塑料模具顶出系统设计
翘曲分析
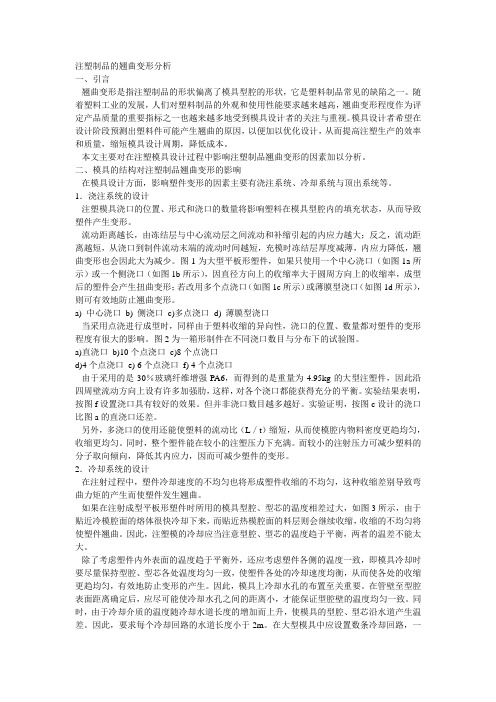
注塑制品的翘曲变形分析一、引言翘曲变形是指注塑制品的形状偏离了模具型腔的形状,它是塑料制品常见的缺陷之一。
随着塑料工业的发展,人们对塑料制品的外观和使用性能要求越来越高,翘曲变形程度作为评定产品质量的重要指标之一也越来越多地受到模具设计者的关注与重视。
模具设计者希望在设计阶段预测出塑料件可能产生翘曲的原因,以便加以优化设计,从而提高注塑生产的效率和质量,缩短模具设计周期,降低成本。
本文主要对在注塑模具设计过程中影响注塑制品翘曲变形的因素加以分析。
二、模具的结构对注塑制品翘曲变形的影响在模具设计方面,影响塑件变形的因素主要有浇注系统、冷却系统与顶出系统等。
1.浇注系统的设计注塑模具浇口的位置、形式和浇口的数量将影响塑料在模具型腔内的填充状态,从而导致塑件产生变形。
流动距离越长,由冻结层与中心流动层之间流动和补缩引起的内应力越大;反之,流动距离越短,从浇口到制件流动末端的流动时间越短,充模时冻结层厚度减薄,内应力降低,翘曲变形也会因此大为减少。
图1为大型平板形塑件,如果只使用一个中心浇口(如图1a所示)或一个侧浇口(如图1b所示),因直径方向上的收缩率大于圆周方向上的收缩率,成型后的塑件会产生扭曲变形;若改用多个点浇口(如图1c所示)或薄膜型浇口(如图1d所示),则可有效地防止翘曲变形。
a) 中心浇口b) 侧浇口c)多点浇口d) 薄膜型浇口当采用点浇进行成型时,同样由于塑料收缩的异向性,浇口的位置、数量都对塑件的变形程度有很大的影响。
图2为一箱形制件在不同浇口数目与分布下的试验图。
a)直浇口b)10个点浇口c)8个点浇口d)4个点浇口e) 6个点浇口f) 4个点浇口由于采用的是30%玻璃纤维增强PA6,而得到的是重量为4.95kg的大型注塑件,因此沿四周壁流动方向上设有许多加强肋,这样,对各个浇口都能获得充分的平衡。
实验结果表明,按图f设置浇口具有较好的效果。
但并非浇口数目越多越好。
实验证明,按图c设计的浇口比图a的直浇口还差。
塑胶模具设计顶出系统
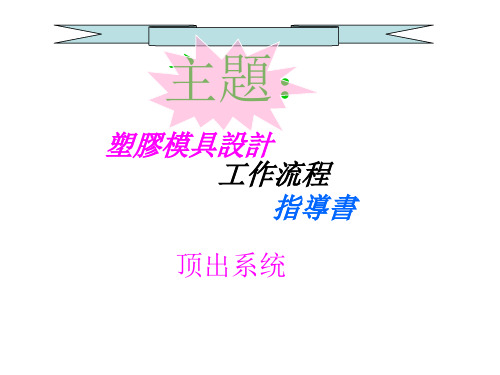
頂出系統
在设计顶出系统时应遵守下列原则: (1). 为使制品不致因顶出产生变形﹐破裂,穿孔等,推力点应作用在制品能 承受力最大的部位,即刚性好的部位,如筋部,突缘,壳体形制品的壁缘等处. (2). 为避免顶出痕迹影响制品外观,顶出装置应设在制品的隐蔽面或非装饰 表面.对于透明制品尤其要注意顶出位置及顶出形式的选择. (3)﹑頂出行程一般在制品脫離模具5~~10mm﹐對于簡單﹑大型的制品可 頂出行程是制品深度的2/3。 (4)﹑回位杆(RP) ﹕在頂杆頂出制品后﹐其頂端會高出模穴許多﹐避免在 下次合模前撞壞模仁﹐必須有保護機構﹐所以設置回位杆(RP)﹐也可設置 拉回機構和彈簧助其復位。 (5)﹑頂杆端面一般會高于模穴面0.05~~0.1mm,以免塑胶上留有顶杆突起 痕迹,但也要依产品情况而定。 (6)﹑有内模镶件的模具,顶杆离镶件边缘不得小于0.80MM.顶杆离运水的 边缘不得小于3MM. (7)﹑顶杆在模仁里的配合长度应小于2D(D<6MM.D为顶杆直径),对于大型 模具不大于1.5D. (8)﹑顶杆的大小根据成品的大小来确定,原则上宁多勿少,直径宁大勿小.
脫料板
頂出系統
6.斜銷 當成品中使用斜銷較多且其它地方不易排頂針時就 可直接用斜銷來頂出成品。用斜销顶出时(特别是较 大的斜销)应考虑产品是否会沾斜顶.并采取相应的措 施预防.
斜銷
頂出系統
7.氣頂 。 氣頂出方式不論是在公模部份或母模部分,其頂出都很方便,不 需要安裝推板.在頂出過程中整個制品的部均受同樣地的壓力,所 以即便是軟的塑料,也可以在不發生變形的條件下脫離模具,通常 氣頂出要求脫模斜度最小大於2∘,所以對於形狀復雜需要較大脫 模力的制品,則無法滿足其要求。
注塑模具设计流程
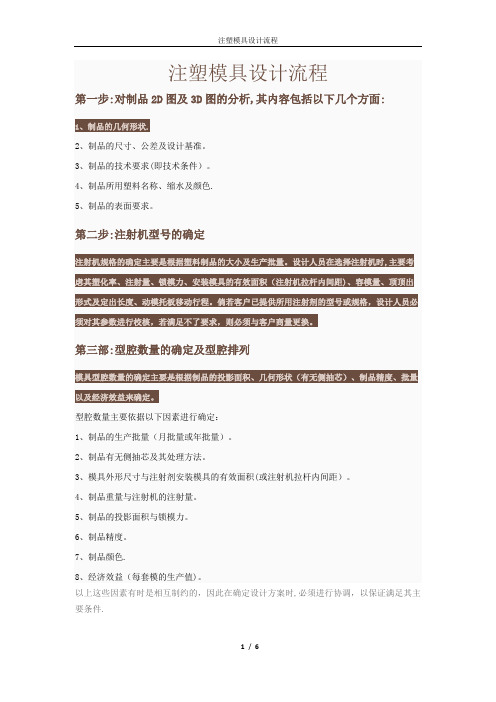
注塑模具设计流程第一步:对制品2D图及3D图的分析,其内容包括以下几个方面:1、制品的几何形状.2、制品的尺寸、公差及设计基准。
3、制品的技术要求(即技术条件)。
4、制品所用塑料名称、缩水及颜色.5、制品的表面要求。
第二步:注射机型号的确定注射机规格的确定主要是根据塑料制品的大小及生产批量。
设计人员在选择注射机时,主要考虑其塑化率、注射量、锁模力、安装模具的有效面积(注射机拉杆内间距)、容模量、顶顶出形式及定出长度、动模托板移动行程。
倘若客户已提供所用注射剂的型号或规格,设计人员必须对其参数进行校核,若满足不了要求,则必须与客户商量更换。
第三部:型腔数量的确定及型腔排列模具型腔数量的确定主要是根据制品的投影面积、几何形状(有无侧抽芯)、制品精度、批量以及经济效益来确定。
型腔数量主要依据以下因素进行确定:1、制品的生产批量(月批量或年批量)。
2、制品有无侧抽芯及其处理方法。
3、模具外形尺寸与注射剂安装模具的有效面积(或注射机拉杆内间距)。
4、制品重量与注射机的注射量。
5、制品的投影面积与锁模力。
6、制品精度。
7、制品颜色.8、经济效益(每套模的生产值)。
以上这些因素有时是相互制约的,因此在确定设计方案时,必须进行协调,以保证满足其主要条件.型腔数量确定之后,便进行型腔的排列,以及型腔位置的布局。
型腔的排列涉及模具尺寸、浇注系统的设计、浇注系统的平衡、抽芯(滑块)机构的设计、镶件型芯的设计以及热流道系统的设计。
以上这些问题由于分型面及浇口位置的选择有关,所以在具体设计过程中,要进行必要的调整,以达到最完美的设计。
第四步:分型面的确定分型面,在一些国外的制品图中已作具体规定,但在很多的模具设计中要由模具人员来确定,一般来讲,在平面上的分型面比较容易处理,有时碰到立体形式的分型面就应当特别注意.其分型面的选择应遵照以下原则:1、不影响制品的外观,尤其是对外观有明确要求的制品,更应注意分型面对外观的影响.2、利于保证制品的精度。
(完整版)塑胶模具顶出系统

1、顶针分类:1)圆顶针 ①单节式,直径在2以上;②双节式,直径在2以下;
2)扁顶针
形等等。
3)异形顶针:截面不为圆形也不为方形,为其它形状,如三角形,半圆
1)圆顶针:单节式,双节式。直径有很多,可以从0.5到很大。标准生产厂家可 以用0.1作为增量,也就是说直径可以从0.6、 0.7 、0.8 、0.9、 1 、1.1、1.2 、1.3 、1.4 等等。一般情况下,当直径小于2毫米时请尽可能采用双节式的圆顶针,有利于强度的提 高。
仁产生很大脫 模力.为使成品易于脫模使用顶出块配合 顶针的顶出结构,L段为逃料以减小顶出回位时与模仁 的磨损.
此側壁太深
• 7.5 顶出装置的种类四
• (2) 对于此类框架状成品,不易排顶针, 当顶出力不平衡时成品会变形,故采用整 整式顶出块.
7.7.1 顶板顶出 顶板顶出适用于筒形塑件,薄壁容器以及
7.8.2 气顶
密封圈
90° ~120
空 氣
7.9 急回机构一 在某些模具中,由于成品结构決定顶出装置与滑块等
抽芯机构发生干涉,导致无法順利合模,改善此种狀况必须 安装急回机构使顶出杆在合模时先回复原位 . 如图所示未装急回机构,滑块与顶管相撞导致無法合模
7.9 急回机构一 如图所示已装急回机构,顶管提前回位可順利合模
頂出或在较浅侧壁侧面進行咬花處理. 4. 顶针配置时在允许范围內直径应尽量加大且为標準 规格品. 5. 每一套模具顶针直径尺寸不宜太多种,以减少加工 时工时换刀时间及出错机率.
7.4 顶出位置之选择二
此處側壁較淺 均分在PL以上 易脫模
PL
此處側壁很深 均分在PL以下 不易脫模 PL
若脫模力不均衡 應考慮在此面作 咬花處理
模具斜顶结构设计和顶出行程计算
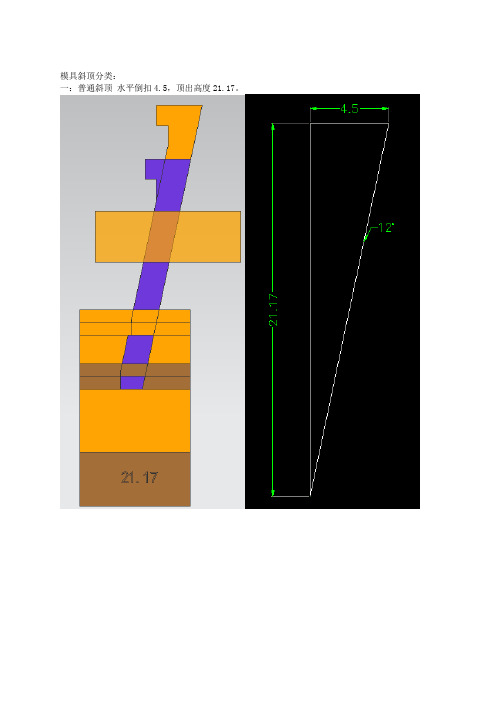
模具斜顶分类:
一:普通斜顶水平倒扣4.5,顶出高度21.17。
模具斜顶分类:
二. (1)斜斜顶(下落斜顶/下坡斜顶/延迟斜顶)水平倒扣4.5,顶出高度21.96
模具斜顶分类:
二. (2)斜斜顶(上坡斜顶/加速斜顶),水平倒,顶出行程20.37
模具斜顶分类:
三.(1)大角度斜顶—平行杆斜顶,计算方法和普通斜顶一样。
详解:产品倒扣较大,斜顶角度超过12°,斜顶多次斜向受力容易损坏,增加平行辅助杆。
可延伸为平行杆斜斜顶结构。
增加了平行杆的斜顶,斜顶座沿着平行杆运动,即:斜顶座也沿着倒扣轨迹运动,斜顶顶出距离和普通斜顶计算方法一样。
三.(2) 大角度交叉杆斜顶。
其他参数不变,分
解的角度5.51°
其他参数不变,分
解的角度5.61°
产品斜向倒扣角度比较大,控制斜斜顶运动轨迹的斜顶座角度太大,容易卡机构。
为了分解斜顶
座角度设置的辅助结构。
资料整理工程:赵小强 2019.11.20 上海立卡塑料托盘制造有限公司。
模具N种顶出结构解说

在注射动作结束后,塑件在模内冷却定型,由于体积收缩,对型芯产生包紧力,当其从模具中推出时,就必须克服因包紧力而产生的摩擦力。
对于不带通孔的筒、壳类塑料制件,脱模推出时还需克服大气压力。
在注射模中,将冷却固化后的塑料制品及浇注系统(水口料)从模具中安全无损坏地推出的机构称为脱模机构,也叫顶出机构或推出机构。
安全无损坏是指脱模时塑件不变形,不损坏,不粘模,无顶白,顶针位置位不影响塑件美观。
1. 注射模的脱模机构包括:1、顶针,司筒,推板,推块等推出零件;2、复位杆,复位弹簧及顶针板先复位机构等推出零件的复位零件;3、顶针固定板和顶针底板等推出零件的固定零件;4、高压气体顶出的气阀等配件;5、内螺纹脱模机构中的齿轮,齿条,马达,油缸等配件。
脱模机构的动作方向与模具的开模方向是一致的。
2. 脱模机构分类塑件顶出方法受塑件材料及形状等影响,由于塑件复杂多变,要求不一,导致胶件的脱模机构也多种多样。
按动力来源分,脱模机构可分为三类:(1)手动推出机构指当模具分开后,用人工操纵脱模机构使塑件脱出,它可分为模内手工推出和模外手工推出两种。
这类结构多用于形状复杂不能设置推出机构的模具或塑件结构简单、产量小的情况,目前很少采用。
(2)机动推出机构依靠注射机的开模动作驱动模具上的推出机构,实现塑件自动脱模。
这类模具结构复杂,多用于生产批量大的情况,是目前应用最广泛的一种推出机构,也是本章的重点。
它包括顶针类脱模,司筒脱模,推板类脱模,气动脱模,内螺纹脱模及复合脱模。
(3)液压和气动推出机构一般是指在注射机或模具上设有专用液压或气动装置,将塑件通过模具上的推出机构推出模外或将塑件吹出模外。
按照模具的结构特征分,脱模机构可分为:一次脱模机构、定模脱模机构、二次或多次脱模机构、浇注系统水口料的脱模机构、带螺纹塑件的脱模机构等。
3. 对脱模机构的要求模具打开时,塑件必须留在有顶出机构的半模上。
由于注射机的推杆在安装后模的一侧,所以注射模的顶出机构一般在后模。
注塑模具设计:第三章:顶出系统
注塑模具设计:第三章:顶出系统第三章顶出系统即产品的脱模装置。
产品在模具中成型后,应以特定的方式从模具的一侧推出。
在这一过程中,产品不会变形,不能满足成型要求,“发白”和粘滞现象。
这个特殊的装置是弹射系统。
此外,当模具关闭时,该装置必须能够在不干扰模具其他部件的情况下返回到弹射前的原始位置,以便进行重复成形加工。
在设计顶出系统时,模具设计者首先需要确定制品的留模形式,顶出系统必须建立在所滞留的模具部分中,通常,由于注塑机的顶出系统是设计在动模板一侧,因此绝大多数模具的顶出系统时安装在动模中的为了提高效率,缩短周期,实现自动化,不仅需要顺利脱模,还需要对浇口中点的塑料有一种特定的脱模方法。
顶出系统的要求就是在规定的时间内将制品不变形且准确的进行脱模。
考虑因素(一)顶出行程:一般规定顶出产品与模具分离5~10mm,有些简单,脱模坡度大筒形制品,可使行程为制品深度的2/3。
不要太长,因为顶杆很细,行程长,容易损坏顶杆。
(二)必须在顶出系统中设置复位杆(返回杆),以帮助顶出器返回。
顶出过程中,顶杆垫板承受很大的顶出压力,强度和刚度不足时,易弯曲变形影响顶杆运动,注意螺丝联接(需从垫板向固定板拧入)避免发生扳手空间不足的困难。
(三)顶杆顶部与型芯(或型腔)平面的关系理论上应处于同一平面,为模具制造与装配简便,实际中大多顶杆的端面超过或降低型芯(或型腔)平面0.05~0.1mm,与设计者协商,取得制品内表面有凸台与凹坑的允许(四)顶杆的形状和尺寸选择除非制品形状限定必须使用其它形状的顶杆外,一般选用圆柱形,且避免采用直径小于3mm的细长顶杆。
增加顶出面积的方法(五)支持由于顶杆固定板和垫板尺寸较大,使动模垫板之间的跨度加大,在较高的注射压力下,动模垫板可能玩去变形,导致顶杆运动不畅或卡死,除了用增加动模垫板的厚度来增强其刚度外,还可在动模固定板与垫板之间设置支撑柱。
(六)定位和引导在制品产量大,或顶出行程长,同时使用较细的顶杆,以及使用顶管顶出并在动模固定板装有细长芯子时,为保护顶杆(或长芯子)使其运动平稳,顶出系统需要设置导向装置,并且在动模板与垫条以及动模固定板之间装有定位销钉,以保证位置精度(七)弹射位置制品凡是有塑料包围钢件的地方,脱模都会困难,这是因为塑料熔体冷却后的收缩应力而产生对钢件的“抱紧”现象所导致的,故这些地方(筋、柱)都应重点考虑喷射器的分类一、圆顶杆,易加工,最普通,最简单的标准件,顶杆需淬火处理,获得足够的轻度和耐磨性。
注塑模具设计第10讲 实例1-2D-09 顶出系统的设计
推管插入第1点
图1-1-62 侧剖视图中的推管
2. 推杆排布及规格选用 (1)推杆排布要点: ①为防止产品变形,受力点应尽量靠近型芯或难以脱模的部位,如细 小的加强筋、柱位、台阶、金属嵌件、局部厚壁等结构复杂部位。相 邻两推杆的排布边距一般为20mm左右,视产品的结构情况而定。 ②受力点应作用在制品能承受最大力的部位,即刚性好的部位。 4
IN2 OUT2
推杆与型芯的配合 段为20mm左右
流道推杆
拉料杆
图1-1-67 推杆在正剖视图中的表达
3. 冷料井及拉料杆的设计 在主流道的末端通常要设计冷料井及拉料杆。 拉料杆结构形式有Z字形拉料杆、锥形拉料杆和圆头形拉料杆等几 种,如图1-1-68所示。图1-1-68 (a)所示为点浇口拉料杆,图1-168 (b)、(c)、(d)所示为侧浇口拉料杆,其中图1-1-68 (b)为常 见的Z字形拉料杆。本例采用较常见的Z字形拉料杆。
注塑模具设计实例教程
型芯
动模板
顶出空间
推杆 固定板
推板
动模座板
推管 C角
推管
推管型芯
无头螺钉
图1-1-60 推管结构
确定推管型芯和推管的大小:本例柱位的内孔直径为Φ2.41mm,外径为 Φ5.02mm,故选用推管型芯直径为Φ2.4mm,推管外径为Φ5.0mm的标准 推管,柱位的C角一般在推管上磨出,以保证推管壁厚的强度。 推管型芯的固定:推管型芯固定于模具的动模座板上。 根据推管型芯直径的大小不同,有不同的固定方式。推管型芯较 小时,采用无头螺钉固定;当推管型芯直径d>8mm或多个推管型 芯相距较近时,采用压板方式固定。 本例的推管型芯较小,故采用无头螺钉固定。
2
塑料模具6大系统
试模和量产的成败以及成本的高低,80%決定于设计阶段。
我们的目标应当是让设计部门担负起试模和量产成败的责任,设计工程师要清楚的知道自己设计的产品和模具是如何历经酸甜苦辣之途,才完成任务的,这样设计水平才能不断精进。
设计工程师也应在最短的时间內将最新的更正设计反映在设计图面和文档上,这样知识和经验才能累积、分享和传承。
加工、钳工和品管的责任是按图施工和品管,並且反馈设计合理化的意见。
这样经年累月下來,竞争力不断增强的模具/注塑厂將脱颖而出。
模具结构----六大系统之一:模具成型零件(排位与订料)概述:模具成型零件----由上下内模(包括行位/镶件)组成,它们形成一个封闭的型腔。
通俗来说,凡是有产品胶位的地方都称为模具成型零件。
排位与订料:1:产品在模仁(内模)的排位以最佳效果形成排放位置,要充分考虑进胶的平衡性,流道尽短地流入型腔,要充分考虑进胶位置和分型面因素,要与制品的外形大小,深度成比例。
2:产品到模仁边的距离与产品之间的距离:小件制品距离一般为15-25MM之间,成品之间一般为15-20MM,如有镶呵则一般为25MM 左右,成品间有主流道的最少要有15MM,大件制品距离边一般为30-50MM,有镶呵最小为35,镶呵出多件产品,刚其之间距离为10-15MM左右,成品长度在200MM以上,宽度在150MM 以上其产品距离应不小于30MM;3:模仁到模胚边距离:300MM以内,模胚为50-60MM之间;330-350MM以内,模胚为60-70MM之间;550MM 以上,模胚一般要在75MM以上。
4:模仁底部到模胚底部距离;公模300MM以内,模胚为40-50MM之间;330以上,模胚为50-70MM之间;母模300MM 以内,模胚为25-30MM之间;330MM以上模胚为25-35MM。
5:模仁用料,母模一般模具国产NAK80,较高要求,则用进口NAK80,有特殊或批量大模具选用热处理材料,有腐蚀性胶料如PVC,POM,NL或透明PMMA,PC等则选择不锈钢系列,如2316,S136,S136H等,公模仁一般选用德国P20,有腐蚀性胶料如PVC,POM,NL或透明PMMA,PC等亦要选择不锈钢系列,斜顶一般选用进口718,法兰一般选用王牌,散热要求高的镶件用铍铜。
塑胶模具设计指引
设计标准目录第一篇产品一、抄图二﹑产品分析与检测三﹑常用塑料分析(一)常用塑料缩水率(二)常用塑料成型性能(三)常用塑料壁厚值(四)常用塑料拔模角度第二篇模具一、排位二﹑模具系统设计(一)浇注系统1.1主流道1.2分流道1.3冷料井1.4浇口1.5转水口1.6典型产品流道浇口布置(二)成形系统2.1行位系统行位斜顶2.2镶件(三)顶出系统4.1顶出系统设计要点4.2顶出机构的基本方式 4.2.1顶针4.2.2司筒4.2.3扁顶针4.2.4直顶4.2.5推板4.3先复位机构(四) 冷却系统5.1.运水位置5.2.水路大小5.3.水路与模胚位置关系5.4.水井(五) 导向定位系统(六) 排气系统7.1产品排气7.2导套排气槽7.3尼龙螺丝排气孔(七)模胚结构件(支撑)及周边辅助件 7.1撑头7.2垃圾钉7.3锁模机构7.4温控箱、水管、紧固件三﹑细水口模设计四、模具零部件材料选择六、分模(一)模具档分模(二)组立档分模七、注射机选择第三篇图档一、出图要求1.排位图2.装配图3.顶针图4.线割图5.零件图6.分模图7.爆炸图二、图纸管理与进度控制(一)图纸管理(二)审图(三)进度三、电脑图档管理第四篇附录一、标准件二、工程表格产品篇抄图一.抄图前,先要看懂,看透产品线图,然后班顺思路,特别是外形面的画法。
抄好产品图要转为2D线图与设计部提供的平面线图套。
要保证主要的视图和边界线完全重合一致。
若有不重合、不一致的情况,首先分析是2D线图本身表达有问题,还是抄图时造成的。
若为2D线图表达问题则应及时标明,并与设计部沟通、反映;若为抄图问题,及时修改。
二.一个产品通常要多次转图与标题栏对上几次逐步确认(看版本),避免最后的问题堆积。
三.在抄图的整个过程中,最为重要的是基体外形面的控制和核对。
四.抄好的UG尽可能保证可以再生,以实现UG的参数设计功能。
五.通常抄图应先抄好影响模具结构之处,如外形面、行位处倒勾、前后模基面加减胶。
- 1、下载文档前请自行甄别文档内容的完整性,平台不提供额外的编辑、内容补充、找答案等附加服务。
- 2、"仅部分预览"的文档,不可在线预览部分如存在完整性等问题,可反馈申请退款(可完整预览的文档不适用该条件!)。
- 3、如文档侵犯您的权益,请联系客服反馈,我们会尽快为您处理(人工客服工作时间:9:00-18:30)。
塑料模具顶出系统设计
制品在模具中冷却固化之后,需切实可靠将其从模具中推顶出来,这一机构称之为顶出系统.同时必须保证,当模具闭合时,它不会与模具其它零部件发生干涉,并回到初始位置,以便开始下一循环。
1 顶出系统设计要点
1.1一般要求使顶出制品脱离模具5~10mm,如图所示,对于大型深腔桶类制品而言,也可使顶出行程为制品深度的2/3,如图。
当产品上有骨位、柱位等结构时,一定要使其完全脱出模具。
1.2 顶出位置
正确的顶出位置,应设在制品脱模困难的地方,制品的骨位﹑柱位以及对内模有包紧力的地方均应考虑设置顶出机构.同时还应考虑顶出机构应设置在不影响制品外观的部位,并且不能与其它零件 (如撑头﹑螺丝等)发生干涉。
1.3设计中尽量选用大的顶针,大模不用小顶针,特别是要尽可能地避免采用3/64"的有托顶针.当在产品有相互配合的地方设置顶针时,顶针应高出后模面0.5MM。
1.4设置顶出机构时,应注意顶出产品的均衡性.
2 顶出机构的基本方式
顶出机构的基本方式有:圆顶针﹑扁顶针﹑司筒﹑直顶﹑推板等 .
2.1圆顶针分为单托和双托两种,
1) 顶针与公模的配合长度一般为2~3倍顶针直径,但不能小于8,常用值为20mm,
如图5-1
当d≦3mm D=d+0.6
当d>3mm D=d+1
2)当产品弧面上设置顶针时﹐为防止顶针顶出时滑动﹐需在顶针端面开“十”形防滑槽﹐槽深0.5mm.。
3)顶针与周边零件的位置关系。
顶针边与骨位﹑镶件的最小距离为2.0mm,与产品边﹑水道最小距离为3.0mm。
.
4)当产品中柱位孔为前模碰穿方式,其下放置顶针时,处理方式如图:
5)顶针的管位.当顶针位于圆弧面或者当顶针和司筒受胶位方向限制时,往往要设置管位装置,管位方式有下列三种:
见图,其中图a为设置管位钉,较常用;图b为加一管位块;图c为将顶针头部加工为直边,此方式较常用于大顶针的场合。
6)镜类产品不允许产品上有顶出痕迹,常采用垃圾钉顶出,产品有扣时,顶针边距产品边2mm,无扣时为3mm,如图:
7)有时,将顶针顶端加工成”z”形头,达到制品留后模的目的,此时应保证,使”z”形头方向一致。
8)当在流道上设置顶针时,要避免犯如下图所示的错误,
图a为镜类产品,中间的顶针应取消。
图b为钮仔,并非要在每一浇道交叉处设置顶针,相隔太近则取消。
图c为CD23C开关柱套钮模,1出16,当产品间距较小时,其第二分流道或第三分流道的顶针可取消。
图d为潜水顶针设置,要保证8的尺寸。
2.2 司筒
1) 当产品带有空心支柱的结构,且其高度较高,要求采用司筒顶出.柱位与司筒的匹配关系见
针为有托顶针,其规格见图.3040以下模胚选用a类司筒针,3040以上模胚选用b类司筒针.如图:
下单时的书写格式为:
ø1/4”x司筒长x ø3.5x30x ø2.6xL
ø1/4”x司筒长x ø3.5x50x ø2.6xL
CD座行位上需设司筒的,司筒规格统一为:
ø6.35x司筒长x ø1/8”x司筒针长
考虑换针的方便。
2) 司筒针一般采用无头螺丝固定,但当多支司筒针相距很近时,采用压块与杯头螺丝固定。
3) 钮仔的固定用孔一般采用司筒顶出,并且一律采用ø3.57xø1.59的标准司筒,当不能用到标准司筒时,应保证孔的尺寸不变,适当加大外圆的尺寸,以选用标准司筒,其司筒针与前模的配合关系见图:
4) 司筒应避开顶棍孔,19安或以上模具,可取消中间顶棍孔。
2.3扁顶针
当制品上有较深的骨位时,采用扁顶针顶出是切实有效的方法.但其加工困难,因此,模具型芯常采用镶拼结构﹐例如手挽。
见图:
扁顶针的规格见附表4-2.3。
2.4 直顶
1) 直顶有两种结构形式:原身直顶和推块+顶针。
2) 直顶与产品完全贴合的一面做1°斜度,其余三面做3°斜度。
3) 当后模原身出时,直顶边与产品胶位内侧距离为0.3~0.5,当后模镶钶时,直顶边紧贴镶钶边.如图:
4) 原身直顶采用T座与杯头螺丝固定,其与后模的配合关系见如图:
5) 当采用推块十顶针的结构时,其位置关系见图,推块四面斜度,靠近胶位一侧1°,其余三面3°。
2.5 推板
对轮廓封闭,周长较长,并且其内外表面均不允许有顶出痕迹的制品,或者当产品过深,又没有足够的位置放置足够的顶针时,常采用推板推出结构。
其基本结构见图:
3 先复位机构
3.1为了保证当模具闭合时,顶出系统能回到初始位置,以便开始下一个循环,必须设置先复位装置,一般模具通常情况下采用弹簧复位。
1)弹簧长度计算:
弹簧总长=顶出高度x3.
弹簧空间=弹簧总长x80%(按预压20%算).
当弹簧空间长度达到150mm,弹簧内要加一支扶针,如图示:
2)复位弹簧统一选用公制黄弹簧,其常用规格有:ø 25﹑ø30﹑ø35﹑ø50﹑ø60。
3)弹簧孔大小,其尺寸标注如图﹕
D=d+2. (d为弹簧外径)
标注孔深H时﹐以顶点标注。
模胚宽度250以下,一般选用两根弹弓,宽度250的模胚,根据产品外形面积大小选择2根或4根弹弓。
宽度超过250选用4根或以上的弹弓。
确定弹弓位置需注意:弹弓孔与模胚边最最小距离为15.0mm,与回针的最小距离为10MM,同时,弹弓孔不得与吊环孔螺丝等干涉。
否则,需调整。
当行位下有直顶﹐顶针等顶出机构时﹐为防止在合模过程中发生碰撞﹐损坏模具,应设置先复位机构﹐先复位机构的基本结构见图﹕。