乘用车平台前端模块化设计
乘用车白车身平台结构设计

乘用车白车身平台结构设计作者:潘承鹏来源:《汽车与驾驶维修(维修版)》2020年第04期摘要:对汽车企业来讲,一个长期可持续开发的车身平台非常重要,企业会基于产品平台开发大量的车型数据、CAE分析模型及验证报告等,对后续二次开发车型具有指导意义,节约后续车型的开发时间及成本。
本文通过对白车身平台全新开发实列的研究和总结,介绍了几种在后续二次开发情况下的结构设计开发方案。
关键词:白车身平台;结构设计中图分类号:U462文献标识码:A当今的汽车企业,需要用最快的时间将新设计的多种变型车型推向市场。
同时,还要控制自身成本,向客户交付高质量、高性能和高安全性的汽车。
为了实现这一目标,车企需要有一个或者多个产品平台。
白车身平台的开发,在概念阶段将对后续车型的固有结构及动态特性產生影响。
因此在概念阶段,设计师及工程师都需要考虑即将投放市场的车型情况,还必须确保此平台在最大限度的满足成本、轻量化及性能等各种条件的情况下,平台能适用于后续开发的其他不同类型车型。
1白车身平台开发实例1.1平台开发需求及目标新平台的基础车定义为SUV车型,而且根据不同的底盘布置要求,需要开发出18款白车身下车体有以下要求。
(1)满足3种不同轴距的布置需求。
(2)满足2种车体空间(宽体/窄体)的布置需求。
(3)满足轿车布置需求。
(4)满足纯电动车布置需求。
(5)满足成本、轻量化及性能要求。
1.2不同轴距开发实例根据开发需求,下车体有3种轴距。
为了在轴距变换的同时满足成本需求,并尽可能提高通用化率,采取的设计方案如下。
(1)发动机舱总成和前地板总成沿用基础车型。
(2)后地板总成局部变更,其中前后地板连接板总成根据总布置所布置的第2排人机位置做相应的调整来满足座椅安装(基础车设计时候应尽可能考虑后续轴距变换时零件的通用性,或者通过更改切边模具等来实现通用性)。
后地板面板分总成根据轴距的变换平移相应距离,后地板骨架总成平移相应距离,同时后纵梁前端需要根据前后地板连接板总成重新匹配设计(图1)。
汽车前端模块总成模块化设计及应用
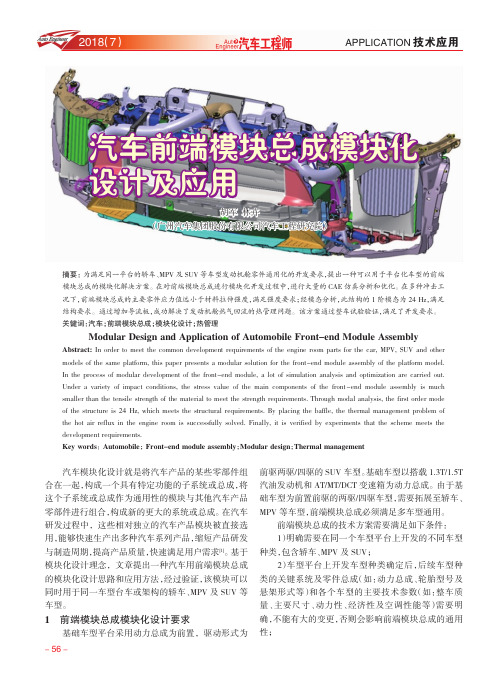
中冷器、散热器及风扇分总成、前端模块骨架总成等主
要零部件组成。其中,冷凝器通过螺栓固定至中冷器, 中冷器与散热器通过螺栓固定,散热器通过软垫固定
图 前端模块总成应力分布
在前端模块骨架总成上。前端模块总成主要部件及发 动机舱总布置简图,如图 1所示。
2018(7)
20技18术年应7用月
汽车前端模块总成模块化 设计及应用
胡军 林卉 (广州汽车集团股份有限公司汽车工程研究院)
摘要:为满足同一平台的轿车、"#$ 及 %&$ 等车型发动机舱零件通用化的开发要求,提出一种可以用于平台化车型的前端 模块总成的模块化解决方案。在对前端模块总成进行模块化开发过程中,进行大量的 '() 仿真分析和优化。在多种冲击工 况下,前端模块总成的主要零件应力值远小于材料拉伸强度,满足强度要求;经模态分析,此结构的 * 阶模态为 +, -.,满足
模块化设计理念,文章提出一种汽车用前端模块总成
2)车型平台上开发车型种类确定后,后续车型种
的模块化设计思路和应用方法,经过验证,该模块可以 类的关键系统及零件总成(如:动力总成、轮胎型号及
同时用于同一车型台车或架构的轿车、MPV及 SUV等 悬架形式等)和各个车型的主要技术参数(如:整车质
车型。
! 前端模块总成模块化设计要求
零部件进行组合,构成新的更大的系统或总成。在汽车 MPV等车型,前端模块总成必须满足多车型通用。
研发过程中,这些相对独立的汽车产品模块被直接选
前端模块总成的技术方案需要满足如下条件:
用,能够快速生产出多种汽车系列产品,缩短产品研发
1)明确需要在同一个车型平台上开发的不同车型
[1]
与制造周期,提高产品质量,快速满足用户需求 。基于 种类,包含轿车、MPV及 SUV;
汽车轻量化之前端模块
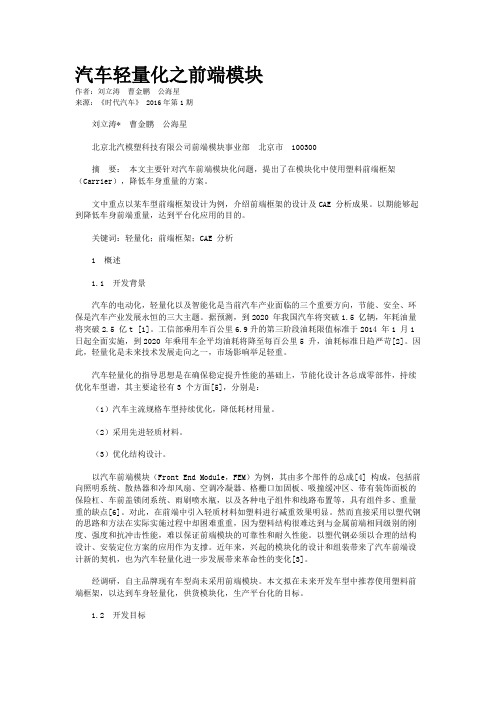
汽车轻量化之前端模块作者:刘立涛曹金鹏公海星来源:《时代汽车》 2016年第1期刘立涛* 曹金鹏公海星北京北汽模塑科技有限公司前端模块事业部北京市100300摘要:本文主要针对汽车前端模块化问题,提出了在模块化中使用塑料前端框架(Carrier),降低车身重量的方案。
文中重点以某车型前端框架设计为例,介绍前端框架的设计及CAE 分析成果。
以期能够起到降低车身前端重量,达到平台化应用的目的。
关键词:轻量化;前端框架;CAE 分析1 概述1.1 开发背景汽车的电动化,轻量化以及智能化是当前汽车产业面临的三个重要方向,节能、安全、环保是汽车产业发展永恒的三大主题。
据预测,到2020 年我国汽车将突破1.5 亿辆,年耗油量将突破2.5 亿t [1]。
工信部乘用车百公里6.9升的第三阶段油耗限值标准于2014 年1 月1日起全面实施,到2020 年乘用车企平均油耗将降至每百公里5 升,油耗标准日趋严苛[2]。
因此,轻量化是未来技术发展走向之一,市场影响举足轻重。
汽车轻量化的指导思想是在确保稳定提升性能的基础上,节能化设计各总成零部件,持续优化车型谱,其主要途径有3 个方面[5],分别是:(1)汽车主流规格车型持续优化,降低耗材用量。
(2)采用先进轻质材料。
(3)优化结构设计。
以汽车前端模块(Front End Module,FEM)为例,其由多个部件的总成[4] 构成,包括前向照明系统、散热器和冷却风扇、空调冷凝器、格栅口加固板、吸撞缓冲区、带有装饰面板的保险杠、车前盖锁闭系统、雨刷喷水瓶,以及各种电子组件和线路布置等,具有组件多、重量重的缺点[6]。
对此,在前端中引入轻质材料如塑料进行减重效果明显。
然而直接采用以塑代钢的思路和方法在实际实施过程中却困难重重,因为塑料结构很难达到与金属前端相同级别的刚度、强度和抗冲击性能,难以保证前端模块的可靠性和耐久性能。
以塑代钢必须以合理的结构设计、安装定位方案的应用作为支撑。
整车模块化平台关键尺寸L113设定

2021年第7期潘彦成赵国栋秦广义安鹏姜显丰(一汽奔腾轿车有限公司,长春130000)【摘要】基于整车平台化、模块化开发策略,论证分析了关键尺寸参数L113的设定过程。
通过对L113的尺寸链分解,提出了各部分对L113的限制因素,并且明确了设定方法。
平台开发过程中,L113的合理规划,既对汽车设计及零部件的成本降低起到重要作用,也对确定平台人机属性具有一定的指导意义。
主题词:L113平台化模块化人机工程中图分类号:U462.2+2文献标识码:ADOI:10.19822/ki.1671-6329.20210019The Key Dimension L113Setting of the Vehicle Modular PlatformPan Yancheng,Zhao Guodong,Qin Guangyi,An Peng,Jiang Xianfeng(FAW Car Co.,Ltd.,Changchun 130000)【Abstract 】Based on the vehicle platform and modular development strategies,the process of setting the key dimension parameter L113is demonstrated and analyzed.By decomposing the dimension chain of L113,the limiting factors of each part on L113are proposed,and the setting method is clarified.In the process of platform development,the reasonable planning of L113not only plays an important role in reducing the cost of automobile design and parts,but alsohas a certain guiding significance to determine the human-machine attributes of the platform.Key words:L113,Platform,Modular,Ergonomics整车模块化平台关键尺寸L113设定【欢迎引用】潘彦成,赵国栋,秦广义,等.整车模块化平台关键尺寸L113设定[J].汽车文摘,2021(7):22-26.【Cite this paper 】Pan Y,Zhao G ,Qin G,et al.The Key Dimension L113Setting of the Vehicle Modular Platform [J].Automotive Di⁃gest (Chinese),2021(7):22-26.1前言随着经济的发展,汽车产业成为了我国国民经济的支柱产业,汽车制造业产值约占经济总量的2%~3%[1]。
基于Android平台的智能行车导航系统设计与开发

基于Android平台的智能行车导航系统设计与开发随着科技的不断发展,智能导航系统已经成为现代汽车行业中不可或缺的一部分。
而基于Android平台的智能行车导航系统更是在用户体验和功能性上有着明显的优势。
本文将介绍基于Android平台的智能行车导航系统的设计与开发过程,包括系统架构设计、功能模块实现、地图数据集成等方面。
一、系统架构设计在设计智能行车导航系统时,系统架构是至关重要的一环。
基于Android平台的智能行车导航系统通常可以分为前端和后端两部分。
前端主要包括用户界面设计、地图显示、路线规划等功能,而后端则负责数据处理、算法计算等核心功能。
1.1 前端设计在前端设计中,用户界面的友好性和易用性是首要考虑的因素。
通过Android平台提供的各种UI组件和交互方式,可以实现地图显示、搜索功能、路线规划等操作。
同时,还可以结合语音识别、手势控制等技术,提升用户体验。
1.2 后端设计后端设计主要涉及到数据处理和算法计算。
地图数据的存储和管理、路线规划算法的选择和优化都是后端设计中需要考虑的问题。
同时,为了提高系统的实时性和准确性,还需要考虑数据更新机制和网络通信方面的设计。
二、功能模块实现基于Android平台的智能行车导航系统具有丰富的功能模块,包括但不限于地图显示、路径规划、实时交通信息、语音导航等功能。
2.1 地图显示地图显示是智能行车导航系统中最基本也是最核心的功能之一。
通过集成地图SDK,可以实现地图的加载、缩放、拖动等操作,并在地图上显示POI点、路况信息等。
2.2 路径规划路径规划是智能行车导航系统中的重要功能之一。
通过选择合适的路径规划算法,并结合实时交通信息和用户偏好,可以为用户提供最优的驾驶路线。
2.3 实时交通信息实时交通信息可以帮助用户避开拥堵路段,选择更加畅通的道路。
通过集成第三方交通数据服务,可以获取实时路况信息,并在地图上进行展示。
2.4 语音导航语音导航是提高驾驶安全性和便利性的重要功能之一。
自动驾驶模块化设计
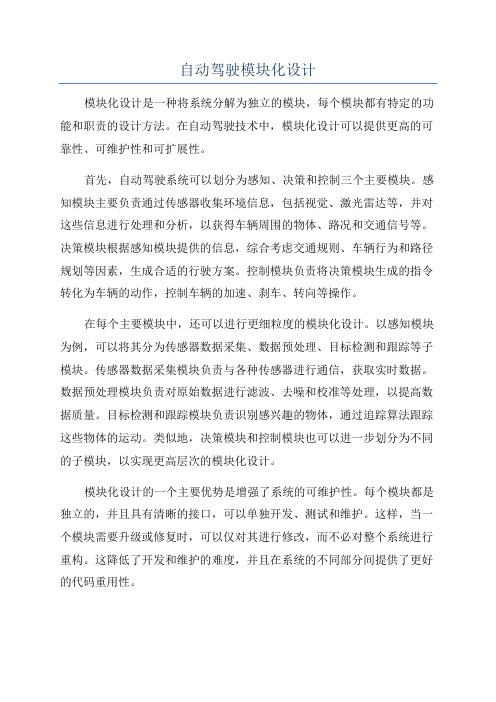
自动驾驶模块化设计模块化设计是一种将系统分解为独立的模块,每个模块都有特定的功能和职责的设计方法。
在自动驾驶技术中,模块化设计可以提供更高的可靠性、可维护性和可扩展性。
首先,自动驾驶系统可以划分为感知、决策和控制三个主要模块。
感知模块主要负责通过传感器收集环境信息,包括视觉、激光雷达等,并对这些信息进行处理和分析,以获得车辆周围的物体、路况和交通信号等。
决策模块根据感知模块提供的信息,综合考虑交通规则、车辆行为和路径规划等因素,生成合适的行驶方案。
控制模块负责将决策模块生成的指令转化为车辆的动作,控制车辆的加速、刹车、转向等操作。
在每个主要模块中,还可以进行更细粒度的模块化设计。
以感知模块为例,可以将其分为传感器数据采集、数据预处理、目标检测和跟踪等子模块。
传感器数据采集模块负责与各种传感器进行通信,获取实时数据。
数据预处理模块负责对原始数据进行滤波、去噪和校准等处理,以提高数据质量。
目标检测和跟踪模块负责识别感兴趣的物体,通过追踪算法跟踪这些物体的运动。
类似地,决策模块和控制模块也可以进一步划分为不同的子模块,以实现更高层次的模块化设计。
模块化设计的一个主要优势是增强了系统的可维护性。
每个模块都是独立的,并且具有清晰的接口,可以单独开发、测试和维护。
这样,当一个模块需要升级或修复时,可以仅对其进行修改,而不必对整个系统进行重构。
这降低了开发和维护的难度,并且在系统的不同部分间提供了更好的代码重用性。
此外,模块化设计还能够提高系统的可靠性。
由于每个模块是独立的,意味着一个模块的故障不会对其他模块产生严重影响。
例如,如果感知模块出现故障,决策和控制模块仍然可以继续工作,并采取相应的措施保证车辆的安全。
这种冗余设计减少了系统的单点故障,并提高了整个系统的可靠性和鲁棒性。
最后,模块化设计还可以提供更好的可扩展性。
当需要增加新的功能时,可以通过添加新的模块来实现扩展,而不影响现有的模块和系统架构。
这种灵活性使得自动驾驶系统能够适应未来的技术和需求的变化,例如增加对新传感器的支持或改进决策算法。
某车型前端模块设计和平台化构想
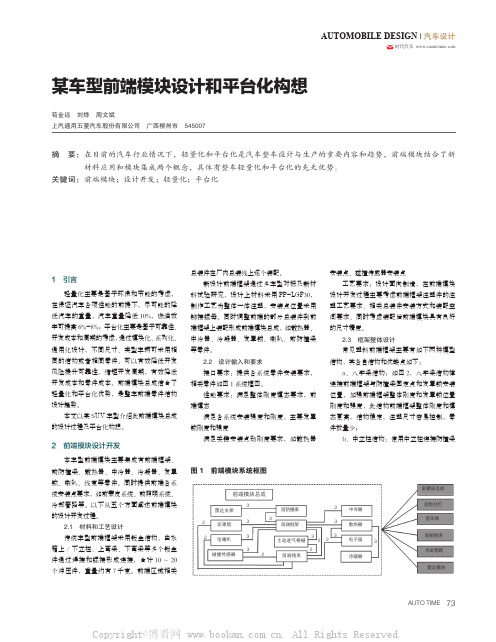
前端模块已实现了前端结构模块化集成, 具有先天平台化基础。初步构想从如下三方 向提供零件共用率,减少零件种类,实现前 端模块平台化。
1)结构和布置统一化:结构和布置的 统一是平台化的基础。在前期设计中需要 尽量考虑各种车型需要,选择合适的布置 位置和安装结构,将安装结构和布置位置 的统一。有效保证设计可靠性和延续性, 同时可以降低开发风险。例如散热器采用 统一的水箱结构,与车身安装点和方式也 统一;中冷器均布置在防撞梁下方,与前 端模块通过 4 颗螺栓前后方向连接,发罩 锁与散热器相对位置(限制造型发罩分缝 特征和位置)。
图 1 前端模块系统框图
前端模块总成
3 雷达支架
2
发罩锁
3
前防撞梁
3 前端框架
3
中冷器
3
散热器
2 电喇叭
3
主动进气格栅
3 2
2
3
电子扇
3
3
碰撞传感器
2
2 前端线束
冷凝器
前蒙皮总成 前组合灯 前车体 前舱线束 冷却管路
雷达模块
AUTO TIME 73
Copyright©博看网 . All Rights Reserved.
AUTOMOBILE DESIGN | 汽车设计
和发罩锁安装点。发罩锁刚度和强度更容易 满足要求,但由于框架整体为矩形,前端框 架相对刚度模态偏低,同时注塑后收缩不稳 定,需要前期多次分析和调整。 图 2 八字梁结构
图 3 中立柱结构
本车型前端框架设计选用中立柱结构。 前端框架整体为矩形,由上 / 下横梁和左右 立柱构成,发罩锁安装区域通过钣金中立柱 连接发罩锁和前防撞梁,有效满足发罩锁安 装各项刚度和强度要求。设计上对横梁与立 柱连接接头位置通过设计三角筋加强连接刚 度。布置上将对刚度和动刚度要求高的零件 布置在立柱上并靠近前端框架与放撞梁连接 部位。
汽车平台研发新趋势:生产模块化零部件通用化

汽车平台研发新趋势:生产模块化零部件通用化前言1.汽车平台概念其实“汽车平台”并没有一个切当的定义,概念较为笼统,主要体现在汽车的研发阶段。
简单而言就是开辟过程中用一个平台可以同时承载不同车型的开辟与生产创造,产生出外形、功能都不尽相同的产品。
在创造方面,同一平台的产品大量采用通用化的零部件和总成,大大降低了创造成本和采购成本;在研发方面,一个平台上实现了技术突破,等于这个平台上搭载的所有产品都实现了技术突破,对研发、对产品的供应链和服务链都产生了革命性的影响,同时为实现世界围的兼并重组。
汽车的大工业生产方式发生过三个转变:20 世纪初,福特公司在创造 T 型车时创造出影响整个世界工业的生产工艺——生产流水线,大幅度降低了生产周期和成本,同时也降低了售价。
流水线方式作为汽车生产的主流方式一致延续到 80 年代。
随着科技进步和市场的变化,一个型号的产品生命周期越来越短,大批量生产方式逐渐变得不能适应竞争。
在 80 年代,产生了一种称为"汽车平台"的概念,“汽车平台”是由汽车创造厂商设计的,几个车型共用的产品平台。
汽车平台与车辆的基本结构相关,出自于同一平台的不同车辆具有相同的结构要素,例如车门立柱、翼子板、车顶轮廓等。
同一平台的车型的轴距普通情况下是相同的,同时一些配件是通用的。
有时候不少种不同品牌的车在一个平台,而同一品牌的不同年度车型反而不在一个平台。
在"模块化"生产方式下,汽车技术创新的重心在零部件方面,零部件要超前发展,并参预汽车厂商的产品设计。
例如德尔福系统公司相继推出了座舱、接口盘制动、车门、前端、集成空气/燃油等模块。
而汽车厂商方面则以全球围作为空间,进行汽车模块的选择和匹配设计,优化汽车设计方案,将汽车装配生产线上的部份装配劳动转移到装配生产线以外的地方去进行。
采用"模块化"生产方式有利于提高汽车零部件的品种、质量和自动化水平,提高汽车的装配质量,并缩短汽车的生产周期。
- 1、下载文档前请自行甄别文档内容的完整性,平台不提供额外的编辑、内容补充、找答案等附加服务。
- 2、"仅部分预览"的文档,不可在线预览部分如存在完整性等问题,可反馈申请退款(可完整预览的文档不适用该条件!)。
- 3、如文档侵犯您的权益,请联系客服反馈,我们会尽快为您处理(人工客服工作时间:9:00-18:30)。
于10倍圆孔直径;长孑L塞焊的开孔长度应不小于75衄,孔
的宽度应不小于板厚的2倍,孔端部呈半圆形;孔的间距应不 大于长孔长度的2倍等。
4厚薄板过渡焊接不满足规范要求 (觎勘要求强力甲板货舱舱口角隅的圆弧半径r应不小
于b/20(b为货舱舱口的宽度)。位于载货区域的货舱舱口角 隅应按规定的形式采用较货舱区域强力甲板增厚0.5倍的加厚 板予以补强。这样一来,与货舱角隅甲板相邻的首部甲板或尾 部甲板厚度差较大,常见的厚度差有时甚至达到10 mm。而检 验中发现,一些在建船舶施焊时没有将较厚板的边缘削斜,且 将不平面布置在甲板背面,造成背面的甲板骨架与甲板的焊接
图3中冷器布置在冷凝器与散热器之间
(2)中冷器位于冷凝器前面,前后布置顺序为中冷器(最
前端)一冷凝器一散热器一冷却风扇(最后端),该布置方式
多用于轿车。根据重力向下的原理,散热器进水管布置在散热 器芯体上部,出水管布置在芯体下部,散热器上部分水温比下 部分水温要高,需要散发的热量更多,需提供更好的散热环 境,且一般车辆前部造型都是上短下长。因此,布置中冷器时 应充分利用下部的空间,把中冷器布置在下部,也使得冷却系 统性能达到最佳。 中冷器采用2种布置形式:①中冷器与冷凝器前后布置, 高度方向上有重叠(如图4所示);②中冷器与冷凝器上下布 置,高度上不重叠,称为“吕”结构(如图5所示)。
厂质检员的角色。这不仅要求我们的验船师要具备专业的检验
技能,熟悉各项工艺要求,熟悉《观}酚要求,同时又要有耐 心,与船厂工人、质检员等保持良好的沟通,努力做到“一 检、二帮、三把关”。
注释 ①由于不同年份的《规范》要求可能存在少许差别,无法逐一罗列,此
处统称为《规范》,具体要求可详细查阅适用的《规范》要求。
向:整车架构开发;李柳林(1986一),男,广西上林人。硕士研究生,上汽通用五菱汽车股份有限公司助理工程师,研究方向:发动机舱物理集 成;李家烽(1983一),男,广西灵山人,上汽通用五菱汽车股份有限公司工程师,研究方向:发动机舱物理集成。
qiyekejiyufazhan
15
万方数据
析。在长度、宽度方向上不能再减小,因此只能降低中冷器高 度,减少l根散热扁管与l条散热带,测试结果见表3,结果 显示高度下降后的中冷器性能依然可以满足发动机性能要求。
【关键词】汽车平台;前端模块;模块化 【中圈分类号】U462 【文献标识码】A 【文章编号】1674—0688(2015)09—0015—02
器和冷却风扇、发动机进气中冷系统、空调冷凝器、散热器框 架集成(散热器左、右立柱总成、散热器上、下横梁总成)、 现今主要乘用车生产企业均采用平台战略构建自己的产品 系列,有行业分析报告指出,汽车平台开发已占据车企研发支 出费用的一半。如何进一步提高产品开发效率、缩短开发周 期,以满足市场需求的变化,将更多的资金用于新能源汽车等 新技术、新产品的开发,已经成为各企业必须面对的共同课 题。进一步削减平台数量、扩大主流单一平台车型覆盖率、提 高平台规模效益是不二选择。据有效统计数据显示,目前全球 主流几大汽车平台的产量占汽车总产销量的40%左右【11。
5其他焊接质量问题
(1)《规≯酚要求凡焊缝长度在300 mm以内者,一律采用 连续焊。骨材端面与板(如有时)、肘板与板或构件的焊接采 用双面连续焊;当船体结构采用间断焊缝时,对骨材的端部、 各种构件的切口、切角、开孑L等部位均应采用连续包角焊缝, 而现实中最常见的现象是肘板端部、骨材端部、构件切口、流 水孔、施焊孔等无包角焊。 (上接第16页) 由台架试验结果可知:经过中冷器的冷却空气会有一定的 温升,根据不同的芯体正面积大小、风速,冷却空气的温升也 不一样,一般为5。25℃,而且在相同条件下,芯子正面积越 小温升越大。中冷器位于各散热元器件的最前面容易使布置于 后面的冷凝器及散热器的冷却温度变高、散热性能变差。为了 实现Car、MPV车型前舱最大化共用且同时满足空调制冷性 能,最终选定方案二。
100
凝器(最前端)一中冷器一散热器一冷却风扇(最后端),如
图3所示。该布置方式多用于SUV、MPV等冷却系统上、下 安装支架空间较大的乘用车。
mm,选用现有中冷器成品,两者高度方向上有120 mm重
叠,中间间隔10mm(如图6所示)。 方案二:中冷器与冷凝器上下布置,冷凝器加高80 mm。新 开发高度降低的中冷器如图7所示。
图6方案一 图7方案二
台架试验约束条件如下。 (1)散热器控制介质:水,迎面风速为4.5 m/s,水流量 为80 Umin,气液温差为52℃(38~90℃)。 (2)中冷器控制迎面风速为45 m/s,热空气流量为0.08 k幽, 环境温度为38℃,进口热空气温度为150℃,进口压力为
220kPa。
(3)冷凝器控制进口压力为1
500
kPa,进口温度为80℃,
出口过冷度为8℃,进风温度为38℃,风速为4.5m/s。 前端模块热交换性台架试验结果见表4。
表4前端模块热交换性台架试验结果
模块总 能力 (kW) 冷凝器 中冷器 散热器 换热量 换热量 换热量 (kW)
(k冒) (kl『)
方案
模块
通风 阻抗 (Pa)
冷凝器 冷媒 流阻 (”a)
根据功能件布置差异分析可知,满足车身右边中冷器进气管布 置空间、大灯安装与散热器的安装工艺空间,散热器在上弯 梁、下弯梁右边固定点位置共用,根据不同的发动机性能要求 选用不同宽度尺寸的散热器,散热器车身框架中的上弯梁与下 弯梁预留安装固定位置,可满足平台散热器框架共用的策略 (如图2所示)。
3平台化前端模块布置
16
qiyekejiyufazhan
(下转第18页)
万方数据
甲板焊接。在现场检验中发现,一些船厂工人为徒省事,存在 弄虚作假的现象:如船舶甲板机械如系缆桩下方的要求为复 板,但看似有一个环形复板,而实际在缆桩下方并无复板,或 是有整块的复板,但塞焊的规格远远达不到规范要求。
(2)舷侧顶列板与甲板边板角接缝对船舶建造质量至关重 要,检验中偶尔会发现,强力甲板的边缘未开坡口,这就难以 保证能完全焊透。
31.410
1.455
6.7“
23.816
179.0
4.0
28.5
3.3
某型增压发动机对中冷器的进气性能的要求见表2。
表2某增压发动机中冷参数要求
l l
中冷器内压降 小于6.8
kPa
30.720
6.733
24.203
177.7
28.4
3.4
35.4ll
7
3ll
6
837
2l
668
173 9
144.0
29.1
企业科技与发展
乘用车平台前端模块化设计
宋建新L2,李柳林2,李家烽2
(1.上海交通大学机械与动力工程学院,上海200240;2.上汽通用五菱汽车股份有限公司,广西柳州545007)
【摘要】文章阐释了目前乘用车平台化的发展状况,然后对乘用车平台开发中前端模块的布置进行了详细的说明
和分析,包括边界条件、重要性能要求。最后分析前端模块的2种布置方案及进行台架试验,结果显示该前端模 块布置方案满足性能要求。
图1乘用车前端模块
1
引言
发盖锁闭系统、前蒙皮、前格栅及各种电子组件和线路布置等
(如图1所示)。
2乘用车平台化发展现状
汽车平台发展至今,已经形成以下3种开发模式。 (1)以“大众”为代表的模块化平台,主要特征是看重跨 车型和跨细分产品的分布,即每个平台可应对普通轿车、 SUV、MPV等多种车型,以及满足各细分车型区隔的要求, 如“大众”横置发动机MBQ模块平台包括了“大众”集团目 前横置平台的所有小型、紧凑型和中型车。 台可满足C级车和D级车的产品开发闭。 (2)以“通用”和“丰田TNGA”为代表的产品架构性平 台,不但总产销规模超800万台,而且单个细分产品区隔的产 销规模也非常巨大,通常超过150万台,因此更加看重每个细 分产品内的最优化。 (3)以“马自达SKYACTIVEE”技术为代表的“泛平 台”,由于企业产销规模小,总产销量在100万台左右,因此
3.1
在某乘用车平台开发项目中规划有2种车型,5座CAR、 7座MPV,动力总成配置有自然进气发动机、增压发动机。为 了降低成本、减少开发费用,平台开发策略定义为前舱功能件 实现布置最大共用。以CAR自然进气发动机车型配置的前端 模块功能件为基础,分析平台前端模块功能件的空间布置差 异,结果见表l。
有较大的间隙,严重影响焊接质量,而(觎≯酚的要求是不同
厚度的钢板进行对接时,若其厚度差大于或等于4 mm时,应 将较厚板的边缘削斜,使其均匀过渡,削斜宽度应不小于厚度 差的4倍。
参考文献
[1]中国船级社.钢质内河船舶建造规范[M].北京:人民交通出版 社,2015. [2]中国海事局.内河船舶法定检验技术规则[M].北京:人民交通 出版社。2015.
(觎
范》中关于塞焊有明确而具体的要求:圆孔塞焊的间距应不大
6结语Байду номын сангаас
以上问题是笔者多年在现场检验及图纸审查中发现的较为 典型的问题,但现实中存在的问题不止于此。由于生产力水平 及船厂质检人员的能力、责任心不够及管理制度存在缺陷,这 些看似简单的质量问题,却在这些小型的私营船厂里层出不 穷。因此,对于地方船检来说,需要做的不仅仅是检验,还需 要指导技术人员施工,指导质检员自检,甚至有时还要充当船
表3某增压发动机中冷器参数 图2散热器框架集成共用布置 l芯体尺寸(长X宽X高)(咖)l面积(m蛩l换热性能舶m/s(们l中冷器内压降(kPa)l
J
630X123X150 77 490 8088 ≤6.8
l
却,再进入发动机中。有数据表明,在相同的空燃比条件下, 增压空气的温度每下降10℃,发动机功率就能提高3%一5%。 增压发动机中冷器一般采用中冷器前置、中冷器侧置、中 冷器顶置3种布置方案。 中冷器前置时,中冷器放置于发动机舱前端、前保险杠后 面,中冷器与散热器、冷凝器及冷却风扇集成一个冷却模块, 方案普遍应用在乘用车上,中冷器前置可采用2种布置形式。 (1)中冷器位于冷凝器与散热器之间,前后布置顺序为冷