风力机叶轮设计
风力发电机组的叶轮设计优化与性能分析

风力发电机组的叶轮设计优化与性能分析1. 引言风力发电作为一种可再生能源的重要形式,被广泛应用于电力供应系统。
叶轮作为风力发电机组中的核心部件,直接影响着发电机组的性能和效率。
本文旨在通过对风力发电机组叶轮的设计优化与性能分析,提出一种能够提高发电效率的叶轮设计方案。
2. 风力发电机组的工作原理风力发电机组利用风能将风动能转化为机械能,然后通过发电机将机械能转化为电能。
叶轮作为风力发电机组中的核心部件,承担着捕捉和利用风能的重要任务。
叶轮优化设计的目标是最大化风能的转化效率,提高发电机组的发电量。
3. 叶轮设计优化3.1 叶片数目和形状设计叶片数目和形状直接影响着风力发电机组的功率转化性能。
一般而言,叶片数目越多,转化效率越高。
然而,叶片数目过多会增加制造成本并增加风力发电机组的重量。
因此,需要综合考虑叶片数目和形状的设计,找到一个平衡点。
3.2 叶片长度和宽度设计叶片长度和宽度的设计也是叶轮设计中的重要因素。
叶片长度越长,捕捉风能的面积越大,风力发电机组的转化效率越高。
然而,过长的叶片会增加风力发电机组的叶轮重量,并对叶轮结构造成一定的负荷。
因此,需要对叶片长度和宽度进行优化设计。
3.3 叶片材料选择叶轮受到来自空气流动的巨大压力和弯曲力的影响,因此在叶片材料的选择上需要考虑其强度、轻量化和耐腐蚀性。
目前常用的叶片材料有玻璃纤维增强塑料(GFRP)和碳纤维增强塑料(CFRP)等。
在叶片材料的选择中,需要综合考虑材料的力学性能和经济性,以实现叶轮结构的优化设计。
4. 叶轮性能分析4.1 基于流体动力学的模拟分析通过建立风力发电机组的叶轮流体动力学模型,可以对叶轮的流场分布和压力分布进行模拟分析,了解叶轮在风力作用下的性能表现。
这可以为叶轮的优化设计提供有力的依据。
4.2 发电机组的发电量模拟叶轮是风力发电机组中能量转化的关键部件,其性能的优化直接影响发电机组的发电效率。
通过基于叶轮性能和风能资源的数据,可以进行发电量的模拟计算,评估叶轮优化设计的效果。
600kW变桨距风力机叶轮优化设计及数值计算

叶轮实度为 : 普朗特 叶尖损失 因子为
F= 2
 ̄
1 . 型的确 定 . 2翼 1
在 翼型 的选 择上 ,本 文设计 的叶片各 截面采用 同一类翼
型——F A系列翼 型。 F
ac 。 ( R rc s 一 B - r
-
) 1
订
c= li ,C o Ic n 一 s4 C= to6 Cs 6 .C cs + a n i
一
11 风 轮 直径的 确定 .1 .
: 一 一
D/ = 、
式 中: 功率 系数 , 一 一般墩 04 — .5 .3 0 ; 4
lb 4 s 6 o ̄ + Fi cs n b 其中 :
力一传动系统效率 , 。 一般取 0 2 .; 9
钾 发 电机效率 , 厂一 一般取 09 。 . 5
(N r w s m o te nel nvr t,i n7 0 7 ,hn ) S a ga j o n nvri , a ga 2 0 3 ,hn ) ’ot et P l eh ia U i sy ' 10 2 ia ( h nh ii t gU i sy h nh i 0 0 0C ia h e y ei X a C a o e tS
=
1 设计 方法简介
11 量 叶素设计 方法 ,动
风力机 叶轮设计主要是确定 叶片数 、 直径 、 翼型 、 安装角和 弦长 5个参 数。
4 b
-
x
6r 铬 =t an c a
口 C
现代风力机 叶尖速 比较高 , 采用三叶片叶轮 。
1n 4 s 2 一 Fi d n ̄
通过分析整个加工的生产过程厦其工作原理进行了多边形箍筋设备的整机结构设计改变了传统箍筋方式的非自动化和不科学的现状使得整个箍筋过程实现了自动化提高了生产效率及箍筋的生产质量
风力机叶片设计的新方法_包耳

( 7)
收稿日期 : 2004- 04- 29; 修订日期 : 2004- 09- 14 基金项目 : 国家民委重点科研资助项目 ( 200116) 作者简介 : 包耳 ( 1956- ) , 女 , 上海人 , 工学士 , 副教授 , 研究方向 : 机械设计及工程材料。
2
一种新的设计方法
下面考虑干涉因子和 翼型 阻力 , 从能 量的 角度 入手 , 对桨 叶气动外形重新进行计算。 根据 Glauer t 环动量理论可初步推算 a、 a c 和 U 值的大小 , 桨叶的功率系数可表示为 :
Cp = $P 1 3 Q v $A 2 = 1 Q w 2 r 8 BC ( Cl s in U - Cd cos U )$ r 2 = 1 3 Q v 2P r dr 2
2005 年 2 月
ac BC Cl sin U- Cd cos U = # 1 + ac 8P r s in U cos U
包耳 , 等 : 风力 机叶片设计的新方法 ( 8)
25
根据所要求的输出功率 , 将式 ( 15) 、 ( 17 ) 作为约束 条件 , 对 式 ( 16) 进行优化 , 即可算得桨叶各个断面的弦长值。 在风力机桨叶翼型参数的设计 过程中 , 各 个参数 的变化 都 会对其它参数的设计产生影响。 在设计 中本着 能够使 单位叶 素 有最大的功率利用系数的原则 , 来选择翼型参数。 贝兹理论仅把 空 气 流动 考 虑成 一 维定 常 流 动 , 对 翼 型 阻 力、 叶梢阻力都没有考 虑 , 仅能 从总 体上 对风 轮性 能确 定一 个 大致的范围 [ 5] 。 Glauert 环动 量理论、 环动 量优化理论、 Wilson 理论分别 考 虑了涡流运动、 叶梢损失的影响 , 但此影响仅在 计算干涉因 子 a 和 ac 时加以考虑 , 在 优化弦 长 C 时 仍采 用动 量理 论的 推导 公 式 , 仅保证了功率系数 为最大 值 , 而 忽略 了所 设计 风力 机实 际 输出功率的限制 , 因而设计的弦长或升力系数值普遍偏大 [ 6] 。 这里提出的设计方法 , 把 CC l 值 的大小与 实际功 率联系 起 来 , 在考虑涡流运动、 翼型阻 力、 叶 片数等 诸多 因素后 , 以保 持 叶轮实度最小 为最 终 条件 进行 优 化 , 在 满 足性 能 要求 的 前 提 下 , 极大地降低了翼弦的取值。
风力发电机组叶轮叶片的改进设计
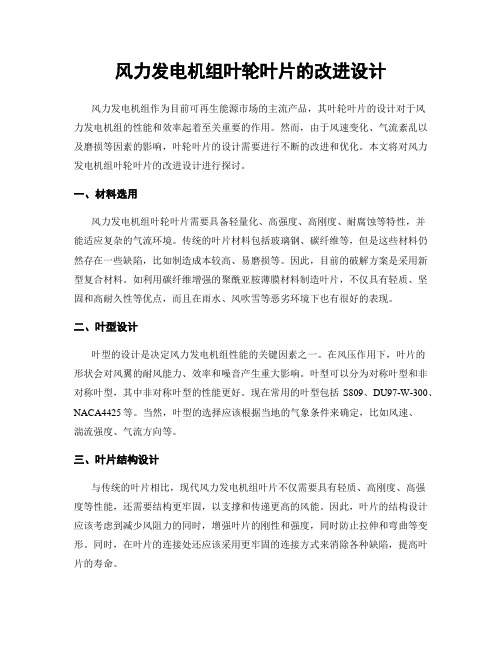
风力发电机组叶轮叶片的改进设计风力发电机组作为目前可再生能源市场的主流产品,其叶轮叶片的设计对于风力发电机组的性能和效率起着至关重要的作用。
然而,由于风速变化、气流紊乱以及磨损等因素的影响,叶轮叶片的设计需要进行不断的改进和优化。
本文将对风力发电机组叶轮叶片的改进设计进行探讨。
一、材料选用风力发电机组叶轮叶片需要具备轻量化、高强度、高刚度、耐腐蚀等特性,并能适应复杂的气流环境。
传统的叶片材料包括玻璃钢、碳纤维等,但是这些材料仍然存在一些缺陷,比如制造成本较高、易磨损等。
因此,目前的破解方案是采用新型复合材料。
如利用碳纤维增强的聚酰亚胺薄膜材料制造叶片,不仅具有轻质、坚固和高耐久性等优点,而且在雨水、风吹雪等恶劣环境下也有很好的表现。
二、叶型设计叶型的设计是决定风力发电机组性能的关键因素之一。
在风压作用下,叶片的形状会对风翼的耐风能力、效率和噪音产生重大影响。
叶型可以分为对称叶型和非对称叶型,其中非对称叶型的性能更好。
现在常用的叶型包括S809、DU97-W-300、NACA4425等。
当然,叶型的选择应该根据当地的气象条件来确定,比如风速、湍流强度、气流方向等。
三、叶片结构设计与传统的叶片相比,现代风力发电机组叶片不仅需要具有轻质、高刚度、高强度等性能,还需要结构更牢固,以支撑和传递更高的风能。
因此,叶片的结构设计应该考虑到减少风阻力的同时,增强叶片的刚性和强度,同时防止拉伸和弯曲等变形。
同时,在叶片的连接处还应该采用更牢固的连接方式来消除各种缺陷,提高叶片的寿命。
四、尾流影响多台风力发电机组并网构成风场,在这种情况下会产生大量的尾流,给设备的耐久性和维护带来很大的挑战。
在叶轮叶片的设计中应该充分考虑尾流的影响,通过优化叶片的结构和尺寸,减少尾流对叶片的影响,从而提高设备的可靠性和稳定性。
五、结论综上所述,每一次机组的重新设计和改进都是在当时的技术状态下取得的最佳结果,希望借助技术的不断发展,让风力发电机组叶轮叶片设计更加优化。
1011第十-十一讲 叶片设计理论

N max
1 2
C
p
sv13
34
而
1 2
sv1正是风速为
v1
的风能,故
Nmax CpT
Cp =0.593说明风吹在叶片上,叶片所能获得的最
大功率为风吹过叶片扫掠面积风能的59.3%.贝茨
理论说明,理想的风能对风轮叶片做功的最高效率
是59.3%。
35
通常风力机风轮叶片接受风能的效率达不到59.3%, 一般设计时根据叶片的数量、叶片翼型、功率等 情况,取0.25~0.45。
' 1 z
2
42
因为, 可得:
a' (Z ) /
Z (a'1)
气流对叶轮的角速度
' 1 (1 a' )
2
(2)
43
三、动量理论
图9 动量理论简图
44
在叶轮上r--r+dr的环域内应用动量定理(如图 9),则风作用在该环域上的轴向推力为
26
s
v1
s1
v
s2 v2
图7 贝茨(Betz)理论计算简图
vv12
s
—叶片前的风速;
v
—风经过叶片后的速度; —风经过叶片时的面积;
ss12
—风经过叶片时的速度; —叶片前风速的面积; —风经过叶片后的面积
27
分析一个放置在移动的空气中的“理想风轮”叶 片上所有受到的力及移动空气对风轮叶片所做的 功。
22
当空气经过风轮圆盘时显然有静压降存在,以至 于空气离开风轮时其压力会小于大气压力。空气 流就会以减小的速度和静压向下游前进——这个 气流域被称为尾流。
风力机叶片设计及翼型气动性能分析

风力机叶片设计及翼型气动性能分析风力机叶片是风力发电机的核心部件之一,其设计和翼型选择对风力机的发电效率、噪音和寿命等都有着非常重要的影响。
本文将介绍风力机叶片的设计及翼型气动性能分析。
一、叶片设计原理风力机叶片的设计目的是将大气中的风能转换成旋转能,并将其通过转轴传递给发电机,从而产生电能。
因此,叶片的设计主要围绕以下几点展开:1. 创造足够的扭矩:风力机的转子需要达到一定的转速才能发电,而叶片的弯曲和扭矩对于旋转速度的影响至关重要。
设计中需要选择合适的曲线形状和长度来实现理想的扭矩和转速。
2. 保证叶片的强度和稳定性:因叶片在高速旋转状态下会受到巨大的惯性力和风力力矩的作用,因此其材料和结构要足够坚固和稳定,以避免可能的断裂等事故。
3. 提高叶片的气动效率:叶片的气动效率是指其转化风能的能力,通常可以通过优化翼型、减小阻力、降低风阻等方法来提高。
二、叶片设计步骤1. 选定叶片长度:叶片长度通常是根据风力机的规格和性能要求来确定的,也可以根据标准长度来选择。
2. 选择翼型:翼型是叶片的重要组成部分,其形状和性能决定了叶片的阻力和气动效率。
目前,常用的翼型有NACA0012、NACA4415等,根据实际需求来选择。
3. 确定叶片曲线:叶片的曲线是决定扭矩和转速的关键因素,可以通过实验或模拟方法得到合适的曲线形状。
4. 优化叶片的结构:结构设计主要涉及到叶片的强度和稳定性,通常需要进行材料选择、计算等工作以保证叶片的安全性和寿命。
5. 模拟叶片气动特性:叶片的气动特性可以通过流场模拟、试验等方式来获取,可以根据实际需求来对叶片进行调整以达到理想的效果。
三、翼型气动性能分析翼型气动性能是指翼型在气流中运动时产生的力和力矩,其中,升力和阻力是翼型气动力的主要组成部分。
通过分析翼型气动性能,可以选择最优化的翼型来设计叶片。
1. 升力和阻力翼型的升力和阻力是由翼型形状、气流速度、攻角等因素共同决定的。
实际上,翼型的气动性能曲线通常都是非线性的,其升力和阻力特性会随着攻角的变化而不断变化。
风力机叶片力学分析报告
1 V2 − (3‐13) 2 2V1
1 。但是 2
上式表明:如果风轮吸收风的全部能量,即 V2 = 0 ,则 a 有一个最大值, a = 实际情况下,风轮只能吸收风能的一部分,所以 a 〈 。 由式(3‐9)和(3‐12)可得: T = 引入风轮轴向力系数 CT CT =
3.1.1 经典的动量理论 经典的动量理论定义了一个通过风轮平面的理想流管,并假设: ⑴气流是不可压缩的均匀定常流; ⑵风轮简化为一个轮盘; ⑶轮盘上没有摩擦力; ⑷风轮流动模型简化为一个单元流管; ⑸风轮前后远方的气流静压相等; ⑹轴向力沿轮盘均匀分布。
图 3.1 风轮流动的单元流管模型 考虑风力机轴向的动量变化,可得到作用在风轮上的轴向力(推力) T 为:
F=
1 ρ Cr Sv 2 (2‐3) 2
式中 S ——翼展面积,等于弦长×翼展长度; Cr ——总的气动系数。 该作用力可以分为两部分:一个是平行于气流速度 v 的分力——阻力 D ;一个是垂直 r 于气流速度 v 的分力——升力 L 。 D 与 L 可分别表示为
翼型中线—从前缘点开始,与上、下表面相切诸圆之圆心的连线,一般为曲线;
f ——翼型中线最大弯度;
f ——翼型相对弯度, f =
α ——攻角,是来流速度方向与弦线间的夹角;
f ; l
φ0 ——零升力角,它是弦线与零升力线间的夹角;
φ ——升力角,来流速度方向与零升力线间的夹角。
α = φ + φ0 (2‐1)
& (V1 − V2 ) (3‐1) T =m
式中, V1 ——风轮前来流速度( V1 = V∞ ) ;
V2 ——风轮后尾流速度;
& ——单位时间流经风轮的空气质量流量,可表示为 m
叶轮螺母的设计原理
叶轮螺母的设计原理
叶轮螺母是一种用于传动力量的装置,常用于离心泵、风力发电机等设备中。
其设计原理主要包括以下几个方面:
1. 叶轮形状设计:叶轮螺母的形状通常为螺旋状,可以将旋转运动转化为推进力。
叶轮的形状和数量会直接影响到传动力量的大小和效果。
2. 螺母设计:螺母是叶轮的核心零件,其设计要考虑到叶轮的旋转速度、传动力量和使用环境等因素。
通常采用高强度材料制作,以确保其能够承受高速旋转和大力量的作用。
3. 叶片设计:叶片是叶轮的关键部分,起到推动流体或空气的作用。
其设计要考虑到叶轮的流体力学特性,如叶片的形状、倾角、弯曲等参数会直接影响到传动力量和效率。
4. 轴承设计:叶轮螺母需要在旋转过程中保持稳定,轴承在其中起到支撑和减小摩擦力的作用。
轴承的设计要考虑到叶轮的旋转速度、负载和使用寿命等因素。
总之,叶轮螺母的设计原理是基于流体力学和机械传动原理,通过合理的叶轮形状、螺母结构、叶片设计和轴承安装等措施,实现将旋转运动转化为推进力的目的。
同时,还要满足材料的强度要求、工作环境的要求,以保证叶轮螺母的安全
可靠运行。
风力发电机旋转叶轮模态分析
( o lg o Me h nc l g n e ig n io o g,Xij n Ag iut r l Cl e f e c a ia En ie rn a d Ja t n ni g a r l a Un v riy c u ie st ,Ur mq u i
自由度 , 用 叶根 固定 连接 于轮 毂 的边 界条 件 , 应 叶片 的质量 矩 阵和 刚度矩 阵是 5 ×5 , 入 方 程可 以计 4 4代
可 以看 出, 每个节 点 的变形量均 归一 化处 理 , 假设 并
叶尖 节点 的位移 量是 1 。
表 2是某 1 5MW 风 力发 电机 的叶片 前 6阶摆 .
t o. w
Ke r s: m o lo h o o ;n t r lf e e c y wo d da ft e r t r a u a r qu n y;m u t— d yn m is;d a i tf e n libo y d a c yn m cs if ni g
叶 片是风 力发 电机 中关 键 零 部件 之一 , 结 构 其
关 系 着 整 个 风 力 发 电 机 的 平 稳 运 行 。兆 瓦 级 风 力 发
并 利用 Malb软件 对某 1 5MW 风力 发 电机 单 个 t a .
叶片和 叶轮 的振动 模 态进 行 了仿 真分 析 , 将 计 算 并
风 力发 电机旋 转 叶轮模 态 分析
汪 萍萍 , 新 维 崔
( 疆农业大学 机械交通学院 , 鲁木齐 新 乌 摘 805) 3 0 2
要 : 在 多体 动 力 学 理 论 的基 础 上 , 于 有 限 元 法 对 叶 片 进行 离散 化 , 立 了 风 力 发 电机 柔 性 叶 片 的 动力 学 方 基 建
风机叶轮强度计算
风机叶轮强度计算全文共四篇示例,供读者参考第一篇示例:风机叶轮是风机中最重要的部件之一,它直接影响到风机的性能和稳定性。
叶轮强度计算是设计和制造风机叶轮时必须进行的重要工作之一。
本文将详细介绍风机叶轮强度计算的基本原理、计算方法和注意事项。
一、叶轮强度计算的基本原理风机叶轮在工作过程中承受风力的作用,需要具备足够的强度来抵抗风力的作用,以保证叶轮的安全运行。
叶轮强度计算的基本原理是根据力学原理和叶轮结构特点,通过计算得出叶轮在不同工况下的受力情况,进而确定叶轮的强度是否满足设计要求。
1. 叶轮的受力分析叶轮在工作过程中受到风力和旋转惯性力的作用,需要通过受力分析来确定叶轮在不同工况下的受力情况。
根据叶轮的结构和受力情况,可以采用有限元分析等方法对叶轮进行受力分析,得出叶轮的应力和变形情况。
通过叶轮的受力分析结果,可以计算出叶轮的应力和变形情况,进而确定叶轮的强度是否满足设计要求。
叶轮的强度计算一般包括弯曲强度、拉伸强度、剪切强度等方面的计算,需要根据叶轮的结构和受力情况进行综合考虑。
1. 叶轮的设计要符合叶轮的工作环境和工作要求,需考虑叶轮的材料、结构和制造工艺等因素。
2. 在叶轮强度计算中,需要充分考虑叶轮在不同工况下的受力情况,避免出现强度不足的情况。
3. 叶轮的强度计算需要遵循相关的标准和规范,确保计算结果准确可靠。
4. 需要进行叶轮的强度验证测试,以确保叶轮的实际强度与计算结果相符。
风机叶轮强度计算是设计和制造风机叶轮时不可忽视的重要工作,只有通过科学的叶轮强度计算,才能确保叶轮在工作过程中具有足够的强度和稳定性,从而保证风机的安全运行和高效性能。
希望本文能对您了解风机叶轮强度计算有所帮助。
第二篇示例:风机是一种常见的动力设备,用来将风力转化为机械能,常用于工业、农业和民用领域。
而风机的核心部件之一就是叶轮,它负责将风能转化为机械能。
叶轮必须具备足够的强度来承受来自气流的巨大压力和力量,否则容易发生断裂、破裂等危险情况。
- 1、下载文档前请自行甄别文档内容的完整性,平台不提供额外的编辑、内容补充、找答案等附加服务。
- 2、"仅部分预览"的文档,不可在线预览部分如存在完整性等问题,可反馈申请退款(可完整预览的文档不适用该条件!)。
- 3、如文档侵犯您的权益,请联系客服反馈,我们会尽快为您处理(人工客服工作时间:9:00-18:30)。
5位数翼型族 美国NACA 6位数翼型族 德国DVL 1、7、8族等 各种修改翼型
英国RAF
命名规则:NACA XYZZ X-----------相对弯度 Y------------最大弯度位置 ZZ----------相对厚度
苏联ЦΑΓИ
叶片优化设计方法 Matlab参与计算 右侧图片的设计过程是按照Glauert 理论设计模型,Willson设计模型设计
案例-------------大型离岸发电机 位于挪威西南部海岸附近卡莫伊岛(Karmoey)10公里处。 浆叶尺寸达到75米,(可以套下整个A380客机)制造方式为在一个巨 大的模具中采用环氧树脂、玻璃纤维和轻木(玻璃钢)进行模铸。 安装完成后,浆刃尖端运动速度在全速运行时可以达到290公里/小时。 由西门子公司负责制造叶片,据说采用了最新的“量子叶片”工艺,设计 的叶片重量只有传统叶片的80%。声称:“减重主要通过对叶片外形的特 殊设计实现,同时设计过程中兼顾了转子在不同风速下的性能。
玻璃钢叶片
• 所谓玻璃钢,就是环氧树脂、不饱和树脂等塑料渗入不通长度的玻璃纤维做成的增强塑料。具有强度高, 重量轻,耐老化,表面可以再缠玻璃纤维及凃环氧树脂,其他部分填充泡沫塑料。玻璃纤维的质量还可以 通过表面改性、上浆和涂覆加以改进。
玻璃钢复合叶 片
• 20世纪末,世界工业发达国家的大、中型商品风力发电机的叶片,基本上采用型钢纵梁、夹层玻璃钢肋梁 及叶片根与轮毂连接用金属结构的复合材料做叶片。美国研究表明,采用射电频率等离子体沉积法涂覆E玻纤,其耐拉伸疲劳就可以达到碳纤维的水平,而且经这种处理后可以降低纤维间微震磨损。
连续性条件
S1v 1 S 2v 2
作用在风机上的力
F Sv(v 1v 2 )
风机吸收的功率
P Fv Sv 2(v 1 v 2 )
图1 风能转换关系图
风轮机前后气体动能改变量
E
1 2 Sv(v 12 v 2 ) 2
因为风轮的功率即是风能改变量,所以 从而可以得到
为小值,所以上式可以再简化为
16 C l nl 9
R r2 4 0 0 2 9 R
2
只需要再确定R和
0 的值即可。
翼型对性能的影响
弯度的影响
翼型弯度加大后,导致上下弧流速度差加大,从而使压力差加大,升力增加 同时,迎流面积加大,阻力增加。相比较而言,阻力上升速度比升力快。
厚度的增加 同一弯度的翼型,采用较厚的翼型时,对应同一攻角的升力增加,阻力也增 加,类似于弯度增加。 前缘影响 实验表明,当翼型的前缘抬高时,在负攻角情况下阻力变化不大,前缘低垂 则阻力迅速增加。
理论基础
风能计算 由一般的流体力学可知,气流的动能可以表示为:
E
1 mv 2 2
设单位时间内气流流过的单位面积 则气流所具有的动能表示为
S 的气体体积为 V
,气体密度为
1 E 3 2
其中密度和风速随着地理位置,海拔高度,地形等因素而改变, 速度为主要因素
贝茨理论
假设条件 叶轮没有轮毂,具有无限多叶片 气流通过风轮时没有阻力 气流经过整个风轮面时是均匀的 气流速度方向在风轮前后通过风轮时是沿风轮轴线方向 气体为不可压缩气体
钢梁玻璃纤维 蒙皮叶片
• 叶片在近代采用钢管或者D型型钢做成纵梁,钢板做肋梁,内填泡沫塑料外覆玻璃钢的结构形式,一般在大 型风力发电机上使用。叶片纵梁的钢管及D型型钢从叶根至叶尖的截面逐渐变小,以满足叶片的扭矩要求并 减轻叶片重量,即做成等强度梁。
铝合金等弦长 挤压成型叶片
• 用铝合金挤压成型的等弦长挤压成型叶片易于制造,可连续生产,又可按设计要求的扭曲进行扭曲加工, 叶根与轮毂连接的轴及法兰可通过焊接螺栓来实现。铝合金叶片重量轻,易于加工,但不能做到从叶根至 叶尖渐缩的叶片,因为技术不行。
Schmitz理论 对于有限长的叶片,该方法不仅考虑了在叶尖造成的涡流损失,还考虑 到了风在通过叶轮后,速度方向产生了偏转而造成的与理论模型的不相 符。
动量---叶素理论 该理论是目前国内外使用最为普遍的方法之一。该方法研究了叶尖部分 的损失和升阻比对叶片最佳性能的影响。
现有翼型介绍
4位数翼型族
最早建立的一个低速翼型族。有较高的 最大升力系数和较低的阻力系数 在4位数上发展而来的。有两种中线, 一种比较简单,另一种为S型 适用于较高速的翼型族,又称层流翼型 前缘半径小,最大厚度位置靠后。
风力发电机叶片设计
叶片形状设计 理论基础 现有翼型及其特点 辅助优化设计方法 制造材料和工艺 现有各种制造材料及其特性的介绍 制造工艺介绍
叶片和翼型的几何形状与空气动力特性
翼型的参数
l -----翼型的弦长,A点到B点的长度 C -----最大厚度,即弦长法线方向之翼型最大厚度 f -----翼型中线最大弯度 -----攻角,是来流速度方向与弦线间的夹角 0 -----零升力角,弦线与零升力线之间的夹角 -----升力角,来流速度方向与零升力线间的夹角
碳纤维复合叶片 强度为所有材料里最强,刚度为玻璃钢复合叶片的2-3倍,质量轻。 对风力发电机而言,碳纤维是即将来临的潮流。
叶片制造工艺
风电叶片是一种高性能的复合材料产品,制造条件要求高,温度要求 16~25℃,空气湿度要求低于70%
手糊工艺:生产效率低,有害物质和溶剂释放,质量不合格,成品率低。 聚胺酯反应注射成型(RIM):投资大,适用于中小尺寸风机叶片大批量生产。 树脂传递模塑(RTM):属于半机械化生产,污染小,生产效率和产品质量高。 真空吸塑成型(VRAM):增加树脂传递动力,排除模具及树脂中的气泡和水分, 提高复合材料性能,对于大尺寸的复合材料尤为合适。
Pmax
1 Sv 13 2
16 0.593 27
假设作用在风轮上的轴向推力与扫掠面积成正比,则
dT v 2dS 2 v 2rdr
考虑静止的翼型受到风吹,风的速度为 此时,作用在叶片上的力
v
,方向与翼型截面平行。
F
1 C r Sv 2 2
同时,这个力可以分解为平行于气流速度的阻力D与垂直于气流速度的升力L
W v U
dF dL
cos
dD
1 C dW 2ldr 2 1 dL C lW 2ldr 2
其合力
-------dF和dL之间的夹角;l
-------距转轴r处叶素的弦长
由于
W
v
sin 1 W2 1 v2 ldr dF C l ldr C l 2 cos 2 sin 2 cos
1 C d Sv 2 2 1 L C lSv 2 2
D
C 其中, d 和C l 分别为阻力系数和升力系数
设风轮叶片在半径r处的一个基本单元叫做叶素,其长度为 弦长为 l 安装角为 。
设叶轮旋转角速度为
dr
r
,则半径为r处叶素的圆周速度 U
此时空气通过该位置,与叶轮的相对速度为 同时:
为叶尖速比---------叶尖圆周速度与风速的比值
3 将 cot 代入 C l nl 的关系式,得到 2
C l nl
16 9
r
4 2 (1 tan ) 9 3
2
设叶尖处和距转轴半径r处的尖速比分别为 同时,由于
0
tan
R v1
和
r v1
,
1 v 2 cos( ) dT C l n ldr 2 2 cos sin
,则有
将上式投影到转轴上,设叶片数为n,则轴向推力为
与上文相同的式子等同,则得到
sin 2 C lnl 4r cos( ) 2 已知在最佳运行条件下 v v 1 ,则 3 r 3 r 3 cot v 2 v1 2
v v1 v 2
2
E P
所以,风轮的功率如下
P
1 2 S(v 1 v 2 )(v 12 v 2 ) 4
2 v 1 是已知条件,所以可得 v 2 1 v 1 时,此时 v v 1 风轮功率最大。 3 3
所以,风轮的功率如下
Pmax
8 Sv 13 27
max
表明粗糙度和雷诺数的影响
粗糙度对表面边界层的影响很大,在叶片失速的时候,噪声会增大,引起震 动。 有限翼展的影响 会在叶尖产生涡流,形成阻力,该阻力称为诱导阻力。
实际工程中设计方法介绍 Glauert理论
对于有限长的叶片,叶轮叶片的下游存在着尾迹涡,从而形成两个主要 的涡区;一个在轮毂附近,一个在叶尖。对于空间的某一个定点,其风 速可以被认为是由非扰动的风速和涡流系统产生的风速之和。
Glauert的升级版,考虑的非工况下 风轮的性能
基于Soildworks的叶片绘制(前端处理)
用Profili软件进行数值模拟
用ANSYS进行叶片动静载荷,震动分析
叶片材料
木制叶片及布 蒙皮叶片
• 近代微、小型,观赏用风力发电机也有用木制叶片,由于叶片不易弯曲,常采用等安装角叶片。在采用木 制叶片的时候需要用强度很好的整体方木做叶片纵梁来承担工作时候所需要承担的力和弯矩。