热电材料外文翻译
工程材料外文翻译【中英文对照】(可编辑)
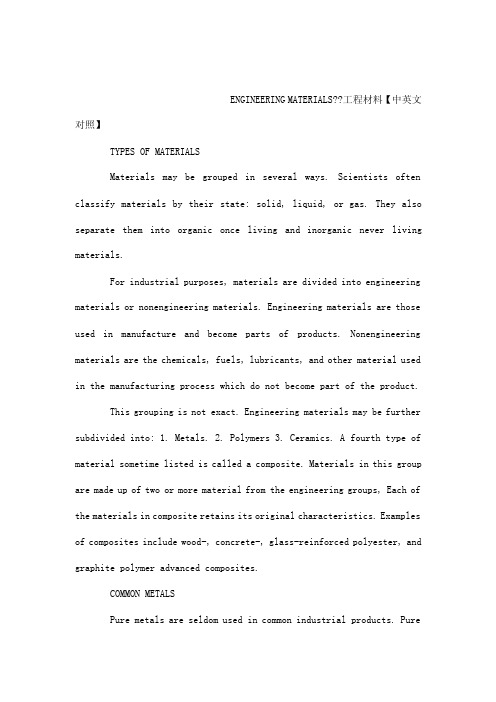
ENGINEERING MATERIALS??工程材料【中英文对照】TYPES OF MATERIALSMaterials may be grouped in several ways. Scientists often classify materials by their state: solid, liquid, or gas. They also separate them into organic once living and inorganic never living materials.For industrial purposes, materials are divided into engineering materials or nonengineering materials. Engineering materials are those used in manufacture and become parts of products. Nonengineering materials are the chemicals, fuels, lubricants, and other material used in the manufacturing process which do not become part of the product.This grouping is not exact. Engineering materials may be further subdivided into: 1. Metals. 2. Polymers 3. Ceramics. A fourth type of material sometime listed is called a composite. Materials in this group are made up of two or more material from the engineering groups, Each of the materials in composite retains its original characteristics. Examples of composites include wood-, concrete-, glass-reinforced polyester, and graphite polymer advanced composites.COMMON METALSPure metals are seldom used in common industrial products. Purecopper is used in electrical applications, in automotive radiators, and gaskets. Pure aluminum has application in the chemical and electrical industries. However, most metals are alloyscombinations of two or more elements. There are over 25,000 different iron-carbon alloyssteel and over 200 standard copper alloys including a number of brasses, bronzes, and nickel silvers. Each of these alloys are identified by a code number.Steel is an alloy of iron and carbon with other elements added to produce specific properties. The various type of steel can be grouped under two major heading:1?Carbon steel. A steel in which the main alloying element is carbon. Carbon steel are further divided into three groups.a.?Low carbon steel. This steel has a carbon content of less than0.30 percent. It is the most common type and is often called mild steel. It is relatively inexpensive, ductile, soft, and is easily machined and forged. Mild steel cannot be heat-treatedhardened. Low carbon steel isa general purpose steel.b.?Medium carbon steel. This steel has a carbon content between0.30 percent and 0.80. Harder and stronger than mild steel, it can be hardened by heat treating. Medium carbon steel is most commonly used for forgings, castings, and machined parts for automobiles, agricultural equipment, machines, and aircraft.c.?High carbon steel. This type of steel is easily heat-treatedto produce a strong, tough part. The material has a carbon content above 0.80 percent. It finds wide use in hand tools, cutting tools, springs, and piano wire.2?High alloy steel. These steels contain significant amounts of other elements in addition to carbon. The common high alloy steel are:a.?Stainless steel which is produced by using chromium as a significant alloying element along with nickel and other metals. The result is a tough, hard, corrosion-resistant metalb.?Tool steel which is a special group of high carbon steels produced in small quantities to high quality specifications. Tool steel are used for a wide range of cutting tools and forming dies.c.?Manganese steel which is an alloy containing 21 percent manganese and one percent carbon. This metal is used in mining, railroad, and construction equipment because of its high tensile strength.PROPERTIES OF MATERIALSAll material have their own properties or characteristics. These properties may be arranged into major groups which include: Physical properties.Mechanical properties.Chemical properties.Thermal properties.Electrical and Magnetic properties.Optical properties.Acoustical properties.1.Physical PropertiesPhysical properties, for this discussion, are restricted to those which describe the basic features of the material. These features are measured or observed without the use of extensive scientific experiments. The common physical properties are size, shape, density, and porosity.Size is the overall dimensions of the object. These dimensions, for most materials, are given as thickness, width, and length or as diameter and length.Shape is the contour or outline of the object., Contour is given to an object by curved, notched, sloped, or other irregular surfaces.Density or specific gravity measures the mass of an object. The measurement is by weight for a unit or a certain volume. Typically, density is measured by pounds per cubic foot or kilograms per cubic meter of material. Density allows the mass of one material to be compared with that of other materials.Porosity is a measure of voidsopen pores in the material. It is generally described as a ratio of open pore volume to total volume of material. This ratio expressed as a percentage. Porosity will provide a measure of liquid-holding power, or the ability of air or gas to move through the material.2.Mechanical PropertiesMechanical properties mean a material’s ability to carry or resist the application of mechanical forces and loads. The material’s reaction to these forces is usually either deformation shape change or fracture.Mechanical properties are probably the most important, to manufacturing processing. They determine the extent to which a material may be formed, sheared, or machined.Typical forces which are applied to a material are tension, compression, shear, and torsion, these forces are used to form and form and shape materials. Furthermore, materials must withstand excess amounts of these forces in product applications. Since screws are used to assemble wood parts, they must absorb torsion forces. Rods holding suspended fixtures must withstand excess tension forces. The head of a hammer must absorb compression forces.1?Stress-strainThe stress-strain relationship is often used to study many mechanical properties. Stress is force applied to material. It is usually measured in either pounds per square inch or kilograms per square centimeter. Strain is the change in the length of a material which is under stress. The strain measurements are given in terms of the? amount of elongation increased length of the material per unit of length. Strain is given inthousandths of an inch per inch of material of millimeters or smaller units per centimeter of material. For most materials, the elongation of a material under stress is quite small A stress-strain diagram, like the one shown in Fig.1.1, is widely used to chart stress-strain relationships. The stress force per unit area is plotted on the vertical axis while the strain elongation of each unit of length is plotted on the horizontal axis.As stress is applied, the material first resists permanent deforming. This area is the material’s elastic range. This is a range in which the material will return to its original length when the force is released.Applying additional stress force will bring the material to its yield point. At this point additional strain elongation occurs without additional force stress being applied. Strain above this point is produced with smaller amounts of force. The force also produces permanent changes in the length of the material.This elongation which is above the material’s elastic limit point at which the material will mot return to its original length is called plastic deformation.As stress is increasingly applied above the yield point, additional strain occurs. Finally, a imum strain is reached and the material begins to fail, Its internal structure begins to come apart This point is called the material’s ultimate strength or tensile strength.Additional stress may cause a reduction in cross-sectional area necking and will finally cause fracture.2 Mechanical strengths.A material can be subjected to a number of different types of forces. They may be tension , shear, torsion, compression, or a combination of these force. Each possible force causes a material to respond in a different way. A material, therefore, has several different mechanical strengthsThe strength depends on the force applied.The most common mechanical strengths are:a.?Tensile strength??the imum tension load a material can withstand before fracturing. Tensile strength is the easiest strength to measure and, therefore, is widely used.b.?Compression strength??the ability to resist forces which tend to squeeze the material into a new shape. It is basically the opposite of tensile strength. Excessive compression force will cause the material to rupture bucking and splitting.c.?Shear strength??the ability to resist fracture under shear forces. The shear forces is caused by offset forces applied in opposite. These forces cause the grains or molecules of the material to slide by one another and eventually fracture.d.?Torsion strength??the ability to resist twisting forces. Forces which exceed the torsion strength modulus of rupture will cause thematerial to rupture e.?Flexure bending strength??the ability of a material to resist the combination of tensile and compression forces. As seen in Fig.1.2, when a material is bent, the material on the inside of? the bend must compress while that on the outside portion must stretch.A material must have flexure strength to undergo bending processes.f.?Fatigue strength??the ability to resist forces which wary in direction and/or magnitude. Typical of forces which cause. Fatigue are constant bending back and forthplastic hinge, applying and releasing tension forcescoil spring, or torsion forcescoil spring, or torsion forcesautomobile torsion bar.g.?Impact strength??the ability to resist a rapidly applied load. This is a more specific measure of tension or compression strengths, Impact strength determines the ability to absorb a tension or compression load which is quickly applied. Impact strength is often called toughness. The action of a hammer on a nail applies such impacts. Forging dies must have high impact strength.3 Plastic flow of materials.In addition to the mechanical properties involving strength, materials have characteristics that govern their behavior during the plastic defomation stage. These properties are usually called ductility and creep.Ductility is the plastic flow characteristic of a material undernormal temperature. The higher the ductility of a material the greater is ability to be formed without fracturing. Highly ductile materials can be easily bent. Drawn into wire, or extruded.Creep is the movement or plastic flow of material under load over an extended period of time. Creep of a material is affected by the stress level force applied, temperature of the material, and the length of time over which the stress is applied. Also different types of material have different creep characteristics. Wood creeps very little. Metal experiences slight amounts of creep. Glass and plastic are more likely to experience significant amounts of creep.4 HardnessHardness is the resistance of a material to penetration or scratching. It accounts for abrasion resistance as well as resistance to denting. Hardness is also directly related to strength. The harder a material the stronger it is. Metallic and ceramic material are almost always harder and stronger than polymeric materials. A number of different testers have been designed to test the hardness of a variety of materials.3.Chemical PropertiesAll materials are used in some types of environment. All environments, except a pure vacuum, contain chemicals. These chemicals may be gases oxygen, hydrogen, chlorine, nitrogen, liquids water, acids, oils or solids other engineering materials. The reaction between the chemicals and a material in an environment is called corrosion.These reactions are complex and require a knowledge of chemistry for a full understanding, In general, these are several types of chemical reactions. These include:1?Oxidation??corrosion caused by a reaction between the material and oxygen in the air. Iron oxidizes to form iron oxide rust. Some polymers are weakened and destroyed by a combination of sunlight and oxygen. Rubber is particularly prone to oxidation which is called aging. As rubber ages it loses its flexibility elasticity and strength.2?Electrochemical corrosion??corrosion caused by electrical currents set up in a material in a liquid or moist environment. Electrical current flows from one point on the material anodic area to another part cathodic. The current removes materials from the anodic area and deposits it at the cathodic area. This action is similar to the operation of the storage battery.3?Water absorption??the tendency of polymers and ceramic material to absorb water. This action increases the material’s weight and volume, water absorption will cause many materials to warp and swell, and lose desirable mechanical and electrical properties.4.Thermal PropertiesAll materials are subjected to thermalheat energy. Heat may cause the material to change its physical form melt, evaporate, to change in size, or to change in temperature. Heat may also change the internalstructure of material.The important thermal properties to material are:1?Heat resistant, the ability of a material to remain stable with changes in temperatureCeramic materials have high heat resistance ratings.2?Thermal conductivity, the ability of a material to transfer heat energy along its length , width, or thickness. The rate of heat transfer for thermal conductivity. Ceramics and polymers have low conductivity rates. They are therefore good heat insulators.3?Thermal expansion, the rate of size change per unit of heat applied. Almost all engineering materials expand as they are heated, The rate of expansion is called the coefficient of linear expansion. The rate of expansion varies greatly among materials.The varying rates of thermal expansion are the basis of the basis of the bimetal thermostat. The metal stripe of the thermostat have greatly different thermal expansion coefficients. When they are bonded together and heated, the metal with the high expansion rate elongates much more than the other strip. This causes the strips to bend and touch the contact point. This action closes an electric circuit which could start a furnace, turn on a cooling fan, or light a warning light.5.Electrical and Magnetic PropertiesElectrical and magnetic properties are similar. The electricalproperties describe the behavior of a material carrying an electrical current , Magnetic properties involve the behavior of materials in an electromagnetic field. These properties include:1?Electrical conductivity??the ability to conduct an electric current, Engineering materials are classified as conductors easily carry electrical current and insulators resistance to conducting current. Other materials are called semiconductors and are the foundation of the computer and data processing industry The opposite of electrical conductivity is electric current resistivity resistance to conducting current. If rsistivity is an important property, it is often discussed as the dielectric property or strength. The dielectric strength is a specific measure of a material’s electrical in sulating qualities. Metals generally are considered conductors of electricity while ceramics and polymers are insulators have high dielectric constants.2?Magnetic properties??the ability to be magnetized an external electromagnetic force. Materials with high magnetic properties are said to be permeable or have high permeability. Iron, nickel, and cobalt which are called ferromagnetic materials have high permeability. They are easily magnetized.6. Optical PropertiesOptical properties govern the m aterial’s reaction to light. These properties include:1?Opacity??the degree to which a material obstructs visible light. Materials with high opacity are said to be opaque. Low-opacity materials are called transparent.2?Color??the appearance of the material which depends on the spectrum of light it reflects to the human eye.3?Transmittance??the measure of the amount of light transmitted by a material. The opposite of transmittance is reflectance. Window glass has high transmittance while polished aluminum has high reflectance.7.Acoustical PropertiesAcoustical properties describe a material’s reaction to sound waves. The most important acoustical property is the sound insulating or absorbing quality quality of the material. This is the ability of the material to absorb sound and is called its sound absorption coefficient. Most ceiling tile has high sound absorption coefficients to reduce echoes in a room.工程材料材料可以在几个方面进行划分。
热电材料(全面的)
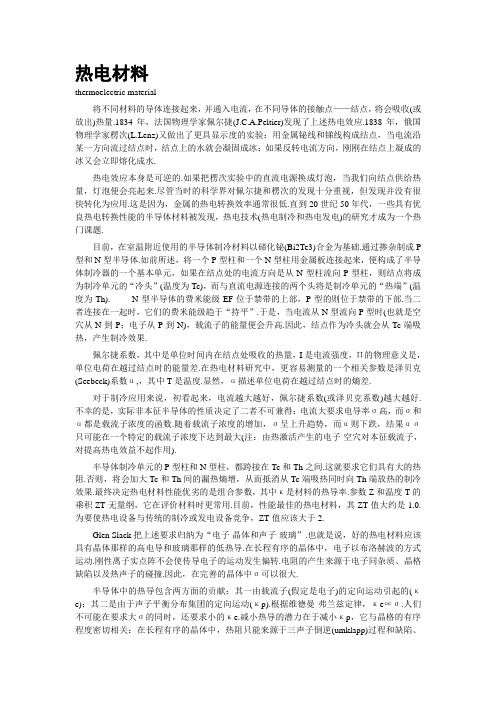
热电材料thermoelectric material将不同材料的导体连接起来,并通入电流,在不同导体的接触点——结点,将会吸收(或放出)热量.1834年,法国物理学家佩尔捷(J.C.A.Peltier)发现了上述热电效应.1838年,俄国物理学家楞次(L.Lenz)又做出了更具显示度的实验:用金属铋线和锑线构成结点,当电流沿某一方向流过结点时,结点上的水就会凝固成冰;如果反转电流方向,刚刚在结点上凝成的冰又会立即熔化成水.热电效应本身是可逆的.如果把楞次实验中的直流电源换成灯泡,当我们向结点供给热量,灯泡便会亮起来.尽管当时的科学界对佩尔捷和楞次的发现十分重视,但发现并没有很快转化为应用.这是因为,金属的热电转换效率通常很低.直到20世纪50年代,一些具有优良热电转换性能的半导体材料被发现,热电技术(热电制冷和热电发电)的研究才成为一个热门课题.目前,在室温附近使用的半导体制冷材料以碲化铋(Bi2Te3)合金为基础.通过掺杂制成P 型和N型半导体.如前所述,将一个P型柱和一个N型柱用金属板连接起来,便构成了半导体制冷器的一个基本单元,如果在结点处的电流方向是从N型柱流向P型柱,则结点将成为制冷单元的“冷头”(温度为Tc),而与直流电源连接的两个头将是制冷单元的“热端”(温度为Th). N型半导体的费米能级EF位于禁带的上部,P型的则位于禁带的下部.当二者连接在一起时,它们的费米能级趋于“持平”.于是,当电流从N型流向P型时(也就是空穴从N到P;电子从P到N),载流子的能量便会升高.因此,结点作为冷头就会从Tc端吸热,产生制冷效果.佩尔捷系数,其中是单位时间内在结点处吸收的热量,I是电流强度,Π的物理意义是,单位电荷在越过结点时的能量差.在热电材料研究中,更容易测量的一个相关参数是泽贝克(Seebeck)系数α,,其中T是温度.显然,α描述单位电荷在越过结点时的熵差.对于制冷应用来说,初看起来,电流越大越好,佩尔捷系数(或泽贝克系数)越大越好.不幸的是,实际非本征半导体的性质决定了二者不可兼得:电流大要求电导率σ高,而σ和α都是载流子浓度的函数.随着载流子浓度的增加,σ呈上升趋势,而α则下跌,结果ασ只可能在一个特定的载流子浓度下达到最大(注:由热激活产生的电子-空穴对本征载流子,对提高热电效益不起作用).半导体制冷单元的P型柱和N型柱,都跨接在Tc和Th之间.这就要求它们具有大的热阻.否则,将会加大Tc和Th间的漏热熵增,从而抵消从Tc端吸热同时向Th端放热的制冷效果.最终决定热电材料性能优劣的是组合参数,其中κ是材料的热导率.参数Z和温度T的乘积ZT无量纲,它在评价材料时更常用.目前,性能最佳的热电材料,其ZT值大约是1.0.为要使热电设备与传统的制冷或发电设备竞争,ZT值应该大于2.Glen Slack把上述要求归纳为“电子-晶体和声子-玻璃”.也就是说,好的热电材料应该具有晶体那样的高电导和玻璃那样的低热导.在长程有序的晶体中,电子以布洛赫波的方式运动.刚性离子实点阵不会使传导电子的运动发生偏转.电阻的产生来源于电子同杂质、晶格缺陷以及热声子的碰撞.因此,在完善的晶体中σ可以很大.半导体中的热导包含两方面的贡献:其一由载流子(假定是电子)的定向运动引起的(κe);其二是由于声子平衡分布集团的定向运动(κp).根据维德曼-弗兰兹定律,κe∝σ.人们不可能在要求大σ的同时,还要求小的κe.减小热导的潜力在于减小κp,它与晶格的有序程度密切相关:在长程有序的晶体中,热阻只能来源于三声子倒逆(umklapp)过程和缺陷、边界散射;在非晶态玻璃结构中,晶格无序大大限制了声子的平均自由程,从而添加了对声子的散射机制.因此,“声子-玻璃”的热导率κ可以很低.以无量纲优值系数ZT来衡量热电材料:BiSb系列适用于50—150K温区;Bi2Te3系列适用于250—500K;PbTe系列适用于500—800K;SiGe系列适用于1100—1300K.低温热电器件(T≤220K)主要用于冷却计算机芯片和红外探测器.高温热电设备可将太阳能和核能转化成电能,主要用于航天探测器和海上漂浮无人监测站的供电.最近,氟里昂制冷剂的禁用,为半导体制冷的发展提供了新的契机.1998年秋季在美国波士顿召开的材料研究学会(MRS)学术会议上,热电材料研究再一次成为讨论的热点.Brian Sales等研究了一类新型热电材料,叫作填隙方钴矿锑化物(filled skutterudite antimonides).未填隙时,材料的化学式是CoSb3(或Co4Sb12).晶体中每个Co4Sb12结构单元包含一个尺寸较大的笼形孔洞.如果将稀土原子(例如La)填入笼形孔洞,则化学式变为LaCo4Sb12.由于La原子处于相对宽松的空间内,它的振动幅值也较大.于是,在LaCo4Sb12中,Co4Sb12刚性骨架为材料的高电导提供了基础,而稀土La在笼中的振动加强了对声子的散射——减小了材料的热导.B.Sales 的工作朝着“电子-晶体和声子-玻璃”的方向迈出了第一步.高压(~2GPa)技术已经被用于改进热电材料的性能.如果在高压下观察到了母材料性能的改善,人们将可以通过化学掺杂的办法获得类似的结构,并将它用于常压条件下.ZrNiSn的σ和α都很高,但它的热导率κ并不低.或许可以通过加入第4或第5组元,增强对声子的“质量涨落散射”,达到减小热导的目的.准晶的结构复杂多变,具有“声子-玻璃”的性能.有关研究的重点是改善准晶的导电性能.将纳米金属(Ag)嵌入导电聚合物,当电流流过这种复合材料时,可以产生大的温度梯度.对此,还没有理论上的解释.有两种低维热电材料具有应用前景:CsBi4Te6实际上就是填隙的Bi2Te3;硒(Se)掺杂的HfTe5,在T<220K的温区,其泽贝克系数α远远超出了Bi2Te3.此外,薄膜、人工超晶格、纳米碳管、Bi纳米线和量子阱系统、类猫眼结构等都展现出了在改进热电材料性能方面的潜力.热电效应所谓的热电效应,是当受热物体中的电子(洞),因随着温度梯度由高温区往低温区移动时,所产生电流或电荷堆积的一种现象。
材料专业英文词汇

材料专业英文词汇(全)来源:李硕的日志化学元素(elements) 化学元素,简称元素,是化学元素周期表中的基本组成,现有113种元素,其中原子序数从93到113号的元素是人造元素。
物质(matter) 物质是客观实在,且能被人们通过某种方式感知和了解的东西,是元素的载体。
材料(materials) 材料是能为人类经济地、用于制造有用物品的物质。
化学纤维(man-made fiber, chemical fiber) 化学纤维是用天然的或合成的高聚物为原料,主要经过化学方法加工制成的纤维。
可分为再生纤维、合成纤维、醋酯纤维、无机纤维等。
芯片(COMS chip) 芯片是含有一系列电子元件及其连线的小块硅片,主要用于计算机和其他电子设备。
光导纤维(optical waveguide fibre ) 光以波导方式在其中传输的光学介质材料,简称光纤。
激光(laser) ( light amplification by stimulated emission of radiation 简写为:laser ) 激光是利用辐射计发光放大原理而产生的一种单色(单频率)、定向性好、干涉性强、能量密度高的光束。
超导(Superconduct) 物质在某个温度下电阻为零的现象为超导,我们称具有超导性质的材料为超导体。
仿生材料(biomimetic matorials) 仿生材料是模仿生物结构或功能,人为设计和制造的一类材料。
材料科学(materials science) 材料科学是一门科学,它从事于材料本质的发现、分析方面的研究,它的目的在于提供材料结构的统一描绘,或给岀模型,并解释这种结构与材料的性能之间的关系。
材料工程(materials engineering) 材料工程属技术的范畴,目的在于采用经济的、而又能为社会所接受的生产工艺、加工工艺控制材料的结构、性能和形状以达到使用要求。
材料科学与工程(materials science and engineering) 材料科学与工程是研究有关材料的成份、结构和制造工艺与其性能和使用性能间相互关系的知识及这些知识的应用,是一门应用基础科学。
结构功能一体化热电材料
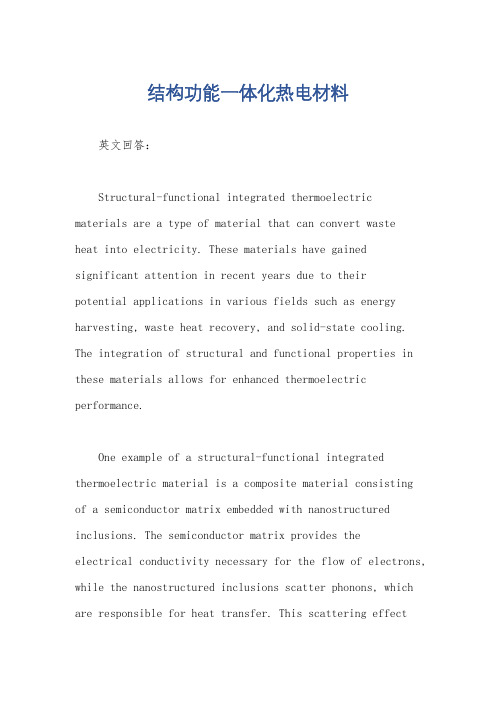
结构功能一体化热电材料英文回答:Structural-functional integrated thermoelectricmaterials are a type of material that can convert wasteheat into electricity. These materials have gainedsignificant attention in recent years due to theirpotential applications in various fields such as energy harvesting, waste heat recovery, and solid-state cooling. The integration of structural and functional properties in these materials allows for enhanced thermoelectric performance.One example of a structural-functional integrated thermoelectric material is a composite material consistingof a semiconductor matrix embedded with nanostructured inclusions. The semiconductor matrix provides theelectrical conductivity necessary for the flow of electrons, while the nanostructured inclusions scatter phonons, which are responsible for heat transfer. This scattering effectreduces the thermal conductivity of the material, leadingto an increased thermoelectric efficiency.Another example is the use of layered materials with a high thermoelectric figure of merit (ZT). These materials have a unique crystal structure that allows for efficient charge transport while maintaining low thermal conductivity. The layered structure provides a pathway for electrons to move through the material, while the weak interlayerbonding hinders phonon transport. This combination of properties results in a high ZT value, indicating a high thermoelectric performance.Structural-functional integrated thermoelectricmaterials can also be designed by controlling the composition and microstructure of the material. For instance, by introducing dopants or defects into the material, the electrical conductivity can be enhanced,while the thermal conductivity can be reduced. This control over the material's properties allows for the optimizationof thermoelectric performance.In addition to their thermoelectric properties,structural-functional integrated thermoelectric materials can also possess other desirable characteristics. For example, some materials exhibit mechanical flexibility, making them suitable for applications in wearable devicesor flexible electronics. Others may have good chemical stability, enabling their use in harsh environments. The integration of these additional functionalities further expands the potential applications of these materials.In conclusion, structural-functional integrated thermoelectric materials are a promising class of materials that can efficiently convert waste heat into electricity.By integrating structural and functional properties, these materials exhibit enhanced thermoelectric performance. The design and control of composition, microstructure, and additional functionalities contribute to their potential applications in various fields.中文回答:结构功能一体化热电材料是一种能够将废热转化为电能的材料。
热电材料

宇宙探测卫星的电源。利 用原子炉的热能发电
热电转换材料的研究现状
• 公认的热电材料有Bi2Te3,PbTe,SiGe等。这些 材料具有的ZT=1,变换效率超过10%的高性能。 但是有耐热,耐氧化性差,原料储藏少,对环境 有污染等问题。 • 热电材料要求导电率σ和Seebeck系数S要大,热 传导率要小。固体中输送电荷的电子同时输送热。 因为热电率对应单位载流子输送的熵,载流子密 度的增大可以使σ变大,但是S变小。也就是说, 决定热电性能三个物性保持互相约束的状态。 • 2007年Ohta(太田 ,名古屋大学)成功的合成 了SrTiO3化合物的人工超格子的2维电子气 (2DEG),得到了高性能的热电材料(ZT=2.4)
• 热电偶材料:热电偶种类很多,已研制的组合 热电偶材料近300种,已经标准化的15种,工 业上广泛应用的8种,有相应标推代号。
• 常用的热电偶的类别
热电偶类别 铂铑30-铂铑6 铂铑10-铂 镍铬-镍硅 镍铬-康铜 铂铑13-铂 代号 WRR WRP WRN WRE WRB 分度号 B S K E R 测温范围 0-1800℃ 0-1600℃ 0-1300℃ 0-800℃ 0-1600℃ 允许偏差限 ±0.25%t ±0.25%t ±0.75%t ±0.75%t ±0.25%t
• (2)温差电热效应 • 在热电回路中,与两接点间的温度差而引起的塞 贝克电动势相反,通电时,在回路中会引起两种 热效应,帕尔贴和汤姆逊热效应。前者出现在不 同的两个电极的接头处;后者一种导体的的两端 上。
帕尔贴效应
塞贝克,帕尔帖和汤姆逊称为热电三效应
汤姆逊效应
• 珀尔帖热效应
• 当直流电通过由两种不同导电材料所构成的回路时,接点 上将产生吸放热现象改变电流方向,吸放热也随之反向该 效应称之为珀尔帖效应。
热能与动力工程专业外文翻译、中英对照、英汉互译
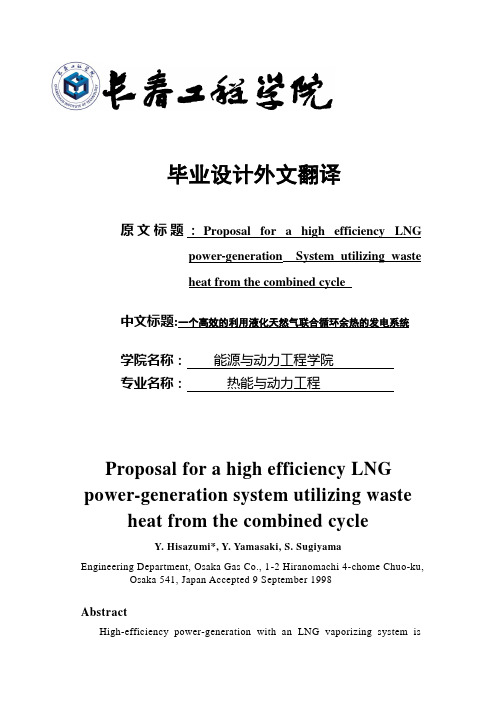
毕业设计外文翻译原文标题:Proposal for a high efficiency LNGpower-generation System utilizing wasteheat from the combined cycle中文标题:一个高效的利用液化天然气联合循环余热的发电系统学院名称:能源与动力工程学院专业名称:热能与动力工程Proposal for a high efficiency LNG power-generation system utilizing waste heat from the combined cycleY. Hisazumi*, Y. Yamasaki, S. SugiyamaEngineering Department, Osaka Gas Co., 1-2 Hiranomachi 4-chome Chuo-ku, Osaka 541, Japan Accepted 9 September 1998AbstractHigh-efficiency power-generation with an LNG vaporizing system isproposed: it utilizesthe LNG's cold energy to the best potential limit. This system can be applied to LNG vaporizers in gas companies or electric power companies and recovers the LNG's cold energy as electric power. The system consists of a Rankine cycle using a Freon mixture, natural-gas. Rankine cycle and a combined cycle with gas and steam turbines. The heat sources for this system are the latent heat from the steam-turbine's condenser and the sensible heat of exhaust gas from the waste-heat recovery boiler. In order to find out the optimal condition of the system, several factors, such as gas turbine combustion pressure, steam pressure, condensing temperature in combined cycle, composition of mixture Freon, and natural gas vaporizing pressure are evaluated by simulation. The results of these studies show that in the total system, about 400 kWh can be generated by vaporizing 1 ton of LNG, including about 60 kWh/LNG ton recovered from the LNG cold energy when supplying NG in 3.6 MPa.. About 8.2MWh can be produced by using 1 ton of LNG as fuel, compared with about 7 MWh by the conventional combined system. A net efficiency of over 53%HHV could be achieved by the proposed system. In the case of the LNG terminal receiving 5 million tons of LNG per year, this system can generate 240 MW and reduce the power of the sea water pump by more than 2MW. 1998 Elsevier Science Ltd. All rights reserved.1. IntroductionIn the fiscal year 1994, the amount of LNG imported to Japan reached about 43 million tons; of this 31 million tons were used as fuel for power generation. As shown in Fig. 1, about 20% of the LNG imported was used for power generation [2]. Fig. 2 shows the major LNG power generation systems now in operation and their outputs. Several commercial LNG power generation plants have been constructed since 1979, and their total output has reached approximately 73 MW. Among the new power-generation plants without CO2 emission, this value of 73 MW is second to the 450 MW input of geo-thermal power generation plants in Japan, with the exception of power generation by refuse incinerators, and is much larger compared with the 35 MW output of solar-power plants and the 14 MW output of wind-power stations.Table 1 shows the LNG power generation plants constructed in Japan. The economics of LNG power generation became worse as the appreciation of the yen madethe cost of energy kept constant but while raising the construction cost; the adoption of the combined cycle utilizing gas-turbine and steam turbine (hereafter called combined cycle) increased the gas send-out pressure and lowered the power output per ton of LNG. Therefore, no LNG powergeneration plants were constructed in the 1990s due to lower cost effectiveness of the systems.As for the thermal power plant using natural gas as fuel, the steam turbine produced only about 6 MWh of power output per ton of LNG. But recently, improvement in blade-cooling technology and materials of the gas turbine enabled a 1400℃class turbine to be designed and increased the combustion pressure up to 3 MPa. Therefore, as shown in Fig. 3, the heat efficiency of the combined cycle has been improved and the electrical output from 1 ton of LNG has reached about 7MWh.In this paper, a proposal is made for the high-efficiency LNG power generation system based on a new concept which fully utilizes the cold energy without discarding it into the sea. The system is composed of the combined cycle and the LNG power-generation plant.2. High-efficiency LNG power-generation system2.1. Basic componentsFig.4 shows the process flow diagram of the high-efficiency LNG power-generation system. This complex system consists of the combined cycle and the LNG power generation cycle. The combined cycle is composed of a gas turbine (GAS-T) and a steam turbine (ST-T) using natural gas (NG) as fuel, while the LNG power generation cycle is composed of a Freon (uorocarbon) mixture turbine (FR-T) and a natural-gas turbine (NG-HT, NG-LT) using the latent heat of condensation from the exhaust steam and the sensible heat of the exhaust gas as heat sources. The plate fin type heat exchanger can be used for the LNG/natural gas (LNG-CON) and LNG/ Freon mixture (FR-CON). The shell-and-tube type can be selected as exchangers for exhaust steam/natural gas (LNG-VAP),exhaust steam/Freon mixture(FR-VAP), and exhaust gas/natural gas (NG-SH) applications according to the operating conditions.Ice thickness on the surface of the heat-exchanger tubes becomes a problem as heat is exchanged between exhaust gas and cold natural gas or Freon mixture. The ice thickness can be estimated by the technology of heat transfer between LNG and sea water, thus enabling one to avoid blockages due to ice inside the tubes.In addition, stable and continuous send-out of gas is made possible by using a bypass system, even if turbines and pumps for the Freon mixture and natural gas circulating systems (FR-RP, LNG-RP) stop.2.2. Features of the systemThe practical use of the following existing technologies in combination shows the high feasibility of the proposed system:. Power generation using Freon or hydrocarbon type Rankine cycle,. Power generation by natural-gas direct expansion],. TRI-EX type vaporizer which vaporizes LNG by using an intermediate medium or vacuum type LNG vaporizer.The Freon mixture is made up of the HFC type, which is a fluorocarbon consisting of H, F, and C and has no adverse influence on the ozone layer; it enables reduction in exergy loss at the heat exchanger and increases itscirculating flow rate to be achieved.The effective recovery of cold exergy and pressure exergy is made possible by the combined system using natural gas and Freon mixture Rankine cycle.Fig. 5 shows the temperature-heat duty relation when vaporizing 1 kg of LNG in the system shown in Fig. 4. Separation of the condensed natural-gas in two sections enables an increase in the heat duty between Freon (FR) and LNG, and a reduction of difference in temperature of LNG and natural gas between the inlet and outlet of the heat exchanger.3. Evaluation of the characteristics of the proposed system3.1. Process simulationThe characteristics of this system were evaluated by using process simulator. The followings are the conditions used for the calculation:Effciencies of rotating machines LNG compositionGas turbine (GAS-T) 88% CH4 89.39%Steam turbine (ST-T) 85% C2H6 8.65%Natural-gas turbine (NG-HT, LT) 88% C3H8 1.55%Freon turbine (FR-T) 88% iC4H10 0.20%Air compressor (AIR-C) 85% nC4H10 0.15%LNG pump (LNG-MP, RP) 70% iC5H12 0.01%Freon pump (FR-RP) 70% N2 0.05%Natural gas gross heat-value: 10,510 kcal/Nm3AIR/NG flow ratio of gas turbine: 323.2. Effects of send-out pressure of the natural gasWhen natural-gas is sent out at 3.5 or 1.8 MPa, evaluations were made of the effects of send-out pressure of the LNG and change in superheating temperature of the natural gas on the total output of the high pressure (NG-HT) and the low pressure (NG-LT) natural-gas expansion-turbines. Fig. 6 shows the results of this calculation, where self consumption of power is calculated from the power, raising the pressure of the LNG up to the inlet pressure of the turbine minus the power required for the original send-out pressure. In both cases, the inlet pressure rise for the turbine causes an increase of self consumption power, but brings about a greater out-put. About 7 MPa of the inlet pressure of the turbine is appropriate considering the pressure tolerance of the heat exchangers.When the superheating temperature of the natural gas at the inlet to the turbine becomes high, the recovery of power increases, but the temperature of the exhaust gas from the outlet of the natural-gas super heater (NG-SH) declines, thus indicating that there is a limitation to superheating gas.3.3. Effects of combustion pressure of the gas turbineThe outputs of the gas turbine and the steam turbine, and the efficiency per gross heating value were evaluated by changing the combustion pressure of the gas turbine operating at 1300℃turbine-inlet temperature - see Fig. 7.If the combustion pressure of the gas turbine becomes high, the output of the gas turbine increases, but the output of the steam turbine decreases because the rise in combustion pressure causes a lowering of the exhaust-gas temperature at the outlet of the gas turbine and consequently a decline in the steam temperature at the inlet of the steam turbine. However, the overall efficiency of the turbines increases upon increasing the combustion pressure because the increment of gas-turbine output exceeds the decrement of steam turbine output. As a result, taking the pressure loss into account, it is appropriate to set the send-out pressure of the natural gas at the LNG terminal at 3.5 MPa.(FR-vap),3.4. Effects of Inlet pressure of the steam turbineFig. 8 shows the relations between the steam-turbines output and exhaust gas temperatures by changing the steam pressure in the range of 3-7 MPa. As the steam pressure increases, the output of the steam turbine rises and the temperature of the exhaust gases also increase. Besides, the power required for the water-supply pump increases with a rise in the steam pressure. Therefore, the current combined cycles operate at steam pressure of 7 MPa or more because the increment of the output of steam turbine exceeds the additional power required for the water-supply pump.3.5. Rankine cycle using a Freon-mixture refrigerant.The Freon refrigerant was selected from the HFC refrigerants on the basis of marketability, boiling point and freezing-point. Table 2 shows the physical properties of HFC Freon.When only HFC-23 is used as the medium, because of its low freezing-point it never freezes even if heat is exchanged between the LNG and HFC-23. But if HFC-23 is heated by the exhaust steam of the steam turbine, the pressure rises approximately up to the critical pressure. Therefore, the use of HFC-23 is not cost effective, because it is then necessary to set a high design pressure. To cope with this problem, we evaluated the compound refrigerant composed of HFC-134a (with high boiling point) and HFC-23.Fig. 9 shows saturated vapor pressure at various temperatures, the boiling point and the dew point at atmospheric pressure for mixtures of HFC-23 andHFC-134a of various compositions. The saturated pressure at each temperature rises with the increasing mole ratio of HFC-23: Hence, 40-45% of the mole ratio of HFC-23 is the optimal value considering the design pressure of the equipment.Fig. 10 shows the plots of the output of the Freon turbine versus the condensing temperature of the steam turbine when changing the composition of the HFC-23. In this figure, the turbine outlet pressure is determined in such a way that thedifference in temperature between the LNG and Freon mixture is not less than 5℃in the Freon condenser (FR-CON). The Freon turbine's inlet-pressure is set to the saturatedtemperature of the Freon mixture, i.e. less than 2℃from the steam-condensing temperature.This figure indicates that the output of the turbine scarcely correlates with the mole ratio of HFC-23. The higher the steam-condensing temperature becomes, the greater the output per ton of LNG the turbine produces, but in such a case, it is necessary to evaluate the system as a whole because more fuel is required, as described below. The result indicates that the optimal mole composition of HFC-23 and HFC-134a is 40%/60% considering both design pressure and the output of the turbine.3.6. Comprehensive evaluation from the viewpoint of the steam-condensing Temperature.As the dew point of the exhaust gas is 42℃, it is wise to set the exit temperature of the exhaust gas from the natural-gas super heater (NG-SH) to 80℃or more in order to prevent white smoke from the smoke stack. Table 3 shows the effect of the steam-condensing temperature on the generated output of the total system. The lower steam-condensing temperature brings about a higher efficiency of the total system, but also causes a lowering in the inlet temperature of natural-gas turbine. Therefore, it is appropriate to set the steam-condensing temperature at approximately 30℃.When the condensing temperature is 30C, the generated outputs per ton of LNG of the combined cycle and LNG power generation plant are 342.83 and67.55 kWh, respectively, resulting in 402.64 kWh of total generated output aftersubtracting the self-use power. As 48.94 kg of fuel is used for operating the system, the generated outputs of the combined cycle and the total system reach about 7 and 8.2 MWh, per ton of fuel respectively.3.7. Evaluation of exergyNatural-gas is liquefied at an LNG liquefaction terminal, with the consumption of about 380 kWh/LNG-ton: 1 ton of LNG having about 250 kWh of physical exergy as cold exergy and 13.5 MWh of chemical exergy. Fig. 11 shows the result of evaluating the exergy of the system shown in Fig. 4 under the optimal condition. The total output of Freon and natural gas turbines is 67.5 kWh, and the effective recovery percentage of cold exergy is 56%. As 90 kWh out of the pressure exergy can be recovered as output, about 157 kWh of net recovery can be obtained, which indicates the recovery percentage reaches about 63% for 250 kWh of LNG cold exergy. This conversion efficiency is higher than that achieved from chemical exergy to electric power.Most of the exergy loss occurs in the heat exchanger and the turbine, and in mixing with re-condensed LNG. As for the turbines, the loss of energy may be improved by using high-efficiency turbines. On the other hand, modification of the heat exchanger to reduce the energy loss may cause increased complexity of the system and is difficult to be done from the economic viewpoint. Though the recovery.percentage of cold energy in this system is low compared with the 80% in air-separation equipment, this system has the advantage of recovering a large amount of the available cold energy.4. ConclusionThe paper has proposed a high-efficiency LNG power generation system in combination with a combined-cycle power generation system fueled by natural-gas. The system utilizes LNG cold energy and it requires no sea water as a heat source.This system can be applied to LNG vaporization and send-out processes of gas companies or electric-power companies. The system recovers LNG coldenergy as an electric-power output without wasting it into sea water. The system consists of Rankine cycle with Freon mixture and a natural-gas Rankine cycle using the latent heat of exhaust steam from the steam turbine and the sensible heat of exhaust gas from the waste-heat recovery boiler. To improve the total efficiency of the system, a simulation was conducted to evaluate several factors, such as the composition of the Freon mixture, natural gas send-out pressure, as well as the combustion pressure steam inlet pressure, and steam-condensing temperature of the combined cycle. As a result, not less than 60 kWh/LNG-ton of output was generated even at a high natural-gas send-out pressure of 3.5 MPa. This value is considerably higher than the output generated at a LNG send-out pressure of 3 or 4 MPa, as given in Table 2.The system can produce about 400 kWh of net output when vaporizing 1 ton of LNG. While the conventional combined-cycle system in operation generates about 7 MWh when 1 ton of LNG is used as fuel, the system using the same amount of fuel generates about 8.2 MWh with a high degree of efficiency: a not-less-than 53% conversion efficiency was achieved per gross heat value.In the case of an LNG terminal receiving 5 million tons of LNG per year, this system can generate a power of about 240 MW when 600 t of LNG is used in an hour. With the elimination of about 24,000 tons per hour of sea water, which has been used for vaporizing 600 t/h of LNG in the conventional system, no less than 2 MW of electric power for operating sea water pumps can be saved.The proposed system emits no CO2, and can generate a large amount of electricity with high cost efficiency when incorporated into a combined cycle, with no use of sea water. Therefore, we consider that installation of this system is the one of the most favorable means of investment to put a new energy source or energy-saving equipment to practical use.To realize the full potential of this system, it is necessary to understand the heat characteristics of the Freon mixture, the icing and heat transfer characteristics of exhaust steam, the controllability of total system and the characteristics against partial load.References[1] The Center for Promotion of Natural gas Foundation. Research and development report of cold energy utilizing system, 1994[2] Japan's Energy and Economy Research Center. Energy and economy statistical data in 1995[3] Abe. Operating results and future prospect of a recent combined-cycle power generation plant. Thermal and Nuclear Power 1995;46(6):33-41[4] Maertens J. Design of Rankine cycles for power generation. Int. Refrig. 1986;9:137-43[5] Terada, Nakamoto. Power generation utilizing LNG cold. Thermal and Nuclear Power Generation 1986;37(10):66-71[6] Ooka, Ueda, Akasaka. Advanced LNG vaporizer and power generation utilizing LNG cold. Chemical Engineering 1981;45(3):187-90[7] Miura. The development of LNG vaporizer using vacuum steam heat (VSV). Journal of Japan Gas Society 1992;45:34-6[8] Nagai. Software-package and the usage. Chemical Equipment1994;August:31-7[9] Daikin Co. Ltd. Freon Data Sheet of HFC23一个高效的利用液化天然气联合循环余热的发电系统日本大阪541燃气有限公司工程部1-2平野町4肖梅中央谷,1998年9月概述本文提出了一个高效液化天然气气化发电系统,它是利用液化天然气冷能的最佳潜能极限。
毕业论文----半导体热电材料的应用及研究进展
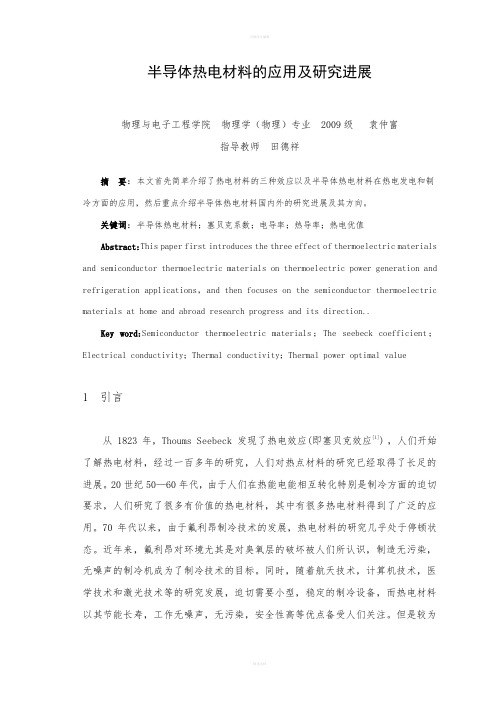
半导体热电材料的应用及研究进展物理与电子工程学院物理学(物理)专业 2009级袁仲富指导教师田德祥摘要:本文首先简单介绍了热电材料的三种效应以及半导体热电材料在热电发电和制冷方面的应用,然后重点介绍半导体热电材料国内外的研究进展及其方向。
关键词:半导体热电材料;塞贝克系数;电导率;热导率;热电优值Abstract:This paper first introduces the three effect of thermoelectric materials and semiconductor thermoelectric materials on thermoelectric power generation and refrigeration applications,and then focuses on the semiconductor thermoelectric materials at home and abroad research progress and its direction..Key word:Semiconductor thermoelectric materials;The seebeck coefficient;Electrical conductivity;Thermal conductivity;Thermal power optimal value1 引言从1823年,Thoums Seebeck 发现了热电效应(即塞贝克效应[1]),人们开始了解热电材料,经过一百多年的研究,人们对热点材料的研究已经取得了长足的进展。
20世纪50—60年代,由于人们在热能电能相互转化特别是制冷方面的迫切要求,人们研究了很多有价值的热电材料,其中有很多热电材料得到了广泛的应用。
70年代以来,由于氟利昂制冷技术的发展,热电材料的研究几乎处于停顿状态。
近年来,氟利昂对环境尤其是对臭氧层的破坏被人们所认识,制造无污染,无噪声的制冷机成为了制冷技术的目标。
金属材料名称中英文解释对照(最全,最完整)

加热炉 heating furnace, reheating furnace火焰炉 flame furnace环形炉 circular rotating furnace退火炉 annealing furnace, annealer真空退火炉 vacuum annealing furnace连续酸洗机组 pickle line processor带钢不间断地通过几个酸性槽进行酸性。
轧辊 roll挤压辊 extrusion roll辊道 roll table延伸辊道 extension roller table芯棒 mandrel卫板 guard导板 guide带卷箱 coil box活套 loop组织性能与测试穿晶断裂 transgranular fracture穿过多晶体材料的晶体内部发生的断裂晶间断裂 intergranular fracture:沿着晶粒界间发生的断裂解理断裂 cleavage fracture:沿着给定的晶面—解理面发生的断裂(是穿晶断裂的方式之一)。
剪切断裂 shear fracture:沿着最大剪应力的作用面发生的断裂。
疲劳断裂 fatigue fracture:在低于材料的屈服强度的反复或交变应力作用下发生的断裂。
延迟断裂 delayed fracture:金属遭受本不足以直接引起断裂的静应力但经过一段时间却发生了断裂。
断口 fracture surface:金属件的断裂面或破裂面。
断口形貌学 fractography杯锥断口 cup cone fracture:圆柱形拉伸试件于延性断裂(韧性断裂)后,一侧的断口呈杯状,另一侧的断口呈锥状,两者合称杯锥断口。
丝状断口 silky fracture:表面光滑、有丝绸光泽的极细晶粒断口。
纤维状断口 fibrous fracture:金属或合金的延性足够大,在断裂前晶粒被拉长了从而总体看上去象许多纤维的断口。
层状断口 lamination fracture:所含非金属夹杂物在轧制过程中被延展成薄层的金属材料垂直于轧制面的断口。
- 1、下载文档前请自行甄别文档内容的完整性,平台不提供额外的编辑、内容补充、找答案等附加服务。
- 2、"仅部分预览"的文档,不可在线预览部分如存在完整性等问题,可反馈申请退款(可完整预览的文档不适用该条件!)。
- 3、如文档侵犯您的权益,请联系客服反馈,我们会尽快为您处理(人工客服工作时间:9:00-18:30)。
Thermoelectric Properties of n -Type Bi 2Te 3/PbSe 0.5Te 0.5Segmented Thermoelectric MaterialSEJIN YOON,1JUN-YOUNG CHO,1HYUN KOO,1SUNG-HWAN BAE,1SEUNGHYUN AHN,1GWI RANG KIM,1JIN-SANG KIM,2and CHAN PARK 1,3,41.—Department of Materials Science and Engineering,Seoul National University,Daehak-dong,Gwanak-gu,Seoul,Republic of Korea.2.—Electronic Materials Research Center,Korea Institute of Science and Technology,Wolgok 2-dong,Seongbuk-gu,Seoul,Republic of Korea.3.—Research Institute of Advanced Materials,Seoul National University,Daehak-dong,Gwanak-gu,Seoul,Republic of Korea.4.—e-mail:pchan@snu.ac.krTo investigate the effects of segmentation of thermoelectric materials on performance levels,n -type segmented Bi 2Te 3/PbSe 0.5Te 0.5thermoelectric material was fabricated,and its output power was measured and compared with those of Bi 2Te 3and PbSe 0.5Te 0.5.The two materials were bonded by diffusion bonding with a diffusion layer that was $18l m thick.The electrical conductivity,Seebeck coefficient,and power factor of the segmented Bi 2Te 3/PbSe 0.5Te 0.5sample were close to the average of the values for Bi 2Te 3and PbSe 0.5Te 0.5.The output power of Bi 2Te 3was higher than those of PbSe 0.5Te 0.5and the segmented sample for small D T (300K to 400K and 300K to 500K),but that of the segmented sample was higher than those of Bi 2Te 3and PbSe 0.5Te 0.5when D T exceeded 300K (300K to 600K and 300K to 700K).The output power of the segmented sample was about 15%and 73%higher than those of the Bi 2Te 3and PbSe 0.5Te 0.5samples,respectively,when D T was 400K (300K to 700K).The efficiency of thermoelectric materials for large temperature differences can be enhanced by segmenting materials with high performance in different temperature ranges.Key words:Thermoelectric material,segmented thermoelectric material,Bi 2Te 3,Pb(Se,Te),output powerINTRODUCTIONMany studies have focused on improving the energy conversion efficiency of thermoelectric materials for their potential use in power-generation and cooling systems.The efficiency of a thermoelectric material is characterized by its dimensionless figure of merit [zT =(S 2r T )/j ,where S is the Seebeck coefficient,r is the electrical conductivity,and j denotes the thermalconductivity].1The upper limit of the efficiency (g ¼g c ffiffiffiffiffiffiffiffiffiffiffiffiffiffiffi1þzT p À1 =ffiffiffiffiffiffiffiffiffiffiffiffiffiffiffi1þzT p þ1Àg c h i ,whereg c =D T /T hot is the Carnot efficiency,and zT is the average zT over the temperature range)is determined by the temperature difference D T ,2,3which means that better energy conversion can be expected with the use of a larger D T .Most thermoelectric materials,how-ever,have high zT over a very limited temperature range,indicating that most thermoelectric materials cannot effectively utilize such a large D T .High ther-moelectric energy conversion efficiency can be obtained when a large D T can be used,which can only be realized by using a thermoelectric material with high zT value across a broad temperature range.Materials with large average zT values over a wide temperature range have to be used to convert large amounts of energy from a large D T .Connection of materials with high zT values in different tempera-ture ranges,forming a segmented thermoelectric(Received May 10,2013;accepted October 14,2013;published online November 27,2013)Journal of ELECTRONIC MATERIALS,Vol.43,No.2,2014DOI:10.1007/s11664-013-2869-4Ó2013TMS414material,can lead to improvement of the efficiency in a wide temperature range.Most research on thermoelectric materials has focused on improving the zT value of a single material by optimizing the carrier concentration with dopants and/or by using low-dimensional structures such as quantum dots and superlattic-es.4–11The zT values of such thermoelectric mate-rials with low-dimensional structures have been significantly improved compared with those of bulk thermoelectric materials.8,11Thermoelectric mate-rials with a low-dimensional structure,however, have mainly been fabricated in the form of thin films or nanowires,for instance,which are not appropriate for use in large-scale energy conversion systems with a large temperature difference. Given that the thermoelectric properties(S,r,j)of materials vary with temperature,Snyder et al.3,12 suggested that different thermoelectric materials could be segmented or cascaded together to improve their efficiency for a large temperature difference. Recently,many research groups have reported calculations and experimental data for segmented thermoelectric materials with improved perfor-mance.Kuznetsov et al.2used various amount of Te and SbI3as dopants to control the carrier concen-tration of Bi2Te3,connecting these materials to improve efficiency from8.8%to10%at D T=200K. Cui reported results for segmented p-type FeSi2/ Bi2Te3,showing1.4times more output power than FeSi2at D T=485K.13Zeng et al.14,15reported that the output power of a thermoelectric module of 16916segmented legs consisting of Bi2Te3/ ErAs:(InGaAs)1Àx(InAlAs)x was6.3W when the heat source was set to610K and the cooling water was kept at285K.Oh fabricated p-type(Bi,Sb)2Te3/ (Pb,Sn)Te by hot-pressing,showing,at a D T value of 320K,output power of$72mW,while(Bi,Sb)2Te3 and(Pb,Sn)Te showed63.9mW and26mW,respec-tively.16Recent studies of segmented thermoelectric materials have shown improved efficiency of seg-mented thermoelectric materials compared with nonsegmented ones,as mentioned above.Detailed understanding of the effects of different fabrication methods and interface properties of segmented materials on the thermoelectric properties will help to improve the efficiency further.In this work,to investigate the effects of segmen-tation of thermoelectric materials on their perfor-mance,an n-type segmented thermoelectric material consisting of Bi2Te3(highest zT at$400K)and PbSe0.5Te0.5(highest zT at$700K)was fabricated by spark plasma sintering(SPS)of Bi2Te3and PbSe0.5Te0.5powders prepared by mechanical alloy-ing.Quantitative elemental analyses were performed by means of wavelength-dispersive spectrometer (WDS)measurements at the interface to investigate the diffusion of the constituent elements.Output powers for various D T conditions(100K,200K, 300K,and400K)and the thermoelectric properties of the segmented Bi2Te3/PbSe0.5Te0.5sample were measured and compared with those of Bi2Te3and PbSe0.5Te0.5made by SPS.EXPERIMENTAL PROCEDURES Sample PreparationElemental Te,Bi,Pb,and Se(>99.999%)powders were weighed according to the stoichiometric com-positions of Bi2Te3and PbSe0.5Te0.5,and charged into a stainless-steel(SS)vial with SS balls under Ar atmosphere.SS balls with diameters of2mm and8mm were used with ball-to-powder weight ratio of10:1.Mechanical alloying of the powders was carried out using high-energy ball milling at 250rpm for20h.Contamination of the powders during the high-energy ball milling process was checked by analyzing the elements present in the powder using an inductively coupled plasma mass spectrometer.The prepared powders were then sintered by SPS. Approximately7g of each powder was packed into a carbon die with diameter of10mm and sintered under vacuum(<200mTorr)at400°C for10min under uniaxial pressure of50MPa.To fabricate the segmented sample,about3.5g Bi2Te3powder was charged into the carbon die and then pressed under 10MPa of uniaxial pressure,followed by charging and pressing of PbSe0.5Te0.5powder under the same conditions as for Bi2Te3.The green body consisting of Bi2Te3and PbSe0.5Te0.5was then spark plasma sintered(SPSed)using the same pressure,temper-ature,and sintering time as the nonsegmented samples.Figure1a and b show an image of the fab-ricated sample and a schematic of the fabrication method of the segmented sample,respectively.Each sample prepared by SPS was machined into bar-type (3mm,3mm,and10mm)and disk-type(1mm and 10mm)samples for further measurements. Characterization of the SamplesTo identify the phases present at each processing step,h–2h x-ray diffraction(XRD,D-8Advance; Bruker)with Cu K a radiation was performed for all powders and sintered samples.WDS quantitative elemental analysis was carried out to investigate the diffusion of elements across the interface of the segmented sample.The electrical conductivity and Seebeck coefficient were measured using a ZEM-2 instrument(Ulvac).Measurements were performed at intervals of50°C from room temperature to 400°C.The temperature difference was kept at 10°C,20°C,and30°C to measure the Seebeck coef-ficient.The relative density was measured by Archimedes’method.The output power of each sample was measured in a vacuum chamber under various D T conditions(D T=100K,200K,300K, and400K)by heating one side of the sample while the other side was in direct contact with a coolingThermoelectric Properties of n-Type Bi2Te3/PbSe0.5Te0.5Segmented Thermoelectric Material415block (300K).During the measurement of the seg-mented sample,Bi 2Te 3and PbSe 0.5Te 0.5were in contact with the cooling block and the heater,respectively.RESULTS AND DISCUSSIONFigure 2shows the XRD patterns of the powders after mechanical alloying and the SPSed samples of Bi 2Te 3and PbSe 0.5Te 0.5.The diffraction peaks were compared with those in the published powder dif-fraction files:PDF 01-082-0358(ICDD,1993)and PDF 03-065-8019(ICDD,1969).The peak positions of the powders and the SPSed samples were iden-tical to those of the PDF data of Bi 2Te 3and PbSe 0.5Te 0.5,indicating that no second phase was formed in the sample during the mechanical alloy-ing or SPS process.Broad peaks can be observed in Fig.2b,e,as the mechanical alloying is accompa-nied by a decrease in the powder size and the occurrence of strain.Grain growth and strain release during the sintering process can lead to a large decrease in the full-width at half-maximum of the diffraction peaks of SPSed samples (Fig.2c,f)compared with those of the powders (Fig.2b,e).To analyze the diffusion of atoms through the interface of the segmented Bi 2Te 3/PbSe 0.5Te 0.5sample,quantitative elemental analysis was per-formed by WDS.The atomic percentages of Bi,Pb,Se,and Te were measured every 2l m across the segmented interface;these results are shown in Fig.3.Pb and Se diffuse into Bi 2Te 3and Bi diffuses into PbSe 0.5Te 0.5to form a diffusion layer at the interface.This is similar to diffusion bonding of bulk materials at high temperature and pressure.17,18The length of the diffusion layer across the interface was about 18l m,much smaller than that reported by Oh,which was 350l m.16These different lengths of the diffusion layer could result from the different sintering conditions applied,which were 10min by SPS at 400°C in this work and 1h by hot pressing at 400°C for the result reported by Oh.The composi-tion of the diffusion layer is different from those of the materials at each side,allowing the diffusion layer to have different thermoelectric properties from the two end materials,which could affect the total efficiency of the sample.Investigation of the thermoelectric properties of the diffusion layer and its effect on the performance of the segmented sample could lead to further optimization of the thermoelectric properties of such segmented ther-moelectricmaterials.Fig.1.(a)Fabricated segmented Bi 2Te 3/PbSe 0.5Te 0.5sample and (b)schematic of the fabrication method of the segmented Bi 2Te 3/PbSe 0.5Te 0.5sample by spark plasmasintering.Fig.2.PDF data of (a)Bi 2Te 3and (d)PbSe 0.5Te 0.5,and XRD pat-terns of (b)the Bi 2Te 3powder,(c)the Bi 2Te 3spark-plasma-sintered sample,(e)the PbSe 0.5Te 0.5powder,and (f)the PbSe 0.5Te 0.5spark-plasma-sinteredsample.Fig.3.WDS data of the segmented Bi 2Te 3/PbSe 0.5Te 0.5sample.Yoon,Cho,Koo,Bae,Ahn,G.R.Kim,J.-S.Kim,and Park416The electrical conductivity and Seebeck coefficient were measured for all three sintered samples at various temperatures in air.The temperature dependences of the electrical conductivity and See-beck coefficient are presented in Fig.4a and b,respectively.The resulting electrical conductivity values for the Bi 2Te 3and PbSe 0.5Te 0.5samples werelower than those reported by Zhao et al.19and Li et al.,20whose samples were fabricated by methods similar to that used in this work.The low electrical conductivity of the samples could result from the low relative densities of the Bi 2Te 3(95.2%)and PbSe 0.5Te 0.5(94.8%)samples compared with the reported relative density of Bi 2Te 3of 98.5%.19This difference in the electrical conductivity can be explained in terms of the effective medium theory (EMT)which provides the relationship between the relative density and the electrical conductivity as r =[(3f À1)r 0]/2,where f is the fraction of the material except the pores and r 0is the electrical conductivity of the material without any pores.21The Seebeck coefficients of Bi 2Te 3and PbSe 0.5Te 0.5were similar to the reported values.19,20The power factor of each sample was calculated from the elec-trical conductivity and Seebeck coefficient,as shown in Fig.4c.The Bi 2Te 3and PbSe 0.5Te 0.5samples showed their highest power factor at 425K and 625K,respectively.The electrical conductivity,Seebeck coefficient,and power factor of the seg-mented Bi 2Te 3/PbSe 0.5Te 0.5sample were close to the average of the values for the nonsegmented samples.Figure 5shows the maximum output power of the Bi 2Te 3,PbSe 0.5Te 0.5,and segmented Bi 2Te 3/PbSe 0.5Te 0.5samples for various D T conditions.The temperature of the cold side was kept at 300K by cooling water,and the hot side of the samplewasFig.4.Temperature dependence of (a)electrical conductivity,(b)Seebeck coefficient,and (c)powerfactor.Fig.5.Output power of the Bi 2Te 3,PbSe 0.5Te 0.5,and segmented Bi 2Te 3/PbSe 0.5Te 0.5samples with temperature differences across the samples from 100K to 400K.Thermoelectric Properties of n -Type Bi 2Te 3/PbSe 0.5Te 0.5Segmented Thermoelectric Material 417heated by a local heater.The output power of the Bi2Te3sample was higher than that of the PbSe0.5Te0.5 and segmented Bi2Te3/PbSe0.5Te0.5samples when the D T value was lower than200K,but that of the seg-mented Bi2Te3/PbSe0.5Te0.5sample was higher than the other samples when D T exceeded300K.The out-put power of the Bi2Te3,PbSe0.5Te0.5,and segmented Bi2Te3/PbSe0.5Te0.5samples was38.8mW,26.0mW, and45.3mW,respectively,when D T was400K.The output power of the segmented sample was about15% and73%higher than that of the Bi2Te3and PbSe0.5Te0.5sample,respectively,at a D T value of 400K.The output power of the segmented sample was improved compared with those of the nonsegmented samples for large D T.Optimizing the length of the segmented materials and controlling the diffusion at the interface could lead to further improvement of the performance of segmented thermoelectric materials at large D T.CONCLUSIONSTo investigate the effects of segmentation of thermoelectric materials on performance levels,a segmented thermoelectric material was fabricated, and its output power was measured and compared with those of the nonsegmented materials.In this study,n-type Bi2Te3and PbSe0.5Te0.5,having their highest zT values at about400K and700K, respectively,were used to make the segmented thermoelectric material.The n-type segmented Bi2Te3/PbSe0.5Te0.5thermoelectric material was fabricated by SPS of a green body consisting of a stacked structure of Bi2Te3and PbSe0.5Te0.5.The two materials were bonded by diffusion bonding with a diffusion layer of$18l m.The electrical conductivity,Seebeck coefficient,and power factor of the segmented Bi2Te3/PbSe0.5Te0.5sample were near the average of the values of the two nonseg-mented materials.The output power of Bi2Te3was higher than those of the PbSe0.5Te0.5and segmented samples for small D T(300K to400K and300K to 500K),but the output power of the segmented sample was higher compared with those of Bi2Te3 and PbSe0.5Te0.5when D T exceeded300K(300K to 600K and300K to700K).The output power of the segmented sample was approximately15%and73% higher than those of the Bi2Te3and PbSe0.5Te0.5 samples,respectively,when D T was400K(300K to700K).The results of this work highlight that seg-mented thermoelectric materials can offer improved efficiency over a wide temperature range,and that optimization of the length of each segment and proper control of the diffusion layer could further increase the efficiency of the thermoelectric mate-rial for large D T.ACKNOWLEDGEMENTSThis research was supported by the Converging Research Center Program through the Ministry of Sci-ence,ICT and Future Planning,Korea(2013K000170) and by the Power Generation&Electricity Delivery of the Korea Institute of Energy Technology Evaluation and Planning(KETEP)grant funded by the Korea government Ministry of Knowledge Economy(No. 20111020400090).REFERENCES1. D.W.Rowe,Thermoelectrics Handbook:Macro to Nano(Boca Raton:CRC/Taylor&Francis,2006).2.V.L.Kuznetsov,L.A.Kuznetsova,A.E.Kaliazin,and D.M.Rowe,J.Mater.Sci.37,14(2002).3.G.J.Snyder,Appl.Phys.Lett.84,13(2004).4.G.Zhang and B.W.Li,Nanoscale2,7(2010).5.G.J.Snyder and E.S.Toberer,Nat.Mater.7,2(2008).6.L.D.Hicks and M.S.Dresselhaus,Phys.Rev.B47,19(1993).7.L.D.Hicks,T.C.Harman,X.Sun,and M.S.Dresselhaus,Phys.Rev.B53,16(1996).8.R.Venkatasubramanian, E.Siivola,T.Colpitts,and B.O’Quinn,Nature413,6856(2001).9.T.C.Harman,P.J.Taylor,M.P.Walsh,and Forge,Science297,5590(2002).10. A.I.Boukai,Y.Bunimovich,J.Tahir-Kheli,J.K.Yu,W.A.Goddard III,and J.R.Heath,Nature451,7175(2008).11.R.Venkatasubramanian,Phys.Rev.B61,4(2000).12.G.J.Snyder and T.S.Ursell,Phys.Rev.Lett.91,14(2003).13.J.L.Cui,Mater.Lett.57,24–25(2003).14.G.Zeng,J.H.Bahk,J.E.Bowers,H.Lu,J.M.O.Zide,A.C.Gossard,R.Singh,Z.Bian,A.Shakouri,S.L.Singer,W.Kim,and A.Majumdar,J.Electron.Mater.37,12(2008).15.G.Zeng,J.H.Bahk,J.E.Bowers,H.Lu,A.C.Gossard,S.L.Singer, A.Majumdar,Z.X.Bian,M.Zebarjadi,and A.Shakouri,Appl.Phys.Lett.95,8(2009).16.T.S.Oh,J.Electron.Mater.38,7(2009).17.P.L.Ratnaparkhi and J.M.Howe,Acta Metall.Mater.42,3(1994).18.P.He,J.H.Zhang,R.L.Zhou,and X.Q.Li,Mater.Charact.43,5(1999).19.L.D.Zhao,B.P.Zhang,J.F.Li,M.Zhou,and W.S.Liu,Phys.B400,1–2(2007).20.J.Q.Li,S.P.Li,Q.B.Wang,L.Wang,F.S.Liu,and W.Q.Ao,pd.509,13(2011).21. C.W.Nan,Prog.Mater Sci.37,1(1993).Yoon,Cho,Koo,Bae,Ahn,G.R.Kim,J.-S.Kim,and Park418。