刻蚀设备与工艺介绍
刻蚀机 腔体结构 工艺
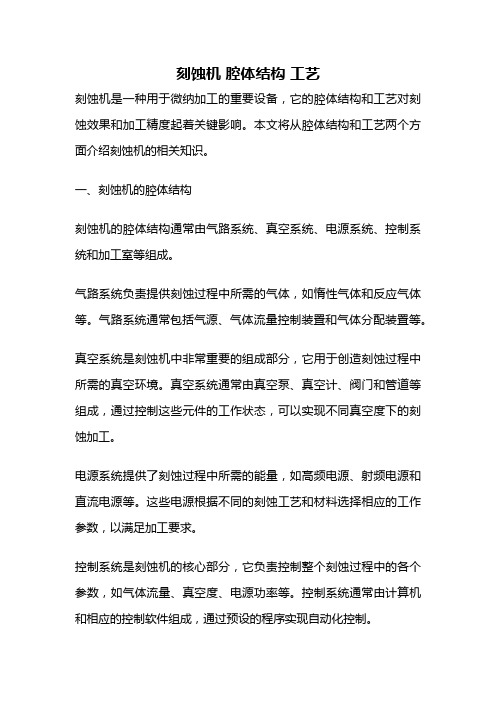
刻蚀机腔体结构工艺刻蚀机是一种用于微纳加工的重要设备,它的腔体结构和工艺对刻蚀效果和加工精度起着关键影响。
本文将从腔体结构和工艺两个方面介绍刻蚀机的相关知识。
一、刻蚀机的腔体结构刻蚀机的腔体结构通常由气路系统、真空系统、电源系统、控制系统和加工室等组成。
气路系统负责提供刻蚀过程中所需的气体,如惰性气体和反应气体等。
气路系统通常包括气源、气体流量控制装置和气体分配装置等。
真空系统是刻蚀机中非常重要的组成部分,它用于创造刻蚀过程中所需的真空环境。
真空系统通常由真空泵、真空计、阀门和管道等组成,通过控制这些元件的工作状态,可以实现不同真空度下的刻蚀加工。
电源系统提供了刻蚀过程中所需的能量,如高频电源、射频电源和直流电源等。
这些电源根据不同的刻蚀工艺和材料选择相应的工作参数,以满足加工要求。
控制系统是刻蚀机的核心部分,它负责控制整个刻蚀过程中的各个参数,如气体流量、真空度、电源功率等。
控制系统通常由计算机和相应的控制软件组成,通过预设的程序实现自动化控制。
加工室是刻蚀过程中的工作区域,通常由真空室和刻蚀室组成。
真空室用于创造刻蚀过程所需的真空环境,而刻蚀室则是实际进行刻蚀加工的地方。
刻蚀室内通常设有夹具、靶材和探针等,以保证加工的稳定性和精度。
二、刻蚀机的工艺刻蚀机的工艺是指刻蚀加工过程中所采用的方法和步骤。
刻蚀工艺的选择和优化直接影响到加工效果和加工质量。
首先是选择合适的刻蚀气体。
刻蚀气体通常分为惰性气体和反应气体两种。
惰性气体主要用于保护加工室和靶材,防止氧化或污染;而反应气体则是实际参与刻蚀反应的气体,它们可以与靶材表面发生化学反应,达到刻蚀的目的。
其次是确定刻蚀参数。
刻蚀参数包括刻蚀气体流量、刻蚀时间、刻蚀功率等。
这些参数的选择应根据具体的刻蚀要求和材料特性来确定,以确保刻蚀过程的稳定性和加工质量。
刻蚀机的工艺还包括刻蚀模式的选择。
常见的刻蚀模式有湿法刻蚀和干法刻蚀两种。
湿法刻蚀是在液体介质中进行的刻蚀,适用于一些化学反应比较剧烈的材料;而干法刻蚀则是在真空或气氛中进行的刻蚀,适用于一些对环境要求较高的材料。
刻蚀机设备和操作规程
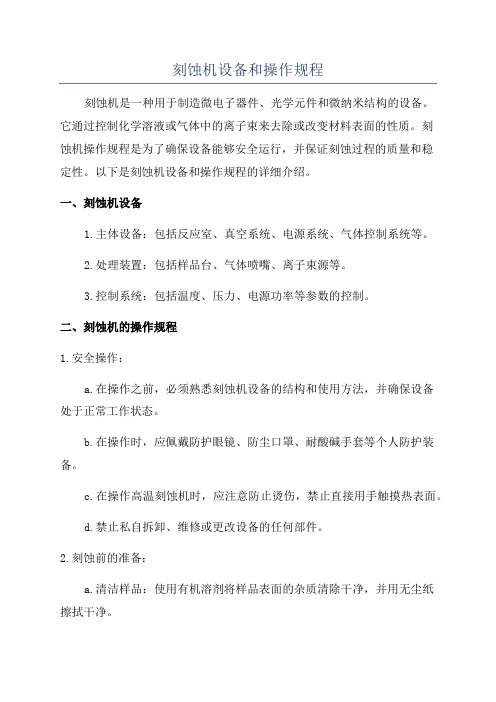
刻蚀机设备和操作规程刻蚀机是一种用于制造微电子器件、光学元件和微纳米结构的设备。
它通过控制化学溶液或气体中的离子束来去除或改变材料表面的性质。
刻蚀机操作规程是为了确保设备能够安全运行,并保证刻蚀过程的质量和稳定性。
以下是刻蚀机设备和操作规程的详细介绍。
一、刻蚀机设备1.主体设备:包括反应室、真空系统、电源系统、气体控制系统等。
2.处理装置:包括样品台、气体喷嘴、离子束源等。
3.控制系统:包括温度、压力、电源功率等参数的控制。
二、刻蚀机的操作规程1.安全操作:a.在操作之前,必须熟悉刻蚀机设备的结构和使用方法,并确保设备处于正常工作状态。
b.在操作时,应佩戴防护眼镜、防尘口罩、耐酸碱手套等个人防护装备。
c.在操作高温刻蚀机时,应注意防止烫伤,禁止直接用手触摸热表面。
d.禁止私自拆卸、维修或更改设备的任何部件。
2.刻蚀前的准备:a.清洁样品:使用有机溶剂将样品表面的杂质清除干净,并用无尘纸擦拭干净。
b.放置样品:将需要刻蚀的样品放置在样品台上,并确保其稳定性。
c.设置参数:根据刻蚀材料和刻蚀深度的要求,设置刻蚀机的参数,如气体种类、气流速度、刻蚀时间等。
d.检查真空度:确保真空系统工作正常,并进行真空泄漏测试。
3.刻蚀操作:a.打开设备开关,开始抽真空。
b.打开气体进气阀门,将预定混合气体引入反应室。
c.设置离子束源的功率、倾角和扫描速度等参数。
d.按下启动按钮,开始刻蚀过程。
e.刻蚀过程结束后,将刻蚀样品取出,并进行后续处理。
4.刻蚀后的清洁:a.刻蚀后,将样品放入有机溶剂中清洗,去除刻蚀产物。
b.将清洗后的样品用纯净水冲洗,并用氮气将其风干。
5.定期维护:a.定期对设备进行维护,检查传动系统、真空系统和电源系统等。
b.柜后对设备进行清洁,清除积尘和杂质。
总结:刻蚀机设备和操作规程是确保刻蚀过程安全和高效的重要保证。
在进行刻蚀操作之前,必须进行充分的准备工作,包括清洁样品、设置参数等。
在刻蚀过程中,要严格遵守安全操作规程,并确保设备处于正常工作状态。
蚀刻技术及工艺分析..

定蚀刻液的再生与更新。
11
蚀刻常用介质
NaOH:是一种常见的重要强碱。固体又被称为烧
碱、火碱、片碱、苛性钠等,是一种白色固体,有 强烈的腐蚀性,在空气中易潮解,且与空气中CO2 二氧化碳起反应(因此要密封存放);除溶于水之 外,氢氧化钠还易溶于乙醇、甘油;但不溶于乙醚、 丙酮、液氨。其液体是一种无色,有涩味和滑腻感 的液体。
滚膜、烘干: A:滚膜机滚轮的压力; B:滚轮速度; C:滚膜膜厚; D:烘干程度; E:油墨的纯净度;
20
蚀刻特点
★ 改变了机械加工金属零件方式; ★ 可对大到传统行业设备使用的大面积微孔滤网, 小到眼睛几乎很难以分辨的细微零件进行加工;
★ 生产过程无外力冲击、不变形、平整度好;生 产周期短、应变快、不需模具的设计、制造;产 品无毛刺、无凸起、两面一样光、一样平;
★ 按图红加工平面凹凸型的金属材料制品,如:文 字、数字及复杂图型、图案。制造各种精密的,任 意形状的通孔零件。
12
来料前处理 烘干 涂膜 烘烤 曝光 显影 全检补漆 蚀刻 脱膜 全检包装
13
蚀刻工艺改进
蚀刻设备的改进, 主要体现:
1.在传送方式、喷淋方式, 目的是提高生产效率、 蚀刻速度和蚀刻均匀性。
2. 喷淋杆或喷嘴的移动为了使溶液能全面地喷淋 到板子表面每个部位, 并促使板面溶液加快流动, 是移 动喷淋杆或喷嘴。 目前的水平传送喷淋式蚀刻设备 的喷嘴与喷淋杆摆动的结构有多样不同。使得喷淋溶 液不固定于一个位置, 就让喷嘴摆动。摆动方式有的 是转动喷管摇摆喷嘴角度, 有的是平移喷管移动喷嘴 位置, 也有水平旋转喷管而使喷嘴旋转喷液。喷嘴摆 动方式不同, 目的是为提高蚀刻均匀性。
刻蚀设备与工艺介绍

刻蚀设备与工艺介绍刻蚀是一种重要的微纳加工技术,用于从薄膜或器件上去除材料以形成所需的图案和结构。
刻蚀可以用于制造各种微纳器件,如集成电路、光子学器件、传感器和微机电系统(MEMS)等。
在刻蚀过程中,通过控制刻蚀设备和工艺参数,可以实现所需的刻蚀深度、尺寸和形状。
刻蚀设备通常包括刻蚀机、刻蚀槽和辅助设备。
刻蚀机是刻蚀的核心设备,主要包括物理刻蚀机和化学刻蚀机。
物理刻蚀机主要通过物理方法,如离子轰击、物理挥发和物理溅射等,去除材料。
常见的物理刻蚀机有反应离子刻蚀(RIE)机、平行板刻蚀机和电子束刻蚀机等。
化学刻蚀机通过化学反应去除材料,常见的化学刻蚀机有浸没式刻蚀机和喷雾式刻蚀机等。
辅助设备包括真空系统、气体供给系统、温控系统和控制系统等,用于提供所需的刻蚀环境和参数控制。
刻蚀工艺是刻蚀的关键,它决定了刻蚀速率、选择比和表面质量等。
常见的刻蚀工艺包括湿刻蚀、干刻蚀和等离子体刻蚀等。
湿刻蚀是一种在液体介质下进行的刻蚀工艺,常用的刻蚀液有酸、碱和溶剂等。
湿刻蚀可以实现高选择性和较大的刻蚀深度,但其刻蚀速率较慢且难以控制。
干刻蚀是一种在气体介质中进行的刻蚀工艺,常用的气体有氧气、氮气和氟化物等。
干刻蚀速率较快且易于控制,但选择比较低且表面质量较差。
等离子体刻蚀是一种在等离子体条件下进行的刻蚀工艺,通过将气体电离产生等离子体,利用等离子体的化学反应和物理效应实现刻蚀。
等离子体刻蚀具有高选择性、较大的刻蚀速率和良好的表面质量,广泛应用于集成电路和光子学器件等领域。
刻蚀工艺的参数对刻蚀结果有重要影响,包括刻蚀气体、功率、压力、温度和刻蚀时间等。
不同的刻蚀工艺需要不同的参数组合,需要通过实验和优化来确定最佳参数。
刻蚀设备和工艺在微纳加工中起着至关重要的作用,它们决定了刻蚀的效率和质量。
随着微纳加工技术的不断发展,刻蚀设备和工艺将进一步提高,以适应更多元化的应用需求。
DryEtch工艺及设备介绍

• Dry Strip 反应气体(SF6/NF3) :
SF6/NF3
CxHy (PR胶) + O2 -----> COx↑ + H2O↑
Active GI
Active GI
1.2 Dry Etch 工艺介绍
2.5 温控系统
Chiller (Heater Exchanger)
Pt Sensor (热电偶):温度测量
Chiller Chiller Hose Connector
2.5 温控系统
TC & BC:
Plasma Connection
Glass
---------
+++++++ --------
+++++++
• Ashing 反应气体(SF6/NF3) :
SF6/NF3
CxHy (PR胶) + O2 -----> COx↑ + H2O↑
Active GI
Active GI
1.2 Dry Etch 工艺介绍
• N+ Etch & Dry Strip
N+ Etch:针对TFT Channel 区域a-Si进行反应,生产挥发性气体的过程。 Dry Strip:针对N+ Etch后Glass表面PR胶进行反应,生成挥发性气体的过程。
• Ash/Act or Act/Ash
Active Etch:针对Pixel 区域a-Si进行反应,生产挥发性气体的过程。 Ashing:针对TFT Channel区域PR胶进行反应,生成挥发性气体的过程。
刻蚀工艺介绍

刻蚀前后对比照片
Metal刻蚀前后:
ITO刻蚀前后:
主要工艺参数
1 刻蚀液浓度 刻蚀液的浓度对刻蚀效果影响较大,所以 我们主要通过:来料检验、首片确认、定 期更换的方法来保证。 温度越高刻蚀效率越高,但是温度过高工 艺方面波动较大,只要通过设备自带温控 器和点检确认。 刻蚀流片的速度与刻蚀速率密切相关 喷淋流量的大小决定了基板表面药液置换 速度的快慢,流量控制可保证基板表面药 液浓度均匀。 过刻量即测蚀量,适当增加测试量可有效 控制刻蚀中的点状不良
辛小刚
刻蚀原理刻蚀不良原因分析
刻蚀原理介绍
刻蚀是用一定比例的酸液把玻璃上未受光刻胶保护的 Metal/ITO膜通过化学反应去除掉 膜通过化学反应去除掉, Metal/ITO膜通过化学反应去除掉,最终形成制程所需 要的图形。 要的图形。
刻蚀种类
目前我司的刻蚀种类主要分两种: 1、Metal刻蚀 刻蚀液主要成分:磷酸、硝酸、醋酸、水。 Metal:合金金属 2、ITO刻蚀 刻蚀液主要成分:盐酸、硝酸、水。 ITO:氧化铟锡(混合物)
刻蚀原理介绍主要工艺参数刻蚀液更换频率的管控刻蚀不良的产生原因单击此处编辑母版标题样式单击此处编辑母版标题样式刻蚀工艺介绍辛小刚刻蚀原理介绍刻蚀主要工艺参数刻蚀液更换频率的管控刻蚀不良原因分析刻蚀是用一定比例的酸液把玻璃上未受光刻胶保护的metalito膜通过化学反应去除掉最终形成制程所需要的图形
刻蚀工艺介绍
2
刻蚀温度
3
刻蚀速度
4
喷淋流量
5
过刻量
刻蚀液更换频率的管控
作业数量管控: 作业数量管控: 每天对生产数量及时记录,达到规定作业片数 及时更换。 作业时间管控: 作业时间管控: 由于药液的挥发,所以如果在规定更换时间未 达到相应的生产片数药液也需更换。 首片和抽检管控: 首片和抽检管控: 作业时需先进行首片确认,且在作业过程中每 批次进行抽检(时间间隔约25min)。
晶圆刻蚀设备的制作方法
晶圆刻蚀设备的制作方法晶圆刻蚀设备是半导体制造过程中必需的一种设备,它可以将晶圆表面的材料刻蚀掉,从而制造出半导体器件。
晶圆刻蚀设备采用了化学反应的原理,在高温高压的环境下进行刻蚀处理。
下面我们将介绍晶圆刻蚀设备的制作方法。
一、设备的外部结构晶圆刻蚀设备的外部是由钢架、玻璃门、观察窗、电子控制屏幕和排风管道组成的,比较简单,可以按照图纸进行制作。
二、设备的内部结构晶圆刻蚀设备的内部结构较为复杂,主要由反应室、氟化氢发生器、气体控制系统、氦气贮存罐、温度控制系统、泵及阀门组成。
1、反应室反应室是晶圆刻蚀设备最重要的部分,它采用了三角形的构造,选择这样的构造是为了更好地利用化学反应进行刻蚀处理。
反应室的材质一般采用聚四氟乙烯(PTFE)或石英玻璃制成。
反应室中间有一个钨丝加热器,可以调节温度。
2、氟化氢发生器氟化氢发生器是晶圆刻蚀设备的核心部分之一,主要负责产生氟化氢气体,氟化氢通过管道送入反应室,与晶圆表面的材料发生化学反应从而进行刻蚀。
氟化氢发生器采用了电石灰法产生氢氟酸的方式来制造氟化氢。
3、气体控制系统气体控制系统包括了气缸、气体流量计、阀门和电磁阀等组成,主要负责将氟化氢、氢气、氦气等气体送入反应室,并控制其流量。
4、氦气贮存罐氦气贮存罐主要用于贮存氦气,并在反应室中起到冷却作用。
氦气可以有效地降低反应室内的温度,从而提高反应的效果。
5、温度控制系统温度控制系统主要用于控制反应室的温度,调节反应的速率。
反应室内的温度可以通过钨丝加热器来调节。
6、泵及阀门泵及阀门主要负责将残余的气体、液体和固体物质排出,从而避免对设备和操作者的危害。
以上就是晶圆刻蚀设备的制作方法,相信大家看完后对晶圆刻蚀设备的制作有了一定的了解。
三、设备的工作原理晶圆刻蚀设备的工作原理是将氟化氢和晶圆表面材料进行化学反应,从而使晶圆表面的材料被刻蚀掉。
氟化氢和晶圆表面的材料反应后,会生成气体或固体物质,这些物质需要通过泵和阀门流出反应室,以避免对设备和操作者的危害。
半导体微细加工中的刻蚀设备及工艺
( 圳 深爱 半 导体 有 限公 司 ,广 东 深 圳 582 ) 深 109 摘 要 :与传 统 湿法 腐 蚀 比较 ,干 法 刻 蚀 具 有各 向异 性 、对 不 同材 料 选择 比 差 别较 大 、均 匀性 与 重 复 性好 、 易 于 实现 自动连 续生 产 等优 点 。 目前 ,刻 蚀技 术 已经 成 为 集成 电路 生产 中的 标 准技 术 ,干 法刻 蚀 设 备 亦成 为 关键 设备 。本 文对 半 导 体 生 产 中刻蚀 的原 理 、分 类 ,结 合 生 产 实际对
刻蚀工艺进行 了较 系统 的论述 ,并介 绍 了随着硅 片尺 寸的增 大,工艺线条进入 亚微 米级 时代 ,
相应 刻 蚀设 备 的发展 趋势 。
关键 词 :刻 蚀 设备 ;刻蚀 工 艺 ;半导 体 ;集 成 电路 ;亚微 米
中 图分类 号 :T 3 5 文献 标识 码 :A 文 章编 号 :17.7 6 (02 0 4 .4 N0 6 1 7 20 )1-0 10 4 1 Applc to a d v l p e f e c e ui m e t a ia i n n de e o m nt o t h q p n nd pr c s n e io o e s i s m c ndu t upe fne lne m a f c urng c or s r i i nu a 刻 蚀分 为湿 法 刻蚀 和 干法 刻蚀 两类 。湿法 刻 蚀
是将硅 片浸泡在 可与被刻蚀薄膜进 行反应 的溶 液 中,用化学方法除去不要部分的薄膜。早期制造业
以湿 法 为主 。 当半 导体 制造 业进 入 微米 、亚微 米 时
方面 ,要求高度 的各 向异性 以得到刻蚀 图形垂直
维普资讯
dse刻蚀设备原理
dse刻蚀设备原理
DSE刻蚀设备原理。
DSE(Deep Silicon Etching,深硅刻蚀)是一种常用于半导体
加工中的刻蚀工艺。
DSE刻蚀设备是用于在硅片上进行深刻蚀的设备,其原理基于化学刻蚀和物理刻蚀相结合的技术。
DSE刻蚀设备的原理主要包括两个步骤,首先是利用化学刻蚀
剂对硅片表面进行化学反应,然后利用物理刻蚀手段去除已被化学
反应改变的硅材料。
在DSE刻蚀设备中,通常采用的化学刻蚀剂是氢氟酸(HF)和
过氧化氢(H2O2)。
HF能够与硅表面发生化学反应,生成氟化硅,
而H2O2则能够提供氧气,促进反应进行。
这样就能够在硅表面产生
氟化硅膜,从而实现对硅的化学刻蚀。
接下来,利用物理刻蚀手段,如离子束刻蚀或等离子刻蚀,去
除已被氟化的硅材料。
这样就能够在硅片上形成所需的深刻蚀结构。
DSE刻蚀设备的原理结合了化学刻蚀和物理刻蚀的优势,能够
实现对硅材料的高效深刻蚀,广泛应用于半导体器件制造、MEMS (Micro-Electro-Mechanical Systems,微机电系统)制造等领域。
总的来说,DSE刻蚀设备的原理是利用化学刻蚀和物理刻蚀相
结合的技术,通过化学反应和物理去除的方式实现对硅材料的深刻蚀,为半导体加工和微纳加工提供了重要的工艺手段。
等离子体刻蚀工艺及设备
等离子体刻蚀工艺及设备
等离子体刻蚀工艺及设备是一种重要的微加工技术,广泛应用于半导体、光电子、MEMS等领域。
该技术利用等离子体对材料进行刻蚀,能够实现高精度、高效率的微米级加工,对于制备微电子器件和微系统具有重要的意义。
等离子体刻蚀工艺的基本原理是利用高频电场在真空中产生等
离子体,将等离子体束聚焦到加工对象表面,利用化学反应或物理撞击的方式将表面材料剥离或刻蚀。
该技术具有非接触、无损伤、高精度等特点,能够加工出各种形状和尺寸的微结构。
等离子体刻蚀设备由真空系统、高频电源、气体供给系统、加工室、聚焦系统等组成。
真空系统用于维持反应室内气体压力低于1 Pa,高频电源产生高频电场,气体供给系统提供刻蚀气体,加工室是等离子体刻蚀的主要区域,聚焦系统用于聚焦等离子体束。
在等离子体刻蚀过程中,刻蚀气体的选择和气体流量对加工效果影响较大。
常用的刻蚀气体有CF4、SF6、Ar等,不同的刻蚀气体能够实现不同的加工效果。
气体流量的调节能够控制刻蚀速率和刻蚀质量,流量过大或过小都会对加工效果产生不良影响。
等离子体刻蚀工艺和设备的发展促进了微电子器件和微系统制
备的进一步发展,未来该技术还将在纳米加工、生物医学等领域展现出更广阔的应用前景。
- 1 -。
- 1、下载文档前请自行甄别文档内容的完整性,平台不提供额外的编辑、内容补充、找答案等附加服务。
- 2、"仅部分预览"的文档,不可在线预览部分如存在完整性等问题,可反馈申请退款(可完整预览的文档不适用该条件!)。
- 3、如文档侵犯您的权益,请联系客服反馈,我们会尽快为您处理(人工客服工作时间:9:00-18:30)。
刻蚀设备与工艺介绍
刻蚀是微纳加工技术中一种常用的工艺步骤,用于在材料表面刻出所
需要的图案或结构。
刻蚀设备主要包括刻蚀机和刻蚀液。
刻蚀机根据刻蚀
的方式不同,可以分为湿法刻蚀机和干法刻蚀机两种。
湿法刻蚀机是基于液相刻蚀原理的设备,主要由液槽、温度控制系统、气泡生成系统、排液系统和控制系统等组成。
其工作原理是将刻蚀液倒入
液槽中,通过加热和搅拌使刻蚀液保持一定的温度和均匀度。
在刻蚀过程中,将待刻蚀的工件放入刻蚀槽中,通过控制刻蚀液的pH值、浓度和刻
蚀时间等参数,实现对工件表面的刻蚀。
干法刻蚀机是通过物理或化学方式对工件表面进行刻蚀的设备。
常用
的干法刻蚀方法包括离子束刻蚀、等离子体刻蚀和反应离子束刻蚀等。
离
子束刻蚀是利用高速离子束的动能击打工件表面,使其表面原子脱落从而
达到刻蚀的目的。
等离子体刻蚀是通过等离子体中的化学反应,使工件表
面发生化学变化,实现刻蚀效果。
反应离子束刻蚀是在离子束中加入反应
气体,使其与工件表面反应,达到刻蚀的目的。
刻蚀液是刻蚀过程中用于腐蚀材料的溶液,根据刻蚀的目的和要求可
以选择不同的刻蚀液。
常用的刻蚀液包括湿式刻蚀液和干式刻蚀液。
湿式
刻蚀液主要是盐酸(HCl)、氟酸(HF)和硝酸(HNO3)等,适用于大多数材料
的刻蚀。
干式刻蚀液主要是气体,如氧气(O2)、氟气(F2)和氯气(Cl2)等,适用于特定材料的刻蚀,如金属和硅。
刻蚀技术在微纳加工中起到了至关重要的作用。
它可以实现微纳器件
的精确加工和制造,如半导体芯片、光电元件和微机电系统等。
刻蚀技术
的精度和效率对于微纳加工的成果和应用具有重要影响,因此需要不断改进和优化。
总结而言,刻蚀设备是微纳加工中一个重要的工艺步骤,包括湿法刻蚀机和干法刻蚀机两种。
刻蚀液根据刻蚀的需求可以选择不同的刻蚀液。
刻蚀技术在微纳加工中具有重要的应用价值,对于制造微纳器件起到了关键作用。