合成氨变换工段
合成氨生产作业变换岗位操作规程

合成氨生产作业变换岗位操作规程一、本岗位任务1、变换:压缩三段来半水煤气,在一定温度、压力催化剂的条件下使CO 与水蒸汽反应,将CO 转换为CO 2脱除至规定的指标(≤0.5%)范围内,同时生成合成氨生产所需的原料气H 2,并在中变触媒的作用下将90%以上的有机硫转变为无机硫。
负责向合成、岗位输送合格的除氧水、脱盐水。
二、反应原理:1、变换工段反应原理:CO 在一定条件下,半水煤气中的CO 与水蒸汽反应,转变为CO2、H 2 的工艺过程,其反应的化学方程式如下:CO+H 2O =CO 2+H 2+41KJ/MOL反应特点:这是一个可逆放热反应,从化学平衡来看,降低反应温度,增加水蒸汽的用量,有利于上述反应生成CO 2、H 2的方向移动,从而提高平衡转换率。
另外提高变换压力,可加快变换反应速度,提高催化剂的催化能力。
2、中变触媒还原反应原理:中变触媒装炉时状态为Fe 2O 3,其本身并不具有活性,必须将其进行还原后,才具有活性,具体反应为:3Fe 2O 3+CO =2Fe 3O 4+CO 2 3Fe 2O 3+H 2=2Fe 3O 4+H 2O还原态的触媒极易与氧发生氧化反应,放出大量的氧化热,所以还原过程中要严格控制氧含量,严防因氧超标,烧坏触媒。
氧化反应为:4Fe 3O 4+O 2=6Fe 2O 3低变触媒硫化反应原理:低变触媒使用前为氧化钴,氧化钼它本身不具有催化活性,必须将其硫化后才具有活性,硫化反应为:C O O+H 2S=C O S+H 2O M O O 3+2H 2S+H 2=M O S 2+3H 2O三、工艺流程 1、工艺流程简图⑴变换工序气相流程简图 水煤气 dffhhjj变换气 变换气⑵软水流程除油器压缩三出来气 饱和塔 分离器热交管内中变电加 中变一二 段中变三段热交段中间二段第二增湿器分离器 冷却器软水加热器热水塔电厂来脱盐水 机械除油器除氧器除氧泵热水塔一、二增湿器 恩德中压蒸汽 热交管间下 第二增湿器 低变一段调温水加低变二三段一水加去脱碳循环冷却水焦炭过滤器软水加热器合成废锅 低压蒸汽2、工艺流程叙述⑴变换工序:变换工艺采用中低变换工艺。
合成氨变换工段工艺中变串低变换热设计
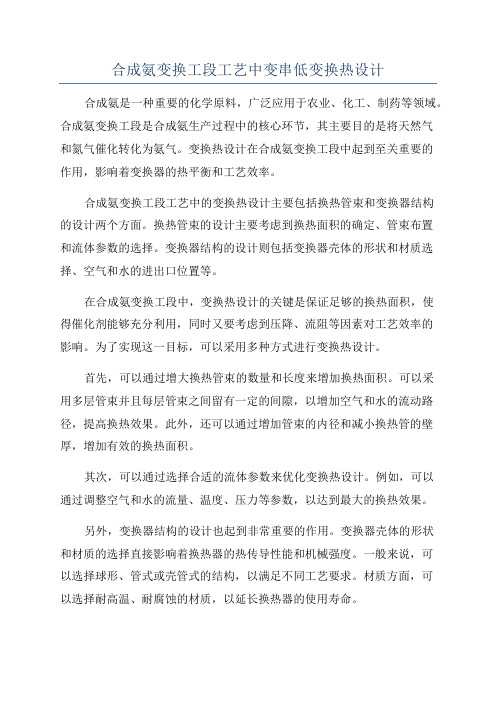
合成氨变换工段工艺中变串低变换热设计合成氨是一种重要的化学原料,广泛应用于农业、化工、制药等领域。
合成氨变换工段是合成氨生产过程中的核心环节,其主要目的是将天然气和氮气催化转化为氨气。
变换热设计在合成氨变换工段中起到至关重要的作用,影响着变换器的热平衡和工艺效率。
合成氨变换工段工艺中的变换热设计主要包括换热管束和变换器结构的设计两个方面。
换热管束的设计主要考虑到换热面积的确定、管束布置和流体参数的选择。
变换器结构的设计则包括变换器壳体的形状和材质选择、空气和水的进出口位置等。
在合成氨变换工段中,变换热设计的关键是保证足够的换热面积,使得催化剂能够充分利用,同时又要考虑到压降、流阻等因素对工艺效率的影响。
为了实现这一目标,可以采用多种方式进行变换热设计。
首先,可以通过增大换热管束的数量和长度来增加换热面积。
可以采用多层管束并且每层管束之间留有一定的间隙,以增加空气和水的流动路径,提高换热效果。
此外,还可以通过增加管束的内径和减小换热管的壁厚,增加有效的换热面积。
其次,可以通过选择合适的流体参数来优化变换热设计。
例如,可以通过调整空气和水的流量、温度、压力等参数,以达到最大的换热效果。
另外,变换器结构的设计也起到非常重要的作用。
变换器壳体的形状和材质的选择直接影响着换热器的热传导性能和机械强度。
一般来说,可以选择球形、管式或壳管式的结构,以满足不同工艺要求。
材质方面,可以选择耐高温、耐腐蚀的材质,以延长换热器的使用寿命。
最后,合成氨变换工段的变换热设计还需要考虑到安全性和可靠性。
例如,需要保证换热器的壳体有足够的强度,能够承受工作压力和温度的变化。
此外,还需要考虑到清洗和维护的便利性,以减少生产中的停机时间和成本。
总之,合成氨变换工段工艺中的变换热设计是一个复杂而关键的问题。
通过合理的换热管束和变换器结构设计,可以实现高效、安全、可靠的合成氨生产。
合成氨变换工段工艺设计

合成氨变换工段工艺设计合成氨是化工工业中的重要原料,广泛应用于制取尿素、硝化铵等农业肥料,以及制取氨水、氨盐、化肥、染料等合成工艺中。
合成氨变换工段是合成氨生产中的关键环节,其工艺设计对合成氨的产量、质量以及能耗等方面有重要影响。
一、工艺概述合成氨的变换反应器是将反应物氮气和氢气通过催化剂的作用,在一定条件下发生气相合成反应,生成合成氨。
反应器通常采用固定床催化剂反应器,催化剂的选择和催化剂床层的设计都是工艺设计的重要环节。
冷凝器主要用于对反应产生的氨气进行冷凝回收,常见的冷凝器有直接冷凝器和间接冷凝器两种形式,工艺设计中需要根据具体情况选择适用的冷凝方式。
循环气压缩机主要用于将反应器中未反应的气体通入新的循环,提高气相合成反应的转化率。
在工艺设计中,需要考虑压缩机的压比、功率消耗等参数。
氨气的分离净化装置主要用于对合成氨中的杂质进行去除,提高合成氨的纯度。
常用的分离净化装置有吸附装置、膜分离装置等,具体的工艺设计需要根据生产要求和经济效益进行选择。
二、工艺参数及控制合成氨的变换工段的工艺参数主要包括反应温度、反应压力、空速、催化剂活性等。
这些参数直接影响合成氨的产率、选择性和能耗。
反应温度是合成氨变换反应的重要参数,通过控制温度可以提高反应速率和转化率,但过高的温度会导致副反应的发生,降低合成氨的选择性。
反应压力主要用于控制氨气的产量和能耗,压力越高产氨越多,但能耗也相应增加。
空速是指单位时间内通过反应器的氮气体积,可以通过调控压力和进气量来实现,过小的空速会影响反应的效果,而过大会导致固定床催化剂的床层冲击和阻力升高,影响反应转化率。
催化剂活性主要指催化剂的活性组分含量和粒径等参数,这些参数会影响合成氨的选择性和催化剂的寿命。
在工艺设计中,需要考虑这些参数的合理选择和控制,以提高合成氨的产量和质量,并降低能耗。
三、能耗控制合成氨的变换工段是合成氨生产中的能耗重点。
能耗的控制主要体现在压力控制、催化剂选择和热交换等方面。
合成氨生产中变换工段的设计

合成氨生产中变换工段的设计
合成氨是化学工业中重要的基础产品,遍布在各个工业应用之中。
为保证合成氨的质量,改造变换工段绝对是大势所趋。
首先,利用先进的技术来改进变换工段,增加产品的质量和效率。
在传统的合成氨设计中,由于变换工段的设计有很大的不足,耗损了大量的能量和原料,从而导致产品质量下降。
因此,现在开始利用现代化技术对变换工段进行改进。
通过改进,可以减少此工段中能量及原料的损耗,从而保证产品质量,增加产品的产量,同时还可增加效率。
其次,实现工段的自动化。
传统的合成氨设计中,每个工序都是手动完成的,需要大量的人力和物力,会导致成本高,工艺操作尚未实现自动化。
为了节省成本,实现高效的生产,现在可以采用工段的自动化技术来实现。
实施后能够减少生产过程中的人力,加快生产进度,同时实现高效和高质量的生产。
最后,建立完善的质量控制体系。
随着生产技术的发展,合成氨工段的质量控制很重要。
因此,必须建立一套完善的质量保证体系,在于执行有关的质量管理措施。
通过完善的质量保证体系,可以有效地提高产品的质量,满足消费者的需求,有利于长期的企业发展。
总之,改进变换工段是当前合成氨生产中一个必要的改革,它可以减少损耗,提高产品质量,同时实现高生产效率和更高的质量。
采用现代化技术,实现自动化,建立完善的质量控制体系,都对保证合成氨高质量有着不可替代的作用。
年产10万吨合成氨变换工段工艺设计
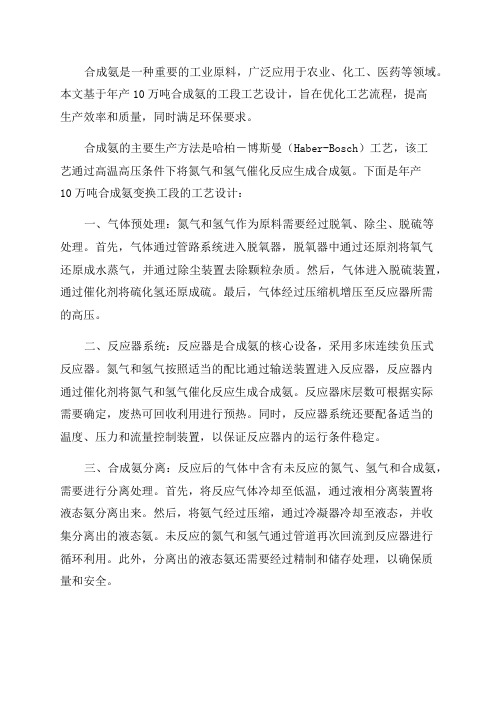
合成氨是一种重要的工业原料,广泛应用于农业、化工、医药等领域。
本文基于年产10万吨合成氨的工段工艺设计,旨在优化工艺流程,提高生产效率和质量,同时满足环保要求。
合成氨的主要生产方法是哈柏-博斯曼(Haber-Bosch)工艺,该工艺通过高温高压条件下将氮气和氢气催化反应生成合成氨。
下面是年产10万吨合成氨变换工段的工艺设计:一、气体预处理:氮气和氢气作为原料需要经过脱氧、除尘、脱硫等处理。
首先,气体通过管路系统进入脱氧器,脱氧器中通过还原剂将氧气还原成水蒸气,并通过除尘装置去除颗粒杂质。
然后,气体进入脱硫装置,通过催化剂将硫化氢还原成硫。
最后,气体经过压缩机增压至反应器所需的高压。
二、反应器系统:反应器是合成氨的核心设备,采用多床连续负压式反应器。
氮气和氢气按照适当的配比通过输送装置进入反应器,反应器内通过催化剂将氮气和氢气催化反应生成合成氨。
反应器床层数可根据实际需要确定,废热可回收利用进行预热。
同时,反应器系统还要配备适当的温度、压力和流量控制装置,以保证反应器内的运行条件稳定。
三、合成氨分离:反应后的气体中含有未反应的氮气、氢气和合成氨,需要进行分离处理。
首先,将反应气体冷却至低温,通过液相分离装置将液态氨分离出来。
然后,将氨气经过压缩,通过冷凝器冷却至液态,并收集分离出的液态氨。
未反应的氮气和氢气通过管道再次回流到反应器进行循环利用。
此外,分离出的液态氨还需要经过精制和储存处理,以确保质量和安全。
四、废气处理:合成氨生产中会产生大量的废气,包括未反应的氮气、氢气、氨气和其他杂质气体。
废气处理主要包括低温分离、吸收、洗涤等步骤。
首先,废气通过低温分离装置将其中的液态氨和水分离出来。
然后,通过吸收剂将氨气吸收,以减少其排放。
最后,利用洗涤液去除废气中的其他杂质气体,确保废气达到环境排放标准。
五、能耗优化:为了降低能耗和提高生产效率,可以采用余热回收和过程优化等措施。
余热回收可通过换热器将反应废热回收利用,进行气体预热和水蒸气生产。
「年产三万吨合成氨厂变换工段工艺设计」

年产三万吨合成氨厂变换工段工艺设计一、工艺流程概述1.原料准备:将天然气(主要是甲烷)与空气作为主要原料,通过气体净化系统去除其中的杂质、硫化物和水分。
2.原料配送:将净化后的天然气和空气分别输送至气体净化系统进行进一步的处理和分析。
3.变换反应槽:将净化后的天然气和空气通过压缩机压缩至一定压力后,经过暖气交换器加热至高温(约500-600℃),再进入变换反应槽。
4.变换催化剂:在变换反应槽中,使用催化剂(通常是高温高压下的铁-钴催化剂)促进N2和H2的反应。
反应生成的合成氨会随气流从反应槽中流出。
5.除气系统:将反应槽中的气体通过除尘器,冷却器和吸附剂等设备进行处理,去除其中的固体颗粒、水分和其他杂质。
6.合成氨回收:经过除气系统处理后的气体中仍含有未反应的氮气和氢气,通过压缩机再次压缩进入蒸馏塔。
在蒸馏塔中,根据不同的沸点,将氨气和氮气分离开来,再通过冷凝器冷凝为液态氨。
7.废水处理:在工艺过程中产生的废水会经过处理系统去除其中的有机物和杂质,以保证排放的废水符合环保要求。
二、设备布置和操作要点1.变换反应槽的设计要考虑到温度、压力和气体流动速度的控制。
同时,需要定期更换催化剂,以维持优良的反应性能。
2.除气系统中的设备要进行定期维护和清洁,确保其正常工作和去除气体中的杂质、固体颗粒和水分。
3.合成氨回收装置要根据产品质量要求设置合适的操作参数,例如蒸馏塔的温度和压力。
此外,冷凝器的冷却水流需要保持稳定,以确保气体顺利冷凝为液态氨。
4.废水处理系统应配置适当的物理和化学处理单元,如过滤器、沉淀池和生物处理等,以达到废水排放标准。
5.需要建立相应的安全措施,如设立监测系统,确保气体和液体在整个工艺中的安全运输和使用。
三、工艺控制和性能优化1.在变换反应槽中,可以通过调节供气比例、压力和温度等参数来控制合成氨的产率和选择性。
同时,也可以根据反馈控制系统监测和调整催化剂的性能。
2.除气系统中的设备可以通过监测气体的组成和温度、压力等参数,来调整操作参数,以达到满足产品质量要求的除气效果。
合成氨变换工段工艺设计

合成氨变换工段工艺设计1. 引言合成氨是一种重要的化工原料,在农业、化工和医药等行业广泛应用。
合成氨的生产过程中,合成氨变换工段是一个关键的工艺环节。
本文将介绍合成氨变换工段的工艺设计。
2. 工艺流程合成氨变换工段的工艺流程包括进料处理、反应器设计、温度控制和产品回收四个重要环节。
2.1 进料处理合成氨的主要原料是氮气和氢气,进料处理环节主要包括氮气和氢气的纯化和混合。
氮气和氢气需要通过特定的纯化设备去除杂质,以确保反应的纯度和效果。
然后,纯化后的氮气和氢气按照一定比例进行混合。
2.2 反应器设计反应器是合成氨变换工段的核心设备,根据反应器设计的不同,可以分为固定床反应器和流化床反应器两种。
固定床反应器是一种较为常见的反应器形式,氮气和氢气催化反应产生合成氨。
固定床反应器需要考虑催化剂的选择、填充物的设计以及反应器的传热设计等因素。
流化床反应器是近年来逐渐应用的一种反应器形式,其优点包括更好的热传递性能和更好的反应效果。
流化床反应器需要考虑反应器的气固分离、催化剂的循环和再生等因素。
2.3 温度控制温度对合成氨反应的影响非常重要,合适的反应温度可以提高反应速率和选择性。
在合成氨变换工段中,需要通过控制进料气体的温度和反应器的温度来实现对反应的控制。
温度控制还需要考虑热量的平衡问题,包括进料气体的预热和产物蒸汽的回收利用等。
2.4 产品回收合成氨变换工段的最终目标是获得高纯度的合成氨产品。
在产品回收环节中,需要进行氨的冷凝和气液分离。
冷凝过程中需要考虑温度和压力的控制,以确保氨的高效冷凝。
气液分离过程中,可以采用吸收液的方式将氨从气相中吸收出来,再进行后续处理和精制。
3. 设备选择合成氨变换工段的设备选择主要包括反应器、纯化设备、冷凝器和分离器等。
反应器的选择需要考虑反应速率、选择性和热传导等因素。
常用的反应器材料有不锈钢、镍基合金等。
纯化设备的选择需要考虑氮气和氢气的纯度要求以及生产规模等因素。
合成氨变换工段设计
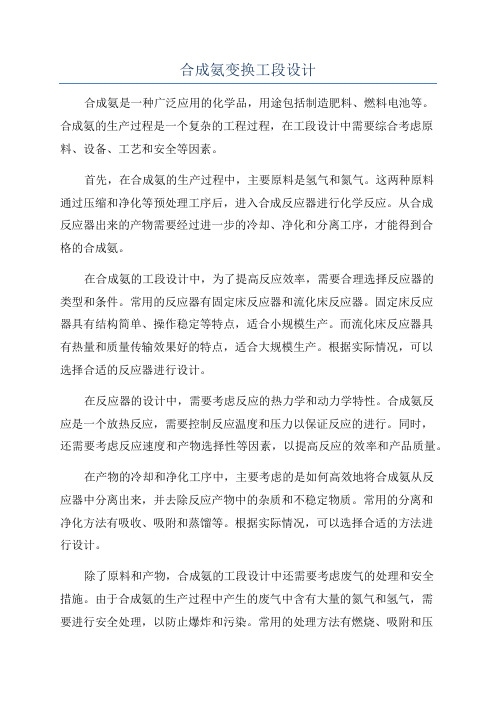
合成氨变换工段设计合成氨是一种广泛应用的化学品,用途包括制造肥料、燃料电池等。
合成氨的生产过程是一个复杂的工程过程,在工段设计中需要综合考虑原料、设备、工艺和安全等因素。
首先,在合成氨的生产过程中,主要原料是氢气和氮气。
这两种原料通过压缩和净化等预处理工序后,进入合成反应器进行化学反应。
从合成反应器出来的产物需要经过进一步的冷却、净化和分离工序,才能得到合格的合成氨。
在合成氨的工段设计中,为了提高反应效率,需要合理选择反应器的类型和条件。
常用的反应器有固定床反应器和流化床反应器。
固定床反应器具有结构简单、操作稳定等特点,适合小规模生产。
而流化床反应器具有热量和质量传输效果好的特点,适合大规模生产。
根据实际情况,可以选择合适的反应器进行设计。
在反应器的设计中,需要考虑反应的热力学和动力学特性。
合成氨反应是一个放热反应,需要控制反应温度和压力以保证反应的进行。
同时,还需要考虑反应速度和产物选择性等因素,以提高反应的效率和产品质量。
在产物的冷却和净化工序中,主要考虑的是如何高效地将合成氨从反应器中分离出来,并去除反应产物中的杂质和不稳定物质。
常用的分离和净化方法有吸收、吸附和蒸馏等。
根据实际情况,可以选择合适的方法进行设计。
除了原料和产物,合成氨的工段设计中还需要考虑废气的处理和安全措施。
由于合成氨的生产过程中产生的废气中含有大量的氮气和氢气,需要进行安全处理,以防止爆炸和污染。
常用的处理方法有燃烧、吸附和压缩等。
同时,还需要配备相应的安全设施,如安全阀、警报器等,以保证生产过程的安全性。
在合成氨的工段设计中,还需要考虑设备的选型和布局。
设备的选型要根据生产量、质量要求和经济效益等因素进行综合考虑。
设备的布局要根据设备之间的流程要求和工艺条件进行合理安排,以提高生产效率和安全性。
总之,合成氨的工段设计是一个综合考虑原料、设备、工艺和安全等因素的过程。
只有根据实际情况进行合理的设计,才能保证合成氨的生产过程稳定、高效和安全。
- 1、下载文档前请自行甄别文档内容的完整性,平台不提供额外的编辑、内容补充、找答案等附加服务。
- 2、"仅部分预览"的文档,不可在线预览部分如存在完整性等问题,可反馈申请退款(可完整预览的文档不适用该条件!)。
- 3、如文档侵犯您的权益,请联系客服反馈,我们会尽快为您处理(人工客服工作时间:9:00-18:30)。
30kt/a合成氨变换工段工艺初步设计摘要变换工段是指一氧化碳与水蒸气反应生成二氧化碳和氢气的过程。
一氧化碳变换既是原料气的净化过程,又是原料气制备的继续。
目前,变换工段主要采用中变串低变的工艺流程。
本设计针对中低温串联变换流程进行设计,对流程中各个设备进行物料、能料衡算、以及设备选型,并绘制了带控制点的流程图。
关键词:合成氨,变换,工艺设计,设备选型30kt/a Retention Of Ammonia SynthesisProcess Preliminary DesignAbstactTransform section refers to the reactions that produce carbon dioxide carbon monoxide and hydrogen and water vapor in the process. Carbon monoxide transformation is the gas material purification process, and the preparation of gas material to continue. At present, the transformation mainly by grow string sections of variable process low. This design of low-temperature series transformation process of process design, materials, each device can material calculation, and the equipment selection, and plotted take control in the flow chart and variable furnace equipment assembly drawing.Keywords:ammonia, transformation, process design,equipment choice目录摘要 (Ⅰ)ABSTRACT (Ⅱ)1绪论 ............................................................................................................. 错误!未定义书签。
1.1前言.............................................................................................................. 错误!未定义书签。
1.2 氨的性质和用途....................................................................................... 错误!未定义书签。
1.2.1 氨的物理性质 .................................................................................... 错误!未定义书签。
1.2.2氨的化学性质 ....................................................................................... 错误!未定义书签。
1.2.3氨的用途 ............................................................................................... 错误!未定义书签。
1.3变换工艺原理.............................................................................................. 错误!未定义书签。
1.4工艺条件...................................................................................................... 错误!未定义书签。
1.4.1 压力...................................................................................................... 错误!未定义书签。
1.4.2 温度...................................................................................................... 错误!未定义书签。
1.4.3汽气比 ................................................................................................... 错误!未定义书签。
1.5工艺流程确定.............................................................................................. 错误!未定义书签。
1.5.1工艺流程简图 ....................................................................................... 错误!未定义书签。
1.5.2流程工序简述 ....................................................................................... 错误!未定义书签。
1.5.3主要设备的选择说明 ............................................................................. 错误!未定义书签。
2物料与热量衡算................................................................................... 错误!未定义书签。
2.1已知条件...................................................................................................... 错误!未定义书签。
2.2中变炉的物料与热量衡算.......................................................................... 错误!未定义书签。
2.2.1水气比的确定 ....................................................................................... 错误!未定义书签。
2.2.2中变炉CO的实际变换率的求取........................................................ 错误!未定义书签。
2.2.3中变炉的物料衡算 ............................................................................... 错误!未定义书签。
2.2.4对出中变炉的变换气的温度进行估算 ............................................... 错误!未定义书签。
2.2.5中变炉的热量衡算 ............................................................................... 错误!未定义书签。
2.2.6中变炉催化剂平衡曲线 ....................................................................... 错误!未定义书签。
2.2.7最佳温度曲线的计算 ........................................................................... 错误!未定义书签。
2.2.8 中变催化剂操作线的计算 .................................................................. 错误!未定义书签。
2.3低变炉的物料与热量衡算 (14)2.3.1低变炉CO的实际变换率的求取........................................................ 错误!未定义书签。
III2.3.2.低变炉的物料衡算............................................................................... 错误!未定义书签。
2.3.3对出低变炉的变换气温度进行估算 ................................................... 错误!未定义书签。
2.3.4低变炉的热量衡算 (17)2.3.5低变炉平衡曲线、最适宜温度曲线及操作线计算 (18)2.4废热锅炉的热量和物料衡算 (20)2.4.1物料衡算 (20)2.4.2热量衡算 (21)2.5水蒸汽的加入 (22)2.6主换器的物料与热量的衡算 (22)2.6.1物料衡算 (22)2.6.2热量计算 (23)2.7调温水加热器的物料与热量衡算.............................................................. 错误!未定义书签。
3设备的计算 ............................................................................................. 错误!未定义书签。
3.1中变炉的计算.............................................................................................. 错误!未定义书签。