大型磷铵装置国产化设计
大型磷酸一铵装置工程设计优化
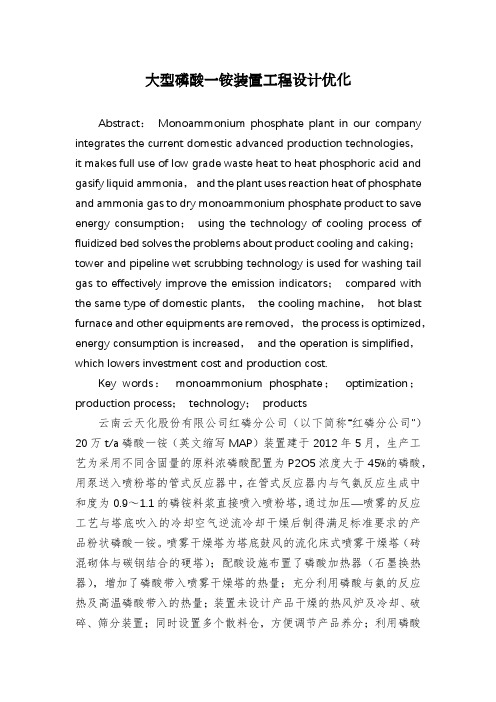
大型磷酸一铵装置工程设计优化Abstract:Monoammonium phosphate plant in our company integrates the current domestic advanced production technologies,it makes full use of low grade waste heat to heat phosphoric acid and gasify liquid ammonia,and the plant uses reaction heat of phosphate and ammonia gas to dry monoammonium phosphate product to save energy consumption;using the technology of cooling process of fluidized bed solves the problems about product cooling and caking;tower and pipeline wet scrubbing technology is used for washing tail gas to effectively improve the emission indicators;compared with the same type of domestic plants,the cooling machine,hot blast furnace and other equipments are removed,the process is optimized,energy consumption is increased,and the operation is simplified,which lowers investment cost and production cost.Key words:monoammonium phosphate;optimization;production process;technology;products云南云天化股份有限公司红磷分公司(以下简称“红磷分公司”)20万t/a磷酸一铵(英文缩写MAP)装置建于2012年5月,生产工艺为采用不同含固量的原料浓磷酸配置为P2O5浓度大于45%的磷酸,用泵送入喷粉塔的管式反应器中,在管式反应器内与气氨反应生成中和度为0.9~1.1的磷铵料浆直接喷入喷粉塔,通过加压—喷雾的反应工艺与塔底吹入的冷却空气逆流冷却干燥后制得满足标准要求的产品粉状磷酸一铵。
国内外磷酸二铵技——黄文雄
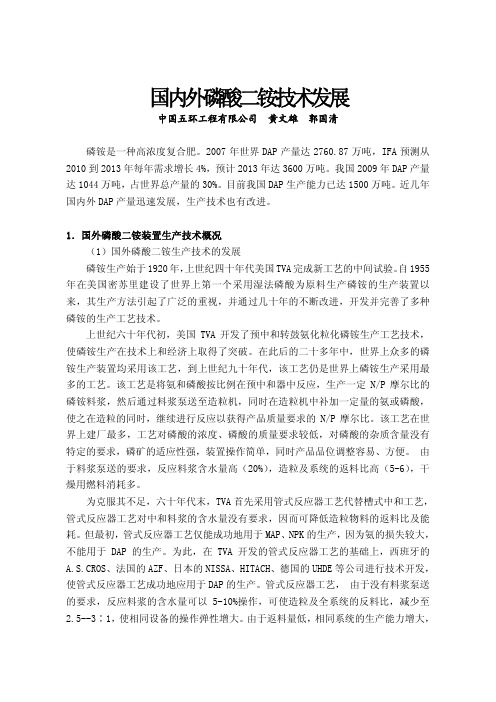
国内外磷酸二铵技术发展中国五环工程有限公司 黄文雄 郭国清磷铵是一种高浓度复合肥。
2007年世界DAP产量达2760.87万吨,IFA预测从2010到2013年每年需求增长4%,预计2013年达3600万吨。
我国2009年DAP产量达1044万吨,占世界总产量的30%。
目前我国DAP生产能力已达1500万吨。
近几年国内外DAP产量迅速发展,生产技术也有改进。
1.国外磷酸二铵装置生产技术概况(1)国外磷酸二铵生产技术的发展磷铵生产始于1920年,上世纪四十年代美国TVA完成新工艺的中间试验。
自1955年在美国密苏里建设了世界上第一个采用湿法磷酸为原料生产磷铵的生产装置以来,其生产方法引起了广泛的重视,并通过几十年的不断改进,开发并完善了多种磷铵的生产工艺技术。
上世纪六十年代初,美国TVA开发了预中和转鼓氨化粒化磷铵生产工艺技术,使磷铵生产在技术上和经济上取得了突破。
在此后的二十多年中,世界上众多的磷铵生产装置均采用该工艺,到上世纪九十年代,该工艺仍是世界上磷铵生产采用最多的工艺。
该工艺是将氨和磷酸按比例在预中和器中反应,生产一定N/P摩尔比的磷铵料浆,然后通过料浆泵送至造粒机,同时在造粒机中补加一定量的氨或磷酸,使之在造粒的同时,继续进行反应以获得产品质量要求的N/P摩尔比。
该工艺在世界上建厂最多,工艺对磷酸的浓度、磷酸的质量要求较低,对磷酸的杂质含量没有特定的要求,磷矿的适应性强,装置操作简单,同时产品品位调整容易、方便。
由于料浆泵送的要求,反应料浆含水量高(20%),造粒及系统的返料比高(5-6),干燥用燃料消耗多。
为克服其不足,六十年代末,TVA首先采用管式反应器工艺代替槽式中和工艺,管式反应器工艺对中和料浆的含水量没有要求,因而可降低造粒物料的返料比及能耗。
但最初,管式反应器工艺仅能成功地用于MAP、NPK的生产,因为氨的损失较大,不能用于DAP的生产。
为此,在TVA开发的管式反应器工艺的基础上,西班牙的A.S.CROS、法国的AZF、日本的NISSA、HITACH、德国的UHDE等公司进行技术开发,使管式反应器工艺成功地应用于DAP的生产。
磷酸一铵设计
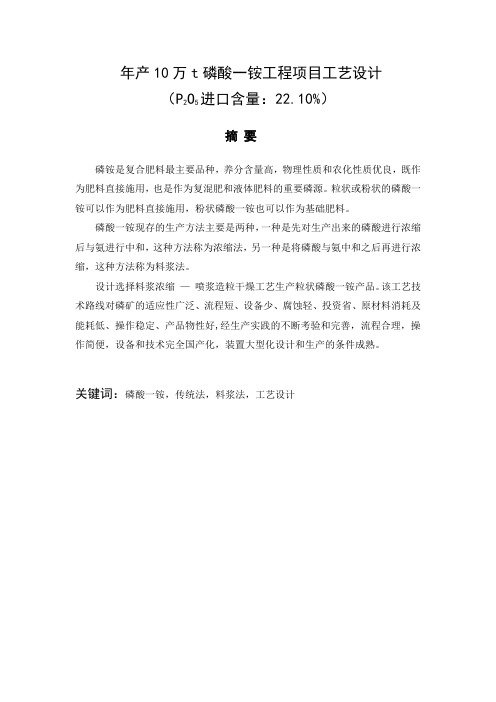
年产 10 万 t 磷酸一铵工程项目工艺设计 (P2O5 进口含量:22.10%)
磷酸一铵又称磷酸二氢铵。无色透明正方晶系晶体,白色粉状或颗粒状物(粒 状产品具有较高的颗粒抗压强度),密度约 1.80g/cm3(19℃),熔点 190℃,易 溶于水,水溶液呈酸性,微溶于醇、不溶于丙酮;堆密度约 960~1040kg/m3;粉 状产品有一定吸湿性。常温下稳定,无氧化还原性;遇高温、酸碱、氧化还原性 物质不会燃烧、爆炸。 磷酸一铵(MAP)宜作饲料添加剂,是一种水溶性速效复 合肥,有效磷(AP2O5)与总氮(TN)含量的比例约 5.44:1,是高浓度磷复肥的 主要品种之一。该产品一般作追肥,也是生产三元复混肥、BB 肥最主要的基础 原料;其中还含有钙、镁、硫、硅、铁等作物生长所需要的中量、微量元素。该 产品广泛适用于水稻、小麦、玉米、高粱、棉花、瓜果、蔬菜等各种粮食作物和 经济作物;广泛适用于红壤、黄壤、棕壤、黄潮土、黑土、褐土、紫色土、白浆 土等各种土质;尤其适合于我国西北、华北、东北等干旱少雨地区施用。贮存时 为了防止产品受潮结块、变质,应放于室内或在产品上铺蓬布等防护物,同时避
20 世纪 50 年代初,美国 Tennessee Valley Authority(简称 TVA)研制了转 鼓氨化造粒机,首先用于普钙或重钙的氨化与造粒,并于 1956 年获准专利。这 种造粒机简单、耐用,从过磷酸钙到 MAP、DAP 和 NPK 三元复合肥均可用它进行 造粒,这在化肥工业上是一项重大的技术革新。从此,预中和-转鼓氨化造粒便 成为生产磷铵和颗粒复合肥的通用流程。但这种流程的缺点是预中和设备庞大和 只能用 P2O5 质量分数小于 40%的磷酸进行氨中和(为避免料浆过稠不便操作和输 送),因而干燥产品要消耗较多燃料。
重庆华强拟建硫酸磷铵装置技改项目
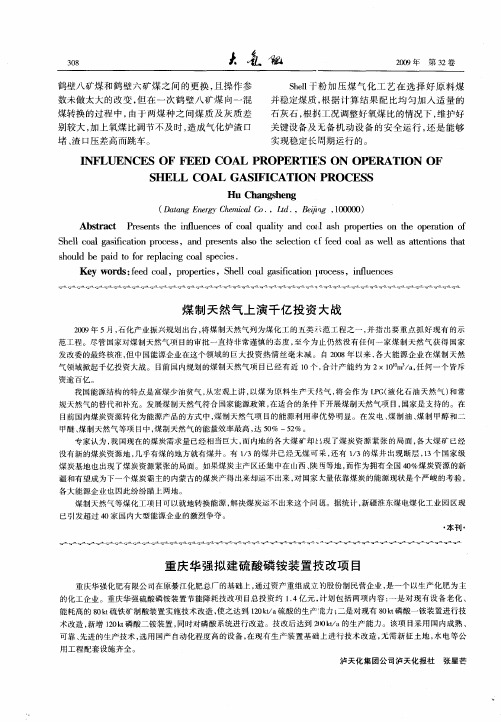
本刊・
4
4
^ _
重庆 华 强拟 建 硫 酸磷 铵装 置 技 改 项 目
重庆华强 拘股份制民营企业 , 是一个以生产化肥为主
的化工企业 。重庆华强硫酸磷 铵装 置节 能降耗技 改项 目总投 资约 14 元 , .亿 计划包括 两项 内容 : 一是对 现有设备 老化 、 能耗高 的 8 k硫铁矿制酸装 置实施技术改造 , 之达到 10 ta 酸的生产’ ; 0t 使 2k 硫 / 拒力 二是对现有 8 k磷 酸一铵装 置进行技 0t 术改造 , 新增 10 t 2 k 磷酸二铵装置 , 同时对磷酸 系统进行改造 。技改后达到 20 ta的生产能力 。该项 目采用 国内成熟 、 ok / 可靠 、 先进的生产技 术 , 选用 国产 自动化程度高的设备 , 在现有生产 装置基础上进行 技术改造 , 无需新 征土地 , 水电等公
Absr c P e e t h n u n e fc a u i n o a h p o e t s o h p r t n o ta t r s ns te if e c s o o lq a t a d c t s rp ri n t e o e ai f l l y l e o s elc a a i c to rc s .a d p e e t lo te s lcin c e d c a swela t n in h t h l o lg sf ain p o e s n rs n s as h ee to fe o la l sat to s t a i f e s o l e p i o frr pa i g c a p ce . h ud b ad t o e lcn o ls e is Ke r s:e d c a ,p o ris h l c a a i c t n l o e s n u n e y wo d fe o l r p t ,S el o lg sf ai  ̄ c s ,i e c s e e i o r l f
云南富瑞化工有限公司30万吨年磷酸装置施工组织设计
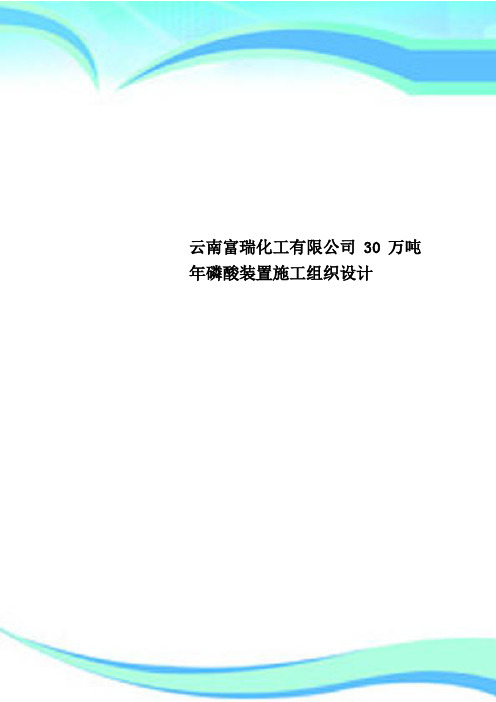
云南富瑞化工有限公司30万吨年磷酸装置施工组织设计云南富瑞化工有限公司30万吨/年磷酸装置施工组织设计编制:陈永宏罗斌林贺曙红李北京审核:张敏审定:李涛中化二建集团有限公司二○○三年一月十八日目录1.编制说明2.编制依据3.工程项目简述4.施工部署5.施工进度计划6.主要施工方法7.劳动力组织8.施工机械设备进场计划9.临时设施规划10.保证工期措施11.质量保证措施12.安全文明健康施工13.环境保护措施14.冬、雨季施工措施15.施工中应遵循的施工标准及规范16.施工中应编制的施工方案17.附图:总体施工进度计划网络图施工平面布置图工程项目质量控制程序图施工技术管理基本程序图项目部安全目标管理流程图钢筋施工质量程序控制图模板施工质量程序控制图混凝土施工质量程序控制图静止设备安装程序图传动设备安装程序图工艺配管施工程序图钢结构预制安装程序现场焊接管理程序1.编制说明本工程为云南富瑞化工有限公司国产化示范项目60万砘/年磷酸工程的配套工程,位于云南省安宁市草铺镇云南磷肥有限公司厂区内,昆畹公路旁,距省会昆明市47KM。
为科学有序地组织施工,特编制本施工组织设计。
2.编制依据2.1 云南富瑞化工有限公司30万吨/年磷酸装置建筑、安装工程公开招标文件2.2 中国五环化工工程公司设计的有关施工图纸2.3《施工组织设计标准》HG20235-982.4 国家现行有关施工及验收规范2.5 同类工程施工经验3.工程项目简述3.1建设地点: 云南省安宁市草铺镇云南磷肥有限公司厂区内3.2合同工期:计划工期 300天3.3工程质量标准: 优良3.4工程自然条件海拔高度: 1879.6~1881.22极端最高气温: 33.3℃极端最低气温: -7℃最热月平均气温: 20.1℃最冷月平均气温: 7.7℃年均降雨量: 900.9mm最大降雨量: 1161.8mm最大日降雨量: 153.3mm最大积雪深度 230 mm3.5磷酸装置的工号组成3.5.1反应贮存工序3.5.2过滤贮存工序3.5.3浓缩、氟吸收工序3.5.4尾气洗涤工序3.6工程特点3.6.1 磷酸装置关键设备过滤机使用PRAYON-BIRP倾覆盖式过滤机,主要材质是904L不锈钢,安装质量要求高,应高度重视.3.6.2衬里设备占80%,防腐质量等级要求高,现场组焊设备占18%,品种多,焊接要求高,这两项工作是磷酸装置安装工作的关键线路。
大型国产化大化肥装置氨合成塔封头大盖安装
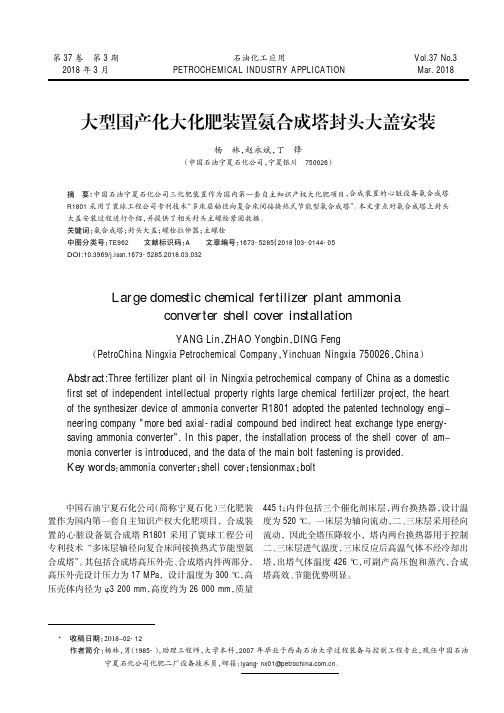
*收稿日期:2018-02-12作者简介:杨林,男(1985-),助理工程师,大学本科,2007年毕业于西南石油大学过程装备与控制工程专业,现任中国石油宁夏石化公司化肥二厂设备技术员,邮箱:lyang-nx01@ 。
Large domestic chemical fertilizer plant ammoniaconverter shell cover installationYANG Lin ,ZHAO Yongbin ,DING Feng(PetroChina Ningxia Petrochemical Company ,Yinchuan Ningxia 750026,China )Abstract:Three fertilizer plant oil in Ningxia petrochemical company of China as a domestic first set of independent intellectual property rights large chemical fertilizer project,the heart of the synthesizer device of ammonia converter R1801adopted the patented technology engi -neering company "more bed axial-radial compound bed indirect heat exchange type energy-saving ammonia converter".In this paper,the installation process of the shell cover of am -monia converter is introduced,and the data of the main bolt fastening is provided.Key words :ammonia converter ;shell cover ;tensionmax ;bolt大型国产化大化肥装置氨合成塔封头大盖安装杨林,赵永斌,丁锋(中国石油宁夏石化公司,宁夏银川750026)摘要:中国石油宁夏石化公司三化肥装置作为国内第一套自主知识产权大化肥项目,合成装置的心脏设备氨合成塔R1801采用了寰球工程公司专利技术“多床层轴径向复合床间接换热式节能型氨合成塔”。
瓮福紫金磷酸磷铵项目10万t/a湿法净化磷酸装置一次化工投料试车成功
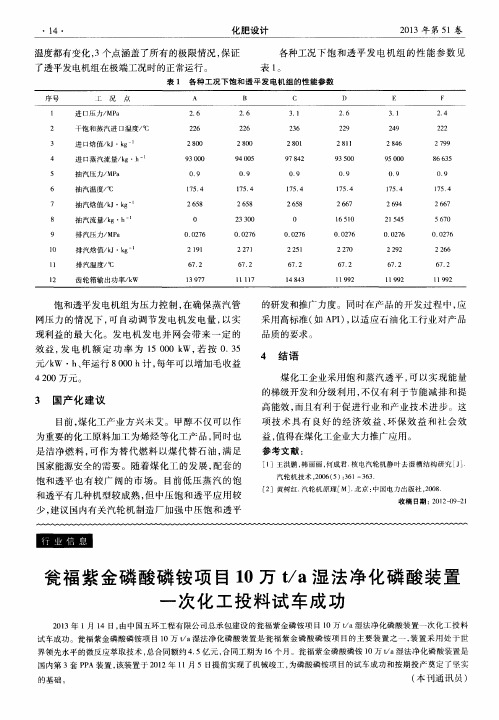
瓮 福 紫 金磷 酸磷 铵 项 目 1 0万 t / a湿 法 净化 磷 酸 装 置 次化 工投 料试 车成 功
一
2 0 1 3年 1月 1 4日, 由中国五环工程有限公 司总承包建设 的瓮福紫金磷铵项 目 1 0万 t / a 湿法净化磷酸装置一次化工投料 试 车成功 。瓮福紫金磷酸磷铵项 目 1 0万 t / a 湿法净化磷酸装置是瓮福 紫金磷酸磷铵 项 目的主要 装置之一 , 装置 采用处于世
的基础。
( 本 刊通 讯 员 )
品质 的要求 。
效益 , 发 电机 额 定 功 率 为 1 5 0 0 0 k W, 若按 0 . 3 5 k W・ h 、 年 运行 8 0 0 0 h计 , 每年可 以增 加毛 收益
4 2 0 0万 元 。
4 结 语
煤化 工企业 采用 饱 和蒸 汽透 平 , 可 以实 现 能量
.
1 4.
化肥设 计
2 0 1 3年 第 5 1 卷
温度 都有 变化 , 3个 点涵 盖 了所有 的极 限情况 , 保 证 了透平 发 电机组 在极 端工 况时 的正 常运行 。
各种工 况 下饱 和透 平发 电机 组 的 性 能 参 数 见 表1 。
表 1 各 种 工 况 下 饱 和 透 平 发 电机 组 的 性 能 参数
进 口蒸 汽 流 量/ k g・ h 抽 汽 压 力/ MP a 抽 汽 温 度/ ℃ 抽汽 焓 值 / k J・ k g 抽汽 流 量 / k g・ h 排 汽 压 力/ MP a 排 汽 焓值 / k J・ k g 排 汽 温 度/ ℃
2 8 0 0
9 3 0 0 0 0 . 9 1 7 5 . 4 2 6 5 8 0 0 . 0 2 7 6 2 1 9 1 6 7 . 2
大型磷铵装置技术探讨及国产化设计
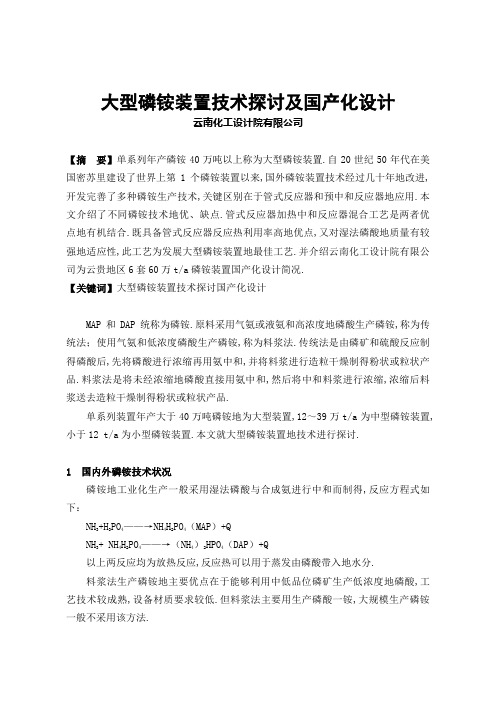
大型磷铵装置技术探讨及国产化设计云南化工设计院有限公司【摘要】单系列年产磷铵40万吨以上称为大型磷铵装置.自20世纪50年代在美国密苏里建设了世界上第1个磷铵装置以来,国外磷铵装置技术经过几十年地改进,开发完善了多种磷铵生产技术,关键区别在于管式反应器和预中和反应器地应用.本文介绍了不同磷铵技术地优、缺点.管式反应器加热中和反应器混合工艺是两者优点地有机结合.既具备管式反应器反应热利用率高地优点,又对湿法磷酸地质量有较强地适应性,此工艺为发展大型磷铵装置地最佳工艺.并介绍云南化工设计院有限公司为云贵地区6套60万t/a磷铵装置国产化设计简况.【关键词】大型磷铵装置技术探讨国产化设计MAP和DAP统称为磷铵.原料采用气氨或液氨和高浓度地磷酸生产磷铵,称为传统法;使用气氨和低浓度磷酸生产磷铵,称为料浆法.传统法是由磷矿和硫酸反应制得磷酸后,先将磷酸进行浓缩再用氨中和,并将料浆进行造粒干燥制得粉状或粒状产品.料浆法是将未经浓缩地磷酸直接用氨中和,然后将中和料浆进行浓缩,浓缩后料浆送去造粒干燥制得粉状或粒状产品.单系列装置年产大于40万吨磷铵地为大型装置,12~39万t/a为中型磷铵装置,小于12 t/a为小型磷铵装置.本文就大型磷铵装置地技术进行探讨.1 国内外磷铵技术状况磷铵地工业化生产一般采用湿法磷酸与合成氨进行中和而制得,反应方程式如下:NH3+H3PO4——→NH4H2PO4(MAP)+QNH3+ NH4H2PO4——→(NH4)2HPO4(DAP)+Q以上两反应均为放热反应,反应热可以用于蒸发由磷酸带入地水分.料浆法生产磷铵地主要优点在于能够利用中低品位磷矿生产低浓度地磷酸,工艺技术较成熟,设备材质要求较低.但料浆法主要用生产磷酸一铵,大规模生产磷铵一般不采用该方法.传统法工艺通常既能生产磷酸一铵,也能生产磷酸二铵,而且可以建设大型磷铵生产装置.1.1 国外磷铵工艺技术简况磷铵是一种高浓度复合肥,自1917年在美国密苏里建设了世界第1个采用湿法磷酸为原料生产磷铵地装置以来,其生产方法引起了广泛地重视,通过几十年地不断改进,开发并完善了多种磷铵地生产工艺技术.20世纪60年代,美国TVA开发了预中和转鼓氨化粒化磷铵生产工艺技术,使磷铵在生产技术上和经济上取得了突破,在此后地20多年中世界上众多地磷铵生产装置均采用该工艺.截止目前,该工艺仍是世界上磷铵生产采用最多地工艺.该工艺对磷矿地适应性强,操作简单,但要求反应槽中和料浆地含水量在12%~25%,以保证料浆地流动性,致使造粒物料地返料比较高,能耗也较高.为克服不足,20世纪70年代末,TVA首先采用管式反应器工艺代替槽式中和工艺.管式反应器工艺对中和料浆地含水量要求低,因而可降低造粒物料地返料比及能耗低.但最初,管式反应器技术仅能成功地用于MAP、NPK地生产,不能用于DAP地生产.为此,在TVA开发地管式反应器工艺基础上,西班牙地INCRO,ESPANDESA,法国地AZF,荷兰荷丰等公司进行技术开发,使管式反应器工艺成功地应用于DAP地生产.同时为方便装置生产和操作控制,美国JACOBS和西班牙地INCRO公司结合管式反应器工艺和预中和器工艺地优点,开发出预中和+管式反应器地联合工艺,该工艺操作简单、灵活.目前国外生产磷铵地工厂主要分布在美国、日本、印度、土耳其、法国等国家.装置规模大型化是国外磷铵生产发展地大趋势,最近几年,已在沙特、印度等许多第三世界国家和地区投资兴建了数套大规模DAP/NPK装置,当前国外单系列最大规模已达到3712t/d磷铵(美国).1.2 国内磷铵工艺技术简况我国在1963年就完成了中和双轴制磷铵地实验,1969年南化磷肥厂建成1套年产3万吨磷铵装置,采用多槽中和喷浆造粒干燥工艺,但由于设备结构不合理,于1974年改为预中和转鼓氨化粒化工艺.针对我国磷矿地特点,近十多年,建设了一批小型“料浆法”磷铵装置,为我国磷复肥生产地发展做出了一定地贡献.为满足农业对磷肥地需要,20世纪80年代以来,我国先后引进国外先进地工艺技术建设了多套DAP装置(见表1).铜陵磷铵厂年产12万吨DAP装置采用喷浆造粒干燥技术;南化、大连年产24万吨DAP装置采用预中和转鼓氨化粒化工艺技术;黄麦岭年产18万吨MAP/DAP装置采用预中和加十字管反应器工艺;中阿化肥有限公司年产48万吨DAP(NPK)装置采用双管式反应器工艺;广西鹿寨、江西贵溪年产24万吨DAP装置,贵州宏福年产60万吨DAP装置采用单管式反应器工艺;云南三环中化嘉吉化肥公司年产60万吨DAP,云南三环年产2×60万吨DAP,贵州开阳2×60万吨DAP,贵州息烽60万吨DAP等装置,均采用预中和加管式反应器混合工艺技术.通过多年地消化、吸收和生产,目前我国在磷铵工程设计、设备制造、生产等方面基本与国际水平接近.表1 国内磷酸二铵地生产装置及技术简况2. 几种典型磷铵生产工艺技术比较磷铵生产地工艺技术较多,大中型装置基本体现在反应系统设置不同,目前主要地生产工艺有:预中和转鼓氨化粒化工艺、预中和+管式反应器工艺、双管式反应器工艺、单管式反应器工艺.下面就几种典型工艺特点介绍如下:2.1 预中和转鼓氨化粒化工艺预中和转鼓氨化粒化工艺是由美国国家肥料开发中心(NFDC)开发研究,又称TVA流程.该工艺是将氨和磷酸按比例在预中和器中反应,生产一定n(N)/n(P)比地磷铵料浆,然后通过料浆泵送至造粒机,同时在造粒机中补加一定量地氨和磷酸,使之在造粒地同时,继续进行反应以获得产品质量要求地n(N)/n(P).该工艺在世界上建厂最多,目前我国已有6套年产24万吨生产装置,大多生产DAP.工艺优点:①从20世纪60年代开发一直使用至今,其技术相当成熟可靠,我国也有丰富地设计和生产经验;②对磷酸地浓度、磷酸地质量要求较低,对磷酸地杂质含量没有特定地要求,对磷矿地适应性强,装置操作简单,同时产品品位调整容易,方便操作容易掌握.该工艺缺点:①技术不够先进;②与管式反应工艺相比,需要中和槽及料浆泵送系统,流程较复杂,设备故障多,维修量大;③由于料浆泵输送地要求料浆含水量较高(20%),造粒及系统地返料比高(5~6),相同规格设备地操作弹性小,干燥能量消耗多;④需要使用消泡剂,操作费用增加;⑤造粒机固体床层内需氨分布器及其支承管梁,氨分布器容易堵塞,支承管梁易产生积料现象,影响装置开工率.2.2 单管式反应器工艺单管反应器工艺是管式反应器安装在造粒机中,氨和磷酸地反应在管式反应器中一次完成.该工艺建厂生产MAP较多,生产DAP地目前全世界约有10余套装置,其中我国有3套装置在生产,即江西贵溪24万吨/年DAP(技改)、广西鹿寨24万吨/年DAP(新建)、贵州宏福24万吨/年DAP(技改).工艺优点:①采用单管反应器工艺,磷酸和氨能够一次氨化到磷铵产品要求地氮磷比,改变操作负荷,调节产品规格、调整中和反应条件容易;②没有中和槽和料浆泵送系统,使流程简化,减少了操作和维修费用;③造粒机固体床层内无需氨分布器(无二次氨化),支承氨分布器地钢结构可以取消,消除了氨分布器容易堵塞而停车以及支承管梁地积料现象;④由于没有料浆泵送地要求,反应料浆地含水量可以降至5%~10%操作,可使造粒及全系统地返料比减至(2.5~3:1),使相同设备地操作弹性增大;⑤由于返料量少,相同规格设备地生产能力增大,单位产品地能耗量低,使干燥能耗少,操作费用减少;⑥可以不用消泡剂,降低操作费用;⑦管式反应器设置蒸汽自动吹扫系统,有效地防止堵塞,保证长周期运转;⑧利用循环洗涤液地热量蒸发液氨,既可以节省蒸汽消耗,又可以降低洗涤液地温度,提高洗涤率.工艺缺点:①对磷酸质量地要求比槽式反应器工艺严格;②生产DAP时造粒机内地反应热量大,需要通过加大空气量移走热量,逸出氨量大(约占总氨量地15%~20%),NH3尾气洗涤器负荷大;③对操作工地要求较高.2.3双管式反应器工艺双管式反应器工艺是2个管式反应器分别安装在造粒机和干燥机中,氨和磷酸地反应在管式反应器中进行.该工艺生产MAP较多,生产DAP地目前全世界约有15套装置,其中我国仅有中阿公司1套年48万吨DAP装置在生产.工艺优点:①采用2个管式反应器,技术先进,造粒机内地反应热容易移走,即热平衡容易解决;②没有中和槽和料浆泵送系统,使流程简化,减少了操作和维修费用;③由于没有料浆泵送地要求,反应料浆地含水量低,可使造粒及全系统地返料比减至3:1,生产系统地操作弹性增大;④由于返料量低,相同规格设备地生产能力增大,干燥用燃料消耗少,单位地能耗低,操作费用减少;⑤可以不用消泡剂,降低操作费用;⑥采用液氨直接加料,节省蒸汽消耗;⑦管式反应器设有自动除垢系统,可以保证装置长周期运转.工艺缺点:①对磷酸质量地要求比槽式反应器工艺严格;②生产DAP时氨需要从3点加入(2个管式反应器及造粒机内固体床层),因此氨地分配复杂,操作调节难度较大;③干燥机内地管式反应器必须使用w(P2O5)50%地浓磷酸;④由于干燥机内管式反应器生产地是磷酸一铵,不可避免要进入成品中,因此,产品地最终氨化度比其它工艺低(即产品地氨含量低);⑤造粒机固体床层内需要氨分布器及其支承管梁,氨分布器容易堵塞,支承管梁易产生积料现象.2.4预中和+管式反应器工艺预中和+管式反应器工艺是结合预中和转鼓氨化粒化工艺和管式反应器工艺地优点发展起来地混合工艺.该工艺相对预中和转鼓氨化粒化工艺,允许反应料浆有更高地含水量,操作弹性更大,对物料适应性更强,料浆输送泵及输送管线不易堵塞;由于造粒机中进行部分氨和磷酸地反应,带入造粒机地水量少,返料系统设备尺寸小,装置投资低;同时干燥系统负荷降低,能耗较低.同时使用预中和反应槽和管式反应器生产磷铵料浆,在氨化粒化机(造粒机)中进一步氨化,在管式反应器中直接使用浓磷酸,并利用反应热蒸发水分,使进入造粒机中地水分减少,从而降低返料比和节约能耗.3 年产60万吨DAP国产化设计简况3.1 简述年产60万吨DAP装置由3部分组成:① 氨、磷酸以及硫酸贮运部分;② DAP等制造部分(含原料准备、反应、造粒、洗涤);③ 成品包装贮运部分.以上3部分地设计包括工艺、设备、土建(含总图)、电气、自控、水道、暖通等.3.2 装置主要技术地基本情况该装置由1条生产线组成,采用管式反应器及预中和器混合工艺技术,能够适应生产60万吨/年DAP(或GMAP)和NPK系列粒状产品.磷酸、氨、硫酸、尿素、钾盐、填料和包裹油等为其必要地原料.该技术是满足氨和磷酸地中和反应而精心设计地,建立在管式反应器(PR)及反应稳定地预中和器(PN)基础上.本装置技术优点:(1)生产能力最大化管式反应器直接安装在造粒机内.它能够生产含水率4%~8%地磷铵料浆,从而使造粒床层地湿度能够调节在造粒所需地最佳条件,同时降低了返料比(4:1左右).特别是用易溶原料硝铵、尿素等生产高浓度NPK产品时,具有能保证粒床在湿度大、产品将趋于大粒化时造粒生产率不变地特点.(2)能耗低由于返料比低(4:1),故成本地构成中,如蒸汽、电、燃料、水等地消耗相应降低.(3)产品质量好本装置由于采用PR与PN工艺联合生产,其产品地品质、粒度、湿度和硬度均达到目前国际先进标准.(4)设备操作简单、维护保养费用低管式反应器地正常操作简单,但反应速率非常高,由于设计了自动清理程序,降低了堵塞几率;管式反应器反应头地设计,能保证磷酸和氨充分混合,达到反应高效和洗涤系统低负荷与高效率;在造粒机设置了1个犁型高效氨分布装置,它平行于造粒机,可防止启动时断裂,又避免物料聚积其上.所有反应均在预中和反应器及造粒机内完成,避免在干燥机使用额外地设备而带来其它不利因素.由于较高地开车率和较低地返料比,从而减少了操作维护费用.(5)高氨化率由于逸出到洗涤系统地氨量随n(N)/n(P)地增加而递增,当n(N)/n(P)比大于1.7后,氨逸出量迅速上升,所以管式反应器可控制一个适合地氨化程度(1.5~1.6最佳),并在造粒机中完成全部氨化反应.本装置由于设计了一个十分合理地氨分布器,使氨被喂入造粒机固体物料深处,而达到降低氨逸出损失,同时有利于颗粒表面发生氨化反应,导致水分额外蒸发和产品更干更硬.(6)无污染由于管式反应器和氨化系统地效率高,其工艺基本上没有污染.逸出地微量氨、粉尘和氟将在高效洗涤系统予以回收.本装置地洗涤系统使用地工回收率大于99%,除氟效率艺及设备设计完善,洗涤效率较高(除尘效率大于99%,NH3大于95%),尾气达标排放.(7)操作参数调节地弹性强将管式反应器和氨化系统2种操作融合起来,在调节造粒床层地湿度和温度方面各种配方都具有高地操作弹性,为低返料比、高粒化率、高生产率和稳定设备操作方面打下了良好地基础.(8)装置地多功能性可以根据市场需求,选用不同地原料,生产不同品种和等级地产品.对DAP和GMAP地生产,均采用液态原料(磷酸、氨和硫酸).DAP地生产,本装置地设计充分考虑各用户地要求,可以分别使用管式反应器+预中和反应器或单独使用预中和反应器生产DAP,并达标达产.对于GMAP产品,仅用管式反应器工艺(PR)即可.对于NPK系列产品,根据氮源,选择液态氨和固态氨混合态几种方案均可.3.3设计中地消化、吸收和改进本装置在消化、吸收和改进国内原引进技术地基础上,我们与业主进行了多次精心地研究,结合业主地实际情况,通过不断优化和完善设计,在设计中主要做了以下几方面地改进:(1)为了确保造粒、干燥机以及收尘、洗涤系统地环境和洗涤效果,需确保造粒、干燥系统处于负压状态下运转,保证含氨、氟、尘等尾气地回收,并结合云贵高原地特点,将主风机K401、K402增加风压头约2kPa,并只引进风机地叶轮及转动部分,其它国内配套,这样可节省较多地投资.实践表明,其改进效果是好地.(2)考虑到强化生产,根据生产磷铵时反应较剧烈地特点,将预中和器地尺寸适当放大,在只采用PN工艺时产量可可以达到90t/h,其粒子地圆整度会更好,但水平衡受到限制.(3)配合预中和反应器地修改,预中和器料浆泵也适当提高流量和扬程.(4)考虑到洗涤系统由于雨季带来地水平衡问题,增设了1个事故水池,系统水不平衡时,可将多余地水置于事故水池中,等正常时,又返回系统.(5)由于尾气洗涤塔塔身直径Ф7300mm,出口管径太大(Ф3400mm),不宜另建80m高地尾气烟囱,因此,利用尾气洗涤塔高27m地塔身为“底座”,在其出口接53m长地排气筒,采用经济实用地钢结构塔架支承,节省投资约100万元,并使装置布置更紧凑合理,减少系统阻力,有利于提高产量和洗涤效果.(6)为尽量减少尾气地带沫现象,在尾气洗涤塔出口处设计旋流板除沫器.(7)为了提高破碎效率,将链式破碎机改为辊式破碎机.(8)为了降低运转成本,将烧油热风炉改为烧煤粉沸腾热风炉,效果很好.(9)干燥机出口皮带秤宽度设计1400mm,以使操作更安全、稳定.(10)在设备及管道选材上,也结合我国及云贵地实际,选择适用、可靠、耐腐蚀、价格较合理地材质,以尽可能降低建设投资.4 初步建议通过对各种典型工艺地先进性、可靠性,对原料地适应性,操作地稳定性,装置投资地综合比较,各种中、大型磷铵装置地生产技术理论上基本相同,但又各有特点,关键区别于管式反应器.由于管式反应器加预中和反应槽混合工艺是把管式反应器和预中和槽反应器有机结合起来,既具备了管式反应器地优点,同时对湿法磷酸地质量有较强地适应性.我们认为发展我国大型磷铵技术,预中和反应器+管式反应器混合工艺为最佳工艺技术.如果只生产GMAP和NPK时,用管式反应器生产即可达到产品质量地要求.目前就我国地设计技术、设备制造技术、材质等水平,年产60万吨磷铵(DAP或MAP)装置可全部国产化.国产化是指全部装置地70%以上由国内供应,我院在给云贵做地6单系列60万吨/年DAP装置均达到80%以上.由于种种原因,目前一些设备或关键部位仍需进口.例如:洗涤及干燥风机地叶轮、干燥机出口斗提机链条、破碎机等.但我们了解到上述设备国内制造商表示,他们可以提供这些设备,例如沈鼓表示他们可以提供洗涤和干燥风机.干燥斗提机、破碎机,昆重等公司表示他们也可以提供,希望得到有关单位地支持.所谓有关单位支持即是由磷肥协会牵头,组织有关设计、制造及生产单位参加地技术攻关小组,先对已引进地类似设备进行测绘开发,在一家有经验地DAP生产厂试用,改进并最后达到和超过“引进”设备地各项指标.我们认为,这是可行地.另外,关于流化床冷却器,目前国内湖北三联节能环保设备厂可以提供,工艺筛及精制筛鞍山矿山机器厂可以提供.综上所述,我们认为装置可以全部国产化.我国国家级磷复肥基地主要在云贵,由于云贵属高原地区,海拔较高,气压较低,同类风机地效率仅为海平面地区地80%左右,就目前而言,综合比较各种因素,发展磷铵生产装置,单系列最大装置能力仍为60万吨/年为宜.实践也表明这一规模是成功地,而其它海拔较低地地区,可适当发展规模为90万吨/年磷铵单系列装置,但应考虑原料地保证供应问题.。
- 1、下载文档前请自行甄别文档内容的完整性,平台不提供额外的编辑、内容补充、找答案等附加服务。
- 2、"仅部分预览"的文档,不可在线预览部分如存在完整性等问题,可反馈申请退款(可完整预览的文档不适用该条件!)。
- 3、如文档侵犯您的权益,请联系客服反馈,我们会尽快为您处理(人工客服工作时间:9:00-18:30)。
大型磷铵装置技术探讨及国产化设计云南化工设计院有限公司【摘要】单系列年产磷铵40万吨以上称为大型磷铵装置。
自20世纪50年代在美国密苏里建设了世界上第1个磷铵装置以来,国外磷铵装置技术经过几十年的改进,开发完善了多种磷铵生产技术,关键区别在于管式反应器和预中和反应器的应用。
本文介绍了不同磷铵技术的优、缺点。
管式反应器加热中和反应器混合工艺是两者优点的有机结合。
既具备管式反应器反应热利用率高的优点,又对湿法磷酸的质量有较强的适应性,此工艺为发展大型磷铵装置的最佳工艺。
并介绍云南化工设计院有限公司为云贵地区6套60万t/a磷铵装置国产化设计概况。
【关键词】大型磷铵装置技术探讨国产化设计MAP和DAP统称为磷铵。
原料采用气氨或液氨和高浓度的磷酸生产磷铵,称为传统法;使用气氨和低浓度磷酸生产磷铵,称为料浆法。
传统法是由磷矿和硫酸反应制得磷酸后,先将磷酸进行浓缩再用氨中和,并将料浆进行造粒干燥制得粉状或粒状产品。
料浆法是将未经浓缩的磷酸直接用氨中和,然后将中和料浆进行浓缩,浓缩后料浆送去造粒干燥制得粉状或粒状产品。
单系列装置年产大于40万吨磷铵的为大型装置,12~39万t/a为中型磷铵装置,小于12 t/a 为小型磷铵装置。
本文就大型磷铵装置的技术进行探讨。
1 国内外磷铵技术状况磷铵的工业化生产一般采用湿法磷酸与合成氨进行中和而制得,反应方程式如下: NH3+H3PO4——→NH4H2PO4(MAP)+QNH3+ NH4H2PO4——→(NH4)2HPO4(DAP)+Q以上两反应均为放热反应,反应热可以用于蒸发由磷酸带入的水分。
料浆法生产磷铵的主要优点在于能够利用中低品位磷矿生产低浓度的磷酸,工艺技术较成熟,设备材质要求较低。
但料浆法主要用生产磷酸一铵,大规模生产磷铵一般不采用该方法。
传统法工艺通常既能生产磷酸一铵,也能生产磷酸二铵,而且可以建设大型磷铵生产装置。
1.1 国外磷铵工艺技术概况磷铵是一种高浓度复合肥,自1917年在美国密苏里建设了世界第1个采用湿法磷酸为原料生产磷铵的装置以来,其生产方法引起了广泛的重视,通过几十年的不断改进,开发并完善了多种磷铵的生产工艺技术。
20世纪60年代,美国TVA开发了预中和转鼓氨化粒化磷铵生产工艺技术,使磷铵在生产技术上和经济上取得了突破,在此后的20多年中世界上众多的磷铵生产装置均采用该工艺。
截止目前,该工艺仍是世界上磷铵生产采用最多的工艺。
该工艺对磷矿的适应性强,操作简单,但要求反应槽中和料浆的含水量在12%~25%,以保证料浆的流动性,致使造粒物料的返料比较高,能耗也较高。
为克服不足,20世纪70年代末,TVA首先采用管式反应器工艺代替槽式中和工艺。
管式反应器工艺对中和料浆的含水量要求低,因而可降低造粒物料的返料比及能耗低。
但最初,管式反应器技术仅能成功地用于MAP、NPK的生产,不能用于DAP的生产。
为此,在TVA开发的管式反应器工艺基础上,西班牙的INCRO,ESPANDESA,法国的AZF,荷兰荷丰等公司进行技术开发,使管式反应器工艺成功地应用于DAP的生产。
同时为方便装置生产和操作控制,美国JACOBS和西班牙的INCRO公司结合管式反应器工艺和预中和器工艺的优点,开发出预中和+管式反应器的联合工艺,该工艺操作简单、灵活。
目前国外生产磷铵的工厂主要分布在美国、日本、印度、土耳其、法国等国家。
装置规模大型化是国外磷铵生产发展的大趋势,最近几年,已在沙特、印度等许多第三世界国家和地区投资兴建了数套大规模DAP/NPK装置,当前国外单系列最大规模已达到3712t/d磷铵(美国)。
1.2 国内磷铵工艺技术概况我国在1963年就完成了中和双轴制磷铵的试验,1969年南化磷肥厂建成1套年产3万吨磷铵装置,采用多槽中和喷浆造粒干燥工艺,但由于设备结构不合理,于1974年改为预中和转鼓氨化粒化工艺。
针对我国磷矿的特点,近十多年,建设了一批小型“料浆法”磷铵装置,为我国磷复肥生产的发展做出了一定的贡献。
为满足农业对磷肥的需要,20世纪80年代以来,我国先后引进国外先进的工艺技术建设了多套DAP装置(见表1)。
铜陵磷铵厂年产12万吨DAP装置采用喷浆造粒干燥技术;南化、大连年产24万吨DAP装置采用预中和转鼓氨化粒化工艺技术;黄麦岭年产18万吨MAP/DAP装置采用预中和加十字管反应器工艺;中阿化肥有限公司年产48万吨DAP(NPK)装置采用双管式反应器工艺;广西鹿寨、江西贵溪年产24万吨DAP装置,贵州宏福年产60万吨DAP装置采用单管式反应器工艺;云南三环中化嘉吉化肥公司年产60万吨DAP,云南三环年产2×60万吨DAP,贵州开阳2×60万吨DAP,贵州息烽60万吨DAP等装置,均采用预中和加管式反应器混合工艺技术。
通过多年的消化、吸收和生产,目前我国在磷铵工程设计、设备制造、生产等方面基本与国际水平接近。
2. 几种典型磷铵生产工艺技术比较磷铵生产的工艺技术较多,大中型装置基本体现在反应系统设置不同,目前主要的生产工艺有:预中和转鼓氨化粒化工艺、预中和+管式反应器工艺、双管式反应器工艺、单管式反应器工艺。
下面就几种典型工艺特点介绍如下:2.1 预中和转鼓氨化粒化工艺预中和转鼓氨化粒化工艺是由美国国家肥料开发中心(NFDC)开发研究,又称TVA流程。
该工艺是将氨和磷酸按比例在预中和器中反应,生产一定n(N)/n(P)比的磷铵料浆,然后通过料浆泵送至造粒机,同时在造粒机中补加一定量的氨和磷酸,使之在造粒的同时,继续进行反应以获得产品质量要求的n(N)/n(P)。
该工艺在世界上建厂最多,目前我国已有6套年产24万吨生产装置,大多生产DAP。
工艺优点:①从20世纪60年代开发一直使用至今,其技术相当成熟可靠,我国也有丰富的设计和生产经验;②对磷酸的浓度、磷酸的质量要求较低,对磷酸的杂质含量没有特定的要求,对磷矿的适应性强,装置操作简单,同时产品品位调整容易,方便操作容易掌握。
该工艺缺点:①技术不够先进;②与管式反应工艺相比,需要中和槽及料浆泵送系统,流程较复杂,设备故障多,维修量大;③由于料浆泵输送的要求料浆含水量较高(20%),造粒及系统的返料比高(5~6),相同规格设备的操作弹性小,干燥能量消耗多;④需要使用消泡剂,操作费用增加;⑤造粒机固体床层内需氨分布器及其支承管梁,氨分布器容易堵塞,支承管梁易产生积料现象,影响装置开工率。
2.2 单管式反应器工艺单管反应器工艺是管式反应器安装在造粒机中,氨和磷酸的反应在管式反应器中一次完成。
该工艺建厂生产MAP较多,生产DAP的目前全世界约有10余套装置,其中我国有3套装置在生产,即江西贵溪24万吨/年DAP(技改)、广西鹿寨24万吨/年DAP(新建)、贵州宏福24万吨/年DAP(技改)。
工艺优点:①采用单管反应器工艺,磷酸和氨能够一次氨化到磷铵产品要求的氮磷比,改变操作负荷,调节产品规格、调整中和反应条件容易;②没有中和槽和料浆泵送系统,使流程简化,减少了操作和维修费用;③造粒机固体床层内无需氨分布器(无二次氨化),支承氨分布器的钢结构可以取消,消除了氨分布器容易堵塞而停车以及支承管梁的积料现象;④由于没有料浆泵送的要求,反应料浆的含水量可以降至5%~10%操作,可使造粒及全系统的返料比减至(2.5~3:1),使相同设备的操作弹性增大;⑤由于返料量少,相同规格设备的生产能力增大,单位产品的能耗量低,使干燥能耗少,操作费用减少;⑥可以不用消泡剂,降低操作费用;⑦管式反应器设置蒸汽自动吹扫系统,有效地防止堵塞,保证长周期运转;⑧利用循环洗涤液的热量蒸发液氨,既可以节省蒸汽消耗,又可以降低洗涤液的温度,提高洗涤率。
工艺缺点:①对磷酸质量的要求比槽式反应器工艺严格;②生产DAP时造粒机内的反应热量大,需要通过加大空气量移走热量,逸出氨量大(约占总氨量的15%~20%),NH3尾气洗涤器负荷大;③对操作工的要求较高。
2.3双管式反应器工艺双管式反应器工艺是2个管式反应器分别安装在造粒机和干燥机中,氨和磷酸的反应在管式反应器中进行。
该工艺生产MAP较多,生产DAP的目前全世界约有15套装置,其中我国仅有中阿公司1套年48万吨DAP装置在生产。
工艺优点:①采用2个管式反应器,技术先进,造粒机内的反应热容易移走,即热平衡容易解决;②没有中和槽和料浆泵送系统,使流程简化,减少了操作和维修费用;③由于没有料浆泵送的要求,反应料浆的含水量低,可使造粒及全系统的返料比减至3:1,生产系统的操作弹性增大;④由于返料量低,相同规格设备的生产能力增大,干燥用燃料消耗少,单位的能耗低,操作费用减少;⑤可以不用消泡剂,降低操作费用;⑥采用液氨直接加料,节省蒸汽消耗;⑦管式反应器设有自动除垢系统,可以保证装置长周期运转。
工艺缺点:①对磷酸质量的要求比槽式反应器工艺严格;②生产DAP时氨需要从3点加入(2个管式反应器及造粒机内固体床层),因此氨的分配复杂,操作调节难度较大;③干燥机内的管式反应器必须使用w(P2O5)50%的浓磷酸;④由于干燥机内管式反应器生产的是磷酸一铵,不可避免要进入成品中,因此,产品的最终氨化度比其它工艺低(即产品的氨含量低);⑤造粒机固体床层内需要氨分布器及其支承管梁,氨分布器容易堵塞,支承管梁易产生积料现象。
2.4预中和+管式反应器工艺预中和+管式反应器工艺是结合预中和转鼓氨化粒化工艺和管式反应器工艺的优点发展起来的混合工艺。
该工艺相对预中和转鼓氨化粒化工艺,允许反应料浆有更高的含水量,操作弹性更大,对物料适应性更强,料浆输送泵及输送管线不易堵塞;由于造粒机中进行部分氨和磷酸的反应,带入造粒机的水量少,返料系统设备尺寸小,装置投资低;同时干燥系统负荷降低,能耗较低。
同时使用预中和反应槽和管式反应器生产磷铵料浆,在氨化粒化机(造粒机)中进一步氨化,在管式反应器中直接使用浓磷酸,并利用反应热蒸发水分,使进入造粒机中的水分减少,从而降低返料比和节约能耗。
3 年产60万吨DAP国产化设计概况3.1 简述年产60万吨DAP装置由3部分组成:①氨、磷酸以及硫酸贮运部分;② DAP等制造部分(含原料准备、反应、造粒、洗涤);③成品包装贮运部分。
以上3部分的设计包括工艺、设备、土建(含总图)、电气、自控、水道、暖通等。
3.2 装置主要技术的基本情况该装置由1条生产线组成,采用管式反应器及预中和器混合工艺技术,能够适应生产60万吨/年DAP(或GMAP)和NPK系列粒状产品。
磷酸、氨、硫酸、尿素、钾盐、填料和包裹油等为其必要的原料。
该技术是满足氨和磷酸的中和反应而精心设计的,建立在管式反应器(PR)及反应稳定的预中和器(PN)基础上。
本装置技术优点:(1)生产能力最大化管式反应器直接安装在造粒机内。