汽车模块化设计的应用与发展
汽车底盘的模块化设计技术思考与应用

汽车底盘的模块化设计技术思考与应用摘要:在时代不断进步与科技技术的快速提升,各个领域迎来更高的发展机遇。
汽车制造业也开始朝着多元化和多功能化发展,传统的汽车设计技术已经无法满足当前时代发展的需求,以往的设计技术也需要进行更深层次的进化与变革,只有这样才能够使得汽车行业在当前制造业激化的竞争过程中真正的站稳脚步。
基于此,本文主要针对汽车底盘使用模块化设计的相关方法进行总结,同时对于汽车底盘产品设计给予相关的研究与分析,使其能够推进我们国家汽车制造业保持持续健康稳定的发展,令我国模块化设计技术能够在汽车制造业里的运用和发展提供有效的借鉴与发展。
关键词:汽车底盘;模块化设计;技术研究引言模块化设计技术的出现和应用对制造行业有着重要的意义,既能帮助产品进行重新的设计和发展,还能通过对产品架构和系统的升级促进产品的更新发展。
近年来,在信息技术的存进和带动下,模块化设计技术和理念在汽车行业的应用愈加广泛,对汽车行业的发展起着至关重要的作用。
1汽车底盘模块化设计技术研究与应用的背景及意义汽车底盘产品的研究设计一直都是一个复杂且庞大的工程,也是汽车制造业中的一大难题;整个底盘包含的零部件多,加上用在其上的技术也繁多且密集,使得整个底盘产品结构和布局十分冗杂,且安装以及技术要求又很严格,设计难度大。
要做到有效减小开发设计的难度,缩短设计周期和研发成本,需要对汽车底盘产品利用模块化设计,将其复杂的结构和功能分成多个相对独立功能模块及具有差异化的系统部件模块库,这样相对于直接对结构繁杂、功能交叉的底盘系统进行设计,开发难度低很多。
在对汽车底盘产品进行模块划分之后,直接利用产品组合的方式,就可以得到新的模块,这样,整个模块组成了一个通用平台,不但减小了底盘产品大大小小零部件的开发,企业生产效率得以提高;通过模块接口的标准化技术,将同种功能模块按照性能差异化方式建立成熟的产品模块库,快速优选相适应的指定模块,就可以快速构建有差异化性能特性的新底盘模块系统。
汽车底盘的模块化设计技术研究与应用

汽车底盘的模块化设计技术研究与应用发布时间:2022-01-20T08:07:41.321Z 来源:《中国科技人才》2021年第30期作者:刘新新[导读] 目前,常见的汽车底盘设计方法有模块化设计方法,对此本文为了了解该方法的有效性,将进行相关的研究工作,研究当中,将介绍底盘功能模块、底盘模块编码与数据管理等,最终结合实例分析其具体应用。
另外,在汽车底盘模块化设计当中,还提倡五化概念,即系统平台化、零部件通用化、标准化、架构化、模块化,此概念可以保障设计有计划、有方向的开展。
刘新新山东交通技师学院山东省临沂市 276000摘要:目前,常见的汽车底盘设计方法有模块化设计方法,对此本文为了了解该方法的有效性,将进行相关的研究工作,研究当中,将介绍底盘功能模块、底盘模块编码与数据管理等,最终结合实例分析其具体应用。
另外,在汽车底盘模块化设计当中,还提倡五化概念,即系统平台化、零部件通用化、标准化、架构化、模块化,此概念可以保障设计有计划、有方向的开展。
关键词:汽车底盘;模块化设计;研究与应用模块化设计技术的出现和应用对制造行业有着重要的意义,既能帮助产品进行重新的设计和发展,还能通过对产品架构和系统的升级促进产品的更新发展。
近年来,在信息技术的存进和带动下,模块化设计技术和理念在汽车行业的应用愈加广泛,对汽车行业的发展起着至关重要的作用。
1. 汽车底盘模块化设计技术研究与应用的重要性在科技生产力不断提升的今天,汽车设计生产行业需要不断地加大对设计生产技术的研发,才能够使生产技术适应不断提升的客户需求和市场环境,实现长效的发展,对汽车底盘模块化设计技术进行研究和有效的应用对整个汽车行业都有着积极的意义。
1.1降低底盘部件开发的难度底盘设计与开发是规模巨大的工程,由于底盘产品的在结构上上复杂性、在部件上的繁多性以及在技术上的密集性特点,使得底盘设计开发工作的难度很大。
利用模块化设计技术进行底盘开发能够讲底盘设计划分为细小的不同模块,对设计研究的难度进行分解,进而对设计难度进行有效的降低,促进底盘产品的开发设计。
汽车模块化的发展

目标 相 一 致 , E 必 须 以在 线 安 装 的 车 身 板 为 基 FM
准 。 管 是否 选 择 安 装仪 表板 , 不 模块 必须 与 许 多 支撑
面和 紧 固区 融 为 一体 , 样才 能顾 及 到 前 照 灯 和 保 这
险杠 的精 密 几何 定 位 。 F M 的 目 的是 支 承 汽 车 前 部 的 所 有 零 件 以及 E 应 付 发动 机前 端 零 件 的多 样 化 。 这 些零 件 中 , 两 在 有 个 对 未来 模块 的 定 义极 其 重要 : 却 系统 和 前 照灯 。 冷
维普资讯
2 2
技 术纵 横
轻 型汽 车 技 术 2 0 ( ) 1 3 0 2 5 总 5
汽 车 模 块 化 的 发 展
■ 李虹 玉 编译
来 自 P a t Omnu lsi c im Au o xeiu 和 t E tr r e 念 有 一定 的 约速 性 。在 保 险 杠表 面 开 口就 允许 从纵 梁 的端 部接 近 模块 装 配 。 不管 怎样 , 使 预装 在 模块 这 上 的 仪表 板 、 格 栅 和 前 照 灯 之 间 的 间 隙 和嵌 平 会 前 处理 得 更 好 。图 1 示 有 不带 仪 表 板 的 F M 。 显 E F M 在 汽 车 上 的定 位非 常 重 要 。例 如 , 必须 E 它 补偿 白车身 的 所有 几 何 变 化 以确 保 前 照灯 和 翼子 板 之 间的 良好 衔接 和 间隙 。为 了保 证换 算 公 差 与造 型
冷 却 系统 有 两种 可 行 的安 装 方 法 。冷却 系 统可 以在 预加 工 线 上 和 发 动 机 装配 到 一 起 ; 却 线 路 中 冷 充 满 乙二 醇 , 用来 检 测 渗漏 , 后 再 装 到车 上 。可供 然 选择 的另一 种做 法 是 把 发 动机 装 上 汽 车之 后再 配 冷 却 系统 ; 装配 中加 注 和检 测 。 在
汽车前端模块总成模块化设计及应用
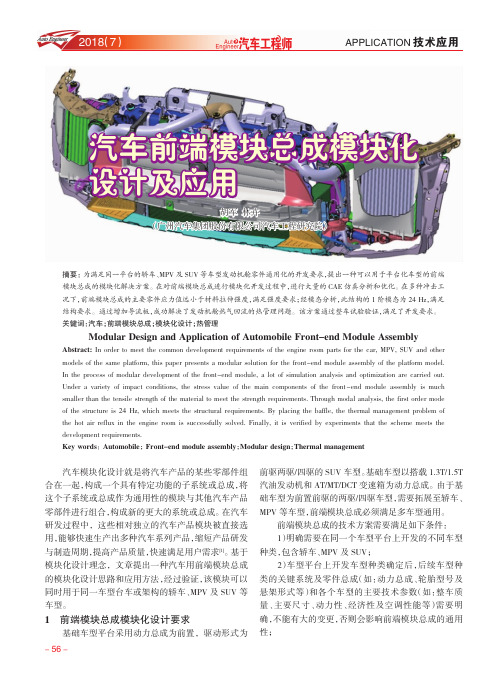
中冷器、散热器及风扇分总成、前端模块骨架总成等主
要零部件组成。其中,冷凝器通过螺栓固定至中冷器, 中冷器与散热器通过螺栓固定,散热器通过软垫固定
图 前端模块总成应力分布
在前端模块骨架总成上。前端模块总成主要部件及发 动机舱总布置简图,如图 1所示。
2018(7)
20技18术年应7用月
汽车前端模块总成模块化 设计及应用
胡军 林卉 (广州汽车集团股份有限公司汽车工程研究院)
摘要:为满足同一平台的轿车、"#$ 及 %&$ 等车型发动机舱零件通用化的开发要求,提出一种可以用于平台化车型的前端 模块总成的模块化解决方案。在对前端模块总成进行模块化开发过程中,进行大量的 '() 仿真分析和优化。在多种冲击工 况下,前端模块总成的主要零件应力值远小于材料拉伸强度,满足强度要求;经模态分析,此结构的 * 阶模态为 +, -.,满足
模块化设计理念,文章提出一种汽车用前端模块总成
2)车型平台上开发车型种类确定后,后续车型种
的模块化设计思路和应用方法,经过验证,该模块可以 类的关键系统及零件总成(如:动力总成、轮胎型号及
同时用于同一车型台车或架构的轿车、MPV及 SUV等 悬架形式等)和各个车型的主要技术参数(如:整车质
车型。
! 前端模块总成模块化设计要求
零部件进行组合,构成新的更大的系统或总成。在汽车 MPV等车型,前端模块总成必须满足多车型通用。
研发过程中,这些相对独立的汽车产品模块被直接选
前端模块总成的技术方案需要满足如下条件:
用,能够快速生产出多种汽车系列产品,缩短产品研发
1)明确需要在同一个车型平台上开发的不同车型
[1]
与制造周期,提高产品质量,快速满足用户需求 。基于 种类,包含轿车、MPV及 SUV;
汽车机械制造的模块化设计与制造
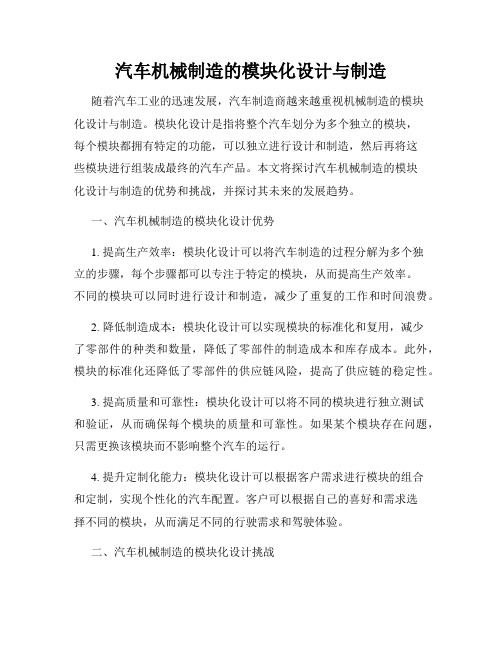
汽车机械制造的模块化设计与制造随着汽车工业的迅速发展,汽车制造商越来越重视机械制造的模块化设计与制造。
模块化设计是指将整个汽车划分为多个独立的模块,每个模块都拥有特定的功能,可以独立进行设计和制造,然后再将这些模块进行组装成最终的汽车产品。
本文将探讨汽车机械制造的模块化设计与制造的优势和挑战,并探讨其未来的发展趋势。
一、汽车机械制造的模块化设计优势1. 提高生产效率:模块化设计可以将汽车制造的过程分解为多个独立的步骤,每个步骤都可以专注于特定的模块,从而提高生产效率。
不同的模块可以同时进行设计和制造,减少了重复的工作和时间浪费。
2. 降低制造成本:模块化设计可以实现模块的标准化和复用,减少了零部件的种类和数量,降低了零部件的制造成本和库存成本。
此外,模块的标准化还降低了零部件的供应链风险,提高了供应链的稳定性。
3. 提高质量和可靠性:模块化设计可以将不同的模块进行独立测试和验证,从而确保每个模块的质量和可靠性。
如果某个模块存在问题,只需更换该模块而不影响整个汽车的运行。
4. 提升定制化能力:模块化设计可以根据客户需求进行模块的组合和定制,实现个性化的汽车配置。
客户可以根据自己的喜好和需求选择不同的模块,从而满足不同的行驶需求和驾驶体验。
二、汽车机械制造的模块化设计挑战1. 模块接口设计:模块化设计需要考虑不同模块之间的接口设计和标准化,确保模块之间的互换性和兼容性。
接口设计需要充分考虑模块的功能和性能要求,避免因接口不匹配而导致的问题。
2. 制造流程优化:模块化设计需要重新优化制造流程,确保各个模块的设计、制造和组装之间的协调和顺畅。
制造流程的优化需要考虑模块的制造工艺、设备和人员配备等因素。
3. 质量控制和测试:模块化设计需要建立完善的质量控制和测试体系,确保每个模块的质量和可靠性。
质量控制和测试需要考虑不同模块的测试要求和方法,确保问题能够及时发现和解决。
4. 供应链管理:模块化设计需要建立高效的供应链管理系统,确保零部件的供应和交付能够满足生产计划和需求。
通用化、系列化、模块化在汽车领域的应用

通用化、系列化、模块化在汽车领域的应用作者:董伟佳李增奎郭正月王威来源:《中国科技博览》2013年第29期摘要:本文通过介绍汽车领域内“三化”的定义及其实现的基本思路,通过对世界级先进OEM的“三化”实现案例的分析,使工程设计人员了解标准化设计的方法,从而实现降低开发成本、缩短开发周期,增强产品企业竞争力的目的。
关键词:汽车通用化系列化模块化标准化中图分类号:TG333.7 文献标识码:A 文章编号:1009-914X(2013)29-426-02汽车产业是一项高投入、技术密集的行业。
在原材料上涨、售价却不断下降的同时,顾客需求却日益成熟和苛刻,如何才能在激烈的市场竞争中胜出,成为每一个OEM厂面临的问题。
经过对世界级先进OEM厂产品的研究,证明提升产品竞争力的主要手段和重要途径是开展产品的“三化”工作,其目的就是将产品设计成一个继承性与创新性有机结合的统一体。
确保以较少的投资、较短的时间和较少的人力投入下,研制出高水平、高质量的产品。
产品的“通用化、系列化、模块化”程度是评价产品设计水平高低的重要标准,直接影响到开发周期、产品质量、生产成本、售后服务等各方面。
本文阐述了产品“三化”的基本定义,并结合先进公司的实例初步阐述实现产品“三化”的思路与方法。
1.汽车领域“三化”的基本定义通用化是指一个单元不加任何改变或修饰就能任意替换另一单元,满足同一产品内或不同产品间大体相同的设计需求。
系列化是通过对同一类产品的需求范围的全面分析和研究,将产品的功能配置、性能参数进行合理的规划,并对其型式和结构进行一定的规定和统一,进而机动灵活的满足不同设计需求。
模块化是对产品进行功能分析和分解,划分并设计出一系列通用模块或标准模块,从中选用并补充新设计的专用模块和零部件一起进行组合,以有限种类的模块组合成大量的、满足各种需求的产品。
总的来说,模块化以通用化、系列化为基础,是一种高级的标准化表现形式。
2.“三化”在汽车领域的应用2.1通用化在汽车领域的应用通用化能最大限度的实现产品内和产品间相同的结构要素和零部件的继承,把已有产品中的先进结构和技术成果继承到产品中不同的部分或新产品上。
探讨新能源汽车系统的模块化设计思路
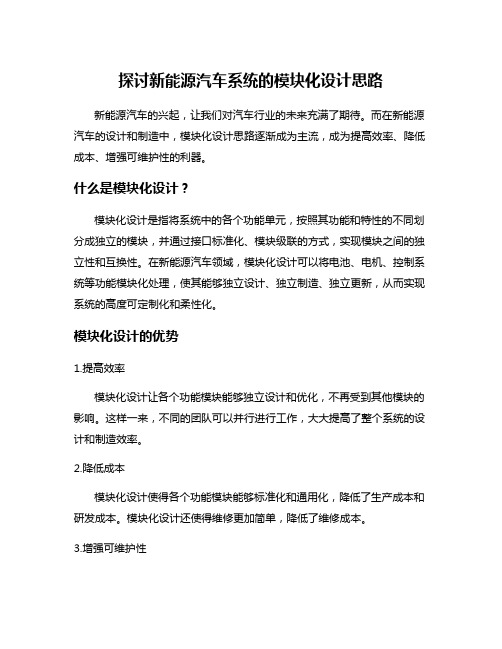
探讨新能源汽车系统的模块化设计思路新能源汽车的兴起,让我们对汽车行业的未来充满了期待。
而在新能源汽车的设计和制造中,模块化设计思路逐渐成为主流,成为提高效率、降低成本、增强可维护性的利器。
什么是模块化设计?模块化设计是指将系统中的各个功能单元,按照其功能和特性的不同划分成独立的模块,并通过接口标准化、模块级联的方式,实现模块之间的独立性和互换性。
在新能源汽车领域,模块化设计可以将电池、电机、控制系统等功能模块化处理,使其能够独立设计、独立制造、独立更新,从而实现系统的高度可定制化和柔性化。
模块化设计的优势1.提高效率模块化设计让各个功能模块能够独立设计和优化,不再受到其他模块的影响。
这样一来,不同的团队可以并行进行工作,大大提高了整个系统的设计和制造效率。
2.降低成本模块化设计使得各个功能模块能够标准化和通用化,降低了生产成本和研发成本。
模块化设计还使得维修更加简单,降低了维修成本。
3.增强可维护性采用模块化设计,如果某个模块出现故障,可以直接更换这个模块,而不需要对整个系统进行大规模的维修。
这样不仅节省了维修时间,也降低了维修难度。
模块化设计在新能源汽车系统中的运用1.电池模块化在新能源汽车中,电池是关键的能源存储单元。
采用电池模块化设计,可以根据需要增减电池模块的数量,实现电池容量的灵活配置,满足不同用户的需求。
2.电机模块化电机作为驱动动力的核心部件,通过电机模块化设计,可以实现电机的更换和升级变得更加简单快捷,同时也方便对电机进行维护和保养。
3.控制系统模块化控制系统是新能源汽车的大脑,控制车辆各个部件的运行和协调。
将控制系统进行模块化设计,可以实现各个功能模块的独立更新,以适应汽车系统的需求变化。
模块化设计为新能源汽车系统的设计和制造提供了全新思路和解决方案。
通过将各个功能模块进行独立设计和优化,新能源汽车可以实现更高效率、更低成本、更强可维护性的优势。
未来,随着模块化设计理念的不断发展和完善,新能源汽车系统将迎来更加灿烂的发展前景。
汽车零部件模块化设计及应用研究

汽车零部件模块化设计及应用研究一、引言随着汽车产业的不断发展,市场竞争日益加剧,车企们需要不断推陈出新,提高汽车的品质和性能。
其中,汽车零部件的设计和改进起到了非常重要的作用,而模块化设计是当前研究的热点之一。
本文将探讨汽车零部件模块化设计的概念、应用以及优势等问题。
二、汽车零部件模块化设计的概念1、什么是模块化设计?模块化设计是指利用已有作为单元的零部件,采用相互连接的方式,形成新的装配式零部件的设计方法。
而模块化设计将相关元件组合在一起,形成一个独立的模块单元,进而用于不同的产品。
2、汽车零部件模块化设计的概念汽车零部件模块化设计是基于标准化的零部件硬件和软件的模块化设计。
其目标是实现不同厂家之间的共享或可互换的零部件,从而加快产品开发速度,降低成本,提高汽车品质。
三、模块化设计的应用1、加速新产品的研发和生产汽车零部件模块化设计可以加速新产品的应用开发与生产。
当新产品需要使用已有的零部件时,利用现有的模块化部件,会降低开发成本、产品开发时间和工程成本,从而加速新产品的开发。
2、降低成本由于模块化设计可以实现不同模块之间的互换性,使得厂家可以在产品生产过程中降低成本。
此外,模块化设计还可以提高生产自动化率,进一步减少成本。
3、提高汽车品质汽车模块化设计可以提高汽车部件的精度和质量控制,从而最终提高汽车整体质量水平。
此外,模块化的部件维修、更换也更加方便,可以减少整体维修成本和劳动力成本。
四、模块化设计的优势1、重复使用模块零部件可以在不同车型中重复使用,节省了生产成本,并减少了生产时间。
2、高度标准化采用模块化设计,可以将零部件变为高度标准化的零部件,从而提高了零部件生产的效率和质量。
3、自动组建通过模块化的设计,零部件可在很短的时间内自动组合成汽车整体装配,这意味着生产速度更快,制造成本大大降低。
4、高度定制化模块化的设计可以根据不同需求灵活地组合零部件成新的装置,从而降低了生产成本。
五、结论随着信息技术和自动化技术的进步,汽车零部件之间的互换性和可重复使用性将成为未来汽车零部件开发的新趋势。
- 1、下载文档前请自行甄别文档内容的完整性,平台不提供额外的编辑、内容补充、找答案等附加服务。
- 2、"仅部分预览"的文档,不可在线预览部分如存在完整性等问题,可反馈申请退款(可完整预览的文档不适用该条件!)。
- 3、如文档侵犯您的权益,请联系客服反馈,我们会尽快为您处理(人工客服工作时间:9:00-18:30)。
3 装配设计原则与非模块化设计的 缺点
3.1装配设计原则 装配设计DFA(DesigII For As8embly)是模块
化设计思想提出的理论基础之一。爱因斯坦曾说 过:“最好的设计是最简单易行的”。装配设计的 原则就指出:第一要把零件数减少到最少;第二要 考虑零件装卸的简易性;第三要考虑最优的联接 方式等。装配设计认为装配总成本是零件数、装 配简易性及再定位数目的函数,如果能够降低装 配的零件数,装配总成本相应会下降。模块化设 计思想很好地体现了装配设计原则。在总装配 时,没有数量众多的单件,它们都事先装配好在各 个模块中,模块之间联接设计简易可靠,装配简单 方便,成本大大下降。 3.2非模块化设计的缺点
厢式货车作为耗油大户,其节能与否已直接影响到我国整体的能源消耗水平,国家对此高度重视。由于汽车轻量化对节能增效的巨大意义,国际各 大汽车生产商都在尽可能的情况下减轻车身质量。汽车的轻量化设计技术已经成为目前汽车研究领域的研究热点之一。
由于货车的使用条件十分恶劣,受力状况非常复杂。骨架应有足够的弯曲刚度,以使装在其上的有关机构之间的相对位置在汽车行驶过程中保持不 变并使车身的变形最小;骨架也应有足够的强度,以保证其有足够的可靠性与寿命。骨架刚度不足会引起振动和噪声,也使得汽车的乘坐舒适性、操作 稳定性及某些机件的可靠性下降。因此,如何设计出满足使用要求的轻量化骨架成了一项具有挑战性的工作。
汽车模块化设计的应用与发展
邱国华 (泛亚汽车技术中心有限公司)
【摘要】 文章论述了模块化设计的概念和优点,介绍了模块化设计在当今国内汽车开发中的应用,以及
模块化设计在国外的新发展。
【主题词】 汽车设计模块发展
1 引言
市场用户的需求变化促使汽车制造商不断地 设计开发新车型。但传统的汽车设计思想是基于 单一车型有大规模产量基础上的,无法满足市场 日益变化的不同需求。因此,要求汽车设计理念 和汽车设计方法不断更新和发展。本文介绍先进 的模块化设计思想在国产车型中的初步应用,结 合装配设计原则讨论模块化设计的优点,并论述 了模块化设计在国外的新发展。
戴姆勒一克莱斯勒提出的一种分块的方法是 将整车分成4个模块:前端模块、乘客单元、车顶 模块和后端模块(见图4)。每个模块分别单独制 造,包括所有的附加于模块上的零部件,仅仅在生 产的最后阶段,才将这些模块按设定的接口快速 地结合在一起。这种全新的制造方式,最大的好 处是在一个车型范围内可以有很多的变形车,极 大地降低成本。据戴姆勒一克莱斯勒的粗略估 算,将会降低多达30%的研发、制造、物流等综合 成本。各大模块可以在整车厂生产,也可以由供 应商提供,当最终将在整车厂装配在一起。
本文所要研究的内容是如何开发一个三层架构的计算机辅助系统,简化工程师的工作,将他们和复杂的虚拟模拟程序隔离开,让他们能够使用一个 相对简单的用户界面提供所需要的输入数据,服务端将负责管理这些提交到服务器的任务,调用相应的虚拟模拟模块进行计算,然后将计算得到的结果 ,例如文本文件,图表,数据表单等发送到相应用户在服务器的存储位置,用户可以利用该系统下载到相应的文件帮助自己完成测试和研发的工作而不 需要关心后台的实现。而使用虚拟模拟软件进行模块开发的工程师也可以随时修改替换原有的模块,调整用户的输入等,所有的修改都是与用户无关的 。这样开发者和使用者都可以统一的利用这个计算机辅助系统进行他们自己相应的工作,而将一些如任务分配,远程调用,文件传输等复杂的细节交给 计算机辅助系统来处理。这就大大的提高了工作的效率,同时也解决了虚拟模拟在公司内推广使用最大的障碍。本文首先阐述了系统的架构结构,然后 结合在公司中应用中出现的问题,分数据库,前端界面和服务器设计三个部分详细阐述如何在系统开发中解决这些问题。本系统可以应用于各种虚拟模 拟,对于虚拟模拟的推广应用有着一定的借鉴意义,目前该系统已在公司亚太区开始应用,反映良好。
Ab8tract
Concept and adVantage of modul盯 design as weU as its application in tlle devel叩ment of dome8tic automobile i8 p舱∞nted in tlIi8 paper.New deVelop- ment in tlIe modlll缸de8ign abmad i8 a180 di8cussed.
3.学位论文 王其光 翼展车厢有限元分析与轻量化设计 2007
翼展式厢式货车车厢骨架是重要的承载件,它的质量也占货车整车整备质量的三分之一左右。车厢骨架的轻量化设计对减轻汽车的质量有着非常重 要的意义。本文就是通过对翼展式厢式货车车厢骨架有限元的分析计算,寻求切实可行的车厢骨架轻量化途径。
有限元法已经成为现代汽车设计的重要工具之一,与传统的设计方法相比,它的优势在于提高汽车产品的质量、降低产品开发与生产制造成本,提 高汽车产品在市场上的竞争力。为了促进厢式货车车厢设计水平的提高,保证整车在市场上的竞争能力,必须将厢式货车车厢有限元分析技术提高到战 略的高度上来。
该车型的总装是分成9大模块完成的,前端 模块、前保险杠总成、后保险杠总成、车门模块、仪 表板总成、座椅、其它内饰件、底盘零件和动力总 成模块。
在总装车间里,整个总装线的安排,不象一般 流水线那样密密麻麻地安插着大量的不同工位, 而是以各个模块或总成分区,在总装线旁边布置 了多个分装线。工人们先是在分装线上装配好各 个模块或总成,然后传送到总装线上装配。这样 就使得总装线工位减少,分工清楚,工人劳动强度 减轻,装配质量也容易得到控制。 4.2前端模块的分析
万方数据
传统非模块设计,即使能很好地控制设计偏 差和零件制造偏差,但由于整车装配零件多,装配 过程偏差还是难以控制,这就限制了整车装配质 量的提高。
4 模块化设计在当今国内车型中的 应用
第一阶段的模块化设计已经不是停留在设计 师们头脑中的概念了,在国外,它已经直接应用在 大批量定制生产的车型中。在国内最近投放市场 的某款车型中,我们已经看到了该车型模块化设 计思想的初步应用以及带来的好处。 4.1模块的组成
·3·
万方数据
汽车模块化设计的应用与发展
作者: 作者单位: 刊名:
英文刊名: 年,卷(期): 引用次数:
邱国华 泛亚汽车技术中心有限公司
上海汽车 SHANHAI AUTO 2002,(11) 1次
相似文献(10条)
1.学位论文 何先卫 基于UG的虚拟车身数字化模型应用研究 2003
虚拟现实(VirtualReality简称VR)技术是二十世纪末才兴起的一门崭新的综合性信息技术,是计算仿真在更高层次上的延伸和拓展。虚拟现实技术 利用计算机生成一种模拟环境,实现用户与该环境直接进行自然交互。汽车设计采用虚拟现实技术能够加快设计和开发过程,缩短产品研发时间,降低 开发成本。目前虚拟现实技术在汽车方面的应用研究主要集中在虚拟原型可视化、虚拟设计、虚拟装配、虚拟试验这几个方面。本文在讨论了虚拟现实 技术的发展及国内外研究现状,并深入分析了虚拟现实技术在汽车设计中应用的基础上,提出了一个基于UG平台上的车身虚拟造型系统,该系统借助于 UG软件强大的曲面、实体造型功能以及二次开发功能,良好的输入输出界面、交互工具,很好的虚拟环境效果来实现车身的三维虚拟概念造型、虚拟装 配。根据汽车虚拟造型的实际需要,在UG平台上进行了二次开发,设计开发了车身表面光顺处理模块,使车身表面具有更好的光顺效果,同时开发了数 据传输模块,读取UG数据库中的实体数据,实现UG数据库中数据与外界的交互传输。
上海汽车
接装配在车身上的零件数目少,装配控制点少,对 车身焊接要求低,不仅降低成本,更能够提高整车 的装配质量。其它各大模块和总成也有类似的设 计思想,它们共同作用,保证了整车装配的高质 量。
5 模块化设计的新发展
上述车型的设计只是模块化设计的刚刚起 步,它只是在目前车型基础上对总装装配零件开 始了模块化设计,同时局部改进了车身设计,但却 还未从整车结构层面上考虑模块化设计。也就是 说还未达到模块化设计的第二阶段。目前国外一 些汽车公司,面对竞争日趋激烈的市场以及变型 车生产成本极其昂贵的现实,已经开始考虑整体 化的模块设计,以满足消费者对有独特风格时尚 车型要求的增长,使他们可以按照“菜单”,选择自 己喜欢的模块配置,然后按他们的需求生产出各 式各样的车型。
相反的,按照传统非模块化设计思想设计汽车, 当油漆完成后的白车身运送到总装线后,几乎大部分 零件都是以单件形式由工人在长长的流水线上一件 一件装到车身上。这种装配方式,一方面造成工位很 多,使得总装车间的流水线布置得相当长,占地面积 大,成本升高;另一方面因为单件太多,在紧张的工作 环境中容易错装或漏装零件,特别是在多种车型共线 的情况下,更容易发生质量事故。
4
我们以前舱的设计来分析模块化设计思想在 该车上应用的优点。传统的车身前舱设计,类似 于一个框架结构,如图1所示。这些零件焊接在 一起,形成了车身前舱。在总装车间,动力总成及 底盘零件,空调冷凝器和散热器,前照大灯及各种 线束等多种零件都一个一个在不同工位安装。
该车型的前舱设计,散热器横梁不是焊接在 白车身上,如图2所示,整个前舱前部是开口结 构。单独设计了一个前端模块,见图3,它上面集 成了散热器横梁、前照灯、空调冷凝器及散热器、 水箱面罩、发动机罩锁扣等相关零件,在前端模块 分装线上装配好后,运送到总装线,以一体化的形 式从前舱开口处推入,只用6个螺钉固定在车身
图4藏一克公司提出的分块图
6 小结
技术的发展是永无止境的。我国的汽车工业 正处在引进国外技术促进自身发展的时期,我们 不仅要引进国外的先进生产技术,而更应着眼于 跟进当今世界汽车先进开发技术,关注新的设计 理念,并结合我国的实际情况,为尽早形成我国汽 车与世界同步的研发水平而努力。模块化设计思 想,正是我们应该积极关注的一项先进开发技术。
2模块化设计的定义
所谓模块化设计,是指设计时把整车按功能 分成几大独立的模块,每个模块上集成多个零件 或总成,各个模块之间的联接是固定的,不会因为 其中零件或总成的变化而改变,在装配时以模块 为基础装配。模块化设计的第一阶段,是总装装 配零件的模块化;第二阶段,要达到整车层面上的 整体模块化设计。