铸造模具工艺和设计
铸造模具工艺流程

铸造模具工艺流程铸造模具是用于铸造金属制品的重要工具,它决定了铸件的形状、尺寸和质量。
铸造模具工艺流程包括模具设计、模具制造和模具使用等环节。
本文将详细介绍铸造模具工艺流程的步骤和流程。
1. 模具设计模具设计是铸造模具工艺流程的第一步,它直接影响到最终铸件的质量和成本。
模具设计的主要任务是根据铸件的形状和尺寸要求,确定模具的结构和尺寸。
模具设计的步骤如下:1.1 铸件分析首先需要对铸件进行分析,了解其形状、尺寸和材料要求。
通过对铸件的分析,可以确定模具的结构和加工工艺。
1.2 模具结构设计根据铸件的形状和尺寸要求,设计模具的结构。
模具结构设计包括模具的分型面、结构形式、加工工艺等。
1.3 模具零件设计根据模具结构设计的要求,设计模具的各个零部件,包括上下模板、芯块、导向柱、滑块等。
模具零件设计需要考虑模具的可制造性和可维修性。
1.4 模具尺寸设计根据铸件的尺寸要求,确定模具的尺寸。
模具尺寸设计需要考虑模具的收缩量和加工余量。
1.5 模具装配设计根据模具的零件设计,进行模具的装配设计。
模具装配设计需要保证模具的精度和稳定性。
2. 模具制造模具制造是铸造模具工艺流程的第二步,它是将模具设计图转化为实际的模具。
模具制造的步骤如下:2.1 材料准备根据模具设计的要求,选择合适的模具材料。
常用的模具材料有铸铁、钢、铝等。
材料准备包括材料的采购、验收和储存等。
2.2 加工工艺根据模具设计的要求,制定模具的加工工艺。
加工工艺包括模具的铣削、钻孔、车削、磨削等。
2.3 数控加工对于复杂的模具零件,可以采用数控加工技术进行加工。
数控加工可以提高模具的加工精度和效率。
2.4 热处理对于需要提高模具硬度和耐磨性的零件,可以进行热处理。
热处理包括淬火、回火、渗碳等。
2.5 组装调试将加工好的模具零件进行组装调试。
组装调试包括模具的装配、调整和测试等。
3. 模具使用模具使用是铸造模具工艺流程的最后一步,它是将模具应用于铸造生产中。
铸造工艺及铸造模具制造与设计

液态收缩 表现为铸型内液态金属或合金的液面下降
凝固收缩 共晶成分或纯金属是在恒温下凝固,凝固收缩只有状态改变引
起,所以收缩较小。
液态收缩和凝固收缩主要表现为铸件体积上的缩减,用体收缩 率(单位体积的百分收缩量)表示。它们是铸件产生缩孔和缩松 的基本原因。 固态收缩
通常直接表现为铸件外形尺寸的减小,可用线收缩率(单位长 度的百分收缩量表示)。固态收缩是铸件产生应力、变形和裂纹 的基本原因。
¾ 热裂
裂纹短、缝隙宽、形状曲折、缝内金属呈氧化 色;
¾ 冷裂
裂纹细小、呈连续直线状或圆滑曲线状、裂纹表 面有金属光泽或呈微氧化色。
复习作业
1.顺序凝固与同时凝固工艺的比较。
实现工艺的不同 优缺点不同
顺序凝固可以有效地防止缩孔和缩松缺陷,但它 又会使铸件各部分的温度差扩大,铸件易产生变形和 裂纹,因此此工艺应用于必须补缩的场合。
硫、磷作为有害杂质,一般限制在0.1%~0.15%以下。
锰能抵消硫的有害作用;余量还可溶入铁素体和渗碳体,提高基 体的强度和硬度;过多的锰则起阻碍石墨化作用。0.6-1.2%
2.温度及冷却速度的影响
铸件的冷却速度对石墨化的影响也很大,即冷却愈 慢,愈有利于扩散,对石墨化便愈有利,而快冷则 阻止石墨化
(2)糊状凝固方式 (3)中间凝固方式
(1)逐层凝固方式
纯金属或共晶成分在凝固过程 中不存在固液混合区。一般说来, 逐层凝固时,合金的充型能力强, 便于防止缩孔和缩松。在常用合金 中,灰铸铁、铝硅合金等倾向于逐 层凝固,易于获得紧实铸件。
(2)糊状凝固方式
合金结晶温度范围很宽,固液并存的凝固区贯穿整个断面。球墨铸铁、 锡青铜、铝铜合金等倾向于糊状凝固。
铸造模具制作的工艺流程
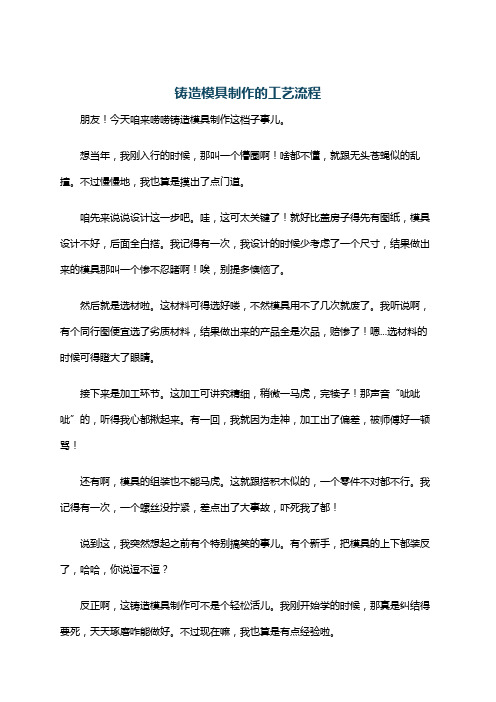
铸造模具制作的工艺流程
朋友!今天咱来唠唠铸造模具制作这档子事儿。
想当年,我刚入行的时候,那叫一个懵圈啊!啥都不懂,就跟无头苍蝇似的乱撞。
不过慢慢地,我也算是摸出了点门道。
咱先来说说设计这一步吧。
哇,这可太关键了!就好比盖房子得先有图纸,模具设计不好,后面全白搭。
我记得有一次,我设计的时候少考虑了一个尺寸,结果做出来的模具那叫一个惨不忍睹啊!唉,别提多懊恼了。
然后就是选材啦。
这材料可得选好喽,不然模具用不了几次就废了。
我听说啊,有个同行图便宜选了劣质材料,结果做出来的产品全是次品,赔惨了!嗯...选材料的时候可得瞪大了眼睛。
接下来是加工环节。
这加工可讲究精细,稍微一马虎,完犊子!那声音“呲呲呲”的,听得我心都揪起来。
有一回,我就因为走神,加工出了偏差,被师傅好一顿骂!
还有啊,模具的组装也不能马虎。
这就跟搭积木似的,一个零件不对都不行。
我记得有一次,一个螺丝没拧紧,差点出了大事故,吓死我了都!
说到这,我突然想起之前有个特别搞笑的事儿。
有个新手,把模具的上下都装反了,哈哈,你说逗不逗?
反正啊,这铸造模具制作可不是个轻松活儿。
我刚开始学的时候,那真是纠结得要死,天天琢磨咋能做好。
不过现在嘛,我也算是有点经验啦。
朋友,你要是开始学这个,可得有耐心,别像我当初似的老犯错。
你说要是遇到难题了,你会咋办?
我这又扯远啦!反正好好学,多实践,准没错!。
铸造工艺的一般步骤
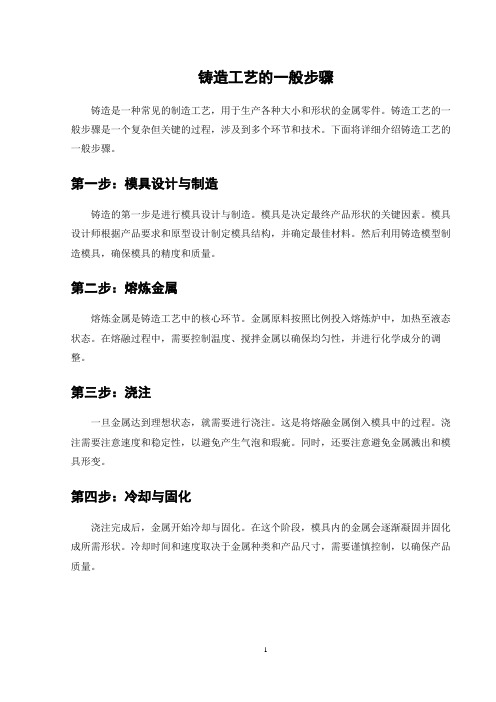
铸造工艺的一般步骤铸造是一种常见的制造工艺,用于生产各种大小和形状的金属零件。
铸造工艺的一般步骤是一个复杂但关键的过程,涉及到多个环节和技术。
下面将详细介绍铸造工艺的一般步骤。
第一步:模具设计与制造铸造的第一步是进行模具设计与制造。
模具是决定最终产品形状的关键因素。
模具设计师根据产品要求和原型设计制定模具结构,并确定最佳材料。
然后利用铸造模型制造模具,确保模具的精度和质量。
第二步:熔炼金属熔炼金属是铸造工艺中的核心环节。
金属原料按照比例投入熔炼炉中,加热至液态状态。
在熔融过程中,需要控制温度、搅拌金属以确保均匀性,并进行化学成分的调整。
第三步:浇注一旦金属达到理想状态,就需要进行浇注。
这是将熔融金属倒入模具中的过程。
浇注需要注意速度和稳定性,以避免产生气泡和瑕疵。
同时,还要注意避免金属溅出和模具形变。
第四步:冷却与固化浇注完成后,金属开始冷却与固化。
在这个阶段,模具内的金属会逐渐凝固并固化成所需形状。
冷却时间和速度取决于金属种类和产品尺寸,需要谨慎控制,以确保产品质量。
第五步:脱模与后处理当金属完全固化后,需要进行脱模和后处理。
脱模是指将成品从模具中取出,需要谨慎操作以避免损坏产品。
随后可以进行表面处理、修磨、清洗等步骤,最终使产品表面光滑并符合要求。
总结铸造工艺的一般步骤包括模具设计与制造、熔炼金属、浇注、冷却与固化、脱模与后处理等关键环节。
每个步骤都至关重要,需要经验丰富的技术人员精心操作,以保证最终产品质量和准确性。
通过不断优化工艺和技术,铸造工艺能够生产出各种形状复杂、精密度高的零部件,满足不同行业的需求。
铸造工艺图及设计实例

汇报人: 日期:
目录
• 铸造工艺图 • 铸造材料及特性 • 铸造设备及工具 • 铸造设计实例 • 铸造工艺优化及改进建议 • 铸造工艺图及设计软件应用
01
铸造工艺图
铸造工艺流程图
造型材料准备
包括对铸造用砂、型砂等的选择 、混砂、配制等过程。
模样和芯盒准备
根据图纸准备木模、木芯盒等。
造型和制芯
将模样放入芯盒内,填入型砂, 形成铸型。
落砂和清理
铸件冷却后打开铸型,去除铸件 表面和内部的残砂和夹杂物。
浇注
将熔融的金属注入铸型中。
合型
将上、下铸型组合起来,形成完 整的铸型。
铸造模具设计图
模具材料选择
根据铸造合金和模具使用条件 选择模具材料,如铸铁、铜合
金等。
模具结构设计
根据产品图纸和铸造工艺要求 ,设计模具结构,包括浇口位 置、分型面选择等。
组成。
数控铣床
用于模具型腔的铣削加工,主要由 主轴、工作台、控制系统等组成。
数控磨床
用于模具型腔的磨削加工,主要由 工作台、主轴、控制系统等组成。
铸造用辅助设备
混砂机
用于混制型砂,一般由混砂转子、型砂输送装置、润 湿装置等组成。
砂处理设备
用于对型砂进行干燥、冷却、输送等处理,一般由干 燥器、冷却器、输送装置等组成。
浇注机
用于浇注金属液体,一般由浇包、浇道、控制系统等 组成。
铸造工具及选用
1 2
模样和芯盒
用于制作铸造用的模样和芯盒,一般由木材或塑 料制成。
浇口杯和分流锥
用于浇注金属液体,一般由耐火材料制成。
3
冒口和冷铁
用于控制铸件的温度和补缩,一般由铸铁或铸钢 制成。
箱体铸造工艺及模具设计

箱体铸造工艺及模具设计箱体铸造是指将铸造合金熔化成液态,倒入箱体型腔中使其凝固而成箱体的工艺。
在进行箱体铸造时,需要设计合适的模具,以保证铸造的准确性和质量。
下面将从工艺流程和模具设计两个方面进行介绍。
一、工艺流程1.原料准备:选用高质量的铸造合金,并进行熔炼。
2.模具设计:根据铸造要求进行模具设计,并进行制造。
3.箱体铸造:(1)装砂:将砂料倒入较大的箱子中,用扫帚将砂料平均地覆盖在箱的底部。
(2)装芯:将芯置入砂料中,以便于芯与箱体组合成为一体。
(3)铸造:将铸造合金熔化,倒入箱体型腔中,等待合金凝固成型。
(4)取样检验:将铸成的箱体取出样品进行检测,以确保铸造质量。
(5)分离砂芯:将铸造成型后,将砂芯从箱体中取出,用气枪将杂质从箱体中清除。
4.后处理:使用切割机将浇口等杂质清除,然后进行热处理、喷漆等工序。
二、模具设计1.模仁:模仁是用来形成箱体内部空腔形状和表面纹理的零件。
在模具设计中,需要考虑铸造合金的流动性、凝固性和热胀冷缩等因素,以确定模仁的尺寸和形状。
2.箱体型腔组装:箱体型腔组装是指将模仁和箱体型腔进行组装。
在进行组装时,需要确保模仁与砂芯的结合紧密,同时还需要考虑砂芯的位置和倾角,以保证铸造合金能够充分填充到型腔中。
3.浇口与放气道的设计:浇口和放气道是箱体铸造过程中的关键部分,其设计直接影响到铸造质量。
浇口应该设置在箱体上部,并且尺寸和形状需要考虑到铸造合金的流动性和凝固时间。
放气道的位置和尺寸也需要充分考虑,以保证砂芯能够顺畅地从型腔中脱出,并且防止气泡产生。
精密铸造工艺流程
精密铸造工艺流程精密铸造工艺是一种通过模具将熔化的金属或合金注入到模具空腔中,在冷却过程中形成所需形状的零件的制造方法。
这种工艺可以保证零件的尺寸精度和表面质量,适用于制造高精度和复杂形状的零件。
下面将详细介绍精密铸造的工艺流程。
1.模具设计:首先需要根据产品的结构和要求进行模具的设计。
模具的设计不仅要满足零件的形状和尺寸要求,还需要考虑到材料流动、冷却和排气等因素。
模具一般由两部分组成,上型和下型。
在设计过程中需要注意模具的易脱模性和耐磨性。
2.模具制造:模具的制造是精密铸造的关键步骤之一、一般来说,模具由金属材料(如钢)制成。
制造过程包括模座加工、型腔制作、钢材加工和热处理等步骤。
在制造模具时,需要使用高精度加工设备和工艺来确保模具的尺寸和表面质量。
3.材料准备:精密铸造一般使用金属或合金作为材料。
在进行铸造之前,需要将原材料进行熔化和净化处理。
熔化一般通过高温熔炼炉将原材料加热至熔点以上进行。
净化包括去除气体和杂质的过程,通常使用真空熔炼或保护气体熔炼来提高材料的质量。
4.注射:注射是精密铸造的核心步骤。
在注射过程中,需要将熔化的金属或合金注入到模具的型腔中,并保持一定的注射压力和速度。
注射过程需要控制金属的温度、流动性和注射时间等参数,以确保零件的形状和尺寸满足要求。
5.冷却:注射完成后,需要等待一段时间进行冷却。
冷却的目的是让熔融金属逐渐固化,形成所需的零件形状。
冷却时间一般根据材料的热导率和尺寸来确定,同时需要控制温度和冷却速度等参数,以避免产生裂纹和变形。
6.脱模:冷却完成后,需要将零件从模具中取出。
脱模的方法一般根据模具的设计和零件的形状来确定,可以通过机械脱模、液压脱模或气体脱模等方式进行。
在脱模过程中需要注意保护零件的表面免受损坏。
7.后处理:脱模完成后,还需要对零件进行一些后处理工艺。
例如,研磨、抛光、喷涂、热处理和表面涂层等工艺可以使零件的表面质量更加光滑和耐磨,并增加零件的功能和使用寿命。
压铸工艺及压铸模具设计
压铸工艺及压铸模具设计1.压铸工艺简介压铸是一种将熔化金属注入模具腔内,然后通过压力固化成型的工艺。
它具有高效、高精度、高复杂度的特点,被广泛应用于制造各种金属零件,如汽车零件、电子零件等。
压铸工艺主要分为准备工作、铸造操作和后处理三个阶段。
准备工作包括选材、设计和制造模具等;铸造操作包括将金属加热至熔点、注入模具等;后处理包括去除模具、修整铸件等。
压铸模具是实现压铸工艺的重要工具,它直接影响着产品质量和生产效率。
模具设计需要考虑以下几个方面。
首先是材料选择。
模具的材料需要具备高强度、高耐磨性、高热稳定性等特点,以保证模具长期使用。
其次是结构设计。
模具结构应该简单、合理,易于加工和维修。
同时,对于复杂的产品,需要设计合适的分型面和可抽出芯等特殊结构。
再次是流道系统设计。
流道系统是将熔化金属导入模腔的通道。
优化的流道系统能够保证铸件充型充满、减小气泡和炸破等缺陷的产生。
最后是冷却系统设计。
良好的冷却系统能够快速、均匀地将铸件冷却,提高生产效率和产品质量。
常见的冷却系统包括水冷却、气冷却等。
3.常见问题及解决方法在压铸工艺和模具设计过程中,常会面临一些问题和挑战。
以下是一些常见问题及其解决方法。
首先是翘曲和变形问题。
由于金属在冷却过程中会有收缩和变形,容易导致铸件产生翘曲和变形。
解决方法可以是增加冷却系统,控制金属温度等。
其次是气孔和缺陷问题。
气孔和缺陷是常见的铸件质量问题,可能是由于金属中的气体未能完全排出或模具内部有不完全填充的区域导致。
解决方法可以是优化流道和冷却系统,增加压力等。
最后是模具使用寿命问题。
模具在使用过程中会受到磨损、冲击和热应力等的影响,容易损坏。
解决方法可以是选用高耐磨材料、增加模具表面硬度等。
4.发展趋势随着科技的发展和需求的变化,压铸工艺和模具设计也在不断发展和改进。
未来的发展趋势主要包括以下几个方面。
首先是数字化和智能化。
通过数字化技术和智能化设备,可以实现对压铸工艺和模具设计的更精确和高效的控制。
铸件工艺流程
铸件工艺流程铸件工艺流程是指将熔融金属或合金浇铸到模具中,并通过冷却和固化过程得到所需形状和尺寸的零件的过程。
铸造工艺是制造复杂零部件的常用方法之一,广泛应用于制造业的各个领域。
下面将详细介绍一下铸件工艺流程。
一、模具设计和制作铸造工艺从模具的设计和制作开始。
模具是铸造过程中用于得到所需零件的模具,也是决定铸造质量的重要因素之一。
模具设计分为结构设计和流道设计两个阶段。
结构设计主要包括模具的形状、尺寸、分型面的确定等方面;流道设计则是确定金属液体进入模腔的路径,以及冷却和排气的方法。
二、模具准备模具制作完成后,需要进行模具准备工作。
首先,要将模具安装到铸造设备上。
然后,根据特定的需要,在模具中涂抹一层隔离剂,用于防止金属液体与模具材料之间的粘结。
接下来,要对模具进行定位和固定,以确保金属液体能够顺利地进入模腔。
三、熔炼金属在进行铸造之前,需要将所需金属或合金熔化。
熔炼金属的方式有很多种,常见的包括电弧炉、感应炉和耐火炉等。
在熔融过程中,要控制好温度和合金成分,以保证所得到的金属液体符合要求。
四、浇注铸造当金属液体达到合适的温度和成分后,就可以进行浇注了。
在浇注过程中,需要将金属液体倒入模具中,待冷却固化后得到所需的铸件。
浇注时要控制好金属液体的流动速度和压力,以避免产生气孔和夹杂物等缺陷。
五、冷却和固化铸件浇注完成后,金属液体会自然冷却并固化。
冷却和固化的时间和方式根据铸件的尺寸和材料来确定。
冷却的过程中,模具起到了保护铸件形状和尺寸的作用。
冷却过程结束后,可以拆卸模具,得到最终的铸件。
六、清理和精加工得到的铸件通常还需要进行清理和精加工,以去除表面的氧化皮和余渣等。
常见的清理方法包括抛光、喷砂和酸洗等。
精加工则是通过切割、修整和加工等方式,使得铸件达到所需的精度和表面质量。
七、质量检验最后,要对铸件进行质量检验。
质量检验的内容包括铸件的尺寸、形状和表面质量等方面。
常见的检验方法有测量、视觉检查和无损检测等。
锻造模具设计
宁德职业技术学院
27
二.模锻件旳分类
1.圆盘类
宁德职业技术学院
28
宁德职业技术学院
29
2.长轴类
宁德职业技术学院
30
宁德职业技术学院
31
三.锻模设计环节
(1)设计锻件图; (2)设计终锻模镗; (3)拟定模锻设备吨位; (4)设计制坯模镗; (5)拟定坯料长度; (6)绘出锻模装配总图,给出锻模技术条件,再绘制
宁德职业技术学院
49
二.预锻模镗设计
1.预锻模镗仅用来降低终锻模镗旳磨损
这种情况下,基本和终锻模镗一样,只有外圆角半径比终 锻模镗相应处大,分模面出圆角也大些。
2.预锻模镗主要用来改善终锻时成型条件
这种情况下预锻模镗设计与终锻模镗有较大区别。能够从 这三个方面考虑其设计:
(1)模镗旳宽和高; (2)模锻斜度; (3)外圆角半径。
除上述切割措施外,还有等离子切割法、电子束切割法、阳极切割法等。
宁德职业技术学院
4
三.锻前加热、锻后冷却和热处理
(一)锻前加热旳目旳与措施
1.锻前加热旳目旳 提升金属旳塑性,降低变形力; 以利于铸造和取得良好旳锻后组织; 降低设备吨位,降低燃料消耗。
2.锻前加热旳措施 根据热源不同,在铸造生产中金属旳加热可分为两大类:
四.圆角半径
在制件公差允许条件下,圆角半径应尽量大。 1.外圆角半径r
一般情况下r值按下式拟定: 2.内圆角半径R
R太小,会使脱模困难,还会造成模锻时金属流动形成旳 纤维被割断甚至产生折叠。
宁德职业技术学院
38
五.冲孔连皮
对内孔不小于25mm旳锻件模锻时不能直接锻出通孔,在 分模面上留有较薄旳一层金属称为连皮。常用连皮有四种形式:
- 1、下载文档前请自行甄别文档内容的完整性,平台不提供额外的编辑、内容补充、找答案等附加服务。
- 2、"仅部分预览"的文档,不可在线预览部分如存在完整性等问题,可反馈申请退款(可完整预览的文档不适用该条件!)。
- 3、如文档侵犯您的权益,请联系客服反馈,我们会尽快为您处理(人工客服工作时间:9:00-18:30)。
● 加工拋光預留量的考慮 ● 分型面的選擇 ● 芯頭的設計與布置 ● 鑄件收縮的考量 ● 拔模斜度的設定
三:模具設計
3.2 模具設計原則
● 液流速度平穩 ● 合金濾渣干淨 ● 保持足夠液流壓力 ● 有效的排氣 ● 對鑄件熱節處進行補縮 ● 鑄件出品率要盡量高
三:模具設計
鑄 2、鑄件尺寸精度和表面粗糙度高。
3、鑄件對工藝因素的孌動敏感、新品試制需
3、鑄件工藝出品率高一般60%以上
進行反復調試才能得出合格鑄件。
4、生產環境好,勞動強度低,安全生產有 保障。
5、生產面積小,易實現機械化作業。
6、工序簡單、生產性靈活,可連續生產。
二:模具工藝
2.4 鑄造結構工藝分析 2.4.1 V和K型連接分析
洗砂
領料
打磨試水
入庫
二:模具工藝
2.1 重力鑄造工藝澆注系統
主澆道
熱節過大易出現 氣縮孔
熱節過大易出現 氣縮孔
內澆道
二:模具工藝
2.2 砂型鑄造工藝澆注系統
二:模具工藝
2.3 鑄造特點比較
優點
缺點
1、批量生產、效率很高
砂
2、生產設備簡單成本低 3、鑄型排氣較好
鑄 4、工藝設計簡單、補縮較好
鑄成一流品質
鑄造模具工藝和設計 成潔鑄造廠
重力技術課 宛移風
課程綱要
一 鑄造定義和流程 二 模具工藝 三 模具設計 四 模具加工制作
一:鑄造的定義和流程
1.1 鑄造原理
鑄造是制造機器零件毛坯的一種金屬液態成形方法。鑄 造過程是將金屬熔煉成具有流動性的液態合金,然後澆入具 有一定幾何形狀、尺寸大小的型腔中,液態合金在重力場或 外力場(壓力或離心力等)的作用下充滿型腔,待凝固冷卻後 就成為所需要的機器零件或毛坯,用鑄造方法制成的零件或 毛坯稱為鑄件。
3.3.1 鑄件外形模具設計
鑄件外型上下模
三:模具設計
3.3.2 鑄件砂芯模具設計
砂芯模上下模
三:模具設計
3.4 重力鑄造模具
重力模
重力砂芯模
三:模具設計
3.5 砂型鑄造模具
中板模
砂鑄砂芯模
四:模具加工制作
4.1 模具加工制造概述
模具制造是一門由切削加工,塑性加工,物理化 學加工,電火花加工等組成的綜合性加工技朮,對于 普通精度的模具,常在機械加工后由技朮熟練的鉗工 進行修正及配制。我們目前接觸到的模具有:重力模、 重力砂芯模、中板模、砂鑄砂芯模、壓鑄模。由于模 具種類較多,結構特點不相同,故制造工藝及要求也 不相同,作為從事模具加工的人員,應掌握多方面的 知識,在加工工藝方面,應根據每副模具的特點,從 各種加工方法中選擇合理的工藝方案,最有效、經濟 地制造模具。
一:鑄造的定義和流程
1.2 重力鑄造
重力鑄造是在重力作用下,將熔融金屬或合金,澆入 金屬材料制成的鑄型內獲得鑄件的工藝方法,也叫金屬型 鑄造或永久型鑄造
一:鑄造的定義和流程
1.3 砂型鑄造
將金屬或合金(銅合金)通過加熱至熔化狀態,再澆入已 准備好的型砂鑄型中,待其凝固成型,形成所需要的具有特 定性質的坯件的整個過程。(其特點:鑄型材料為粘土型砂)
一:鑄造的定義和流程
1.4 重力鑄造流程
模具安裝
砂芯模安裝
模具預熱
模具加熱
配樹脂砂
下砂芯合模
射砂加熱
澆注 開模打料 模腔清理
洗砂
熔化 配爐料 切割澆冒口
開模刮砂芯 領料
打磨試水
入庫
一:鑄造的定義和流程
1.5 砂型鑄造流程
裝模調機
砂芯模安裝
造型
模具加熱
配樹脂砂
下砂芯套箱
射砂加熱
壓鐵澆注 拆箱倒模 去除冒口
四:模具加工制作
4.2 模具加工設備
CNC程式加工
普通機床加工
四:模具加工制作
4.3 實例重力砂芯模的結構分解
打桿 抽芯
回位桿
彈簧 定模
安裝孔
動模 定位銷
頂針
固定板
四:模具加工制作
4.4 實例:重力鑄造砂芯模加工裝配工藝流程圖示
谎郴皐狾
称
CNC谎 的
郴皐狾籔 砰皌苝郴皐ふ 確 ふ
ó┾
耎郴皐狾↖ふ 苝脸ふ 皌篒郴皐
郴皐杆 郴皐㏕﹚狾 ﹚
郴皐㏕﹚狾杆
砰縤郴皐
谎ゴ
杆ゴ
砰 苝矗杆ふ 代放ふ 逼 ふ 逼 ふ
杆┾
造就衛浴航母
歡迎來鑄造廠參觀指導
謝謝
1、鑄件表面粗糙、結晶組織不致密,水密封 性不好。 2、占地面積大,生產環境差,勞動強度大。 3、鑄件出品率低、一般占40% 4、生產連慣性不強,浪費時間較多 。
1、金屬型導熱性高、散熱快,可以得細小、 1、一次性投資高
重
致密的結晶組織提高鑄件的力學性能小, 密封性好。
2、重力模排氣條件差,鑄件冷卻速度快,不 易補縮,工藝設計難度較大
二:模具工藝
2.4.2 十和Y型連接分析
二:模具工藝
2.4.3 過渡連接分析
(1) 不正確
(2) 正確
(1) 不正確
過渡連接 不同壁厚45度倒角過渡
(2) 正確
二:模具工藝
2.5 鑄造缺陷分析 1. 氣孔 2. 縮孔、縮松、疏松 3. 冷裂、熱裂、冷隔 4. 夾渣、夾砂、金屬夾雜
三:模具設計