管道钻孔机结构设计
打孔机设计

软塑胶管打孔机设计一、所给出的数据及参数1、材质:塑胶2、具体成品模型见图成品模型及尺寸要求3、已知设计数据:D=Φ8.2±0.2mm d=Φ4.7±0.2mm 小孔d1=Φ1.9~Φ2.2mm 总长L=138±3mm打孔距离: L 1=15mm, L 2=25mm, L 3=25mm, L 4=25mm 二、需要注意并且考虑到的问题1、 该产品为塑胶软管,材质比较软轻,需要在其上精准打穿4个小孔,小孔直径:d 1=Φ1.9~Φ2.2mm ,每个小孔在空间上相互垂直,成90度角。
2、 本次设计目的:围绕塑胶管设计出一专门打孔机器提高打孔效率,原则上能够实现6s 生产出来一个成品件,因此生产效率要求比较高。
塑胶管尺寸比较小,所打孔的孔径小,因而生产的精度和准确性也要求比较高。
三、软塑胶管打孔机工作原理及 设计方案(一)小电机气缸注解:1、四个气缸一起推动四个小电机运动。
动作协调一致。
2、整个运动控制过程可以通过PLC或单片机编程实现。
图片说明:1、中间盘设计成八方盘,上面设计八个能放置并且固定软塑胶管的塞子。
2、八方盘下面用电机带动,初步选用伺服电机。
通过变速器控制八方盘的转动。
3、打孔时候用四个气缸推动四个小电机进行伸缩运动。
气缸通过压力传感器传递信号到PLC。
4、小电机的开启和停止转动通过PLC控制。
5、大电机经过变速器控制后,通过PLC进行角度控制。
每次使得八方盘转动45度角。
四、图片样式详解八方盘整体示意1八方盘整体示意2固定塞子(需要改进设计)小型气缸小电机推力圆柱滚子轴承五、设计本身应该考虑的问题1、角推力轴承的稳定性和定位精度是否能够达到设计要求。
2、电机的选择:小电机能否买到并且满足设计要求,大电机的急停急启动,并且转动要求比较慢,伺服电机能否满足要求。
3、塞子设计不合理,应该进行改进。
否则装和取都不方便。
很难实现6s完成工件。
4、整个运动过程用PLC能否通过编程实现。
打孔机的结构原理设计

打孔机的结构原理设计打孔机是一种用于在材料上打孔的机械设备。
它主要由机架、传动系统、控制系统和辅助系统四部分组成。
下面将详细介绍打孔机的结构、原理和设计。
1.机架打孔机的机架是整个机器的主要承载部分,它需要具备足够的刚性和稳定性。
机架通常由坚固的钢板焊接而成,保证机器在工作时不会产生明显的振动和变形。
2.传动系统打孔机的传动系统主要由电机、减速器和传动装置组成。
电机是打孔机的动力源,通过输出旋转运动的力来驱动整个机器。
减速器和传动装置则用于将电机输出的高速旋转转换为打孔机需要的低速高扭矩旋转。
3.打孔机构打孔机构是打孔机的核心部件。
它通常由主轴、刀具和导向装置等组成。
主轴是实现刀具旋转运动的主要部件,它需要具备足够的刚性和精度。
刀具则用于在材料上进行孔洞的切削,它通常由硬质合金材料制成,并根据需要采用不同形状的切削刃。
导向装置用于确保切削刀具在工作过程中的稳定性和精度。
4.控制系统打孔机的控制系统主要由PLC和人机界面组成。
PLC负责对打孔机的各个部件进行协调和控制,包括电机的启停、切削参数的设定等。
人机界面则用于操作员与打孔机进行交互,通过触摸屏或按钮等方式来实现对机器运行状态的监控和控制。
5.辅助系统打孔机的辅助系统包括润滑系统、冷却系统和除尘系统等。
润滑系统用于对打孔机的各个运动部件进行润滑,减少摩擦和磨损。
冷却系统用于对切削区域进行冷却,提高切削效率和刀具的使用寿命。
除尘系统则用于清除切削过程中产生的粉尘和切屑,保持工作环境的清洁和人员的健康安全。
在设计打孔机时,需要注意以下几点:1.根据工件材料的特性和要求,选择适合的切削方式和刀具。
不同的材料可能需要不同的切削参数和切削刃,需要根据实际情况进行调整。
2.考虑机器的稳定性和刚性。
在机架设计和选材时,要保证机器具备足够的稳定性和刚性,避免在工作时产生振动和变形。
3.选择合适的传动比和传动元件。
根据工件的大小、材料等要求,确定合适的传动比和传动元件,以确保机器具备足够的切削力和转速。
打孔机的结构原理设计

打孔机的结构原理设计打孔机是一种用于在材料上进行孔设计或加工的设备。
它具有高效率、精确度高、操作简单等特点。
打孔机的结构原理设计主要包括机身结构、传动系统、控制系统等几个方面。
一、机身结构:打孔机的机身结构通常由底座、立柱、主轴箱、工作台等组成。
1.底座:底座是打孔机的基础结构,一般采用铸造或焊接方法制成,以确保机器的稳定性和刚性。
底座上通常设有调节螺钉,可以调节机器的水平度和平稳度。
2.立柱与横梁:立柱与横梁是打孔机的固定和支撑结构。
立柱在底座上固定,而横梁则与立柱连接,支撑主轴箱和工作台。
3.主轴箱:主轴箱是打孔机的核心部件,它包含主轴、滑座、推杆等。
主轴通过滑座与横梁相连,可以实现上下运动。
主轴上设有夹具,用于夹持刀具,完成孔的加工。
4.工作台:工作台是打孔机的工作平台,位于主轴下方。
工作台具有平整的工作面和固定夹具,用于放置待加工材料。
在工作台上通常还设有定位孔或T型槽,以方便固定材料。
二、传动系统:打孔机的传动系统是控制主轴运动的关键部件,主要包括电机、皮带、链条、齿轮等。
1.电机:电机是驱动主轴旋转的动力源。
通常采用交流电机或直流电机,其功率和转速根据打孔机的需求进行选择。
2.皮带与链条:通过皮带或链条将电机与主轴箱连接起来,实现转动的传递。
皮带与链条具有一定的弹性和韧性,可以缓解由于转动不平稳造成的冲击和振动。
3.齿轮:齿轮是打孔机传动系统中常用的传动装置。
通过不同规格的齿轮组合,可以实现主轴的多速度调节,满足不同孔径的加工需求。
三、控制系统:打孔机的控制系统用于控制机器的运行和加工过程,主要包括控制面板、传感器、液压系统等。
1.控制面板:控制面板上设有开关、按钮、旋钮等,用于启动和停止机器,调节主轴的转速和运动方向,控制加工步骤等。
面板上通常还设有显示屏,用于显示加工参数和工艺状态。
2.传感器:传感器用于监测机器的工作状态和加工过程。
例如,通过光电传感器可以实现自动定位和自动停止,确保孔的准确定位和加工质量。
全套管钻机方案

全套管钻机方案简介全套管钻机是一种用于在井下钻探油气井的工程设备。
与传统的常规钻机相比,全套管钻机采用了全套管钻探技术,可以实现一次下井就能完成套管下套作业和钻井作业,提高作业效率和钻井安全性。
本文将介绍全套管钻机的工作原理、主要组成部分、优势和应用领域,以及全套管钻机方案的选型要点和市场发展趋势。
工作原理全套管钻机是一种设备,可以在井下进行连续的套管下套作业和钻井作业。
其工作原理如下:1.钻机安装在一个钻井井架上,通过钻杆将动力传递到钻头。
2.钻井井架提供支撑和稳定,以确保钻机的正常运行。
3.钻头通过旋转和推进的方式将钻头推入地下,同时使用冲洗液将岩屑带出井口。
4.钻井井架的高度可以根据钻井深度进行调整,以适应不同的作业需求。
5.钻进过程中,会逐段施加套管,形成井套,并逐段固井。
6.钻进到目标层后,可以进行开拓性试井或水力压裂等作业。
主要组成部分全套管钻机包括以下主要组成部分:1.钻机底架:提供给钻机安装和支撑的基础结构。
2.钻机井架:提供支撑和稳定的结构,包括支腿、千斤顶和调整机构等。
3.钻杆:连接钻机和钻头,并将动力传递到钻头。
4.钻头:用于在地下钻探的工具,可以选择不同类型的钻头来适应不同地质条件。
5.冲洗液系统:用于将岩屑从井底带到井口的系统,包括泥浆泵、搅拌器和相关管道等。
6.控制系统:负责钻机操作和监控的系统,包括控制台、传感器和计算机等。
7.钻井辅助工具:包括测井仪、电缆、防喷器等。
优势和应用领域全套管钻机相比传统的常规钻机有以下优势:1.提高钻井作业效率:全套管钻机可以在一次下井完成套管下套和钻井作业,减少了下井次数,提高了作业效率。
2.减少作业风险:全套管钻机实现了井下作业的自动化和连续化,减少了人工操作,从而降低了作业风险。
3.适应复杂地质条件:全套管钻机可以选择不同类型的钻头,以适应不同地质条件下的钻井作业。
4.减少环境污染:全套管钻机的冲洗液系统可以循环使用,减少了废液排放,降低了对环境的污染。
打孔机结构原理设计机械系统设计大作业

打孔机结构原理设计机械系统设计大作业本文旨在介绍打孔机的重要性和使用背景,并说明本次大作业的目的和意义。
打孔机是一种常见的机械设备,用于在纸张、塑料、金属等材料上制作孔洞。
它在日常生活和工业生产中具有广泛的应用。
例如,在办公室里,我们经常使用打孔机来整理文件并将它们放入文件夹中。
在制造业中,打孔机被用于制造零件、产品组装和材料处理等领域。
本次大作业的目的是设计一个打孔机的结构原理和机械系统。
通过深入研究打孔机的工作原理和内部结构,我们可以更好地理解和掌握该设备的设计和使用。
这将有助于加深我们对机械系统设计和工程原理的理解,并为我们未来在相关领域的职业发展奠定坚实的基础。
在本文中,我们将详细介绍打孔机的工作原理、结构设计和机械系统设计的关键要点。
我们还将探讨与打孔机相关的材料选择、零件制造和装配过程等方面的问题。
最后,我们将总结本次大作业的主要研究成果和所获得的经验教训。
希望通过本次大作业的完成,我们能够提高我们的机械设计和工程能力,并为将来在机械制造和相关领域取得更大的成就打下基础。
详细说明打孔机的结构组成,包括基本部件、传动系统和控制系统等方面。
基本部件:框架:打孔机的结构基础,支撑和固定各个组件。
工作台:用于固定待打孔材料,保持其稳定性。
打孔模具:用于实现打孔操作,包括孔径和排列等设计参数。
按钮/触发器:用于控制打孔机的启停和操作。
传动系统:电动机:提供动力,驱动打孔机的运转。
皮带/链条传动:将电动机的转动传递给打孔模具,实现打孔操作。
控制系统:电路板:控制打孔机的各个功能和动作。
开关:用于手动控制打孔机的启停和操作。
打孔机的结构原理设计是通过上述的基本部件、传动系统和控制系统的合理组合和设计来实现打孔功能的。
在设计过程中,需要考虑打孔机的稳定性、操作性和安全性等因素,确保其能够有效地完成打孔任务。
本文旨在阐述打孔机的机械系统设计,包括结构设计、优化设计和性能参数确定等方面。
结构设计打孔机的结构设计应考虑以下几个方面:打孔机框架:选择适当的材料和结构形式,以确保机械的稳定性和刚度。
打孔机的结构原理设计
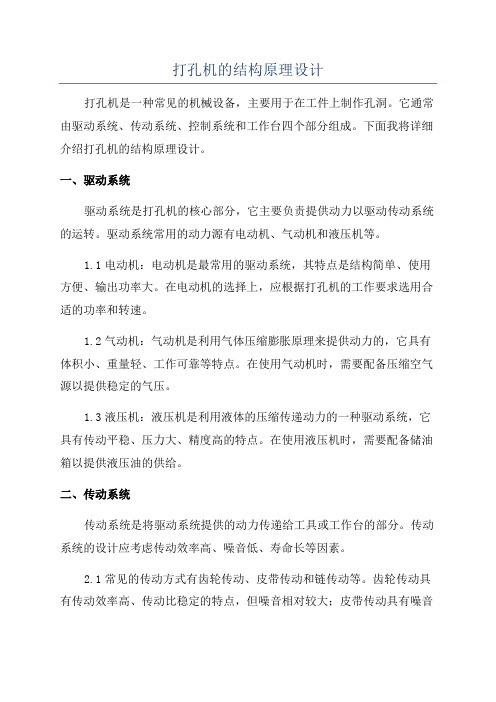
打孔机的结构原理设计打孔机是一种常见的机械设备,主要用于在工件上制作孔洞。
它通常由驱动系统、传动系统、控制系统和工作台四个部分组成。
下面我将详细介绍打孔机的结构原理设计。
一、驱动系统驱动系统是打孔机的核心部分,它主要负责提供动力以驱动传动系统的运转。
驱动系统常用的动力源有电动机、气动机和液压机等。
1.1电动机:电动机是最常用的驱动系统,其特点是结构简单、使用方便、输出功率大。
在电动机的选择上,应根据打孔机的工作要求选用合适的功率和转速。
1.2气动机:气动机是利用气体压缩膨胀原理来提供动力的,它具有体积小、重量轻、工作可靠等特点。
在使用气动机时,需要配备压缩空气源以提供稳定的气压。
1.3液压机:液压机是利用液体的压缩传递动力的一种驱动系统,它具有传动平稳、压力大、精度高的特点。
在使用液压机时,需要配备储油箱以提供液压油的供给。
二、传动系统传动系统是将驱动系统提供的动力传递给工具或工作台的部分。
传动系统的设计应考虑传动效率高、噪音低、寿命长等因素。
2.1常见的传动方式有齿轮传动、皮带传动和链传动等。
齿轮传动具有传动效率高、传动比稳定的特点,但噪音相对较大;皮带传动具有噪音低、安装调整方便的特点,但传动效率相对较低;链传动则是介于前两者之间,具有传动平稳、寿命长的特点。
三、控制系统控制系统是打孔机的智能部分,它负责对打孔机的运行和操作进行控制。
控制系统的设计应考虑操作简便、精度高、稳定性强等因素。
3.1控制方式:控制方式可采用手动方式或自动方式。
在手动方式下,操作人员需要通过按钮或手柄控制打孔机的启停、前进后退等动作;在自动方式下,可通过编程或传感器等方式实现自动控制。
3.2控制元件:控制元件主要包括电控部分和液压控制部分等。
在电控部分,常用的元件有继电器、PLC、触摸屏等;在液压控制部分,常用的元件有液压阀、液压泵等。
四、工作台工作台是打孔机进行打孔操作的平台,它需要具有稳定性和可调节的特点,以适应不同工件的加工需求。
打孔机的结构原理设计[机械系统设计大作业]
![打孔机的结构原理设计[机械系统设计大作业]](https://img.taocdn.com/s3/m/6129f60dccbff121dd3683bd.png)
AB=8.53 BC=84.42 CD=60 DA=60 CE=40 EF=8
该尺寸可以满足设计要求,即滑块的左右运动为40,ABCD的极位夹角为12度。
图 9
2.凸轮摆杆机构的设计:
由进刀规律,我们设计了凸轮摆杆机构,又以齿轮齿条的啮合来实现刀头的上下
运动;用凸
轮摆杆机构和圆弧形齿条所构成的同一构件,凸轮摆杆从动件的摆动就可以实现
机械系统设计
课程作业
(打孔机的设计)
一、设计任务书
编号
名称
半自动打孔机
设计单位
起止时间
2015.11
主要设计人员
设计费用
1
功能
主要功能:实现工件自动打孔
2
适应性
对象:需要打孔的工件
环境:远离振动源;要有电源
3
性能
动力:转速为1450 r/min,功率N = 1.2 kW
4
可靠度
整机99.9%
5
使用寿命
方案一:A1+B3+C3+D3+E2
方案二:A1+B2+C1+D3+E2
定轴轮系传动;传动比很大,要用多级传动。
由于在空间上轴与轴之间的距离较大,但四杆的曲柄滑块机构行程太小。故优先选用六杆机构
综合评价,所以选择方案一
九、画出方案简图
1.减速机构:
由于电动机的转速是1450r/min,而设计要求的主轴转速为2r/min,利用行星轮进行大比例
2:对大功率传动,应优先考虑传动的效率,降低运转费用和维修费用。
3:当执行机构要求变速时,若能与动力机调速比相适应,可直接连接或采用定传动比的传动装置;当执行机构要求变速范围大,用动力机调速不能满足机械特性和经济性要求时,则应采用变传动比传动;除执行机构要求连续变速外,尽量采用有级变速。
水平定向钻进扩孔器结构设计方法及新产品设计

水平定向钻进扩孔器结构设计方法及新产品设计水平定向钻进扩孔器结构设计方法及新产品设计水平定向钻进铺管是一种发展迅速、技术先进、应用广泛的非开挖施工技术,可用于铺设或更新市政公用行业的各种管道。
目前在水平定向钻进铺管中,大量的钻进时间消耗在扩孔这一关键工序。
适当的扩孔器形状、尺寸对其工作过程中所受阻力、阻力矩和消耗功率的大小有重要影响,直接关系到水平定向铺管的工作效率。
由于国内水平定向钻进铺管钻具系统的设计缺乏相应的设计理论和方法、产品创新程度低,市面上钻具品种单一、适应性差,这严重影响水平定向钻进铺管的效率和应用。
针对上述现象对水平定向钻进铺管中的扩孔钻具进行研究:首先,总结各种扩孔器的形状及地层的适应性,提出扩孔器结构设计理论。
其次,对扩孔钻具钻进时的工作原理、结构设计的相关参数进行详细论证,提出扩孔钻具的设计思路及主要参数的取值方法。
最后,按照新型扩孔器设计需要结合参数设计方法得出该型扩孔器主要的设计参数进行取值。
在收集国内外大量的相关技术资料基础上,运用类比法对现有扩孔器的优缺点进行分析;运用土力学基础对土体的压缩性和切削原理进行研究;分析扩孔钻头在扩孔过程中的工作机理和受力,结合岩土钻掘基本理论、机械设计最优化理论和数学计算对扩孔器结构尺寸进行研究得到以下成果和结论:1、设计出适应软土层的扩孔器—翼片挤压式扩孔钻头,该型扩孔钻头特点是:排粉能力强,具有导向,切削,挤密、压实钻孔壁的功能。
2、提出扩孔钻头参数取值方法○1通过对保证钻杆柱安全工作的孔身极限弯强、扩孔钻具顺利通过孔身的极限弯强和保证管道安全工作的孔身极限弯强进行计算论证得出扩孔钻头的长度;○2通过计算得出土层塑性圈的直径,根据土层的压缩曲线得出最优厚度,从而根据地层性质调整滚轮轴线的倾角;○3通过分析切削具的切削速度和功率消耗之间的关系,得出在相同工作面的情况下翼片的最优倾角。
3、提出扩孔钻头工作中所需回拖力、扭矩以及钻机功率等参数取值的计算公式,为钻机选型提供了依据。
- 1、下载文档前请自行甄别文档内容的完整性,平台不提供额外的编辑、内容补充、找答案等附加服务。
- 2、"仅部分预览"的文档,不可在线预览部分如存在完整性等问题,可反馈申请退款(可完整预览的文档不适用该条件!)。
- 3、如文档侵犯您的权益,请联系客服反馈,我们会尽快为您处理(人工客服工作时间:9:00-18:30)。
目录一、绪论......................................................................................................... 错误!未定义书签。
1.1打孔机简介与种类.......................................................................... 错误!未定义书签。
1.2打孔机得发展情况.......................................................................... 错误!未定义书签。
1.3.研究得背景与意义......................................................................... 错误!未定义书签。
二、总体设计方案确定及动力元件选择................................................... 错误!未定义书签。
2.1总体设计的要求.............................................................................. 错误!未定义书签。
2.2机型与传动形式得选择.................................................................. 错误!未定义书签。
2.2.1机型得选择............................................................................ 错误!未定义书签。
2.2.2传动形式的选择.................................................................... 错误!未定义书签。
2.3 打孔机的整体布局......................................................................... 错误!未定义书签。
2.3.1打孔机得总体布局................................................................ 错误!未定义书签。
2.3.2打孔机的驱动和动力输入方式............................................ 错误!未定义书签。
2.3.3打孔机整体参数确定............................................................ 错误!未定义书签。
2.4钻机的功能单元及实现方法.......................................................... 错误!未定义书签。
2.4.1钻具........................................................................................ 错误!未定义书签。
2.4.2回转机构................................................................................ 错误!未定义书签。
2.5 电动机的选型................................................................................. 错误!未定义书签。
三、减速装置设计..................................................................................... 错误!未定义书签。
3.1传动比确定及各级传动比分配...................................................... 错误!未定义书签。
3.2 运动参数及动力参数计算............................................................. 错误!未定义书签。
3.2.1 计算各轴转速....................................................................... 错误!未定义书签。
3.2.2 计算各轴的功率................................................................... 错误!未定义书签。
3.2.2 计算各轴的功率................................................................... 错误!未定义书签。
3.3 齿轮传动的设计计算..................................................................... 错误!未定义书签。
3.3.1 第一级齿轮传动副的设计计算........................................... 错误!未定义书签。
3.3.2第二级齿轮传动副的设计计算............................................ 错误!未定义书签。
3.3.3 三级齿轮传动副的设计计算............................................... 错误!未定义书签。
3.4 传动轴的设计................................................................................. 错误!未定义书签。
3.4.1第一传动轴的设计及计算.................................................... 错误!未定义书签。
3.4.2第二轴的结构设计及计算.................................................... 错误!未定义书签。
3.4.3三轴的结构设计及计算........................................................ 错误!未定义书签。
3.5减器箱体结构尺寸.......................................................................... 错误!未定义书签。
3.5.1结构尺寸................................................................................ 错误!未定义书签。
3.5.2油标........................................................................................ 错误!未定义书签。
3.5.3通气罩.................................................................................... 错误!未定义书签。
3.5.4.螺塞........................................................................................ 错误!未定义书签。
四、链传动设计............................................................................................. 错误!未定义书签。
4.1链传动的特点.................................................................................. 错误!未定义书签。
4.2链的类型.......................................................................................... 错误!未定义书签。
4.3链传动选择...................................................................................... 错误!未定义书签。
五、支架的设计............................................................................................. 错误!未定义书签。
5.1.机架设计准则................................................................................. 错误!未定义书签。
5.2.支架的效核..................................................................................... 错误!未定义书签。
5.2.1 ................................................................................................. 错误!未定义书签。
5.3梁的效核.......................................................................................... 错误!未定义书签。
5.3.1梁的强度效核........................................................................ 错误!未定义书签。
5.4传动轮的设计.................................................................................. 错误!未定义书签。