乙醇-水精馏塔设计报告
乙醇及水的精馏塔设计

乙醇及水的精馏塔设计
首先,需要确定乙醇和水的混合物的物理性质。
乙醇和水的沸点非常
接近,因此在设计精馏塔时,必须考虑适当的操作条件,以便有效地分离
乙醇和水。
在精馏塔的设计过程中,首先需要选择适当的塔型。
常见的乙醇和水
的分离塔包括简单塔和精馏塔。
简单塔由一个塔板组成,可用于低温分离,而精馏塔则包含多个塔板,可以提供更高的分离效率。
其次,需要考虑精馏塔的高度。
精馏塔的高度决定了分离的效率。
通
常情况下,精馏塔的高度越高,分离效率越高。
然而,高塔会增加成本和
能耗,因此需要在效率和经济性之间做权衡。
此外,需要选择适当的回流比。
回流比是指流经塔板上部的液体返回
到塔底的比例。
适当的回流比可以提高分离效率,但过高的回流比可能导
致能耗过高。
还需要考虑乙醇和水的进料浓度。
通常情况下,浓度较高的进料可以
提高分离效果,但也会增加能耗。
因此,需要找到一个经济和效率之间的
平衡点。
在设计乙醇和水的精馏塔时,还需要考虑传热和传质方面的问题。
特
别是在塔内的塔板上,需要考虑适当的传热和传质设备,以确保有效的分离。
最后,需要进行塔的热力学计算和模拟,以评估设计的可行性和最佳
性能。
这可以通过使用软件模拟工具,如Aspen Plus、CHEMCAD等来完成。
综上所述,乙醇及水的精馏塔设计需要考虑塔的类型、高度、回流比、进料浓度等因素。
通过综合考虑这些关键参数,可以设计出经济、高效的
乙醇和水精馏塔,满足工业生产的需求。
乙醇和水的精馏塔设计

乙醇和水的精馏塔设计精馏是一种分离液体混合物中组分的常用方法,可通过蒸馏分离甲醇和水的混合物。
对于乙醇和水的精馏塔设计,需要考虑一系列参数和流程,包括进料组成、操作压力、图形塔塔板、冷凝器设计、降低能量消耗等。
以下是一个基本的乙醇和水的精馏塔设计方案。
1.塔板设计在乙醇和水的精馏塔设计中,决定了塔板数的重要参数是所需的乙醇纯度。
一般来说,纯度要求越高,所需的塔板数就越多。
可使用的常用塔板设计方法有McCabe-Thiele方法和Ponchon-Savarit方法。
2.冷凝器设计冷凝器用于冷凝乙醇蒸汽,使其凝结成液体后下降到下部分的收集器中。
冷凝器设计需要考虑的重要参数包括进料温度、出料温度、乙醇和水的蒸汽压力和流量等。
一般来说,选择多管冷凝器比单管冷凝器更适合于高效的冷凝过程。
3.降低能量消耗乙醇和水的精馏过程中,能量消耗是一个重要的考虑因素。
为了降低能量消耗,可以引入热回收系统,如热交换器,将高温的废气中的热能回收使用。
此外,也可以考虑采用较低的操作压力,通过降低汽化温度来减少所需的加热能量。
4.控制塔板温度在乙醇和水的精馏塔设计中,控制各个塔板的温度非常重要,以确保塔板能够正常工作。
一种常见的温度控制方法是在塔板上设置温度传感器,并通过自动化控制系统调节冷凝器的冷却剂流量来控制塔板温度。
5.回流比的选择回流比是决定乙醇和水精馏塔效率的重要因素。
回流比的选择应根据塔板的数量、损失和乙醇纯度等因素来合理决定。
一般来说,较高的回流比可以提高纯度,但同时也会增加能源消耗。
6.热平衡以上是一个基本的乙醇和水的精馏塔设计方案。
根据实际情况和具体需求,还需要根据实际的进料组成、产量、纯度和环境要求等因素进行调整。
乙醇_水精馏塔设计说明

乙醇_水精馏塔设计说明
1.设备选型
2.工艺流程
(1)加热阶段:将乙醇_水混合物加热到沸点,使其部分汽化,进入下一个阶段。
(2)蒸馏阶段:乙醇和水在塔内进行汽液两相的分离,高纯度的乙醇向上升腾,低纯度的水向下流动。
(3)冷凝阶段:将高纯度的乙醇气体冷凝成液体,便于收集和储存。
(4)分离阶段:将冷凝后的液体进一步分离,得到纯度较高的乙醇和水。
3.操作参数
(1)温度控制:加热阶段需要将混合物加热到适当的沸点,通常控制在80-100摄氏度。
而在蒸馏阶段,控制塔顶和塔底的温度差异,有助于提高分离效果。
(2)压力控制:塔的进料和出料口通常需要控制一定的压力,以保证流量的稳定。
(3)流量控制:塔内液体的流速对塔的操作效果有较大影响,需保持适当的流速,通常通过调节塔顶和塔底的流量或液位来实现。
4.塔的结构及内件设计
乙醇_水精馏塔的结构包括塔壳、进料装置、分离器、冷凝器、再沸器、集液器等。
其中,塔内需要配置一些内件,如填料和板式塔板等,以
提高传质和传热效果。
填料可采用金属或塑料材料,板式塔板可选用槽式、波纹式等不同形式。
通过合理配置和设计这些内件,提高乙醇_水分离效果。
综上,乙醇_水精馏塔的设计需要综合考虑设备选型、工艺流程、操
作参数以及塔的内部结构等因素。
通过合理的设计和选择,可以实现高效
分离乙醇和水的目的。
乙醇-水精馏实验报告

竭诚为您提供优质文档/双击可除乙醇-水精馏实验报告篇一:精馏法分离乙醇—水报告化工基础实验报告精馏法分离乙醇—水体系姓名:李伟峰学号:系别:_____化学工程系______专业:石油加工生产技术年级:20XX级同组人:_赖仪凤,周春丹,陈茂飞,李伟勇指导教师:_____陈少峰,梁燕,________20XX年11月13一、实验目的(1)熟悉板式塔的结构及精馏流程;(2)理论联系实际,掌握精馏塔的操作;(3)学会精馏塔塔效率的测定方法。
(4)了解填料精馏塔的基本结构,熟悉精馏的工艺流程。
(5)掌握精馏过程的基本操作及调节方法。
(6)掌握测定塔顶、塔釜溶液浓度的实验方法。
(7)掌握精馏塔性能参数的测定方法,并掌握其影响因素。
(8)掌握用图解法求取理论板数的方法。
二.实验方法本实验采用精馏法对乙醇—水混合液进行分离提纯,通过对全回流和部分回流条件下各参数的测定,进而由图解法求取其理论塔板数,确定出最适宜的精馏分离操作条件,并采用等板高度(heTp)来表示其分离能力。
1.实验装置与流程本实验装置的主体设备是填料精馏塔,配套的有加料系统、回流系统、产品出料管路、残液出料管路、进料泵和一些测量、控制仪表。
精馏装置由板式精馏塔主体(包括塔釜、塔身和塔顶冷凝器)、加料系统,产品贮槽及测量仪表所组成。
本精馏装置所采用的精馏塔为筛板塔,塔内径为50mm,塔板15块,板间距为100mm,开孔率4-6%、降液管管径φ14*2;塔釜以2支1kw的电加热棒进行加热,其中一支是常加热,而另一支通过自耦变压器可在0~1kw范围内调节;塔顶为盘管式冷凝器,上升蒸汽在盘管外冷凝,冷凝液流至分配器储槽,一部分回流至塔内,一部分作为产品输出。
料液由泵输送,经转子流量计计量后加入塔内。
本实验料液为乙醇溶液,由进料泵打入塔内,釜内液体由电加热器加热汽化,经填料层内填料完成传质传热过程,进入盘管式换热器管程,壳层的冷却水全部冷凝成液体,再从集液器流出,一部分作为回流液从塔顶流入塔内,另一部分作为产品馏出,进入产品贮罐;残液经釜液转子流量计流入釜液贮罐。
乙醇-水精馏塔化工设计9
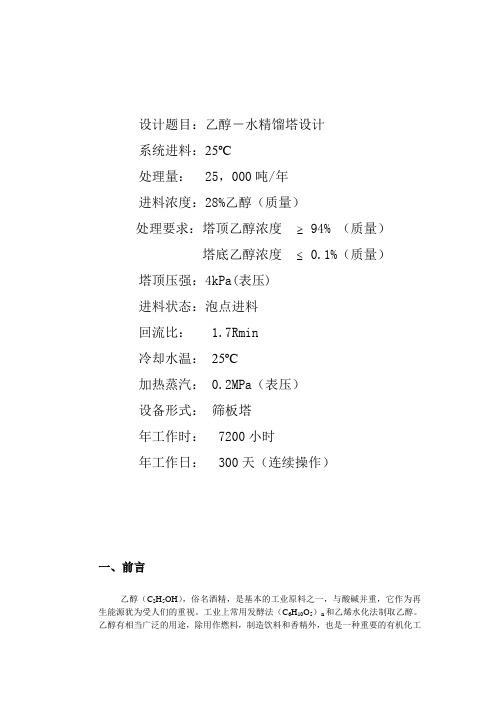
设计题目:乙醇-水精馏塔设计系统进料:25ºC处理量: 25,000吨/年进料浓度:28%乙醇(质量)处理要求:塔顶乙醇浓度≥ 94% (质量)塔底乙醇浓度≤ 0.1%(质量)塔顶压强:4kPa(表压)进料状态:泡点进料回流比: 1.7Rmin冷却水温:25ºC加热蒸汽: 0.2MPa(表压)设备形式:筛板塔年工作时: 7200小时年工作日: 300天(连续操作)一、前言乙醇(C2H5OH),俗名酒精,是基本的工业原料之一,与酸碱并重,它作为再生能源犹为受人们的重视。
工业上常用发酵法(C6H10O5)n和乙烯水化法制取乙醇。
乙醇有相当广泛的用途,除用作燃料,制造饮料和香精外,也是一种重要的有机化工原料,如用乙醇制造乙酸、乙醚等;乙醇又是一种有机溶剂,用于溶解树脂,制造涂料。
众所周知,在医药卫生方面,乙醇作为消毒杀菌剂而造福于人类。
人类餐饮饭桌上饮用各种酒品,乙醇也是其中不可或缺的组成部分,如:啤酒含3%~5%,葡萄酒含6%~20%,黄酒含8%~15%,白酒含50%~70%(均为体积分数)。
据有关资料表明,乙醇对人体具有营养价值。
现在,乙醇成为了一种新型替代能源-乙醇汽油。
按照我国的国家标准,乙醇汽油是用90%的普通汽油与10%的燃料乙醇调和而成。
它可以有效改善油品的性能和质量,降低一氧化碳、碳氢化合物等主要污染物排放。
它不影响汽车的行驶性能,还减少有害气体的排放量。
乙醇汽油作为一种新型清洁燃料,是目前世界上可再生能源的发展重点,符合我国能源替代战略和可再生能源发展方向,技术上成熟安全可靠,在我国完全适用,具有较好的经济效益和社会效益。
乙醇精馏是生产乙醇中极为关键的环节,是重要的化工单元。
其工艺路线是否合理、技术装备性能之优劣、生产管理者及操作技术素质之高低,均影响乙醇生产的产量及品质。
工业上用发酵法和乙烯水化法生产乙醇,单不管用何种方法生产乙醇,精馏都是其必不可少的单元操作。
乙醇—水溶液精馏塔设计

乙醇-水溶液连续精馏塔设计目录1.设计任务书 (3)2.英文摘要前言 (4)3.前言 (4)4.精馏塔优化设计 (5)5.精馏塔优化设计计算 (5)6.设计计算结果总表 (22)7.参考文献 (23)8.课程设计心得 (23)精馏塔设计任务书一、设计题目乙醇—水溶液连续精馏塔设计二、设计条件1.处理量: 15000 (吨/年)2.料液浓度: 35 (wt%)3.产品浓度: 93 (wt%)4.易挥发组分回收率: 99%5.每年实际生产时间:7200小时/年6. 操作条件:①间接蒸汽加热;②塔顶压强:1.03 atm(绝对压强)③进料热状况:泡点进料;三、设计任务a) 流程的确定与说明;b) 塔板和塔径计算;c) 塔盘结构设计i. 浮阀塔盘工艺尺寸及布置简图;ii. 流体力学验算;iii. 塔板负荷性能图。
d) 其它i. 加热蒸汽消耗量;ii. 冷凝器的传热面积及冷却水的消耗量e) 有关附属设备的设计和选型,绘制精馏塔系统工艺流程图和精馏塔装配图,编写设计说明书。
乙醇——水溶液连续精馏塔优化设计前言乙醇在工业、医药、民用等方面,都有很广泛的应用,是很重要的一种原料。
在很多方面,要求乙醇有不同的纯度,有时要求纯度很高,甚至是无水乙醇,这是很有困难的,因为乙醇极具挥发性,也极具溶解性,所以,想要得到高纯度的乙醇很困难。
要想把低纯度的乙醇水溶液提升到高纯度,要用连续精馏的方法,因为乙醇和水的挥发度相差不大。
精馏是多数分离过程,即同时进行多次部分汽化和部分冷凝的过程,因此可使混合液得到几乎完全的分离。
化工厂中精馏操作是在直立圆形的精馏塔内进行的,塔内装有若干层塔板或充填一定高度的填料。
为实现精馏分离操作,除精馏塔外,还必须从塔底引入上升蒸汽流和从塔顶引入下降液。
可知,单有精馏塔还不能完成精馏操作,还必须有塔底再沸器和塔顶冷凝器,有时还要配原料液预热器、回流液泵等附属设备,才能实现整个操作。
浮阀塔与20世纪50年代初期在工业上开始推广使用,由于它兼有泡罩塔和筛板塔的优点,已成为国内应用最广泛的塔型,特别是在石油、化学工业中使用最普遍。
乙醇水精馏塔实验实验报告
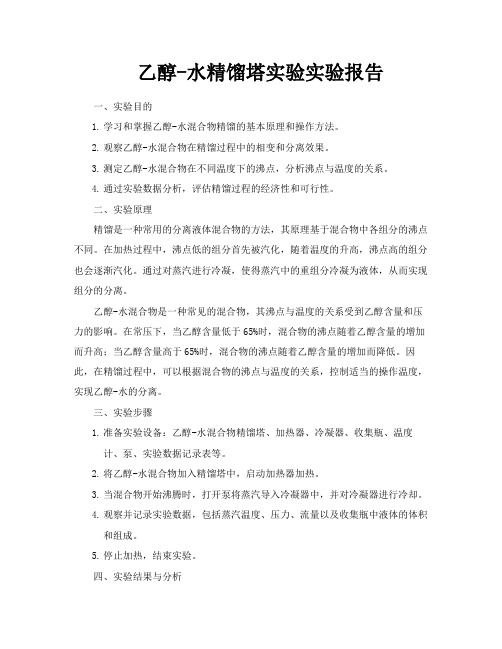
乙醇-水精馏塔实验实验报告一、实验目的1.学习和掌握乙醇-水混合物精馏的基本原理和操作方法。
2.观察乙醇-水混合物在精馏过程中的相变和分离效果。
3.测定乙醇-水混合物在不同温度下的沸点,分析沸点与温度的关系。
4.通过实验数据分析,评估精馏过程的经济性和可行性。
二、实验原理精馏是一种常用的分离液体混合物的方法,其原理基于混合物中各组分的沸点不同。
在加热过程中,沸点低的组分首先被汽化,随着温度的升高,沸点高的组分也会逐渐汽化。
通过对蒸汽进行冷凝,使得蒸汽中的重组分冷凝为液体,从而实现组分的分离。
乙醇-水混合物是一种常见的混合物,其沸点与温度的关系受到乙醇含量和压力的影响。
在常压下,当乙醇含量低于65%时,混合物的沸点随着乙醇含量的增加而升高;当乙醇含量高于65%时,混合物的沸点随着乙醇含量的增加而降低。
因此,在精馏过程中,可以根据混合物的沸点与温度的关系,控制适当的操作温度,实现乙醇-水的分离。
三、实验步骤1.准备实验设备:乙醇-水混合物精馏塔、加热器、冷凝器、收集瓶、温度计、泵、实验数据记录表等。
2.将乙醇-水混合物加入精馏塔中,启动加热器加热。
3.当混合物开始沸腾时,打开泵将蒸汽导入冷凝器中,并对冷凝器进行冷却。
4.观察并记录实验数据,包括蒸汽温度、压力、流量以及收集瓶中液体的体积和组成。
5.停止加热,结束实验。
四、实验结果与分析1.实验数据记录表(1)随着加热时间的延长,混合物的温度逐渐升高,蒸汽流量逐渐减小。
这是由于混合物中的水分逐渐蒸发,乙醇含量增加,导致混合物的沸点升高。
同时,随着压力的降低,蒸汽流量也会减小。
(2)随着蒸汽流量的变化,收集瓶中液体的体积逐渐增加。
这是由于蒸汽中的重组分冷凝为液体,被收集在收集瓶中。
同时,随着加热时间的延长,收集瓶中液体的乙醇含量逐渐增加。
这是由于乙醇的沸点较低,更容易蒸发并冷凝在收集瓶中。
(3)在实验过程中,我们可以观察到精馏塔顶部的蒸汽温度较高,而底部的蒸汽温度较低。
分离乙醇水的精馏塔设计
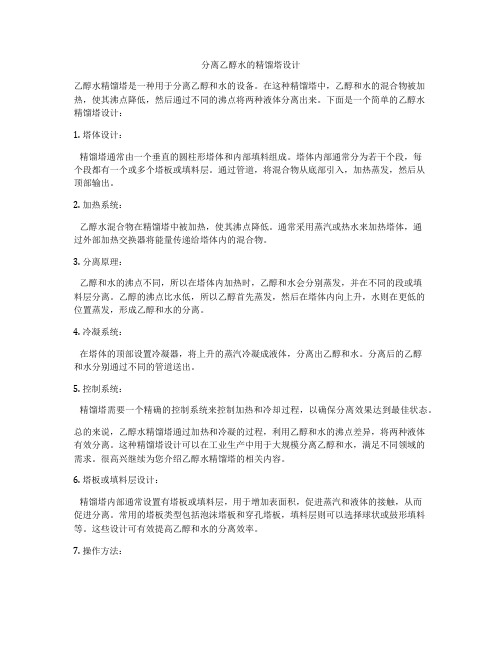
分离乙醇水的精馏塔设计乙醇水精馏塔是一种用于分离乙醇和水的设备。
在这种精馏塔中,乙醇和水的混合物被加热,使其沸点降低,然后通过不同的沸点将两种液体分离出来。
下面是一个简单的乙醇水精馏塔设计:1. 塔体设计:精馏塔通常由一个垂直的圆柱形塔体和内部填料组成。
塔体内部通常分为若干个段,每个段都有一个或多个塔板或填料层。
通过管道,将混合物从底部引入,加热蒸发,然后从顶部输出。
2. 加热系统:乙醇水混合物在精馏塔中被加热,使其沸点降低。
通常采用蒸汽或热水来加热塔体,通过外部加热交换器将能量传递给塔体内的混合物。
3. 分离原理:乙醇和水的沸点不同,所以在塔体内加热时,乙醇和水会分别蒸发,并在不同的段或填料层分离。
乙醇的沸点比水低,所以乙醇首先蒸发,然后在塔体内向上升,水则在更低的位置蒸发,形成乙醇和水的分离。
4. 冷凝系统:在塔体的顶部设置冷凝器,将上升的蒸汽冷凝成液体,分离出乙醇和水。
分离后的乙醇和水分别通过不同的管道送出。
5. 控制系统:精馏塔需要一个精确的控制系统来控制加热和冷却过程,以确保分离效果达到最佳状态。
总的来说,乙醇水精馏塔通过加热和冷凝的过程,利用乙醇和水的沸点差异,将两种液体有效分离。
这种精馏塔设计可以在工业生产中用于大规模分离乙醇和水,满足不同领域的需求。
很高兴继续为您介绍乙醇水精馏塔的相关内容。
6. 塔板或填料层设计:精馏塔内部通常设置有塔板或填料层,用于增加表面积,促进蒸汽和液体的接触,从而促进分离。
常用的塔板类型包括泡沫塔板和穿孔塔板,填料层则可以选择球状或鼓形填料等。
这些设计可有效提高乙醇和水的分离效率。
7. 操作方法:在精馏过程中,需要注意控制加热温度、冷却温度、流速等参数,以保证所得到的乙醇和水的纯度和分离效率。
为此,通常采用自动化控制系统,监测和调整各项参数,提高操作的稳定性和效率。
8. 安全措施:在乙醇水精馏过程中,需要注意防止乙醇的挥发和着火,避免发生危险。
因此,需要设置相应的通风排气系统,并且保证设备的密封性良好。
- 1、下载文档前请自行甄别文档内容的完整性,平台不提供额外的编辑、内容补充、找答案等附加服务。
- 2、"仅部分预览"的文档,不可在线预览部分如存在完整性等问题,可反馈申请退款(可完整预览的文档不适用该条件!)。
- 3、如文档侵犯您的权益,请联系客服反馈,我们会尽快为您处理(人工客服工作时间:9:00-18:30)。
(封面)XXXXXXX学院乙醇-水精馏塔设计报告题目:院(系):专业班级:学生姓名:指导老师:时间:年月日目录第一章设计任务书 (1)第二章设计方案的确定及流程说明 (2)2.1 塔类型的选择 (2)2.2 塔板形式的选择 (3)2.3 设计方案的确定 (4)第三章塔的工艺计算 (6)3.1物料衡算 (6)3.2理论板数,板效率及实际板数的计算 (10)3.3平均参数、塔径、塔高的计算 (14)第四章塔板结构设计 (21)4.1塔板结构尺寸的确定 (21)4.2塔板流体力学计算 (23)第五章塔板负荷性能图 (28)5.1 精馏段 (28)5.2提馏段 (30)第六章附属设备设计 (33)6.1产品冷却器 (33)6.2接管 (34)6.3其他 (35)第七章设计方案的比较与讨论 (36)第一章设计任务书一、设计题目:乙醇—水精馏塔本设计是根据生产实际情况并加以一定程度的简化而提出的。
二、设计任务及条件1.进精馏塔料液含乙醇25%(质量),其余为水。
2.产品乙醇含量不得低于94%(质量)。
3.残液中乙醇含量不得高于0.1%(质量)。
4.生产能力为日产(24小时)50吨94%的乙醇产品5.操作条件:精馏塔顶压力:4KPa(表压)进料状况:泡点进料回流比:R/R min=1.6单板压降:不大于667 Pa加热蒸汽压力:101.3kPa(表压)6.设备形式:浮阀塔7.厂址:天津地区第二章设计方案的确定及流程说明2.1 塔类型的选择塔设备的种类很多,按操作压力可分为常压塔、加压塔和减压塔;按塔内气液相接触构件的结构形式又可分为板式塔和填料塔两大类。
板式塔和填料塔各有适用的环境,具体板式塔和填料塔性能的比较可见下表1:表1 板式塔和精馏塔的比较类型板式塔填料塔结构特点每层板上装配有不同型式的气液接触元件或特殊结构,如筛板、泡罩、浮阀等;塔内设置有多层塔板,进行气液接触塔内设置有多层整砌或乱堆的填料,如拉西环、鲍尔环、鞍型填料等散装填料,格栅、波纹板、脉冲等规整填料;填料为气液接触的基本元件操作特点气液逆流逐级接触微分式接触,可采用逆流操作,也可采用并流操作设备性能空塔速度(亦即生产能力)高,效率高且稳定;压降大,液气比的适应范围大,持液量大,操作弹性小大尺寸空塔气速较大,小尺寸空塔气速较小;低压时分离效率高,高压时分离效率低,传统填料效率较低,新型乱堆及规整填料效率较高;大尺寸压力降小,小尺寸压力降大;要求液相喷淋量较大,持液量小,操作弹性大制造与维修直径在600mm以下的塔安装困难,安装程序较简单,检修清理容易,金属材料耗量大新型填料制备复杂,造价高,检修清理困难,可采用非金属材料制造,但安装过程较为困难适用场合处理量大,操作弹性大,带有污垢的物料处理强腐蚀性,液气比大,真空操作要求压力降小的物料在本设计中,之所以选用板式塔,塔底为直接蒸汽加热,板式塔塔底无需再添加气体初始分布装置,且塔顶和进料口位置无需添加液体初始分布装置;另一方面,塔板所需费用要远低于规整填料,正式是因为板式塔的结构简单,造价较低两大优点,导致具有比较大的经济优势。
2.2 塔板形式的选择塔板形式很多,常见的有泡罩塔板、筛孔塔板、浮阀塔板、网孔塔板、垂直塔板、无降液管塔板(常见的有穿流式栅板、穿流式筛板)、导向筛板、多降液管塔板和斜喷型塔板(常见的有舌型塔板、斜孔塔板、浮动舌型塔板、浮动喷射塔板)等。
泡罩塔板是工业上应用最早的塔板,它由升气管及泡罩构成。
泡罩安装在升气管的顶部,分圆形和条形两种,以前者使用较广。
泡罩有φ80、φ100和φ150mm三种尺寸,可根据塔径大小选择。
泡罩下部周边开有很多齿缝,齿缝一般为三角形、矩形或梯形。
泡罩在塔板上为正三角形排列。
优点是操作弹性较大,液气比范围较大,不易堵塞,适用于处理各种物料,操作稳定可靠。
缺点是结构复杂,造价高;板上液层厚,塔板压降大,生产能力及板效率较低,除特殊需要,一般不选用。
筛孔塔板简称筛板,其结构特点是在塔板上开有许多均匀小孔,孔径一般为3~8mm。
筛孔在塔板上为正三角形排列。
塔板上设置溢流堰,使板上能保持一定厚度的液层。
优点是结构简单,造价低;板上液面落差小,气体压降低,生产能力较大;气体分散均匀,传质效率高。
缺点是筛孔易堵塞,不宜处理易结焦、粘度大的物料。
浮阀塔板的结构特点是在塔板上开有若干个阀孔,每个阀孔装有一个可上下浮动的阀片,阀片本身连有几个阀腿,插入阀孔后将阀腿底脚拨转90°,以限制阀片升起的最大高度,并防止阀片被气体吹走。
阀片周边冲出几个略向下弯的定距片,当气速很低时,由于定距片的作用,阀片与塔板呈点接触而坐落在阀孔上,可防止阀片与板面的粘结。
优点是结构简单、制造方便、造价低;塔板开孔率大,生产能力大;由于阀片可随气量变化自由升降,故操作弹性大;因上升气流水平吹入液层,汽液接触时间较长,故塔板效率较高。
缺点是处理易结焦、高粘度的物料时,阀片易与塔板粘结;在操作过程中有时会发生阀片脱落或卡死等现象,使塔板效率和操作弹性降低。
表2 塔板性能的比较塔盘类型优点缺点适用场合泡罩板浮阀板较成熟、操作稳定结构复杂、造价高、塔板阻力大、处理能力小特别容易堵塞的物系效率高、操作范围宽浮阀易脱落分离要求高、负荷变化大筛板结构简单、造价低、塔板效率高易堵塞、操作弹性较小分离要求高、塔板数较多舌型板结构简单且阻力小操作弹性窄、效率低分离要求较低的闪蒸塔表3 主要塔板性能的量化比较塔板类型生产能力塔板效率操作弹性压降结构成本泡罩板 1.0 1.051复杂1浮阀板 1.2-1.3 1.1~1.290.6一般0.7-0.9筛板 1.2-1.4 1.130.5简单0.4-0.5舌型板 1.3-1.5 1.130.8简单0.5-0.6本设计采用浮阀塔板,因为浮阀具有生产能力大、操作弹性宽、塔板效率高等优点。
本设计采用技术成熟的F1型浮阀,F1型浮阀已有系列标准,各种设计数据完善,便于设计和对比。
F1型浮阀分为轻阀(代表符号Q)和重阀(代表符号Z)两种。
轻阀采用厚度为1.5mm 的薄板冲压制成,质量约25g;重阀采用厚度为2mm薄板冲压制成,质量约为33g。
一般重阀应用广泛,轻阀泄漏量大,只有在要求压降小的时候(如减压蒸馏)才采用。
本设计采用应用最广泛的F1型重阀。
2.3 设计方案的确定(1)装置设备:包括精馏塔、原料预热器、塔顶全凝器、釜残液冷却器、馏出液冷却器、产品贮罐、塔顶回流泵(一开一备)、进料泵(一开一备)、低压蒸汽透平等设备。
(2)操作压力:乙醇-水采用常压精馏就能够实现初步分离要求,考虑实际情况,塔顶压力设置至4kPa(表压)。
(3)进料热状况:精馏塔一般采用泡点进料,其优势在于将物料温度加热到泡点所需要的蒸汽品味,相比塔釜加热所需热品味要低很多,可以用较低温流股等预热,有利于节省总能耗;泡点进料能平衡精馏段和提馏段的气液相负荷,维持塔内气相负荷相对稳定,塔径较接近,无需变径;泡点进料易达气液平衡,塔板效率高,理论板数相对于过热和过冷进料要少;此外,泡点进料为液体进料,进料接管管径较小,开孔对塔壁影响小。
(4)塔釜加热方式:直接蒸汽加热使用与含有水且水为重组分的物系。
因此,对于乙醇-水的混合物,可以采用直接蒸汽加热的方式,这样只需在塔釜内安装鼓泡管,省去一个再沸器,且可利用压力较低的蒸汽来进行加热,操作费用和设备费用均可降低。
但由于蒸汽冷凝水的稀释作用,使残液的轻组分浓度降低,所需的塔板数略有增加。
而在本设计中,乙醇-水物系低浓度时的相对挥发度很大,所增加的塔板数并不多,采用直接蒸汽加热是合理的。
(5)塔顶冷凝方式:考虑到塔顶乙醇为最终产物,冷凝所需能耗不大,因此本设计采用全凝器,以便于准确的控制回流比和塔器操作的稳定。
(6)塔板溢流方式:溢流方式与降液管布置方式有关,常见的布置方式有U形流、单溢流、双溢流及阶梯式双溢流。
U形流液体流经长,可以提高板效率,但液面落差大,适用于小塔及液体流量小的场合。
单溢流流经较长,塔板效率较高,结构简单,加工方便,适用于直径小于2.2m的塔。
双溢流液体流动路径短,可降低液面落差,但塔板结构复杂,板面利用率低,一般用于直径大于2m的塔。
阶梯式双溢流可在不缩短液体流经的情况下减小液面落差,但是结构复杂,适用于塔径很大、液流量很大的特殊场合。
结合本设计的精馏塔尺寸,选用单溢流方式。
(7)精馏塔装置流程:见附图生产工艺流程图。
第三章塔的工艺计算3.1物料衡算1.计算各流股的摩尔分数水的摩尔质量:M w=18.015kg/kmol 乙醇的摩尔质量:M o=46.069kg/mol 因此:进料摩尔分数:x F=0.2546.069⁄0.2546.069⁄+0.7518.015⁄=0.1153馏出液摩尔分数:x D=0.9446.69⁄0.9446.069⁄+0.0618.015⁄=0.8597釜液摩尔分数:x W=0.00146.069⁄⁄⁄=0.00042.计算各流股平均摩尔质量:进料:M F=46.069×0.1153+18.015×(1−0.1153)=21.25k g/k mol 馏出液:M D=46.069×0.8597+18.015×(1−0.8597)=42.13kg/kmol 釜液:M W=46.069×0.0004+18.015×(1−0.0004)=18.03kg/kmol3.计算最小回流比:查资料得常压下乙醇—水系统的t-x-y数据如下:表4 常压下乙醇—水系统的t-x-y数据根据数据作出乙醇—水系统的汽液平衡相图可知,该曲线存在凹陷段,因此不能用一般的方法求其最小回流比,需要通过作切线确定。
图1 最小回流比求解图初步估计切点在曲线凹段,因此用origin将曲线后半段10个点进行拟合图2 最小回流比切线图得其方程:y =3.5787x4−10.0208x3+10.9311x2−4.8680x+1.3801(1)求导得y,=14.3150x3−30.0625x2 −9.7360+1.3801(2)对于过点(x D,x D)的切线,设其切点为(x0,y0),满足方程(2),则该曲线在曲线上点(x0,y0)的切线方程为y=y0,(x−x0)+y0(3)将(2)代入方程(3),x D=85.97,并于(1)联立,解得:x0=0.7686 y0=0.7982切线纵截距:b=0.2787b=x DR min+1算得R min=2.08514.确定回流比根据生产任务:R R min=1.6⁄因此R=1.6×R min=1.6×2.0851=3.33615.确定精馏段、提馏段操作线方程精馏段操作线方程:y=RR+1x+1R+1x D=3.33613.3361+1x+13.3361+1×0.8597=0.7694x+0.2042(4)饱和液体进料,所以q线方程为:q=x F=0.1153 (5)则由(4)、(5)得q线与精馏段操作线的交点为:x q=0.1153 y q=0.4573连接点(x q,y q)、(x W,0)即得提馏段操作线方程:y =3.9781x−0.00166.进行物料衡算直接蒸汽加热精馏塔全塔物料衡算:F+V0=D+W(6)其中:F—进料流量,kmol/s;V0—蒸汽流量,kmol/s;D—馏出液流量,kmol/s;W—釜液流量,kmol/s;根据生产任务,D=50t/d=50×100041.985×24=49.44kmol/h根据恒摩尔流假设,物料衡算式如下:D=1000×503600×24×M D=1000×503600×24×42.13=0.0137 kmol/s(7)乙醇的物料衡算:Fx F=Dx D+Wx W(8)由(6)、(7)、(8)解得F=0.05185kmol/s W=0.03810kmol/sV0=D+L=D+D×R=0.0137+0.0137×3.3361=0.0594kmol s⁄=213.86kmol h⁄3.2理论板数,板效率及实际板数的计算1.理论板数确定根据汽液平衡相图以及精馏段、提馏段操作线方程作梯级图由图得理论板数:N T=26其中:精馏段22块板,提馏段4块板图3 图解理论板图4 图解理论板(塔顶局部放大)图5 图解理论板(塔底局部放大)2. 塔顶温度计算对非理想物系,有修正的拉乌尔定律可得:P =γA x A p A 0+γB (1−x A )p B 0(9)式中,p A 0,p B 0为纯组分A ,B 的饱和蒸汽压;γA ,γB 为组分A,B 的活度系数。