14孔的常规加工方法
孔加工方法及实例
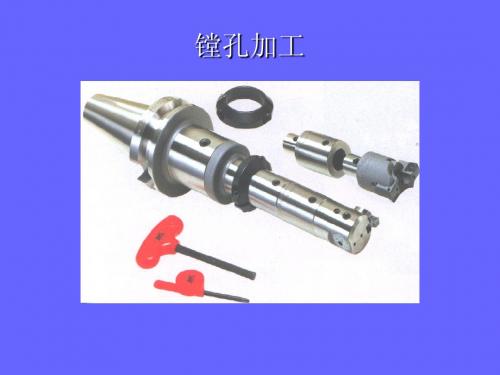
加工精度高(形位精度好)
加工效率高(切削速度高, 不同材质对应不同刀片) 柔性好(直径可调) 加工范围宽:Φ1-880mm 成本低(刀片可换)
孔加工案例一
用户: 工件: 材质: 硬度: 孔径: 粗糙度: 柳工箱体厂 箱体 球墨铸铁 HB190 Φ25 0+0.021 Ra1.6
位置精度: ±0.01 机床: 牧野加工中心
前后刃高度差:0.4mm 原工艺:铣刀铣削,铣刀刃磨困难, 效率低 镗削效果:一次完成,效率高,换 刀片成本低
段差加工
反镗加工
用户:北京机床所
工件:机床立柱 材质:HT200 孔径:Φ80mm 镗刀组合:BT50-CK6-300 镗头:EWN68-150CKB6 刀片:TCGT110204FN(H1)
精镗: 刀柄BT50-CK6-300
减径器:CK63-80 粗镗头 TWN32-51CKB3 刀片座:TW3242A 刀片: SCMM090308EFM(AC700G) 精镗: 刀柄BT50-CK6-300 减径器:CK63-80 精镗头 EWN32-60 刀片TPGD080204FN(H1ZX)
非标镗刀
切削速度: V= 80m/min 工序三 精镗达要求 刀柄: BT50-CK1-135
精镗头:EWN20-36CKB1 S=1020rpm 进给量:F=0.06mm/rev
刀片:
TPGD080204FN
切削速度: V= 80m/min
深孔加工案例
用户:浙江凯达机床 工件:数控车床传动箱
材质:HT250
精镗: 刀柄BT50-CK7-360 法兰座 FL135/90 精镗头 EWN150 平衡块 BWN150-200 滑架 SL150-200
CA6140说明书

前言机械制造技术基础课程设计是我们在学完了大学的全部基础课,专业基础课以及专业课后进行的。
这是我们在进行毕业设计之前对所学的各科课程一次深入的综合性总复习,也是一次理论联系实际的训练。
因此,他在我们的大学三年生活中占有重要的地位。
机械加工工艺规程是规定产品或零部件机械加工工艺过程和操作方法等的工艺文件。
对加工工艺规程的设计,可以了解了加工工艺对生产、工艺水平有着极其重要的影响。
生产规模的大小、工艺水平的高低以及解决各种工艺问题的方法和手段都要通过机械加工工艺来体现。
对专用夹具的设计,可以了解机床夹具在切削加工中的作用:可靠地保证工件的加工精度,提高加工效率,减轻劳动强度,充分发挥和扩大机床的给以性能。
本夹具设计可以反应夹具设计时应注意的问题,如定位精度、夹紧方式、夹具结构的刚度和强度、结构工艺性等问题。
就我个人而言,我希望通过这次课程设计对自己未来将从事的工作进一步适应性的训练,希望自己在设计中能锻炼自己的分析问题、解决问题、查资料的能力,为以后的工作打下良好的基础。
由于能力有限,设计尚有很多不足之处,希望各位老师给予指导。
目录1、杠杆加工工艺规程设计............................................................................................................ - 3 -1.1零件的分析....................................................................................................................... - 3 -2、选择毛坯,确定毛坯尺寸,设计毛坯图 ........................................................................ - 4 -2.1确定毛坯的制造形式....................................................................................................... - 4 -2.2确定机械加工余量,毛坯尺寸和公差 ........................................................................... - 4 -3.1基面的选择....................................................................................................................... - 5 -4、机械加工余量、工序尺寸及毛坯尺寸的确定 ........................................................................ - 7 -5、确定切削用量............................................................................................................................ - 7 -6、确定基本工时.......................................................................................................................... - 17 -7、工艺卡片.................................................................................................................................. - 22 -8、专用夹具设计.......................................................................................................................... - 22 -8.1加工工艺孔Φ25夹具设计............................................................................................ - 22 -8.2小结................................................................................................................................. - 26 - 总结................................................................................................................................................ - 27 - 参考文献........................................................................................................................................ - 28 - 致谢.............................................................................................................................................. - 30 -1、杠杆加工工艺规程设计1.1零件的分析1.1.1零件的作用题目所给的零件是CA6140车床的杠杆。
常规夹片和锚板加工工艺及质量控制介绍

三、夹片质量确认站
• • • • 建立边界样本。 标准化作业规程。 预防机制。 过程质量控制。
四、锚板工艺技术参数
• 现有生产能力300万孔/月,其中挤压锚板60万孔/ 月,精铰240万孔/月。 • 锚板使用材料为45#钢或40Cr。 • 锚板热处理20~32HRC。 • 热处理锚板(1~14孔)硬度采用洛氏硬度计 • 热处理锚板(15~55孔)硬度采用布氏硬度计。
理化室化学成份分析
一、夹片生产工艺与检验流程
• 材料进场→(原材料成份及尺寸检验 )→挤压→ 铰孔→车(以车代磨)→攻牙→锯→(外形尺寸 与牙形检验) →热处理→滚砂→(硬度检验) → 包装 • 在一台专用车床上实现了车外锥、磨外锥、车内 锥三道工序合为一道加工出来,极大的简化了工 艺,缩短生产周期,可获得较好的经济效益。 • 夹片车间主要设备有:a.以车代磨数控车床,b. 磨床,c.车内锥数控车床,d.攻丝机,e.锯床,f. 压字机,g.制作工装的设备及磨刀设备等。
三、夹片机加工车间
三、夹片质量确认站
1 质量确认站建立 1、 为了及时的反馈、处理、跟踪质量问题,分析、公布质量信息, 建立质量确认站。 2、 每日质量例会制度,由站长主持,检验员、工艺所技术人员、 分厂领导、车间主任、班长参加,及时反馈、解决质量问题。
确认站开站仪式早会质量异常分析三、夹片 Nhomakorabea量确认站
三、夹片检验设备
• 渗层厚度检验与金相分析
测夹片长度
三、夹片质量确认站
3 质量异常问题处理流程2项
为保证质量异常的有序、及时、高效处理,建立 了质量反馈处理制流程。
三、夹片质量确认站
4 质量跟踪机制3项
1、变化关注控制点: 为避免因人、机、料、法、测等方面的变化引起
热加工工艺基础第四章 孔加工
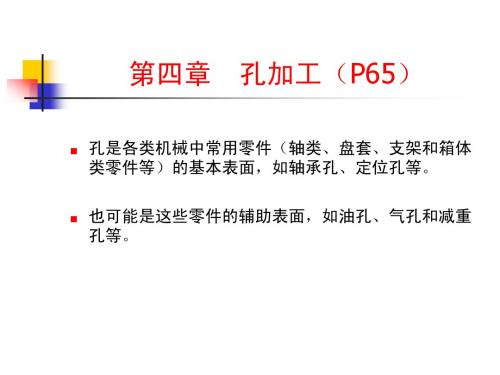
钻孔最常用的刀具是麻花钻头(视频)。
一、钻床加工简介(P66)
钻床主要用于加工中小型的孔。钻床上钻削时, 刀具旋转为主运动,同时刀具沿直线进行进给运动; 在车床上钻孔时,工件旋转,刀具进给。 钻孔简介 1)台式钻床:加工小型工件,一般孔径<13mm。 2)立式钻床:加工中小型工件,一般孔径<50mm,可自 动走刀。 3)摇臂钻床:如图13-25所示,结构完善,操作方便。 加工大中型工件,一般孔径<80mm。
1、镗孔的方法和刀具(P70)
1)在车床上镗孔:如P71图4-12所示;主运动为工件的旋 转、进给运动为镗刀装在小刀架上作纵向或横向的移 动。适合车回转体的轴心孔。
2)在镗床上镗孔:如P71图4-13和图4-14所示: 主运动— 镗刀刀杆装在机床主轴锥孔中,随主轴一起 旋转; 进给运动—工作台带动工件作纵向移动,也可以由主 轴带动镗刀作轴向移动来实现。
2、选用孔加工方案的几点说明(P79)
(2)淬火钢件:淬火之前,一般采用钻和镗,淬火之后只 能磨削。其加工方案为钻 镗 (淬火) 磨。
3)精度为IT7以上,Ra值为0.4以下的孔,在精加工以后 应进行光整加工,除短孔外,一般采用珩磨。 4)对于有色金属,不能采用磨削加工,其精加工常采用 精镗、精细镗、精铰或手铰方案。
第四章 孔加工(P65)
孔是各类机械中常用零件(轴类、盘套、支架和箱体 类零件等)的基本表面,如轴承孔、定位孔等。 也可能是这些零件的辅助表面,如油孔、气孔和减重 孔等。
§4-1
概述
一、孔的技术要求(P65)
1、尺寸精度:孔径大小和深度;
2、形状精度:孔的圆度、圆柱度及轴线的直线度; 3、位置精度:孔与孔、孔与外圆表面的同轴度;孔与孔、 孔与其它表面的平行度; 4、表面质量:表面粗糙度、表层的加工硬化和组织变化 等。
拨叉零件加工完成图所示拨叉零件加工

拨叉零件加工完成图所示拨叉零件加工。
图1拨叉一、分析零件工艺结构性;CA6140车床的拨叉。
它位于车床变速机构中,主要起换档,使主轴回转运动按照工作者的要求工作,获得所需的速度和扭矩的作用。
通过上方的力拨动下方的齿轮变速。
两件零件铸为一体,加工时分开。
(1)以φ14为中心的加工表面这一组加工表面包括:φ14的孔,以及其上下端面,上端面与孔有位置要求(2)以φ40为中心的加工表面这一组加工表面包括:φ40的孔,以及其上下两个端面。
这两组表面有一定的位置度要求,即φ40的孔上下两个端面与φ14的孔有垂直度要求。
由上面分析可知,加工时应先加工一组表面,再以这组加工后表面为基准加工另外一组。
二、选用毛坯或明确来料状况;零件材料为ZG45。
考虑零件在机床运行过程中所受冲击不大,零件结构又比较简单,故选择铸件毛坯。
有的采用HT200三、基面的选择基面选择是工艺规程设计中的重要工作之一。
基面选择得正确与合理可以使加工质量得到保证,生产率得以提高。
否则,加工工艺过程中回问题百出,更有甚者,还会造成零件的大批报废,是生产无法正常进行。
(1)粗基准的选择。
对于零件而言,尽可能选择不加工表面为粗基准。
而对有若干个不加工表面的工件,则应以与加工表面要求相对位置精度较高的不加工表面作粗基准。
根据这个基准选择原则,现选取φ14孔的不加工外轮廓表面作为粗基准,利用一组共两块V形块支承这两个φ25作主要定位面,限制5个自由度,再以一个销钉限制最后1个自由度,达到完全定位,然后进行铣削(2)精基准的叉零件加工完成图所示拨叉零件加工。
图1拨叉一、分析零件工艺结构性;CA6140车床的拨叉。
它位于车床变速机构中,主要起换档,使主轴回转运动按照工作者的要求工作,获得所需的速度和扭矩的作用。
通过上方的力拨动下方的齿轮变速。
两件零件铸为一体,加工时分开。
(1)以φ14为中心的加工表面这一组加工表面包括:φ14的孔,以及其上下端面,上端面与孔有位置要求(2)以φ40为中心的加工表面这一组加工表面包括:φ40的孔,以及其上下两个端面。
14孔的常规加工方法
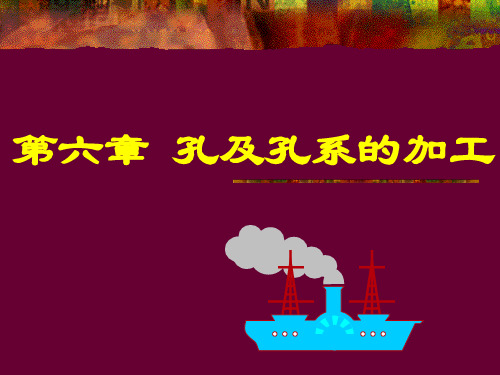
钻头 切削 部分
5个刀刃
两条主切削刃 两条副切削刃 一条横刃
6个刀面
两个螺旋形前刀面 两个经刃磨获得的后刀面 两个圆弧段的副后刀面
一、钻孔
3. 钻削用量 1) 背吃刀量asp
单位: mm
asp do
一、钻孔
3. 钻削用量 2)钻削速度vc
单位: m/min
vc do n 1000
一、钻孔
二、扩孔 2.扩孔钻的结构
图6-10 1) 齿数多(3.4齿); 2)不存在横刃; 3)切削余量小, 排屑容易。。
扩孔钻
三、铰孔 1.铰刀的类型
直柄机用铰刀 锥柄机用铰刀 硬质合金锥柄机用铰刀
手用铰刀
可调节手用铰刀 图6-14 铰刀的类型
套式机用铰刀
直柄莫氏圆锥铰刀 手用1: 50 锥度铰刀
三、铰孔 2.铰削过程的实质
1) 内圆磨削的表面较外圆磨削的粗糙。 2) 生产率较低。 3) 磨削接触区面积较大,砂轮易堵塞,散热和切削液
冲刷困难。
因此内孔磨削一般仅适用于淬硬工件的精加工, 在单件、小批生产中和在大批大量生产中都有应用。
七、高精度孔的珩磨
1.珩磨头及珩磨原理
图6-22)加工精度可达为IT7~IT6; 3)孔的表面粗糙度可控制在Ra6.3 ~
0.8μm。 4)能修正前工序造成的孔轴线的弯曲、
偏斜等形状位置误差;
四、镗孔
2.镗刀结构
五、拉孔
1.拉削过程
五、拉孔
1.拉削过程
图6-27 拉削圆孔
五、拉孔
1.拉削过程
图6-26 拉削键槽
五、拉孔
1.拉削过程
六、内圆磨削
六、内圆磨削
1. 工艺特点 1)磨削是零件精加工的主要方法之一; 2)对长径比小的, 内孔磨削的经济精度可达IT5~
花键套零件的机械加工工艺规程及工序的设计计算
课程设计学院:机械工程学院班级:数控1311班学号:设计地点(单位): 2教学楼设计题目:花键套的工艺设计完成日期:2015 年 5 月 29日机械学院课程设计任务书设计题目:花键套零件的机械加工工艺规程及工序的设计计算教研室主任:贾伟杰指导教师:韩健2013年 6月 8日目录1 零件的分析 .......................................... 错误!未定义书签。
零件的工艺分析 ..................................... 错误!未定义书签。
花键套的技术要求 ................................... 错误!未定义书签。
2 毛坯的选择 .......................................... 错误!未定义书签。
毛坯种类的选择 .................................... 错误!未定义书签。
毛坯制造方法的选择 ................................. 错误!未定义书签。
毛坯形状及尺寸的确定 ............................... 错误!未定义书签。
3 工艺路线的拟定 ...................................... 错误!未定义书签。
定位基准的选择 .................................... 错误!未定义书签。
零件表面加工方案的选择 ............................ 错误!未定义书签。
加工阶段的划分 .................................... 错误!未定义书签。
工序顺序的安排 .................................... 错误!未定义书签。
机械加工顺序 .................................... 错误!未定义书签。
7、孔加工
对于直径小于φ30mm无底孔的孔加工,通常采用 锪平端面——打中心孔——钻——扩——孔口倒角——铰加工方案, 对有同轴度要求的小孔,需采用锪平端面——打中心孔——钻——半 精镗——孔口倒角——精镗(或铰)加工方案。
二、孔加工方法的选择原则
内孔表面加工方法选择实例:
Φ40H7内孔可选择钻孔—粗镗(或扩孔)—半精镗—精镗方 案。阶梯孔Φ 13和Φ 22没有尺寸公差要求,因而可选择钻孔—锪 孔方案。
③ 孔加工:以切削进给的方式执行孔加工的动作。
④ 在孔底的动作:包括暂停、主轴准停、刀具位移 等动作。 ⑤ 返回到R点:继续孔的加工而又可以安全移动刀
具时选择R点。
⑥ 返回到初始点:孔加工完成后一般应选择初始点
四、固定循环功能
表1
2、固定循环的代码组成
① 固定循环平面 初始平面 初始平面是为了安全下刀而规定的一个平 面。初始平面到零件表面的距离可以任意设定在一个 安全的高度上 R点平面 R点平面又叫R参考平面,这个平面是刀具 下刀时自快进转为工进的高度平面。距工件表面的距 离主要考虑工件表面尺寸的变化,一般可取2~5mm。 孔底平面 加工盲孔时孔底平面就是孔底的Z轴高度, 加工通孔时一般刀具还要伸出工件底平面一段距离, 主要是保证全部孔深都加工到尺寸,钻削加工时还应 考虑钻头钻尖对孔深的影响。
60 80
40
25
3)高速深孔往复排屑循环G73 指令格式:G73
X_ Y_ Z_ R_ Q_ F_ ;
功能:该循环用于深孔加工。 孔加工动作如图所示,钻头先快速定位至X、Y所指定的坐标 位置,再快速定位至R点,接着以F所指定的进给速度向下钻 削至Q所指定的距离(Q必须为正值,用增量值表示),再快 速回退d 距离(d 是CNC系统内部参数设定的)。依此方式 进刀若干个Q,最后一次进刀量为剩余量(小于或等于q), 到达Z所指的孔底位置。G73指令是在钻孔时间断进给,有利 于断屑、排屑,冷却、润滑效果佳。
端盖零件的机械加工工艺规程及Φ14孔工艺装备设计
襄樊学院机械制造技术课程设计题目:设计端盖的机械加工工艺规程院、系:襄樊学院机械工程系班级:机械1012班姓名:毕文浩学号:10316201指导教师:刘海生二零一三年六月三日摘要机械制造工艺学课程设计是我们学完了大学的全部基础课、技术基础课以及大部分专业课之后进行的.这是我们在进行毕业设计之前对所学各课程的一次深入的综合性的总复习,也是一次理论联系实际的训练,因此,它在我们四年的大学生活中占有重要的地位。
这次设计的是端盖,有零件图、毛坯图、装配图各一张,机械加工工艺过程卡片和与所设计夹具对应那道工序的工序卡片各一张。
首先我们要熟悉零件,题目所给的零件是端盖。
了解了端盖的作用,接下来根据零件的性质和零件图上各端面的粗糙度确定毛坯的尺寸和机械加工余量。
然后我们再根据定位基准先确定精基准,后确定粗基准,最后拟定端盖的工艺路线图,制定该工件的夹紧方案,画出夹具装配图。
端盖零件图 (1)一.端盖的分析1端盖的工艺分析及生产类型的确定 (4)1.1端盖的用途 (4)1.2端盖的技术要求: (5)1.3审查端盖的工艺性 (5)二. 端盖的工艺规程设计2.确定毛胚、绘制毛胚简图 (6)2.1选择毛胚 (6)2.2端盖铸造毛坯尺寸工差及加工余量 (6)2.3绘制端盖毛坯简图 (7)3.拟定端盖工艺路线 (7)3.1 定位基准的选择 (7)3.1.1精基准的选择 (7)3.2.2.粗基准的选择 (7)3.2表面加工方法的确定 (8)3.3加工阶段的划分 (8)3.4工序的集中与分散 (8)3.5工序顺序的安排 (8)3.6确定工艺路线 (9)4.加工余量、工序尺寸和工差的确定 (10)5.切削用量、时间定额的计算 (10)6时间定额的计算 (11)三.机床夹具的设计7.1提出问题 (13)7.2设计思想 (14)7.3夹具设计 (14)7.3.1、定位分析 (14)7.3.2切削力及夹紧力的计算 (15)7.3夹具操作说明 (15)7.4.确定导向装置 (16)8.参考文献 (16)端盖零件图1端盖的工艺分析及生产类型的确定1.1端盖的用途端盖主要用于零件的外部,起密封,阻挡灰尘的作用。
各公差等级对应的经济加工方法
粗刨(12~14);细插削;粗铣切(12~14),(11②);快速铣切(12~14);纵进刀半细车削(12~14);无钻模钻孔(12~14);扩孔(12~14);黑皮粗扩孔(12~15);半细镗孔(12~14);壳型铸造——黑色金属零件(12~14);冷冲裁冲切的平面零件的外形尺寸;砂轮切割(12~15)
7~8
金刚石精车削或金刚石精镗孔;金刚石细车、细镗(6~9);细铰,精铰(6~7)②;细拉削、精拉削;外圆细磨;平面细磨,精磨;细抛光(7~9);铰孔或铰孔后用滚珠或心轴定径加工;滚珠或滚柱滚压或扩径(6~9);细扩孔;细研磨;普通拉削;粗研磨;平面镗磨;预研磨和中研磨;阳极-机械粗磨削(6~9),细磨削;装饰电抛光(6~9);普通机电车削(6~9),机电细车削;机电刨削;冷冲裁——经修整和校准过的平面零件的外形尺寸
10
细扩孔(10~11);冷拉延——简单形状的空心零件外径(10~11)。也可参看9级标准公差(公差等级的可能变化范围)所采用的加工方法
11
细刨削(10~13),(10②);细铣削(10②);快速细铣削(11~13);横进刀细车削(11~13);快速车削;端面切割(11~13);钻模钻孔(11~13);粗刮削;阳极-机械普通切割毛坯(11~13),特种切割;板材电接触切割(11~13);熔模铸造黑色金属小零件(11~13);拉延模冷拉延——简单形状的空心零件拉深;平面零件落料。也可参看9级和10级标准公差(公差等级的可能变化范围)所采用的加工方法
8~9
9
精刨削(7②;8③);精铣切(7②);横进刀精车削(8~11);半细铰(9~10),铸铁半细铰(8);半细拉削;精刮;钳工锉(9~11);切割和铣切后砂布修整(9~11);外圆半细磨(8~11);钻削后用滚珠或心轴定径加工孔;冷拉延形——状简单的空心零件的高度尺寸(9~12);冷冲裁——修正过的平面零件的外形尺寸;未经校准的热体积模压。
- 1、下载文档前请自行甄别文档内容的完整性,平台不提供额外的编辑、内容补充、找答案等附加服务。
- 2、"仅部分预览"的文档,不可在线预览部分如存在完整性等问题,可反馈申请退款(可完整预览的文档不适用该条件!)。
- 3、如文档侵犯您的权益,请联系客服反馈,我们会尽快为您处理(人工客服工作时间:9:00-18:30)。
四、镗孔
2. 镗刀结构
五、拉孔
1. 拉削过程
五、拉孔
1. 拉削过程
图6-27 拉削圆孔
五、拉孔
1. 拉削过程
图6-26 拉削键槽
五、拉孔
1. 拉削过程
齿升量
2. 拉削工艺范围
图6-22 常见的拉削截形(A~G为内拉拉削,H~L为外拉削)
五、拉孔
3. 拉刀结构
图6-25
圆拉刀结构
五、拉孔
对于精度要求不高的孔,如螺栓的贯穿孔、 对于精度要求不高的孔,如螺栓的贯穿孔、 油孔以及螺纹底孔,可直接采用钻孔。 油孔以及螺纹底孔,可直接采用钻孔。
一、钻孔
2. 高速钢麻花钻的结构
一、钻孔
5个刀刃 个刀刃 钻头 切削 部分 6个刀面 个刀面
2. 高速钢麻花钻的结构
两条主切削刃 两条副切削刃 一条横刃 两个螺旋形前刀面 两个经刃磨获得的后刀面 两个圆弧段的副后刀面
六、内圆磨削
六、内圆磨削
1. 工艺特点 1)磨削是零件精加工的主要方法之一; 2)对长径比小的,内孔磨削的经济精度可达IT5~ IT6,表面粗糙度可控制到Ra0.8mm~Ra0.2mm; 3)可加工较硬的金属材料和非金属材料,如淬火钢、 硬质合金和陶瓷等。
六、内圆磨削
内圆磨削与外圆磨削相比,存在如下一些主要问题: 内圆磨削的表面较外圆磨削的粗糙。 1) 内圆磨削的表面较外圆磨削的粗糙。 生产率较低。 2) 生产率较低。 磨削接触区面积较大,砂轮易堵塞, 3) 磨削接触区面积较大,砂轮易堵塞,散热和切削液 冲刷困难。 冲刷困难。 因此内孔磨削一般仅适用于淬硬工件的精加工, 因此内孔磨削一般仅适用于淬硬工件的精加工, 在单件、小批生产中和在大批大量生产中都有应用。 在单件、小批生产中和在大批大量生产中都有应用。
பைடு நூலகம்
三、铰孔
4. 工艺特点 铰孔是孔的精加工方法; 1)铰孔是孔的精加工方法; 可加工精度为IT7 IT8、IT9的孔 IT7、 的孔; 2)可加工精度为IT7、IT8、IT9的孔; 孔的表面粗糙度可控制在Ra3.2 0.2μm; 3)孔的表面粗糙度可控制在Ra3.2 ~ 0.2μm; 铰刀是定尺寸刀具; 4)铰刀是定尺寸刀具; 切削液在铰削过程中起着重要的作用。 5)切削液在铰削过程中起着重要的作用。
三、铰孔
2.铰削过程的实质 2.铰削过程的实质
铰削过程不完全 是一个切削过程, 而是包括切削、刮 削、挤压、熨平和 摩擦等效应的一个 综合作用过程。 综合作用过程。
三、铰孔
3. 铰削用量 1)铰削余量 粗铰余量为0.10mm~ 0.10mm mm; 粗铰余量为0.10mm~0.35 mm; 精铰余量为0.04mm~0.06mm。 0.04mm 精铰余量为0.04mm~0.06mm。 2)切削速度和进给量 铰削速度为 1.5m/min ~ 5m/min; 1.5m/min m/min; 铰削钢件时, 0.3mm/r mm/r; 铰削钢件时,进给量为 0.3mm/r ~ 2mm/r; 铰削铸铁件时, 0.5mm/r mm/r。 铰削铸铁件时,进给量为 0.5mm/r ~ 3mm/r。
4. 工艺特点 拉削生产率高。 1) 拉削生产率高。 拉削精度高,质量稳定。拉削精度一般可达IT9 IT92) 拉削精度高,质量稳定。拉削精度一般可达IT9IT7级 1.6µ IT7级,表面粗糙度一般可控制到Ra1.6µm~ Ra0.8µm,拉削表面的形状、尺寸精度和表面质量 0.8µ 拉削表面的形状、 主要依靠拉刀设计、制造及正确使用保证。 主要依靠拉刀设计、制造及正确使用保证。 拉削成本低,经济效益高。 3) 拉削成本低,经济效益高。 拉刀是定尺寸、高精度、高生产率专用刀具, 4) 拉刀是定尺寸、高精度、高生产率专用刀具,制 造成本很高,所以,拉削加工只适用于批量生产, 造成本很高,所以,拉削加工只适用于批量生产, 最好是大批大量生产,一般不宜用于单件、 最好是大批大量生产,一般不宜用于单件、小批 生产。 生产。
二、扩孔
2. 扩孔钻的结构
图6-10 1) 齿数多(3、4齿); 齿数多( 、 齿 2)不存在横刃; )不存在横刃; 3)切削余量小,排屑容易。 )切削余量小,排屑容易。
扩孔钻
三、铰孔
1. 铰刀的类型
直柄机用铰刀 套式机用铰刀 锥柄机用铰刀 硬质合金锥柄机用铰刀 直柄莫氏圆锥铰刀
手用铰刀
手用1:50 锥度铰刀 可调节手用铰刀 图6-14 铰刀的类型
第六章 孔及孔系的加工
第二节 孔的常规加工方法
一、钻孔
钻头 钻套 钻模板
工件
一、钻孔
1. 工艺特点
1)钻孔是孔的粗加工方法; 钻孔是孔的粗加工方法; 可加工直径0.05 125mm的孔; 0.05~ mm的孔 2)可加工直径0.05~125mm的孔; 孔的尺寸精度在IT10以下; IT10以下 3)孔的尺寸精度在IT10以下; 孔的表面粗糙度一般只能控制在Ra12.5μm Ra12.5μm。 4)孔的表面粗糙度一般只能控制在Ra12.5μm。
三、铰孔
5. 铰刀的结构
图6-13
手铰刀结构
四、镗孔
1. 工艺特点
1)镗孔可不同孔径的孔进行粗、半精和精加工; 镗孔可不同孔径的孔进行粗、半精和精加工; 加工精度可达为IT7 IT6; IT7~ 2)加工精度可达为IT7~IT6; 孔的表面粗糙度可控制在Ra6.3 0.8μm。 3)孔的表面粗糙度可控制在Ra6.3 ~ 0.8μm。 能修正前工序造成的孔轴线的弯曲、 4)能修正前工序造成的孔轴线的弯曲、偏斜等形 状位置误差; 状位置误差;
二、扩孔
1. 工艺特点 扩孔是孔的半精加工方法; 1)扩孔是孔的半精加工方法; 一般加工精度为IT10 IT9; IT10~ 2)一般加工精度为IT10~IT9; 孔的表面粗糙度可控制在Ra6.3 3.2μm。 3)孔的表面粗糙度可控制在Ra6.3 ~ 3.2μm。 30mm 直径的孔时, mm直径的孔时 当钻削 dw>30mm 直径的孔时 , 为了减小钻削力 及扭矩,提高孔的质量,一般先用( 及扭矩,提高孔的质量,一般先用(0.5~0.7)dw 大小的钻头钻出底孔,再用扩孔钻进行扩孔, 大小的钻头钻出底孔,再用扩孔钻进行扩孔,则可 较好地保证孔的精度和控制表面粗糙度, 较好地保证孔的精度和控制表面粗糙度,且生产率 比直接用大钻头一次钻出时还要高。 比直接用大钻头一次钻出时还要高。
一、钻孔
3. 钻削用量 1) 背吃刀量asp 单位:mm 单位:
∑ asp = do
一、钻孔
3. 钻削用量 2)钻削速度vc 单位:m/min 单位:
vc =
π do n
1000
一、钻孔
3. 钻削用量 钻削进给量与进给速度: 3)钻削进给量与进给速度: f fz Vf 单位:mm/r 单位: 单位: 单位:mm/z 单位: 单位:mm/min
七、高精度孔的珩磨
1. 珩磨头及珩磨原理
图6-29
珩磨原理与珩磨头结构