内孔加工的对刀操作与输入PPT课件
《在铣床上加工孔》课件

在加工过程中,要使用冷却液 或润滑剂,以降低切削温度、 减少刀具磨损和改善切削条件
。
03
CATALOGUE
铣床的选择与操作
铣床的类型与选择
总结词
根据加工需求选择合 适的铣床类型
卧式铣床
适用于加工大型零件 ,能进行多面和多轴 加工
立式铣床
适用于加工小型零件 ,主轴垂直设置,操 作方便
龙门铣床
《在铣床上加工 孔》PPT课件
contents
目录
• 引言 • 铣床加工孔的基本知识 • 铣床的选择与操作 • 孔加工的工艺流程 • 实际操作演示 • 安全注意事项
01
CATALOGUE
引言
课程介绍
课程背景
介绍铣床加工孔在机械制造中的重要 性和应用领域,说明课程的目的和意 义。
课程性质
说明该课程是实践性较强的技能培训 课程,重点在于培养学生的实际操作 能力和解决问题的能力。
问题处理演示
模拟遇到问题时的处理方 式,如刀具磨损、孔位偏 差等,展示应对措施。
演示总结与反馈
总结
对整个演示过程进行总结,强调关键操作步骤和注意事项。
反馈
收集观众的反馈意见,对演示内容进行改进和完善,提高教学质量。
06
CATALOGUE
安全注意事项
操作过程中的安全防护措施
01
02
03
佩戴安全帽、防护眼镜 、手套等个人防护装备 ,确保操作过程中的安
根据加工需求,调整铣床的主轴 转速、进给速度等参数,确保加 工过程的稳定性和精度。
孔加工的步骤
定位孔
使用钻头在工件上钻出定位孔,作为后续孔 加工的基准。
铣孔
将铣刀插入定位孔,通过铣床的旋转和进给 运动,对工件进行铣孔加工。
对刀的方法

以下内容只有回复后才可以浏览一、对刀对刀的目的是确定程序原点在机床坐标系中的位置,对刀点可以设在零件上、夹具上或机床上,对刀时应使对刀点与刀位点重合。
数控车床常用的对刀方法有三种:试切对刀、机械对刀仪对刀(接触式)、光学对刀仪对刀(非接触式),如图 3-9 所示。
1、试切对刀1 )外径刀的对刀方法如图 3-10 所示。
Z 向对刀如 (a) 所示。
先用外径刀将工件端面 ( 基准面 ) 车削出来;车削端面后,刀具可以沿 X 方向移动远离工件,但不可 Z 方向移动。
Z 轴对刀输入:“ Z0 测量”。
X 向对刀如 (b) 所示。
车削任一外径后,使刀具 Z 向移动远离工件,待主轴停止转动后,测量刚刚车削出来的外径尺寸。
例如,测量值为Φ 50.78mm, 则 X 轴对刀输入:“ X50.78 测量”。
2 )内孔刀的对刀方法类似外径刀的对刀方法。
Z 向对刀内孔车刀轻微接触到己加工好的基准面(端面)后,就不可再作 Z 向移动。
Z 轴对刀输入:“ Z0 测量”。
X 向对刀任意车削一内孔直径后,Z 向移动刀具远离工件,停止主轴转动,然后测量已车削好的内径尺寸。
例如,测量值为Φ 45.56mm, 则 X 轴对刀输入:“ X45.56 测量”。
3 )钻头、中心钻的对刀方法如图 3-11 所示。
Z 向对刀如( a )所示。
钻头 ( 或中心钻 ) 轻微接触到基准面后,就不可再作 Z 向移动。
Z 轴对刀输入:“ Z0 测量”。
X 向对刀如( b )所示。
主轴不必转动,以手动方式将钻头沿 X 轴移动到钻孔中心,即看屏幕显示的机械坐标到“ X0.0 ”为止。
X 轴对刀输入:“ X0 测量”。
2、机械对刀仪对刀将刀具的刀尖与对刀仪的百分表测头接触,得到两个方向的刀偏量。
有的机床具有刀具探测功能,即通过机床上的对刀仪测头测量刀偏量。
3、光学对刀仪对刀将刀具刀尖对准刀镜的十字线中心,以十字线中心为基准,得到各把刀的刀偏量。
二、刀具补偿值的输入和修改根据刀具的实际参数和位置,将刀尖圆弧半径补偿值和刀具几何磨损补偿值输入到与程序对应的存储位置。
第七课 数车内孔、内腔和套类零件加工(理论讲解)
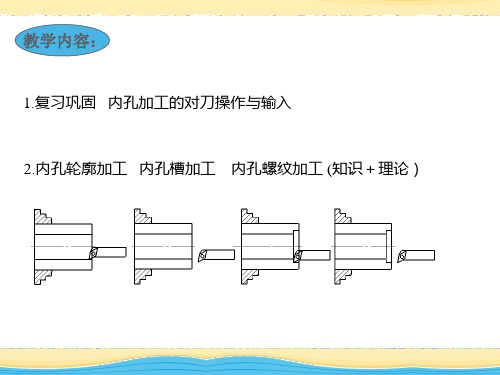
7.孔的精度 套类零件的精度有下列几个项目。
(1)孔的位置精度。 同轴度(孔之间或孔与某些表面间的尺寸精度)、平 行度、垂直度、径向圆跳动和端面圆跳动等。
铰孔是对较小和未淬火孔的精加工方法之一,在成批生
产中已被广泛采用。铰孔之前,一般先镗孔,镗孔后留些 余量,一般粗铰为0.15mm~0.3mm,精铰为0.04mm~ 0.15mm,余量大小直接影响铰孔的质量。
4.孔加工方法的选择 在车床中,孔的加工方法与孔的精度要求、孔径以及
孔的深度有很大的关系。一般来 讲,在精度等级为IT12、 IT13时,一次钻孔就可以实现。在精度等级为IT11,孔径 ≤10mm时,采用一次钻孔方式;当孔径>10~30mm时, 采用钻孔和扩孔方式;孔径>30~80mm时,采用钻孔、扩 钻、扩孔刀或车刀镗孔方式。在精度等级为ITl0、IT9,孔 径≤10mm时,采用钻孔以及铰孔方式;当孔径 >10~30mm时,采用钻孔、扩孔和铰孔方式;孔径 >30~80mm时,采用钻孔、扩孔、铰孔、或者用扩孔刀镗 孔方式。在精度等级为IT8、IT7,孔径≤10mm时,采用钻 孔及一次或二次铰孔方式;当孔径>10~30mm时,采用钻 孔、扩孔、一次或二次铰孔方式;当孔径>30~80mm时, 采用钻孔、扩钻(或者用扩孔刀镗孔)以及一次或二次铰孔 方式。
如出现Z方向的误差,则其修整办法相同。
二、内孔、内腔和套类零件(知识+理论)
课题一 盲孔零件的加工
本课题要求编程并加工如图6.1所示盲孔零件,毛 坯为φ53mm×100mm的棒料,材料为45钢。
a)零件图 b)实体图 图6.1 盲孔零件
一、基础知识 1.孔加工特点 (1)孔加工是在工件内部进行的,观察切削情况比较困 难,尤其是小孔、深孔更为突出。
数控车床对刀点与换刀点的确定: PPT课件

1
第二章 数控加工的工艺分析
2.2.6、对刀点与换刀点的确定: 1.对刀点的确定 在使用对刀点确定加工原点时,就需要进行 “对刀”。 所谓对刀是指使“刀位点”与“对刀点”重 合的操作。每把刀具的半径与长度尺寸都是不同 的,刀具装在机床上后,应在控制系统中设置刀 具的基本位置。“刀位点”是指刀具的定位基准 点。如下图所示,圆柱铣刀的刀位点是刀具中心 线与刀具底面的交点;球头铣刀的刀位点是球头 的球心点或球头顶点;车刀的刀位点是刀尖或刀 尖圆弧中心;钻头的刀位点是钻头顶点。 2
5
第二章 数控加工的工艺分析
(a)
(b)
(a) 数控铣床坐标系; (b) 铣削加工零件
6
第二章 数控加工的工艺分析
7
第二章 数控加工的工艺分析
2.换刀点的确定
换刀点是为加工中心、数控车床等采用多刀
进行加工的机床而设置的,因为这些机床在加工
过程中要自动换刀。对于手动换刀的数控铣床,
也应确定相应的换刀位置。为防止换刀时碰伤零
9
第二章 数控加工的工艺分析
对点位控制机床,只要求定位精度较高,定位过程尽
可能快,而刀具相对于工件的运动路线无关紧要。因此,
这类机床应按空程最短来安排加工路线。但对孔位精度要
求较高的孔系加工,还应注意在安排孔加工顺序时,防止
将机床坐标轴的反向间隙带入而影响孔位精度。如图所示
零件,若按(a)图所示路线加工时,由于5、6孔与1、2、3、
件、刀具或夹具,换刀点常常设置在被加工零件
的轮廓之外,并留有一定的安全量。
2.2.7 刀具走刀路线的确定
走刀路线就是刀具在整个加工工序中的运动
轨迹,它不但包括了工步的内容,也反映出工步
数控车床对刀步骤
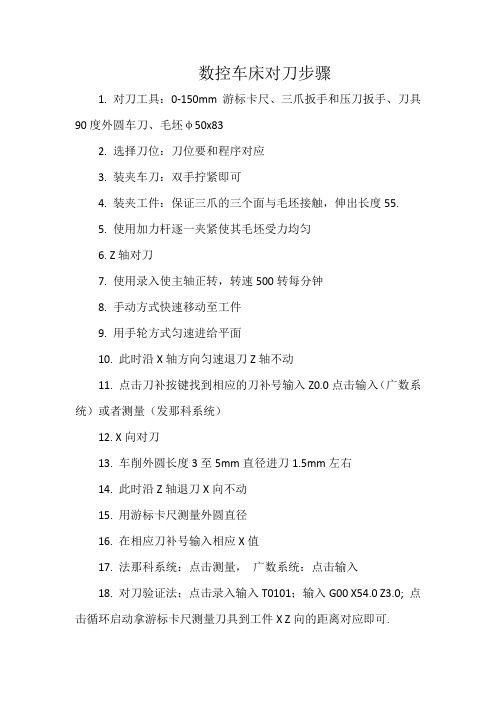
数控车床对刀步骤
1. 对刀工具:0-150mm游标卡尺、三爪扳手和压刀扳手、刀具90度外圆车刀、毛坯φ50x83
2. 选择刀位:刀位要和程序对应
3. 装夹车刀:双手拧紧即可
4. 装夹工件:保证三爪的三个面与毛坯接触,伸出长度5
5.
5. 使用加力杆逐一夹紧使其毛坯受力均匀
6. Z轴对刀
7. 使用录入使主轴正转,转速500转每分钟
8. 手动方式快速移动至工件
9. 用手轮方式匀速进给平面
10. 此时沿X轴方向匀速退刀Z轴不动
11. 点击刀补按键找到相应的刀补号输入Z0.0点击输入(广数系统)或者测量(发那科系统)
12. X向对刀
13. 车削外圆长度3至5mm直径进刀1.5mm左右
14. 此时沿Z轴退刀X向不动
15. 用游标卡尺测量外圆直径
16. 在相应刀补号输入相应X值
17. 法那科系统:点击测量,广数系统:点击输入
18. 对刀验证法:点击录入输入T0101;输入G00 X54.0 Z3.0; 点击循环启动拿游标卡尺测量刀具到工件X Z向的距离对应即可.。
4.1 车削通孔
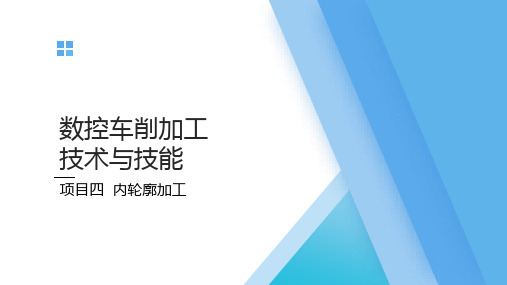
程序初始化
换1号外圆刀 主轴正转1000r/min 刀具快速移动到换刀点 快速接近工件,准备车削端面 平整端面,进给量0.2mm/r
轮廓粗加工
主轴停止 暂停程序,测量工件并修正刀补 刀具运行 定位至精车循环起点 主轴正转1000 r/min 执行精车循环 回换刀点,程序结束
参考程序
程序段号
N10 N20 N30 N40 N50 N60 N70 N80 N90 N100 N110 N120 N130 N140 N150 N160 N170 N180 N190
如何钻孔
2.孔的加工方法 常规孔的加工方法有钻孔、扩孔、铰孔、镗孔、拉孔、磨孔等。 钻孔的工具为麻花钻。
如何钻孔
3.麻花钻的安装方法 在车床上安装麻花钻的方法一般有四种: (1)用钻夹头安装
如何钻孔
3.麻花钻的安装方法 (2)用钻套安装
如何钻孔
3.麻花钻的安装方法 (3)用V形槽铁安装
如何钻孔
说明
程序初始化 换2号内孔刀,调用02号刀补 主轴正转600r/min 刀具快速移动到换刀点 快速接近工件,准备车削端面
内孔粗加工
主轴停止 暂停程序,测量工件并修正刀补 刀具运行 定位至精车循环起点 主轴正转1000 r/min 内孔精加工
回换刀点,程序结束
内孔车刀对刀
内孔车刀X方向和Z方向对刀如图所示
程序内容
G99 G21; T0202; M03 S600; G00 X100 Z100; G00 X22 Z2; G90 X26 Z-35 F0.1; X28 X29 G00 Z100; X100; M05; M00 ; T0202; G00 X22 Z2; M03 S1000; G90 X30 Z-35 F0.1 G00 X100 Z100; M05; M30;
数控加工常见的对刀方法
数控加工常见的对刀方法对刀是数控加工中的主要操作和重要技能。
在一定条件下,对刀的精度可以决定零件的加工精度,同时,对刀效率还直接影响数控加工效率。
仅仅知道对刀方法是不够的,还要知道数控系统的各种对刀设置方式,以及这些方式在加工程序中的调用方法,同时要知道各种对刀方式的优缺点、使用条件等。
一、对刀原理对刀的目的是为了建立工件坐标系,直观的说法是,对刀是确立工件在机床工作台中的位置,实际上就是求对刀点在机床坐标系中的坐标。
对于数控车床来说,在加工前首先要选择对刀点,对刀点是指用数控机床加工工件时,刀具相对于工件运动的起点。
对刀点既可以设在工件上(如工件上的设计基准或定位基准),也可以设在夹具或机床上,若设在夹具或机床上的某一点,则该点必须与工件的定位基准保持一定精度的尺寸关系。
对刀时,应使指刀位点与对刀点重合,所谓刀位点是指刀具的定位基准点,对于车刀来说,其刀位点是刀尖。
对刀的目的是确定对刀点(或工件原点)在机床坐标系中的绝对坐标值,测量刀具的刀位偏差值。
对刀点找正的准确度直接影响加工精度。
在实际加工工件时,使用一把刀具一般不能满足工件的加工要求,通常要使用多把刀具进行加工。
在使用多把车刀加工时,在换刀位置不变的情况下,换刀后刀尖点的几何位置将出现差异,这就要求不同的刀具在不同的起始位置开始加工时,都能保证程序正常运行。
为了解决这个问题,机床数控系统配备了刀具几何位置补偿的功能,利用刀具几何位置补偿功能,只要事先把每把刀相对于某一预先选定的基准刀的位置偏差测量出来,输入到数控系统的刀具参数补正栏指定组号里,在加工程序中利用T指令,即可在刀具轨迹中自动补偿刀具位置偏差。
刀具位置偏差的测量同样也需通过对刀操作来实现。
二、对刀方法在数控加工中,对刀的基本方法有试切法、对刀仪对刀和自动对刀等。
本文以数控铣床为例,介绍几种常用的对刀方法。
1、试切对刀法这种方法简单方便,但会在工件表面留下切削痕迹,且对刀精度较低。
数控机床编程与操作任务2.1 数控车床的对刀操作
刀位点是指刀具的定位基准点。在进行数控加工编程时,往往将整个刀具浓缩视为一个
点,那就是“刀位点”。它是在刀具上用于表现刀具位置的参照点。常用车刀的刀位点如图 2-8所示,其中(a)是90°偏刀,(b)是螺纹车刀,(c)是切断刀,(d)是圆弧车刀。
图2-8 常用车刀刀具的刀位点
知识准备: 二、数控车刀类型及刀位点
以外圆车刀为例,对刀时选择工件右端面中心点为工件坐标系原点,刀尖为编程与对刀到 位点,对刀步骤如下。
1)刀具Z方向对刀
①MDI模式下输入“M03 S400”指令,按数控启动铵钮 ,使主轴正转。 ②切换成手动(JOG)模式,移动刀具车削工件右端面,再按+X建退出刀具(刀具Z方向位 置不能移动),如图2-10所示。
图2-5机床参考点
b)刀架后置的机床参考点
知识准备: 一、数控车床的坐标系统
任务2.1 数控车床的对刀操作
2. 工件坐标系
工件坐标系是编程人员根据零件图形状特点和尺寸标注的情况,为了方便计算出编程的坐 标值而建立的坐标系。工件坐标系的坐标轴方向必须与机床坐标系的坐标轴方向彼此平行且一 致。数控车削零件的坐标系原点一般位于零件右端面或左端面与轴线的交点上。如图2-6所示。
3)报警处理及报警界面切换 根据报警原因或查阅发那科系统说明书中报警一览表,消除引起报警的原因,然后按 复位键。处于报警界面时,通过消除报警或按下信息功能键返回到显示报警界面前所显示 的界面。
任务2.1 数控车床的对刀操作
当数控机床出现故障、操作失误或程序错误时,数控系统就会报警,显示报警界面(或报 警信息),机床停止运行;数控机床报警后,应查找报警原因并加以消除后才能继续进行零 件加工。
1.FANUC系统数控机床报警与诊断
中职教育-《车工技术项目训练教程》课件:项目7.1 孔车削的基本知识.ppt
(a)高速钢扩孔钻
(b)硬质合金扩孔钻
图7-13 扩孔钻
2.铰孔 铰孔是精加工孔的方法之一。经过铰孔的工件,既
光洁又精确,它不仅质量好、效率高,而且操作也很方 便,目前在批量生产中已被广泛采用。铰刀如图7-14所 示。
在铰孔前,一般先经过钻孔、扩孔或车孔等半精加 工,并留有适当的铰削余量,余量的大小直接影响到铰 孔的质量。铰孔余量一般为0.08 ~ 0.15 mm ,用高速钢 铰刀铰削余量取小值,用硬质合金铰刀取大值。铰削时, 切削速度愈低,表面粗糙度值愈小(一般选VC < 5 m/min)。由于切削余量少,而且铰刀有较长的修光定位 部分定位,进给量可取得大一些。在铰孔的同时,必须 及时注入切削液,以保证表面光洁。
图7-5 钻孔的方法
③盲孔车刀靠近工件端面,移动小滑板,使车刀刀尖与 端面轻微接触,将小滑板和床鞍刻度调至零位。 ④将车刀伸入孔口内,移动中滑板,刀尖进给至与孔口 刚好接触时,车刀纵向退出,此时将中滑板刻度调至零 位。 ⑤用中滑板刻度指示控制切削深度(孔径留0.3 ~ 0.4 mm 精车余量),若机动纵向进给车削平底孔时要防止车 刀与孔底面碰撞。因此,当床鞍刻度指示离孔底面还有2 ~ 3 mm 距离时,应立即停止机动进给改用手动进给。如 孔大而浅,一般车孔底面时能看清。若孔小而深,就很 难观察到是否已车到孔底。此时通常要凭感觉来判断刀 尖是否已车到孔底。若切削声音增大,表明刀尖已车到 孔底。
根据被测最工件的内孔直径,用外径千分尺将内径表对 准“零”位后,方可进行测量,其测量方法,如图7-9所 示。测量时取最小值为孔径的实际尺寸。
图7-9 内径百分表的测量方法
三、知识拓展
孔的车削除了用镗刀车削外还有扩孔钻扩孔与铰刀 铰孔。 1.用扩孔刀具扩大工件孔径的方法称为扩孔。
加工中心对刀操作教学设计
加工中心对刀操作教学设计引言:加工中心是一种高效、精确的数控机床,广泛应用于各种具有高要求的工件加工中。
而对刀操作是加工中心调校和调试的重要环节,直接影响加工质量和效率。
本文将介绍加工中心对刀操作的步骤和技巧,在实际教学设计中提供一种有效的教学方案。
一、对刀操作的步骤1. 安全准备在进行任何操作之前,首先需要做好安全准备工作。
确保加工中心及其周围环境的干净整洁,并检查加工中心的各项安全设施是否完好。
2. 准备工作将加工中心上的旧刀具卸下,并清洁刀具槽与主轴孔。
检查新刀具的安装孔是否干净无异物,确保刀具与夹持装置配合良好。
3. 确定刀具坐标将加工中心切换到手动操作模式,在坐标系选择页面中选择刀具安装的位置,并记录下初始刀具坐标。
4. 定位刀具将新刀具插入刀具槽中,并用专用工具紧固刀具,确保刀具位置准确无误。
5. 编写自动对刀程序根据实际需要,编写自动对刀的程序。
程序中需要包含相应的坐标偏移补偿和刀具定位指令,确保刀具能够准确定位。
6. 运行对刀程序运行编写好的自动对刀程序,在操作界面上显示出刀具坐标,并记录下自动对刀后的刀具坐标。
7. 检查刀具偏差将自动对刀后的刀具与实际需要加工的工件进行比对,检查刀具的偏差情况。
如果存在偏差,需要进行相应的补偿调整。
8. 调整刀具坐标根据检查结果,对刀具进行适当的调整。
可通过修改刀具坐标值或调整刀具夹持装置来达到更加准确的刀具位置。
9. 确认对刀结果重新运行对刀程序,确认调整后的刀具是否符合要求。
如果不符合要求,需要再次进行调整。
10. 记录和备份将最终调整后的刀具坐标和对刀程序进行记录和备份,以备后续使用。
二、教学设计方案在教学设计中,应充分考虑学生的实际情况和经验水平,采用逐步引导的方式进行教学。
1. 知识概述在开始教学之前,对加工中心对刀操作的意义和重要性进行说明,让学生了解对刀操作对加工质量的影响。
2. 理论讲解通过教师的讲解,向学生介绍加工中心对刀操作的步骤和技巧,并强调操作中需要注意的安全事项。
- 1、下载文档前请自行甄别文档内容的完整性,平台不提供额外的编辑、内容补充、找答案等附加服务。
- 2、"仅部分预览"的文档,不可在线预览部分如存在完整性等问题,可反馈申请退款(可完整预览的文档不适用该条件!)。
- 3、如文档侵犯您的权益,请联系客服反馈,我们会尽快为您处理(人工客服工作时间:9:00-18:30)。
1 .按工作方式区下的MDI键。 2 .按PROG键切换屏幕,输入“T0101;”,按INSRT键,按循环 启动键,使1号刀(内孔车刀)处于工作位置。 3 . 输入“M03 S500;”,按INSRT键,按循环启动键,使主轴
转动。 4 .按工作方式区下的手动键,利用方向键结合快速移动键及 进给倍率旋钮移动1号刀,接近工件毛坯端面。 5 .进行Z方向对刀。
.
4
二、内孔车刀的对刀方法
Produced by Miss Xie
车刀接近工件端面
刀尖和端面重合
沿X方向退刀
移动刀具时注意控制进给速度,不能太快,还要均匀,一般 训练初期对刀用手摇方式,熟练后方可选用手动方式,当刀具 距离工件较近时,一定改为手摇方式。
.
5
二、内孔车刀的对刀方法
Produced by Miss Xie
数控车常用的对刀方法有试切对刀、机械对刀仪对刀、
光学对刀仪对刀等,数控车最常用试切对刀法进行对刀操作。
刀架转位后,各刀具的刀尖不在同一点上。对刀操作可以调
整数控车床每一把刀,将各刀的刀位点统一到同一个工件坐
标系的某个位置,使各刀尖点均能按同一工件坐标系指定的
位置移动,从而使编程时不用考虑刀具的安装位置。对刀的
N00001
T 0 0 0 0 0 0 0 0
MEM *** *** ***
S 0 T0101 08:16:18
【磨耗】 【形状】 【 】 【 】 【(操作)】
.
8
内孔加工的对刀操作与输入
.
机械制造技术《数控车加工》 1
内孔加工的对刀操作与输入
一
对刀
二 内孔车刀的对刀方法
Produced by Miss Xie
.
2
一、对刀
Produced by Miss Xie
对刀是数控机床加工前必需的准备工作。对刀是数控加 工中的主要操作和重要技能,在一定条件下,对刀精度可以 决定零件的加工精度,同时,对刀效率还直接影响数控加工 效率。
0.000
0.000
G05
0.000
0.000
G06
0.000
0.000
G07
0.000
0.000
G08
0.000
0.000
MEM *** *** *** 【磨耗】 【形状】 【 】
0.000
0
0.000
0
0.000
0
0.000
0
0.000
0
0.000
0
0.000
0
0.000
0
S 0 T0101
08:16:18
【 】 【(操作)】
.
6
二、内孔车刀的对刀方法
7.切削内孔,进行X方向对刀。
Produced by Miss Xie
车刀接近工 件下屑即可 X方向进刀
切削外圆
沿X方向退刀
.
7
二、内孔车刀的对刀方法
Produced by Miss Xie
8.用卡尺或千分尺测量切削外圆直径。 9 .按OFSJSET键,显示画面下图所示,然后按[形状]下的软功 能键,用↑键或↓键移动光标到相应的刀号位置,如4号刀在 G04,输入“X直径值”,按测量软键,完成X方向对刀。
6.按OFSJSET键,显示画面如下所示,然后按[形状]下的软功 能键,用↑键或↓键移动光标到相应的刀号位置,如1号刀在 G01,输入“Z0”,按测量软键,完成Z方向对刀。
工具补正/形状
番号
X
O0001
N00001ZR NhomakorabeaT
G01
0.000
0.000
G02
0.000
0.000
G03
0.000
0.000
G04
工具补正/形状
番号
X
G01
0.000
G02
0.000
G03
0.000
G04
0.000
G05
0.000
G06
0.000
G07
0.000
G08
0.000
Z 0.000 0.000 0.000 0.000 0.000 0.000 0.000 0.000
O0001
R 0.000 0.000 0.000 0.000 0.000 0.000 0.000 0.000
目的就是确定编程原点在机床坐标系中的位置,并将对刀数
据(X、Z方向零点位置)输入到相应的存储位置,数控车床
根据程序自动计算出刀具在机床坐标系中的坐标,从而指挥
刀具运动,对刀点可以设在零件上、夹具上或机床上,对刀
时应使用对刀点与刀位点重合。试切对刀的对刀点一般在零
件上。
.
3
二、内孔车刀的对刀方法
Produced by Miss Xie