挤出机机头设计
新型高效过滤挤出机头结构设计与控制优化
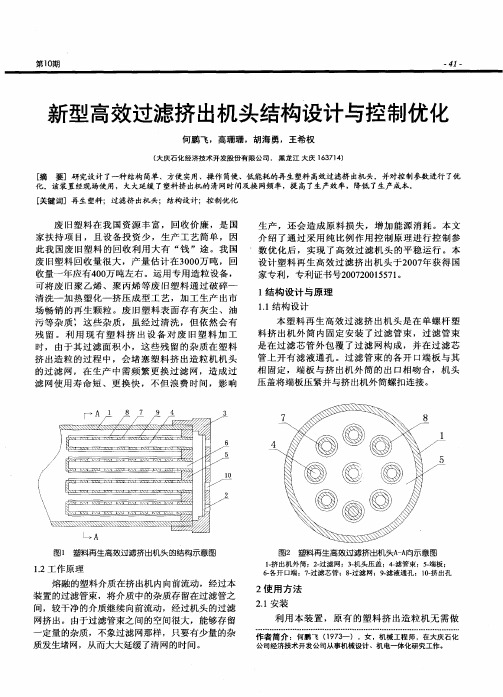
挤 出机 头 的 长 周 期平 稳 运 行 对 自动 化 技 术提 出 了很 高要 求 ,挤 出机 主 体驱 动 装 置 启 动 速度 必 须 与牵 引或 切 割 等 辅助 装 置 的驱 动 保 持 同 步 ,称 重 定量 进 料 系 统 应 当确 保 原 材 料 的持 续供 给 ,通 过 采 用 纯 比例 作 用控 制 进 行 参 数 优 化后 , 实现 了 高效 过滤 机 头 的平 稳运 行 。
生 产 , 还 会造 成 原 料 损 失 ,增加 能源 消耗 。本 文 介 绍 了通 过采 用 纯 比例 作 用控 制 原理 进 行 控 制 参 数 优 化 后 , 实现 了高 效 过 滤 机 头 的平 稳 运 行 。本 设计 塑 料 再 生 高 效 过 滤挤 出机 头 于2 0 年 获 得 国 07 家专 利 ,专利证 书 号2 0 2 0 5 7 。 0 7 0 1 5 1
4结 论
( ) 塑 料 再 生 高 效 过 滤 挤 出 机 头 设 计 科 1 学 、结构 简 单 、控 制参 数 合理 。 ( 2)增 大 了过 滤 管 束 比表 面积 ,过 滤 效 果 显 著 。使用 本 装 置 ,可 以大 大 延缓 清 网时 间及 换 网频 率 ,提 高生 产 效 率 ,降 低 生产 成 本 ,具 有使 用 方便 、节 能 降耗 、成 本低 的优 点 。 ( )本 设 计 已于 2 0 年 获 得 国家 专 利 ,专 3 07
图 1 塑料再生高效过滤挤出机头的结构示意图
图2 塑料再生高效过滤 挤出机头A A — 向示意图
1挤出机外简 ;2过滤网;3机头压盖 ;4滤管束;5端板 ; 。 一 - 一 一 6各 开 1端 ;7过 滤 芯 管 ; 8过 滤 网 ;9滤 液 通 孔 ; 1一 出孔 . 2 1 一 . . O挤
两台挤出机共挤复合三层塑料管材的机头设计
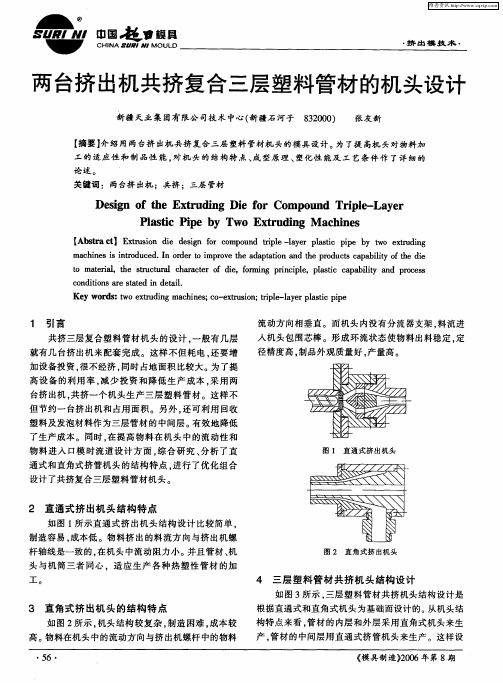
如 图 3所 示 , 渡套 4主要 为 了消 除 分流 器支 架 过 中分流 筋 产生 的熔 接 痕 。单 独增 设 了一 件过渡 套来 增 加 物 料 的密 实 , 高管 材 的强 度 。 同时 避免 1模 在 调 提 3 整 时 直 接与 分 流器 支 架 两 接触 面 的误 差 , 生 的死 角 产
成 形制 品 的关 键部 件 。
45 过 渡 套 .
4 1 人 字 流 道 连 接 器 .
如 图 3所示 。 字 流 道 连 接器 是 成 型塑 料 管材 的 人 内层和外 层 流道 。物料 从 挤 出机 B进入 机 头 。先 行分 成 两 股进 入 内层 流道 的同 时 , 内层 的 物 料 穿过 分 流 器 支 架 , 向 芯棒 中心 流 道 , 汇 人 1 被 分 流 挤 出定 转 而 3模
维普资讯
B R I由 趋 | 具 UI 由 超 一 N 国 模
~ D CH I NA BI #I N IMOUL I
’
・ 出 模 技 术 ・ 挤
两台挤 出机共挤复合三层塑料管材 的机头设计
新疆天业集 团有 限公司技术中心( 新疆石河子 82 0 ) 30 0 张友新 【 摘要】 介绍用两台挤 出机共挤复合三层塑料 管材机头的模具设计。 了 高机头对物料加 为 提
1 引言
共挤三层复合塑料管材机头 的设计 。 一般有几层 就有几台挤 出机来配套完成 。这样不但耗 电, 还要增 加设备投资 , 很不经济 , 同时 占地面积 比较大。 了提 为 高设 备的利用率 , 减少投资 和降低生产成 本 , 采用两
台挤 出机 , 挤 一个 机 头 生 产三 层 塑 料 管 材 。这 样 不 共 但 节 约一 台挤 出机 和 占用 面 积 。 另 外 , 可 利 用 回收 还
挤出机机头

上述三种机头的特征对比
管材机头尺寸设计
8、螺旋芯棒模头
优点: 1) 熔体能沿着口模的圆周均匀分布, 在制品上没有流动痕迹( 结合线) , 制品在圆 周方向上的厚度公差和各种性能均匀; 2) 压 力降和流动阻力较低, 在较高的产量下挤出物 的温度较低; 3) 机械应力和热应力较低,制品 有良好的机械强度; 4) 模头结构坚固, 适合高 粘度材料的吹塑成型, 同时, 机头的装拆操作
2.芯棒 1)芯棒的外径 芯棒的外径由管材的内径决定, 根据生产经验: d= D-2e 式中 d一芯棒的外径(mm); D一口模的内径(mm); e一口模与芯棒的单边间隙(mm), e =(0.83-0.94)t t一材料壁厚(mm)。
2)定型段、压缩段L2和收缩角 a、芯棒定型段的长度与L1相等或稍长。 b、L2可按下面经验公式计算: L2=(1.5-2.5)D0 式中 L2一芯棒的压缩段长度(mm); D0一塑料熔体在过滤板出口处的流道 直径(mm)。 c、芯模收缩角: 低粘度塑料 =45°-60° 高粘度塑料 =30°-50°
的环隙截面积之比,反映出塑料熔体的压实
程度。 低粘度塑料ε =4-10 高粘度塑料 ε =2.5-6.0
7管材挤出机的机头
分类
1)直通式机头
2)直角式机头
3)旁侧式机头
1)直通式机头 结构简单、制造容易、成本低、料流阻 力小等优点;但这种机头的缺点是在生产外 径 大的管材时芯模加热困难,分流器支架 造成的接缝处管材强度低。适用于加工RPVC、 SPVC、 PA、PC、PE和PP等塑料管材,一般 用于挤小口径的管材。
3、挤出机头设计原则
1.内腔呈流线型 :为了使塑料熔体能沿着机
头中的流道均匀平稳地流动而顺利挤出 (表面粗
挤出机机头与机口的确定与制作

式中, ——轴向力; ——周向力; ——轴 向速度; ——周向速度 ; 绞刀螺旋升角。
轴向
F1
的原料 , 表现 的流体特性明显, 对机头结构要求较
低; 塑性指数偏低的原料 , 其表 现的固体特性 比较 明显 , 料 之 间 的 亲 和力 较 低 , 原 在机 头 内挤 压 较难 实现形成稳定平衡泥流, 因而对机头的尺寸和 内部
逐渐过渡为矩形的筒体 。机头后端的圆形法兰和
泥缸 的前法 兰联 接, 前端 的方形法 兰用来 固定机
口( 木 龙 口 ) 或 。机头 的 内腔后 端 为 圆形 , 径 等于 直 泥 缸衬 套 的 内径 ( 衬套 时 为 泥缸 内径 )前 端 的形 无 ,
1 ——长方形法兰;——连接部分;——后段圆形法兰 2 3
料在螺旋运动中所受的挤压力 ,可分解为轴 向力
和周向力 , 运动速度 v同样可以分解为轴向速 度 和周向速度 , 具体如下。
对于机头与机 口连接处 , 一种情况是机头出口 内尺寸与机 V进 H内尺寸相一致 ( t 机头无死泥区 ) ,
科 技纵 横
8Jie fc l6 lc c l I00 1 6
设计 。 口设计和制作也缺乏严密的科学性。 机 因此 , 提高机头和机 口的设计与制造质量 , 对提高砖坯质 量及 企业 的生产 意义重 大 。
1 机 头几何 尺寸和 结构 的确 定 11 机 头 的特征 和作 用 .
机头的作用是促使泥料在螺旋绞刀的作用下 , 逐渐挤压使其成为结构致密、 向机 E方 向整体移动 l 的泥段 。图 l 为机 头 的结 构 , 头通 常 为 圆柱 形 并 机
作 方 法 以及 注 意 问题 。
关键词 : 出机 ; 头; 口; 挤 机 机 确定; 制作
挤出机头的分类及特点有哪些机头设计的主要

挤出机头的分类及特点有哪些机头设计的主要
挤出机头是塑料挤出机中的关键部件,负责将加热融化的塑料通过模具的形状挤出成型。
根据挤出机头的不同设计和结构,可以将其分为多种分类,并且每种分类都具有其独特的特点和优势。
首先,从结构形式上来看,挤出机头可以分为光圈式机头、螺杆式机头和板式机头三种主要类型。
光圈式机头由针管和鞍座组成,适用于挤出螺纹、型材、带材等产品;螺杆式机头主要由挤出螺杆和机筒组成,适用于挤出管材、板材等产品;板式机头由板状合模和螺杆组成,适用于挤出薄膜、片材等产品。
不同类型的机头适用于不同的产品挤出加工,有着各自独特的特点和优势。
其次,从挤出成型方式上来看,挤出机头又可以分为单层机头、多层机头、中空机头等。
单层机头适用于一次性成型的产品,结构简单、生产效率高;多层机头可以实现多层产品挤出成型,产品层次丰富,适用于复合产品的生产;中空机头适用于中空结构产品的挤出,如管材、异形材等,具有独特的设计和挤出方式。
最后,挤出机头的特点还包括挤出均匀性、调节精准、耐磨耐高温等。
好的挤出机头设计可以保证挤出产品的均匀性和一致性,提高生产效率和产品质量;精准的调节设计可以使挤出机头适应不同材料和产品的生产需求;耐磨耐高温的材质和表面处理则可以延长机头的使用寿命,减少维护成本。
综上所述,挤出机头作为塑料挤出机中的重要组成部分,其分类和特点根据不同的设计和结构而有所不同,每种类型都有其适用的领域和优势。
在实际生产中,选择合适的挤出机头设计将对产品的质量和生产效率产生重要影响,因此选择合适的挤出机头至关重要。
1。
挤出机机头设计原则和参数选择 韩兵
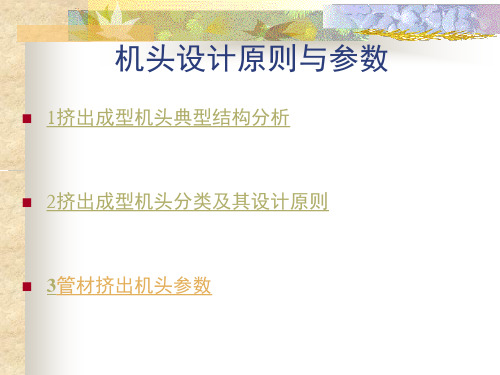
2.管材挤出机头零件的设计 (1) 口模
口模是成型管材外表面的零件,其 结构如图8-6所示。口模内径不等于塑料 管材外径,因为从口模挤出的管坯由于 压力突然降低,塑料因弹性恢复而发生 管径膨胀,同时,管坯在冷却和牵引作 用下,管径会发生缩小。这些膨胀和收 缩的大小与塑料性质、挤出温度和压力 等成型条件以及定径套结构有关,目前 尚无成熟的理论计算方法计算膨胀和收 缩值,一般是根据要求的管材截面尺寸, 按拉伸比确定口模截面尺寸。所谓拉伸 比是指口模成型段环隙横截面积与管材 横截面积之比。
L2=(1.5~2.5)D0
(8-4)
式中D0——栅板出口处直径。 芯模直径d1可按下式计算;
d1=d—2δ
(8-5)
式中δ—芯模与口模之间间隙;
d—口模内径。
由于如上所述塑料熔体挤出口模后的膨胀 与收缩,使δ不等于制品壁厚,δ可按下式计 算式:中k—经验系 数 ,kt k=1.(168~-61).20;
5.机头体 用来组装机头各零件及挤出机连接。 6.定径套 使制品通过定径套获得良好的表面粗糙度,正确 的尺寸和几何形状。 7.堵塞 防止压缩空气泄漏,保证管内一定的压力。
挤出成型机头分类及其设计原则
1.分类 由于挤出制品的形状和要求不同,因此要有相应
的机头满足制品的要求,机头种类很多,大致 可按以下三种特征来进行分类: (1)按机头用途分类 可分为挤管机头、吹管机头、挤板机头等;
2.设计原则
为了使挤出制品具有外观光洁性、尺寸准确性、形状与位置精确 准确性、单位长度的质量和物理力学性能等,一般遵循下面几个原 则:
(1)流道呈流线型 为使物料能沿着机头的流道充满并均匀地被挤 出,同时避免物料发生过热分解,机头内流道应 呈流线型,不能急剧地扩大或缩小,更不能有死 角和停滞区,流道应加工得十分光滑,表面粗糙 度应在Ra 0.4um以下。 (2)足够的压缩比 满足具体制品对机头压力的要求从而使制品密 实和消除因分流器支架造成的结合缝,根据制品 和塑料种类不同,应设计足够的压缩比。
挤出成型机头应设置适当的_装置
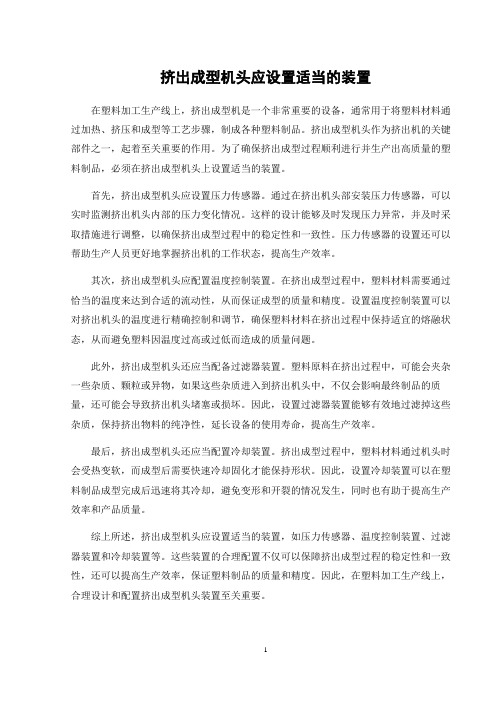
挤出成型机头应设置适当的装置在塑料加工生产线上,挤出成型机是一个非常重要的设备,通常用于将塑料材料通过加热、挤压和成型等工艺步骤,制成各种塑料制品。
挤出成型机头作为挤出机的关键部件之一,起着至关重要的作用。
为了确保挤出成型过程顺利进行并生产出高质量的塑料制品,必须在挤出成型机头上设置适当的装置。
首先,挤出成型机头应设置压力传感器。
通过在挤出机头部安装压力传感器,可以实时监测挤出机头内部的压力变化情况。
这样的设计能够及时发现压力异常,并及时采取措施进行调整,以确保挤出成型过程中的稳定性和一致性。
压力传感器的设置还可以帮助生产人员更好地掌握挤出机的工作状态,提高生产效率。
其次,挤出成型机头应配置温度控制装置。
在挤出成型过程中,塑料材料需要通过恰当的温度来达到合适的流动性,从而保证成型的质量和精度。
设置温度控制装置可以对挤出机头的温度进行精确控制和调节,确保塑料材料在挤出过程中保持适宜的熔融状态,从而避免塑料因温度过高或过低而造成的质量问题。
此外,挤出成型机头还应当配备过滤器装置。
塑料原料在挤出过程中,可能会夹杂一些杂质、颗粒或异物,如果这些杂质进入到挤出机头中,不仅会影响最终制品的质量,还可能会导致挤出机头堵塞或损坏。
因此,设置过滤器装置能够有效地过滤掉这些杂质,保持挤出物料的纯净性,延长设备的使用寿命,提高生产效率。
最后,挤出成型机头还应当配置冷却装置。
挤出成型过程中,塑料材料通过机头时会受热变软,而成型后需要快速冷却固化才能保持形状。
因此,设置冷却装置可以在塑料制品成型完成后迅速将其冷却,避免变形和开裂的情况发生,同时也有助于提高生产效率和产品质量。
综上所述,挤出成型机头应设置适当的装置,如压力传感器、温度控制装置、过滤器装置和冷却装置等。
这些装置的合理配置不仅可以保障挤出成型过程的稳定性和一致性,还可以提高生产效率,保证塑料制品的质量和精度。
因此,在塑料加工生产线上,合理设计和配置挤出成型机头装置至关重要。
挤出机机头设计
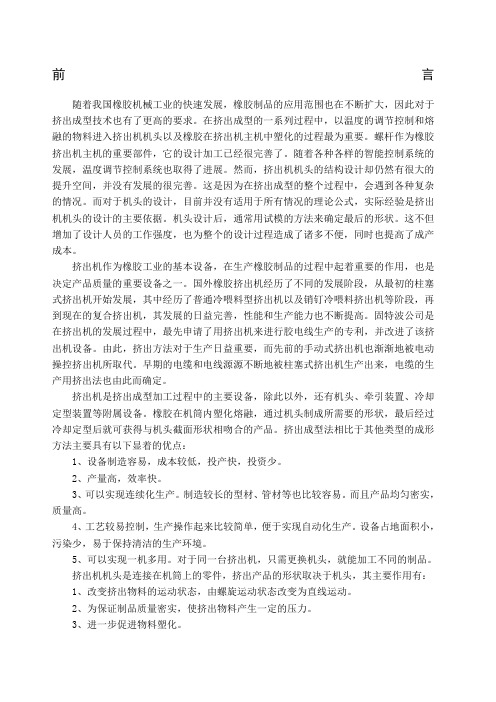
前言随着我国橡胶机械工业的快速发展,橡胶制品的应用范围也在不断扩大,因此对于挤出成型技术也有了更高的要求。
在挤出成型的一系列过程中,以温度的调节控制和熔融的物料进入挤出机机头以及橡胶在挤出机主机中塑化的过程最为重要。
螺杆作为橡胶挤出机主机的重要部件,它的设计加工已经很完善了。
随着各种各样的智能控制系统的发展,温度调节控制系统也取得了进展。
然而,挤出机机头的结构设计却仍然有很大的提升空间,并没有发展的很完善。
这是因为在挤出成型的整个过程中,会遇到各种复杂的情况。
而对于机头的设计,目前并没有适用于所有情况的理论公式,实际经验是挤出机机头的设计的主要依据。
机头设计后,通常用试模的方法来确定最后的形状。
这不但增加了设计人员的工作强度,也为整个的设计过程造成了诸多不便,同时也提高了成产成本。
挤出机作为橡胶工业的基本设备,在生产橡胶制品的过程中起着重要的作用,也是决定产品质量的重要设备之一。
国外橡胶挤出机经历了不同的发展阶段,从最初的柱塞式挤出机开始发展,其中经历了普通冷喂料型挤出机以及销钉冷喂料挤出机等阶段,再到现在的复合挤出机,其发展的日益完善,性能和生产能力也不断提高。
固特波公司是在挤出机的发展过程中,最先申请了用挤出机来进行胶电线生产的专利,并改进了该挤出机设备。
由此,挤出方法对于生产日益重要,而先前的手动式挤出机也渐渐地被电动操控挤出机所取代。
早期的电缆和电线源源不断地被柱塞式挤出机生产出来,电缆的生产用挤出法也由此而确定。
挤出机是挤出成型加工过程中的主要设备,除此以外,还有机头、牵引装置、冷却定型装置等附属设备。
橡胶在机筒内塑化熔融,通过机头制成所需要的形状,最后经过冷却定型后就可获得与机头截面形状相吻合的产品。
挤出成型法相比于其他类型的成形方法主要具有以下显着的优点:1、设备制造容易,成本较低,投产快,投资少。
2、产量高,效率快。
3、可以实现连续化生产。
制造较长的型材、管材等也比较容易。
而且产品均匀密实,质量高。
- 1、下载文档前请自行甄别文档内容的完整性,平台不提供额外的编辑、内容补充、找答案等附加服务。
- 2、"仅部分预览"的文档,不可在线预览部分如存在完整性等问题,可反馈申请退款(可完整预览的文档不适用该条件!)。
- 3、如文档侵犯您的权益,请联系客服反馈,我们会尽快为您处理(人工客服工作时间:9:00-18:30)。
刖吕随着我国橡胶机械工业的快速发展,橡胶制品的应用范围也在不断扩大,因此对于挤出成型技术也有了更高的要求。
在挤岀成型的一系列过程中,以温度的调节控制和熔融的物料进入挤出机机头以及橡胶在挤出机主机中塑化的过程最为重要。
螺杆作为橡胶挤出机主机的重要部件,它的设计加工已经很完善了。
随着各种各样的智能控制系统的发展,温度调节控制系统也取得了进展。
然而,挤出机机头的结构设计却仍然有很大的提升空间,并没有发展的很完善。
这是因为在挤出成型的整个过程中,会遇到各种复杂的情况。
而对于机头的设计,□前并没有适用于所有情况的理论公式,实际经验是挤出机机头的设计的主要依据。
机头设计后,通常用试模的方法来确定最后的形状。
这不但增加了设计人员的工作强度,也为整个的设计过程造成了诸多不便,同时也提高了成产成本。
挤出机作为橡胶工业的基本设备,在生产橡胶制品的过程中起着重要的作用,也是决定产品质量的重要设备之一。
国外橡胶挤出机经历了不同的发展阶段,从最初的柱塞式挤出机开始发展,其中经历了普通冷喂料型挤出机以及销钉冷喂料挤出机等阶段,再到现在的复合挤出机,其发展的日益完善,性能和生产能力也不断提高。
固特波公司是在挤出机的发展过程中,最先申请了用挤出机来进行胶电线生产的专利,并改进了该挤出机设备。
山此,挤出方法对于生产日益重要,而先前的手动式挤出机也渐渐地被电动操控挤出机所取代。
早期的电缆和电线源源不断地被柱塞式挤出机生产出来,电缆的生产用挤出法也山此而确定。
挤出机是挤出成型加工过程中的主要设备,除此以外,还有机头、牵引装置、冷却定型装置等附属设备。
橡胶在机筒内塑化熔融,通过机头制成所需要的形状,最后经过冷却定型后就可获得与机头截面形状相吻合的产品。
挤出成型法相比于其他类型的成形方法主要具有以下显著的优点:1、设备制造容易,成本较低,投产快,投资少。
2、产量高,效率快。
3、可以实现连续化生产。
制造较长的型材、管材等也比较容易。
而且产品均匀密实, 质量高。
4、工艺较易控制,生产操作起来比较简单,便于实现自动化生产。
设备占地面积小, 污染少,易于保持清洁的生产环境。
5、可以实现一机多用。
对于同一台挤出机,只需更换机头,就能加工不同的制品。
挤出机机头是连接在机筒上的零件,挤出产品的形状取决于机头,其主要作用有:1、改变挤出物料的运动状态,由螺旋运动状态改变为直线运动。
2、为保证制品质量密实,使挤出物料产生一定的压力。
3、进一步促进物料塑化。
4、使物料的截面形状满足产品设计要求。
XJ-150挤出机机头的设讣1挤出机机头设计要求概述1.1挤出机机头通用设计原则挤出机机头要遵循一定的合理的原则来进行相关设计,总结起来讲,主要有以下儿个原则:1、为缩短清洗时间和组装时间,挤出机机头的零部件要尽量少,而且要注意各个零部件的相互配合以及对中性。
2、要尽量减少机头中相关的连接环节。
部件数量减少的同时不但可以节约成本,也可以减少各个零部件在流道中的连接环节。
连接部位连接不良不但有可能导致漏料现象产生,也有可能使物料降解。
此外,连接部位要易于清洗。
3、运动部件与静止部件之间的间隙要进行密封。
主要方法是可以通过加上大尺寸的密封条或者填充绳来进行密封,需要注意点是应该加在静部件的半圆形或矩形沟槽内部。
用来做密封元件的材料主要有像PTFE这类耐热性比较好的塑料以及像铅这样的低硬度金属。
4、为确保整个密封表面的密封力分布均匀,要尽可能使密封表面平且小,同时要对这里的表面压力进行校核。
5、挤出机机头尽量有法兰可以转动,而且比较大的机头要安装在可以移动的或者可以调节的上面。
6、挤出机机头的组装紧固尽量不选用多个小的螺钉(这是因为直径大的螺栓寿命更长),而用比较少的耐热螺栓;螺栓在安装时尽量使其不必拆卸加热器,要尽量使其安装容易。
7、若挤出机机头的各个零部件温度并不完全相同,设计时,要考虑到热膨胀的问题。
8、挤出机机头设计时,不但要考虑温度传感器、压力传感器、螺栓孔对机头强度的影响,还要保证机头在受力产生形变时的尺寸符合要求。
当流道的结构确定时,要注意以下要求:1、熔融的物料要尽量沿着中心位置进入流道。
2、流道中截面积大的区域流速也低,熔融的物料在这样的区域滞留的时间也就越长, 这会引起像PE这样的热敬感型混合物料的降解。
针对这类材料,要服从最小流道体积原则,可以通过减小缝隙挤出机机头分配流道的方法,以便缩短挤出机机头的轴向长度。
3、机头流道中要避免物料流动方向的突变,也要防止截面积突变,即流道中不能有死角,所以各个位置的半径不能小于3mm。
4、在设计挤出机机头的平行成型区时,要消退流道端部的可逆的形变,且要根据生产的产品的性质和所加工熔融物料来进行设计。
5、要进行流道设计时,要减少流痕的数量,甚至要避免产生流痕。
这是因为流痕会影响挤出机挤出物料的质量。
1.2机头材料的选用 1.2.1挤出机机头选用材料要求挤出机机头在进行相应的设计时,一定要选用合理的材料,要符合以下儿点要求:1、便于加工2、刚度和强度足够大3、足够的耐磨性、耐压性和耐热性4、表面硬度也要要足够大5、便于进行相应的热处理6、进行热处理时形变要尽可能小7、便于获得合理的、无气孔的表面8、便于进行镀锯等处理9、具有良好的防腐性10、消除内应力11、具有良好的导热性1.2.2机头材料特殊要求以上这些在其他的加工中也有要求,并非挤出加工所特有。
显然,只用一种材料并不能满足所有的以上的要求,因此,在进行材料的选择时要注意下面儿点:1、所加工的聚合物的种类。
填充物料和腐蚀性对于磨损的影响,以及加工温度对磨损的影响。
2、挤出机机头的加工工艺。
材料强度在600N/mm=- 800N/mm2最适于加工,最高强度要求应该在1500N/mm-以下。
3、考虑材料的加工强度。
太脆的高强度钢不适合用来加工大的挤出机机头,这是因为在进行材料的选择时一定要考虑到弯曲应力。
4、要釆用的热处理。
为防止引起变形,除了可以选用部分有色金属之外,通常选用以下合理的钢材作为挤出机机头的材料。
5、钢材进行氮化处理6、钢材进行表面硬化处理7、选用不锈钢8、调质钢材9、安全硬化钢材表1-1机头主要零件选用的材料XJ-150挤出机机头的设讣表1-2护套材料参数1.3 XJ-150挤出机机头设计要求在进行XJ150挤出机机头的设计时,要满足以下要点:1、关于机头的内腔的形状应该设计成流线型。
为防止物料因为受阻停滞而产生过热分解的状况,保证熔融的物料能够沿着流道均匀的向前挤出,机头中不允许出现突变、急剧减小的设计,也不允许出现停滞区和死角,要尽可能的保证合理的设计使流道表面设计光滑,表面粗糙度Rd的值建议最好不高于0. 4 u mo2、截面形状要准确。
机头的成型截面形状跟产品实际的截面形状存在一定的差距,这是山于橡胶的性能和收缩率的因素,以及压力和温度的不同而造成的。
为了使挤出机机头的挤出产品有准确的截面形状,在设计过程中应该能够考虑到这一相应的影响。
3、选用合理的材料。
制造机头的材料应该耐磨耐腐蚀性能好,硬度大,抗拉强度高, 部分机头应根据实际情况进行镀锯。
4、压缩比要合理。
为了消除因为分流支架的原因而造成的结合缝,需要根据橡胶制品及橡胶种类的不同,来设汁可以产生足够压缩比的挤出机机头,保证制品质量密实。
5、结构紧凑,拆装方便,连接严密。
在满足力学性能要求的前提下,应使机头结构紧凑,拆装方便,传热均匀,连接严密,且不能泄料漏料。
挤出机是进行挤出生产的主要设备,在进行挤出生产时,每套模具只能够安装在跟其相匹配的挤出机上。
在进行机头的设计时,除了要满足制品的材料性能和形状尺寸要求外, 还需要掌握螺杆结构参数、端部结构尺寸和生产率等挤出机的技术规范,并且要保证挤出机的工艺参数满足设讣的要求。
机头的设讣不但要达到制品的强度指标,还要满足橡胶制品的外观质量要求,同时还要求挤出机的相关参数和机头的物料性能相适应,即要求挤出机机头能够安装在与之相应的挤出机上,并且在给定的转速下能够正常工作,否则的话,挤出工作就不能正常进行。
因此,机头的设计应该考虑到挤出机的因素,二者有着密切的联系。
不同型号的挤出机机头安装部位的装配尺寸也不相同。
2机头尺寸设计要求2. 1计算要求在进行机头的尺寸设计计算时,需注意以下儿点:1、选用合理的机头类型。
这主要取决于挤出产品的形状以及种类。
2、确定机头内流道的尺寸。
需要根据挤出量和挤出压力,分析流道内物料的运动状态。
3、对机头主要零部件的强度是否符合生产要求进行一系列的校核,本次设计主要考虑螺栓是否符合要求。
需要考虑熔融的物料在挤出机机头内的所具有的压力大小。
4、对机头进行相应的热平衡计算,选择合理的温度控制系统。
表2-1主要参数2. 2尺寸选取原则机头类型主要山挤出产品自身决定,流道的尺寸主要运用高分子材料流变学中的剪切理论决定,根据挤出产品截面形状的不同,依次对机头的压力、生产能力、流道内物料的速度分布、以及口型长度进行相应的分析计算求得。
为方便起见,不妨做如下假设:1、物料是不能被压缩的2、物料在机头中的温度沿机头的方向呈一致性分布3、物料在机头内流道上不会滑动,即物料在此处的速度为04、物料遵循非牛顿流体的指数方程XJ-150挤出机机头的设讣3主要零部件尺寸计算3. 1模具选择原则橡胶电缆产品质量的优劣,与橡胶本身的质量、挤出的温度、挤出机的性能、牵引芯线速度、芯线的预热、橡胶挤出后的冷却定型、挤出机机头模具的设计等诸多因素有关。
模具作为在橡胶电缆用挤出机进行挤出生产过程中最后用来进行相应定型的主要零部件,是影响所生产电缆产品最终质量的最关键因素之一。
模具的相关参数直接决定了电缆加工能否成功,比如:模具的形状、模具的尺寸、结构设计、压力的大小和温度的高低等。
正因为如此,任何橡胶电缆电线产品的生产都高度重视模具的相关设计、模具的选配以及保温措施。
挤压式模具是电缆电线生产的主要模具类型之一。
挤压式模具是模具的一种,它乂被称为圧力式模具,挤压式的特点是相比于其他类型的模具其模芯并没有存在管状承径的那一部分,并且不同的是它是缩在模套承径部分的后面。
熔融物料的定型是靠螺杆产生的压力通过模套来实现的。
挤压式模具挤出的橡胶层结构密实,表面光滑平整。
熔融橡胶压力的大小取决于模套与模芯之间夹角的大小,橡胶层的质量和最终挤出的电缆的质量也受此影响。
而挤出电缆制品的表面质量和儿何形状尺寸直接取决于模套和模芯的表面光洁度及其尺寸大小。
橡胶挤出后的膨胀和冷却后尺寸的收缩等因素对模套孔径的大小有一定的影响。
挤压式模具的出胶量和挤管式模具相比要低很多,这是因为压力式挤出会使橡胶在挤出机机头模口处产生较大的反作用力,从而减少了挤出量。
除了部分电缆护套(或绝缘层)的生产采用半挤管式和挤管式模具之外,II 前大部分电缆电线护套(或绝缘层)的生产都采用挤压式模具。