风机叶片材料 设计与简介
风机叶片组成材料

风机叶片组成材料风机叶片是风机的重要组成部分,它直接影响着风机的性能和效率。
在选择风机叶片的材料时需要考虑多个因素,包括材料的强度、耐磨性、耐腐蚀性、重量等。
本文将介绍几种常用的风机叶片组成材料,并对它们的特点和应用进行详细分析。
1. 铝合金叶片铝合金叶片是目前应用最广泛的风机叶片材料之一。
它具有重量轻、强度高、耐磨性好等特点,适用于各种工业风机和通风设备。
铝合金叶片通常采用铝硅合金、铝镁合金等材料制成,具有良好的抗腐蚀性和耐高温性能。
此外,铝合金叶片还可以通过表面涂层或喷涂等方式进行处理,以提高其耐磨性和耐腐蚀性。
2. 碳纤维叶片碳纤维叶片是近年来新兴的风机叶片材料,它具有重量轻、强度高、刚度好等特点,能够有效提高风机的效率和性能。
碳纤维叶片通常由碳纤维复合材料制成,具有优异的耐磨性、耐腐蚀性和抗疲劳性能。
此外,碳纤维叶片还具有良好的导热性能,可以有效降低风机叶片的温度,延长使用寿命。
3. 玻璃钢叶片玻璃钢叶片是一种常用的风机叶片材料,它由玻璃纤维和树脂复合材料制成,具有重量轻、强度高、耐磨性好等特点。
玻璃钢叶片适用于一些特殊环境下的风机,如耐腐蚀、耐高温等要求较高的场合。
此外,玻璃钢叶片还具有良好的绝缘性能和阻燃性能,能够有效提高风机的安全性能。
4. 不锈钢叶片不锈钢叶片是一种常用的耐腐蚀叶片材料,适用于一些特殊环境下的风机,如化工、海洋等领域。
不锈钢叶片具有优异的耐腐蚀性、耐高温性和耐磨性能,能够在恶劣环境下保持良好的工作状态。
不锈钢叶片通常采用316L不锈钢材料制成,具有良好的机械性能和耐蚀性能。
5. 塑料叶片塑料叶片是一种轻质、低成本的风机叶片材料,适用于一些低压、低速的风机。
塑料叶片通常采用聚丙烯、聚乙烯等材料制成,具有良好的耐腐蚀性和耐磨性能。
尽管塑料叶片的强度和刚度较低,但在一些特殊应用场合下,如化学实验室、医疗设备等领域,塑料叶片仍然具有一定的优势。
风机叶片的组成材料对风机的性能和效率有着重要的影响。
风电基础知识培训风机叶片结构

风电基础知识培训风机叶片结构风电作为一种清洁能源,近年来迅猛发展。
而风机叶片作为风力发电的核心组成部分之一,其结构设计和材料选择直接关系到风机的性能和寿命。
本文将介绍风机叶片的结构和相关知识。
一、风机叶片的概述风机叶片是将风能转化为机械能的重要部件,其主要作用是捕捉风能,并将风能转化为旋转能量,驱动发电机发电。
叶片的设计和制造直接影响了风机的效率和稳定性。
二、风机叶片的构造1. 叶片型号风机叶片通常采用空气动力学原理设计,常见的叶片型号有直线型、扭曲型、三维型等。
在选择叶片型号时,需要考虑风机所处的环境、风力特点以及预期的发电效率。
2. 叶片材料常见的叶片材料有玻璃钢和碳纤维复合材料。
玻璃钢叶片具有成本低、易加工等优点,但其强度和刚度相对较低;碳纤维复合材料叶片具有优良的机械性能,但成本较高。
选择合适的叶片材料需要综合考虑经济性和可靠性。
3. 叶片结构叶片一般由根部、腹板、翼尖和翼面等部分组成。
根部是叶片与风机轴连接的部位,需要具备足够的强度和刚度。
腹板是叶片最宽的部分,承担风压的主要作用。
翼尖则是叶片的末端部位,其形状和角度对风机的性能有直接影响。
叶片的翼面则通过空气动力学原理,利用不同的曲率和厚度分布实现对风能的捕捉和转化。
三、风机叶片的设计原则1. 力学强度风机叶片需要经受来自风力的巨大压力和外力的作用,因此在叶片设计过程中,需要考虑强度和刚度,以确保叶片能够承受外界的力量而不发生破坏。
2. 空气动力性能叶片的空气动力性能直接关系到风机发电效率。
在叶片设计过程中,需要采用合理的空气动力学曲线,以最大程度地捕捉和利用风能。
3. 质量和成本在选择叶片材料和结构设计时,需要兼顾质量和成本的平衡。
选择合适的材料和合理的结构设计,既可以确保叶片的强度和刚度,又可以降低生产成本。
四、风机叶片的制造工艺1. 叶片模具制造叶片模具是制造风机叶片的关键步骤之一。
叶片模具需要经过精确的设计和制造,以确保叶片的尺寸和形状符合设计要求。
【风力发电技术】_风电机组叶片介绍
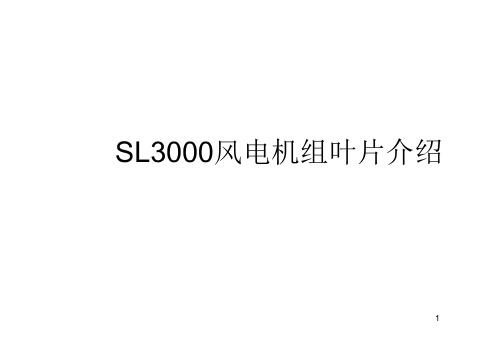
—喷面漆―配重
—►装铭牌、重心 ―k称重,完成生产 点标识
29
,
原材料检验项 目
1、 纤维织物 2、 树脂 3、 胶粘剂 4、 PVC泡沫 5、 轻木 6、 螺栓/螺母
30
,
出厂检验项目
1、 0度角测量 2、 重量及重心点记录 3、 测量螺栓伸出法兰面长 度 4、 外观检查一目测 5、 导线电阻测量
开启真空系统及模具加热系统
40〜50 °C预固化6小时
筋板定位安装
8
^fti
华锐风电 S I N O V E L WIND CO . 4 LTD .
胶接面间隙测量 筋板高度调 整 上胶粘剂
合模,60r加热后固化6小时 脱模
9
,
2.3铺层过程详解
1、 刷胶衣树脂 2、 铺设双轴纤维布 3、 在叶片根部铺设多层二轴纤维布 4、 铺设轻木(铺设范围距离根部3米到27米处铺设) 5、 铺设大梁(单轴纤维,铺设范围距离根部从3米多到37米多位置处) 6、 铺设PVC泡沫 7、 在叶片根部铺设多层二轴纤维布 8、 在根部距离1米多到6米处附近铺设轻木
SL3000风电机组叶片介绍
1
,
1、叶片基本Байду номын сангаас绍—
1.1叶片简介
叶片被称为变速变桨叶片,能将风能转换 为机械能并传递到轮毂上
2
,
1.2基本参数
长 度:44 m 最大 弦长:3.7m 适合风 况:海上IEC 翼 型: DU 根部连接:螺栓64XM36,螺栓中心圆直径
2.3m,材质为10.9级铬钼钢,且需经淬火、冋 火 工作温度:一30 °C〜+50°C
上,R20.00以后从T筋板中间平滑过渡到SS面筋板底部并一 直到法兰区。
高压轴流风机叶片的设计方案

高压轴流风机叶片的设计方案
1. 叶片几何形状:叶片的形状直接影响风机的性能。
一般而言,高压轴流风机叶片应该采用厚度逐渐减小的曲线形状,以提供高效的气流导向和较小的能量损失。
同时,叶片的弯曲程度也会对风机的性能产生影响,需要进行合适的设计以实现高效能的气流。
2. 叶片材料:叶片需要具备足够的强度和耐疲劳性能,以应对高压环境下的工作要求。
常见的叶片材料包括铝合金、镍基合金和复合材料等。
根据具体要求,可以选择合适的材料并进行适当的制造工艺。
3. 叶片调节机构:为了适应不同工况下的工作要求,高压轴流风机通常需要配备叶片调节机构。
这样可以通过调节叶片的角度或者变化叶片的截面形状来实现风机的流量、压力和效率的控制。
4. 叶片表面涂覆:叶片表面涂覆可以改善叶片的表面摩擦系数,减小风机运行时的能源损失。
一般常用的涂层材料有硅橡胶、光滑聚合物等。
以上是高压轴流风机叶片设计的一些基本方案,具体需要根据具体要求和实际情况进行综合考虑和调整。
轴流风机叶片技术要求
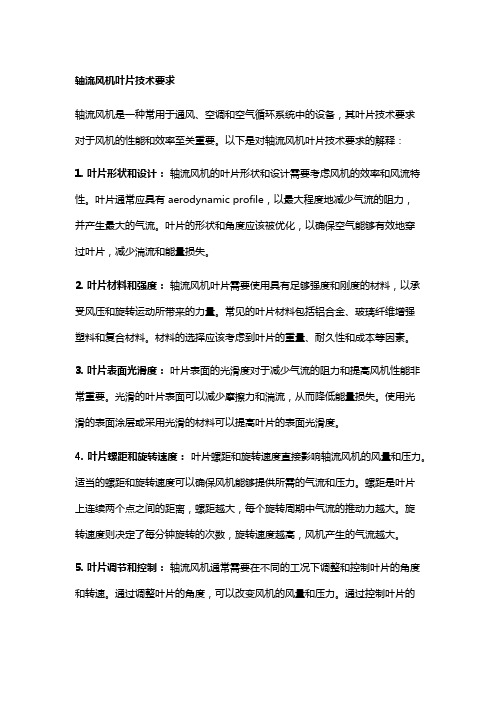
轴流风机叶片技术要求轴流风机是一种常用于通风、空调和空气循环系统中的设备,其叶片技术要求对于风机的性能和效率至关重要。
以下是对轴流风机叶片技术要求的解释:1. 叶片形状和设计:轴流风机的叶片形状和设计需要考虑风机的效率和风流特性。
叶片通常应具有 aerodynamic profile,以最大程度地减少气流的阻力,并产生最大的气流。
叶片的形状和角度应该被优化,以确保空气能够有效地穿过叶片,减少湍流和能量损失。
2. 叶片材料和强度:轴流风机叶片需要使用具有足够强度和刚度的材料,以承受风压和旋转运动所带来的力量。
常见的叶片材料包括铝合金、玻璃纤维增强塑料和复合材料。
材料的选择应该考虑到叶片的重量、耐久性和成本等因素。
3. 叶片表面光滑度:叶片表面的光滑度对于减少气流的阻力和提高风机性能非常重要。
光滑的叶片表面可以减少摩擦力和湍流,从而降低能量损失。
使用光滑的表面涂层或采用光滑的材料可以提高叶片的表面光滑度。
4. 叶片螺距和旋转速度:叶片螺距和旋转速度直接影响轴流风机的风量和压力。
适当的螺距和旋转速度可以确保风机能够提供所需的气流和压力。
螺距是叶片上连续两个点之间的距离,螺距越大,每个旋转周期中气流的推动力越大。
旋转速度则决定了每分钟旋转的次数,旋转速度越高,风机产生的气流越大。
5. 叶片调节和控制:轴流风机通常需要在不同的工况下调整和控制叶片的角度和转速。
通过调整叶片的角度,可以改变风机的风量和压力。
通过控制叶片的转速,可以调节风机的工作状态和效率。
叶片调节和控制通常通过电机、变频器或机械装置实现。
6. 叶片间隙和密封:叶片与风机壳体之间的间隙和叶片与轴之间的间隙需要控制在适当的范围内。
过大的间隙会导致气体泄漏和能量损失,而过小的间隙会增加摩擦力和磨损。
适当的密封装置和间隙控制可以提高风机的效率和性能。
以上是对轴流风机叶片技术要求的解释。
了解和满足这些要求对于设计、制造和维护轴流风机至关重要,以确保风机能够稳定、高效地提供所需的气流和压力。
第5章 叶片材料及制造工艺
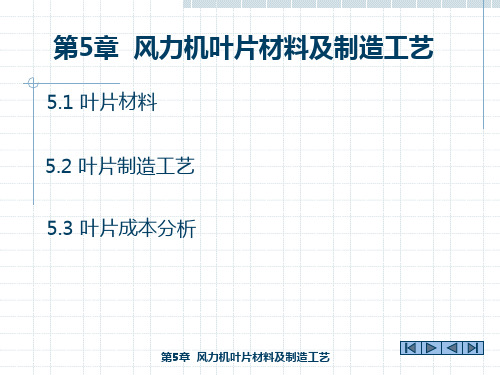
风力发电机叶片生产过程_腾讯视频 https:///x/page/g0331e7 8nfz.html?ptag=qqbrowser
5.2 叶片制造工艺
具体成型工艺大致可分为手糊成型、模压成型、拉挤 成型、纤维缠绕、树脂传递模塑、预浸料成型以及真空灌 注成型等7种工艺。
第 5章
风力机叶片材料及制造工艺
5.1 叶片材料
5.1.3.3 夹芯材料 夹芯材料一般使用在叶片前缘、后缘以及剪切腹板处, 可增加结构刚度,防止局部失稳,提高整个叶片的承载能力 并降低叶片重量。
1、硬质泡沫
2、轻木
第 5章
风力机叶片材料及制造工艺
5.1 叶片材料
5.1.3.4 胶黏剂 胶黏剂的作用是对叶片上壳体与下壳体、壳体与剪切 腹板进行黏接,并填实壳体缝隙。
5.2 叶片制造工艺
5.2.1 手糊成型工艺
传统的复合材料叶片多采用手糊工艺制造。
材料准备剪裁 手糊成型 制品固化 后处理
胶衣/树脂
第 5章
风力机叶片材料及制造工艺
5.2 叶片制造工艺
5.2.2 模压成型工艺 模压成型工艺首先将增强材料和树脂置于双瓣模具中, 然后闭合模具,加热加压,再进行固化脱模。
常见材料:一般的聚乙烯塑料和聚氯乙烯塑料都 是热塑性。雨衣,食品袋或包装袋
热固性
热固性指加热时不能软化和反复塑制,也不在 溶剂中溶解的性能,体型聚合物具有这种性能。
第一次加热时可以软化流动,加热到一定温度, 产生化学反应一交联固化而变硬,这种变化是 不可逆的,此后,再次加热时,已不能再变软 流动了。正是借助这种特性进行成型加工,利 用第一次加热时的塑化流动,在压力下充满型 腔,进而固化成为确定形状和尺寸的制品。这 种材料称为热固性塑料。
风机叶片材料

风机叶片材料
风机叶片材料广泛应用在工业和家用风机中,其主要功能是转动并推动空气流动。
因此,风机叶片材料的选择很重要,既要具备足够的强度和耐用性,又要轻便且易于加工。
以下是常用的风机叶片材料和其特点。
1. 塑料材料
塑料材料具有重量轻、成本低、绝缘性好等特点,因此在一些小型风机或家用风扇中广泛使用。
常见的塑料材料有聚丙烯(PP)、聚乙烯(PE)、聚氯乙烯(PVC)等。
这些材料有较好的耐腐蚀性和绝缘性,但其强度和耐磨性相对较差,在高速运转的风机中使用相对有限。
2. 玻璃纤维增强塑料(GFRP)
玻璃纤维增强塑料是将玻璃纤维与树脂复合制成的复合材料,具有轻质、高强度、耐磨性好等特点。
玻璃纤维增强塑料广泛用于一些大型工业风机中,尤其是用于高速旋转的叶片。
由于其具有高强度和耐磨性,可以在恶劣的工作环境下长期使用。
3. 铝合金
铝合金是一种轻质、耐腐蚀、导热性好的材料。
在一些需要提高散热性能的风机中,常采用铝合金制造叶片。
铝合金材料的制造工艺相对简单,且成本相对较低,适用于中小型风机。
4. 不锈钢
不锈钢具有良好的耐腐蚀性和高强度,适用于一些在腐蚀性工作环境中需要长期使用的风机。
不锈钢材料相对重量较大,但
其耐腐蚀性能和强度优于其他材料,可以确保风机在恶劣条件下的稳定运行。
总之,风机叶片材料的选择要考虑到其强度、耐磨性、耐腐蚀性和重量等因素。
不同类型的风机在选择叶片材料时应根据具体的工作条件和要求做出合适的选择。
风机叶片结构设计及优化

风机叶片结构设计及优化风机是一个广泛应用于工业、建筑以及能源等领域的重要工具。
作为其中的核心组成部分,风机叶片的结构设计和优化显得尤为关键。
本文将着重探讨风机叶片结构设计的相关技术和优化策略。
一、风机叶片的结构设计1. 叶片形状风机叶片的形状是决定其性能的关键因素之一。
基本的叶片形状通常有三种:翼型、蝶形和直线形。
其中翼型叶片是最常见的,可以分为对称型和非对称型两种。
不同翼型的叶片在不同的工况下表现也不同,设计师需要根据具体需求灵活选择。
2. 叶片材料风机叶片的材料通常选择纤维增强塑料(FRP)、玻璃钢、铝合金、镍基合金以及复合材料等。
不同材料的优缺点不同,例如FRP具有较好的耐腐蚀性和轻重量比,适合在恶劣的环境下使用;而铝合金则具有较高的强度和刚度等优点,适合在高负荷的情况下使用。
3. 叶片尺寸叶片的尺寸也是设计中需要考虑的重要因素。
一般来说,叶片的长度具有一定的比例关系,通常为直径的1.5~2倍。
不同长度的叶片会影响到其在特定空间内的布局和使用效果。
4. 叶片数量风机的叶片数量可以根据具体需求在2~8片之间选择。
一般情况下,叶片数量越多,风机的转速越低,稳定性也越高。
但在设计过程中需要考虑到实际使用场合的工况和空间,以避免过度设计。
二、风机叶片的优化策略1. 流体力学优化叶片的流线型形状可以影响其对气流的捕捉和传递能力。
设计者可以针对流体力学特征进行优化,如通过调整叶片厚度分布、弯曲角度以及叶片的扭转角度等来提高叶片的效率和性能。
2. 材料优化在选择叶片材料时,设计师需要考虑到其强度、刚度、耐热、耐腐蚀等多重指标。
优化材料选择的策略包括增强材料、改善制造工艺以及提升材料组织结构等。
3. 结构优化风机叶片的整体结构需要考虑到叶片的受力情况以及轴对称性等。
在叶片设计中,设计师可以通过优化叶片弯曲度、调整叶片内部支撑结构等方式来同时提高叶片的强度和刚度。
结语总体来说,风机叶片的结构设计和优化需要综合考虑多个因素,包括叶片形状、材料、尺寸、数量等。
- 1、下载文档前请自行甄别文档内容的完整性,平台不提供额外的编辑、内容补充、找答案等附加服务。
- 2、"仅部分预览"的文档,不可在线预览部分如存在完整性等问题,可反馈申请退款(可完整预览的文档不适用该条件!)。
- 3、如文档侵犯您的权益,请联系客服反馈,我们会尽快为您处理(人工客服工作时间:9:00-18:30)。
风机叶片材料、设计与工艺简介
核心提示:复合材料风机叶片是风力发电系统的关键动部件,直接影响着整个系统的性能,并要具有长期在户外自然环境条件下使用的耐候性和合理的价格。
因此,叶片的材料、设计和制造质量水平十分重要,被视为风力发电系统的关键技术和技术水平代表。
复合材料风机叶片是风力发电系统的关键动部件,直接影响着整个系统的性能,并要具有长期在户外自然环境条件下使用的耐候性和合理的价格。
因此,叶片的材料、设计和制造质量水平十分重要,被视为风力发电系统的关键技术和技术水平代表。
影响风机叶片相关性能的因素主要有原材料、风机叶片设计及叶片的制造工艺三种。
一风机叶片的原料
目前的风力发电机叶片基本上是由聚酯树脂、乙烯基树脂和环氧树脂等热固性基体树脂与E-玻璃纤维、S-玻璃纤维、碳纤维等增强材料,通过手工铺放或树脂注入等成型工艺复合而成。
对于同一种基体树脂来讲,采用玻璃纤维增强的复合材料制造的叶片的强度和刚度的性能要差于采用碳纤维增强的复合材料制造的叶片的性能。
但是,碳纤维的价格目前是玻璃纤维的10左右。
由于价格的因素,目前的叶片制造采用的增强材料主要以玻璃纤维为主。
随着叶片长度不断增加,叶片对增强材料的强度和刚性等性能也提出了新的要求,玻璃纤维在大型复合材料叶片制造中逐渐出现性能方面的不足。
为了保证叶片能够安全的承担风温度等外界载荷,风机叶片可以采用玻璃纤维/碳纤维混杂复合材料结构,尤其是在翼缘等对材料强度和刚度要求较高的部位,则使用碳纤维作为增强材料。
这样,不仅可以提高叶片的承载能力,由于碳纤维具有导电性,也可以有效地避免雷击对叶片造成的损伤。
风电机组在工作过程中,风机叶片要承受强大的风载荷、气体冲刷、砂石粒子冲击、紫外线照射等外界的作用。
为了提高复合材料叶片的承担载荷、耐腐蚀和耐冲刷等性能,必须对树脂基体系统进行精心设计和改进,采用性能优异的环氧树脂代替不饱和聚酯树脂,改善玻璃纤维/树脂界面的粘结性能,提高叶片的承载能力,扩大玻璃纤维在大型叶片中的应用范围。
同时,为了提高复合材料叶片在恶劣工作环境中长期使用性能,可以采用耐紫外线辐射的新型环氧树脂系统。
二风机叶片的设技
以最小的叶片重量获得最大的叶片面积,使得叶片具有更高的捕风能力,叶片的优化设计显得十分重要,尤其是符合空气动力学要求的大型复合材料叶片的最佳外形设计和结构优化设计的重要性尤为突出,它是实现叶片的材料/工艺有效结合的软件支撑。
另外,计算机
仿真技术的应用也使得叶片的结构与层合板设计更加细化,有力的支持了最佳工艺参数的确定。
早在1920年,德国的物理学家Albert Betz 就对风力发电叶片进行过详细的计算。
基于当时的计算条件和对风力发电叶片的认识,Betz 在叶片计算时采用了一些假设条件。
随着计算机技术发展,计算手段的显著提高,风力发电技术的快速发展,人们对风力发电叶片的认识和理解也在逐渐深入。
尤其是近十年来,经过研究人员对风力发电叶片进行的多次现场载荷、声音和动力测量以后,发现叶片的理论预测值与实际记录值有较大的偏离。
这可能是由于过多的相信了风洞实验,而对叶片服役期间可能遇到的较强动态环境和湍流条件考虑不足造成的。
因此,一些相关人员对当时的叶片计算采用假设条件提出了质疑。
流体动力学计算和软件的改进使得研究人员能够更精确的模拟叶片实际的受力状态。
在此基础上,进一步改善叶片的空气动力学特征,即使叶片在旋转速度降低5%的情况下,捕风能力仍可以提高5%;随着叶片旋转速度的降低,叶片运行的噪音大约可以降低3dB。
同时,较低的叶片旋转速度要求的运行载荷也较低,旋转直径可以相应的增加。
在此项研究的基础上,德国的Enercon 公司将风力发电机的旋转直径由30米增加到33米,复合材料叶片也随着相应的增加。
由于叶片长度的增加,叶片转动时扫过的面积增大,捕风能力大约提高25%。
Enercon 公司还对33米叶片进行了空气动力实验,经过精确的测定,叶片的实际气动效率为56%,比按照Betz 计算的最大气动效率低约3~4个百分点。
为此,该公司对大型叶片外形型面和结构都进行了必要的改进:包括为了抑制生成扰流和旋涡,在叶片端部安装“小翼”;为改善和提高涡轮发电机主舱附近的捕风能力,对叶片根茎进行重新改进,缩小叶片的外形截面,增加叶径长度;对叶片顶部和根部之间的型面进行优化设计。
在此基础上,Enercon 公司开发出旋转直径71米的2MW 风力发电机组,改进后叶片根部的捕风能力得异提高。
Enercon 公司在4.5MW风力发电机设计中继续采用此项技术,旋转直径为112米的叶片端部仍安装的倾斜“小翼”,使得叶片单片的运行噪音小于3个叶片(旋转直径为66米)运行使产生的噪音。
丹麦的LM公司在61.5米复合材料叶片样机的设计中对其叶片根部固定进行了改进,尤其是固定螺栓与螺栓空周围区域。
这样,在保持现有根部直径的情况下,能够支撑的叶片长度可比改进前增加20%。
另外,LM公司的叶片预弯曲专有技术也可以进一步降低叶片重量和提高产能。
三风机叶片的制造工艺
随着风力发电机功率的不断提高,安装发电机的塔座和捕捉风能的复合材料叶片做的越来越大。
为了保证发电机运行平稳和塔座安全,不仅要求叶片的质量轻也要求叶片的质量分布必须均匀、外形尺寸精度控制准确、长期使用性能可靠。
若要满足上述要求,需要相应的成型工艺来保证。
传统复合材料风力发电机叶片多采用手糊工艺(Hand Lay-up)制造。
手糊工艺的主要特点在于手工操作、开模成型(成型工艺中树脂和增强纤维需完全暴露于操作者和环境中)、生产效率低以及树脂固化程度(树脂的化学反应程度)往往偏低,适合产品批量较小、质量均匀性要求较低复合材料制品的生产。
因此手糊工艺生产风机叶片的主要缺点是产品质量对工人的操作熟练程度及环境条件依赖性较大,生产效率低和产品的而且产品质量均匀性波动较大,产品的动静平衡保证性差,废品率较高。
特别是对高性能的复杂气动外型和夹芯结构叶片,还往往需要粘接等二次加工,粘接工艺需要粘接平台或型架以确保粘接面的贴合,生产工艺更加复杂和困难。
手糊工艺制造的风力发电机叶片在使用过程中出现问题往往是由于工艺过程中的含胶量不均匀、纤维/树脂浸润不良及固化不完全等引起的裂纹、断裂和叶片变形等。
此外,手糊工艺往往还会伴有大量有害物质和溶剂的释放,有一定的环境污染问题。
因此,目前国外的高质量复合材料风机叶片往往采用RIM、RTM、缠绕及预浸料/热压工艺制造。
其中RIM工艺投资较大,适宜中小尺寸风机叶片的大批量生产(>50,000片/年);RTM工艺适宜中小尺寸风机叶片的中等批量生产(5,000-30,000片/年);缠绕及预浸料/热压工艺适宜大型风机叶片批量生产。
RTM工艺主要原理为首先在模腔中铺放好按性能和结构要求设计好的增强材料预成型体,采用注射设备将专用低粘度注射树脂体系注入闭合模腔,模具具有周边密封和紧固以及注射及排气系统以保证树脂流动顺畅并排出模腔中的全部气体和彻底浸润纤维,并且模具有加热系统可进行加热固化而成型复合材料构件。
其主要特点有:
闭模成型,产品尺寸和外型精度高,适合成型高质量的复合材料整体构件(整个叶片一次成型);
初期投资小(与SMC及RIM相比);
制品表面光洁度高;
成型效率高(与手糊工艺相比),适合成型年产20,000件左右的复合材料制品;
环境污染小(有机挥发份小于50ppm,是唯一符合国际环保要求的复合材料成型工艺)。
由此可看出,RTM工艺属于半机械化的复合材料成型工艺,工人只需将设计好的干纤维预成型体放到模具中并合模,随后的工艺则完全靠模具和注射系统来完成和保证,没有任何树脂的暴露,并因而对工人的技术和环境的要求远远低于手糊工艺并可有效地控制产品质
量。
RTM工艺采用闭模成型工艺,特别适宜一次成型整体的风力发电机叶片(纤维、夹芯和接头等可一次模腔中共成型),而无需二次粘接。
与手糊工艺相比,不但节约了粘接工艺的各种工装设备,而且节约了工作时间,提高了生产效率,降低了生产成本。
同时由于采用了低粘度树脂浸润纤维以及采用加温固化工艺,大大提高了复合材料质量和生产效率。
RTM 工艺生产较少的依赖工人的技术水平,工艺质量仅仅依赖确定好的工艺参数,产品质量易于保证,产品的废品率低于手糊工艺。
RTM工艺与手糊工艺的区别还在于,RTM工艺的技术含量高于手糊工艺。
无论是模具设计和制造、增强材料的设计和铺放、树脂类型的选择与改性、工艺参数(如注射压力、温度、树脂粘度等)的确定与实施,都需要在产品生产前通过计算机模拟分析和实验验证来确定,从而有效保证质量的一致性。
这对生产风力发电机叶片这样的动部件十分重要。