自动断浇口支架注射模设计
剪切式切断浇口凝料的注射模结构设计

•塑料注射模技术•剪切式切断浇口凝料的注射模结构设计郭新玲陕西工业职业技术学院(陕西咸阳 712000)【摘要】注射模结构类型和凝料的脱出方式因浇口形式的不同而不同针对模外切断侧浇 口凝料存在生产效率低,剪切质量差等问题,提出了模内剪切块式切断侧浇口凝料的注射 模结构,并分析了其设计要点。
关键词:凝料;剪切块;浇口;切断;注射模中图分类号:TQ320.66 文献标识码:BDOI :10.12147/ki.l 671-350&2020.010.012Design of the Injection Mold Structurewith Cutting the Gate Sprue Through Shear[Abstract] The injection mold structure and the sprue pulling type differs from the gate type. According to the low efficiency of cutting side gate sprue on the outside of die, and the poor quality of shearing, the injection mold structure with cutting the side gate sprue using the shear block on the inside of die are proposed, and the design essentials are analyzed.Key words: the sprue; shear block; gate; cutting ; injection mold1浇注系统结构分析浇注系统是从注塑机喷嘴开始到模具型腔入口为止的一段熔体通道,其作用是将熔融的塑料由注塑机喷嘴引向闭合的模具型腔,一般可分为点浇口浇注系统和侧浇口浇注系统,分别如图1、图2所示叫由于注射成型结束后,浇注系统中的塑料冷却形成废料需要与塑件分离,所以,在注射模设计时常常应考虑浇口的去除和修整方便。
注射模具模架设计方案
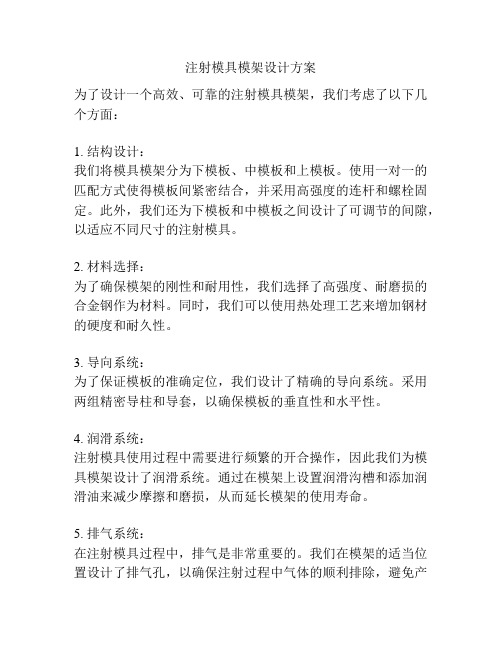
注射模具模架设计方案
为了设计一个高效、可靠的注射模具模架,我们考虑了以下几个方面:
1. 结构设计:
我们将模具模架分为下模板、中模板和上模板。
使用一对一的匹配方式使得模板间紧密结合,并采用高强度的连杆和螺栓固定。
此外,我们还为下模板和中模板之间设计了可调节的间隙,以适应不同尺寸的注射模具。
2. 材料选择:
为了确保模架的刚性和耐用性,我们选择了高强度、耐磨损的合金钢作为材料。
同时,我们可以使用热处理工艺来增加钢材的硬度和耐久性。
3. 导向系统:
为了保证模板的准确定位,我们设计了精确的导向系统。
采用两组精密导柱和导套,以确保模板的垂直性和水平性。
4. 润滑系统:
注射模具使用过程中需要进行频繁的开合操作,因此我们为模具模架设计了润滑系统。
通过在模架上设置润滑沟槽和添加润滑油来减少摩擦和磨损,从而延长模架的使用寿命。
5. 排气系统:
在注射模具过程中,排气是非常重要的。
我们在模架的适当位置设计了排气孔,以确保注射过程中气体的顺利排除,避免产
生缺陷。
总之,我们的设计方案结合了结构设计、材料选择、导向系统、润滑系统和排气系统等多个方面的考虑,旨在提供一个高效、可靠的注射模具模架。
自动切断浇口的模具(三板模和四板模)

自动切断浇口的模具(三板模和四板模)时间:2009-5-31 12:39:14 中国废旧物资网为了省去切断浇口的二次操作,Gastrow早在1938年就已设计出了借助于模具的开模动作,使塑件和流道系统自动切断的注射模具。
对这一技术申请专利是迫切的,但是在第二次世界大战结束后,也没有申请对这一技术授予专利,以致自动切断浇口的技术没有任何专利保护。
自动切断浇口的原理自动切断浇口的模具需要两个分型面。
在第一个分型面上,熔体由主流道通过分流道被分配,然后熔体流动通过设在中间板上的立式通道,在立式通道末端设置通向型腔的浇口。
在模具的第二分型面上设置成型的塑件。
当模具打开时,包含流道系统的分型面首先打开,并且流道系统留在定模一侧,目的在于使中间板上的浇口和塑件切断。
必须考虑分型面打开的距离要适当,一旦分型面打开了适当的距离,分流道和主流道能被顶出。
然后包含塑件的第二个分型面再打开。
在第二个分型面打开所要求的距离后,塑件采用常见的方式顶出。
对于模具来说,依次打开的两个分型面需要足够大的开模行程,遗憾的是在许多注射成型机的没计中没有加以考虑这一情况。
并且模具还需要比较大的安装高度,特别是深形塑件,因此对于两级开模的驱动装置要提供足够的空间。
点浇口惊人的是,已发现所谓点浇口(总是在三板模或四板模的形式中出现)如果满足一定的先决条件,很小的浇口就足够了。
还发现薄壁塑件用点浇口比用设在分型面上的浇口充模更好。
对于厚壁塑件用点浇口比用设在分型面上的比较大的浇口更易防止塌坑:对这种现象的说明很可能是;如果点浇口设计适当,尽管在狭窄的浇口处有一个显著的压力降,但由于这一压力降的结果,使熔体骤然加热而导致良好的充模。
在浇口周围钢材的局部加热是更进一步的影响,因为在钢材表面温度的局部上升而防止了浇口过早凝固,由于这个原因,熔体能在保压压力的作用下通过点浇口继续注入型腔进行补缩。
然而,为了易于充模和保持保压压力,一个基本的先决条件是分流道要足够大,一方面为了防止熔体过早凝固,另一方面为了防止通过分流道流动时,造成过大的压力降。
注塑模具毕业设计样本

(学校名称)毕业论文题目:天线盖上盖模具设计系别:专业:学号:姓名:指引教师:12月30日前言毕业设计是在修完所有课程之后,咱们走向社会之前一次综合性设计。
在本次设计中,重要用到所学注射模设计,以及机械设计等方面知识。
着重阐明了一副注射模普通流程,即注射成型分析、注射机选取及有关参数校核、模具构造设计、注射模具设计关于计算、模具总体尺寸拟定与构造草图绘制、模具构造总装图和零件工作图绘制、全面审核投产制造等。
其中模具构造设计既是重点又是难点,重要涉及成型位置及分型面选取,模具型腔数拟定及型腔排列和流道布局和浇口位置选取,模具工作零件构造设计,侧面分型及抽芯机构设计,推出机构设计,拉料杆形式选取,排气方式设计等。
通过本次毕业设计,使我更加理解模具设计含义,以及懂得如何查阅有关资料和如何解决在实际工作中遇到实际问题,这为咱们后来从事模具职业打下了良好基本。
在这个过程中,我学到了许多课本上学不到知识,将理论知识运用到实际中去,进一步理解了注射模构造、设计以及生产。
在完毕大学三年课程学习,我纯熟地掌握了机械制图、机械设计、机械原理等专业基本课和专业课方面知识,对机械制造、加工工艺有了一种系统、全面理解,达到了学习目。
对于模具设计这个实践性非常强设计课题,咱们进行了大量实训。
通过一种月毕业设计实训,我对于模具特别是塑料模具设计环节有了一种全新结识,丰富了各种模具构造和动作过程方面知识,而对于模具制造工艺更是实现了零突破。
在指引教师协助和解说下,同步在图书馆借阅了许多有关手册和书籍,设计中,我将充分运用和查阅各种资料,并与同窗进行充分讨论,尽最大努力搞好本次毕业设计。
在设计过程中,将有一定困难,但有指引教师悉心指引和自己努力,相信会完满完毕毕业设计任务。
由于学生水平有限,并且缺少经验,设计中不当之处在所难免,肯请各位教师指正。
摘要塑料工业是一门新兴产业,自塑料问世后几十年,塑料来源丰富,制作以便及成本低廉、金属零件塑料化发展不久,在机械电子、国防、交通、通讯、建筑、农业、轻工业和寻常生活用品等行业中都得到了广泛应用,对塑料模具规定量增长。
自动切断浇口注射模的设计

因版权原因,仅展示原文概要,查看原文内容请购买
自动切断浇口注射模的设计
王润华ห้องสมุดไป่ตู้
【期刊名称】《模具工业》
【年(卷),期】1991()10
【摘 要】注射模自动切断浇口,通常采用点浇口与潜伏式浇口,但随着一些制品设计要求的提高,这些常用方法满足不了制品的要求;因此必需采用其它的特殊方式。
【总页数】2页(P34-35)
【关键词】注射成型;模具;自动化;浇口
【作 者】王润华
【作者单位】江西省吉安市塑料工厂
【正文语种】中 文
【中图分类】TQ320.662
【相关文献】
1.注射模侧浇口自动切断结构探讨 [J], 张文玉;向厚淼
2.有机玻璃件侧浇口自动切断注射模设计 [J], 刘黛鹂
3.侧浇口自动切断注射模 [J], 许思光
4.内侧边浇口自动切断注射模设计 [J], 朱卫锋
TB注塑机上侧浇口自动切断模具的设计

TB注塑机上侧浇口自动切断模具的设计发布:2010-5-5 10:02:10 来源:模具网编辑:佚名1.TB注塑机简介TB注塑机(或曰T款注塑机)的结构如下图所示,包括现有普通注塑机的锁模油缸1、锁模机构3、动板4、头板7、控制面板、喷嘴、射移油缸10、料筒12、料斗13、注射油缸14、机身15等,其独有机构就是在已有技术注塑机的头板增加了一套“流道推板”机构6,该机构通过一组油缸8、电磁阀等与塑机的液压系统相连,通过电脑控制程序,使该机构根据所需时间在头板内进行往复运动。
通过流道推板推顶设在模具上的推杆,以配合各种类型模具完成各种不同的动作,从而达到降低开模费、提高注塑效率、降低注塑成本等之目的。
TB注塑机可以很简单的实现侧浇口的自动切断;简单的实现点浇口,点、侧复合浇口与流道的自动分离。
很简单的实现静模的竖向抽芯、侧抽芯、倒装模等。
本篇介绍在TB注塑机上侧浇口自动切断模具的设计。
只要浇口位于图2.2 TB注塑机的流道推板(L x W x D - d)的范围内,侧浇口注射模均可实现浇口的自动切断。
2. 动模切刀侧浇口自动切断注射模的设计图4.1所示为在TB注塑机上使用的侧浇口自动切断注射模。
与在普通注塑机上使用的模具相比,主结构相同,增加的零件有(每腔)浇口切刀6、切刀复位块8、弹簧5和推杆9各一件。
左下a图为浇口切刀6与切刀复位块8的侧面投影图。
其动作原理(顺序)为:注射(注塑机流道推板6在推板油缸8的作用下使图4.1推杆9位于图示位置,融溶塑料通过流道12、浇口切刀6和切刀复位块8之间的浇口进入型腔7,直至填充结束)——浇口切断(制品7固化成型后,注塑机流道推板6后退,使图4.1浇口切刀6、切刀复位块8、推杆9在弹簧5的作用下前进,将流道12与制品7分离)——开模(动模固定板1、动模4等随图2. 1注塑机动板4后退,使静模10与动模4等分离,制品7与流道12滞留在动模镶件14上,直至开模结束)——制品、流道顶出(注塑机顶出杆前进,带动图4.1推杆3、13、复位杆15等前进,将制品7和流道12顶出动模镶件14,取走或自动落下)——合模(注塑机顶出杆与流道推板6复位,动板2带动图4.1动模4等前进,推杆3、13、推杆固定板2等在复位杆15的作用下复位;浇口切刀6、弹簧5在推杆9、切刀复位块8的作用下复位;直至合模结束)。
塑料注射成型模具浇注系统设计-文档资料

停滞现象容易使工件的某些部 分过度保压,某些部分保压不足, 从而使內应力增加许多。
1.要能保证塑件的质量(避免常见的充填问题 )
尽量避免出现熔接痕
熔接痕的存在主要会影响外 观,使得产品的表面较差;而出 现熔接痕的地方強度也会较差。
1.要能保证塑件的质量(避免常见的充填问题 ) 尽量避免过度保压和保压不足
有利于保证塑件质量
要考虑飞边在塑件上的位置
分型面的选择要有利于简化模具结构
尽可能的避免侧向分型或者抽芯
分型面的选择要有利于简化模具结构
尽可能的避免侧向分型或者抽芯
分型面的选择要有利于简化模具结构
尽量地把侧向分型抽芯机构留在动模一侧
分型面的选择要有利于简化模具结构
塑件不止有一个抽芯的时候,在选择分型面时要使较大的 型芯与开模方向一致
4.分流道的布置
流道排列的原则 尽可能使熔融塑料从主流道到各浇口的距离相等。 使型腔压力中心尽可能与注射机的中心重合。
流道的布置 自然平衡 人工平衡
不平衡
自然平衡
人工平衡
§4.3普通浇注系统的设计
五、分流道设计与制造
4.分流道的布置
§4.3普通浇注系统的设计
五、分流道设计与制造
5.分流道制造要点
1.分流道的截面形状 六角形截面
其面积仅为圆形流道 的82%,是最理想的浇 道,但是制造不易, 通常不考虑使用。
2.分流道的设计要点 制品的体积和壁厚,分流道的截面厚度要大于制品的壁厚。
成型树脂的流动性,对于含有玻璃纤维等流动性较差的树 脂, 流道截面要大一些。
流道方向改变的拐角处, 应适当设置冷料穴。
重叠浇口
重叠浇口与侧浇口类似﹐浇口与成品侧壁 或成品表面有重叠。 典型的浇口尺寸为:厚度0.4至 6.4mm﹐宽度为1.6至12.7mm。
《注射模设计》
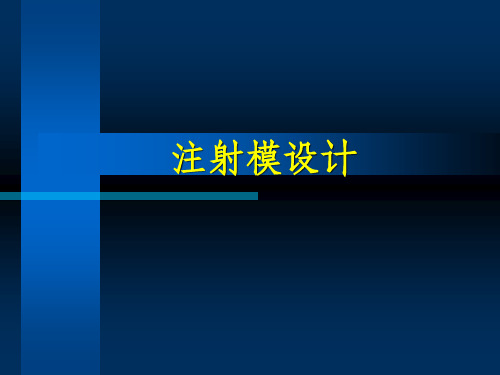
.
39
(二)型腔的布置
1.平衡式浇注系统
分流道到浇口及型腔,其形状、长宽尺寸、圆角、模 壁的冷却条件都完全相同,熔体能以相同的成型压 力和温度同时充满所用型腔。
缺点:流道 总长度要长 些,热量压 力损失大, 模板尺寸大。
.
40
(二)型腔的布置
2.非平衡式浇注系统 由于主流道到各型腔的分流道长度各不相同或 者各型腔形状尺寸不同而使得浇注系统不平衡。
.
16
一、分型面设计 (一)分型面的形式
分型面:是模具上开模时用于取出塑件和(或)浇 注系统冷凝料的可分离的接触表面。
分型面的分类:
1.按其位置与注射机开模运动方向的关系来分类:
垂直于注射机开模运动方向,平行于开模方向,倾 斜于开模方向
2.按分型面的形状来分类 :平面分型面,曲面分型面, 阶梯分型面和斜面分型面
定范围,也不意味浇口浇口越小越好。
.
46
(一)浇注系统流变学
(2)合理的选择剪切速率
在较低的剪切速率范围内,由于剪切速率的微 小变化会引起粘度的巨大变化。这将使注射成型难 以控制,使塑件出现表面不良、充模不匀、密度不 均、内应力高、翘曲以及收缩不均等毛病。所以,
要在ηa ~γ́ 曲线上选取这么一段剪切速率,使它
.
20
(二)选择分型面的原则
使塑件开模时留在动模侧:
.
21
(二)选择分型面的原则
简化模具制造:
.
22
(二)选择分型面的原则
有利于抽芯(活动型芯置于动模):
.
23
(二)选择分型面的原则
有利于抽芯(缩短抽芯距离):
.
24
(二)选择分型面的原则
- 1、下载文档前请自行甄别文档内容的完整性,平台不提供额外的编辑、内容补充、找答案等附加服务。
- 2、"仅部分预览"的文档,不可在线预览部分如存在完整性等问题,可反馈申请退款(可完整预览的文档不适用该条件!)。
- 3、如文档侵犯您的权益,请联系客服反馈,我们会尽快为您处理(人工客服工作时间:9:00-18:30)。
摘要塑料工业是当今世界上增长最快的工业门类之一,而注塑模具是其中发展较快的种类,因此,研究注塑模具对了解塑料产品的生产过程和提高产品质量有很大意义。
本设计首先说明了塑料工业的重要地位和当今注塑模具的现状,随着经济的发展,塑料工业将继续呈现蓬勃发展之势。
其次介绍了注塑件的一般设计原则,对塑件的特征如倒圆角、加强筋等做了说明,从实际来看,几乎所有的注塑件都遵循这些原则。
在做好注塑成型的准备工作之后,接着介绍了模具设计的内容,冷流道注塑模具无外乎包括四大系统:浇注系统、温度调节系统、顶出系统和机构系统(其实也可以归为顶出系统,该系统如斜导柱、滑块和开闭器等)。
在浇注系统的设计中根据经验公式取流道横截面形状,确定浇口尺寸,对流道剪切速率进行校核;温度调节系统说明了设计的一般步骤,确定冷却时间,计算体积流量等;顶出系统着重说明了推杆,推管的安装要求,并进行强度校核;该模具属于简单脱模机构,无滑块抽芯机构,也无开模先后顺序的要求,做完这些工作之后,该模具的设计到此结束。
关键词:注塑;瓶盖;模具ABSTRACTplastic industry is in the world grows now one of quickest industry classes, but casts the mold is development quick type, therefore, the research casts the mold to understand the plastic product the production process and improves the product quality to have the very big significance.This design introduced the injection takes shape the basic principle, specially single is divided the profile to inject the mold the structure and the principle of work, to cast the product to propose the basic principle of design; Introduced in detail the cold flow channel injection evil spirit mold pours the system, the temperature control system and goes against the system the design process, and has given the explanation to the mold intensity request; Finally introduced now in the world the most popular three dimensional CAD/CAM system standard software PRO/ENGNEER's PROGRAM module, and led the wrap to the guide pillar to carry on the parametrization design.Through this design, may to cast the mold to have a preliminary understanding, notes in the design certain detail question, understands the mold structure and the principle of work; Through to the PROGRAM study, may establish the simple components the components storehouse, thus effective enhancement working efficiency.Key word: Injection;Cap;Mold目录1成型工艺拟定及选用设备 (4)1.1制品成型工艺的分析。
(4)1.2成型工艺规程的拟定。
(4)1.2.1 ABS 塑料的成型特性:(查表1—5,塑料模设计手册,机工版) 41.2.2成型工艺规程: (4)1.2.3成型设备的类型、型号及技术参数选择。
(5)(1) 估算制件的体积、重量以及正面投影面积: (5)2模具结构设计 (7)2.1模具类型及结构形式的确定。
(7)2.2制件分型面的确定。
(7)2.3型腔数目的确定和排列。
(7)2.4 确定浇注系统的位置和类型。
(8)2.5 型腔零件的结构设计。
(8)2.5.1 成型零件工作尺寸的计算。
(8)2.5.2 成型零件的结构设计 (9)2.6动模部分的支承板设计 (12)2.7模具结构零件设计 (12)2.7.1导柱、导套的设计 (12)2.7.2抽芯机构设计 (14)2.7.3脱模机构设计: (16)2.7.4浇口套的设计 (19)3模具温度调节系统设计 (20)3.1冷却系统的设计 (20)3.1.1冷却水管道的设计计算: (20)3.1.2冷却水管道的布置. (22)4模具总体尺寸的确定 (23)4.1模具总厚度设计 (23)4.2模具外型轮廓尺寸校核 (23)4.3模具安装槽的校核: (23)4.4锁模力的校核: (23)5典型工作零件的热处理及加工工艺的制订 (25)5.1定模板。
(25)5.2主型芯。
(25)6本设计在实用过程中可能存在的问题及解决办法 (26)7毕业设计小结 (27)8主要参考文献 (28)致谢 (29)1成型工艺拟定及选用设备1.1制品成型工艺的分析。
①该制品属盖壳类塑件,形状结构较简单,壁厚均匀;因塑件的尺寸精度和外形精度要求较高。
故可选用收缩率较小的常用塑料 ABS。
②.根据制件的表面质量要求高、壁厚中等及 ABS塑料成型流动性差的特点,可选中心点浇口,以保证塑件壁厚均匀。
表面无明显浇口痕迹。
③.为了防止制件在顶出时不变形,采用推板+推杆+推管的组合方式将制件顶出。
④.因制件的侧形状简单,尺寸较小,抽芯距离不大,抽芯力小等特点,故采用弹簧侧抽芯机构。
⑤.该制件的技术要求及所选用的塑料成型特性,宜采用注射成型的方式成型。
1.2成型工艺规程的拟定。
1.2.1 ABS 塑料的成型特性:(查表1—5,塑料模设计手册,机工版)①无定形塑料,其品种牌号很多,各种的机电性能及成型特性也各有差异。
应按品种确定成形方法及成形条件。
②吸湿性强,含水量应小于0.3%,必须充分干燥。
要求表面光泽的塑件应要求长时间预热干燥。
③流动性中等,溢边料0.04毫米左右。
(流动性比聚苯乙烯,AS差,但比聚碳酸酯、聚氯乙烯好。
)④比聚苯乙烯加工困难,宜取高料温,模温。
⑤模具设计时要注意浇注系统对料六阻力小,进料口出外观不良,易发生熔接痕,应注意选择进料口位置,形式,顶出力过大或机械加工时塑料表面呈现“白色”痕迹,脱模斜度宜取2°以上。
1.2.2成型工艺规程:①注射成形机类型:螺杆式。
②料筒温度:前段: 180~200℃中段: 165~180℃后段: 150~170℃③预热:温度 80~85℃时间 2~3小时。
④.喷咀温度: 180℃~190℃⑤.模具温度: 50 ~80 ℃⑥.注射压力: 100 ~ 140 ℃⑦.成型时间:a.注射时间:20—90秒b.高压时间:0—5秒c.冷却时间:20—150秒。
说明:塑料成型的料筒温度、模具温度、保压时间的控制对于制品的成型质量是非常重要的,实践中必须根据多次试模,不断调整成型工艺参数,以达到制件的生产要求的工艺参数。
1.2.3成型设备的类型、型号及技术参数选择。
(1) 估算制件的体积、重量以及正面投影面积:a.体积 V体:V1=3.14×4.4×0.3-3.14×4.0 ×4.0×0.3=3.16 cm3V2=3.14×(4×4-3.7×3.7)=14.5 cm3V3=3.14×3.7×3.7×0.3=12.9 cm3V4=3.14×2.1(0.7×07-0.4×0.4)=2.17 cm3V5=3.14×0.33×2=0.17 cm3V6=V1+V2+V3+V4-V5=3.2+14.5+12.9+2.17-0.17=32.6 cm3b.塑件重量G:查表1—4(塑料设计手册,机工版)得ABS的比重:1.05g /cm3G = PV=1.05×32.6= 34 克c.正面投影面积 F投:F投 = 3.14×404×4.4=60.8 cm2①成型设备选择。
a.容量V注的计算:由公式: 0.8V注≥V件得:V注 = V件/0.8= 32.6/0.8=40.7 cm3b.根据初步估算的注射容量,查表8(塑料模设计手册)得到预选注塑机的类型、型号及技术参数:XS—ZY—60型注塑机技术规范及特性2模具结构设计2.1模具类型及结构形式的确定。
根据制件的基本结构,为满足已拟定好的成型工艺,即使于浇注系统的废料取出、侧孔的成型抽心要求。
故该模具可选定双分型面注射模。
2.2制件分型面的确定。
便于塑件的取出及有利于侧向抽心,应采用如图所示的分型面。
即Ⅰ--Ⅰ分型面:3 - 1图2.3型腔数目的确定和排列。
因该制件的年产量只有1万件,批量不大,精度要求较高,故宜采用将型腔排在模具中心部位。
2.4 确定浇注系统的位置和类型。
根据所选用塑料成型特性和模具类型,为保证制件的成型和质量,采用中心点浇口形式,如3—1图所示。
2.5 型腔零件的结构设计。
2.5.1 成型零件工作尺寸的计算。
根据制件图所给的尺寸,所选塑料的收缩率,脱模斜度等有关数据进行计算。
取脱模斜度 2°,ABS塑料的收缩率: S =0.6%.(1)型腔尺寸计算:①φ88-0.20尺寸变换为:φ88.1-0.30L1 =[Ls(HS)-3/4△]+δ2=[88.1(1+0.6%)-3/4×0.30]+(0.3×1/4)=88.4+0.075②φ80-0.10L2 =[80(1+0.6%)-3/4×0.10]+(0.10×1/4)=80.4+0.025③φ14.1L3 =[Ls(1+S)-3/4△]+δ2=[14.1(1+0.6%)-3×0.1/4]+(1/4×0.2)=14.1+0.05④ 20-0.10H4 =[Hs(1+s)-2/3Δ]+δ2=[20(1+0.6%)-2/3×0.1]+(0.1×1/4)=20.06+0.075⑤ 21-0.10H5=[Hs(1+s)-2/3Δ]+δ2=[21(1+0.6%)-2/3×0.1]+(0.1×1/4)=21.08+0.025(2)型芯尺寸的计算。