孔加工工艺
5.2 孔的常规加工方法

4.铰削用量
(2)切削速度和进给量
铰削速度为 1.5 ~ 5m/min; 铰削钢件时,进给量为 0.3 ~ 2mm/r; 铰削铸铁件时,进给量为 0.5 ~ 3mm/r。
5.工艺特点
(1)铰孔是孔的精加工方法; (2)可加工精度为IT7、IT8、IT9的孔; (3)孔的表面粗糙度可控制在Ra3.2 ~ 0.2μm; (4)铰刀是定尺寸刀具; (5)切削液在铰削过程中起着重要的作用。
1) 2) 3) 4) 不能直接观察到刀具的切削情况。 切削热不易传散。 切屑不易排出。 工艺系统刚性差。
2.深孔钻的结构
枪钻 内排屑深孔钻 深孔麻花钻 套料钻 深孔扁钻
单齿内排屑深孔钻结构
导向块
刀齿
刀体
枪钻
枪钻钻孔深度与直径之比超过100,最大可
至250;钻孔精度为IT7~IT9;钻孔表面粗糙 度Ra为3.2~0.4µ m。
5.2.2 扩孔
1.扩孔钻
(1)不存在横刃; (2)齿数多(3、4齿); (3)切削余量小,排屑容易。
asp d0 d w
2.工艺特点
(1)扩孔是孔的半精加工方法; (2)一般加工精度为IT10~IT9; (3)孔的表面粗糙度可控制在Ra6.3~3.2μm。
3.扩孔的应用
当钻削 dw>30mm直径的孔时,为了减小钻削 力及扭矩,提高孔的质量,一般先用(0.5~ 0.7)dw大小的钻头钻出底孔,再用扩孔钻进行 扩孔,则可较好地保证孔的精度和控制表面粗 糙度,且生产率比直接用大钻头一次钻出时还 要高。
第5章 孔加工
刘英 副教授 重庆大学
5.2 孔的常规加工方法
刘英 副教授 重庆大学
孔的常规加工方法
钻孔、扩孔、铰孔、镗孔、拉孔、磨孔
《钳工工艺与技能训练》第6章孔加工

切削深度是指已加工表面与待加工表面间的垂直距离,对于 钻孔而言,切削深度为ap=D/2(mm),即等于钻头的半径。
2.钻孔切削用量的选择
(1)切削深度的选择
钻孔时,切削深度是由钻头的直径所决定,钻头直径越大, 切削深度也就越大。而钻头的直径又决定于所加工孔的孔径。 所以对直径小于30mm的孔,可一次钻出;而对直径为30~ 80mm的孔,为减小切削深度以降低所需机床功率,一般分两 次钻削,即先用(0.5~0.7)D(D为要求的孔径)的钻头钻孔, 然后用直径为D的钻头将孔扩大。这样不仅可以提高钻孔的质 量,同时也可以保护机床。
钻头的直径和进给量确定后,切削速度按钻头的合理耐用度进行 选择。当材料的强度、硬度高,钻孔直径较大时,宜用较低的切削 速度,转速也相应降低些,进给量也应减小。反之,则可选用较高 的转速,进给量也可适当增加。当钻头直径小于5mm时,应选用很高 的转速,但进给量不能过大,一般应采用手动进给,以免折断钻头。
1.修磨主切削刃
将主切削刃置于水平状态,钻头中心线和砂 轮圆柱面母线在水平面内形成的夹角等于钻头顶 角的一半。刃磨时,右手握住钻头的头部作定位 支点,左手握住钻柄,将刃口平行接触砂轮面, 逐渐刃磨。在刃磨时,将钻头沿轴线顺时针转动 35°~40°,钻柄向下摆动约等于后角。如此反 复进行2~3次,即可磨好一条主切削刃。再反转 180 °磨另一条主切削刃,此时应保持钻头只绕 其轴线做转动,而不改变空间位置,这样即可磨 出与轴线对称的顶角。
a) 钻头变径套 b) 拆卸方法
(六)钻孔的切削用量和冷却润滑
1.钻孔切削用量 ①切削速度v
切削速度v是钻孔时钻头直径上最外一点的线速度,可由 下式计算
v=πDn/1000
(m/min)
孔的精加工方法有哪些

孔的精加工方法有哪些孔的精加工方法有以下几种:1. 钻孔加工:钻孔是将钻头(如钻铰刀)放置在工件上,并以旋转的方式将其逐渐进给至所需深度的过程。
钻孔加工可以分为手工钻孔和机械钻孔两种方式。
手工钻孔通常用于小型工件的钻孔,而机械钻孔则适用于大型和批量加工的情况。
2. 铰孔加工:铰孔是通过铰刀以旋转和进给的方式将工件上的孔加工至所需的尺寸和形状。
铰孔加工通常用于加工孔的精度要求较高的情况,如对准孔、啮合孔等。
3. 刨孔加工:刨孔是利用刨刀将工件上的孔加工至所需深度的过程。
刨孔加工通常用于大直径和大深度的孔加工,且要求孔的表面粗糙度较高的情况。
4. 磨孔加工:磨孔是利用磨头以旋转和进给的方式将工件上的孔加工至所需尺寸和形状的过程。
磨孔加工通常用于加工孔的精度要求较高,如径向孔、深孔等。
5. 切削液加工:切削液加工是在孔加工过程中使用液体冷却剂和润滑剂,以降低温度、延长刀具寿命、提高加工质量的方法。
切削液加工可以采用内冷式、外冷式等不同的方式,常见的切削液包括水溶液、油剂等。
6. 拉孔加工:拉孔是通过将带有拉刀的拉床放置在工件上,以拉动拉刀将孔逐渐加工至所需深度的过程。
拉孔加工常用于大直径和大深度的孔加工,以及对孔精度和表面质量要求较高的情况。
7. 电火花加工:电火花加工是通过在工件表面产生电火花放电的方式将工件上的孔加工至所需尺寸和形状。
电火花加工通常用于高硬度材料和特殊形状的孔加工,且对孔的精度和表面质量要求较高。
以上是常见的孔的精加工方法,每种方法在实际应用中都有其适用的场景和优缺点。
在选择合适的加工方法时,需要考虑工件材料、孔的尺寸和形状要求、加工效率和成本等因素,并结合具体的加工设备和工艺条件进行综合考虑。
孔的加工方法

孔的加工方法孔的加工是机械加工中的一项重要工艺,它在许多领域都有着广泛的应用。
孔的加工方法多种多样,根据不同的工件材料、形状和精度要求,选择合适的孔加工方法对于提高加工效率和产品质量至关重要。
下面将介绍几种常见的孔的加工方法。
首先,钻孔是最常见的孔加工方法之一。
钻孔是利用钻头在工件上旋转切削,形成孔洞的加工方法。
钻孔适用于一般的孔加工,如在金属、塑料、木材等材料上加工圆孔。
钻孔的工艺简单、成本较低,适用于中小批量生产。
其次,铰削是一种用铰刀在工件上旋转切削,形成内螺纹孔或外螺纹孔的加工方法。
铰削适用于加工螺纹孔,如在机械零件中常见的螺纹孔加工。
铰削工艺精度高,表面质量好,适用于要求较高的螺纹孔加工。
另外,镗削是利用镗刀在工件上旋转切削,形成孔洞的加工方法。
镗削适用于加工大孔径、大深度、高精度的孔洞,如在汽车发动机缸体上的气缸孔加工。
镗削工艺适用范围广,加工效率高,适用于大型工件的孔加工。
最后,激光打孔是利用激光束对工件进行瞬间加热,使其熔化或汽化,形成孔洞的加工方法。
激光打孔适用于金属、塑料、陶瓷等材料的孔加工,尤其适用于复杂形状、高精度要求的孔加工。
激光打孔工艺无接触、无切削力,适用于对工件表面要求严格的孔加工。
综上所述,不同的孔加工方法各有特点,根据具体的加工要求选择合适的孔加工方法至关重要。
在实际生产中,应根据工件材料、形状、精度要求等因素综合考虑,选择最合适的孔加工方法,以提高加工效率和产品质量。
同时,随着科技的不断进步,孔的加工方法也在不断创新和发展,相信在未来会有更多更先进的孔加工方法出现,为各行各业的生产提供更加高效、精准的孔加工解决方案。
热加工工艺基础第四章 孔加工
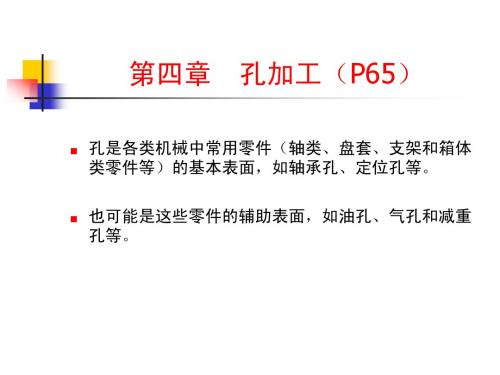
钻孔最常用的刀具是麻花钻头(视频)。
一、钻床加工简介(P66)
钻床主要用于加工中小型的孔。钻床上钻削时, 刀具旋转为主运动,同时刀具沿直线进行进给运动; 在车床上钻孔时,工件旋转,刀具进给。 钻孔简介 1)台式钻床:加工小型工件,一般孔径<13mm。 2)立式钻床:加工中小型工件,一般孔径<50mm,可自 动走刀。 3)摇臂钻床:如图13-25所示,结构完善,操作方便。 加工大中型工件,一般孔径<80mm。
1、镗孔的方法和刀具(P70)
1)在车床上镗孔:如P71图4-12所示;主运动为工件的旋 转、进给运动为镗刀装在小刀架上作纵向或横向的移 动。适合车回转体的轴心孔。
2)在镗床上镗孔:如P71图4-13和图4-14所示: 主运动— 镗刀刀杆装在机床主轴锥孔中,随主轴一起 旋转; 进给运动—工作台带动工件作纵向移动,也可以由主 轴带动镗刀作轴向移动来实现。
2、选用孔加工方案的几点说明(P79)
(2)淬火钢件:淬火之前,一般采用钻和镗,淬火之后只 能磨削。其加工方案为钻 镗 (淬火) 磨。
3)精度为IT7以上,Ra值为0.4以下的孔,在精加工以后 应进行光整加工,除短孔外,一般采用珩磨。 4)对于有色金属,不能采用磨削加工,其精加工常采用 精镗、精细镗、精铰或手铰方案。
第四章 孔加工(P65)
孔是各类机械中常用零件(轴类、盘套、支架和箱体 类零件等)的基本表面,如轴承孔、定位孔等。 也可能是这些零件的辅助表面,如油孔、气孔和减重 孔等。
§4-1
概述
一、孔的技术要求(P65)
1、尺寸精度:孔径大小和深度;
2、形状精度:孔的圆度、圆柱度及轴线的直线度; 3、位置精度:孔与孔、孔与外圆表面的同轴度;孔与孔、 孔与其它表面的平行度; 4、表面质量:表面粗糙度、表层的加工硬化和组织变化 等。
高精度孔的加工方法

高精度孔的加工方法
高精度孔的加工方法是指对于精度要求较高的孔进行加工的方法,例如在精密机械、航空航天、高速列车等领域中需要使用的孔。
高精度孔的加工需要保证孔的直径、圆度、表面质量等指标都达到一定的要求。
目前常见的高精度孔加工方法有以下几种:
1. 珩磨加工:珩磨是一种高速旋转的研磨工艺,通过磨头在被加工物表面的摩擦作用中去除材料,从而达到加工目的。
珩磨加工可以在孔内进行,可以加工出高精度圆度的孔。
2. 钻孔加工:钻孔是最常见的孔加工方法之一,可以使用林格曼钻头等工具进行。
钻孔加工可以达到较高的精度要求,但是对于深孔加工会出现偏差的问题。
3. 放电加工:放电加工是一种特殊的非机械加工方法,通过电火花放电来将被加工物表面的材料溶解或脱落,从而达到加工的目的。
放电加工可以加工出高精度的孔,但是加工速度较慢。
4. 激光加工:激光加工是一种高精度的非机械加工方法,通过激光束直接照射被加工物表面,将材料蒸发或熔化,从而达到加工目的。
激光加工可以加工出极高精度的孔,但是设备价格高昂,适用范围有限。
- 1 -。
孔加工技术
第三节孔加工与外圆表面加工相比,孔加工的条件要差得多,加工孔要比加工外圆困难。
这是因为:(1)孔加工所用刀具的尺寸受被加工孔尺寸的限制,刚性差,容易产生弯曲变形和振动;(2)用定尺寸刀具加工孔时,孔加工的尺寸往往直接取决于刀具的相应尺寸,刀具的制造误差和磨损将直接影响孔的加工精度;(3)加工孔时,切削区在工件内部,排屑及散热条件差,加工精度和表面质量都不易控制。
一、钻孔与扩孔1.钻孔钻孔是在实心材料上加工孔的第一个工序,钻孔直径一般小于。
钻孔加工有两种方式(图图3-27 两种钻孔方式a)钻头旋转b)工件旋转如在车床上钻孔。
上述两种钻孔方式产生的误差是不相同的。
在钻头旋转的钻孔方式中,由于切削刃不对称和钻头刚性不足而使钻头引偏时,被加工孔的中心线会发生偏斜或不直,但孔径基本不变;而在工件旋转的钻孔方式中则相反,钻头引偏会引起孔径变化,而孔中心线仍是直的。
常用的钻孔刀具有:麻花钻、中心钻、深孔钻等。
其中最常用的是麻花钻,其直径规格为。
标准麻花钻的结构如图3-28所示,其柄部是钻头的夹持部分,并用图3-28 标准麻花钻的结构a)锥柄b)直柄来传递扭矩;钻头柄部有直柄与锥柄两种,前者用于小直径钻头,后者用于大直径钻头。
颈部供制造时磨削柄部退砂轮用,也是钻头打标记的地方,为制造方便直柄麻花钻一般不设颈部。
工作部分包括切削部分和导向部分,切削部分担负着主要切削工作,钻头有两条主切削刃,两条副切削刃和一条横刃,如图3-29所示;螺旋槽表面为钻头的前刀面,切削图3-29 麻花钻的切削部分削刃可视为一正一反安装的两把外圆车刀。
如图中虚线所示。
导向部分有两条对称的螺旋槽和刃带,螺旋槽用来形成切削刃和前角,并起排屑和输送冷却液作用;刃带起导向和修光孔壁的作用;刃带有很小的倒锥,由切削部分向柄部每长度上直径减小,以减小钻头与孔壁的摩擦。
麻花钻的主要几何角度有顶角、前角、后角、横刃斜角和螺旋角,如图3-30所示。
顶角是两条主切削刃在与其平行的平面上投影的夹角,加工钢料和图3-30 标准麻花钻的几何角度铸铁的钻头顶角取为118°±2°。
孔的加工及其达到的精度
孔的加工及其达到的精度孔的加工及其达到的精度一、钻孔1. 工艺特点1)钻孔是孔的粗加工方法;2)可加工直径0.05〜125mm勺孔;3)孔的尺寸精度在IT10 以下;4)孔的表面粗糙度一般只能控制在Ra12.5卩m。
对于精度要求不高勺孔,如螺栓勺贯穿孔、油孔以及螺纹底孔,可直接采用钻孔。
二、扩孔工艺特点1)扩孔是孔的半精加工方法;2)一般加工精度为IT10 〜IT9 ;3)孔的表面粗糙度可控制在Ra6.3〜3.2卩m。
当钻削dw>30mm直径的孔时,为了减小钻削力及扭矩,提高孔的质量,一般先用(0.5〜0.7 )dw大小的钻头钻出底孔,再用扩孔钻进行扩孔,则可较好地保证孔的精度和控制表面粗糙度,且生产率比直接用大钻头一次钻出时还要高。
三、铰孔铰削过程的实质铰削过程不完全是一个切削过程,而是包括切削、刮削、挤压、熨平和摩擦等效应的一个综合作用过程。
铰削用量1)铰削余量粗铰余量为0.10mm- 0.35 mm; 精铰余量为0.04mm- 0.06mm。
2)切削速度和进给量铰削速度为1.5m/min - 5m/min ;铰削钢件时,进给量为0.3mm/r - 2mm/r ;铰削铸铁件时,进给量为0.5mm/r - 3mm/r 。
工艺特点1 )铰孔是孔的精加工方法;2)可加工精度为IT7 、IT8 、IT9 的孔;3)孔的表面粗糙度可控制在Ra3.2〜0.2卩m4)铰刀是定尺寸刀具;5)切削液在铰削过程中起着重要的作用。
四、镗孔工艺特点1)镗孔可不同孔径的孔进行粗、半精和精加工;2)加工精度可达为IT7 -IT6 ;3)孔的表面粗糙度可控制在Ra6.3〜0.8卩4)能修正前工序造成的孔轴线的弯曲、偏斜等形状位置误差;五、拉孔工艺特点1) 拉削生产率高。
2) 拉削精度高,质量稳定。
拉削精度一般可达IT9-IT7 级,表面粗糙度一般可控制到Ra1.6mm- Ra0.8mm拉削表面的形状、尺寸精度和表面质量主要依靠拉刀设计、制造及正确使用保证。
钻孔加工工艺方法
钻孔加工工艺方法
钻孔加工工艺方法主要包括钻圆柱孔和钻螺孔,利用切削刀具加工出圆柱形孔。
以下是该工艺方法的几个关键步骤和特点:
1.钻孔方式:有两种主要的钻孔方式,一种是钻头旋转,例如在钻床、镗床上钻孔;另一种是工件旋转,例如在车床上钻孔。
这两种方式产生的误差是不相同的,因此在选择钻孔方式时需要考虑到工件的特性和加工要求。
2.切削条件:切削条件的选择对于钻孔加工至关重要,包括进给速度和切削速度等。
合理的切削条件可以提高加工效率,保证加工质量,同时延长刀具的使用寿命。
3.刀具选择:常用的钻孔刀具包括麻花钻、中心钻、深孔钻等。
其中,麻花钻是最常用的一种,其直径规格范围广泛。
选择刀具时需要考虑工件的材质、孔径大小、加工精度等因素。
4.断屑与排屑:钻孔加工中产生的切屑必须及时排出,否则会影响加工质量和刀具寿命。
因此,断屑与排屑是钻孔
加工工艺中的重要环节。
可以采取增大进给量、断续进给、修磨横刃、装断屑器等方法来改善断屑和排屑效果。
5.提高定位精度:为提高定位精度,可以采取先钻中心孔、用立铣刀铣孔座、选用切入性好、刚性好的钻头以及降低进给速度等措施。
6.毛刺处理:钻削加工中,在孔的入口及出口处可能会出现毛刺,需要进行处理。
可以采取修磨钻头、调整切削条件等方法来减少毛刺的产生。
钻孔加工工艺方法需要综合考虑多个因素,包括切削条件、刀具选择、断屑与排屑、定位精度和毛刺处理等。
在实际应用中,需要根据工件的特性和加工要求来选择合适的工艺方法和参数,以获得高质量的加工效果。
孔加工知识
孔加工知识4.1任务:端盖零件上沉头螺钉孔和销孔的加工端盖零件如图4-1所示,底平面、两侧面和φ40H8型腔已在前面工序加工完成。
本工序加工端盖的4个沉头螺钉孔和2个销孔,试编写其加工程序。
零件材料为HT150,加工数量为5000个/年。
4.2 孔加工的工艺知识 1.孔加工的方法孔加工在金属切削中占有很大的比重,应用广泛。
在数控铣床上加工孔的方法很多,根据孔的尺寸精度、位置精度及表面粗糙度等要求,一般有点孔、钻孔、扩孔,锪孔、铰孔、镗孔及铣孔等方法。
2.孔加工的刀具1)钻孔刀具及其选择钻孔刀具较多,有普通麻花钻、可转位浅孔钻、喷吸钻及扁钻等。
应根据工件材料、加工尺寸及加工质量要求等合理选用。
在数控镗铣床上钻孔,普通麻花钻应用最广泛,尤其是加工¢30mm 以下的孔时,以麻花钻为主,如图6-2所示。
图6-2 普通麻花钻在数控镗铣床上钻孔,因无钻模导向,受两种切削刃上切削力不对称的影响,容易引起钻孔偏斜。
为保证孔的位置精度,在钻孔前最好先用中心钻钻一中心孔,或用一刚性较好的短钻头钻一窝。
中心钻主要用于孔的定位,由于切削部分的直径较小,所以中心钻钻孔时,应选取较高的转速。
对深径比大于5而小于100的深孔由于加工中散热差,排屑困难,钻杆刚性4.1端盖零件图差,易使刀具损坏和引起孔的轴线偏斜,影响加工精度和生产率,故应选用深孔刀具加工。
2)扩孔刀具及其选择扩孔多采用扩孔钻,也有用立铣刀或镗刀扩孔。
扩孔钻可用来扩大孔径,提高孔加工精度。
用扩孔钻扩孔精度可达IT11~IT10,表面粗糙度值可达Ra6.3~3.2um 。
扩孔钻与麻花钻相似,但齿数较多,一般为3~4个齿。
扩孔钻加工余量小,主切削刃较短,无需延伸到中心,无横刃,加之齿数较多,可选择较大的切削用量。
图6-3所示为整体式扩孔钻和套式扩孔钻。
3)铰孔刀具及其选择铰孔加工精度一般可达IT9~IT8级,孔的表面粗糙度值可达Ra1.6~0.8um ,可用于孔的精加工,也可用于磨孔或研孔前的预加工。
- 1、下载文档前请自行甄别文档内容的完整性,平台不提供额外的编辑、内容补充、找答案等附加服务。
- 2、"仅部分预览"的文档,不可在线预览部分如存在完整性等问题,可反馈申请退款(可完整预览的文档不适用该条件!)。
- 3、如文档侵犯您的权益,请联系客服反馈,我们会尽快为您处理(人工客服工作时间:9:00-18:30)。
结论 : 应用定径销孔钻头加工零件销孔可实现以 下四方面的作用。
1.效率提高节约加工费用,降低生产成本。 通过试验可以看出,使用定径销孔钻头后加
工效率提高,零件加工时间大大缩短,可节省人
工费、设备占用费、综合管理费等,即工缴费用。
按月产细纱机100台,全年降低零件加工费60万元。
2.减少数控设备占用时间,提升企业生产能力。 按每件龙筋节约实际加工时间300秒计算,
采用定径销孔钻头仅加工头尾段龙筋,按月产
100台,每年可减少数控设备占用时间2950小时
约合368.8天(即节省一台数控设备)。
3.提高零件加工质量水平
定径销孔钻头加工出的孔一致性很好,目前
我们试验检测出的孔径相差均在0.004-0.005,
因此可以很大程度的提高工序能力和产品质量水
平。
4.降低工具费用 定径销孔钻头由于本身材料及涂层的原因,其
1、起钻
预钻锥形定心孔,即先用小顶角起钻或中心钻,钻一个锥 形浅坑,作为钻孔的定位孔,再用所需尺寸的钻头钻孔。由于 横刃未参加工作,因而钻头不会出现由此引起的弯曲。
2、钻
钻削是使用钻头在实体材料上加工孔的
最常用的方法,其加工精度可达IT12~IT11 表面粗糙度Ra可达12.5~6.3μm,可作为攻 丝、扩孔、铰孔和镗孔的预备加工。
• 零件:
孔数:
落纱传动管
2
零件材料: 20#冷拉钢管
使用设备: 辛辛那提加工中心
原工艺 工序 起钻-钻-扩-铰
新工艺 钻(1道工序)
刀具
中心钻,钻头,扩孔钻,铰刀 合金钻头Φ11H9 V:55-90mm/min F:0.2mm/r 孔一致性:0.002-0.003 圆度: 0.004 轴对称度:0.03
①. 长向件,平面打孔
加工简图 1
• 新旧工艺对比(完成一件龙筋)
• 零件:
孔数:
龙筋
4
零件材料:铸铁
使用设备:门式加工中心
原工艺 工序 刀具
新工艺
起钻-钻-扩-铰(4道工序) 钻(1道工序) 中心钻,钻头,扩孔钻,铰刀 合金钻头Φ13H8 V:55-95mm/min F:0.2mm/r 孔一致性:0.002-0.003 圆度: 0.004 Ra0.8-1.6
• 4、铰孔
用铰刀从工件孔壁上切除微量金属层,以提高其 尺寸精度和降低表面粗糙度的加工方法。
由于铰刀的刀齿数量多,切削余量小,切削阻力
小,导向性好,加工精度高。 一般尺寸精度可达IT7~IT9级,表面粗糙度值可
达 Ra 0.8~3.2μm。
• 5、镗刀
镗刀是广泛使用的孔加工刀具。一般镗孔达到精
度IT9~IT8,精细镗孔时能达到IT6,表面粗糙度为
质孔钻 量径头 差容定 。易心 扩性 大差 ,, 且易 加震 工动 后、 的引 表偏 面,
•
3、扩孔
• 在钻孔之后,用于修正钻孔中心线位置和降低
表面粗的程度值,提高孔质量。
• 公差等级:IT9~IT10 • 表面粗糙度:6.3 ~3.2
• 特点:导向性好、无横刃、钻心较厚、扩孔余量小、改
善了切削条件;强度和刚度较高,可选择较大切削用量; 加工质量和生产率均均优于麻花钻。
Ra1.6~0.8μm。镗孔能纠正孔的直线性误差,获得高 的位置精度,特别适合于箱体零件的孔系加工。镗孔是 加工大孔的唯一精加工方法。镗刀种类很多,可分为单 刃镗刀和双刃镗刀。 销孔因尺寸较小一般不采用镗。
二、强力钻
背景:
2009年生产任务猛增,销孔加工占用数控 设备严重,为提高加工效率,解决生产瓶颈, 提出采用复合刀具减少加工工序的需求。
Ra0.8-1.6 25秒
V:30mm/min以下, 切削参数 F:0.1mm/r
孔精度 孔光度
孔一致性: 0.01-0.02 孔圆度: 0.005-0.01 孔轴对称度:0.05
Ra3.2
加工时间 210秒(包含换刀时间)
结论:效率提高 210/25=8.4倍
中 墙 板 专 机
• 龙筋销子孔专机
V:30mm/min以下 切削参数 F:0.1mm/r
孔精度 孔光度 孔一致性: 孔圆度: Ra3.2 0.01-0.02 0.005-0.01
加工时间 340秒(包含辅助换刀时间) 41秒
• 结论: 效率提高 340/41=8.3倍
②. 管类零件,圆柱面打孔
加工简图 2
• 新旧工艺对比(完成一件落纱传动管)
• 常规的复合刀具
a)钻-扩 b)扩-铰 c)钻-铰
1、定径销孔钻头开发
一把刀具、一次加工,同时达到零件尺寸、位置及粗糙度 等多方面的要求,刀具本身应集钻、铰功能为一体,且有极好
的刚性和自定心能力。而且该刀具为定径刀具,要求刀具的寿
命高、尺寸稳定性好。 为此我们针对龙筋、中墙板、传动杆等不同材料,不同形
而且铣削刃口校正了孔的形状度、位置度,使
铰削余量均匀,保证了孔的尺寸精度和光洁度。
Vc:30-40M/min
•
铝 加 工
纺纱器零件Φ8H7*50、Φ12H7*40孔加工, (其材料为压铸铝ZL111,要求粗糙度Ra1.6)原 来工艺为钻孔-扩孔-铰孔,不仅工序长,效率低, 而且刀具悬伸长磨损、振动严重,造成零件孔尺寸 缩小,且孔内粗糙度值超差,改用铣铰刀后,产品 质量明显提高,一把刀可加工1200余件,是普通 铰刀的6倍多。明显降低了制造成本。
效率是麻花钻的5倍以上。
孔径可根据需要自由无级调整,调整 范围可达1.5mm。 但由于受刀具结构及刀片精度的影响, 调整难度很大。整体设计精度为IT13。
四、铣铰刀
用于已有底孔的精加工,加工精度H7,零件材质可以是 钢料、铸铁、有色金属等。
铣铰刀由于其特有的刃口形状,兼有铣、扩、
铰功能。加工中铣-扩-铰一次完成,减少了工 序,提高了效率。
状零件分别设计和试验了钻头形式,尤其对钻头尺寸、钻尖、
螺旋角、修光刃等重点部位的设计参数做了多次试验改进。
① 选用整体合金钻头进行改良 ② 选用小螺旋角,适合恶劣的钻孔加工条件;钻头芯
厚采用超大正锥,提高钻头刚性;抛物线采用槽形
槽宽与背宽比 1.6:1 ,增强在大芯厚条件下的排屑能 力。
③
减少前角以增强刃口强度,并通过增大后角减少 对工件摩擦。
⑥
钻头横刃按自定心钻头设计,实现起钻功能。
• 加工铸铁刀具参数:
主刃顶角:125˚
槽形:
特殊槽形,增加断屑能力
刀尖R值: 0.8 横刃修正:R型内刃、主切削刃圆弧过渡 涂层: 刃径: 柄部: 超H涂层 公差±0.002 直柄h6
• 加工钢料刀具参数:
主刃顶角:140˚ 槽形: 涂层: 刃径: 芯厚: 柄部: 双棱边,增加排屑能力 超H涂层 公差±0.002 加强芯厚 直柄h7 横刃修正:F型内刃、主切削刃相切
相信同行们还有很多关于孔加工的先进技术和
经验,希望能有更多的机会向兄弟企业学习。
②.零件表面粗糙度Ra1.6-Ra0.8。
③.零件孔一致性为0.002-0.003;圆度0.003-0.004。 ④.零件孔径尺寸精度7级以下,位臵度小于0.01。 ⑤.管类零件上钻孔,轴对称度小于0.03。 另外,钻头修磨与再涂层可以进行4次,结合修磨效果, 刀具成本可降低至50%。
四、 定径销孔钻头加工实例及效率、效益分析
新型销孔刀具的开发应用
经纬股份榆次分公司
• • • •
一、常规销孔加工工艺及刀具的特点 二、强力钻 三、浅孔钻U钻加工 四、铣铰刀
• 一、常规销孔加工工艺及刀具的特点
销孔精度要求相对较高,一般尺寸精度在IT9 级以上,位臵精度0.005—0.02,粗糙度Ra1.6。 传统的工艺为使用数控机床及高速钢刀具,分起 钻-钻-扩-铰四道工序加工完成。
耐磨性很好、寿命很高,加之钻头还可以进行多
次修磨,因此刀具费用将比原4把刀具降低,目前
合金钻头已完成15000个孔的加工(铸铁零件),
刀具仍然完好不需重磨。
三、浅孔钻U钻加工
头部装有两个可转位刀片,成交错排 列,钻头定心稳定,切屑排除流畅,加工 时以钻为主,兼有镗扩功能,使用方便。 切削速度80-120m/min,进给0.1-0.2/转,
为提高切削系统的稳定性和刚性,对机床和夹 具进行了调整和选择。
①.使用加工中心或数控设备等功率大、刚性好的设
备,主轴径向跳动(刀头处)小于0.01,最好使用 冷却装置。
②.使用热装夹头或弹簧夹头,使刀具夹持稳定、牢
靠,定心精度高。杜绝使用铣夹头、钻夹头。 ③.夹具对零件的夹持、支撑牢固、可靠,特别是零 件加工点处要求弹性变形小。
2、定径销孔钻头的应用效果
目前,定径销孔钻头已在我公司广泛应用于 中墙板、龙筋、落纱传动管等几十种零件的加工,
销孔尺寸有Φ6D8、Ф9H8、Φ11H9、Φ13H8、
Ф20H9等,零件有墙板类、轴类;材料有铸铁、
钢料,零件加工精度完全达到图纸要求,并一次
加工完成:
①.一道钻孔工序取代原来起钻—钻—扩—铰四道工序。
④
采用抛物线槽形、副切削刃宽度由窄变宽,以减
少加工过程中的震动,最大限度的提高尺寸精度,
并保证钻头在恶劣工作条件下的使用寿命和稳定性。
⑤
取消易磨损并产生孔壁划伤的刀尖,对主切削刃
和副Байду номын сангаас削刃进行圆弧过渡,保证刀尖强度与加工表面
质量;通过刀尖圆弧的几何参数优化,控制副切削刃
进入工件的顺序,降低切削阻力而提高孔壁表面质量, 实现“以钻代铰”,加工效率获得极大提高。