挤出机机头
挤出机的基本知识

挤出机的基本知识塑料挤出机的主机是挤塑机,它由挤压系统、传动系统和加热冷却系统组成1.挤压系统挤压系统包括螺杆、机筒、料斗、机头、和模具,塑料通过挤压系统而塑化成均匀的熔体,并在这一过程中所建立压力下,被螺杆连续的挤出机头。
(1)螺杆:是挤塑机的最主要部件,它直接关系到挤塑机的应用范围和生产率,由高强度耐腐蚀的合金钢制成。
(2)机筒:是一金属圆筒,一般用耐热、耐压强度较高、坚固耐磨、耐腐蚀的合金钢或内衬合金钢的复合钢管制成。
机筒与螺杆配合,实现对塑料的粉碎、软化、熔融、塑化、排气和压实,并向成型系统连续均匀输送胶料。
一般机筒的长度为其直径的15~30倍,以使塑料得到充分加热和充分塑化为原则。
(3)料斗:料斗底部装有截断装置,以便调整和切断料流,料斗的侧面装有视孔和标定计量装置。
(4)机头和模具:机头由合金钢内套和碳素钢外套构成,机头内装有成型模具。
机头的作用是将旋转运动的塑料熔体转变为平行直线运动,均匀平稳的导入模套中,并赋予塑料以必要的成型压力。
塑料在机筒内塑化压实,经多孔滤板沿一定的流道通过机头脖颈流入机头成型模具,模芯模套适当配合,形成截面不断减小的环形空隙,使塑料熔体在芯线的周围形成连续密实的管状包覆层。
为保证机头内塑料流道合理,消除积存塑料的死角,往往安置有分流套筒,为消除塑料挤出时压力波动,也有设置均压环的。
机头上还装有模具校正和调整的装置,便于调整和校正模芯和模套的同心度。
挤塑机按照机头料流方向和螺杆中心线的夹角,将机头分成斜角机头(夹角120o)和直角机头。
机头的外壳是用螺栓固定在机身上,机头内的模具有模芯坐,并用螺帽固定在机头进线端口,模芯座的前面装有模芯,模芯及模芯座的中心有孔,用于通过芯线;在机头前部装有均压环,用于均衡压力;挤包成型部分由模套座和模套组成,模套的位置可由螺栓通过支撑来调节,以调整模套对模芯的相对位置,便于调节挤包层厚度的均匀性。
机头外部装有加热装置和测温装置。
双螺杆挤出机的结构及原理

双螺杆挤出机的结构及原理双螺杆挤出机是一种常用的塑料加工设备,广泛应用于塑料加工行业,本文将介绍双螺杆挤出机的结构及其原理。
结构双螺杆挤出机主要包括机头、料斗、螺旋输送机、缸体、螺杆组、电控系统等组件。
•机头:双螺杆挤出机的出料口,通过机头将挤出的熔融塑料进行成型。
•料斗:贮存塑料原料。
•螺旋输送机:将料斗中的塑料原料输送到缸体中。
•缸体:分为加热区和冷却区,加热区通过电热管加热,使塑料原料熔化并提高其流动性;冷却区通过水循环冷却,使塑料原料快速降温固化。
•螺杆组:可以分为驱动螺杆和被动螺杆,驱动螺杆由电机提供动力,通过传动装置带动被动螺杆旋转,将塑料原料在缸体中挤出。
•电控系统:控制双螺杆挤出机的启动、停止、加热、冷却和速度等参数。
原理双螺杆挤出机的工作原理是将塑料原料经过加热融化变成熔融塑料,通过螺杆的旋转将熔融塑料挤出机头形成管材、板材等形状。
具体工作过程如下:1.将塑料原料放入料斗中,由螺旋输送机将原料运送到缸体中。
2.缸体中的螺杆组由电机驱动旋转,将原料挤压向机头。
被动螺杆通过沟槽的作用将塑料原料送向驱动螺杆处。
3.加热区电热管的加热作用使塑料原料快速熔化变成熔融状态。
4.熔融塑料在螺杆的作用下,完全混合均匀后,通过机头挤出。
5.冷却区水循环制冷,使挤出的塑料快速降温固化成型。
6.控制系统可以实现对双螺杆挤出机的启停、加热、冷却、速度等参数的调节和控制。
总结双螺杆挤出机的结构及其原理相对简单,但具有高效、稳定、可靠的特点,广泛应用于塑料加工领域。
通过加热、挤出和冷却三个步骤,能够实现对塑料原料的自动化加工和成型,满足不同行业对塑料制品的需求。
挤出机机头设计
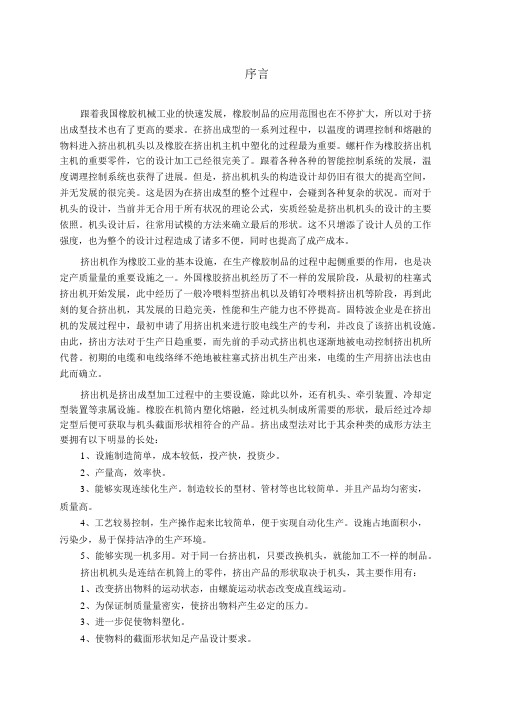
序言跟着我国橡胶机械工业的快速发展,橡胶制品的应用范围也在不停扩大,所以对于挤出成型技术也有了更高的要求。
在挤出成型的一系列过程中,以温度的调理控制和熔融的物料进入挤出机机头以及橡胶在挤出机主机中塑化的过程最为重要。
螺杆作为橡胶挤出机主机的重要零件,它的设计加工已经很完美了。
跟着各种各种的智能控制系统的发展,温度调理控制系统也获得了进展。
但是,挤出机机头的构造设计却仍旧有很大的提高空间,并无发展的很完美。
这是因为在挤出成型的整个过程中,会碰到各种复杂的状况。
而对于机头的设计,当前并无合用于所有状况的理论公式,实质经验是挤出机机头的设计的主要依照。
机头设计后,往常用试模的方法来确立最后的形状。
这不只增添了设计人员的工作强度,也为整个的设计过程造成了诸多不便,同时也提高了成产成本。
挤出机作为橡胶工业的基本设施,在生产橡胶制品的过程中起侧重要的作用,也是决定产质量量的重要设施之一。
外国橡胶挤出机经历了不一样的发展阶段,从最初的柱塞式挤出机开始发展,此中经历了一般冷喂料型挤出机以及销钉冷喂料挤出机等阶段,再到此刻的复合挤出机,其发展的日趋完美,性能和生产能力也不停提高。
固特波企业是在挤出机的发展过程中,最初申请了用挤出机来进行胶电线生产的专利,并改良了该挤出机设施。
由此,挤出方法对于生产日趋重要,而先前的手动式挤出机也逐渐地被电动控制挤出机所代替。
初期的电缆和电线络绎不绝地被柱塞式挤出机生产出来,电缆的生产用挤出法也由此而确立。
挤出机是挤出成型加工过程中的主要设施,除此以外,还有机头、牵引装置、冷却定型装置等隶属设施。
橡胶在机筒内塑化熔融,经过机头制成所需要的形状,最后经过冷却定型后便可获取与机头截面形状相符合的产品。
挤出成型法对比于其余种类的成形方法主要拥有以下明显的长处:1、设施制造简单,成本较低,投产快,投资少。
2、产量高,效率快。
3、能够实现连续化生产。
制造较长的型材、管材等也比较简单。
并且产品均匀密实,质量高。
挤出成型机头的作用和用途
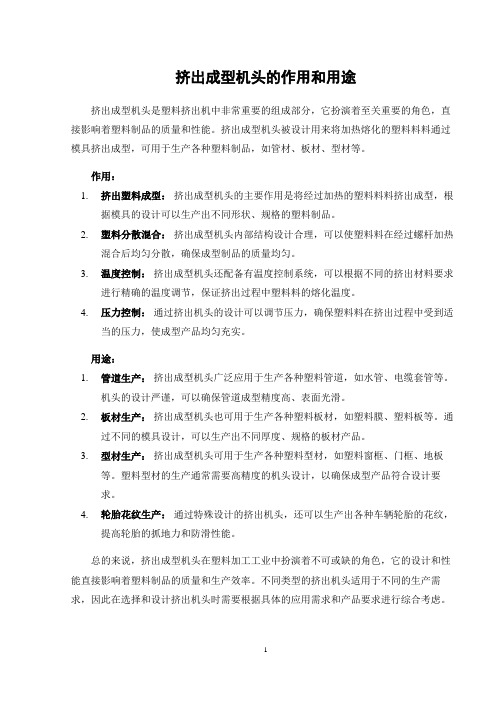
挤出成型机头的作用和用途挤出成型机头是塑料挤出机中非常重要的组成部分,它扮演着至关重要的角色,直接影响着塑料制品的质量和性能。
挤出成型机头被设计用来将加热熔化的塑料料料通过模具挤出成型,可用于生产各种塑料制品,如管材、板材、型材等。
作用:1.挤出塑料成型:挤出成型机头的主要作用是将经过加热的塑料料料挤出成型,根据模具的设计可以生产出不同形状、规格的塑料制品。
2.塑料分散混合:挤出成型机头内部结构设计合理,可以使塑料料在经过螺杆加热混合后均匀分散,确保成型制品的质量均匀。
3.温度控制:挤出成型机头还配备有温度控制系统,可以根据不同的挤出材料要求进行精确的温度调节,保证挤出过程中塑料料的熔化温度。
4.压力控制:通过挤出机头的设计可以调节压力,确保塑料料在挤出过程中受到适当的压力,使成型产品均匀充实。
用途:1.管道生产:挤出成型机头广泛应用于生产各种塑料管道,如水管、电缆套管等。
机头的设计严谨,可以确保管道成型精度高、表面光滑。
2.板材生产:挤出成型机头也可用于生产各种塑料板材,如塑料膜、塑料板等。
通过不同的模具设计,可以生产出不同厚度、规格的板材产品。
3.型材生产:挤出成型机头可用于生产各种塑料型材,如塑料窗框、门框、地板等。
塑料型材的生产通常需要高精度的机头设计,以确保成型产品符合设计要求。
4.轮胎花纹生产:通过特殊设计的挤出机头,还可以生产出各种车辆轮胎的花纹,提高轮胎的抓地力和防滑性能。
总的来说,挤出成型机头在塑料加工工业中扮演着不可或缺的角色,它的设计和性能直接影响着塑料制品的质量和生产效率。
不同类型的挤出机头适用于不同的生产需求,因此在选择和设计挤出机头时需要根据具体的应用需求和产品要求进行综合考虑。
1。
挤出机头的分类及特点有哪些机头设计的主要

挤出机头的分类及特点有哪些机头设计的主要
挤出机头是塑料挤出机中的关键部件,负责将加热融化的塑料通过模具的形状挤出成型。
根据挤出机头的不同设计和结构,可以将其分为多种分类,并且每种分类都具有其独特的特点和优势。
首先,从结构形式上来看,挤出机头可以分为光圈式机头、螺杆式机头和板式机头三种主要类型。
光圈式机头由针管和鞍座组成,适用于挤出螺纹、型材、带材等产品;螺杆式机头主要由挤出螺杆和机筒组成,适用于挤出管材、板材等产品;板式机头由板状合模和螺杆组成,适用于挤出薄膜、片材等产品。
不同类型的机头适用于不同的产品挤出加工,有着各自独特的特点和优势。
其次,从挤出成型方式上来看,挤出机头又可以分为单层机头、多层机头、中空机头等。
单层机头适用于一次性成型的产品,结构简单、生产效率高;多层机头可以实现多层产品挤出成型,产品层次丰富,适用于复合产品的生产;中空机头适用于中空结构产品的挤出,如管材、异形材等,具有独特的设计和挤出方式。
最后,挤出机头的特点还包括挤出均匀性、调节精准、耐磨耐高温等。
好的挤出机头设计可以保证挤出产品的均匀性和一致性,提高生产效率和产品质量;精准的调节设计可以使挤出机头适应不同材料和产品的生产需求;耐磨耐高温的材质和表面处理则可以延长机头的使用寿命,减少维护成本。
综上所述,挤出机头作为塑料挤出机中的重要组成部分,其分类和特点根据不同的设计和结构而有所不同,每种类型都有其适用的领域和优势。
在实际生产中,选择合适的挤出机头设计将对产品的质量和生产效率产生重要影响,因此选择合适的挤出机头至关重要。
1。
挤出机机头设计原则和参数选择 韩兵
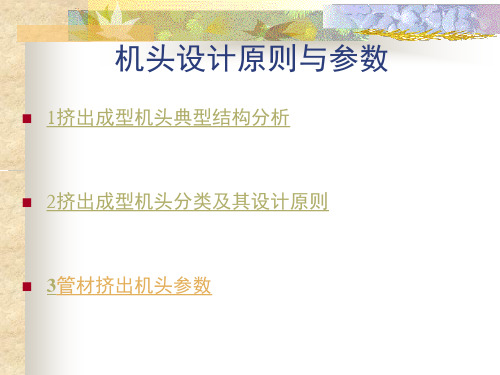
2.管材挤出机头零件的设计 (1) 口模
口模是成型管材外表面的零件,其 结构如图8-6所示。口模内径不等于塑料 管材外径,因为从口模挤出的管坯由于 压力突然降低,塑料因弹性恢复而发生 管径膨胀,同时,管坯在冷却和牵引作 用下,管径会发生缩小。这些膨胀和收 缩的大小与塑料性质、挤出温度和压力 等成型条件以及定径套结构有关,目前 尚无成熟的理论计算方法计算膨胀和收 缩值,一般是根据要求的管材截面尺寸, 按拉伸比确定口模截面尺寸。所谓拉伸 比是指口模成型段环隙横截面积与管材 横截面积之比。
L2=(1.5~2.5)D0
(8-4)
式中D0——栅板出口处直径。 芯模直径d1可按下式计算;
d1=d—2δ
(8-5)
式中δ—芯模与口模之间间隙;
d—口模内径。
由于如上所述塑料熔体挤出口模后的膨胀 与收缩,使δ不等于制品壁厚,δ可按下式计 算式:中k—经验系 数 ,kt k=1.(168~-61).20;
5.机头体 用来组装机头各零件及挤出机连接。 6.定径套 使制品通过定径套获得良好的表面粗糙度,正确 的尺寸和几何形状。 7.堵塞 防止压缩空气泄漏,保证管内一定的压力。
挤出成型机头分类及其设计原则
1.分类 由于挤出制品的形状和要求不同,因此要有相应
的机头满足制品的要求,机头种类很多,大致 可按以下三种特征来进行分类: (1)按机头用途分类 可分为挤管机头、吹管机头、挤板机头等;
2.设计原则
为了使挤出制品具有外观光洁性、尺寸准确性、形状与位置精确 准确性、单位长度的质量和物理力学性能等,一般遵循下面几个原 则:
(1)流道呈流线型 为使物料能沿着机头的流道充满并均匀地被挤 出,同时避免物料发生过热分解,机头内流道应 呈流线型,不能急剧地扩大或缩小,更不能有死 角和停滞区,流道应加工得十分光滑,表面粗糙 度应在Ra 0.4um以下。 (2)足够的压缩比 满足具体制品对机头压力的要求从而使制品密 实和消除因分流器支架造成的结合缝,根据制品 和塑料种类不同,应设计足够的压缩比。
挤出成型机头应设置适当的_装置
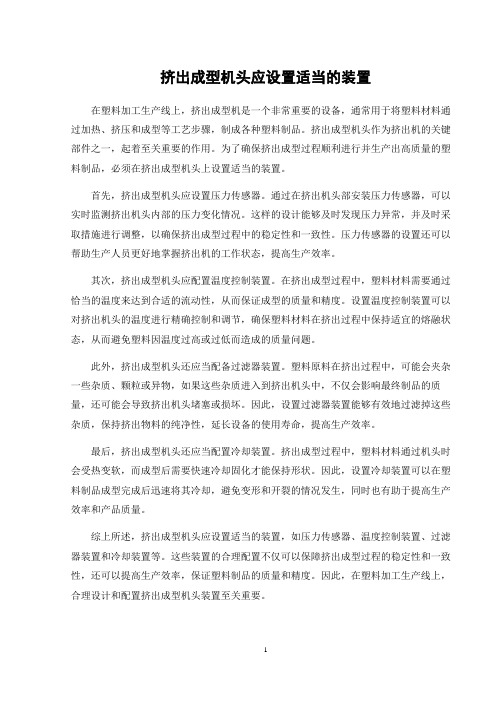
挤出成型机头应设置适当的装置在塑料加工生产线上,挤出成型机是一个非常重要的设备,通常用于将塑料材料通过加热、挤压和成型等工艺步骤,制成各种塑料制品。
挤出成型机头作为挤出机的关键部件之一,起着至关重要的作用。
为了确保挤出成型过程顺利进行并生产出高质量的塑料制品,必须在挤出成型机头上设置适当的装置。
首先,挤出成型机头应设置压力传感器。
通过在挤出机头部安装压力传感器,可以实时监测挤出机头内部的压力变化情况。
这样的设计能够及时发现压力异常,并及时采取措施进行调整,以确保挤出成型过程中的稳定性和一致性。
压力传感器的设置还可以帮助生产人员更好地掌握挤出机的工作状态,提高生产效率。
其次,挤出成型机头应配置温度控制装置。
在挤出成型过程中,塑料材料需要通过恰当的温度来达到合适的流动性,从而保证成型的质量和精度。
设置温度控制装置可以对挤出机头的温度进行精确控制和调节,确保塑料材料在挤出过程中保持适宜的熔融状态,从而避免塑料因温度过高或过低而造成的质量问题。
此外,挤出成型机头还应当配备过滤器装置。
塑料原料在挤出过程中,可能会夹杂一些杂质、颗粒或异物,如果这些杂质进入到挤出机头中,不仅会影响最终制品的质量,还可能会导致挤出机头堵塞或损坏。
因此,设置过滤器装置能够有效地过滤掉这些杂质,保持挤出物料的纯净性,延长设备的使用寿命,提高生产效率。
最后,挤出成型机头还应当配置冷却装置。
挤出成型过程中,塑料材料通过机头时会受热变软,而成型后需要快速冷却固化才能保持形状。
因此,设置冷却装置可以在塑料制品成型完成后迅速将其冷却,避免变形和开裂的情况发生,同时也有助于提高生产效率和产品质量。
综上所述,挤出成型机头应设置适当的装置,如压力传感器、温度控制装置、过滤器装置和冷却装置等。
这些装置的合理配置不仅可以保障挤出成型过程的稳定性和一致性,还可以提高生产效率,保证塑料制品的质量和精度。
因此,在塑料加工生产线上,合理设计和配置挤出成型机头装置至关重要。
挤出机头的分类

(2)按挤出塑件的出口方向分类: 直通机头:熔体在机头内的挤出流向与挤 出机螺杆的轴线平行。
(图4.4 为直通式管材机头)
角式机头:熔体在机头内的挤出流向与 挤出机螺杆的轴线呈一定角度。
图4.6为直角式管材机头
(3) 按塑料熔体在机头内所受压力分类:
➢<
挤出机头的分类
➢ 按挤出成型的塑料制件分类 ➢ 按挤出塑件的出口方向分类 ➢ 按塑料熔体在机头内所受压力分类
(1) 按挤出成型的塑料制件分类:
挤出成型塑件:管材、棒材、板材、 片材、网材、单丝、粒料、各种异型材、 吹塑薄膜、带有塑料包覆层的电线电缆等。
相应的机头分别称为:管机头、棒机
塑料成型工艺与模具设计
- 1、下载文档前请自行甄别文档内容的完整性,平台不提供额外的编辑、内容补充、找答案等附加服务。
- 2、"仅部分预览"的文档,不可在线预览部分如存在完整性等问题,可反馈申请退款(可完整预览的文档不适用该条件!)。
- 3、如文档侵犯您的权益,请联系客服反馈,我们会尽快为您处理(人工客服工作时间:9:00-18:30)。
上述三种机头的特征对比
管材机头尺寸设计
8、螺旋芯棒模头
优点: 1) 熔体能沿着口模的圆周均匀分布, 在制品上没有流动痕迹( 结合线) , 制品在圆 周方向上的厚度公差和各种性能均匀; 2) 压 力降和流动阻力较低, 在较高的产量下挤出物 的温度较低; 3) 机械应力和热应力较低,制品 有良好的机械强度; 4) 模头结构坚固, 适合高 粘度材料的吹塑成型, 同时, 机头的装拆操作
2.芯棒 1)芯棒的外径 芯棒的外径由管材的内径决定, 根据生产经验: d= D-2e 式中 d一芯棒的外径(mm); D一口模的内径(mm); e一口模与芯棒的单边间隙(mm), e =(0.83-0.94)t t一材料壁厚(mm)。
2)定型段、压缩段L2和收缩角 a、芯棒定型段的长度与L1相等或稍长。 b、L2可按下面经验公式计算: L2=(1.5-2.5)D0 式中 L2一芯棒的压缩段长度(mm); D0一塑料熔体在过滤板出口处的流道 直径(mm)。 c、芯模收缩角: 低粘度塑料 =45°-60° 高粘度塑料 =30°-50°
的环隙截面积之比,反映出塑料熔体的压实
程度。 低粘度塑料ε =4-10 高粘度塑料 ε =2.5-6.0
7管材挤出机的机头
分类
1)直通式机头
2)直角式机头
3)旁侧式机头
1)直通式机头 结构简单、制造容易、成本低、料流阻 力小等优点;但这种机头的缺点是在生产外 径 大的管材时芯模加热困难,分流器支架 造成的接缝处管材强度低。适用于加工RPVC、 SPVC、 PA、PC、PE和PP等塑料管材,一般 用于挤小口径的管材。
3、挤出机头设计原则
1.内腔呈流线型 :为了使塑料熔体能沿着机
头中的流道均匀平稳地流动而顺利挤出 (表面粗
糙度应小于1.6-3.2m );
2.足够的压缩比 :为使制品密实和消除因分
流器支架造成的结合缝 ;
3.正确的截面形状和尺寸 :要对口模进行适
当的形状和尺寸补偿;
4.合理的选择材料:为提高机头的使用寿命,
机头材料应选择耐磨、耐腐蚀、硬度高的钢 材或合金钢。
4、挤出机机头的结构组成
挤出模的主要零件:
口模、芯棒、过滤板、过滤网、分
流器、分流器支架、调节螺钉、定型套
和机头体。
主要结构的作用:
1)口模和芯模分别成型制品内外表面,定型 部分决定了制品的横截面形状 和尺寸; 2)分流器是使通过它的熔体变成薄环状,平 稳地进入成形区。同时,进一步加热和塑化 塑料 ; 3)定型套对成形管材进行冷却定型,以保证 制品良好质量,正确的尺寸和几何形状; 4)调节螺钉用来控制成形区内的口模和芯棒 之间的间隙及同轴度,以保证挤出塑件壁厚 的均匀 。
1、挤出机机头分类 2、挤出机机头的作用 3、挤出机机头的设计原则 4、挤出机机头的组件 5、工艺参数计算 6、管材挤出的机头介绍
1、挤出机头的分类 :
(1) 按挤出成型的塑料制件分类:有管材、棒材、板
材、片材、网材、单丝、粒料、各种异型材、吹塑薄
膜、电线电缆等。 (2) 按制品出口方向分类:有料流方向与挤出机螺 杆轴向一致的直向机头如硬管机头和料流方向与 挤出机螺杆轴向成某一角度横向机头如电缆机头。
工艺参数的确定
1.口模 1)口模外径:
D=d/k 式中 D-口模的内径(mm)。 D-管材的外径(mm) K-补偿系数,见表5-4
表5-4 补偿系数k值
2)定型段长度L1 a、按管材外径计算: L1=(0.5—3)D 通常当管子直径较大时定型长度取小值,因为 此时管子的被定型面积较大,阻力较大,反 之就取大值。同时考虑到塑料的性质,一般 挤软管取大值,挤硬管取小值。 b、按管材壁厚计算:L1=nt 式中 t一管材壁厚(mm); n一 系数,见表5-5。
3.分流器
(1)分流锥的角度(扩张角):
低粘度塑料 =30°-80° 高粘度塑料 =30°-60° 扩张角>收缩角过大时料流的流动阻力 大,熔体易过热分解;过小时不利于机头对其 内的塑料熔休均匀加热,机头体积也会增大。
(2)分流锥长度L5 L5=(1-1.5)D0 式中 D0一头于过滤板相连处的流道直径 (mm),如图5-6所示。 (3)分流锥尖角处圆弧半径R: R=(0.5-2) mm R不易过大, 否则熔体容易 在此处发 生滞留
(3) 按机头内压力大小分类 :有低压机头(料流压力
小于4MPa)、中压机头(料流压力为4—1OMPa)和
高压机头(料流压力大于1OMPa).
2、挤出机头主要作用:
(1)使物料由螺旋运动 变为直线运动。 (2)产生必要的成型压 力,保证制品密实。 (3)使物料通过机头得 到进一步塑化。 (4)通过机头成型所需 要的断面形状的塑料 制品。
(4)分流器表面粗糙度Ra Ra<0.4-0.2m (5)栅板与分流锥顶间隔L6 L6=(10-20)mm 或L5<0.1D1 式中 D1一 杆直径,如图5-8所示。
拉伸比和压缩比
拉伸比和压缩比是与口模和芯棒尺寸相关 的工艺参数。根据管材断面尺寸确定口模环 隙截面尺时,一般尚凭拉伸比确定 (1)拉伸比I 所谓管材的拉伸比是口模和芯棒的
5、口模、芯模定型部分长度的选择
为消除熔接缝, 使物料压力稳定且均匀 挤出, 口模、芯模定型部分长度通常为 口模间隙宽度的15 倍以上, 定型段长度
为分流处芯棒直径的2 倍以上。
6、压缩比
压缩比ε即流道最大截面积与挤出口模环隙面 积之比, ε值体现了压力降的大小。ε值过小, 易造成 泡膜挤压不实, 膜厚不均; ε值过大, 则熔料在流道中 易过热且在出口发生熔胀。一般取1.5~ 3 为宜。
环隙截面积与管材成型后的截面积之比,其
计算公式如下:
I
式中
D1 D2 d1 d 2
2
2
2
2
I一拉伸比; D1一口模内径(mm); D2一芯棒外径(mm); d1一 塑料管材的外径(mm); d2一塑料管材的内径(mm)。
(2)压缩比ε
所谓管材的压缩比是机头和
多孔板相接处最大进料截面积与口模和芯棒
2)直角式机头 这种结构芯模一端为支承端。不存在 分流器支架,熔料从机头一端进人芯模对 面汇集,只可能生一条接缝线。定径精度 较髙,而且管材的内外壁同时进行冷却, 出料均勻,管材质量好,产量高。
3)旁侧式机头
来自挤出机的料流先流过一个弯形流道再 进入机头一侧,料流包芯模后沿机头轴向流 出。这种设计可使管材的挤出方向与挤出机 呈任意角度,亦可与挤出机螺杆轴线相平行。 但机头结构比较复杂,造价较髙。