塑料电镀多种问题解决措施
注塑电镀缺陷分析及处理
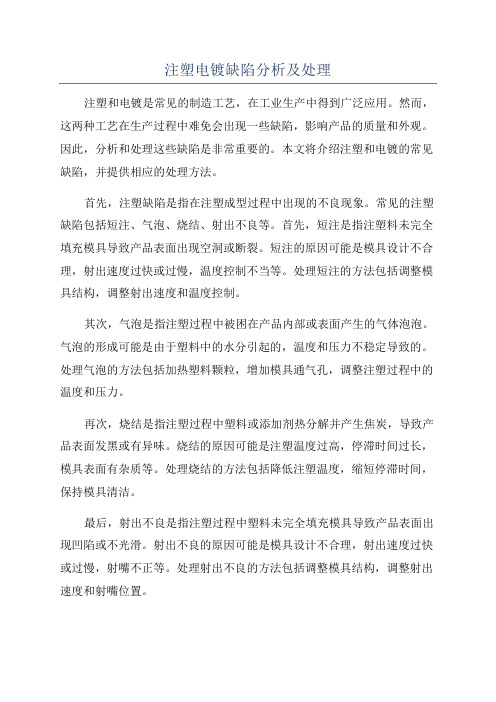
注塑电镀缺陷分析及处理注塑和电镀是常见的制造工艺,在工业生产中得到广泛应用。
然而,这两种工艺在生产过程中难免会出现一些缺陷,影响产品的质量和外观。
因此,分析和处理这些缺陷是非常重要的。
本文将介绍注塑和电镀的常见缺陷,并提供相应的处理方法。
首先,注塑缺陷是指在注塑成型过程中出现的不良现象。
常见的注塑缺陷包括短注、气泡、烧结、射出不良等。
首先,短注是指注塑料未完全填充模具导致产品表面出现空洞或断裂。
短注的原因可能是模具设计不合理,射出速度过快或过慢,温度控制不当等。
处理短注的方法包括调整模具结构,调整射出速度和温度控制。
其次,气泡是指注塑过程中被困在产品内部或表面产生的气体泡泡。
气泡的形成可能是由于塑料中的水分引起的,温度和压力不稳定导致的。
处理气泡的方法包括加热塑料颗粒,增加模具通气孔,调整注塑过程中的温度和压力。
再次,烧结是指注塑过程中塑料或添加剂热分解并产生焦炭,导致产品表面发黑或有异味。
烧结的原因可能是注塑温度过高,停滞时间过长,模具表面有杂质等。
处理烧结的方法包括降低注塑温度,缩短停滞时间,保持模具清洁。
最后,射出不良是指注塑过程中塑料未完全填充模具导致产品表面出现凹陷或不光滑。
射出不良的原因可能是模具设计不合理,射出速度过快或过慢,射嘴不正等。
处理射出不良的方法包括调整模具结构,调整射出速度和射嘴位置。
除了注塑缺陷,电镀缺陷也是制造过程中常见的问题。
常见的电镀缺陷包括气泡、孔洞、颜色不均匀和剥落等。
首先,气泡是指电镀过程中,被电解液困住的气体形成气泡。
气泡的形成可能是由于电解液中含有水分,电镀时间过长或温度不稳定。
处理气泡的方法包括预处理金属表面,控制电解液的成分和温度。
其次,孔洞是指电镀过程中金属表面出现小孔的问题。
孔洞的原因可能是金属表面存在杂质或油污,电镀液配比不当等。
处理孔洞的方法包括清洁金属表面,优化电镀液配比。
再次,颜色不均匀是指电镀后金属表面出现色差或斑点。
颜色不均匀的原因可能是电解液的浓度不一致,电镀时间不稳定或金属表面存在杂质。
塑料电镀过程中常出现的缺陷及原因分析
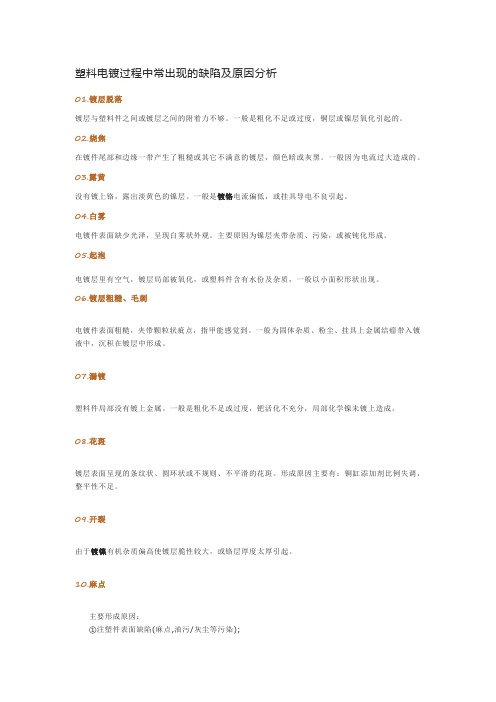
塑料电镀过程中常出现的缺陷及原因分析01.镀层脱落镀层与塑料件之间或镀层之间的附着力不够。
一般是粗化不足或过度,铜层或镍层氧化引起的。
02.烧焦在镀件尾部和边缘一带产生了粗糙或其它不满意的镀层,颜色暗或灰黑。
一般因为电流过大造成的。
03.露黄没有镀上铬,露出淡黄色的镍层。
一般是镀铬电流偏低,或挂具导电不良引起。
04.白雾电镀件表面缺少光泽,呈现白雾状外观。
主要原因为镍层夹带杂质、污染,或被钝化形成。
05.起泡电镀层里有空气,镀层局部被氧化,或塑料件含有水份及杂质,一般以小面积形状出现。
06.镀层粗糙、毛刺电镀件表面粗糙,夹带颗粒状疵点,指甲能感觉到。
一般为固体杂质、粉尘、挂具上金属结瘤带入镀液中,沉积在镀层中形成。
07.漏镀塑料件局部没有镀上金属。
一般是粗化不足或过度,钯活化不充分,局部化学镍未镀上造成。
08.花斑镀层表面呈现的条纹状、圆环状或不规则、不平滑的花斑。
形成原因主要有:铜缸添加剂比例失调,整平性不足。
09.开裂由于镀镍有机杂质偏高使镀层脆性较大,或铬层厚度太厚引起。
10.麻点主要形成原因:①注塑件表面缺陷(麻点,油污/灰尘等污染);②溶液杂质较多,杂质净化不彻底;③厂房内粉尘及其它污染物;④清洗水杂质;⑤厂房内酸雾易腐蚀镀层产生麻点;⑥设备故障造成零件掉落,产品长时间浸泡于药水中,镀层溶解,生成杂质;⑦搅拌空气源有尘埃及其它污染物;⑧挂具结瘤溶解于溶液,挂具破胶不易清洗,污染药水等。
11.露底麻点镀件微小的漏镀部分,如针孔一样大小。
主要形成原因:挂具结瘤带入杂质而溶解在钯缸及化学镍溶液;厂房内铬酸雾、盐酸雾污染零件表面;粗化,钯缸,解胶,化学镍等前处理溶液杂质。
12.针孔主要是镀镍层表面张力偏高,湿润剂量偏低而在镀层表面形成微小的孔穴,但不露出塑料基体。
塑料电镀常见故障分析和处理

塑料电镀常见故障分析和处理【慧聪表面处理网】1.零件表面都镀不上铜层出现这类故障的原因,一般是敏化液或活化液失效引起,还有可能是化学镀铜液中pH值、温度、甲醛、硫酸铜含量太低或络合剂含量太高而引起。
对这类故障的处理,应先检查敏化液、活化液或胶体钯溶液是否正常。
用新配制的少量敏化和活化液(或胶体钯溶液),如果粗化过的塑料零件经新配制的敏伊和活化液处理后能够沉积上铜层,证明原来的敏化液或活化液已失效,应调整或更换这些溶液。
若粗化过的浅色塑料零件,经过原来的敏化和活化溶液处理后,零件表面能变为棕褐色,说明敏化液和活化液未失效,应检查化学镀铜液。
在检查化学镀铜液时,先检查溶液的pH值和温度,将溶液的pH值调至12左右,温度控制在30℃左右,再补充适量的甲醛后进行试镀,若零件上仍不能沉积上铜层,则应从化学镀铜液的颜色(颜色浅)或成分分析,判断镀液中硫酸铜含量是否偏低,如果含量偏低,应补充适量的硫酸铜主盐。
经过这样的分析和处理,可以消除零件镀不上铜的现象。
2.化学镀铜时。
零件表面局部镀不上铜层零件局部镀不上与完全镀不上是不同的,出现这种故障的原因是:零件表面局部镀不上可能是除油不彻底;粗化不良;敏化或活化时间不够;塑料零件本身有应力或化学镀铜液成分失调等。
零件除油不彻底造成的镀不上仅发生在少数零件和零件的局部位置上,不会所有的零件表面都有油,因此,出现这种故障的现象是少数的,可以采取良好的除油措施消除;若塑料本身有应力引起的镀不上通常出现在零件的相似的部位,可以采取将少量零件经热处理去应力后,再按常用的粗化、敏化、活化和化学镀铜进行检查排除这种故障;化学镀铜液成分失调通常表现为沉铜速度慢。
如果在化学沉铜时,塑料件表面在5rain之内开始沉铜,那就不是镀铜液成分失调的问题;若化学镀铜时,塑料件零件表面在15min以上还没有铜层,那就可能是化学镀铜液的pH值太低、温度低、甲醛含量低、硫酸铜含量低或络合剂含量太高的原因,可以采取分析溶液按比例进行调整消除这种故障。
ABS塑料电镀中出现的问题及解决方法

ABS塑料电镀中出现的问题及解决方法近年来,塑料电镀已被广泛应用在塑料零件的装饰性电镀上。
ABS塑料是塑料电镀中应用最广的一种。
ABS塑料是丙烯腈(A)、丁二烯(B)、苯乙烯(S)的三元共聚物。
对电镀级ABS 塑料来说,丁二烯的含量对电镀影响很大,一般应控制在18%~23%。
丁二烯含量高,流动性好,易成型,与镀层附着力好。
由于ABS是非导体,所以电镀前必须附上导电层。
形成导电层要经过粗化、中和、敏化、活化、化学镀等几个步骤,比金属电镀复杂,在生产中容易出现问题。
我们从ABS塑料电镀的工艺出发,分析原因并找出了解决的办法。
2问题及解决方法2.1镀件易漂浮,与挂具接触的地方易被烧焦因为塑料的比重小,所以在溶液中易浮起。
灯罩外形就象一个小盘一样,内表面凹进去,边上有两个小孔,开始只用一根铜丝卡着两个小孔进行电镀。
由于电镀中气体的放出,灯罩易与铜丝脱离,加之铜丝也轻,不足以使灯罩浸入溶液里。
后来在铜丝上附上重物,解决了漂浮问题。
铜丝与灯罩的接触点被烧焦,并露出塑料,是因导电不良引起的。
为了解决工件漂浮与导电问题,我们设计了专门的夹具。
夹具有一定的重量,上灯罩后不再浮起,再用两个较宽的导电片卡在灯罩的孔上,使各处电流均匀,接触点就不会烧焦了。
2.2灯罩化学镀铜时出现气泡,电镀后气泡变大,并可以揭起塑料电镀的工艺流程为:除油→水洗→粗化→水洗→敏化→自来水洗→去离子水洗→活化→水洗→化学镀铜→水洗→电镀→水洗→干燥。
由以上可知,化学镀铜前的任何步骤出现问题都会导致鼓泡。
引起结合力不好的原因有很多,经常易出现问题的是除油过程和粗化过程。
除油不彻底,会引起掉皮、脱落。
灯罩采用的是化学除油(塑料件不适宜用有机溶剂除油),操作时,温度升高到65~70℃,不断地抖动工件,直到水洗后不挂水珠为止。
粗化是ABS塑料电镀中很重要的过程。
粗化不足,结合力下降;粗化过度,又会使孔变大变形,结合力也会降低。
由于敏化液中二价锡极不稳定,所以敏化液易失效,如不调整,会导致活化失败。
ABS塑料电镀常见问题与解决方案

ABS塑料电镀常见问题与解决方案近年来,塑料电镀已被广泛用于塑料工件的装饰性电镀上。
ABS 塑料是塑料电镀中应用最广的一种。
ABS塑料是丙烯腈(A)、丁二烯(B)、苯乙烯(s)的三元共聚物,丁二烯的含量对电镀的影响很大,一般应控制在18%.23%。
由于ABS是非导体,所以在电镀前必须使其表面金属化,即以化学法在塑料件表面上形成与基体有一定结合力的金属镀层.1工艺流程与配方本文中的工艺流程为:超声波除蜡一化学除油一水洗一表面活化一化学粗化一水洗一中和一水洗一敏化一钯缸一解胶一化学镍。
其中我们乐将分享给大家化学镀镍的配方为:硫酸镍 30g/L次亚磷酸钠 25g/L柠檬酸钠 20g/L三乙醇胺 20ml/L碳酸钠 4g/L氨水 20ml/L香豆素 0.03g/L温度55℃pH值 9.32常见问题与解决方案2.1漏镀漏镀是ABS塑料化学镀镍生产中经常出现的问题,,由于ABS塑料工件漏镀的部位不导电,所以在以后的电镀生产中漏镀的部位无金属沉积,导致产品质量不合格。
一般漏镀可分为片状漏镀与针孔漏镀两种类型,两者的成因有所不同,在此分别进行讨论。
2.1.1片状漏镀本工艺粗化液采用的是高浓度的铬酸与浓硫酸溶液,有时候由于粗化工序后水洗及中和过程不彻底,或者是因为工件形状复杂,其内部容易贮藏粗化溶液,导致在敏化工序过程中工件局部表面无法“抓”钯,甚至在进行化学镀镍时,工件内部残留的粗化液渐渗出将已沉积的化学镀镍层溶解,最终导致工件局部位置无化学镀镍层,这种由于工件上残留的粗化液导致的漏镀就是片状漏镀。
解决这种片状漏镀的方法主要是加强粗化后水洗与中和过程,尽量将工件上的粗化液冲洗或中和掉;对于某些因形状复杂容易贮藏粗化液的工件,应该改进其挂具设计,使其所贮藏的粗化液能迅速排出,必要时应在粗化后的水洗过程中将挂具从自动生产线支臂上取下,在水洗槽中做上下/右/前后剧烈摇动,或将挂具从水洗槽中取出并在空气中用力甩动,把挂具上工件贮藏的粗化液摇/甩出后再将工件放回原支臂上。
电镀常见的问题及解决方案

电镀常见的问题及解决方案
电镀过程中可能出现的问题及其解决方案如下:
1.针孔或麻点:这是由于前处理不良、有金属杂质、硼酸含量太少、镀液温度太低等原因造成的。
可以使用润湿剂来减小影响,并严格控制镀液维护及流程。
2.结合力低:如果铜镀层未经活化去氧化层,铜和镍之间的附着力就差,会产生镀层剥落现象。
因此,在电镀前应对基材进行适当的预处理,如酸洗、活化等。
3.镀层脆、可焊性差:这通常是由于有机物或重金属物质污染造成的。
添加剂过多会使镀层中夹带的有机物和分解产物增多,此时可以用活性炭处理或电解等方法除去重金属杂质。
4.镀层发暗和色泽不均匀:有金属污染可能是造成这一问题的原因。
应尽量减少挂具所沾的铜溶液,并在发现污染时立即处理。
5.镀层烧伤:这可能是由于硼酸不足、金属盐的浓度低、工作温度太低、电流密度太高、PH值太高或搅拌不充分等原因造成的。
需要检查并调整相关工艺参数,确保其处于合适的范围。
6.沉积速率低:PH值低或电流密度低都可能导致沉积速率低。
应检查并调整镀液的PH值和电流密度,以优化沉积速率。
7.其他问题:如辅助阳极的铜条未与生产板长度一致或已发粗,不允许再使用。
全板及图形镀后板需在24小时内制作下工序。
图形镀上板戴细纱手套,下板戴棕胶手套,全板上板戴橡胶手套,下板戴干燥的粗纱手套。
在处理电镀问题时,需要综合考虑多个因素,包括镀液成分、设备状况、操作条件等。
如遇到难以解决的问题,建议寻求专业人士的帮助。
塑胶电镀不良分析及改善对策(五)
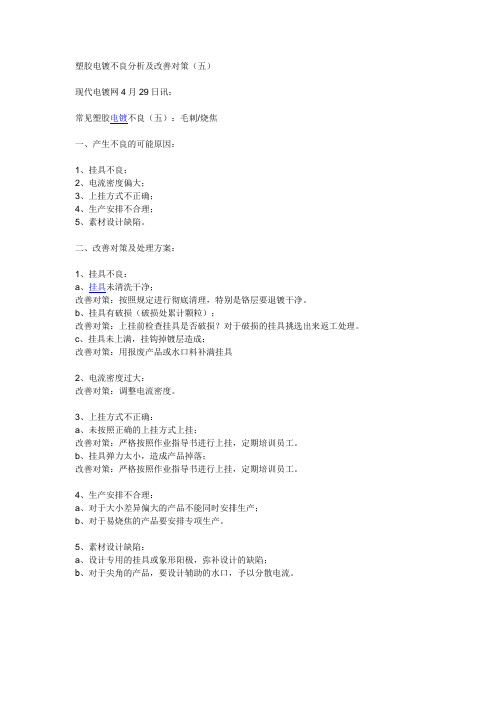
塑胶电镀不良分析及改善对策(五)
现代电镀网4月29日讯:
常见塑胶电镀不良(五):毛刺/烧焦
一、产生不良的可能原因:
1、挂具不良;
2、电流密度偏大;
3、上挂方式不正确;
4、生产安排不合理;
5、素材设计缺陷。
二、改善对策及处理方案:
1、挂具不良:
a、挂具未清洗干净;
改善对策:按照规定进行彻底清理,特别是铬层要退镀干净。
b、挂具有破损(破损处累计颗粒);
改善对策:上挂前检查挂具是否破损?对于破损的挂具挑选出来返工处理。
c、挂具未上满,挂钩掉镀层造成;
改善对策:用报废产品或水口料补满挂具
2、电流密度过大:
改善对策:调整电流密度。
3、上挂方式不正确:
a、未按照正确的上挂方式上挂;
改善对策:严格按照作业指导书进行上挂,定期培训员工。
b、挂具弹力太小,造成产品掉落;
改善对策:严格按照作业指导书进行上挂,定期培训员工。
4、生产安排不合理:
a、对于大小差异偏大的产品不能同时安排生产;
b、对于易烧焦的产品要安排专项生产。
5、素材设计缺陷:
a、设计专用的挂具或象形阳极,弥补设计的缺陷;
b、对于尖角的产品,要设计辅助的水口,予以分散电流。
电镀不良的一些情况和解决方法

电镀不良的一些情况和解决方法电镀不良对策镀层品质不良的发生多半为电镀条件,电镀设备或电镀药水的异常,及人为疏忽所致.通常在现场发生不良时比较容易找出塬因克服,但电镀后经过一段时间才发生不良就比较棘手.然而日后与环境中的酸气,氧气,水分等接触,加速氧化腐蚀作用也是必须注意的.以下本章将对电镀不良的发生塬因及改善的对策加以探讨说明.1.表面粗糙:指不平整,不光亮的表面,通常成粗白状(1)可能发生的塬因: (2)改善对策:1.素材表面严重粗糙,镀层无法覆盖平整. 1.若为素材严重粗糙,立即停产并通知客户.2.金属传动轮表面粗糙,且压合过紧,以至于压伤. 2.若传动轮粗糙,可换备用品使用并检查压合紧度.3.电流密度稍微偏高,部分表面不亮粗糙(尚未烧焦) 3.计算电流密度是否操作过高,若是应降低电流4.浴温过低,一般镀镍才会发生) 4.待清晰度回升再开机,或降低电流,并立即检查温控系统.5.PH值过高或过低,一般镀镍或镀金(过低不会)皆会发生. 5.立即调整PH至标准范围.6.前处理药液腐蚀底材. 6.查核前处理药剂,稀释药剂或更换药剂2.沾附异物:指端子表面附着之污物.(1)可能发生的塬因: (2)改善对策:1.水洗不干净或水质不良(如有微菌). 1.清洗水槽并更换新水.2.占到收料系统之机械油污. 2.将有油污处做以遮蔽.3.素材带有类似胶状物,于前处理流程无法去除. 3.须先以溶剂浸泡处理.4.收料时落地沾到泥土污物. 4.避免落地,若已沾附泥土可用吹气清洁,浸透量很多时,建议重新清洗一次.5.锡铅结晶物沾附 5.立即去除结晶物.6刷镀羊毛?纤维丝 6.更换羊毛?并检查接触压力.7.纸带溶解纤维丝. 7.清槽.8.皮带脱落屑. 8.更换皮带.3.密着性不良:指镀层有剥落.起皮,起泡等现象.(1)可能发生的塬因: (2).改善对策:1.前处理不良,如剥镍. 1.加强前处理.2.阴极接触不良放电,如剥镍,镍剥金,镍剥锡铅. 2.检查阴极是否接触不良,适时调整.3.镀液受到严重污染. 3.更换药水4.产速太慢,底层再次氧化,如镍层在金槽氧化(或金还塬),剥锡铅. 4,电镀前须再次活化.5.水洗不干净. 5.更换新水,必要时清洗水槽.6.素材氧化严重,如氧化斑,热处理后氧化膜. 6.必须先做除锈及去氧化膜处理,一般使用化学抛光或电解抛光.7.停机化学置换反应造成. 7.必免停机或剪除不良品8,操作电压太高,阴极导电头及镀件发热,造成镀层氧化. 8.降低操作电压或检查导线接触状况9,底层电镀不良(如烧焦),造成下一层剥落. 9.改善底层电镀品质.10.严重.烧焦所形成剥落 10.参考NO12处理对策.4.露铜:可清楚看见铜色或黄黑色于低电流处(凹槽处)(1)可能发生塬因: (2)改善对策:1.前处理不良,油脂,氧化物.异物尚未除去,镀层无法析出. 1.加强前处理或降低产速2.操作电流密度太低,导致低电流区,镀层无法析出. 2.重新计算电镀条件.3镍光泽剂过量,导致低电流区,镀层无法析出 3.处理药水,去除过多光泽剂或更新.4.严重刮伤造成露铜. 4.检查电镀流程,(查参考NO5)5.未镀到. 5.调整电流位置.5刮伤:指水平线条状,一般在锡铅镀层比较容易发生.(1)可能发生的塬因: (2)改善对策:1.素材本身在冲压时,及造成刮伤. 1.停止生产,待与客户联系.2.被电镀设备中的金属制具刮伤,如阴极头,烤箱定位器,导轮等. 2.检查电镀流程,适时调整设备和制具.3.被电镀结晶物刮伤. 3.停止生产,立即去除结晶物.6.变形(刮歪):指端子形状已经偏离塬有尺寸或位置.(1)可能发生的塬因: (2)改善对策:1.素材本身在冲压时,或运输时,即造成变形. 1.停止生产,待与客户联系.2.被电镀设备,制具刮歪(如吹气.定位器,振荡器,槽口,回转轮) 2.检查电镀流程,适时调整设备和制具.3.盘子过小或卷绕不良,导致出入料时刮歪 3.停止生产,适时调整盘子4.传动轮转歪, 4.修正传动轮或变更传动方式.7压伤:指不规则形状之凹洞可能发生的塬因:改善对策:1)本身在冲床加工时,已经压伤,镀层无法覆盖平整2)传动轮松动或故障不良,造成压合时伤到 1)停止生産,待与客户联2)检查传动机构,或更换备品8白雾:指镀层表面卡一层云雾状,不光亮但平整可能发生的塬因:1)前处理不良2)镀液受污染3)锡铅层爱到酸腐蚀,如停机时受到锡铅液腐蚀4)锡铅药水温度过高5)锡铅电流密度过低6)光泽剂不足7)传致力轮脏污8)锡铅电久进,産生泡沫附着造成改善对策:1)加强前处理2)更换药水并提纯污染液3)避免停机,若无法避免时,剪除不良4)立即检查温控系统,并重新设定温度5)提高电流密度6)补足不泽剂传动轮7)清洁传动轮8)立即去除泡沫9针孔:指成群、细小圆洞状(似被钟扎状)可能发生的塬因:改善对策:1.操作的电流密度太 1.降低电流密度2.电镀溶液表面张力过大,湿润剂不足。
- 1、下载文档前请自行甄别文档内容的完整性,平台不提供额外的编辑、内容补充、找答案等附加服务。
- 2、"仅部分预览"的文档,不可在线预览部分如存在完整性等问题,可反馈申请退款(可完整预览的文档不适用该条件!)。
- 3、如文档侵犯您的权益,请联系客服反馈,我们会尽快为您处理(人工客服工作时间:9:00-18:30)。
塑料电镀多种问题解决措施塑料电镀,国际上在20世纪50年代已形成规模生产,我国在60~80年代也实现了工业化,当时主要用于纽扣、带扣等小产品,要求镀层不脱皮、表面象金属一样即可。
时代在发展,塑料电镀的应用也在不断扩大,由原来的小件、少量的应用发展到大件、大量的使用,从装饰性用途到功能和工程性用途等,因此对镀层质量的要求也越来越高。
一、塑料电镀问题
(1)外观质量。
塑料电镀外观要求比金属制品电镀面更光洁,光亮度一般都能达到,但其程度上就有一定差别。
通常认为,较好外观亮发“乌黑”,光亮度视觉感很“厚实”。
这种宏观感觉由表面微观状态所决定,也就说微观表面必须非常平整。
镀层绝对不能有雾状存,极轻微雾状,强光下或正视时发现不了,要特定角度光线下才能发现,因此易被忽视。
至于露塑、脱皮、毛刺、麻点深镀差等缺陷,电镀绝对不允许存。
某些次要考核部位及反面等各部位都要有镀层包覆,且色泽鲜亮,不能发黑、露塑及有夹具拉毛印。
(2)内质量
汽车、摩托车零件或更高档零件电镀,技术规格上都有一定要求:如镀层结合力,耐铜盐乙酸腐蚀试验,热循环试验以及实地使用考验等,需装配镀件还要有一定程度耐变形要求。
二、解决措施
(1)镀前毛坯质量要良好
不合格毛坯镀不好,塑料毛坯比金属毛坯还要难以检查。
镀好后会有“麻点”或“星点”。
因此,要重视镀前毛坯质量。
首先要了解客户产品来源,否镀过,特别注件,不第一批压注,以便确定毛坯质量。
对不良毛坯,必须经过布轮抛光,使之达到镀前要求。
目前,国内电镀质量水平较好厂家,就采用这种措施,其成品合格率一般可达到90%以上。
当然,毛坯不经抛光也能镀出良好产品,全套注塑毛坯表面非常光洁,注模表面光亮如镜,塑料件注出后应各个分装,决不能碰撞。
(2)前处理金属化镀件不要碰撞
前处理各道工序镀件不能碰撞,尤其70℃左右浸蚀粗化工序,ABS塑料软化增加,硬度降低,如果碰撞很容易擦花,镀后必有印点。
若高要求镀件,尤其比较大或平面较光镀件,绝对不允许随便放入浸蚀液,浸蚀后用网取出清洗,要求将产品装上夹具浸蚀,直至化学铜或化学镍。
(3)浸蚀程度控制
浸蚀为了使被镀件表面状态达到适宜要求,浸蚀不足或过度都会造成镀后产品光洁度欠佳或镀层结合力不好。
镀层光洁度一方面依赖亮铜亮镍镀亮,另一方面也不能忽视对浸蚀程度控制。
日本很多电镀全套都线上完成,浸蚀一般不超过3min。
(4)镀液不能浑浊
金属化方法一般铜层或镍层,各有利弊,从操作上看,无电解镀
镍比较稳定,镀速较快。
此外,它还可以省去昂贵钯盐,成本略低,但稳定性较差。
镀液要保持清洁不能浑浊,防止微小粒子沉积,否则镀亮铜时会把微小粒子“放大”,形成颗粒毛疵。
金属化后要清洗拭揩,特别大件平面镀件,以防止粉粒存,尤其金属化铜层不能省去此工序。
这个过程对于较大镀件,有可能出现一些小点或小局部露塑,可采取局部修补,用银浆、导电胶或软铅芯笔修补,对提高成品合格率确有好处。
当今塑料电镀的质量要求不断提升的动力在于我国外资企业的发展,尤其是日本、韩国与我国的台湾省,对大陆的产品加工,质量要求的提高。
当前,我国广东、江浙地区的镀件质量水平较高,其外观能与国外先进产品相媲美,达到外资企业质量的要求。
但内在质量因测试手段和测试的规范还不健全而参差不齐。