风电叶片设计流程
风电叶片模具制作步骤介绍

风电叶片模具制作步骤介绍1. 确定设计要求在制作风电叶片模具之前,首先需要明确设计要求。
根据风电叶片的尺寸、形状和材料等要求,确定模具的设计参数。
2. 制作模具设计图纸在确定设计要求后,根据要求绘制风电叶片模具的设计图纸。
设计图纸包括叶片形状、模具尺寸、模具结构等详细信息。
可以使用CAD 软件进行绘制,确保设计准确无误。
3. 准备模具材料根据设计图纸确定的模具尺寸和形状,选择合适的模具材料。
常见的模具材料包括铝、铜、钢等。
根据具体要求,考虑模具的强度、耐磨性和可加工性等因素进行选择。
4. 制作模具原型根据设计图纸,制作模具的原型。
可以使用铣床、车床和激光切割等机械设备进行加工。
根据叶片的形状和尺寸,将模具原型雕刻或切割成相应形状。
5. 制作模具壳体使用模具原型制作模具壳体。
根据模具原型的形状,制作合适大小的模具壳体。
模具壳体包围着叶片模具,起到固定和支撑的作用。
6. 制作模具芯部制作模具芯部,用于在模具壳体内形成叶片的空间。
根据模具原型和设计图纸,制作模具芯部的形状和尺寸。
模具芯部可以使用铁、铝或塑料等材料制作。
7. 组装模具壳体和模具芯部将模具壳体和模具芯部进行组装。
将模具芯部放入模具壳体内,并严密固定。
确保模具芯部和模具壳体的精确配合,保证叶片的精度和质量。
8. 进行模具加工根据风电叶片模具的设计要求,进行模具的加工和处理。
可以使用钳工、铣床、切割机等工具进行精度加工,确保模具的形状和尺寸的准确性。
9. 进行模具调试和调整制作完成的风电叶片模具需要进行调试和调整。
通过测试模具的使用效果,发现并解决一些可能存在的问题,比如模具的拆卸和装配是否顺畅,叶片的质量是否满足要求等。
10. 进行模具试产完成模具调试和调整后,进行模具的试产。
根据风电叶片的要求制作相应数量的叶片试产。
通过试产,验证模具的可用性和叶片的质量。
11. 对模具进行维护和保养完成模具试产后,需要对模具进行定期的维护和保养。
清洁模具表面的灰尘和腐蚀物,涂抹保护剂防止生锈。
风电叶片模具制作步骤介绍

风电叶片模具制作步骤介绍风电叶片是风能发电机的核心部分,其质量和性能直接影响发电效果。
为了提高风电叶片的质量和效率,需要对其进行不断优化和改进。
而制作优质叶片的关键之一就是模具制作。
本文将介绍风电叶片模具制作的详细步骤。
一、模具设计模具设计是模具制作的第一步,决定了模具的尺寸和形状。
首先要根据风电叶片的外形和尺寸来设计出模具的形状和尺寸。
同时根据叶片材料的特性以及叶片工艺的需求,设计出合适的结构和壁厚等参数。
通常,模具设计需要结合CAD/CAM/CAE技术进行。
二、模具制造当模具设计完成后,需要进行模具的加工和制造。
制造模具的方法有很多种,包括CNC加工、电火花加工等。
在制造过程中,需要注意模具的平整度和精度,以及模具的结构和强度等方面的要求。
三、模具样品制作当模具制造完成后,需要进行模具样品的制作。
模具样品是模具制作过程中的一个关键环节,也是检验模具质量的重要环节。
根据模具的设计要求和叶片材料特性,制作出叶片模具的样品。
在制作过程中需要注意模具的温度、压力、速度等参数,以及模具与叶片材料之间的匹配度,确保样品的平整度和精度,以及模具的使用寿命和性能。
四、样品测试和调整当模具样品制作完成后,需要进行测试和调整。
测试叶片样品的强度、平整度、表面光洁度等各项参数,以及使用模具的方便程度和效率等方面。
根据测试结果进行调整和修改,提高叶片的质量和性能,并确定模具的可行性和适用性。
五、批量制造叶片当模具样品测试和调整完成后,可以进行批量制造叶片。
根据模具的设计要求和样品测试结果,制造出符合要求的叶片。
同时需要注意叶片的工艺流程和工艺参数,确保叶片的质量和性能,提高叶片的制造效率和降低成本。
六、模具维修和保养模具制作完成后,需要进行模具的维修和保养。
随着使用次数的增加,模具的磨损和损坏也会逐渐增加,需要进行定期的维修和保养。
维护模具的平整度和精度,增加模具的使用寿命和性能,提高制造效率和降低成本。
综上所述,风电叶片模具制作需要经过模具设计、模具制造、模具样品制作、样品测试和调整、批量制造叶片、模具维修和保养等多个环节。
叶片设计开发流程-概述说明以及解释
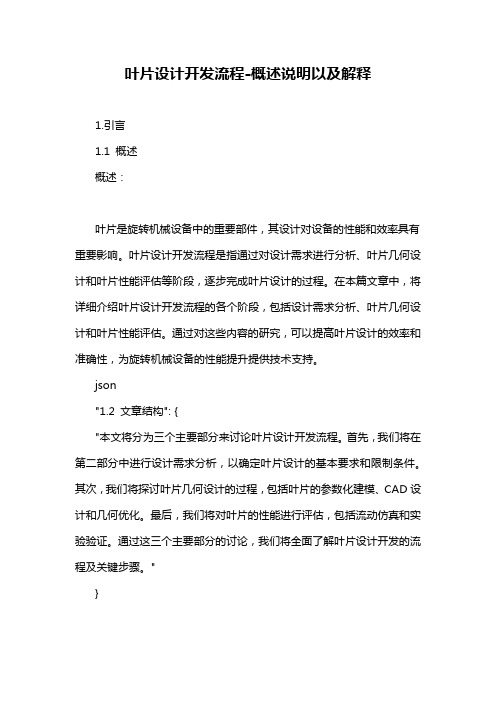
叶片设计开发流程-概述说明以及解释1.引言1.1 概述概述:叶片是旋转机械设备中的重要部件,其设计对设备的性能和效率具有重要影响。
叶片设计开发流程是指通过对设计需求进行分析、叶片几何设计和叶片性能评估等阶段,逐步完成叶片设计的过程。
在本篇文章中,将详细介绍叶片设计开发流程的各个阶段,包括设计需求分析、叶片几何设计和叶片性能评估。
通过对这些内容的研究,可以提高叶片设计的效率和准确性,为旋转机械设备的性能提升提供技术支持。
json"1.2 文章结构": {"本文将分为三个主要部分来讨论叶片设计开发流程。
首先,我们将在第二部分中进行设计需求分析,以确定叶片设计的基本要求和限制条件。
其次,我们将探讨叶片几何设计的过程,包括叶片的参数化建模、CAD设计和几何优化。
最后,我们将对叶片的性能进行评估,包括流动仿真和实验验证。
通过这三个主要部分的讨论,我们将全面了解叶片设计开发的流程及关键步骤。
"}1.3 目的本文的目的是介绍叶片设计开发的流程,通过对设计需求分析、叶片几何设计和叶片性能评估这三个关键步骤的详细讨论,帮助读者全面了解如何进行叶片设计。
同时,通过总结设计开发流程,提供一些建议和技巧,帮助读者更高效地进行叶片设计开发工作。
另外,本文还将展望未来叶片设计的发展方向,为读者提供更多的思路和启发。
通过本文的学习,读者可以更深入地了解叶片设计的复杂性和重要性,为未来的叶片设计工作提供有益的参考和借鉴。
2.正文2.1 设计需求分析设计需求分析是叶片设计开发流程中的关键步骤之一,通过对产品需求的详细分析,可以明确叶片设计的具体要求和目标。
在进行设计需求分析时,需要考虑以下几个方面:首先,要对叶片的使用环境进行充分了解。
这包括叶片所用的领域和具体应用场景,例如是用于风力发电、航空发动机还是水泵等。
不同的使用环境将对叶片的材料、形状、尺寸等设计要求产生影响。
其次,需要明确叶片的性能需求。
风力发电机叶片工艺流程

风力发电机叶片制作工艺流程传统能源资源的大量使用带来了许多的环境问题和社会问题,并且其存储量大大降低,因而风能作为一种清洁的可循环再生的能源,越来越受到世界各国的广泛关注。
风力发电机叶片是接受风能的最主要部件,其良好的设计、可靠的质量和优越的性能是保证发电机组正常稳定运行的决定因素,其成本约为整个机组成本的15%-20%。
根据“风机功价比法则”,风力发电机的功率与叶片长度的平方成正比,增加长度可以提高单机容量,但同时会造成发电机的体积和质量的增加,使其造价大幅度增加。
并且,随着叶片的增大,刚度也成为主要问题。
为了实现风力的大功率发电,既要减轻叶片的重量,又要满足强度与刚度要求,这就对叶片材料提出了很高的要求。
1 碳纤维在风力发电机叶片中的应用叶片材料的发展经历了木制、铝合金的应用,进入了纤维复合材料时代。
纤维材料比重轻,疲劳强度和机械性能好,能够承载恶劣环境条件和随机负荷,目前最普遍采用的是玻璃纤维增强聚酯(环氧)树脂。
但随着大功率发电机组的发展,叶片长度不断增加,为了防止叶尖在极端风载下碰到塔架,就要求叶片具有更高的刚度。
国外专家认为,玻璃纤维复合材料的性能已经趋于极限,不能满足大型叶片的要求,因此有效的办法是采用性能更佳的碳纤维复合材料。
1)提高叶片刚度,减轻叶片质量碳纤维的密度比玻璃纤维小约30%,强度大40%,尤其是模量高3~8倍。
大型叶片采用碳纤维增强可充分发挥其高弹轻质的优点。
荷兰戴尔弗理工大学研究表明,一个旋转直径为120m的风机的叶片,由于梁的质量超过叶片总质量的一半,梁结构采用碳纤维,和采用全玻璃纤维的相比,质量可减轻40%左右;碳纤维复合材料叶片刚度是玻璃纤维复合材料叶片的2倍。
据分析,采用碳纤维/玻璃纤维混杂增强方案,叶片可减轻20%~30%。
Vesta Wind System 公司的V90型3.0 MW发电机的叶片长44m,采用碳纤维代替玻璃纤维的构件,叶片质量与该公司V80 型2.0MW发电机且为39m长的叶片质量相同。
风电叶片设计流程

叶片设计流程一. 空气动力设计1.确定风轮的几何和空气动力设计参数2.选择翼型3.确定叶片的最佳形状4.计算风轮叶片的功率特性5.如果需要可以对设计进行修改并重复步骤4,以找到制造工艺约束下的最佳风轮设计。
6.计算在所有可遇尖速比下的风轮特性对于每个尖速比可采用上面步骤4所述的方法,确定每个叶素的空气动力状态,由此确定整个风轮的性能。
7.风力机叶片三维效应分析8.非定常空气动力现象9.风力机叶片的动态失速10.叶片动态入流.风机载荷计算作为风力机设计和认证的重要依据,用于风力机的静强度和疲劳强度分析。
国际电工协会制定的IEC61400-1标准、德国船级社制定的GL规范和丹麦制定的DS 472标准等对风力机的载荷进行了详细的规定。
2.1 IEC61400-1标准规定的载荷情况2.2 风机载荷计算1计算模型1)风模型(1)正常风模型(2)极端风模型(3)三维湍流模型2)风机模型风机模型包括几何模型、空气动力学模型、传动系统动力学模型、控制系统闭环模型和运行状态监控模型等。
2风力机载荷特性1)叶片上的载荷(1)空气动力载荷包括摆振方向的剪力Q yb和弯矩M Xb、挥舞方向的剪力Q b和弯矩M Jb以及与变浆距力矩平衡的叶片俯仰力矩M b。
可根据叶片空气动力设计步骤4中求得的叶素上法向力系数Cn和切向力系数Ct,通过积分求出作用在叶片上的空气动力载荷。
(2)重力载荷作用在叶片上的重力载荷对叶片产生的摆振方向弯矩,随叶片方位角的变化呈周期变化,是叶片的主要疲劳载荷。
(3)惯性载荷(4)操纵载荷2 )轮毂上的载荷3)主轴上的载荷4)机舱上的载荷5)偏航系统上的载荷6)塔架上的载荷三.风力机气动弹性当风力机在自然风条件下运行时,作用在风力机上的空气动力、惯性力和弹性力等交变载荷会使结构产生变形和振动,影响风力机的正常运行甚至导致风力机损坏。
因此,在风力机的设计中必须考虑系统的稳定性和在外载作用下的动力响应,主要有①风力机气动弹性稳定性和动力响应②风力机机械传动系统的振动③风力机控制系统(包括偏航系统和变浆距系统等) 的稳定性和动力响应④风力机系统的振动。
风力发电机叶片设计—

风力发电机叶片的设计经济、能源与环境的协调发展是实现国家现代化目标的必要条件。
随着全世界气候变暖与化石能源的不断消耗及其对环境的影响问题,其他能源的开发愈来愈受到重视,如核能、地热能、风能、水能等新能源及生物质能、氢能的二次能源的开发应用也日趋发展起来。
而在这些新兴的能源种类中,核能的核废料处置相当困难,而且其日污染相较火电厂更为严重,同时需要相当周密的监管控制能力以避免其泄露而产生不可估量的破坏,国际上这些例子也是相当多的。
而地热能的开发必将要依赖与高科技,在现今对地热开发利用还不完善的现状下,更是难以做到,而且其开发对地表的影响也相当大。
而风能则作为太阳能的转换形式之一,它是取之不尽、用之不竭的清洁可再生能源,不产生任何有害气体和废料,不污染环境。
海上,陆地可利用开发的可达2×1010kW,远远高于地球水能的利用,风能的发展潜力庞大,前景广漠。
自20世纪70年代中期以来,世界主要发达国家和一些发展中国家都在加紧对风能的开发和利用,减少二氧化碳等温室气体的排放,保护人类赖以生存的地球。
风力发电技术相对太阳能、生物质等可再生能源技术更为方便,本钱更低,对环境破环更小,作为清洁能源的主要利用方式而飞速发展,且日趋规模化。
一、叶片设计的意义在风力发电机中叶片的设计直接影响风能的转换效率,直接影响其年发电量,是风能利用的重要一环。
本文主如果设计气动性能较好的翼型与叶片并进行气动分析。
而翼型作为叶片的气动外形,直接影响叶片对风能的利用率。
此刻翼型的选择有很多种,FFA-W系列翼型的长处是在设计工况下具有较高的升力系数和升阻比,而且在非设计工况下具有良好的失速性能。
叶片的气动设计方式主要有依据贝茨理论的简化设计方式,葛老渥方式与维尔森方式。
简化的设计方式未考虑涡流损失等因素的影响,一般只用于初步的气动方案的设计进程;葛老渥方式则忽略了叶尖损失与升阻比对叶片性能的影响,同时在非设计状态下的气动性能也并未考虑;维尔森方式则较为全面是现今常常利用的叶片气动外形设计方式。
风力发电叶片工艺技术规范
风力发电叶片工艺技术规范风力发电叶片是风力发电机组的核心部件之一,其工艺技术规范的标准化对于提高叶片的质量和性能非常重要。
以下是一份风力发电叶片工艺技术规范的范例,共700字:一、叶片材料:1. 主要采用玻璃纤维增强塑料(GFRP)材料制作叶片,其具有重量轻、韧性好、耐腐蚀等特点。
2. 叶片表面涂层材料应具有良好的抗紫外线、防腐蚀和耐候性能,以延长叶片的使用寿命。
二、叶片设计:1. 叶片应具有良好的气动性能和结构强度,能够在任何风速下高效转动。
2. 叶片的外形设计应考虑到风力机组的年平均风速和最大风速,以保证风力机组在各种气候条件下都能正常运行。
三、叶片制造工艺:1. 叶片制造采用模具成型技术,确保叶片的尺寸精准和一致性。
2. 在叶片制造过程中,应严格控制传统工艺中常见的缺陷,如气泡、毛孔、挤出不良等,以确保叶片的质量。
3. 叶片制造过程中应有专门的质量控制部门进行质量检测,并记录相关数据,以便追溯和改进。
四、叶片装配:1. 叶片装配前,应对叶片进行全面的检查,确保叶片表面平整、无明显的损伤和裂纹。
2. 在叶片装配过程中,应使用合适的工具和设备,避免对叶片造成二次损伤。
3. 叶片的安装位置和姿态应符合设计要求,以确保整个风力机组的运行稳定性和效率。
五、叶片维护和保养:1. 定期检查叶片表面涂层的状态,如有损坏或老化,应及时进行修复或更换。
2. 定期清洁叶片表面的污垢和积聚物,以保持叶片的表面光滑,减少风阻。
3. 定期检查叶片的结构和连接件,如有松动或损坏,应及时予以修复或更换。
六、叶片性能测试:1. 在叶片制造完成后,应进行性能测试,包括叶片的阻力系数、弯曲刚度、疲劳寿命等。
2. 应建立完善的测试方法和设备,确保测试结果的准确性和可靠性。
3. 根据测试结果,对叶片的设计和制造工艺进行改进和优化,以提高叶片的性能和可靠性。
综上所述,风力发电叶片工艺技术规范对于提高叶片的质量和性能至关重要。
通过合理选材、精确制造、合理装配和定期维护,可以保证叶片在各种条件下稳定运行,提高风力发电机组的发电效率。
风电叶片结构设计
另外的一个问题是即使是迎风型叶片仍然会承受塔架周围的波动气流压力。这将增加疲 劳载荷(尽管没有顺风型风机严重)。更为重要的是将引起叶片共振。共振现象就像孩 子在荡秋千,如果持续以相同的频率施加外力给秋千,秋千会越荡越高,如果以不同的 频率施加外力,秋千就会变低。叶片产生的共振会显著地增加摆动,加大叶片以及轮榖 和传动轴承的疲劳载荷。因此叶片必须具有较高的刚性和较轻的重量以防止扫过塔架时 产生共振。而为了提高刚性增加的材料又会导致自重升高,因此必须通过加厚叶片来改 变自身的震动频率。 叶片通过连接件与轮毂连接,每个叶片的振动都会影响到其他叶片。因此每只叶片自 身的振动频率都不能和自身或其他叶片扫过塔架的频率相同。例如,如果一个叶片以 每2秒钟的频率扫过塔架,则叶片自身的振动频率就不能是1秒或3秒。对于变速风机而 言,这种要求更加难以实现
纤维类型
玻璃钢复合材料中最为常用的增强纤维是碳纤维和芳纶纤维。碳纤维的强度是玻纤的两 倍,模量是玻纤的3倍。高模量使得碳纤维复合材料具有更好的疲劳性能。但是因为碳 纤维的造价高昂,因此只被用在叶片中要求高强度和模量的部分。
SPX 8080 / EGL 1600 / 32%. FVF=54%. 24 Micron OCF R25H R=0.1 Frequency=4Hz
Remaining static strength = 97%
典型风机叶片的疲劳载荷-循环次数曲线
WE Handbook- 3- Structural Design
WE Handbook- 3- Structural Design
如果叶壳全部采用玻璃钢复合材料制造,达到要求的强度所需厚度只有几毫米。但是因 为从梁帽到后缘的距离有1米多长,如果采用几毫米的厚度则刚度不足。这也会导致空 气动力学问题和发生脱粘现象。 增加玻璃钢层的厚度可以解决这个问题,但又会导致重量和成本增加。因此叶壳部分多 采用内部夹杂低密度芯材的夹芯结构。常用芯材多为硬质泡沫或轻木。夹芯结构的工作 原理和工字梁以及盒式大梁相同,芯材主要承担剪切载荷,上下表层提供弯曲刚性。在 放置梁帽处一般不铺放芯材,这样做可以增大梁帽间的距离,如上所述这样做会提高整 体的抗弯强度。
风力机叶片的设计ppt课件
73.1583
-0.0125
75.252
-0.011
76.5039
-0.0093
75.8358
-0.0075
7风7力.7机3叶72 片的设计-0.0063
风力机叶片的设计
(5)、确定各个截面的安装角和弦长。
1)、确定翼型的设计升力系数和最佳攻角 2)、应用Glauert方法设计
风力机叶片的设计
1)、确定翼型的设计升力系数和最佳攻 角 根据Profili软件输入翼型型号NACA23012,可得到表3-1和图3-1、图3-2、图3-3及图3-4如下所示
0.01 0.0103 0.0107
0.011 0.0114
0.012 0.0123 0.0127 0.0134 0.0137
Cl/Cd
Cm
-30.917
-0.0119
-34.019
-0.0078
-35
-0.0043
-35.7263
-0.0014
-33.976
-0.0049
-31.9481
-0.009
Alfa -8
-7.5 -7
-6.5 -6
-5.5 -5
-4.5 -4
-3.5 -3
-2.5 -2
-1.5 -1 0
0.5 1
1.5 2
2.5 3
3.5 4
4.5 5
5.5 6
6.5 7
7.5 8
8.5
Cl -0.7451 -0.7144
-0.679 -0.6395 -0.5674
-0.492 -0.4268
350 1400
1.13
4
r
r4 R
4.51
风力机叶片的设计PPT课件
φi
50.366 40.862 33.368 27.714 23.469 20.238 17.731 15.744 14.138 12.819 11.717 10.785 9.988 9.298 8.695 8.335
β
c
φ角的弧度
阻力系 数
βi
ci φi*П/180 Cdi
40.866 209.578 0.87904697 0.0149
第7页/共20页
1)、确定翼型的设计升力系数和最佳攻 角 根据Profili软件输入翼型型号NACA23012,可得到表3-1和图3-1、图3-2、图3-3及图3-4如下所示
Alfa -8
-7.5 -7
-6.5 -6
-5.5 -5
-4.5 -4
-3.5 -3
-2.5 -2
-1.5 -1 0
0.5 1
1.285 136.745 0.188241327 0.0149
0.488 127.182 0.174318549 0.0149
-0.202 118.807 0.162275277 0.0149
-0.805 111.423 0.151761481 0.0149
-1.165 106.971 0.145466244 0.0149
1.158 1.158 1.158 1.158 1.158 1.158 1.158 1.158 1.158 1.158 1.158 1.158 1.158 1.158 1.158 1.158
周速比 λi
0.258 0.548 0.838 1.128 1.417 1.707 1.997 2.287 2.577 2.867 3.157 3.447 3.737 4.027 4.317 4.510
- 1、下载文档前请自行甄别文档内容的完整性,平台不提供额外的编辑、内容补充、找答案等附加服务。
- 2、"仅部分预览"的文档,不可在线预览部分如存在完整性等问题,可反馈申请退款(可完整预览的文档不适用该条件!)。
- 3、如文档侵犯您的权益,请联系客服反馈,我们会尽快为您处理(人工客服工作时间:9:00-18:30)。
叶片设计流程
一.空气动力设计
1.确定风轮的几何和空气动力设计参数
2.选择翼型
3.确定叶片的最佳形状
4.计算风轮叶片的功率特性
5.如果需要可以对设计进行修改并重复步骤4,以找到制造
工艺约束下的最佳风轮设计。
6.计算在所有可遇尖速比下的风轮特性
对于每个尖速比可采用上面步骤4所述的方法,确定每个叶素的空气动力状态,由此确定整个风轮的性能。
7.风力机叶片三维效应分析
8.非定常空气动力现象
9.风力机叶片的动态失速
10.叶片动态入流
二.风机载荷计算
作为风力机设计和认证的重要依据,用于风力机的静强度和疲劳强度分析。
国际电工协会制定的IEC61400-1标准、德国船级社制定的GL 规范和丹麦制定的DS 472标准等对风力机的载荷进行了详细的规定。
2.1IEC61400-1 标准规定的载荷情况
2.2风机载荷计算
1计算模型
1)风模型
(1)正常风模型
(2)极端风模型
(3)三维湍流模型
2)风机模型
风机模型包括几何模型、空气动力学模型、传动系统动力学模型、控制系统闭环模型和运行状态监控模型等。
2风力机载荷特性
1)叶片上的载荷
(1)空气动力载荷
包括摆振方向的剪力Q yb和弯矩M xb、挥舞方向的剪力Q xb和弯矩M yb以及与变浆距力矩平衡的叶片俯仰力矩M zb。
可根据叶片空气动力设计步骤4中求得的叶素上法向力系数Cn和切向力系数Ct, 通过积分求出作用在叶片上的空气动力载荷。
(2)重力载荷
作用在叶片上的重力载荷对叶片产生的摆振方向弯矩,随叶片方位角的变化呈周期变化,是叶片的主要疲劳载荷。
(3)惯性载荷
(4)操纵载荷
2)轮毂上的载荷
3)主轴上的载荷
4)机舱上的载荷
5)偏航系统上的载荷
6)塔架上的载荷
三.风力机气动弹性
当风力机在自然风条件下运行时,作用在风力机上的空气动力、惯性力和弹性力等交变载荷会使结构产生变形和振动,影响风力机的正常运行甚至导致风力机损坏。
因此,在风力机的设计中必须考虑系统的稳定性和在外载作用下的动力响应,主要有①风力机气动弹性稳定性和动力响应②风力机机械传动系统的振动③风力机控制系统(包括偏航系统和变浆距系统等)的稳定性和动力响应④风力机系统的振动。
3.1风力机气动弹性现象
1.风力机叶片气动弹性稳定性问题
2.风力机系统振动和稳定性问题
3.2风力机气动弹性分析
目的是保证风力机在运行过程中不出现气动弹性不稳定。
主要的方法是特征值法和能量法。
特征值法是在求解弹性力学的基本方
程中,考虑作用在风力机叶片上的非定常空气动力,建立离散的描述风力机叶片气动弹性运动的微分方程。
采用Floquet理论求解,最后
稳定性判别归结为状态转移矩阵的特征值计算。
1.风力机气动弹性模型
1)结构模型
2)空气动力模型
2.风力机动力学方程
风力机动力学方程建立时,将风力机分为叶片、机舱和塔架三部分进行建模。
由于风力机运动的复杂性,可在非惯性坐标系中建立风力机动力学方程。
3.风力机气动弹性动力响应分析
4.风力机气动弹性稳定性分析
风力机气动弹性稳定性分析是在求解稳态动力响应之后进行的,并假设系统相对于稳态动力响应解具有小扰动。
系统初始摄动时间为零,并假设系统在弹性力惯性力和空气动力载荷的相互作用下自由运动。
因此,可以将风轮/机舱/塔架耦合系统动力学方程的解表示为稳态解和增量解。
四.风机空气动力试验
作为风机设计和研究的重要环节,除在风洞中进行试验外,还可以在风电场中进行试验。
4.1风洞试验
1.风洞试验要求
1)流场模拟
2)模型模拟
风机模型风洞试验时,风力机风轮模型要求满足下列相似准则。
1.几何相似
2.运动相似
3.动力相似
2.风洞试验项目
①风机风轮性能试验
目的是测量风轮功率系数、风轮轴向力(推力)系数和风轮转矩系数随风轮叶尖速比的变化曲线。
在不同风速和不同偏航角下测出风轮转矩M、风轮轴向力(推力)T和风轮转速n后,就能得到风力机风轮的功率特性、轴向力特性和转矩特性。
风轮转矩M和风轮轴向力(推力)T可以用测力传感器或应变天平进行测量,风轮转速n 可以用测速仪或测速传感器进行测量。
风洞试验时,为了得到准确的结果,要对风洞试验数据进行洞壁干扰修正,主要是阻塞效应的修正。
可以采用壁压信息矩阵法。
②风机风轮载荷试验
目的主要是测量叶片根部处挥舞方向和摆振方向的弯矩以及作用在风轮上的空气动力和力矩。
叶片根部弯矩可以用一台位于叶片和轮毂之间的二分量应变天平进行测量;叶片根部弯矩随叶片方位角变化,还要用角度传感器同步测量叶片的方位角。
风轮上的空气动力和力矩可以用一台位于风轮模型底座和塔架之间的六分量应变天平进行测量。
风洞试验数据要进行如下的处理和修正:
(1)风洞试验前后,对天平信号的零漂进行测量和修正。
(2)风洞试验时,在每个转速下采集风轮旋转5转的数据进行平均处理。
(3)六分量应变天平测量的数据要转换到风轮旋转中心为原点的体轴坐标系。
(4)对测力数据要进行洞壁干扰修正,修正方法一般可以采用“壁压信息矩阵法”。
③风力机叶片压力分布试验
目的是测量叶片不同剖面处的向压力分布,并将压力分布数据换算成叶片径向载荷分布、风轮轴向力(推力)系数和风轮功率系数等。
叶片上测压点所感受的压力可以用安装在风轮整流罩内,与轮毂连在一起的压力扫描阀装置(包括压力传感器)进行测量。
试验时,用安装在整流罩上的总压管所感受的来流总压作为参考压力;并选用2s时间使压力稳定,然后再对每个测压孔采集风轮旋转三周的数据,进行平均处理。
由于离心力对压力管内气体的作用,使叶片上的压力与安装在风轮旋转轴上的传感器所感受的压力之间有一定的差别,要进行离心力效应修正。
④风力机叶片流动显示试验
(1)叶片表面流动显示试验
目的主要是观察叶片表面的流动分离现象,还可以观察到叶片上的
三维流动和非定常流动现象等。
表面流动显示的方法一般采用丝线
法,通常沿叶片展向等距离布置20-30排丝线,每一排沿弦向等间
距布置10个丝线点。
试验时,
为拍摄流动图象,将摄像机固定在风轮传动轴上,将聚光灯安装在风轮浆毂上。
叶片表面流动随叶片方位角变化而变化,还要用角度传感器同步测量叶片方位角。
在进行图像分析时,通常,在进行静止叶片模型试验时,当丝线沿弦向不排列成行时,则可以判断流动是否发生了分离;在旋转叶片模型试验时,判据将包括一个估计丝线与弦线之间允许的最大傾角的准则。
(2)叶片空间流动显示试验
目的主要是观察叶片尖部的旋涡运动,一般采用烟流法。
⑤风力机尾流效应试验
⑥风力机叶片气动弹性稳定性试验
⑦风力机控制特性试验
5.2风场试验
风场试验时,用风力机实物在自然风况和带负荷的情况下进行长时间的测量,模拟真实。
一般,风场试验的场地选择在空旷开阔、地形比较平坦、风速风向比较稳定的地区,避免周围地形和障碍物的影响。
风场试验时,风力机的空气动力特性受外界环境的影响很大,需要对试验条件进行严格的控制,以测量到能
真实反映风力机空气动力特性的数据。
从风力机认证的角度,风力机风场试验的项目包括:气象参数测量、安全和功能试验、电能品质试验、功率特性试验、噪声试验和载荷试验;从风力机研发的角度,在风电场中还需要进行流场显示试验和压力分布试验
等。
1气象参数测量
2风力机功率特性测试
3 风力机噪声测试
4载荷测试
①叶片根部的挥舞弯矩和摆振弯矩;
②风轮的俯仰力矩、偏航力矩和转矩;
③塔架底部两个方向的弯矩和扭矩等。