汽车变速器计算参考
变速器传动比计算公式
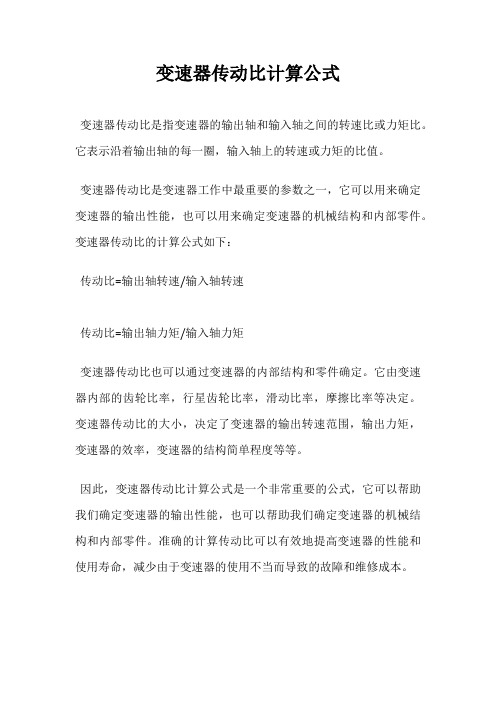
变速器传动比计算公式
变速器传动比是指变速器的输出轴和输入轴之间的转速比或力矩比。
它表示沿着输出轴的每一圈,输入轴上的转速或力矩的比值。
变速器传动比是变速器工作中最重要的参数之一,它可以用来确定变速器的输出性能,也可以用来确定变速器的机械结构和内部零件。
变速器传动比的计算公式如下:
传动比=输出轴转速/输入轴转速
传动比=输出轴力矩/输入轴力矩
变速器传动比也可以通过变速器的内部结构和零件确定。
它由变速器内部的齿轮比率,行星齿轮比率,滑动比率,摩擦比率等决定。
变速器传动比的大小,决定了变速器的输出转速范围,输出力矩,变速器的效率,变速器的结构简单程度等等。
因此,变速器传动比计算公式是一个非常重要的公式,它可以帮助我们确定变速器的输出性能,也可以帮助我们确定变速器的机械结构和内部零件。
准确的计算传动比可以有效地提高变速器的性能和使用寿命,减少由于变速器的使用不当而导致的故障和维修成本。
转速和车速的计算公式
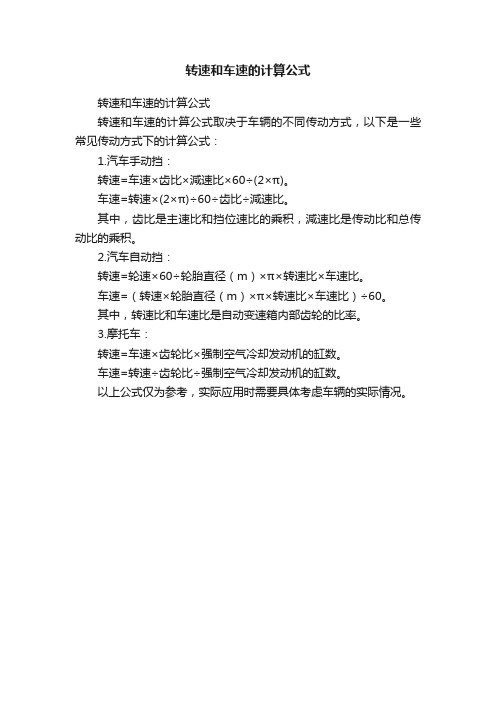
转速和车速的计算公式
转速和车速的计算公式
转速和车速的计算公式取决于车辆的不同传动方式,以下是一些常见传动方式下的计算公式:
1.汽车手动挡:
转速=车速×齿比×減速比×60÷(2×π)。
车速=转速×(2×π)÷60÷齿比÷減速比。
其中,齿比是主速比和挡位速比的乘积,減速比是传动比和总传动比的乘积。
2.汽车自动挡:
转速=轮速×60÷轮胎直径(m)×π×转速比×车速比。
车速=(转速×轮胎直径(m)×π×转速比×车速比)÷60。
其中,转速比和车速比是自动变速箱内部齿轮的比率。
3.摩托车:
转速=车速×齿轮比×强制空气冷却发动机的缸数。
车速=转速÷齿轮比÷强制空气冷却发动机的缸数。
以上公式仅为参考,实际应用时需要具体考虑车辆的实际情况。
课程设计--- 变速器的设计计算

设计说明书题目:货车机械变速器学号:姓名:变速器的设计计算1.1 变速器的选择变速器的种类很多,按前进档位的不同可分为三、四、五和多档变速器,根据轴的型式的不同,又有固定轴式和旋转轴式(常配合行星齿轮传动)两类。
固定轴式又有两轴式、中间轴式、双中间轴式和多中间轴式变速器。
固定轴式应用广泛,其中两轴式变速器多用于发动机前置前轮驱动的汽车上,中间轴式变速器多用于发动机前置后轮驱动的汽车上。
旋转轴式主要用于液力机械式变速器。
2-1-1 中间轴式变速器从结构外形看中间轴式变速器有三根轴:一轴和二轴在一条中心线上。
将它们连接即为直接档,此时,齿轮、轴承不承受载荷而只传递转矩,故而传动效率高,而且摩损小,寿命长,噪音也较小。
而在其他档位上,经过两对连续齿轮传动,传动效率稍低。
由于本设计中的汽车为重型货车,且档位多,传动比大,故本设计采用这种型式。
2-1-2 变速器齿轮型式变速器中的齿轮一般只有两种:直尺圆柱齿轮和斜齿圆柱齿轮。
直齿圆柱齿轮多用为滑动式,故使用在一档和倒档的较多,它们的结构简单,制造容易。
但是在换档时齿轮端部产生冲击,噪声很大,从而加剧端部磨损,使齿轮的寿命降低,而且由于噪声大,容易造成驾驶员的疲劳。
斜齿圆柱齿轮传动平稳,噪声很小,磨损小,寿命长。
唯一的缺点是工作时有轴向力的产生,而且结构复杂,这个缺点可以在进行轴的载荷计算时予以平衡。
通过比较两种型式齿轮的优缺点,本设计中,倒档采用直齿圆柱齿轮,这是考虑到倒档的使用率较低,综合衡量经济性和便利性而定的,其余各档全部采用斜齿圆柱齿轮传动,这样充分发挥其传动平稳,噪声小等优点。
2-1-3变速器的换档结构变速器的换档机构形式有以下几种:直齿滑动齿轮、啮合套和同步器换档。
(1) 直齿滑动齿轮换档该结构形式制造容易,结构简单。
但缺点较多:汽车行驶时各档齿轮有不同的角速度,因此用轴向滑动直齿齿轮的方式换档,会在轮齿端面产生冲击,并伴随有噪声。
这使齿轮端部磨损加剧并过早损坏,造成汽车的行驶安全性降低,同时使驾驶员精神紧张,而换档产生的噪声又会使乘坐舒适应大大的降低。
汽车设计课程设计 题目(变速器设计)
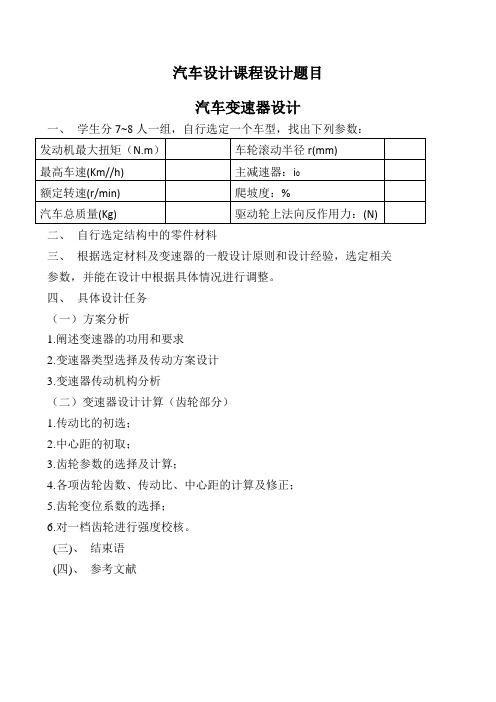
汽车设计课程设计题目
汽车变速器设计
一、学生分7~8人一组,自行选定一个车型,找出下列参数:
二、自行选定结构中的零件材料
三、根据选定材料及变速器的一般设计原则和设计经验,选定相关参数,并能在设计中根据具体情况进行调整。
四、具体设计任务
(一)方案分析
1.阐述变速器的功用和要求
2.变速器类型选择及传动方案设计
3.变速器传动机构分析
(二)变速器设计计算(齿轮部分)
1.传动比的初选;
2.中心距的初取;
3.齿轮参数的选择及计算;
4.各项齿轮齿数、传动比、中心距的计算及修正;
5.齿轮变位系数的选择;
6.对一档齿轮进行强度校核。
(三)、结束语
(四)、参考文献。
毕业设计(论文)-汽车变速器设计计算说明书[管理资料]
![毕业设计(论文)-汽车变速器设计计算说明书[管理资料]](https://img.taocdn.com/s3/m/ce283f069e3143323868934c.png)
目录第1章变速器主要参数的选择 ....................................................... - 1 -.档数................................................................................................................... - 1 -.传动比范围....................................................................................................... - 1 -第2章变速器各档传动比的确定 ................................................... - 2 -.主减速器传动比的确定................................................................................... - 2 -.最抵档传动比计算........................................................................................... - 2 -第3章变速器各档速比的配置 ....................................................... - 4 -.按等比级数分配其它各档传动比,............................................................... - 4 -第4章中心距的选择 ....................................................................... - 4 -.初选中心距可根据经验公式计算................................................................... - 4 -.变速器的外形尺寸........................................................................................... - 5 -第5章齿轮参数的选择 ................................................................... - 5 -.模数................................................................................................................... - 5 -.压力角............................................................................................................... - 6 -.螺旋角............................................................................................................... - 6 -.齿宽................................................................................................................... - 6 -.齿顶高系数....................................................................................................... - 7 -第6章各档齿轮齿数的分配及传动比的计算 ............................... - 7 -.一档齿数及传动比的确定............................................................................... - 7 -.二档齿数及传动比的确定............................................................................... - 9 -.计算三档齿轮齿数及传动比......................................................................... - 10 -.计算四档齿轮齿数及传动比......................................................................... - 12 -.计算五档齿轮齿数及传动比......................................................................... - 13 -.计算倒档齿轮齿数及传动比......................................................................... - 15 -第7章齿轮材料的选择原则 ......................................................... - 19 -.满足工作条件的要求..................................................................................... - 19 -.合理选择材料配对......................................................................................... - 19 -.考虑加工工艺及热处理工艺......................................................................... - 19 -第8章变速器齿轮弯曲强度校核 ................................................. - 19 -.一档齿轮校核................................................................................................. - 21 -. 主动齿轮:........................................................................................................... - 21 - . 从动齿轮:........................................................................................................... - 21 - .二档齿轮校核................................................................................................. - 21 -.主动齿轮:..................................................................................................... - 21 -. 从动齿轮............................................................................................................... - 22 - .三档齿轮校核................................................................................................. - 22 -. 主动齿轮:........................................................................................................... - 22 - . 从动齿轮............................................................................................................... - 22 - .四档齿轮校核................................................................................................. - 23 -. 主动齿轮............................................................................................................... - 23 - . 从动齿轮............................................................................................................... - 23 - .五档齿轮校核................................................................................................. - 23 -. 主动齿轮:........................................................................................................... - 23 - . 从动齿轮............................................................................................................... - 24 -第9章第10轮齿接触应力校核 ................................................... - 24 -. 一档齿轮接触应力校核....................................................................................... - 25 - . 倒档齿轮的校核................................................................................................... - 26 - .、齿面接触疲劳许用应力的计算....................................................................... - 26 - . .齿根弯曲疲劳许用应力计算.............................................................................. - 26 - . 接触疲劳强度校核............................................................................................... - 27 - .齿根弯曲疲劳强度校核................................................................................. - 28 -第10章轴的结构和尺寸设计 ......................................................... - 28 -. 初选轴的直径....................................................................................................... - 29 - . 轴的强度验算与轴的刚度计算........................................................................... - 30 - . 轴的强度计算....................................................................................................... - 33 -第11章轴承选择与寿命计算 ......................................................... - 35 -. 输入轴轴承的选择与寿命计算........................................................................... - 36 - . 输出轴轴承的选择与寿命计算........................................................................... - 38 -第12章参考文献 ............................................................................. - 44 -第1章变速器主要参数的选择本次毕业设计是在给定主要整车参数的情况下进行设计,:乘用车整车主要技术参数1.1. 档数近年来,为了降低油耗,变速器的档数有增加的趋势。
变速器各部件阶次计算
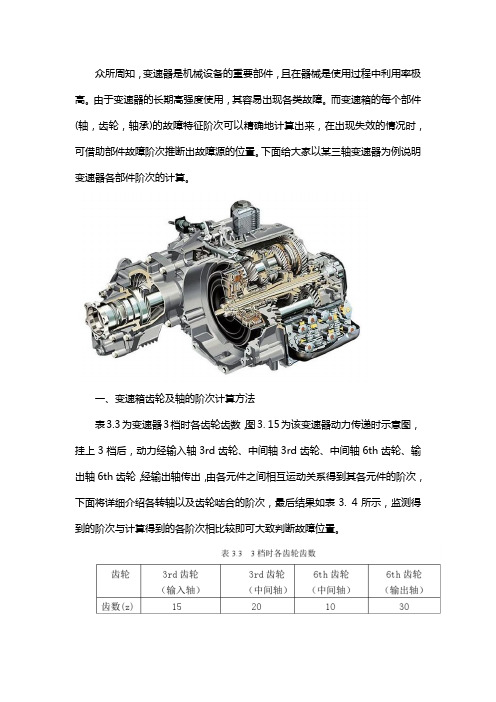
众所周知,变速器是机械设备的重要部件,且在器械是使用过程中利用率极高。
由于变速器的长期高强度使用,其容易出现各类故障。
而变速箱的每个部件(轴,齿轮,轴承)的故障特征阶次可以精确地计算出来,在出现失效的情况时,可借助部件故障阶次推断出故障源的位置。
下面给大家以某三轴变速器为例说明变速器各部件阶次的计算。
一、变速箱齿轮及轴的阶次计算方法
表3.3为变速器3档时各齿轮齿数,图3. 15为该变速器动力传递时示意图,挂上3档后,动力经输入轴3rd齿轮、中间轴3rd齿轮、中间轴6th齿轮、输出轴6th齿轮,经输出轴传出,由各元件之间相互运动关系得到其各元件的阶次,下面将详细介绍各转轴以及齿轮啮合的阶次,最后结果如表3. 4所示,监测得到的阶次与计算得到的各阶次相比较即可大致判断故障位置。
以上就是由四川志方科技有限公司为大家提供整理的变速器各部件阶次计算,变速器容易产生故障失效,因此,在使用过程中需要经常对其进行检测,但是变速器的测试过程比较繁琐,如果专门派人做变速器检测,将耗费大量人力,不如购置一台专业的变速器测试系统,将专业的工作交给专业的人去做,既节约人力又提升效率。
四川志方科技有限公司研发的减速器测试系统采用模块化设计,依据国内外最新测试标准,结合用户测试需求,可完成各种精密减速器的生产出厂、性能测试及科研、教学演示。
毕业设计 变速器设计计算说明书

毕业设计变速器设计计算说明书1.绪论1.1 课题背景及目的本课题是取材于汽车中比较实用的皮卡汽车,皮卡车在载货或在雨、雪路面上行驶时,动力性好,越野性能出色。
为了满足消费者对汽车高性能、安全、可靠、舒适性的需求,所以对变速器的性能要求也更高。
因此,本课题主要是对机械式变速器的设计。
本课题目的根据给定皮卡车的车型参数,来设计皮卡车变速器系统,使汽车在各种工况获得不同的牵引力和速度,同时使发动机在最有利的工况范围内工作。
通过对皮卡汽车变速器的课题的深入分析和研究,强化我们的开发和设计能力。
运用所学习的知识和技能去分析和解决实际问题,树立严谨的科学态度和工作作风,培养不断思考和学习的能力。
1.2 国内外研究状况汽车变速器在汽车传动系中扮演着至关重要的角色。
现在的汽车上广泛采用活塞式内燃机,其转矩和变速范围较小,而复杂的使用条件则要求汽车的牵引力和车速能在相当大的范围内变化,为了解决这一矛盾,在传动系中设置了变速器,以满足复杂条件的使用要求。
随着科技的高速发展,人们对汽车的性能要求越来越来高,使用寿命,能源消耗,振动噪声等在很大程度上取决于变速器的性能。
1894年变速器由法国人路易斯·雷纳·本哈特和埃米尔·拉瓦索推广在汽车上使用,从此变速器在汽车上就得到广泛的运用。
经过100多年的发展,汽车变速器的技术达到了一个空前的高度,尤其在近几十年,汽车工业在各个国家的高速发展,更加带动了变速器的进步。
随着各个领域的科学技术的发展,在未来变速器主要发展方向:1)节能与环境保护:研究高效率的传动副,来节约能源,采用零污染的工作介质或润滑油来避免环境污染,根据发动机的特性和行驶工况来设计变速器,使发动机工作在最佳状态,以保证汽车在最高传动效率和最低污染物排放区运行,2)应用新型材料:各种新材料的使用推动汽车技术的发展和性能的提高。
3)高性能,低成本,微型化:对变速器进行机构创新的研究,探索变速器的新类型;对传动副的材料和机理进行研究,提高寿命,减小质量;进行变速器的动力学特性和振动研究,以求提高特性,降低噪声;采用先进的制造技术提高变速器的性能和降低成本。
汽车变速器齿轮强度计算方法
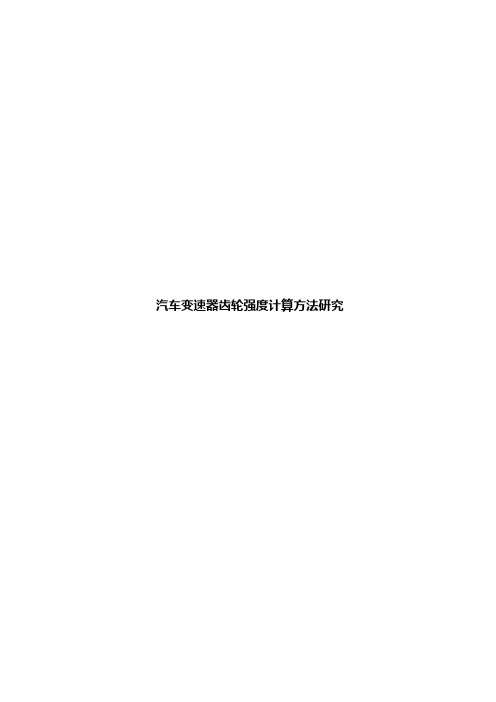
汽车变速器齿轮强度计算方法研究摘要汽车变速器齿轮强度的计算比较复杂,有些参数需通过多次选取和计算,才能达到设计要求,需要耗费大量的时间。
通过学习研究一些国外变速器的齿轮计算方法,通过VB6.0编程实现计算机辅助汽车变速器齿轮强度计算,找到一种简便的、快速的计算方法。
同时使用S-N曲线对计算后的齿轮强度进行校核。
Solidworks是法国达索公司开发的集三维建模、运动模拟及有限元分析为一体的,功能强大且操作简单的机械设计软件。
可对齿轮进行快速建模,并应用集成cosmosworks 对啮合齿轮进行有限元分析,为设计提供依据。
本文以某六档机械式汽车变速器为实例进行设计计算。
关键词:汽车变速器,齿轮强度计算,cosmosworks,VB汽车变速器齿轮的强度计算和校核1.1 齿轮强度计算1.1.1 变速箱齿轮的失效形式通常变速箱齿轮损坏有三种形式:轮齿折断、齿面点蚀、齿面胶合。
齿轮在啮合过程中,轮齿表面将承受集中载荷的作用。
轮齿相当于悬臂梁,根部弯曲应力很大,过渡圆角处又有应力集中,故轮齿根部很容易发生断裂。
折断有两种情况:一是轮齿受足够大的突然载荷冲击作用导致发生断裂;二是受多次重复载荷的作用,齿根受拉面的最大应力区出现疲劳裂缝,裂缝逐渐扩展到一定深度,轮齿突然折断。
变速箱齿轮折断多数是疲劳破坏。
齿面点蚀是闭式齿轮传动常出现的一种损坏形式。
因闭式齿轮传动的齿轮在润滑油中工作,齿面长期受到脉动的接触应力作用,会逐渐产生大量与齿面成尖角的小裂缝。
而裂缝中充满了润滑油,啮合时由于齿面互相挤压,裂缝中油压升高,使裂缝继续扩展,最后导致齿面表层一块块剥落,齿面出现大量扇形小麻点,此即齿面点蚀。
理论上靠近节圆的根部齿面处要较靠近节圆顶部齿面处点蚀更严重;互相啮合的齿轮副中,主动的小齿轮点蚀较严重。
在变速箱齿轮中,齿面胶核损坏的情况不多,故一般设计计算无须校核齿面胶合的情况。
齿轮计算载荷的确定在齿轮强度计算中占据至关重要的地位,而影响轮齿载荷的因素却有很多,也比较复杂,目前在国际上的各种齿轮强度计算方法的主要区别,就是对载荷影响因素的计算方法的不同。
- 1、下载文档前请自行甄别文档内容的完整性,平台不提供额外的编辑、内容补充、找答案等附加服务。
- 2、"仅部分预览"的文档,不可在线预览部分如存在完整性等问题,可反馈申请退款(可完整预览的文档不适用该条件!)。
- 3、如文档侵犯您的权益,请联系客服反馈,我们会尽快为您处理(人工客服工作时间:9:00-18:30)。
max max 0r g e mg r i T i ψη≥§2.1 变速器主要参数的选择一、档数和传动比近年来,为了降低油耗,变速器的档数有增加的趋势。
目前,乘用车一般用4~5个档位的变速器。
本设计也采用5个档位。
选择最低档传动比时,应根据汽车最大爬坡度、驱动轮与路面的附着力、汽车的最低稳定车速以及主减速比和驱动轮的滚动半径等来综合考虑、确定。
汽车爬陡坡时车速不高,空气阻力可忽略,则最大驱动力用于克服轮胎与路面间的滚动阻力及爬坡阻力。
故有则由最大爬坡度要求的变速器Ⅰ档传动比为(2-1)式中 m ----汽车总质量;g ----重力加速度;ψmax ----道路最大阻力系数;r r ----驱动轮的滚动半径;T emax ----发动机最大转矩;i 0----主减速比;η----汽车传动系的传动效率。
根据驱动车轮与路面的附着条件求得的变速器I 档传动比为:(2-2)式中 G 2----汽车满载静止于水平路面时驱动桥给路面的载荷;φ----路面的附着系数,计算时取φ=0.5~0.6。
由已知条件:满载质量 1800kg ;r r =337.25mm ;T e max =170Nm ;i 0=4.782;η=0.95。
根据公式(2-2)可得:i gI =3.85。
超速档的的传动比一般为0.7~0.8,本设计去五档传动比i g Ⅴ=0.75。
2.551.691.12(1)gII gIII gIV i i i ===修正为A K=中间档的传动比理论上按公比为:(2-3)的等比数列,实际上与理论上略有出入,因齿数为整数且常用档位间的公比宜小些,另外还要考虑与发动机参数的合理匹配。
根据上式可的出:q =1.51。
故有:二、中心距中心距对变速器的尺寸及质量有直接影响,所选的中心距、应能保证齿轮的强度。
三轴式变速器的中心局A (mm )可根据对已有变速器的统计而得出的经验公式初定:(2-4)式中 K A ----中心距系数。
对轿车,K A =8.9~9.3;对货车,K A =8.6~9.6;对多档主变速器,K A =9.5~11;T I max ----变速器处于一档时的输出扭矩:T I max =T e max i g I η =628.3N ﹒m故可得出初始中心距A=77.08mm 。
三、轴向尺寸变速器的横向外形尺寸,可根据齿轮直径以及倒档中间齿轮和换档机构的布置初步确定。
轿车四档变速器壳体的轴向尺寸3.0~3.4A 。
货车变速器壳体的轴向尺寸与档数有关:四档(2.2~2.7)A五档(2.7~3.0)A六档(3.2~3.5)A当变速器选用常啮合齿轮对数和同步器多时,中心距系数K A 应取给出系数的上限。
为检测方便,A 取整。
本次设计采用5+1手动挡变速器,其壳体的轴向尺寸是3⨯77.08mm=231.24mm ,变速器壳体的最终轴向尺寸应由变速器总图的结构尺寸链确定。
四、齿轮参数(1)齿轮模数建议用下列各式选取齿轮模数,所选取的模数大小应符合JB111-60规定的标准值。
第一轴常啮合斜齿轮的法向模数m nm=n(2-5)其中T=170Nm,可得出m n=2.5。
emax一档直齿轮的模数mm=(2-6) 通过计算m=3。
同步器和啮合套的接合大都采用渐开线齿形。
由于制造工艺上的原因,同一变速器中的结合套模数都去相同,轿车和轻型货车取2~3.5。
本设计取2.5。
(2)齿形、压力角α、螺旋角β和齿宽b汽车变速器齿轮的齿形、压力角、及螺旋角按表2-1选取。
压力角较小时,重合度大,传动平稳,噪声低;较大时可提高轮齿的抗弯强度和表面接触强度。
对轿车,为加大重合度已降低噪声,取小些;对货车,为提高齿轮承载力,取大些。
在本设计中变速器齿轮压力角α取20°,啮合套或同步器取30°;斜齿轮螺旋角β取30°。
应该注意的是选择斜齿轮的螺旋角时应力求使中间轴上是轴向力相互抵消。
为此,中间轴上的全部齿轮一律去右旋,而第一轴和第二轴上的的斜齿轮去左旋,其轴向力经轴承盖由壳体承受。
齿轮宽度b的大小直接影响着齿轮的承载能力,b加大,齿的承载能力增高。
但试验表明,在齿宽增大到一定数值后,由于载荷分配不均匀,反而使齿轮的承载能力降低。
所以,在保证齿轮的强度条件下,尽量选取较小的齿宽,以有利于减轻变速器的重量和缩短其轴向尺寸。
10912Z Z Z Z i gI ⋅=91012Z Z i Z Z gI ⨯=76.112=Z Z 通常根据齿轮模数的大小来选定齿宽:直齿 b=(4.5~8.0)m ,mm斜齿 b=(6.0~8.5)m ,mm第一轴常啮合齿轮副齿宽的系数值可取大一些,使接触线长度增加,接触应力降低,以提高传动的平稳性和齿轮寿命。
§2.2各档传动比及其齿轮齿数的确定在初选了中心距、齿轮的模数和螺旋角后,可根据预先确定的变速器档数、传动比和结构方案来分配各档齿轮的齿数。
下面结合本设计来说明分配各档齿数的方法。
1.确定一档齿轮的齿数一档传动比(2-7) 为了确定Z 9和Z 10的齿数,先求其齿数和∑Z :(2-8)其中 A =77.08mm 、m =3;故有4.51=∑Z 。
图2-1 五档变速器示意图当轿车三轴式的变速器9.3~5.3=gI i 时,则范围内选择可在17~1510Z ,此处取10Z =16,则可得出9Z =35。
上面根据初选的A 及m 计算出的∑Z 可能不是整数,将其调整为整数后,从式(2-8)看出中心距有了变化,这时应从∑Z 及齿轮变位系数反过来计算中心距A ,再以这个修正后的中心距作为以后计算的依据。
这里∑Z 修正为51,则根据式(2-8)反推出A =76.5mm 。
2.确定常啮合齿轮副的齿数由式(2-7)求出常啮合齿轮的传动比(2-9) 由已经得出的数据可确定 ①βcos 2)(21Z Z m A n +=nm A Z Z βcos 221=+91.3=gI i 8712Z Z Z Z i g ⋅=∏425.187=Z Z n m A Z βcos 2=∑1212131311Z Z Z Z Z Z i gr ⋅⋅=)(211312Z Z m n +55.2=∏g i 而常啮合齿轮的中心距与一档齿轮的中心距相等(2-10)由此可得: (2-11)而根据已求得的数据可计算出:5321=+Z Z 。
②① 与②联立可得:1Z =19、2Z =34。
则根据式(2-7)可计算出一档实际传动比为: 。
3.确定其他档位的齿数二档传动比(2-12)而 ,故有: ③ 对于斜齿轮, (2-13) 故有:5387=+Z Z ④③ 联立④得:223187==Z Z 、。
按同样的方法可分别计算出:三档齿轮 272665==Z Z 、;四档齿轮371643==Z Z 、。
4.确定倒档齿轮的齿数一般情况下,倒档传动比与一档传动比较为接近,在本设计中倒档传动比gr i 取3.7。
中间轴上倒档传动齿轮的齿数比一档主动齿轮10略小,取1312=Z 。
而通常情况下,倒档轴齿轮13Z 取21~23,此处取13Z =23。
由(2-14)可计算出2711=Z 。
故可得出中间轴与倒档轴的中心距A′ =(2-15))(211311Z Z A +='' =50mm而倒档轴与第二轴的中心:(2-16)=72.5mm 。
§2.3 齿轮变位系数的选择齿轮的变位是齿轮设计中一个非常重要的环节。
采用变位齿轮,除为了避免齿轮产生根切和配凑中心距以外,它还影响齿轮的强度,使用平稳性,耐磨性、抗胶合能力及齿轮的啮合噪声。
变位齿轮主要有两类:高度变位和角度变位。
高度变位齿轮副的一对啮合齿轮的变位系数的和为零。
高度变位可增加小齿轮的齿根强度,使它达到和大齿轮强度想接近的程度。
高度变位齿轮副的缺点是不能同时增加一对齿轮的强度,也很难降低噪声。
角度变位齿轮副的变位系数之和不等于零。
角度变位既具有高度变位的优点,有避免了其缺点。
有几对齿轮安装在中间轴和第二轴上组合并构成的变速器,会因保证各档传动比的需要,使各相互啮合齿轮副的齿数和不同。
为保证各对齿轮有相同的中心距,此时应对齿轮进行变位。
当齿数和多的齿轮副采用标准齿轮传动或高度变位时,则对齿数和少些的齿轮副应采用正角度变位。
由于角度变位可获得良好的啮合性能及传动质量指标,故采用的较多。
对斜齿轮传动,还可通过选择合适的螺旋角来达到中心距相同的要求。
变速器齿轮是在承受循环负荷的条件下工作,有时还承受冲击负荷。
对于高档齿轮,其主要损坏形势是齿面疲劳剥落,因此应按保证最大接触强度和抗胶合剂耐磨损最有利的原则选择变位系数。
为提高接触强度,应使总变位系数尽可能取大一些,这样两齿轮的齿轮渐开线离基圆较远,以增大齿廓曲率半径,减小接触应力。
对于低档齿轮,由于小齿轮的齿根强度较低,加之传递载荷较大,小齿轮可能出现齿根弯曲断裂的现象。
总变位系数越小,一对齿轮齿更总厚度越薄,齿根越弱,抗弯强度越低。
但是由于轮齿的刚度较小,易于吸收冲击振动,故噪声要小些。
根据上述理由,为降低噪声,变速器中除去一、二档和倒档以外的其他各档齿轮的总变位系数要选用较小的一些数值,以便获得低噪声传动。
其中,一档主动齿轮10的齿数Z 10〈17,因此一档齿轮需要变位。
1717Z ξ-=10t f W F K K btyσσ=102/t g F T d=K σ102/g F T d =g T 变位系数(2-17)式中 Z 为要变位的齿轮齿数。
第三章 变速器齿轮的强度计算与材料的选择§3.1 齿轮的损坏原因及形式齿轮的损坏形式分三种:轮齿折断、齿面疲劳剥落和移动换档齿轮端部破坏。
轮齿折断分两种:轮齿受足够大的冲击载荷作用,造成轮齿弯曲折断;轮齿再重复载荷作用下齿根产生疲劳裂纹,裂纹扩展深度逐渐加大,然后出现弯曲折断。
前者在变速器中出现的很少,后者出现的多。
齿轮工作时,一对相互啮合,齿面相互挤压,这是存在齿面细小裂缝中的润滑油油压升高,并导致裂缝扩展,然后齿面表层出现块状脱落形成齿面点蚀。
他使齿形误差加大,产生动载荷,导致轮齿折断。
用移动齿轮的方法完成换档的抵挡和倒挡齿轮,由于换档时两个进入啮合的齿轮存在角速度茶,换档瞬间在齿轮端部产生冲击载荷,并造成损坏。
§3.2 齿轮的强度计算与校核与其他机械设备使用的变速器比较,不同用途汽车的变速器齿轮使用条件仍是相似的。
此外,汽车变速器齿轮所用的材料、热处理方法、加工方法、精度等级、支撑方式也基本一致。
如汽车变速器齿轮用低碳合金钢制造,采用剃齿或齿轮精加工,齿轮表面采用渗碳淬火热处理工艺,齿轮精度不低于7级。
因此,比用于计算通用齿轮强度公式更为简化一些的计算公式来计算汽车齿轮,同样、可以获得较为准确的结果。
在这里所选择的齿轮材料为40Cr 。