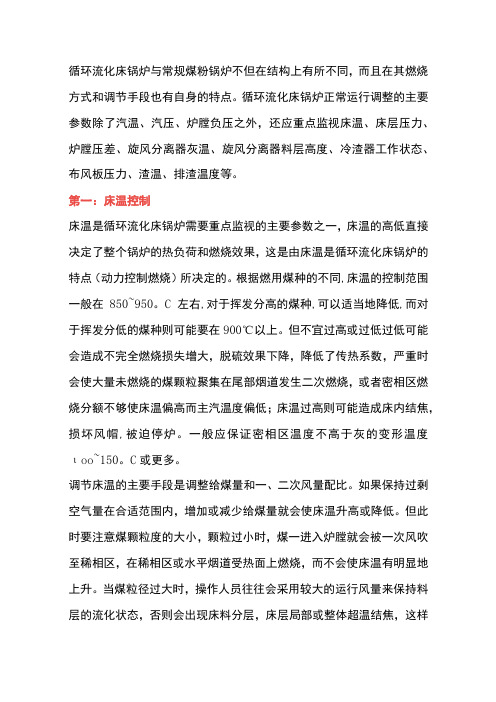
循环流化床锅炉与常规煤粉锅炉不但在结构上有所不同,而且在其燃烧方式和调节手段也有自身的特点。
循环流化床锅炉正常运行调整的主要参数除了汽温、汽压、炉膛负压之外,还应重点监视床温、床层压力、炉膛压差、旋风分离器灰温、旋风分离器料层高度、冷渣器工作状态、布风板压力、渣温、排渣温度等。
第一:床温控制床温是循环流化床锅炉需要重点监视的主要参数之一,床温的高低直接决定了整个锅炉的热负荷和燃烧效果,这是由床温是循环流化床锅炉的特点(动力控制燃烧)所决定的。
根据燃用煤种的不同,床温的控制范围一般在850~950。
C左右,对于挥发分高的煤种,可以适当地降低,而对于挥发分低的煤种则可能要在900℃以上。
但不宜过高或过低过低可能会造成不完全燃烧损失增大,脱硫效果下降,降低了传热系数,严重时会使大量未燃烧的煤颗粒聚集在尾部烟道发生二次燃烧,或者密相区燃烧分额不够使床温偏高而主汽温度偏低;床温过高则可能造成床内结焦,损坏风帽,被迫停炉。
一般应保证密相区温度不高于灰的变形温度ιoo~150。
C或更多。
调节床温的主要手段是调整给煤量和一、二次风量配比。
如果保持过剩空气量在合适范围内,增加或减少给煤量就会使床温升高或降低。
但此时要注意煤颗粒度的大小,颗粒过小时,煤一进入炉膛就会被一次风吹至稀相区,在稀相区或水平烟道受热面上燃烧,而不会使床温有明显地上升。
当煤粒径过大时,操作人员往往会采用较大的运行风量来保持料层的流化状态,否则会出现床料分层,床层局部或整体超温结焦,这样就会推迟燃烧时间,床温下降,炉膛上部温度在一段时间后升高。
当一次风量增大时,会把床层内的热量吹散至炉膛上部,而床层的温度反而会下降,反之床温会上升。
当然,一次风量一旦稳定下来,一般不要频繁调整,否则会破坏床层的流化状态,所以很多循环流化床锅炉都把一次风量小于某一值作为主燃料切除(MFT)动作的条件。
但在小范围内调节一次风量却仍是调整床温的有效手段。
二次风可以调节氧量,但不如在煤粉炉当中那么明显,有时增加二次风后就加强了对炉膛上部的扰动作用,会出现床温暂时下降的趋势,但过一段时间后因氧量的增加,床温总体上会呈现上升势头。
循环流化床锅炉低氮燃烧的技术改造实践
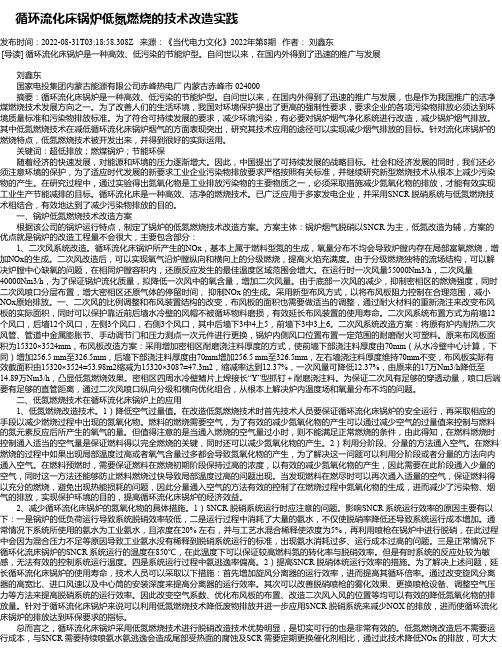
循环流化床锅炉低氮燃烧的技术改造实践发布时间:2022-08-31T03:18:58.308Z 来源:《当代电力文化》2022年第8期作者:刘鑫东[导读] 循环流化床锅炉是一种高效、低污染的节能炉型。
自问世以来,在国内外得到了迅速的推广与发展刘鑫东国家电投集团内蒙古能源有限公司赤峰热电厂内蒙古赤峰市 024000摘要:循环流化床锅炉是一种高效、低污染的节能炉型。
自问世以来,在国内外得到了迅速的推广与发展,也是作为我国推广的洁净煤燃烧技术发展方向之一。
为了改善人们的生活环境,我国对环境保护提出了更高的强制性要求,要求企业的各项污染物排放必须达到环境质量标准和污染物排放标准。
为了符合可持续发展的要求,减少环境污染,有必要对锅炉烟气净化系统进行改造,减少锅炉烟气排放。
其中低氮燃烧技术在减低循环流化床锅炉烟气的方面表现突出,研究其技术应用的途径可以实现减少烟气排放的目标。
针对流化床锅炉的燃烧特点,低氮燃烧技术被开发出来,并得到很好的实际运用。
关键词:超低排放;燃煤锅炉;节能环保随着经济的快速发展,对能源和环境的压力逐渐增大。
因此,中国提出了可持续发展的战略目标。
社会和经济发展的同时,我们还必须注意环境的保护,为了适应时代发展的新要求工业企业污染物排放要求严格按照有关标准,并继续研究新型燃烧技术从根本上减少污染物的产生。
在研究过程中,通过实验得出氮氧化物是工业排放污染物的主要物质之一,必须采取措施减少氮氧化物的排放,才能有效实现工业生产节能减排的目标。
循环流化床是一种高效、洁净的燃烧技术。
已广泛应用于多家发电企业,并采用SNCR 脱硝系统与低氮燃烧技术相结合,有效地达到了减少污染物排放的目的。
一、锅炉低氮燃烧技术改造方案根据该公司的锅炉运行特点,制定了锅炉的低氮燃烧技术改造方案。
方案主体:锅炉烟气脱硝以SNCR 为主,低氮改造为辅,方案的优点就是锅炉的改造工程量不会很大,主要包含部分:1、二次风系统改造。
- 1、下载文档前请自行甄别文档内容的完整性,平台不提供额外的编辑、内容补充、找答案等附加服务。
- 2、"仅部分预览"的文档,不可在线预览部分如存在完整性等问题,可反馈申请退款(可完整预览的文档不适用该条件!)。
- 3、如文档侵犯您的权益,请联系客服反馈,我们会尽快为您处理(人工客服工作时间:9:00-18:30)。
循环流化床燃烧技术一、概念循环流化床(CFB)燃烧技术是一项近二十年发展起来的清洁煤燃烧技术。
它具有燃料适应性广、燃烧效率高、氮氧化物排放低、低成本石灰石炉内脱硫、负荷调节比大和负荷调节快等突出优点。
自循环流化床燃烧技术出现以来,循环床锅炉在世界范围内得到广泛的应用,大容量的循环床锅炉已被发电行业所接受。
循环流化床低成本实现了严格的污染排放指标,同时燃用劣质燃料,在负荷适应性和灰渣综合利用等方面具有综合优势,为煤粉炉的节能环保改造提供了一条有效的途径。
二、循环流化床燃烧技术发展历史回顾主循环回路是循环流化床锅炉的关键,其主要作用是将大量的高温固体物料从气流中分离出来,送回燃烧室,以维持燃烧室稳定的流态化状态,保证燃料和脱硫剂多次循环、反复燃烧和反应,以提高燃烧效率和脱硫效率。
分离器是主循环回路的关键部件,其作用是完成含尘气流的气固分离,并把收集下来的物料回送至炉膛,实现灰平衡及热平衡,保证炉内燃烧的稳定与高效。
从某种意义上讲,CFB锅炉的性能取决于分离器的性能,所以循环床技术的分离器研制经历了三代发展,而分离器设计上的差异标志了CFB燃烧技术的发展历程。
●(一)绝热旋风筒分离器德国Lurgi公司较早地开发出了采用保温、耐火及防磨材料砌装成筒身的高温绝热式旋风分离器的CFB锅炉[1]。
分离器入口烟温在850℃左右。
应用绝热旋风筒作为分离器的循环流化床锅炉称为第一代循环流化床锅炉,目前已经商业化。
Lurgi公司、Ahlstrom公司、以及由其技术转移的Stein、ABB-CE、AEE、EVT等设计制造的循环流化床锅炉均采用了此种形式。
这种分离器具有相当好的分离性能,使用这种分离器的循环流化床锅炉具有较高的性能。
但这种分离器也存在一些问题,主要是旋风筒体积庞大,因而钢耗较高,锅炉造价高,占地较大,旋风筒内衬厚、耐火材料及砌筑要求高、用量大、费用高启动时间长、运行中易出现故障;密封和膨胀系统复杂;尤其是在燃用挥发份较低或活性较差的强后燃性煤种时,旋风筒内的燃烧导致分离下的物料温度上升,引起旋风筒内或回料腿回料阀内的超温。
这些问题在我国实际生产条件下显得更突出。
Circofluid的中温分离技术在一定程度上缓解了高温旋风筒的问题,炉膛上部布置较多数量的受热面,降低了旋风筒入口烟气温度和体积,旋风筒的体积和重量有所减小,因此相当程度上克服了绝热旋风筒技术的缺陷,使其运行可靠性提高,但炉膛上部布置有过热器和高温省煤器等,需要采用塔式布置,炉膛较高,钢耗量大,锅炉造价提高。
同时,它的CO排放及检修问题在一定程度上限制了该技术的发展。
●(二)水(汽)冷旋风筒分离器为保持绝热旋风筒循环流化床锅炉的优点,同时有效地克服该炉型的缺陷,Foster Wheeler公司设计出了堪称典范的水(汽)冷旋风分离器。
应用水(汽)冷分离器的循环流化床锅炉被称为第二代循环流化床锅炉。
该分离器外壳由水冷或汽冷管弯制、焊装而成,取消绝热旋风筒的高温绝热层,代之以受热面制成的曲面及其内侧布满销钉涂一层较薄厚度的高温耐磨浇注料,壳外侧覆以一定厚度的保温层。
水(汽)冷旋风筒可吸收一部分热量,分离器内物料温度不会上升,甚至略有下降,同时较好地解决了旋风筒内侧防磨问题。
该公司投运的循环流化床锅炉从未发生回料系统结焦的问题,也未发生旋风筒内磨损问题,充分显示了其优越性。
这样,高温绝热型旋风分离循环床的优点得以继续发挥,缺点则基本被克服。
当然,任何一种设计都难以尽善尽美,FW式水(汽)冷旋风分离器的问题是制造工艺及生产成本,这使其商业竞争力下降,通用性和推广价值受到了限制。
同时该分离器的结构形式与高温绝热旋风筒并无本质差异,因此锅炉结构仍未恢复到传统锅炉完美的形式。
为了各部件的热膨胀而设置的大型膨胀节成为该炉型最薄弱的环节,损坏事故频繁发生(见第15届FBC国际会议Operator Section)。
因此调整分离器的形状,进一步提高紧凑性和可靠性问题成为循环流化床燃烧技术发展的关键。
●(三)方型水冷分离器为克服汽冷旋风筒锅炉的结构问题及制造成本高的问题,芬兰Ahlstrom公司创造性地提出了Pyroflow Compact设计构想。
Pyroflow Compact循环床锅炉采用其独特专利技术的方型分离器,分离器的分离机理与圆形旋风筒本质上无差别,壳体仍采用FW式水(汽)冷管壁式,但因筒体为平面结构而别具一格。
这就是第三代循环流化床锅炉。
它与常规循环流化床锅炉的最大区别是采用了方型的气固分离装置,分离器的壁面作为炉膛壁面水循环系统的一部分,因此与炉膛之间免除热膨胀节。
同时方型分离器可紧贴炉膛布置从而使整个循环床锅炉的体积大为减少,布置显得十分紧凑。
借鉴汽冷旋风筒成功的防磨经验,方型分离器水冷表面敷设了一层薄的耐火层,分离器成为受热面的一部分,为锅炉快速启停提供了条件。
三、方型分离器循环床技术url]芬兰Ahlstrom公司的方型分离器紧凑型设计推出之后,立即引起了广泛的重视。
但人们对该技术一直持观望态度。
但经过多台锅炉5年的运行实践,已经为人们所接受,其标志为1999年5月第15届国际流化床燃烧会议上该专利持有人Timo荣获唯一的ASME最高贡献奖。
Foster Wheeler公司和Ahlstrom 公司合并后即将方型分离器循环流化床锅炉作为大型化方向予以重点发展。
采用方型分离器的紧凑型布置循环床锅炉的市场份额逐年增加。
目前各循环流化床锅炉制造厂家和研究机构都十分重视循环流化床锅炉的大型化,方型分离器在大型化方面具有很大的优势。
1993年清华大学在实验室对国外方型分离器专利进行了验证实验,并改进了入口段设计,实验表明这个改进是完全正确的,这个改进最终取得了中国专利—“水冷异型分离器”。
为进一步优化分离器的效果和验证改进可靠性,在实验室冷态实验、热态实验的基础上应用于75t/h完善化循环流化床锅炉,并取得成功。
该分离器是四周用膜式水冷壁组成的方型分离器,烟气入口加速段由水冷壁管弯制成圆弧形。
该设计低成本有效地克服了绝热旋风筒的后燃结焦问题和圆形汽(水)冷旋风筒的结构问题,被认为达到九十年代国际先进水平。
对几种不同当量尺寸的方型分离器进行了一些卓有成效的试验和较为深入的研究,取得了许多有价值的结果。
对这些成果进行较全面的分析、整理和比较表明,方型分离器的放大性能要优于圆形旋风分离器,至少绝不逊于后者,特征尺寸在10m以内的方型分离器大型化的前景相当乐观。
清华大学在该方面的研究成果以及220t/h、410t/h采用方型分离器的循环流化床锅炉设计得到国际同行的充分肯定和高度评价,在15届FBC国际会议上被评为最佳论文。
四、循环流化床锅炉的效率循环流化床燃烧技术具有以下特点:气固混合很好;燃烧速率高,特别是对粗颗粒燃料;绝大部分未燃烬的燃料被再循环至炉膛,因而其燃烧效率可与煤粉炉相媲美,通常达到97.5%~99.5%。
根据统计资料,循环流化床燃烧效率受煤种影响较大。
对较为年轻的褐煤、泥煤,燃烧效率可达到98%以上;而对于变质程度较高的无烟煤到烟煤,飞灰含碳量往往高达10%以上。
一般来讲,各种形式的旋风筒对100μm以下的细颗粒分离效率不可能很高,因此旋风筒对细颗粒燃尽是无能为力的,应当采取飞灰回送等措施解决难燃煤种燃烬问题,而这是目前国际上比较成熟的技术。
关于提高循环流化床锅炉效率的问题,目前比较一致的看法是提高参数。
据分析,超临界循环流化床锅炉电厂的效率可达43%~44%。
根据法国Stein Industrie公司对超临界参数Lurgi循环流化床锅炉的研究,由于Lurgi型循环流化床锅炉有外置换热器,而外置换热器的工作温度在700°C左右,使用清洁空气流化,在外置换热器内布置高温换热器可防止高温腐蚀,因而采用超临界参数比煤粉炉更为有利。
采用超临界参数可使发电效率提高约6%。
五、煤粉炉改造为循环流化床锅炉的方案煤粉炉改造为循环流化床锅炉是一项复杂的工作,因为不同煤粉炉的型号规格不同,同一型式的锅炉运行时间不同,受热面的寿命也不一定相同,这样改造方法和难易程度就有可能不同。
目前国内技术用于410t/h及以下煤粉炉的改造是有把握的。
●(一)410t/h煤粉炉简介单锅筒自然循环高压煤粉炉,膜式壁双框架,半露天布置;燃料室为正方形,煤粉燃烧器四角布置,燃烧室上部布置有后屏过热器,水平烟道依次布置二级过热器和一级过热器。
尾部竖井为轻型护板炉墙,分别布置高温省煤器、高温空气预热器、低温省煤器和低温空预器。
●(二)改造方案研究考虑各部分承压受热面在改造中利用的可能性。
现有钢架以及基础不变动,原场地布置已经比较紧凑,改造不增加占地面积。
对流管束烟气速度应保证长期稳定运行的可靠性。
改造后的出力不变。
考虑到上述要求,在原有钢结构范围内进行改造。
由于场地的限制,采用单炉膛、四个方型分离器前后布置、过顶烟道的总体方案。
采用单炉筒自然循环,自前向后依次布置前分离器、燃烧室及过顶烟道、后分离器、尾部竖井。
膜式壁采用悬吊结构,省煤器及空气预热器采用支撑结构。
在原有钢架范围内重新布置各部分受热面。
燃烧室为膜式壁,净高度30951mm,截面积维持原形状结构,为利用原水冷壁创造条件。
燃烧室前后均布置两个当量直径为4990mm的水冷异型分离器,前分离器出口烟气流经过顶烟道与后分离器出口烟气汇合进入转向室和尾部竖井。
燃烧室标高21.000m以上由水冷屏将燃烧室前后方向分为两部分,通过前后分离器阻力设计不同以及水冷屏的分隔作用解决前后分离器烟气平衡问题。
垂直于水冷屏方向布置了过热屏,过热屏穿越过顶烟道。
燃烧室侧水冷壁、分离器侧水冷壁、前分离器的后水冷壁向上延伸组成侧墙,和顶部汽冷包墙以及分离器顶棚、燃烧室顶棚构成过顶烟道。
尾部竖井自上向下依次布置末级过热器,一级过热器、省煤器、一次风空气预热器热段、二次风空气预热器、一次风空气预热器冷段。
其中末级过热器和初级过热器位于汽冷包墙内。
包墙的前墙一部分在转向室进口穿越烟道形成吊挂管,另一部分向前形成水平烟道的下包墙,在后分离器处向上吊挂。
省煤器、空预器均为护板炉墙。
尾部对流受热面均为前后方的出管,末级过热器为f 42´ 5的五管圈两管组构成;初级过热器为f 38´ 5的双管圈、三管组。
省煤器为f 32´ 4,双管圈三管组;空气预热器采用水平卧式,以有效解决漏风问题。
对流受热面的改造均可由原受热面改造形成。
全部高温受热面区域均采用膜式壁炉墙,避免使用膨胀节,以解决密封问题,采用固定膨胀中心。
Z1至Z3柱钢架不变,Z4、Z5需增加高度至50850mm与原Z1平齐。
经核算,钢架改造后基础仍然是安全的。
为充分节约启动用油,采用水冷布风板,床下点火。