海洋钻井平台防腐技术的研究
关于海洋工程结构与船舶防腐技术措施分析

关于海洋工程结构与船舶防腐技术措施分析海洋工程结构和船舶是在海洋环境中运行和工作的,因此防腐技术是非常重要的。
下面将对海洋工程结构和船舶防腐技术措施进行分析。
海洋工程结构包括钻井平台、海底管道、海上风力发电设施等。
由于它们长期在海洋环境中受到潮湿、盐分、温度变化和海水的腐蚀,而且海洋环境条件复杂,所以必须采取有效的防腐技术措施。
针对海洋工程结构的防腐技术主要有以下几种:1. 防腐涂层:采用防腐涂料对结构物进行涂覆,以阻隔结构物与海水的接触,减少结构物的腐蚀。
常见的防腐涂层材料有环氧树脂、聚氨酯、煤沥青等,这些涂层具有良好的耐腐蚀性能和耐海水侵蚀能力。
2. 金属防腐:采用金属的防腐技术,如热浸镀锌、热镀铝等,对结构物表面进行处理,增加金属表面对海水的抵抗能力。
金属防腐技术适用于钢结构和铁制结构,可以有效地延长结构物的使用寿命。
3. 材料选择:在海洋工程结构的设计和施工过程中,选择具有良好耐腐蚀性的材料,如不锈钢、合金材料等。
这些材料具有较强的耐腐蚀性能,能够有效地抵抗海水的侵蚀。
船舶作为在海洋中长时间运行的大型设备,也需要采取防腐技术措施来延长其使用寿命和保证航行安全。
船舶防腐技术主要包括以下几种:1. 防腐涂层:船舶在制造过程中常常使用防腐涂层对船体进行防腐处理。
防腐涂层可以有效隔绝海水和船体的接触,减少船体的腐蚀。
常见的船舶涂层包括船底防污涂料、船舶外壳涂料等。
2. 阳极保护:船舶使用金属阳极对船体进行保护。
阳极通常由锌或铝等金属材料制成,它们能够吸收腐蚀电流,从而减少船体的腐蚀。
阳极保护是一种被广泛应用于船舶的防腐技术。
3. 尽量避免海水侵蚀:船舶在停泊期间,特别是长时间停泊时,应该尽量避免船体与海水的接触,如使用船舶停泊设备,在船底加装船垫或使用船坞进行船体检修等措施。
海洋工程结构和船舶防腐技术措施非常重要。
通过采用适当的防腐技术措施,可以有效地保护海洋工程结构和船舶的表面,减少腐蚀损失,延长使用寿命,保证运行安全。
海洋石油平台工艺管线防腐技术进展
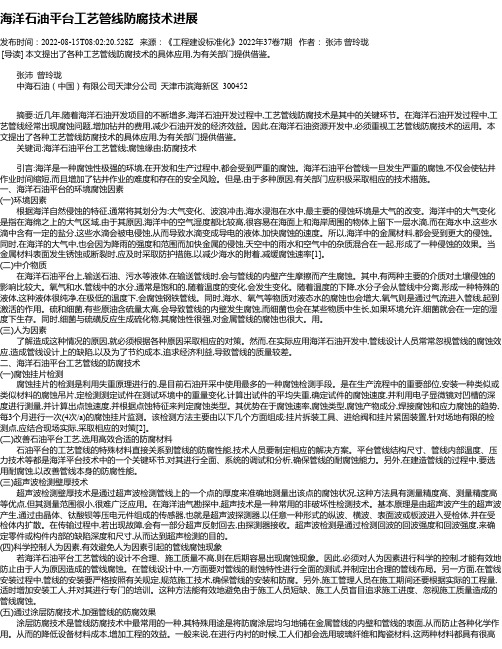
海洋石油平台工艺管线防腐技术进展发布时间:2022-08-15T08:02:20.528Z 来源:《工程建设标准化》2022年37卷7期作者:张沛曾玲珑[导读] 本文提出了各种工艺管线防腐技术的具体应用,为有关部门提供借鉴。
张沛曾玲珑中海石油(中国)有限公司天津分公司天津市滨海新区 300452摘要:近几年,随着海洋石油开发项目的不断增多,海洋石油开发过程中,工艺管线防腐技术是其中的关键环节。
在海洋石油开发过程中,工艺管线经常出现腐蚀问题,增加钻井的费用,减少石油开发的经济效益。
因此,在海洋石油资源开发中,必须重视工艺管线防腐技术的运用。
本文提出了各种工艺管线防腐技术的具体应用,为有关部门提供借鉴。
关键词:海洋石油平台工艺管线;腐蚀缘由;防腐技术引言:海洋是一种腐蚀性极强的环境,在开发和生产过程中,都会受到严重的腐蚀。
海洋石油平台管线一旦发生严重的腐蚀,不仅会使钻井作业时间缩短,而且增加了钻井作业的难度和存在的安全风险。
但是,由于多种原因,有关部门应积极采取相应的技术措施。
一、海洋石油平台的环境腐蚀因素(一)环境因素根据海洋自然侵蚀的特征,通常将其划分为:大气变化、波浪冲击,海水浸泡在水中,最主要的侵蚀环境是大气的改变。
海洋中的大气变化是指在海绵之上的大气区域,由于其原因,海洋中的空气湿度都比较高,很容易在海面上和海岸周围的物体上留下一层水滴,而在海水中,这些水滴中含有一定的盐分,这些水滴会被电侵蚀,从而导致水滴变成导电的液体,加快腐蚀的速度。
所以,海洋中的金属材料,都会受到更大的侵蚀。
同时,在海洋的大气中,也会因为降雨的强度和范围而加快金属的侵蚀,天空中的雨水和空气中的杂质混合在一起,形成了一种侵蚀的效果。
当金属材料表面发生锈蚀或断裂时,应及时采取防护措施,以减少海水的附着,减缓腐蚀速率[1]。
(二)中介物质在海洋石油平台上,输送石油、污水等液体,在输送管线时,会与管线的内壁产生摩擦而产生腐蚀。
海洋工程中的防腐技术研究

海洋工程中的防腐技术研究海洋,占据着地球表面的大部分区域,蕴含着丰富的资源和巨大的经济潜力。
随着人类对海洋的探索和开发不断深入,海洋工程逐渐成为了重要的领域。
然而,海洋环境极为苛刻,具有高湿度、高盐度、强腐蚀性等特点,这给海洋工程设施带来了严峻的腐蚀挑战。
为了确保海洋工程的安全、可靠和长期运行,防腐技术的研究和应用显得尤为关键。
一、海洋环境对工程设施的腐蚀影响海洋环境中的腐蚀因素众多。
首先是海水本身,其富含的氯离子能够穿透金属表面的氧化膜,引发点蚀和缝隙腐蚀。
其次,海洋生物的附着会形成局部缺氧环境,加速腐蚀进程。
再者,海浪的冲击、海流的冲刷以及温度和压力的变化都会对工程设施造成机械损伤,使得腐蚀更容易发生。
在海洋工程中,常见的受腐蚀设施包括海上石油平台、港口码头、船舶以及海底管道等。
这些设施一旦遭受严重腐蚀,不仅会影响其正常功能,还可能导致泄漏、倒塌等重大安全事故,造成巨大的经济损失和环境污染。
二、常见的海洋防腐技术1、涂层防护涂层防护是应用最为广泛的防腐方法之一。
通过在金属表面涂覆一层具有良好耐腐蚀性、附着力和阻隔性能的涂层,可以有效地阻止海水、氧气和其他腐蚀性物质与金属接触。
常见的涂层材料包括环氧涂料、聚氨酯涂料和氟碳涂料等。
为了提高涂层的防护效果,常常采用多层涂覆的方式,并在施工过程中严格控制表面处理质量和涂层厚度。
2、阴极保护阴极保护是一种通过向被保护金属结构施加阴极电流,使其电位负移至免蚀区,从而抑制腐蚀的电化学保护方法。
分为牺牲阳极阴极保护和外加电流阴极保护两种。
牺牲阳极通常采用锌、铝等活泼金属,它们在海水中优先溶解,为被保护结构提供阴极电流。
外加电流阴极保护则通过直流电源和辅助阳极向被保护结构提供阴极电流。
3、耐蚀材料的应用选用耐蚀性能良好的材料是预防腐蚀的根本措施之一。
例如,不锈钢、钛合金和镍基合金等在海洋环境中具有较好的耐蚀性。
但由于成本较高,这些材料往往只用于关键部位或对耐蚀性要求极高的场合。
基于海洋石油平台工艺管线防腐研究

基于海洋石油平台工艺管线防腐研究发布时间:2022-08-15T08:04:09.767Z 来源:《工程建设标准化》2022年37卷7期作者:曾玲珑[导读] 随着我国经济的快速发展,海洋石油的开发力度也随之增加。
曾玲珑中海石油(中国)有限公司天津分公司天津市滨海新区 300452摘要:随着我国经济的快速发展,海洋石油的开发力度也随之增加。
目前,为促进我国经济发展,满足国内需求,需要大量的海洋原油开采,而海洋石油平台技术是海上石油开采的基础,可以加速海上原油的开采,但在海上钻井过程中,管道会被腐蚀,从而降低海上原油的生产效率和经济效益。
本文结合实际案例,讨论了海上油田生产过程管道的防腐技术。
关键词:工艺管线防腐;海洋石油;策略引言:海洋石油平台长期处于暴晒、盐雾、海浪、海浪等复杂的环境中,很可能会因为环境的变化和杂质而发生腐蚀,从而造成管道的腐蚀,从而降低钻井平台的工作时间,增加钻井作业的难度和安全风险。
同时,海洋中蕴藏着丰富的矿物资源,各种原因都有可能导致工艺管线防腐,从而对海洋石油平台的安全运行产生潜在的影响,从而导致重大的经济和安全事故。
因此,对工艺管线防腐技术的研究是非常有实际意义的。
一、影响工艺管线腐蚀的原因在海洋中,环境是非常复杂的,影响管线使用寿命的因素有很多,比如海浪的冲击、烟雾的腐蚀、阳光的照射、海水的温度的急剧变化,在这种复杂的情况下,管线很容易受到腐蚀,腐蚀速度也很快。
对工艺管线防腐,有局部腐蚀是指管道发生的局部腐蚀,如:电偶腐蚀、点腐蚀、氢脆、应力腐蚀、晶间腐蚀等。
另外,海上石油钻井平台的管道要储存各种液体,如污水、水、天然气及原油等在管线与各类介质接触的过程中也引起内表面出现腐蚀问题。
管道的腐蚀是由于人为的。
在管道设计中,设计者对防腐效果的关注不够,导致了设计上的一些不足。
另外,有关的施工人员受经济利益的驱动,在工程建设中更注重进度,或不注重工程质量,以进一步减少工程造价。
海上油气开采设备的防水防腐技术与材料选择
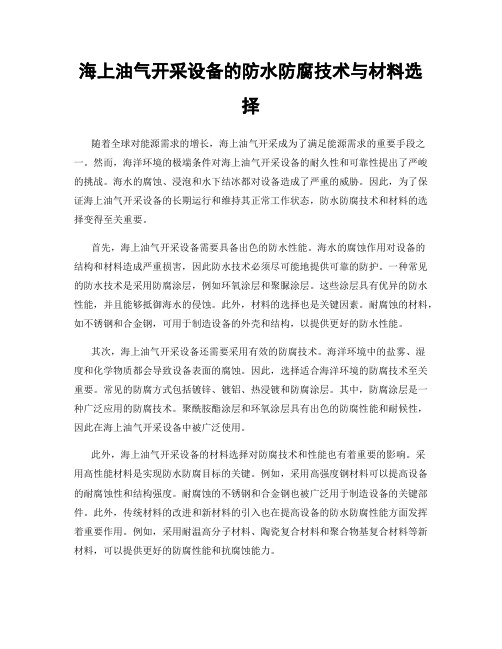
海上油气开采设备的防水防腐技术与材料选择随着全球对能源需求的增长,海上油气开采成为了满足能源需求的重要手段之一。
然而,海洋环境的极端条件对海上油气开采设备的耐久性和可靠性提出了严峻的挑战。
海水的腐蚀、浸泡和水下结冰都对设备造成了严重的威胁。
因此,为了保证海上油气开采设备的长期运行和维持其正常工作状态,防水防腐技术和材料的选择变得至关重要。
首先,海上油气开采设备需要具备出色的防水性能。
海水的腐蚀作用对设备的结构和材料造成严重损害,因此防水技术必须尽可能地提供可靠的防护。
一种常见的防水技术是采用防腐涂层,例如环氧涂层和聚脲涂层。
这些涂层具有优异的防水性能,并且能够抵御海水的侵蚀。
此外,材料的选择也是关键因素。
耐腐蚀的材料,如不锈钢和合金钢,可用于制造设备的外壳和结构,以提供更好的防水性能。
其次,海上油气开采设备还需要采用有效的防腐技术。
海洋环境中的盐雾、湿度和化学物质都会导致设备表面的腐蚀。
因此,选择适合海洋环境的防腐技术至关重要。
常见的防腐方式包括镀锌、镀铝、热浸镀和防腐涂层。
其中,防腐涂层是一种广泛应用的防腐技术。
聚酰胺酯涂层和环氧涂层具有出色的防腐性能和耐候性,因此在海上油气开采设备中被广泛使用。
此外,海上油气开采设备的材料选择对防腐技术和性能也有着重要的影响。
采用高性能材料是实现防水防腐目标的关键。
例如,采用高强度钢材料可以提高设备的耐腐蚀性和结构强度。
耐腐蚀的不锈钢和合金钢也被广泛用于制造设备的关键部件。
此外,传统材料的改进和新材料的引入也在提高设备的防水防腐性能方面发挥着重要作用。
例如,采用耐温高分子材料、陶瓷复合材料和聚合物基复合材料等新材料,可以提供更好的防腐性能和抗腐蚀能力。
最后,应综合考虑设备的运行环境,以选择最合适的防水防腐技术和材料。
不同的海域和水深环境对设备的防水防腐要求不同。
例如,对于浅海湿地,对海上油气开采设备的防腐性能要求更高,因为该地区更容易受到海水的侵蚀和损害。
因此,在设备设计和制造过程中,必须考虑到不同环境条件下的防水防腐需求,并确保所选择的技术和材料能够在任何条件下保持设备的完整和性能。
海洋平台的腐蚀及防腐技术

腐蚀原理
海洋平台腐蚀的主要原因是电化 学、化学反应和生物侵蚀等。
电化学腐蚀是由于海洋平台结构材料与海水、海洋生物等接触,形成原电池反 应,导致金属腐蚀。这种腐蚀在海洋平台中最为普遍,严重时可能导致平台结 构削弱。
化学反应腐蚀主要是由于海洋平台结构材料与海水、盐分等化学物质发生反应, 导致腐蚀。例如,钢铁材质的海洋平台在海水中会发生氧化反应,形成铁锈, 导致结构材料的腐蚀。
挑战与机遇
当前,微生物腐蚀及防腐技术的研究仍面临着一系列的挑战。首先,微生物腐 蚀的机制尚不完全清楚,需要进一步深入研究;其次,现有防腐技术的效果还 需要进一步提高,以满足更为严苛的防腐要求;此外,新型防腐技也带来了诸多机遇。随着环境保护意识的 提高和绿色可持续发展的要求,对于环保型防腐技术的需求不断增加。例如, 生物防腐剂和生物防护技术的发展前景十分广阔。此外,随着材料科学和纳米 技术的快速发展,新型防腐材料的研发和应用也将为微生物腐蚀及防腐技术的 发展带来新的机遇。
2、化学方法
化学方法主要包括使用缓蚀剂和杀菌剂。缓蚀剂是一种能够减缓金属腐蚀的物 质,如亚硝酸盐、铬酸盐等。杀菌剂则用于消灭海洋生物,防止生物污损引起 的腐蚀。然而,这些化学物质有可能对海洋生态系统造成负面影响,因此需要 慎重使用。
3、生物方法
生物方法主要利用某些生物的耐腐蚀特性,如海藻、珊瑚等,以降低海水的腐 蚀性。此外,生物污损也可以形成保护层,提高金属的耐腐蚀性能。生物方法 具有环保性和长效性,但需要充分考虑生物生态平衡以及不同生物对不同材料 的适应性。
未来展望
随着科技的不断进步,海洋环境腐蚀控制技术将迎来更多的发展机遇。新型材 料和涂层技术的研发将为海洋腐蚀控制提供更多选择。此外,智能防腐技术也 将成为未来的研究热点,包括智能涂层、自修复材料等。同时,随着海洋工程 的发展,针对深海和极地等特殊环境的腐蚀控制技术也将得到进一步研究和发 展。
海洋石油平台腐蚀防控技术探讨

海洋石油平台腐蚀防控技术探讨摘要:涵盖了海洋生产平台不同区域的腐蚀环境和腐蚀规律,对海洋石油平台防腐涂料的选择及配套体系进行简要叙述。
针对海洋时候平台的长效防腐防护要求,介绍了几种具有长效的防腐材料和防腐技术特点,包括海洋石油平台热喷涂长效防腐技术、锌加保护技术、海洋石油平台桩腿防腐套包缚技术等,为我们石油生产平台防腐实际工作提供参考。
关键词:海洋石油、腐蚀区、防腐技术、"锌加保护"1.海洋石油平台的腐蚀规律1.1海洋石油平台环境的腐蚀区域界定南海石油平台的使用环境极其恶劣,阳光暴晒、盐雾、海浪的冲击、复杂的海水体系、温度和湿度的变化及海洋生物的侵蚀等使得海洋石油平台的腐蚀速率较快。
海洋石油平台在不同的环境下,腐蚀过程和腐蚀特点会有比较大的差异。
因此要对海洋石油平台结构在海洋环境中腐蚀区域的腐蚀情况进行分析和界定,才能针对性地提出有效的保护措施。
根据海洋环境的腐蚀特点和腐蚀速率的不同,海洋石油平台在海洋环境中可分为海洋大气区、飞溅区和潮差区、海水全浸区和海泥区,即5大腐蚀区域。
1.2海洋钢结构腐蚀情况海洋大气区:钢铁在潮湿的空气中,会在表面形成一层薄水膜,这层水膜会导致钢铁表面产生电化学腐蚀。
钢铁腐蚀的产物,是铁的氧化物的水合物(铁锈),其质地疏松,不能隔绝钢铁与氧和水的继续接触,因此,在潮湿的空气中,腐蚀会不断地继续发展。
钢铁表面形成引起腐蚀的水膜与空气的相对湿度有关,当空气的相对湿度达到100%或者钢铁表面温度低于露点时,潮气就会在国内钢铁表面结露。
飞溅区:金属构件在海水飞溅条件下发生的腐蚀。
飞溅区指风浪、潮汐等激起的海浪、飞沫溅散到的区域。
通常,金属构件在海洋飞溅区的全面腐蚀速率最高。
由于经常潮湿的表面,表面供氧充足,无海生物污损。
长时间湿润表面与短时间干燥表面的交替作用和浪花的冲刷,造成物理与电化学腐蚀为主的腐蚀破坏,且破坏最大。
潮差区:钢结构在潮差区的腐蚀最低,甚至低于海水全浸区和海泥区的腐蚀速率。
海洋平台腐蚀特点及防腐分析

海洋平台腐蚀特点及防腐分析海洋平台防腐措施可以有效延长使用寿命,为海上安全运行提供有力保障。
通过分析海洋平台腐蚀特点及相应的防腐措施,旨在为防腐技术在平台防腐工程中的应用提供参考。
标签:海洋;平台;防腐1 海洋平台腐蚀特点海洋平台处于严酷的工作环境中,长期面临腐蚀危害。
海洋平台的主要结构材料为钢铁,海洋大气中水分含量较大,氯化钠微粒会在钢铁表面形成有强腐蚀性的水膜。
空气中的某些强腐蚀性介质如二氧化硫,溶于钢铁表面的水膜中,加大了水膜的腐蚀性。
海洋平台的飞溅区是一个特殊的腐蚀环境,在这一区域,平台表面会受到海水的周期冲击润湿[1]。
这种干湿变换的情况,加重了该区域的腐蚀状况。
海洋平台的水下部分,焊缝部位容易出现电化学腐蚀。
2 涂层防腐涂层防腐措施是海洋平台防腐技术中比较常见的方式之一,主要通过隔断平台钢结构与腐蚀介质实现防腐工作。
涂层的防腐蚀作用可归纳为以下几点:第一,性能优良的涂料可抑制水、氧、二氧化碳等物质透过涂层接触钢结构,并可以抑制微生物活动,减少微生物的附着污损。
第二,由于钢结构在海水中会出现电化学腐蚀,而涂层可通过抑制阳极金属离子在腐蚀介质中的溶解和阴极的放电现象,起到保护作用。
为了实现较好的涂装效果,在喷涂之前,应该对平台表面进行洁净度检查,并将表面残留物及杂质清除。
可以采用喷砂除锈,不方便喷砂的区域,可进行刮刀手动除锈,然后用压缩空气吹扫,并需要涂抹防护底漆。
如对旧涂层进行修缮涂装,则要根据旧涂层的状态,确定表面处理的方法。
轻度缺陷用刮刀和砂纸等打磨处理即可,中等缺陷要采用动力工具打磨光滑,而情况严重的区域,则要采用喷砂处理方式。
高性能涂料对表面光滑度的要求,要高于普通的油性涂料。
防锈漆的附着性能及渗水性能是关键参数,所含成分应避免电化学腐蚀,并且干燥后弹性良好,保证不开裂,不剥落。
采用上述处理,可以保证涂装的质量,减少平台表面腐蚀性。
海洋平台的使用时限及其特殊的作业环境,会对涂装的整理质量要求产生影响。
- 1、下载文档前请自行甄别文档内容的完整性,平台不提供额外的编辑、内容补充、找答案等附加服务。
- 2、"仅部分预览"的文档,不可在线预览部分如存在完整性等问题,可反馈申请退款(可完整预览的文档不适用该条件!)。
- 3、如文档侵犯您的权益,请联系客服反馈,我们会尽快为您处理(人工客服工作时间:9:00-18:30)。
海洋钻井平台防腐技术的研究
摘要:海洋钻井平台的防腐技术一直是海洋工程长期面临的一个问题,特别是
在钻井平台使用环境较为恶劣的地区,维护保养费用一直是笔较大的支出,维护
不好容易造成设备使用周期缩短,甚至导致生产事故。
本研究提出了新型防腐技
术的应用,以期提高钻井平台的防腐蚀能力,延长其使用年限。
关键词:海洋钻井平台;防腐技术;研究
前言:海洋覆盖了地球表面的71%左右,当今世界,人类的生产生活离不开
海洋,海洋产业已经成为重要的经济支柱。
在油气资源开发领域,陆地油气资源
逐年下降,海洋油气是未来发展的希望。
海上平台是一种海上大型工程结构,其
钢结构长期处于高盐雾、高潮气、高速率腐蚀的海洋环境中,还要受到海水及海
洋生物的侵蚀。
为了保证油气田生产的安全运行,做好海上平台的防腐工作十分
重要。
1海洋工程与腐蚀
海洋工程的实施过程非常的复杂,并且对于技术水平的要求较高,为保证海
洋工程顺利开展,需要对工程的安全性以及稳定性进行有力地保障,使其能够为
海洋石油开采工作奠定一个坚实的基础。
腐蚀作为现阶段我国海洋工程中所面临的最常见也是最为严重的一个问题,
受到了越来越多人的关注。
腐蚀是由于金属材料受环境的影响,在化学或电化学
的作用下引起结构的变质和破坏,在钻井平台中使用的多半是钢铁材料,钢铁材
料属于铁基,在氧和水的作用下形成含水氧化物,这种腐蚀的产物通常称为铁锈。
大气区、飞溅区以及内部、外部全浸区等是海洋钻井最常出现腐蚀现象的区域。
为解决容易发生腐蚀现象的这一问题,需要对海洋环境涂装系统进行不断地改进,为海洋工程涂装防腐设计的应用与发展奠定一个良好的基础。
2海洋钻井平台遭受腐蚀的原因分析
现阶段我国海洋钻井平台出现腐蚀情况的具体原因有以下几点:
2.1环境因素影响
海洋钻井平台设施的腐蚀主要分为四个区域:大气区、飞溅区,外部全浸区
和压载水舱(内部全浸区)等,外部全浸区也包括海底设施(采油树、管汇等)。
大部分海洋钻井平台位于海洋石油平台设施水面以上的大气区,主要面临的就是
海洋环境(高湿度、高盐分、长时间阳光暴晒)带来的腐蚀,在海洋大气环境中
钢铁的腐蚀速率相比陆地要高出4~5倍,处于大气区的平台一般用涂层进行保护,相对其它区域维修比较容易,施工成本较低;少部分位于外部全浸区和压载水舱,在防腐措施不完善时容易受到海水环境(海水的深度、温度、溶解程度等)的影响,从而导致严重的后果,维修比较困难、维修作业有时需动用大型施工船舶,
维修作业成本巨大,处于全浸区和压载水舱的工艺管线一般用涂层加牺牲阳极进
行保护;极少数管线位于飞溅区,经常遭受潮汐和海浪的冲击以及海生物的侵蚀
和腐蚀,其腐蚀速率约为全浸区的3~5倍,在防腐措施不完善时发生的腐蚀程度
最为严重。
2.2流体介质因素
海洋石油平台流体介质中的多相组分如固体颗粒、微生物、海生物以及CO2,H2S、CL-等物质含量以及流体介质的物理特性(如温度、压力、流动状态等)是
导致海洋石油平台产生内部腐蚀的关键因素,根据流体介质性质的不同,内部腐
蚀的速率不一,危害程度也不同,危害严重的会导致工艺管线腐蚀穿孔、油气泄
漏。
3新型防腐技术探讨
3.1新型防腐涂料
(1)高固体分、无溶剂防腐涂料
聚天门冬氨酸酯树脂聚脲涂料高固含、低VOC、防腐耐候性能良好等特点。
单一涂层可用于C3环境,若与富锌漆配套使用可用于C4-C5腐蚀环境。
石墨烯防腐涂料
石墨烯作为目前最薄、最硬的纳米材料,具有稳定的sp2杂化平面片状结构,具有良好的阻隔性。
涂料中的石墨烯可形成致密隔绝层,具有理性的屏蔽作用。
在富锌防腐漆中加入适量石墨烯可减少锌粉用量,减少粉尘污染,降低涂料密度,有利环保。
3.2热喷铝技术
热喷涂技术是一种表面加工技术,利用气体、激光、电弧等热源将碳化物、
金属、合金等材料加热到半熔融或熔融状态,再用气流以雾化的方式将这些喷涂
材料高速喷射到零件表面,形成喷层。
(1)加工过程
采用独特的熔炼工艺制备多元锌铝合金,熔炼后采用连铸的方法得到多元锌
铝合金圆形铸锭。
接着,将铸锭放入350-450℃的电炉内4-8个小时,进行均匀化处理。
再用350-500吨的挤压机,在380-420℃下热挤压材料,使材料通过圆形
模具,形成直径4.5-8mm的线材。
将线材在真空退火炉内180-280℃退火1.5-3小时,进行拉拔。
重复以上退火、拉拔步骤,直到制成1.5-4.0mm的丝材。
(2)热喷铝技术流程
首先:表面处理。
服役于海洋环境和浸没环境的钢结构喷砂应满足标准ISO 8501 Sa3;表面可溶盐污染物水平应符合合同的要求。
为保证热喷涂金属涂层和
钢结构间具有足够的结合强度,钢结构基材的粗糙度至关重要,其粗糙度要求远
高于喷涂有机涂层。
热喷涂金属涂层金属基材表面粗糙度应≥65μm,最好在
85~110μm,并且喷砂后表面要有尖角。
表面粗糙度应按照标准SATMD 4417的方
法C(复制胶带法,超粗,38~113μm或方法B(粗糙度计),或两者同时进行测量。
其次,进行材料喷涂。
铝容易被氧化,用铝线材来代替铝粉,可以有效地减
少氧化程度。
按ISO2063-1991和GB/T9793-1997的规定,铝线材为半硬态,直径
为3mm,纯度≥99.5%。
再次,热喷涂铝。
表面喷砂后的四小时内应进行热喷涂铝,采用QX-1气体金属线材喷枪并根据不同的喷涂要求来确定工件、喷枪的移动速度和距离以及喷涂
时间。
最后,热扩散。
喷铝层有一定的孔隙率,存在较多微孔,酸性离子会穿透这
些孔隙致使金属发生腐蚀。
因此,应将喷铝后的工件加热,进行热扩散以提高耐
腐蚀性,加热温度控制在430~450℃左右。
3.3环保型Al-Zn-Si水溶性涂层技术
这种新材料将新型铝锌基合金制成微米级粉体,加入稀释剂、固化剂和纳米
增强剂,形成水溶性合金涂料。
利用喷涂、刷涂等方法在工件表面形成耐腐蚀、
耐磨、抗冲蚀纳米颗粒增强复合材料涂层。
它适用于大气多雨、高温、多盐雾和
强风流等海洋腐蚀性恶劣环境,零部件耐海洋气候腐蚀寿命超过20年。
新材料
不仅在耐腐蚀性能和耐磨性能好,而且不含六价Cr离子,不会对环境造成任何污
染。
其关键技术有:(1)稀土铝锌硅粉体制备技术。
气体雾化法制备微米级高纯度鳞片状锌铝粉,使涂层具有更改的耐蚀、耐磨性能,且具有成本低的优势。
(2)制取铬酸盐取代剂。
3.4防腐维护
在海洋钻井平台使用过程中,设备外表面防腐被破坏,需要做现场修补。
一般修补工艺流程:结构处理→表面处理→预先涂刷→冷喷锌→环氧封闭底漆→环氧中间漆→氟碳面漆。
底漆的施工方法:先将涂料进行混合,冷喷锌涂料容易沉淀,搅拌均匀后才施工,施工过程中应不时搅拌,防止沉淀。
现场涂装方法为刷涂、辊涂、喷涂等方法,喷涂孔径为0.5mm,喷出压力为10MPa左右,喷枪的距离约为50cm,第一道环氧封闭漆喷涂时,要加入20%的稀释剂,形成喷雾状,使得表面得到全部湿润以便更好的渗入到冷喷锌涂层中去。
环氧中间漆的施工也可以采用喷涂,压力在100kg/cm2,施工后湿膜厚度须在120μm以上。
最小涂装间隔为16h,施工过程中每一道工序应保持表面清洁,避免厚度不足或者超标,中间漆应保持无气泡、无针孔,施工温度和湿度控制在合理的范围,漆膜干燥后应平整光滑。
施工过程中也须穿戴好劳保用品,现场严禁明火,高空作业须做好安全防范措施,保证通风良好。
4结束语
综上所述,海洋工程在开展过程中会受海洋环境或应力损坏等因素影响造成腐蚀现象,而钻井平台作为其中的重要部分,腐蚀性相对较为严重,甚至影响到了海洋工程的进展。
因此,实际工作中,应当采取涂装防腐技术实施处理,使性能得到保障,从而提高海洋工程的工作效率和质量,保障国家海洋油气资源的顺利开采。
参考文献:
[1]王永才,厉嘉滨,王涛.海上钻井平台涂层寿命评估研究及应用[J].涂料技术与文摘,2017,38(07):24-28+36.
[2]鲁运来,胡彪,张国辉,罗军.石油钻机腐蚀问题及处理措施[J].设备管理与维修,2017(10):56-57.
[3]熊月潮.海洋石油平台工艺管线防腐技术的发展研究[J].石化技术,2017,24(10):282+238.。