压缩机生产工艺流程
压缩机工艺流程

压缩机工艺流程压缩机工艺流程是指通过一系列的生产工序将各个零件加工、装配成成品压缩机的过程。
下面将分为六个步骤来详细介绍压缩机的工艺流程。
第一步:零件加工首先进行的是压缩机零件的加工。
这些零件包括压缩机的主体、转子、气缸等等。
通过数控机床进行加工,保证每个零件的尺寸和形状的精确度和一致性。
第二步:表面处理加工完成的零件需要进行表面处理,以提高零件的耐腐蚀性和表面光滑度。
常用的表面处理方法包括喷涂、电镀、阳极氧化等。
这些处理可以提高零件的使用寿命和整体质量。
第三步:装配装配是将加工完成的各个零件进行组装成成品压缩机的过程。
装配过程需要保证每个零件的相互协调和紧密结合,使得压缩机能够正常运转。
同时也需要测试和调整零件的位置和功能,保证整个压缩机的运行稳定性和性能可靠性。
第四步:检测和调试装配完成后,通常需要对压缩机进行检测和调试。
检测可以采用多种方式,如压力测试、温度测试、振动测试等。
通过检测,可以确定压缩机的工作性能是否符合要求。
如果检测结果正常,就进入到调试阶段,对压缩机的各个参数进行调整和优化,以达到最佳的工作状态。
第五步:试运行在检测和调试完成后,可以对压缩机进行试运行。
试运行的目的是检查压缩机的运行情况和工作效果。
通过试运行,可以验证压缩机的性能和质量,并排除可能存在的问题。
如果试运行没有问题,说明压缩机可以正式投入使用。
第六步:包装和出厂最后一步是将压缩机进行包装和出厂。
包装主要是保护压缩机免受运输过程中的损坏,包括外包装和內部填充物。
出厂时,对压缩机进行最后的检查和验收,并提供必要的使用说明书和质保证书。
综上所述,压缩机的工艺流程包括零件加工、表面处理、装配、检测和调试、试运行、包装和出厂。
这些步骤保证了压缩机在制造过程中的质量和性能,并最终成功完成产品的生产。
空气压缩机研发生产方案(一)
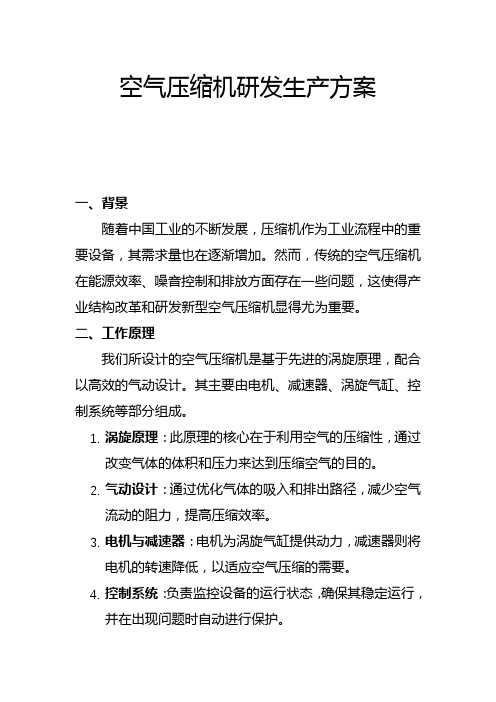
空气压缩机研发生产方案一、背景随着中国工业的不断发展,压缩机作为工业流程中的重要设备,其需求量也在逐渐增加。
然而,传统的空气压缩机在能源效率、噪音控制和排放方面存在一些问题,这使得产业结构改革和研发新型空气压缩机显得尤为重要。
二、工作原理我们所设计的空气压缩机是基于先进的涡旋原理,配合以高效的气动设计。
其主要由电机、减速器、涡旋气缸、控制系统等部分组成。
1.涡旋原理:此原理的核心在于利用空气的压缩性,通过改变气体的体积和压力来达到压缩空气的目的。
2.气动设计:通过优化气体的吸入和排出路径,减少空气流动的阻力,提高压缩效率。
3.电机与减速器:电机为涡旋气缸提供动力,减速器则将电机的转速降低,以适应空气压缩的需要。
4.控制系统:负责监控设备的运行状态,确保其稳定运行,并在出现问题时自动进行保护。
三、实施计划步骤1.市场调研与需求分析:深入了解当前市场的需求,以及同行业产品的优缺点。
2.产品设计与研发:基于调研结果,进行产品的初步设计。
3.样品制作与测试:制作样品,并进行严格的性能测试。
4.改进与优化:根据测试结果,对产品设计进行改进和优化。
5.量产准备:完成产品的最终设计,准备进入量产阶段。
6.市场推广与销售:制定市场推广策略,开展销售活动。
四、适用范围此款空气压缩机适用于各种工业领域,如石油化工、电力、制冷等,也可用于需要大量压缩空气的其他领域,如气动工具、呼吸空气等。
五、创新要点1.高效涡旋设计:通过优化涡旋形状和角度,提高了压缩效率。
2.低噪音设计:采取一系列降噪措施,使压缩机的运行噪音大大降低。
3.智能化控制系统:采用先进的物联网技术,实现远程监控和故障预警。
4.节能模式:在低负荷情况下,设备能够自动切换到节能模式,进一步降低能耗。
5.环保排放:优化排放设计,减少废气排放。
六、预期效果与收益1.提高压缩效率:预计压缩效率提高20%。
2.降低运营成本:预计运营成本降低15%。
3.增加销售收入:预计新增销售收入30%。
压缩机工艺流程
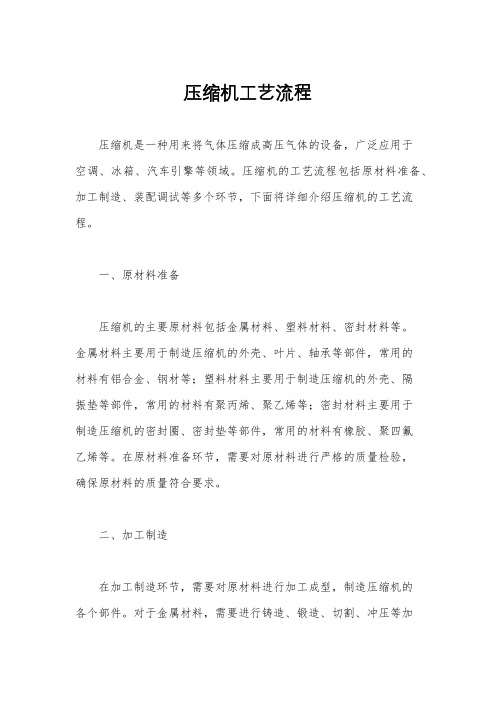
压缩机工艺流程压缩机是一种用来将气体压缩成高压气体的设备,广泛应用于空调、冰箱、汽车引擎等领域。
压缩机的工艺流程包括原材料准备、加工制造、装配调试等多个环节,下面将详细介绍压缩机的工艺流程。
一、原材料准备压缩机的主要原材料包括金属材料、塑料材料、密封材料等。
金属材料主要用于制造压缩机的外壳、叶片、轴承等部件,常用的材料有铝合金、钢材等;塑料材料主要用于制造压缩机的外壳、隔振垫等部件,常用的材料有聚丙烯、聚乙烯等;密封材料主要用于制造压缩机的密封圈、密封垫等部件,常用的材料有橡胶、聚四氟乙烯等。
在原材料准备环节,需要对原材料进行严格的质量检验,确保原材料的质量符合要求。
二、加工制造在加工制造环节,需要对原材料进行加工成型,制造压缩机的各个部件。
对于金属材料,需要进行铸造、锻造、切割、冲压等加工工艺,制造外壳、叶片、轴承等部件;对于塑料材料,需要进行注塑、挤出等加工工艺,制造外壳、隔振垫等部件;对于密封材料,需要进行压延、模压等加工工艺,制造密封圈、密封垫等部件。
在加工制造环节,需要严格控制加工精度,确保压缩机的各个部件符合设计要求。
三、装配调试在装配调试环节,需要将加工制造好的各个部件进行装配组合,组装成完整的压缩机。
在装配过程中,需要进行各个部件的配合检查,确保各个部件之间的配合精度符合要求;同时还需要进行密封性检查、运转试验等,确保压缩机的性能符合要求。
在调试过程中,需要对压缩机的各个部件进行调整,确保压缩机的运行稳定、噪音低、效率高。
四、质量检验在整个工艺流程中,质量检验是非常重要的环节。
质量检验包括原材料的质量检验、加工制造过程中的质量检验、装配调试过程中的质量检验等多个方面。
在质量检验过程中,需要对原材料的外观、尺寸、化学成分等进行检验,确保原材料的质量符合要求;对于加工制造过程中的各个环节,需要进行工艺检验、尺寸检验、外观检验等,确保加工制造的各个部件符合要求;对于装配调试过程中的各个环节,需要进行装配配合检查、密封性检查、运转试验等,确保压缩机的性能符合要求。
合成氨工艺设计总流程及压缩机
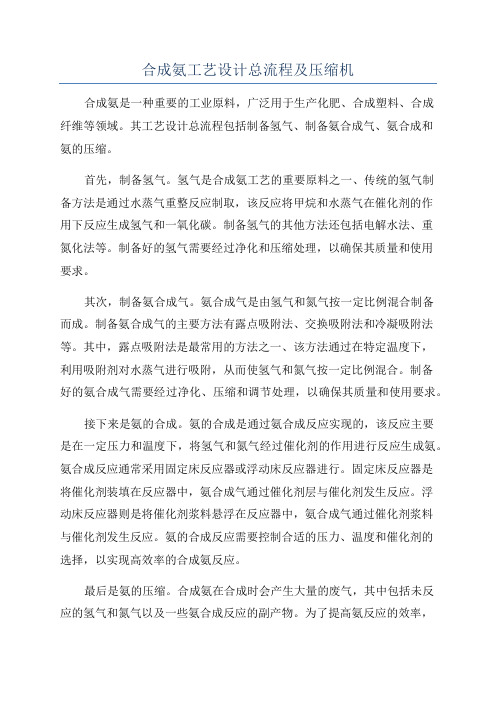
合成氨工艺设计总流程及压缩机合成氨是一种重要的工业原料,广泛用于生产化肥、合成塑料、合成纤维等领域。
其工艺设计总流程包括制备氢气、制备氨合成气、氨合成和氨的压缩。
首先,制备氢气。
氢气是合成氨工艺的重要原料之一、传统的氢气制备方法是通过水蒸气重整反应制取,该反应将甲烷和水蒸气在催化剂的作用下反应生成氢气和一氧化碳。
制备氢气的其他方法还包括电解水法、重氮化法等。
制备好的氢气需要经过净化和压缩处理,以确保其质量和使用要求。
其次,制备氨合成气。
氨合成气是由氢气和氮气按一定比例混合制备而成。
制备氨合成气的主要方法有露点吸附法、交换吸附法和冷凝吸附法等。
其中,露点吸附法是最常用的方法之一、该方法通过在特定温度下,利用吸附剂对水蒸气进行吸附,从而使氢气和氮气按一定比例混合。
制备好的氨合成气需要经过净化、压缩和调节处理,以确保其质量和使用要求。
接下来是氨的合成。
氨的合成是通过氨合成反应实现的,该反应主要是在一定压力和温度下,将氢气和氮气经过催化剂的作用进行反应生成氨。
氨合成反应通常采用固定床反应器或浮动床反应器进行。
固定床反应器是将催化剂装填在反应器中,氨合成气通过催化剂层与催化剂发生反应。
浮动床反应器则是将催化剂浆料悬浮在反应器中,氨合成气通过催化剂浆料与催化剂发生反应。
氨的合成反应需要控制合适的压力、温度和催化剂的选择,以实现高效率的合成氨反应。
最后是氨的压缩。
合成氨在合成时会产生大量的废气,其中包括未反应的氢气和氮气以及一些氨合成反应的副产物。
为了提高氨反应的效率,并方便运输和储存,需要对合成氨进行压缩处理。
氨的压缩通常采用多级压缩的方式进行,通过多级压缩机将合成氨的压力提高到所需的工艺压力。
压缩机的选型需要根据氨的流量和压力要求进行,压缩机的排气温度需要进行控制,以避免催化剂受热而失效。
总之,合成氨工艺设计总流程包括制备氢气、制备氨合成气、氨的合成和氨的压缩。
其中制备氢气和制备氨合成气是提供合成氨原料的关键步骤,氨的合成是核心反应步骤,氨的压缩则是提高效率和方便运输的必要步骤。
压缩机培训演示文稿(工作原理及结构)1

工程
业主员工培训
沈阳远大压缩机股份有限公司
1.压缩机的工作原理
1.1压缩机工作原理内容: 压缩机工作时,电动机带动压缩机的曲轴旋转,通过连杆 与十字头的传动(曲柄连杆机构),使活塞做往复运动,由 气缸内壁、气缸盖和活塞顶面所构成的工作容积则会发生 周期性变化。当活塞从气缸盖处开始运动时,气缸内的工 作容积逐渐增大,这时,气体即沿着进气管,推开吸气阀 而进入气缸,直到工作容积变到最大时为止,吸气阀关闭; 往复式压缩机的活塞反向运动时,气缸内工作容积缩小, 气体压力升高,当气缸内压力达到并略高于排气压力时, 排气阀打开,气体排出气缸,直到活塞运动到极限位置为 止,排气阀关闭。当往复式压缩机的活塞再次反向运动时, 上述过程重复出现。总之,往复式压缩机的曲轴旋转一周, 活塞往复一次,气缸内相继实现进气、压缩、排气的过程, 即完成一个工作循环,以上就为往复式压缩机机的工作原 理。
2.4 充氮及漏气回收流程
工艺过程主要是现场氮气源通过减压阀将氮气压力将到0.15MPa,然 后充入填料中,用氮封的方式保证填料的密封;填料还设有漏气回收 口,将填料泄露出的氮气及微量工艺气体收集到集液罐中,再由集液 罐的放空口接至火炬。
2.5 气量调节流程
气量调节主要是由气缸部分的卸荷器完成,由仪表风及电磁阀控制, 当仪表风接通时,卸荷器会作用在气阀上,使气阀处于卸荷状态,由 此实现0-%50-%100的气量调节。
刮油环组
刮油器部件
刮油环
3.7 活塞部分
活塞与气缸内壁及气缸盖构成容积可变的工作腔,并由曲轴通过连杆 带动,在气缸内做往复运动,实现气缸内气体的压缩。 活塞部件由活塞体、活塞杆、活塞螺母、活塞环及支承环组成。活塞 力的传递由活塞杆凸肩及螺母承担,对于铝制活塞体,考虑到铝的强 度较低,需在活塞杆凸肩与活塞体间及螺母与活塞体间加承压块以增 大承压面积(或加大螺母及凸肩外圆) ; 活塞杆与活塞连接时依靠圆柱面与活塞的配合定中心,依靠凸缘和螺 母的夹持紧固。由于工作时活塞受交变作用力,以及温度变化时活塞 杆与被夹持部分膨胀可能不一致,因此螺母易于松动,故需采取防松 措施,大、中型压缩机采用电加热方式紧固(将活塞杆端部加热后, 按设计要求将螺母旋转一定角度,待冷却后产生预紧力即达到防松目 的);
药厂压缩空气系统工艺流程

药厂压缩空气系统的工艺流程如下:
1.空气压缩机:药厂使用空气压缩机将周围空气抽入并压缩到所需的压力,通常通过活塞式或螺杆式压缩机完成。
2.空气过滤:在将空气压缩之前,需要对空气进行过滤,以去除其中的杂质和水分,避免对生产设备和产品质量的影响。
3.冷却系统:压缩空气会产生热量,因此需要进行冷却以降低温度,通常使用空气冷却器或水冷却器进行散热。
4.分离系统:压缩空气中会含有一定量的水分和油分,需要通过分离系统将其去除,以确保提供干净的空气给药厂的生产设备和工艺。
压缩机生产工艺流程
压缩机生产工艺流程
图四 旋转式压缩机生产流程
(1板金加工
板金工艺是运用各种加工方法将板金材料加工成型出所须形状、尺寸的工 艺统称。
主要加工工艺:冲压、焊接、切削、清洗、热处理;
加工部件:主壳体部件、上壳体、下壳体、机架、定子铁芯、转子铁芯部 件; 板金车间加工的零部件经过清洗、抽检后,送装配车间。
关键过程/特殊过程:焊接、热处理
(2)部品加工(机械加工)
部品加工车间主要承担旋转式压缩机泵体部分的加工,泵体称之为压缩机 的心脏,所以该车间是重要的加工车间,其设备最多,投资最大。
主要加工工艺:车削、磨削、清洗;
加工部件:气缸、曲轴、滚动活塞、滑片、主、副轴承;
力卩工特点:部品配合的表面加工精度、尺寸精度控制在卩级;清洗、检查 要求严格(使用超声波清洗机清洗;气动量仪、专用检具检测,多数尺寸、精度 进行全检)。
压缩机入库
关键过程:气缸、曲轴、滚动活塞精磨
(3)卷线(电机)车间卷线车间进行电机定子绝缘纸、电磁线以及引出线的插入、整形和检查;目前有2 条生产线,生产自动化程度高。
关键过程:线圈绝缘检测
(4)装配车间装配车间是将从机加工、板金、电机加工的部件进行选配、组装、壳体焊接、表面涂装、性能检测;涉及的检查项目有:工序间的装配尺寸检查、电气性能检查、整机密封性以及最终的安全和性能检查。
装配是压缩机生产过程中的关键工序,压缩机装配无论从设备、工艺及装配环境、人员素质都有较高的要求。
主要工艺流程如下:选配一阀片铆接一泵体装配T转子热套一壳体热套T壳体和储液器焊接一气密检查T 涂装T真空干燥T在线试验
特殊过程:壳体和储液器焊接、涂装
关键过程:真空干燥、在线试验。
合成氨工艺设计总流程及压缩机
合成氨工艺总流程本装置以中原油田天然气为原料,采用传统流程的一二段烃类水蒸气转化,上下变,脱碳及甲烷化法。
1、原料气压缩和脱硫来自界区,压力2.25巴〔绝〕、温度30℃,含总硫50p.p.m的天然气,经别离器(01-F001)别离掉所带油水后,进入原料气压缩机(01-K001),经四段压缩至52.5巴〔绝〕、温度114℃。
出原料气压缩机的气体与来自合成压缩机〔07-K001〕的少量合成气相集合,控制含2-5%H2,作为予脱硫钴-钼加氢转化用。
一二段烃类水蒸汽转化是在镍催化剂上进展,硫及其化合物对镍催化剂毒害极大,要求进入转化的原料气中含硫量在0.1p.p.m以下,因此转化前必须脱硫。
经压缩和返氢后的原料气,入对流段盘管〔03-B002E04〕加热至370℃,于钴-钼加氢反响器〔01-R001〕中反响,将有机硫转化为无机硫。
然后在氧化锌脱硫槽〔01-R002A/B〕里硫被脱除,控制含硫小于0.1p.p.m。
2、转化经脱硫的原料气与来自工艺冷凝液汽提塔〔05-C003〕的水蒸汽和来自冰机的蒸汽透平〔09-MT01〕或发电机蒸汽透平〔85-MT01〕的背压蒸汽,按比例调节进展混合,控制水碳比为2.75左右、温度在372℃。
此原料-水蒸汽混合气相继进入一段转化炉对流段盘管〔03-B002E01A〕和〔03-B002E01B〕换热,在两盘管间还设置喷雾温度调节器〔03-B002E08〕用它来调节出盘管〔03-B002E01B〕的混合气加热至580℃。
此混合气从转化炉管顶部进入,在镍催化剂作用下进展转化反响。
出一段炉的转化气压力43.5巴、温度804℃,含16.3%CH4。
含CH416.3%的一段转化气自二段炉〔03-R001〕底部进入,经中心管至炉顶,与来自空压机〔02-K001〕,压缩至45巴,途径加热盘管〔03-B002E03〕加热至500℃的工艺空气相混合,于炉中上部空间进展燃烧反响,反响后气体温升至1250℃左右。
压缩机工作原理及工作过程
51
空气压缩机的主要参数性能(续)
• 含油量 ppm(百万分之一)
• 噪声声压级 Noise Level: 分贝(A), dB(A)
• 比功率Specific Power:指定排气压力下单位排气量所消耗的 功率, 单位 kw/m3/min
• 配套电动机 Electric Motor 型号 Model
• 透平压缩机 Turbine Compressor 离心压缩机 Centrifugal Compressor 轴流压缩机 Axial-flow Compressor
• 容积压缩机 Positive Displacement Compressor
往复压缩机 Reciprocating Compressor
整理课件
53
压缩机的主要参数性能(续)
压缩机每级的排气温度
Td= T Se(n-1)/n 式中 T S-该级的吸气温度;
e-该级压比,排气压力与吸气压 力之比
n-级的压缩过程指数,取决物性、能量损失 喷油压缩机Td不大于120℃ 非喷油压缩机Td不大于180℃ 特殊气体有不同要求
整理课件
54
各类压缩机的应用范围
整理课件
21
典型主机结构(带增速齿轮)
整理课件
22
无油工艺螺杆压缩机(带同步齿轮)
整理课件
23
无油工艺螺杆压缩机
注 油
回 充进
氮气
充 氮注
油
回 油
排 气
进
整理课件
气
回 油
24
内容
整理课件
25
单螺杆压缩机
整理课件
26
整理课件
27
滚动活塞压缩机
整理课件
压缩机生产工艺流程
压缩机生产工艺流程
压缩机是一种将气体进行压缩的设备,广泛应用于空调、冰箱、汽车空调等领域。
它的生产工艺流程主要包括铸造、加工、组装和测试等几个主要环节。
首先是铸造环节。
压缩机主要由铸铁或铝合金材料制成。
在铸造过程中,首先需要制作铸模,然后将铸模放入铸造机器中,加热到一定温度。
在恰当的温度下,将液态金属倒入铸模中,待金属凝固后,取出铸模,完成铸造过程。
接下来是加工环节。
在加工环节中,要对铸造出来的零部件进行修磨、切割、钻孔、铣削等工艺处理。
这些加工操作是根据设计图纸上的要求进行的,以保证零部件的尺寸和形状符合规定。
然后是组装环节。
在组装环节中,将已经加工好的零部件按照一定的顺序进行组装。
首先,将各个部件按照图纸上的要求进行预装,然后逐步进行正式的组装。
组装过程中需要特别注意零部件之间的配合度和装配顺序,以确保压缩机的正常工作。
最后是测试环节。
在测试环节中,对组装好的压缩机进行各种性能和功能的测试。
包括压力测试、噪音测试、震动测试等。
通过测试,检测压缩机是否达到设计要求,并及时发现并解决可能存在的问题。
整个生产工艺流程中还包括材料采购、热处理、表面处理、包装等环节。
材料采购是保证生产的原材料质量的重要环节,热
处理是对零部件进行硬度调节的过程,表面处理是为了防止零部件表面氧化和腐蚀,包装是为了保护压缩机在运输和储存过程中的安全和完整。
以上就是压缩机生产工艺流程的简要介绍。
随着科技的不断进步,压缩机的生产工艺也在不断改进和创新,以提高生产效率和产品质量。
- 1、下载文档前请自行甄别文档内容的完整性,平台不提供额外的编辑、内容补充、找答案等附加服务。
- 2、"仅部分预览"的文档,不可在线预览部分如存在完整性等问题,可反馈申请退款(可完整预览的文档不适用该条件!)。
- 3、如文档侵犯您的权益,请联系客服反馈,我们会尽快为您处理(人工客服工作时间:9:00-18:30)。
压缩机生产工艺流程
图四
旋转式压缩机生产流程
(1)板金加工
板金工艺是运用各种加工方法将板金材料加工成型出所须形状、尺寸的工艺统称。
主要加工工艺:冲压、焊接、切削、清洗、热处理;
加工部件:主壳体部件、上壳体、下壳体、机架、定子铁芯、转子铁芯部件;
板金车间加工的零部件经过清洗、抽检后,送装配车间。
关键过程/特殊过程:焊接、热处理
(2)部品加工(机械加工)
部品加工车间主要承担旋转式压缩机泵体部分的加工,泵体称之为压缩机的心脏,所以该车间是重要的加工车间,其设备最多,投资最大。
主要加工工艺:车削、磨削、清洗;
加工部件:气缸、曲轴、滚动活塞、滑片、主、副轴承;
加工特点:部品配合的表面加工精度、尺寸精度控制在μ级;清洗、检查要求严格(使用超声波清洗机清洗;气动量仪、专用检具检测,多数尺寸、精度进行全检)。
关键过程:气缸、曲轴、滚动活塞精磨
(3)卷线(电机)车间
卷线车间进行电机定子绝缘纸、电磁线以及引出线的插入、整形和检查;目前有2条生产线,生产自动化程度高。
关键过程:线圈绝缘检测
(4)装配车间
装配车间是将从机加工、板金、电机加工的部件进行选配、组装、壳体焊接、表面涂装、性能检测;涉及的检查项目有:工序间的装配尺寸检查、电气性能检查、整机密封性以及最终的安全和性能检查。
装配是压缩机生产过程中的关键工序,压缩机装配无论从设备、工艺及装配环境、人员素质都有较高的要求。
主要
工艺流程如下:
选配→阀片铆接→泵体装配→转子热套→壳体热套→壳体和储液器焊接→气密检查→涂装→真空干燥→在线试验
特殊过程:壳体和储液器焊接、涂装
关键过程:真空干燥、在线试验。