汽车轻量化技术及实现途径
汽车轻量化的主要途径

汽车轻量化是指通过减少车辆总重来提高燃油效率、降低排放并改善性能的一种方法。
以下是汽车轻量化的主要途径:
1. 材料选择:使用轻量化材料可以显著降低车辆重量。
常用的轻量化材料包括高强度钢、铝合金、镁合金、碳纤维复合材料等。
这些材料具有较高的强度和刚度,同时相对较轻。
2. 零部件优化:通过重新设计和优化汽车的零部件,可以减少材料使用量,降低重量。
采用先进的设计和制造技术,如拓扑优化、结构优化、减少零部件数量和合理布局等,可以实现轻量化。
3. 引入新技术:引入新的技术可以在不降低安全性能的前提下实现轻量化。
例如,采用先进的焊接、粘接和铆接技术可以减少结构重量;应用模块化设计和3D打印技术可以减少部件数量和重量。
4. 增加复合材料使用:复合材料具有高强度、高刚度和轻质化的特点,可用于替代传统的金属材料。
在汽车制造中广泛应用碳纤维复合材料、玻璃纤维增强塑料等,以降低车辆重量。
5. 车身结构优化:优化车身结构可以减少重量,提高刚度和安全性能。
采用合理的设计和材料使用,如采用单壳体结构、蜂窝结构、组合结构等,可以实现轻量化效果。
6. 动力总成改进:通过采用高效的动力总成技术,如混合动力系统、电动驱动系统等,可以减少发动机重量,从而实现整体轻量化效果。
综合使用上述途径,汽车制造商可以有效降低车辆重量,提高燃油经济性和环境友好性,同时保持车辆的性能和安全性能。
新能源汽车轻量化技术路线和应用策略

新能源汽车轻量化技术路线和应用策略随着全球对可持续发展和环保的不断推动,新能源汽车已经成为未来汽车发展的主流方向之一。
作为新一代汽车技术的代表,新能源汽车具有环保、节能、高效等特点,尤其在轻量化方面有着巨大的发展潜力。
本文将重点探讨新能源汽车轻量化技术路线和应用策略,以期为新能源汽车的未来发展提供一定的参考和借鉴。
1. 材料轻量化材料轻量化是新能源汽车轻量化的关键技术之一。
传统汽车主要采用钢铁作为车身和车架的主要材料,但钢铁的密度大、重量重,在一定程度上影响了汽车的整体重量和燃油效率。
新能源汽车在材料选择上更加注重轻量化,例如采用高强度铝合金、镁合金、碳纤维等新型轻质材料,从而有效降低整车的重量。
2. 结构设计优化新能源汽车轻量化还需要依托先进的结构设计技术,对汽车的各个部件和结构进行优化设计,使其在保证强度和安全性的前提下,尽可能减少材料的使用量,从而降低整车的重量。
结构设计优化涉及到材料力学、工艺工程、仿真技术等多方面的知识,需要整车制造企业与相关研发机构共同合作,共同推动技术的发展和应用。
3. 动力系统轻量化动力系统是新能源汽车的核心部件之一,也是汽车整体重量的重要组成部分。
对动力系统的轻量化设计和优化工作尤为重要。
采用高效率、轻量化的电池系统和电机系统,采用先进的热管理技术和冷却系统,优化整车的动力传动系统等,都可以有效降低动力系统的重量,提高汽车的续航里程和整体性能。
4. 节能环保轻量化材料的研发与应用在新能源汽车轻量化过程中,节能环保型轻量化材料的研发和应用至关重要。
这类材料主要包括可降解塑料、再生材料、生物基材料等,可以有效减少汽车制造过程中的资源消耗和环境污染,从而实现新能源汽车全生命周期的环保目标。
二、新能源汽车轻量化应用策略1. 政府引导政策政府在新能源汽车轻量化领域可以制定相关政策,包括对轻量化材料的研发与推广给予财政支持和税收优惠,鼓励企业加大对轻量化技术的投入和研发力度。
汽车轻量化技术的发展现状及其实施途

汽车轻量化技术的发展现状及其实施途汽车轻量化技术是汽车工业发展的重要方向之一、随着环保意识的提高和国家对汽车轻量化的要求,汽车制造商和技术研发机构一直在不断努力,开发和应用轻量化技术。
目前,汽车轻量化技术已经取得了一些重要的进展,并且在实施中展示了广泛的应用前景。
首先,材料轻量化技术是实现汽车轻量化的重要手段之一、汽车零部件材料的选择和设计对汽车整体重量具有重要影响。
目前,汽车轻量化的常用材料主要包括铝合金、镁合金、高强度钢、碳纤维等。
这些材料具有较高的强度和较低的密度,能够在保证安全性的前提下减轻汽车的自重。
同时,新型复合材料的研发也为汽车轻量化提供了更多的可能性。
其次,设计优化是实施汽车轻量化的另一个重要途径。
汽车的结构设计对整车的轻量化起着关键作用。
通过改进车身结构、优化零部件布局、减少连接件数量等方式,可以降低汽车整体重量。
同时,先进的计算机辅助设计和仿真技术的应用,也为汽车设计提供了更准确的数据和更全面的分析手段。
此外,先进制造技术的应用也为汽车轻量化提供了技术支持。
例如,自动化生产线和机器人技术的应用,可以提高生产效率,减少废品率,降低成本,从而推动汽车轻量化的实施。
同时,三维打印技术的发展也为汽车零部件制造提供了新的思路和方法。
当前,汽车轻量化技术已经在实践中取得了一些显著的成果。
许多车辆制造商已经开始采用轻量化材料,如铝合金和高强度钢,来制造车身和其他零部件。
例如,宝马采用了碳纤维复合材料来制造i3和i8等汽车,大大减轻了整车重量。
福特采用了高强度钢和铝合金来制造F-150等车型,减轻车身重量并提高燃油经济性。
此外,一些新兴车企也在积极研发和应用轻量化技术,以提升产品竞争力。
汽车轻量化技术的实施具有重要的经济和环境效益。
首先,汽车轻量化可以显著减少燃料消耗和尾气排放,提高汽车的燃油经济性和环保性能。
这可以降低车主的油费支出,减少对环境的污染。
其次,汽车轻量化可以提高汽车的操控性能和舒适性,增加驾乘者的驾驶乐趣和出行体验。
汽车轻量化技术及其实施途径

产 品 的各类 零 件 用材 中 ,钢铁 材 料 占有最 高 比例 。例 如 ,神 龙汽 车 有限 公 司 的富康 轿 车为5 %;德 系家 庭用 轿 车为5 %;美 系 中型轿 车 为5 %。为此 ,汽 4 8 1
车轻 量化 的 目标 与材 料 ,特别 是 构成 汽 车主体 的钢铁 材料 密切 相 关 。另 一 方
有 效 的措 施 之 一 ,汽 车 轻 量化 已 成 为 汽 车产 业 发 展 中 的一 项 关 键 性 研 究课
题
汽 车 轻 量 化 的技 术 内 涵
汽 车轻 量化 的技 术 内涵 ,即采用 现代 设 计方 法 和有效 的手 段对 汽 车产 品 进行 优 化设计 ,或使 用 新型 材料 在 确保 汽车 综合 性 能指 标 的前 提下 ,尽 可 能 降低 汽车 产品 自身重 量 ,以达 到 减重 、降耗 、环 保 、安全 的综 合 目标 。
到1 2 k ,预计 到2 1 年 ,美 国轿 0g 2 00
汽 车轻 量化 进行 了研究 ,但 与世 界 发 达 国家相 比,还有很 大 的差距 。 1 在铝 合金 使用 方面 .
Istt) 为 最 大 限 度 减 轻 汽 车 自 ntue i 重 ,组 织 了全 球 1 个 国家3 家著 名 8 5 汽 车企 业 和钢 铁 企业 参加 ,开展 了
汽 轻量 技术及 施 车 化 其实
口 范 叶 杨 沿平 孟先春 唐 杰
已于2 0 年7 正 式 实 施 ;第 二 阶段 标 准在 第 一 阶段 的基 础 上 进 一 步 严 格 , 05 月
将 于2 0 年 1 开 始 实 施 。 而我 国 的 现 实情 况 是 ,汽 车保 有 量 的快 速 增 长 , 08 月 关 ,对 外依 存 度超 过4 %。 而其 中汽车 燃 油消 耗不 仅 是 中 国石 油 消费 总 量 中 0
新能源汽车实现汽车轻量化的主要途径

新能源汽车实现汽车轻量化的主要途径
新能源汽车在当前的车辆发展领域中扮演着越来越重要的角色。
为了提高能源效率和减少对环境的影响,汽车制造商们致力于实现新能源汽车的轻量化。
轻量化是指使用更轻的材料来构建汽车结构和构件,以减少整车的重量。
下面是新能源汽车实现轻量化的主要途径:
首先,采用新型材料。
传统汽车主要使用钢铁材料来制造车身和其他结构,但钢材相对较重,不利于轻量化。
而新能源汽车则采用了更轻的材料,如铝合金、碳纤维、镁合金等。
这些材料具有重量轻、强度高的特点,可以在保证车身安全性的同时减少整车重量。
其次,优化设计。
新能源汽车在设计过程中注重优化结构,通过改变零部件的形状和厚度,以及减少结构中的空隙,来降低重量。
此外,新能源汽车还使用了更加紧凑的电力传动系统,减少了传动部件的数量和重量。
第三,采用先进制造技术。
轻量化汽车需要采用先进的制造技术来确保零部件的合理连接和质量控制。
例如,采用先进的焊接技术可以减少连接部位的重量和增强结构强度;使用数控加工设备可以减少零部件的误差和浪费。
第四,运用智能控制技术。
新能源汽车可以运用智能控制技术来提高能源利用率和降低能源消耗。
通过使用智能电池管理系统、智能驱动控制系统以及智能能量回收系统等,可以实现对能源的高效利用,减少能源浪费。
总之,新能源汽车实现轻量化的主要途径包括采用新型材料、优化设计、先进制造技术以及运用智能控制技术。
这些途径的综合应用可以显著降低整车重量,提高能源效率,推动新能源汽车的发展。
新能源汽车轻量化技术路线和应用策略

新能源汽车轻量化技术路线和应用策略新能源汽车轻量化技术是指通过采用轻量化材料、设计优化及创新制造工艺等手段,以降低整车质量,提高能源利用效率和续航里程,减少污染排放为目标的技术。
在新能源汽车发展的背景下,轻量化技术成为了促进汽车能效提升、行驶里程增加的重要手段之一。
新能源汽车轻量化技术的路线主要包括以下几个方面:(1)采用轻量化材料:传统汽车通常使用钢铁材料,而新能源汽车轻量化技术可以采用高强度铝合金、碳纤维复合材料等轻量化材料来替代部分结构件、车身及内饰件。
这些轻量化材料相比传统材料具有重量轻、强度高等优点,可以有效降低整车质量。
(2)设计优化:通过优化车身结构、车轮悬挂和传动系统等设计,减少零部件数量和尺寸,提高结构强度和刚度,降低车身重量。
采用空气动力学设计理念,减小空气阻力,提高车辆运行效率。
(3)创新制造工艺:采用先进的制造工艺,如锻造、激光焊接、数控加工等,提高零部件的制造精度和成型工艺,减少材料损耗和能源消耗。
(2)电池系统轻量化:电池是新能源汽车的重要组成部分,其重量占整车重量的比重较大。
通过减少电池的重量,可以有效提高新能源汽车的续航里程。
采用新型的高能量密度锂离子电池材料,可以减轻电池重量,并提高电池的能量转化效率。
(3)动力系统轻量化:新能源汽车的动力系统包括电机、减速器等部分,也是重要的轻量化对象。
通过采用高性能、高效率、重量轻的电机和减速器,可以减轻整个动力系统的重量,并提高能源利用效率。
(4)零部件轻量化:轻量化应用策略还可以在零部件层面进行,通过减少零部件的数量、尺寸和重量等方式,降低整车的质量。
采用模块化设计和集成化组装工艺,可以减少零部件之间的连接和嵌入,简化零部件结构和加工工艺。
汽车轻量化的技术与方法
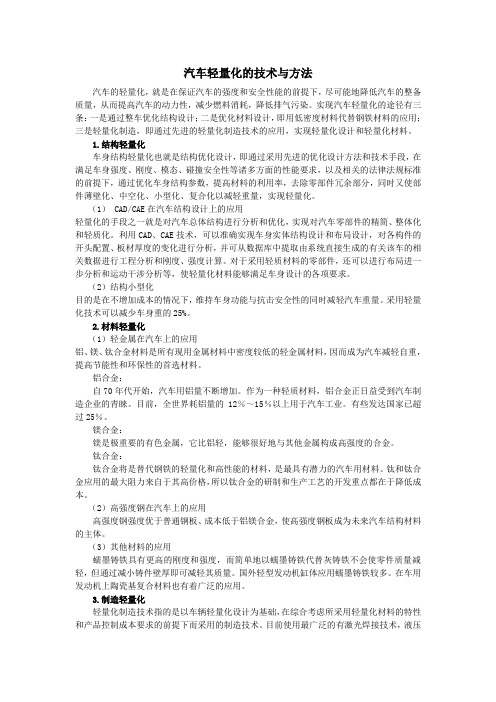
汽车轻量化的技术与方法汽车的轻量化,就是在保证汽车的强度和安全性能的前提下,尽可能地降低汽车的整备质量,从而提高汽车的动力性,减少燃料消耗,降低排气污染。
实现汽车轻量化的途径有三条:一是通过整车优化结构设计;二是优化材料设计,即用低密度材料代替钢铁材料的应用;三是轻量化制造,即通过先进的轻量化制造技术的应用,实现轻量化设计和轻量化材料。
1.结构轻量化车身结构轻量化也就是结构优化设计,即通过采用先进的优化设计方法和技术手段,在满足车身强度、刚度、模态、碰撞安全性等诸多方面的性能要求,以及相关的法律法规标准的前提下,通过优化车身结构参数,提高材料的利用率,去除零部件冗余部分,同时又使部件薄壁化、中空化、小型化、复合化以减轻重量,实现轻量化。
(1) CAD/CAE在汽车结构设计上的应用轻量化的手段之一就是对汽车总体结构进行分析和优化,实现对汽车零部件的精简、整体化和轻质化。
利用CAD、CAE技术,可以准确实现车身实体结构设计和布局设计,对各构件的开头配置、板材厚度的变化进行分析,并可从数据库中提取由系统直接生成的有关该车的相关数据进行工程分析和刚度、强度计算。
对于采用轻质材料的零部件,还可以进行布局进一步分析和运动干涉分析等,使轻量化材料能够满足车身设计的各项要求。
(2)结构小型化目的是在不增加成本的情况下,维持车身功能与抗击安全性的同时减轻汽车重量。
采用轻量化技术可以减少车身重的25%。
2.材料轻量化(1)轻金属在汽车上的应用铝、镁、钛合金材料是所有现用金属材料中密度较低的轻金属材料,因而成为汽车减轻自重,提高节能性和环保性的首选材料。
铝合金:自70年代开始,汽车用铝量不断增加。
作为一种轻质材料,铝合金正日益受到汽车制造企业的青睐。
目前,全世界耗铝量的12%~15%以上用于汽车工业。
有些发达国家已超过25%。
镁合金:镁是极重要的有色金属,它比铝轻,能够很好地与其他金属构成高强度的合金。
钛合金:钛合金将是替代钢铁的轻量化和高性能的材料,是最具有潜力的汽车用材料。
实现汽车轻量化的途径
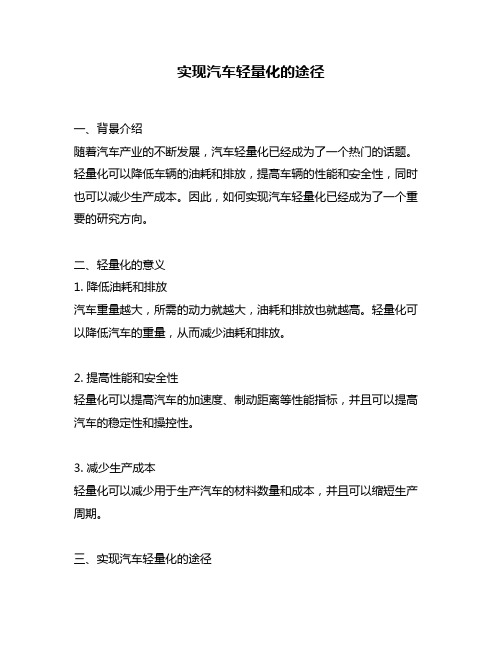
实现汽车轻量化的途径一、背景介绍随着汽车产业的不断发展,汽车轻量化已经成为了一个热门的话题。
轻量化可以降低车辆的油耗和排放,提高车辆的性能和安全性,同时也可以减少生产成本。
因此,如何实现汽车轻量化已经成为了一个重要的研究方向。
二、轻量化的意义1. 降低油耗和排放汽车重量越大,所需的动力就越大,油耗和排放也就越高。
轻量化可以降低汽车的重量,从而减少油耗和排放。
2. 提高性能和安全性轻量化可以提高汽车的加速度、制动距离等性能指标,并且可以提高汽车的稳定性和操控性。
3. 减少生产成本轻量化可以减少用于生产汽车的材料数量和成本,并且可以缩短生产周期。
三、实现汽车轻量化的途径1. 材料选择材料是影响汽车重量最主要的因素之一。
目前常用于制造汽车的材料包括钢铁、铝合金、碳纤维等。
其中,钢铁是最常用的材料,但其密度较大,因此需要使用更多的钢铁来制造车身,从而增加了车辆的重量。
铝合金和碳纤维密度较小,可以减少汽车的重量,但其价格相对较高。
因此,在选择材料时需要综合考虑材料的性能、成本等因素。
2. 结构优化汽车结构的优化也可以实现轻量化。
通过优化结构设计,可以减少用于制造汽车的材料数量,并且可以提高汽车的强度和稳定性。
例如,在汽车底盘设计中使用空心结构或者梁式结构可以减少底盘重量,并且提高底盘强度。
3. 零部件轻量化除了整车轻量化外,零部件轻量化也是实现汽车轻量化的重要途径。
例如,在发动机设计中使用轻质材料和先进技术可以减少发动机重量,并且提高发动机效率。
4. 制造工艺改进制造工艺也是影响汽车重量的一个因素。
通过改进制造工艺,可以减少生产过程中产生的废弃物和能源消耗,并且可以提高生产效率。
例如,在焊接汽车车身时使用激光焊接技术可以减少焊接时间和能源消耗。
5. 智能化技术智能化技术也可以实现汽车轻量化。
例如,在汽车制造中使用3D打印技术可以精确制造零部件,并且可以减少材料浪费。
此外,智能化技术还可以实现汽车的轻量化设计和优化。
- 1、下载文档前请自行甄别文档内容的完整性,平台不提供额外的编辑、内容补充、找答案等附加服务。
- 2、"仅部分预览"的文档,不可在线预览部分如存在完整性等问题,可反馈申请退款(可完整预览的文档不适用该条件!)。
- 3、如文档侵犯您的权益,请联系客服反馈,我们会尽快为您处理(人工客服工作时间:9:00-18:30)。
西南大学网络教育学院毕业论文论文题目:汽车轻量化技术及实现途径学生冉航学号 *************类型网络教育专业车辆工程层次专升本指导教师赵金斗日期 2016年10月17日西南大学网络教育学院毕业论文(设计)评定表目录摘要: (3)1.前言 (3)2.轻量化技术及其发展现状 (3)3.实现汽车轻量化的主要途径 (4)3.1合理的结构设计 (5)3.2使用新型材料 (6)3.2.1有色合金材料 (7)3.2.2高强度钢 (8)3.2.3塑料和复合材料 (8)3.2.4其他轻量化材料 (9)4.汽车轻量化发展面临的问题 (9)5.结论 (10)参考文献 (11)汽车轻量化设计技术摘要:本文简要介绍了目前汽车轻量化技术的发展状况,包括轻量化设计概况、各种轻量化材料的性能及运用,阐述了汽车轻量化的实施途径。
关键词:汽车轻量化发展1.前言有关研究数据表明, 若汽车整车质量降低10%, 燃油效率可提高6% ~ 8% ; 若滚动阻力减少10%, 燃油效率可提高3% ; 若车桥、变速器等机构的传动效率提高10% , 燃油效率可提高7%。
由此可见, 伴随轻量化而来的突出优点就是油耗显著降低。
汽车车身约占汽车总质量的30% , 空载情况下, 约70% 的油耗用在车身质量上, 因此车身的轻量化对减轻汽车自重, 提高整车燃料经济性至关重要。
同时, 轻量化还将在一定程度上带来车辆操控稳定性和一定意义上碰撞安全性的提升。
车辆行驶时颠簸会因底盘重量减轻而减轻,整个车身会更加稳定; 轻量化材料对冲撞能量的吸收, 又可以有效提高碰撞安全性。
因此汽车轻量化已成为汽车产业发展中的一项关键性研究课题。
2.轻量化技术及其发展现状汽车轻量化的技术内涵是:采用现代设计方法和有效手段对汽车产品进行优化设计,或使用新材料在确保汽车综合性能指标的前提下,尽可能降低汽车产品自身重量,以达到减重、降耗、环保、安全的综合指标。
然而,汽车轻量化绝非是简单地将其小型化。
首先应保持汽车原有的性能不受影响,既要有目标地减轻汽车自身的重量,又要保证汽车行驶的安全性、耐撞性、抗振性及舒适性,同时汽车本身的造价不被提高,以免给客户造成经济上的压力。
汽车轻量化技术包括汽车结构的合理设计和轻量化材料的使用两大方面。
一方面汽车轻量化与材料密切相关;另一方面,优化汽车结构设计也是实现汽车轻量化的有效途径。
与汽车自身质量下降相对应,汽车轻量化技术不断发展,主要表现在:(1)轻质材料的使用量不断攀升,铝合金、镁合金、钛合金、高强度钢、塑料、粉末冶金、生态复合材料及陶瓷等的应用越来越多;(2)结构优化和零部件的模块化设计水平不断提高,如采用前轮驱动、高刚性结构和超轻悬架结构等来达到轻量化的目的,计算机辅助集成技术和结构分析等技术也有所发展;(3)汽车轻量化促使汽车制造业在成形方法和联接技术上不断创新。
目前,国内汽车轻量化材料正在加速发展,新型智能材料逐渐在汽车制造中得到应用。
车用高性能钢板、镁合金已在汽车上有所应用。
如上海大众桑塔纳轿车变速器壳体采用镁合金。
随着镁合金材料的技术进步及其抗蠕变性能的进一步改善,自动变速器壳体以及发动机曲轴箱亦适合改用镁材料制造。
若曲轴箱由铝改为镁,则可减轻30%左右。
传统的轿车车身结构是钢车身,现今也越来越多地采用高强度钢、精练钢、铝合金和夹层钢车身结构,其制造工艺有柔性化板材辊轧、剪拼焊接工艺技术、薄壁制造技术等。
不锈钢与强度较高的碳钢相比,表现出不少优点,例如延展性更好、强度更高、更适合形状复杂的覆盖件成形。
上世纪80年代,重庆汽车研究所就开展了双相钢研究;一汽轿车、奇瑞汽车公司也在轿车车身上进行了高强度钢板的初步应用试验。
在结构设计方面可以采用前轮驱动、高刚性结构和超轻悬架结构等来达到轻量化目的,国内已从主要依靠经验设计逐渐发展到应用有限元等现代设计方法进行静强度计算和分析阶段。
目前出现了一批拥有自主知识产权的汽车车身模具开发技术,如湖南大学与上汽通用五菱在薄板冲压工艺与模具设计理论方面开展了较深入的研究;北京航空航天大学开发了CAD系统CAXA,并已经开展了客车轻量化技术的研究,利用有限元法和优化设计方法进行结构分析和结构优化设计,以减少车身骨架、发动机和车身蒙皮的重量等。
3.实现汽车轻量化的主要途径汽车轻量化在保证汽车整体质量和性能不受影响的前提下,应最大限度地减轻各零部件的质量,努力谋求高输出功率、低噪声、低振动和良好的操纵性、高可靠性等,降低燃油消耗,减少排放污染。
通过轻量化技术的内涵可知,汽车的轻量化主要通过合理的结构设计和使用轻质材料的方式来实现。
3.1合理的结构设计目前国内外汽车轻量化技术发展迅速,主要的轻量化措施是轻量化的结构设计和分析,设计已经融合到了汽车设计的前期。
轻质材料在汽车上的应用,包括铝、镁、高强度钢、复合材料、塑料等,与结构设计以及相应的装配、制造、防腐、连接等工艺的研究应用融为一体。
在现代汽车工业中,利用CAD/CAE/CAM一体化技术起着非常重要的作用,涵盖了汽车设计和制造的各个环节。
运用这些技术可以实现汽车的轻量化设计、制造。
轻量化的手段之一就是对汽车总体结构进行分析和优化,实现对汽车零部件的精简、整体化和轻质化。
利用CAD/CAE/CAM一体化技术,可以准确实现车身实体结构设计和布局设计,对各构件的开头配置、板材厚度的变化进行分析,并可从数据库中提取由系统直接生成的有关该车的相关数据进行工程分析和刚度、强度计算。
对于采用轻质材料的零部件,还可以进行布局分析和运动干涉分析等,使轻量化材料能够满足车身设计的各项要求。
此外利用CAD/CAE/CAM技术可以用仿真模拟代替实车进行试验,对轻量化设计的车身进行振动、疲劳和碰撞分析。
通过开发汽车车身、底盘、动力传动系统等大型零部件整体加工技术和相关的模块化设计和制造技术,使节能型汽车从制造到使用各个环节都真正实现节能、环保。
通过结合参数反演技术、多目标全局优化等现代车身设计方法,研究汽车轻量化结构优化设计技术,包括多种轻量化材料的匹配、零部件的优化分块等。
从结构上减少零部件数量,确保在汽车整车性能不变的前提下达到减轻自重的目的。
具体结构合理设计有以下3个方面:(1)通过结构优化设计,减小车身骨架及车身钢板的质量,对车身强度和刚度进行校核,确保汽车在满足性能的前提下减轻自重。
(2)通过结构的小型化,促进汽车轻量化,主要通过其主要功能部件在同等使用性能不变的情况下,缩小尺寸。
(3)采取运动结构方式的变化来达到目的。
比如采用轿车发动机前置、前轮驱动和超轻悬架结构等,使结构更紧凑,或采取发动机后置、后轮驱动的方式,达到使整车局部变小,实现轻量化的目标。
3.2使用新型材料据统计,汽车车身、底盘(含悬架系统)、发动机三大件约占一辆轿车总重量的65%以上。
其中车身内外覆盖件的重量又居首位。
因此减少汽车白车身重量对降低发动机的功耗和减少汽车总重量具有双重的效应。
为此,首先应该在白车身制造材料方面寻找突破口。
具体可以有如下几种方案:(1)使用密度小、强度高的轻质材料,像铝镁合金、塑料聚合物材料、陶瓷材料等;(2)使用同密度、同弹性模量而且工艺性能好的截面厚度较薄的高强度钢;(3)使用基于新材料加工技术的轻量化结构用材,如连续挤压变截面型材、金属基复合材料板、激光焊接板材等。
3.2.1有色合金材料铝具有良好的机械性能,其密度只有钢铁的1/3,机械加工性能比铁高4. 5倍,耐腐蚀性、导热性好。
其合金还具有高强度、易回收、吸能性好等特点。
汽车工业运用最多的是铸造铝合金和形变铝合金。
运用形变铝材制造车身面板的技术已经比较成熟,包括发动机罩、行李箱罩、车门、翼子板等。
保险杠、轮毂和汽车结构零件也广泛使用铝合金材料。
运用铝合金也面临不少问题,比如,铝合金加工难度比钢材高,成型性还需继续改善;由于铝导热性好,导致铝合金的焊接性能差;不能像钢板那样采用磁力搬运等。
其中,关键是成本问题,目前铝价还比较高,成本控制对铝合金的运用非常重要。
镁合金具有与铝合金相似的性能,但是镁的密度更低,它们的密度之比为 1. 8∶3,是当前最理想、重量最轻的金属结构材料,因而成为汽车减轻自重、以提高其节能性和环保性的首选材料。
但其铸造性差,后处理工艺复杂,成本高。
我国的镁资源非常丰富,储量占世界首位。
但是国内用量很少,尤其汽车行业用量极少,因此前景非常广阔。
而西方工业发达国家对铝基、镁基的金属基复合材料的开发与应用,已达到了产业化阶段,如表1。
3.2.2高强度钢用高强度钢替代原使用材料,能适当减小零件尺寸。
世界上广泛通过进一步提高合金钢、弹簧钢、不锈钢等钢种的比强度和比刚度,以及粉末冶金配件具有的多孔密度低、精度高、成本低等特点,来作为汽车轻量化的措施。
采用高强度钢板在等强度设计条件下可以减少板厚,但是车身零件选定钢板厚度大都以元件刚度为基准,因此实际板厚减少率不一定能达到钢板强度的增加率,不可能大幅度地减轻车重。
高强度钢板在汽车上应用的目的主要有3点:增加构件的变形抗力,提高能量吸收能力和扩大弹性应变区。
由于运用高强度钢板的经济性和相对容易性,因此应大力提倡在汽车上运用高强度钢板。
现在各国都在加速高强度钢和超高强度钢在汽车车身、底盘、悬架、转向等零部件上的运用。
3.2.3塑料和复合材料与相同结构性能的钢材相比,塑料和复合材料一般可减轻部件的重量在35%左右。
低密度与超低密度片状成型复合材料的发展提供了更多的潜力,在重量减轻与强度方面达到甚至超过了铝材,整体成本通常更低。
塑料是由非金属为主的有机物组成的,具有密度小、成型性好、耐腐蚀、防振、隔音隔热等性能,同时又具有金属钢板不具备的外观色泽和触感。
目前,塑料大都使用在汽车的内外饰件上,如仪表板、车门内板、顶棚、副仪表板、杂物箱盖、座椅及各类护板、侧围内衬板、车门防撞条、扶手、车窗、散热器罩、座椅支架等。
而后逐渐向结构件和功能件扩展。
例如发电机及其相关系统、冷却系统等。
塑料也在向制作车身覆盖件方向发展。
复合材料即纤维增强塑料,是一种增强纤维和塑料复合而成的材料。
常用的是玻璃纤维和热固性树脂的复合材料。
增强用的纤维除玻璃外,还有高级的碳纤维、合成纤维。
复合材料作为汽车材料具有很多优点:密度小、设计灵活美观、易设计成整体结构、耐腐蚀、隔热隔电、耐冲击、抗振等。
目前玻璃钢复合材料的应用非常广泛,尤其在欧美车系中。
其中尤以SMC和GMT的应用最为广泛。
曼、雷诺、沃尔沃、奔驰、依维柯、达夫等欧洲重型卡车制造商的驾驶室材料中,都大量选用了SMC。
在国内, SMC材料在汽车领域也得到了广泛的应用,尤其是商用汽车领域。
中国重汽、陕西重汽、福田欧曼、重庆红岩等主要重型卡车制造商,其驾驶室的制造都不同程度地采用了SMC材料。
3.2.4其他轻量化材料精细陶瓷是继金属、塑料之后发展起来的第3大类材料。