合成氨生产中变换工段的设计
合成氨变换工段工艺中变串低变换热设计
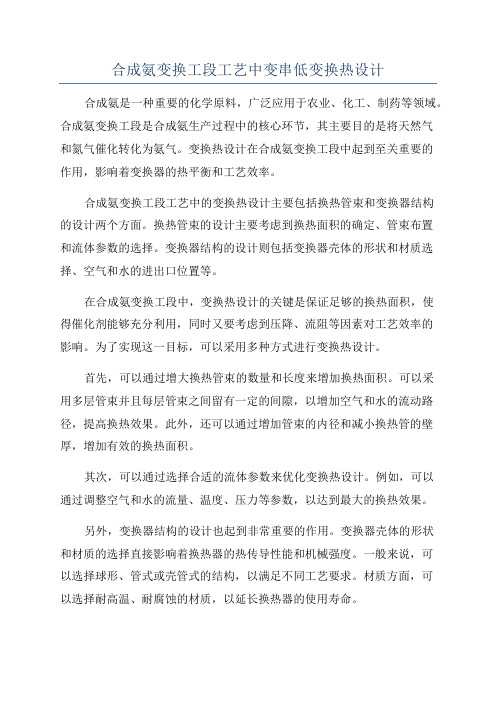
合成氨变换工段工艺中变串低变换热设计合成氨是一种重要的化学原料,广泛应用于农业、化工、制药等领域。
合成氨变换工段是合成氨生产过程中的核心环节,其主要目的是将天然气和氮气催化转化为氨气。
变换热设计在合成氨变换工段中起到至关重要的作用,影响着变换器的热平衡和工艺效率。
合成氨变换工段工艺中的变换热设计主要包括换热管束和变换器结构的设计两个方面。
换热管束的设计主要考虑到换热面积的确定、管束布置和流体参数的选择。
变换器结构的设计则包括变换器壳体的形状和材质选择、空气和水的进出口位置等。
在合成氨变换工段中,变换热设计的关键是保证足够的换热面积,使得催化剂能够充分利用,同时又要考虑到压降、流阻等因素对工艺效率的影响。
为了实现这一目标,可以采用多种方式进行变换热设计。
首先,可以通过增大换热管束的数量和长度来增加换热面积。
可以采用多层管束并且每层管束之间留有一定的间隙,以增加空气和水的流动路径,提高换热效果。
此外,还可以通过增加管束的内径和减小换热管的壁厚,增加有效的换热面积。
其次,可以通过选择合适的流体参数来优化变换热设计。
例如,可以通过调整空气和水的流量、温度、压力等参数,以达到最大的换热效果。
另外,变换器结构的设计也起到非常重要的作用。
变换器壳体的形状和材质的选择直接影响着换热器的热传导性能和机械强度。
一般来说,可以选择球形、管式或壳管式的结构,以满足不同工艺要求。
材质方面,可以选择耐高温、耐腐蚀的材质,以延长换热器的使用寿命。
最后,合成氨变换工段的变换热设计还需要考虑到安全性和可靠性。
例如,需要保证换热器的壳体有足够的强度,能够承受工作压力和温度的变化。
此外,还需要考虑到清洗和维护的便利性,以减少生产中的停机时间和成本。
总之,合成氨变换工段工艺中的变换热设计是一个复杂而关键的问题。
通过合理的换热管束和变换器结构设计,可以实现高效、安全、可靠的合成氨生产。
合成氨变换工段工艺设计

合成氨变换工段工艺设计合成氨是化工工业中的重要原料,广泛应用于制取尿素、硝化铵等农业肥料,以及制取氨水、氨盐、化肥、染料等合成工艺中。
合成氨变换工段是合成氨生产中的关键环节,其工艺设计对合成氨的产量、质量以及能耗等方面有重要影响。
一、工艺概述合成氨的变换反应器是将反应物氮气和氢气通过催化剂的作用,在一定条件下发生气相合成反应,生成合成氨。
反应器通常采用固定床催化剂反应器,催化剂的选择和催化剂床层的设计都是工艺设计的重要环节。
冷凝器主要用于对反应产生的氨气进行冷凝回收,常见的冷凝器有直接冷凝器和间接冷凝器两种形式,工艺设计中需要根据具体情况选择适用的冷凝方式。
循环气压缩机主要用于将反应器中未反应的气体通入新的循环,提高气相合成反应的转化率。
在工艺设计中,需要考虑压缩机的压比、功率消耗等参数。
氨气的分离净化装置主要用于对合成氨中的杂质进行去除,提高合成氨的纯度。
常用的分离净化装置有吸附装置、膜分离装置等,具体的工艺设计需要根据生产要求和经济效益进行选择。
二、工艺参数及控制合成氨的变换工段的工艺参数主要包括反应温度、反应压力、空速、催化剂活性等。
这些参数直接影响合成氨的产率、选择性和能耗。
反应温度是合成氨变换反应的重要参数,通过控制温度可以提高反应速率和转化率,但过高的温度会导致副反应的发生,降低合成氨的选择性。
反应压力主要用于控制氨气的产量和能耗,压力越高产氨越多,但能耗也相应增加。
空速是指单位时间内通过反应器的氮气体积,可以通过调控压力和进气量来实现,过小的空速会影响反应的效果,而过大会导致固定床催化剂的床层冲击和阻力升高,影响反应转化率。
催化剂活性主要指催化剂的活性组分含量和粒径等参数,这些参数会影响合成氨的选择性和催化剂的寿命。
在工艺设计中,需要考虑这些参数的合理选择和控制,以提高合成氨的产量和质量,并降低能耗。
三、能耗控制合成氨的变换工段是合成氨生产中的能耗重点。
能耗的控制主要体现在压力控制、催化剂选择和热交换等方面。
年产10万吨合成氨变换工段工艺设计
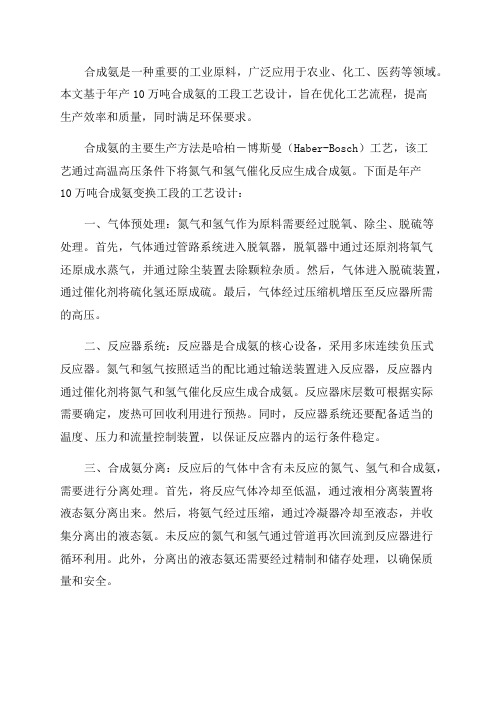
合成氨是一种重要的工业原料,广泛应用于农业、化工、医药等领域。
本文基于年产10万吨合成氨的工段工艺设计,旨在优化工艺流程,提高生产效率和质量,同时满足环保要求。
合成氨的主要生产方法是哈柏-博斯曼(Haber-Bosch)工艺,该工艺通过高温高压条件下将氮气和氢气催化反应生成合成氨。
下面是年产10万吨合成氨变换工段的工艺设计:一、气体预处理:氮气和氢气作为原料需要经过脱氧、除尘、脱硫等处理。
首先,气体通过管路系统进入脱氧器,脱氧器中通过还原剂将氧气还原成水蒸气,并通过除尘装置去除颗粒杂质。
然后,气体进入脱硫装置,通过催化剂将硫化氢还原成硫。
最后,气体经过压缩机增压至反应器所需的高压。
二、反应器系统:反应器是合成氨的核心设备,采用多床连续负压式反应器。
氮气和氢气按照适当的配比通过输送装置进入反应器,反应器内通过催化剂将氮气和氢气催化反应生成合成氨。
反应器床层数可根据实际需要确定,废热可回收利用进行预热。
同时,反应器系统还要配备适当的温度、压力和流量控制装置,以保证反应器内的运行条件稳定。
三、合成氨分离:反应后的气体中含有未反应的氮气、氢气和合成氨,需要进行分离处理。
首先,将反应气体冷却至低温,通过液相分离装置将液态氨分离出来。
然后,将氨气经过压缩,通过冷凝器冷却至液态,并收集分离出的液态氨。
未反应的氮气和氢气通过管道再次回流到反应器进行循环利用。
此外,分离出的液态氨还需要经过精制和储存处理,以确保质量和安全。
四、废气处理:合成氨生产中会产生大量的废气,包括未反应的氮气、氢气、氨气和其他杂质气体。
废气处理主要包括低温分离、吸收、洗涤等步骤。
首先,废气通过低温分离装置将其中的液态氨和水分离出来。
然后,通过吸收剂将氨气吸收,以减少其排放。
最后,利用洗涤液去除废气中的其他杂质气体,确保废气达到环境排放标准。
五、能耗优化:为了降低能耗和提高生产效率,可以采用余热回收和过程优化等措施。
余热回收可通过换热器将反应废热回收利用,进行气体预热和水蒸气生产。
「年产三万吨合成氨厂变换工段工艺设计」

年产三万吨合成氨厂变换工段工艺设计一、工艺流程概述1.原料准备:将天然气(主要是甲烷)与空气作为主要原料,通过气体净化系统去除其中的杂质、硫化物和水分。
2.原料配送:将净化后的天然气和空气分别输送至气体净化系统进行进一步的处理和分析。
3.变换反应槽:将净化后的天然气和空气通过压缩机压缩至一定压力后,经过暖气交换器加热至高温(约500-600℃),再进入变换反应槽。
4.变换催化剂:在变换反应槽中,使用催化剂(通常是高温高压下的铁-钴催化剂)促进N2和H2的反应。
反应生成的合成氨会随气流从反应槽中流出。
5.除气系统:将反应槽中的气体通过除尘器,冷却器和吸附剂等设备进行处理,去除其中的固体颗粒、水分和其他杂质。
6.合成氨回收:经过除气系统处理后的气体中仍含有未反应的氮气和氢气,通过压缩机再次压缩进入蒸馏塔。
在蒸馏塔中,根据不同的沸点,将氨气和氮气分离开来,再通过冷凝器冷凝为液态氨。
7.废水处理:在工艺过程中产生的废水会经过处理系统去除其中的有机物和杂质,以保证排放的废水符合环保要求。
二、设备布置和操作要点1.变换反应槽的设计要考虑到温度、压力和气体流动速度的控制。
同时,需要定期更换催化剂,以维持优良的反应性能。
2.除气系统中的设备要进行定期维护和清洁,确保其正常工作和去除气体中的杂质、固体颗粒和水分。
3.合成氨回收装置要根据产品质量要求设置合适的操作参数,例如蒸馏塔的温度和压力。
此外,冷凝器的冷却水流需要保持稳定,以确保气体顺利冷凝为液态氨。
4.废水处理系统应配置适当的物理和化学处理单元,如过滤器、沉淀池和生物处理等,以达到废水排放标准。
5.需要建立相应的安全措施,如设立监测系统,确保气体和液体在整个工艺中的安全运输和使用。
三、工艺控制和性能优化1.在变换反应槽中,可以通过调节供气比例、压力和温度等参数来控制合成氨的产率和选择性。
同时,也可以根据反馈控制系统监测和调整催化剂的性能。
2.除气系统中的设备可以通过监测气体的组成和温度、压力等参数,来调整操作参数,以达到满足产品质量要求的除气效果。
年产二十万吨合成氨变换工段工艺设计

合成氨变换工段是合成氨生产过程中的关键工艺环节之一,它将合成气中的氮气和氢气在催化剂的作用下,通过催化反应转化为合成氨。
本文将围绕年产二十万吨合成氨的变换工段工艺设计进行详细阐述,旨在提供一个完整的工艺设计方案。
首先,变换工段的催化剂选择非常重要。
对于年产二十万吨合成氨的工艺,常用的催化剂有铁素体、铁铬铝混合催化剂等。
这些催化剂在一定的操作条件下,能够实现高效的合成氨转化率和选择性。
在实际应用中,应根据具体工艺要求和经济效益进行选择。
其次,合成气的净化和预热是变换工段的重要准备工作。
合成气中常含有一定的杂质,如氧、水蒸气、二氧化碳等,这些杂质会影响催化剂的活性和寿命。
因此,合成气需要通过一系列净化设备,如除氧、除硫、除水等步骤,将其净化为适合变换反应的合成气。
同时,为了提高反应的热效应,还需要对合成气进行预热,一般可以采用换热器进行热量回收。
接下来是变换反应的具体设计。
变换反应是一个平衡反应,根据Le Chatelier原理,可以通过提高反应温度、降低反应压力、增加氢气过量等方式推动平衡向产氨方向偏移。
在实际设计中,应在考虑较高转化率的前提下,平衡反应速率和催化剂活性与寿命的关系,做出合理的选择。
另外,变换反应需要保持一定的循环气速和循环气气体组成。
循环气速过高会造成能耗增加,循环气速过低则会影响气体传质效果。
循环气气体组成应符合催化剂的操作条件,一般应保持一定的氢气过量,同时控制氮气和氢气的比例。
最后是变换工段的控制策略。
合成氨变换工段是一个高温高压的工艺过程,对于安全和稳定运行,需要建立完善的自动化控制系统。
控制策略应包括反应温度和压力的控制、循环气速和气体组成的控制、催化剂的修复和更换等。
在实际设计中,应结合具体的工艺要求和设备性能,进行综合技术经济分析,选取最佳的工艺参数和操作条件。
同时,在设计过程中还应考虑到工艺的可持续性和环境保护要求,合理利用资源,减少废物排放,实现工艺的可持续发展。
合成氨变换工段工艺设计

合成氨变换工段工艺设计1. 引言合成氨是一种重要的化工原料,在农业、化工和医药等行业广泛应用。
合成氨的生产过程中,合成氨变换工段是一个关键的工艺环节。
本文将介绍合成氨变换工段的工艺设计。
2. 工艺流程合成氨变换工段的工艺流程包括进料处理、反应器设计、温度控制和产品回收四个重要环节。
2.1 进料处理合成氨的主要原料是氮气和氢气,进料处理环节主要包括氮气和氢气的纯化和混合。
氮气和氢气需要通过特定的纯化设备去除杂质,以确保反应的纯度和效果。
然后,纯化后的氮气和氢气按照一定比例进行混合。
2.2 反应器设计反应器是合成氨变换工段的核心设备,根据反应器设计的不同,可以分为固定床反应器和流化床反应器两种。
固定床反应器是一种较为常见的反应器形式,氮气和氢气催化反应产生合成氨。
固定床反应器需要考虑催化剂的选择、填充物的设计以及反应器的传热设计等因素。
流化床反应器是近年来逐渐应用的一种反应器形式,其优点包括更好的热传递性能和更好的反应效果。
流化床反应器需要考虑反应器的气固分离、催化剂的循环和再生等因素。
2.3 温度控制温度对合成氨反应的影响非常重要,合适的反应温度可以提高反应速率和选择性。
在合成氨变换工段中,需要通过控制进料气体的温度和反应器的温度来实现对反应的控制。
温度控制还需要考虑热量的平衡问题,包括进料气体的预热和产物蒸汽的回收利用等。
2.4 产品回收合成氨变换工段的最终目标是获得高纯度的合成氨产品。
在产品回收环节中,需要进行氨的冷凝和气液分离。
冷凝过程中需要考虑温度和压力的控制,以确保氨的高效冷凝。
气液分离过程中,可以采用吸收液的方式将氨从气相中吸收出来,再进行后续处理和精制。
3. 设备选择合成氨变换工段的设备选择主要包括反应器、纯化设备、冷凝器和分离器等。
反应器的选择需要考虑反应速率、选择性和热传导等因素。
常用的反应器材料有不锈钢、镍基合金等。
纯化设备的选择需要考虑氮气和氢气的纯度要求以及生产规模等因素。
合成氨变换工段工艺过程设计
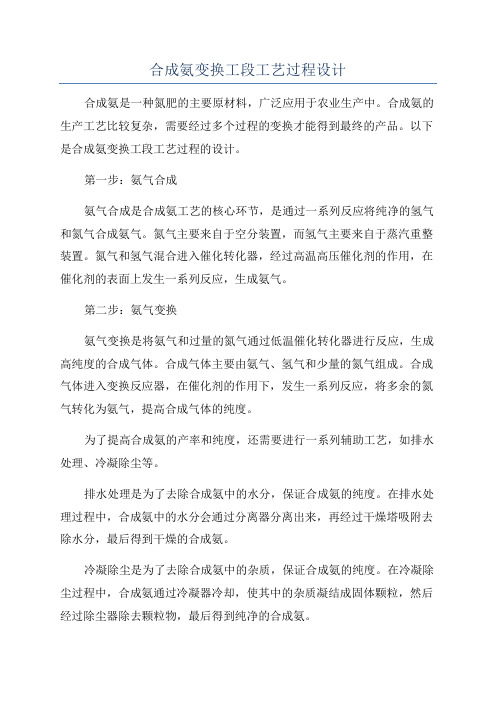
合成氨变换工段工艺过程设计
合成氨是一种氮肥的主要原材料,广泛应用于农业生产中。
合成氨的生产工艺比较复杂,需要经过多个过程的变换才能得到最终的产品。
以下是合成氨变换工段工艺过程的设计。
第一步:氨气合成
氨气合成是合成氨工艺的核心环节,是通过一系列反应将纯净的氢气和氮气合成氨气。
氮气主要来自于空分装置,而氢气主要来自于蒸汽重整装置。
氮气和氢气混合进入催化转化器,经过高温高压催化剂的作用,在催化剂的表面上发生一系列反应,生成氨气。
第二步:氨气变换
氨气变换是将氨气和过量的氮气通过低温催化转化器进行反应,生成高纯度的合成气体。
合成气体主要由氨气、氢气和少量的氮气组成。
合成气体进入变换反应器,在催化剂的作用下,发生一系列反应,将多余的氮气转化为氨气,提高合成气体的纯度。
为了提高合成氨的产率和纯度,还需要进行一系列辅助工艺,如排水处理、冷凝除尘等。
排水处理是为了去除合成氨中的水分,保证合成氨的纯度。
在排水处理过程中,合成氨中的水分会通过分离器分离出来,再经过干燥塔吸附去除水分,最后得到干燥的合成氨。
冷凝除尘是为了去除合成氨中的杂质,保证合成氨的纯度。
在冷凝除尘过程中,合成氨通过冷凝器冷却,使其中的杂质凝结成固体颗粒,然后经过除尘器除去颗粒物,最后得到纯净的合成氨。
综上所述,合成氨变换工段工艺过程的设计包括氨气合成和氨气变换两个主要步骤,同时还需要进行排水处理和冷凝除尘等辅助工艺。
这些步骤的设计要考虑反应温度、反应压力、催化剂的选择和管理,以及对产物的分离、干燥和净化等。
通过合理的工艺设计和操作管理,可以提高合成氨的生产效率和产品质量。
小合成氨厂低温变换工段工艺设计

小合成氨厂低温变换工段工艺设计1.工艺流程合成氨的低温变换工艺流程包括氨气脱除、氢气供应、氮氢混合、压缩、变换反应和冷却净化等步骤。
具体流程如下:(1)氨气脱除:从合成气中去除氨气。
合成气通常包括氮气、氢气和少量的甲烷、一氧化碳等。
氨气脱除可以采用吸收剂或者低温冷凝的方式进行。
(2)氢气供应:合成氨需要大量的氢气供应。
氢气可以通过蒸汽重整、部分氧化等方式产生。
(3)氮氢混合:将氮气和氢气按照一定的比例混合,以提供合适的反应物组成。
(4)压缩:将混合气体压缩到合适的工艺压力,以增加反应速率和提高反应效果。
(5)变换反应:将压缩的气体通入低温变换器中,反应产生氨气。
这个过程是一个放热反应,需要控制反应温度和催化剂的作用。
(6)冷却净化:将变换产生的气体冷却,去除其中的杂质和不稳定的气体组分,以获得高纯度的合成氨。
2.工艺参数合成氨的低温变换工段的设计需要考虑多个工艺参数,包括反应温度、反应压力、气体流量、催化剂选择等。
(1)反应温度:低温变换反应需要控制在适当的温度范围内进行。
反应温度过高会导致催化剂失活,而温度过低则会影响反应速率和产氨量。
(2)反应压力:反应压力是影响反应平衡的重要参数,对氨气产率和选择性有很大影响。
通常情况下,反应压力较高可以提高氨气产率,但同时也增加了设备的投资和运行成本。
(3)气体流量:气体流量直接影响反应物在催化剂上的接触和反应速率。
合适的气体流量可以提高反应效果,但如果流量过大,会增加压力损失和能耗。
(4)催化剂选择:催化剂是低温变换反应的关键,其选择需要考虑活性、稳定性和寿命等因素。
常用的催化剂有铁、铂、钼等,可以单一使用或者组合使用。
3.安全控制在低温变换工段的设计中,安全控制是非常重要的。
一方面,低温反应需要保证设备和管道的密封性和抗冻性,以防止设备爆炸和泄漏事故。
另一方面,反应温度和压力需要在合适的范围内稳定控制,以防止设备超负荷运行和产生危险反应。
此外,还需要考虑废气处理、电力供应等问题,以确保低温变换工段的安全和稳定运行。
- 1、下载文档前请自行甄别文档内容的完整性,平台不提供额外的编辑、内容补充、找答案等附加服务。
- 2、"仅部分预览"的文档,不可在线预览部分如存在完整性等问题,可反馈申请退款(可完整预览的文档不适用该条件!)。
- 3、如文档侵犯您的权益,请联系客服反馈,我们会尽快为您处理(人工客服工作时间:9:00-18:30)。
合成氨生产中变换工段的设计
合成氨是化学工业中重要的基础产品,遍布在各个工业应用之中。
为保证合成氨的质量,改造变换工段绝对是大势所趋。
首先,利用先进的技术来改进变换工段,增加产品的质量和效率。
在传统的合成氨设计中,由于变换工段的设计有很大的不足,耗损了大量的能量和原料,从而导致产品质量下降。
因此,现在开始利用现代化技术对变换工段进行改进。
通过改进,可以减少此工段中能量及原料的损耗,从而保证产品质量,增加产品的产量,同时还可增加效率。
其次,实现工段的自动化。
传统的合成氨设计中,每个工序都是手动完成的,需要大量的人力和物力,会导致成本高,工艺操作尚未实现自动化。
为了节省成本,实现高效的生产,现在可以采用工段的自动化技术来实现。
实施后能够减少生产过程中的人力,加快生产进度,同时实现高效和高质量的生产。
最后,建立完善的质量控制体系。
随着生产技术的发展,合成氨工段的质量控制很重要。
因此,必须建立一套完善的质量保证体系,在于执行有关的质量管理措施。
通过完善的质量保证体系,可以有效地提高产品的质量,满足消费者的需求,有利于长期的企业发展。
总之,改进变换工段是当前合成氨生产中一个必要的改革,它可以减少损耗,提高产品质量,同时实现高生产效率和更高的质量。
采用现代化技术,实现自动化,建立完善的质量控制体系,都对保证合成氨高质量有着不可替代的作用。