「年产三万吨合成氨厂变换工段工艺设计」
【毕业设计】年产30万吨合成氨工艺设计

毕业设计题目名称:年产30万吨合成氨转变工序设计系别:化学工程系专业:应用化学班级: 06101学生:学号:指导教师(职称):(教授)摘要氨是重要的基础化工产品之一,在国民经济中占有重要地位。
合成氨生产经过多年的发展,现已发展成为一种成熟的化工生产工艺。
本设计是以天然气为原料年产三十万吨合成氨转变工序的设计。
近年来合成氨工业发展很快,大型化、低能耗、清洁生产均是合成氨设备发展的主流,技术改进主要方向是开发性能更好的催化剂、降低氨合成压力、开发新的原料气净化方法、降低燃料消耗、回收和合理利用低位热能等方面上。
设计采用的工艺流程简介:天然气经过脱硫压缩进入一段转化炉,把CH4和烃类转化成H2,再经过二段炉进一步转化后换热进入高变炉,在催化剂作用下大部分CO和水蒸气反应获H2和CO2,再经过低变炉使CO降到合格水平,去甲烷化工序。
本设计综述部分主要阐述了国内外合成氨工业的现状及发展趋势以及工艺流程、参数的确定和选择,论述了建厂的选址;介绍了氨变换工序的各种流程并确定本设计高-低变串联的流程。
工艺计算部分主要包括转化段和变换段的物料衡算、热量衡算、平衡温距及空速计算。
设备计算部分主要是高变炉催化剂用量的具体计算,并根据设计任务做了转化和变换工序带控制点的工艺流程图。
本设计的优点在于选择较为良好的厂址和原料路线,确定良好的工艺条件、合理的催化剂和能源综合利用。
另外,就是尽量减少设备投资费用。
关键字:合成氨;天然气;转化;变换;AbstractAmmonia is the most important one of basic chemical products, plays an important role in the national economy. Ammonia production after years of development, now has developed into a mature chemical production processes. The design is based on annual output of 300,000 tons of natural gas as raw material, the design of synthetic ammonia transformation process. In recent years, the large-scale industrial development soon ammonia, low energy consumption, the clean production of synthetic ammonia equipment development are the main direction of technical improvement, is to develop better performance of catalyst, reducing ammonia synthesis pressure, the development of new materials gas purification methods, reduce fuel consumption, low heat recovery and reasonable utilization, etc.The design process used in brief are: compressed natural gas afterdesulfurization and conversion into a furnace, the methane and hydrocarbons into hydrogen, through the Secondary reformer further transformed into the highly variable furnace heat exchanger, the great catalyst part of the reaction of carbon monoxide and hydrogen and carbon dioxide vapor, then through the low-temperature shift to reduce to an acceptable level of carbon monoxide to methanation process. The design review described some of the major domestic and international situation and the development of synthetic ammonia industry trends and technological process, parameter identification and selection, discusses the plant's location; introduced the transformation process of the various processes and determine the design of high temperature shift and low temperature Transformation series of the process. Calculation of some of the major transformation process, including segment and transform section material balance, heat balance, equilibrium temperature and airspeed calculation. Calculation of some of the major equipment is a high temperature shift catalyst of specific terms, and according to the design task to do the conversion and transformation process flow chart with control points.Advantage of this design is to choose a better site and raw materials line to determine the good conditions, reasonable catalyst and energy utilization. In addition, investment in equipment designed to minimize costs.Keywords: ammonia; natural gas; transformation; transformation;目录摘要 (I)Abstract (II)目录 (IV)1 综述.................................................................. - 1 -1.1 氨的性质、用途及重要性.......................................... - 1 -1.1.1 氨的性质................................................... - 1 -1.1.2 氨的用途及在国民生产中的作用............................... - 1 -1.2 合成氨生产技术的发展............................................ - 2 -1.2.1世界合成氨技术的发展....................................... - 2 -1.2.2中国合成氨工业的发展概况................................... - 5 -1.3合成氨转变工序的工艺原理......................................... - 6 -1.3.1 合成氨的典型工艺流程介绍................................... - 6 -1.3.2 合成氨转化工序的工艺原理................................... - 8 -1.3.3合成氨变换工序的工艺原理................................... - 8 -1.4 设计方案的确定.................................................. - 9 -1.4.1 原料的选择................................................. - 9 -1.4.2 工艺流程的选择............................................ - 10 -1.4.3 工艺参数的确定............................................ - 10 -1.4.4 工厂的选址................................................ - 11 -2 设计工艺计算......................................................... - 13 -2.1 转化段物料衡算................................................. - 13 -2.1.1 一段转化炉的物料衡算...................................... - 14 -2.1.2 二段转化炉的物料衡算...................................... - 17 -2.2 转化段热量衡算................................................. - 20 -2.2.1 一段炉辐射段热量衡算...................................... - 20 -2.2.2 二段炉的热量衡算.......................................... - 27 -2.2.3 换热器101-C、102-C的热量衡算............................. - 28 -2.3 变换段的衡算................................................... - 30 -2.3.1 高温变换炉的衡算.......................................... - 30 -2.3.2 低温变换炉的衡算.......................................... - 32 -2.4 换热器103-C及换热器104-C的热负荷计算......................... - 35 -2.4.1 换热器103-C热负荷........................................ - 35 -2.4.2 换热器104-C热负荷........................................ - 35 -2.5 设备工艺计算................................................... - 36 -参考文献............................................................... - 40 -致谢................................................................... - 41 -附录................................................................... - 41 -1 综述1.1 氨的性质、用途及重要性1.1.1 氨的性质氨分子式为NH,在标准状态下是无色气体,比空气轻,具有特殊的刺激性臭味。
合成氨生产中变换工段的设计

合成氨生产中变换工段的设计
合成氨是化学工业中重要的基础产品,遍布在各个工业应用之中。
为保证合成氨的质量,改造变换工段绝对是大势所趋。
首先,利用先进的技术来改进变换工段,增加产品的质量和效率。
在传统的合成氨设计中,由于变换工段的设计有很大的不足,耗损了大量的能量和原料,从而导致产品质量下降。
因此,现在开始利用现代化技术对变换工段进行改进。
通过改进,可以减少此工段中能量及原料的损耗,从而保证产品质量,增加产品的产量,同时还可增加效率。
其次,实现工段的自动化。
传统的合成氨设计中,每个工序都是手动完成的,需要大量的人力和物力,会导致成本高,工艺操作尚未实现自动化。
为了节省成本,实现高效的生产,现在可以采用工段的自动化技术来实现。
实施后能够减少生产过程中的人力,加快生产进度,同时实现高效和高质量的生产。
最后,建立完善的质量控制体系。
随着生产技术的发展,合成氨工段的质量控制很重要。
因此,必须建立一套完善的质量保证体系,在于执行有关的质量管理措施。
通过完善的质量保证体系,可以有效地提高产品的质量,满足消费者的需求,有利于长期的企业发展。
总之,改进变换工段是当前合成氨生产中一个必要的改革,它可以减少损耗,提高产品质量,同时实现高生产效率和更高的质量。
采用现代化技术,实现自动化,建立完善的质量控制体系,都对保证合成氨高质量有着不可替代的作用。
年产3万吨合成氨变换工段可行性研究

年产3万吨合成氨变换工段可行性研究目录一.总论 (2)二.需求预测 (2)三.企业现状产品生产方案与生产规模 (4)四.工艺技术方案 (6)五.公司简介 (7)六.建厂条件和厂址选择布局方案 (9)七.公用工程及辅助设施方案 (11)八.环境保护及安全卫生 (13)九.工厂组织、劳动定员人员培训 (14)十.项目实施规划 (15)十一.结论 (16)十二.参考文献 (17)一总论:氨分子式:NH3分子量:237.93物化性质:氨在自然界中,是动物体,特别是蛋白质腐败的产物。
它是没有颜色、具有刺激性气味的气体。
在标准状况下,氨的密度是0.771g/L,比同体积的空气轻。
氨很容易液化,在常压下冷却到-33.35℃或在常温下加压7*105~8*10 Pa,气态氨就凝结为无色的液体,同时放出大量的热。
液态氨汽化是要吸收大量的热,能使它周围物质的温度急剧降低,因此,氨常用作制冷剂。
在常温常压下,1体积水约溶解700体积氨。
(可以做喷泉实验)氨的水溶液叫氨水。
氨是一种无色有毒气体,易溶于水,形成氢氧化铵,还可以溶于乙醚等有机溶剂。
氨的主要用途是直接活间接作为肥料(液体氨或固体肥料如尿素、硫铵、硝铵等),约占消费总量的85~90%。
在美国,2001年合成氨的消费量为1810万吨,其中大约有22.7%的合成氨直接用作肥料,20.2%的合成氨用于生产尿素,16.2%的用于生产磷酸铵,14.5%的用于生产硝酸,1%的作为工业用气,9.9%的用于生产硝酸铵和3.9的用于生产硫酸铵,用作其他用途的合成氨只占消费总量的1.6%。
氨(NH3)常态下是有特殊气味的强刺激性气体,相对密度为0.5971(空气=1),易燃,自燃点为65112,能与空气形成爆炸性混合物(爆炸极限15.7%~27.4%)。
氨气常温加压即可液化(临界压力11.4MPa,临界温度132.512),沸点为-33.512、凝固点为-77.712。
氨的水溶液称为氨水,呈碱性。
合成氨变换工段工艺设计

合成氨变换工段工艺设计1. 引言合成氨是一种重要的化工原料,在农业、化工和医药等行业广泛应用。
合成氨的生产过程中,合成氨变换工段是一个关键的工艺环节。
本文将介绍合成氨变换工段的工艺设计。
2. 工艺流程合成氨变换工段的工艺流程包括进料处理、反应器设计、温度控制和产品回收四个重要环节。
2.1 进料处理合成氨的主要原料是氮气和氢气,进料处理环节主要包括氮气和氢气的纯化和混合。
氮气和氢气需要通过特定的纯化设备去除杂质,以确保反应的纯度和效果。
然后,纯化后的氮气和氢气按照一定比例进行混合。
2.2 反应器设计反应器是合成氨变换工段的核心设备,根据反应器设计的不同,可以分为固定床反应器和流化床反应器两种。
固定床反应器是一种较为常见的反应器形式,氮气和氢气催化反应产生合成氨。
固定床反应器需要考虑催化剂的选择、填充物的设计以及反应器的传热设计等因素。
流化床反应器是近年来逐渐应用的一种反应器形式,其优点包括更好的热传递性能和更好的反应效果。
流化床反应器需要考虑反应器的气固分离、催化剂的循环和再生等因素。
2.3 温度控制温度对合成氨反应的影响非常重要,合适的反应温度可以提高反应速率和选择性。
在合成氨变换工段中,需要通过控制进料气体的温度和反应器的温度来实现对反应的控制。
温度控制还需要考虑热量的平衡问题,包括进料气体的预热和产物蒸汽的回收利用等。
2.4 产品回收合成氨变换工段的最终目标是获得高纯度的合成氨产品。
在产品回收环节中,需要进行氨的冷凝和气液分离。
冷凝过程中需要考虑温度和压力的控制,以确保氨的高效冷凝。
气液分离过程中,可以采用吸收液的方式将氨从气相中吸收出来,再进行后续处理和精制。
3. 设备选择合成氨变换工段的设备选择主要包括反应器、纯化设备、冷凝器和分离器等。
反应器的选择需要考虑反应速率、选择性和热传导等因素。
常用的反应器材料有不锈钢、镍基合金等。
纯化设备的选择需要考虑氮气和氢气的纯度要求以及生产规模等因素。
3万吨NH3Y合成氨厂中变串低变工艺设计(毕业设计)

目录摘要 (2)Abstract (3)第一章绪论 (4)1.1 合成氨工艺的背景、现状及展望 (4)1.2 氨的性质及用途 (5)1.3 CO变换的基本原理及工艺流程 (7)1.4 变换催化剂 (8)1.5 中变串低变的意义 (10)1.6 设备的选用及特点 (10)1.7 设计说明书计算部分 (12)第二章物料及热量衡算 (13)2.1 课题条件 (13)2.2 中变炉工艺条件的计算 (13)2.3 中温变换炉的物料衡算 (19)2.4 低变换炉的工艺条件计算 (21)2.5 低变换炉的物料和热量衡算 (25)2.6 热水塔出口热水温度的估算 (26)2.7 半水煤气换热器物料热量衡算 (27)2.8 饱和塔物料热量衡算 (28)2.9 热水塔物料热量衡算 (29)第三章设备计算 (31)3.1 饱和热水塔计算 (31)3.2 中变炉计算 (40)总结 (43)致谢 (45)参考文献 (46)摘要3万吨NH3/Y合成氨厂中变串低变工艺设计摘要:此次设计充分运用了化学基础知识和专业理论知识,结合国内外合成氨工艺现状背景,考虑了环境因素和节能减排方面的影响,用最合理的方法对整个工艺流程进行优化,使其达到预期效果。
设计中涉及到大量参数,包括温度,压力,平衡常数,密度,黏度,饱和蒸汽压等。
另外,设计中包括一些设备计算,如:物料衡算,热量衡算和设备计算三部分内容。
关键词:设计、参数、工艺、合成氨AbstractThe Design of Low-temperature Shift afterHigh-temperature Shift T echnology with Production of30000t/y Ammonia PlantAbstract: The design of the full use of the chemical basis of theoretical knowledge and professional expertise, combined with the background of domestic and international status of synthetic ammonia process, taking into account environmental factors and energy saving aspects, the most reasonable way to optimize the entire process so that the desired effect. Design involves a large number of parameters, including temperature, pressure, equilibrium constant, density, viscosity, saturated vapor pressure and so on. In addition, the design includes a number of computing devices, such as: material balance, heat balance calculation of three parts and equipment.Keywords: design, parameters, process, ammonia wuhan institut第一章绪论1.1合成氨工艺的背景、现状及展望中国合成氨生产时从20世纪30年代开始的,但当时仅在南京、大连两地建有氨厂,最高年产量不超过50kt(1941年)。
年产万吨合成氨变换工段工艺设计终稿
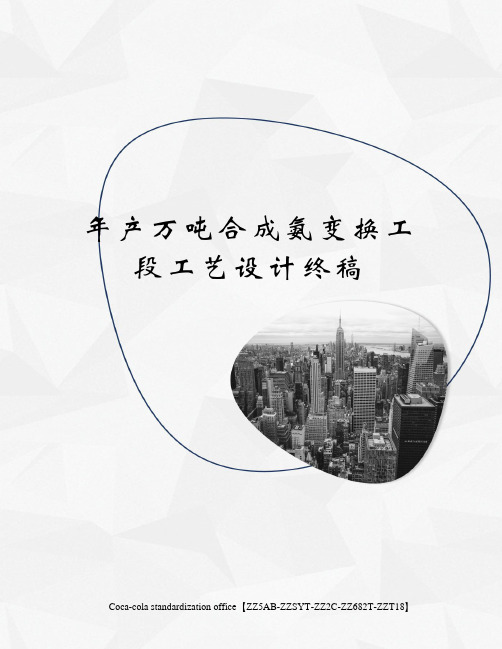
Abstract:This design was mainly for the synthetic ammonia plant shift conversion section.The technological process used the middle temperature changefirst ,and then used the low temperature change .Process calculation mainly included material balance, energy balance and equipmentselection.
变换过程需在高温高压使用催化剂条件下进行,因此变换工序是合成氨生产的高成本工序,其成本降低对合成氨成本的降低有重要意义。
1.3
1.
我国的氮肥工业自20世纪50年代以来,不断发展壮大,目前合成氨产量已跃居世界第一位,已掌握了以焦炭、无烟煤、焦炉气、天然气及油田伴生气和液态烃多种原料生产合成氨、尿素的技术,形成了特有的煤、石油、天然气原料并存和大、中、小生产规模并存的生产格局。目前合成氨总生产能力为5000万吨/年左右[3],氮肥工业已基本满足了国内需求,在与国际接轨后,具备与国际合成氨产品竞争的能力,今后发展重点是调整原料和产品结构,进一步改善经济性。
合成氨变换工段 (2)

合成氨变换工段简介合成氨是一种重要的化学原料,广泛应用于农业、化工、医药等领域。
合成氨变换工段是合成氨生产过程中的一个关键环节。
本文将介绍合成氨变换工段的工艺流程、设备及操作要点。
工艺流程合成氨变换工段是将合成气体中的氮气(N2)和氢气(H2)转化为氨气(NH3)的过程。
其工艺流程一般包括以下几个步骤:压缩经过合成气压缩工段后的合成气体进入合成氨变换工段前,需要进行进一步的压缩处理,以适应变换反应的要求。
压缩一般采用多级压缩方式,以提高压缩效率和能量利用率。
变换反应压缩后的合成气体进入变换反应器,其中装填有合适的催化剂。
变换反应是一个放热的反应,因此需要进行冷却,以控制反应温度在合适范围内。
反应器一般采用多床反应器并联运行,以确保反应的高转化率和低副反应产物含量。
分离变换反应生成的气体中含有未反应的氮气、氢气和产生的氨气,并伴有少量惰性气体。
为了获得纯度高的氨气,需要对气体进行分离。
常用的分离方法有吸收、膜分离和压力摩擦等。
吸收法是最常用的方法,一般采用水溶液吸收来分离氨气。
设备合成氨变换工段所需设备主要包括压缩机、反应器和分离塔等。
压缩机压缩机是将合成气体压缩到变换反应的所需压力的主要设备。
常用的压缩机有离心式压缩机和轴流式压缩机。
压缩机的选型应根据合成气体流量、压力和压缩比等参数来确定。
反应器反应器是合成氨变换工段的核心设备,其设计应考虑反应热平衡、传热效果和催化剂的使用寿命等因素。
常见的反应器类型有管状反应器、固定床反应器和流化床反应器等。
分离塔分离塔用于对变换反应生成的气体进行分离,以获取高纯度的氨气。
常见的分离塔类型有吸收塔和膜分离塔。
分离塔的选型应考虑气体流量、分离效率和运行成本等因素。
操作要点合成氨变换工段的操作要点包括以下几个方面:温度控制变换反应是一个高温反应,需要保持适宜的反应温度。
过高的温度会导致催化剂失活,过低的温度会降低反应速率。
因此,在操作过程中需要严格控制反应器的温度,并根据催化剂的性质和寿命进行调整。
合成氨变换工段设计

合成氨变换工段设计一、工艺简介合成氨(NH3)是一种重要的化学原料,广泛应用于肥料、化工、冶金等领域。
合成氨通常是通过哈伯-博士过程进行合成的,该过程主要有三个阶段:气化反应、变换反应和分离装置。
其中,变换反应是合成氨反应的核心环节。
二、工艺流程1.进料系统:将氮气(N2)和氢气(H2)以一定的比例通入反应器。
进料系统应包括氮气和氢气的净化装置,以确保进入反应器的气流中不含有不利于反应的杂质。
2.反应器:反应器是合成氨变换的关键装置,需要选择适当的催化剂,并控制合适的反应温度和压力。
反应器的设计应满足以下要求:具有高的转化率和选择性、较小的压力损失、对催化剂具有良好的分布和稳定性。
3.除尘装置:合成氨反应会产生一些固体杂质,如烟尘颗粒等。
除尘装置主要用于去除这些固体杂质,以确保产品的纯度。
4.产品收集系统:将合成氨收集并进行后续的分离和提纯。
收集系统应包括冷凝器、吸收塔等设备,以确保合成氨的回收率。
三、工艺参数1.反应温度:合成氨变换反应通常在300-500°C的温度范围内进行,具体温度的选择应考虑催化剂的活性和热力学平衡等因素。
2.反应压力:合成氨变换反应的压力通常在10-30MPa之间,压力的选择应使反应的平衡位置有利于产生高的氨气浓度。
3.氮气和氢气的比例:氮气和氢气的比例对合成氨反应的转化率和选择性有重要影响,一般通过调节氮气和氢气的流量比例来控制。
4.催化剂的选择:催化剂的选择应考虑其活性和稳定性,促使反应的进行,并提高催化剂的利用率。
四、工艺设备1.反应器:选用合适的反应器,如固定床反应器或流化床反应器,确保催化剂的分布均匀和反应的高转化率。
2.净化装置:包括氮气和氢气的净化装置,用于去除进料中的杂质。
3.冷凝器:用于冷却和冷凝反应器出口的气体,以便进行后续的分离和提纯。
4.吸收塔:用于收集合成氨气体,并进行后续的分离和提纯。
五、工艺控制1.温度控制:根据反应的热力学特性,控制反应温度在适当的范围内,以提高反应的转化率和选择性。
- 1、下载文档前请自行甄别文档内容的完整性,平台不提供额外的编辑、内容补充、找答案等附加服务。
- 2、"仅部分预览"的文档,不可在线预览部分如存在完整性等问题,可反馈申请退款(可完整预览的文档不适用该条件!)。
- 3、如文档侵犯您的权益,请联系客服反馈,我们会尽快为您处理(人工客服工作时间:9:00-18:30)。
年产三万吨合成氨厂变换工段工艺设计
一、工艺流程概述
1.原料准备:将天然气(主要是甲烷)与空气作为主要原料,通过气体净化系统去除其中的杂质、硫化物和水分。
2.原料配送:将净化后的天然气和空气分别输送至气体净化系统进行进一步的处理和分析。
3.变换反应槽:将净化后的天然气和空气通过压缩机压缩至一定压力后,经过暖气交换器加热至高温(约500-600℃),再进入变换反应槽。
4.变换催化剂:在变换反应槽中,使用催化剂(通常是高温高压下的铁-钴催化剂)促进N2和H2的反应。
反应生成的合成氨会随气流从反应槽中流出。
5.除气系统:将反应槽中的气体通过除尘器,冷却器和吸附剂等设备进行处理,去除其中的固体颗粒、水分和其他杂质。
6.合成氨回收:经过除气系统处理后的气体中仍含有未反应的氮气和氢气,通过压缩机再次压缩进入蒸馏塔。
在蒸馏塔中,根据不同的沸点,将氨气和氮气分离开来,再通过冷凝器冷凝为液态氨。
7.废水处理:在工艺过程中产生的废水会经过处理系统去除其中的有机物和杂质,以保证排放的废水符合环保要求。
二、设备布置和操作要点
1.变换反应槽的设计要考虑到温度、压力和气体流动速度的控制。
同时,需要定期更换催化剂,以维持优良的反应性能。
2.除气系统中的设备要进行定期维护和清洁,确保其正常工作和去除气体中的杂质、固体颗粒和水分。
3.合成氨回收装置要根据产品质量要求设置合适的操作参数,例如蒸馏塔的温度和压力。
此外,冷凝器的冷却水流需要保持稳定,以确保气体顺利冷凝为液态氨。
4.废水处理系统应配置适当的物理和化学处理单元,如过滤器、沉淀池和生物处理等,以达到废水排放标准。
5.需要建立相应的安全措施,如设立监测系统,确保气体和液体在整个工艺中的安全运输和使用。
三、工艺控制和性能优化
1.在变换反应槽中,可以通过调节供气比例、压力和温度等参数来控制合成氨的产率和选择性。
同时,也可以根据反馈控制系统监测和调整催化剂的性能。
2.除气系统中的设备可以通过监测气体的组成和温度、压力等参数,来调整操作参数,以达到满足产品质量要求的除气效果。
3.合成氨回收装置可以通过蒸馏塔的操作参数、冷凝器的冷却水流量等参数调整,以优化合成氨的回收率和纯度。
4.废水处理系统应根据废水的性质和排放标准,优化处理单元和操作参数,以实现高效、经济和环保的废水处理。
综上所述,年产三万吨合成氨厂变换工段的工艺设计包括原料准备、原料配送、变换反应槽、变换催化剂、除气系统、合成氨回收和废水处理等环节。
在设备布置和操作要点上,需要考虑温度、压力和气体流动速度
的控制,以及定期维护和清洁设备。
工艺控制和性能优化方面,可以通过调节参数和监测系统来实现产率、选择性和产品质量的优化。