压铸试模加工报告范文
压铸工艺实验报告(3篇)

第1篇一、实验目的1. 了解压铸工艺的基本原理和操作流程。
2. 掌握压铸工艺参数对铸件质量的影响。
3. 提高对压铸工艺缺陷的分析和解决能力。
二、实验设备与材料1. 实验设备:压铸机、压铸模具、加热炉、冷却水系统、实验台等。
2. 实验材料:铝合金、锌合金等。
三、实验原理压铸工艺是一种将熔融金属在高压下快速充填型腔,并在冷却固化后获得所需形状和尺寸的金属零件的加工方法。
实验主要研究压铸工艺参数对铸件质量的影响,包括压力、速度、温度、时间等。
四、实验步骤1. 准备工作:根据实验要求,选择合适的压铸模具和材料,并对模具进行清洗和预热。
2. 加热:将熔融金属加热至适宜的温度,确保金属流动性好,便于充填型腔。
3. 充填:启动压铸机,将熔融金属在高压下快速充填型腔。
4. 冷却:在金属凝固过程中,通过冷却水系统对模具进行冷却,保证铸件尺寸精度。
5. 开模取件:待金属凝固后,打开模具取出铸件。
6. 检查与分析:对铸件进行外观检查,分析铸件缺陷产生的原因,并提出改进措施。
五、实验结果与分析1. 铸件外观质量:实验过程中,铸件外观质量良好,无明显的缩孔、气孔、裂纹等缺陷。
2. 铸件尺寸精度:实验中,铸件尺寸精度较高,与模具设计尺寸基本一致。
3. 铸件内部质量:实验中,铸件内部质量良好,无明显的缩松、夹渣等缺陷。
六、实验结论1. 压铸工艺参数对铸件质量有显著影响。
在实验过程中,通过优化压力、速度、温度、时间等参数,可提高铸件质量。
2. 压铸模具的设计对铸件质量有重要影响。
合理设计模具结构,有利于提高铸件尺寸精度和内部质量。
3. 在压铸过程中,应注意控制熔融金属的温度和流动性,以保证铸件质量。
七、实验改进措施1. 优化压铸工艺参数:通过实验,进一步优化压力、速度、温度、时间等参数,以提高铸件质量。
2. 优化模具设计:针对铸件缺陷,对模具结构进行改进,以提高铸件尺寸精度和内部质量。
3. 加强操作技能培训:提高操作人员对压铸工艺的理解和操作技能,确保实验顺利进行。
铸造锻造压铸实习报告

铸造锻造压铸实习报告在过去的一个月里,我有幸参与了铸造、锻造和压铸三个环节的实习。
这段时间的学习和实践,使我对金属成型工艺有了更深入的了解,同时也让我认识到了理论与实际相结合的重要性。
以下是我在实习过程中的所见、所闻和所感。
一、铸造实习铸造实习主要是了解和掌握砂型铸造的基本工艺流程。
在实习过程中,我学会了如何制作砂型、选择合适的铸造合金以及进行熔炼和浇注。
此外,我还了解了铸件的冷却、打磨和清理等后续工艺。
通过实习,我认识到铸造工艺的复杂性和对精度的要求。
在实际操作中,我深刻体会到了理论知识在解决实际问题中的指导作用。
二、锻造实习锻造实习让我对锻造工艺有了更直观的认识。
在实习过程中,我学会了如何选择合适的锻造设备和工具,以及如何确定锻造工艺参数。
通过实际操作,我了解了锻造过程中的变形规律、应力分布和裂纹产生原因等。
同时,我还掌握了锻造后产品的热处理工艺。
这次实习使我认识到锻造工艺在提高金属材料性能方面的重要性。
三、压铸实习压铸实习是我这次实习的重点。
在实习过程中,我了解了压铸工艺的基本原理、设备结构和操作方法。
我学会了如何制备压铸模具、选择合适的压铸材料以及控制压铸过程中的温度和压力。
通过实际操作,我掌握了压铸过程中模具的打开、取出铸件和清理等操作。
这次实习使我深刻认识到压铸工艺在生产高精度、复杂形状产品方面的高效性。
总结:通过这次实习,我对铸造、锻造和压铸三种金属成型工艺有了全面的了解。
在实际操作中,我学会了如何运用理论知识解决实际问题,也认识到了实践是检验真理的唯一标准。
同时,我还培养了动手能力和团队协作精神。
这次实习对我的专业学习和未来职业生涯具有重要意义。
在今后的学习和工作中,我将继续努力,将所学知识与实践相结合,为我国金属成型工艺的发展贡献自己的力量。
压铸试模总结报告范文(3篇)

第1篇一、项目背景随着我国汽车、电子、电器等行业的发展,对精密金属制品的需求日益增加。
压铸作为一种高效、节能、环保的金属成型工艺,广泛应用于各类产品的制造中。
为了确保压铸件的质量和性能,试模环节至关重要。
本报告针对某型号压铸件进行试模,总结试模过程中的经验与教训,为后续生产提供参考。
二、试模目的1. 确保压铸件尺寸精度和表面质量;2. 优化模具结构,降低生产成本;3. 提高生产效率,缩短生产周期;4. 评估压铸工艺参数,为生产提供依据。
三、试模过程1. 模具设计:根据产品图纸,设计压铸模具,包括型腔、浇注系统、冷却系统等。
2. 模具加工:按照模具设计图纸,进行模具加工,确保模具精度和表面质量。
3. 模具装配:将加工好的模具零件进行装配,确保模具的刚性和密封性。
4. 工艺参数确定:通过实验,确定压铸工艺参数,如熔体温度、压射速度、保压压力、冷却时间等。
5. 压铸实验:在确定的工艺参数下,进行压铸实验,观察压铸件的尺寸精度、表面质量、内部缺陷等。
6. 数据分析:对实验数据进行整理和分析,评估压铸件的质量和性能。
四、试模结果1. 尺寸精度:压铸件尺寸精度达到产品图纸要求,无明显的尺寸偏差。
2. 表面质量:压铸件表面光滑,无明显的缺陷,如气孔、夹杂等。
3. 内部缺陷:压铸件内部无明显的缩松、冷隔等缺陷。
4. 生产成本:通过优化模具结构和工艺参数,降低了生产成本。
5. 生产效率:压铸实验证明,压铸件生产周期可缩短20%。
五、总结与建议1. 优化模具设计:在保证模具刚性和密封性的前提下,简化模具结构,降低生产成本。
2. 严格控制工艺参数:根据实验结果,确定合理的熔体温度、压射速度、保压压力、冷却时间等工艺参数。
3. 加强过程控制:在生产过程中,严格控制熔体温度、压射速度、保压压力等关键参数,确保压铸件质量。
4. 优化生产线:提高生产线自动化程度,降低人工成本,提高生产效率。
5. 持续改进:针对试模过程中发现的问题,持续改进模具设计、工艺参数和生产工艺,提高产品质量。
压铸模具试模报告

压铸模具试模报告一、试模目的本次试模的目的是验证设计的压铸模具的可行性和合理性,确保模具能够顺利进行压铸生产,并满足产品的质量要求。
二、试模流程1.准备工作:将设计好的压铸模具部件进行加工和组装,并进行调试和检验,确保各个部分的相互配合良好。
2.模具安装:将加工好的模具安装到压铸机上,并进行调整和固定,确保模具的稳定性和安全性。
3.试模参数设置:根据要压铸的产品要求,设置合适的压射速度、压射压力和保压时间等参数。
4.试模过程:根据设定的参数,进行试模生产,观察模具的工作情况和产品的成型情况。
5.试模结果评估:根据试模生产的结果,评估模具的性能和产品的质量,对需要改进的地方进行记录,以供后续优化和改进。
三、试模结果本次试模生产顺利完成,模具的设计和制造都符合要求,试模生产过程中,模具工作稳定,产品形状完整,尺寸准确,表面光洁度良好。
经过试模生产的检验,模具能够满足产品的质量要求,达到了设计的预期效果。
四、试模存在问题和改进方案1.模具开模力不稳定:在试模过程中发现模具的开模力变化较大,可能导致产品形状不一致。
改进方案是对模具的开模机构进行检查和调整,确保开模力的稳定性。
2.产品表面有毛刺:在试模生产的产品上发现有些部分的表面有明显的毛刺,影响了产品的外观质量。
改进方案是对模具的冷却系统进行优化,增加冷却介质的流动,提高冷却效果,减少产品的毛刺现象。
3.模具寿命较短:经过试模生产后,发现模具的使用寿命较短,需要频繁更换和维修,增加了生产成本。
改进方案是对模具的材质和加工工艺进行优化,提高模具的硬度和韧性,延长使用寿命。
五、结论通过本次试模生产,我们验证了设计的压铸模具的可行性和合理性,同时也发现了一些模具存在的问题和需要改进的地方。
在优化和改进之后,这个模具将会更加稳定和可靠,能够满足产品的生产需求,提高生产效率和产品质量。
同时,本次试模生产也为以后的压铸模具设计和制造提供了宝贵的经验和参考依据。
压力铸造生产试验总结汇报

压力铸造生产试验总结汇报压力铸造生产试验总结报告一、试验目的及背景压力铸造是一种常用的金属铸造工艺,通过在金属液面加压的方式,使金属在模具中快速凝固形成所需形状的铸件。
本次试验旨在探索压力铸造工艺的可行性,为实际生产提供参考和指导。
二、试验设计与步骤1. 原材料准备:选取铝合金材料作为试验对象,按照一定比例配制合金料。
2. 模具设计与制备:设计制造适合压力铸造工艺的模具。
3. 设备准备:根据试验需求,确保压力铸造机正常运转。
4. 试验操作:将铝合金液倒入模具中,打开压力铸造机,加压到合适的数值,并保持一段时间,待金属充分凝固。
5. 铸件处理:将压力铸造得到的铸件进行去除毛刺、清洗等处理。
三、试验结果1. 铸件质量:通过试验,我们成功地得到了符合要求的铸件,其外观光滑,尺寸精确,没有明显的缺陷。
2. 成型效率:压力铸造相对于传统铸造工艺,具有快速成型的优势,试验中,我们成功地在短时间内完成了多次铸造,整体效率较高。
3. 成本控制:压力铸造过程中,可以节约原材料的同时,降低了人工成本,有效提升了生产效益。
四、试验中的问题与改进措施1. 压力控制:试验过程中,对于合适的压力选择存在一定难度,需要进一步优化设备参数,以确保铸件的成型效果。
2. 模具设计:试验中,模具的设计对铸件质量和成型效率有着重要影响,需要进一步改进模具结构,提高其稳定性和使用寿命。
3. 工艺参数的优化:通过进一步研究和探索,需要优化铝合金的成组比例、温度控制等工艺参数,以获得更好的成型效果。
五、试验结论与展望1. 通过本次压力铸造生产试验,我们证明了压力铸造工艺在铸件生产中的可行性和优势。
2. 在实际生产中,我们可以结合试验结果,进一步完善压力铸造工艺流程和参数设定,提高铸件质量和生产效率。
3. 同时,我们也将继续研究和改进压力铸造工艺,探索更广泛的应用领域,提高工艺水平和技术竞争力。
六、参考文献[1] 压力铸造工艺的研究与应用,XXX,XXX出版社,2018年[2] 压力铸造工艺参数优化的方法研究,XXX,XXX期刊,2020年以上是本次压力铸造生产试验的总结报告,感谢各位的支持与参与!。
压铸模具设计实训报告
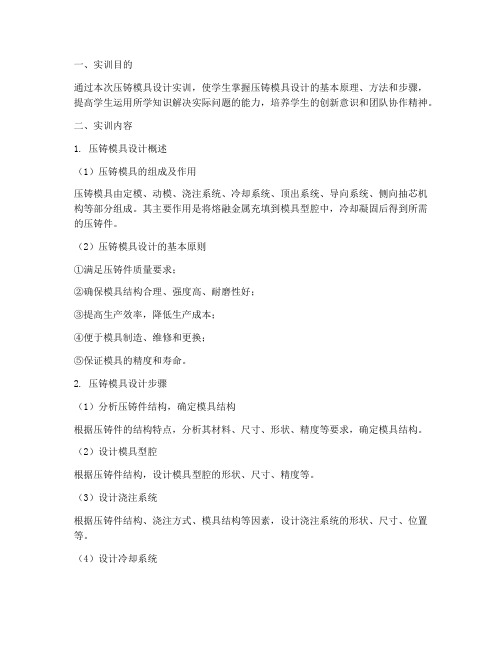
一、实训目的通过本次压铸模具设计实训,使学生掌握压铸模具设计的基本原理、方法和步骤,提高学生运用所学知识解决实际问题的能力,培养学生的创新意识和团队协作精神。
二、实训内容1. 压铸模具设计概述(1)压铸模具的组成及作用压铸模具由定模、动模、浇注系统、冷却系统、顶出系统、导向系统、侧向抽芯机构等部分组成。
其主要作用是将熔融金属充填到模具型腔中,冷却凝固后得到所需的压铸件。
(2)压铸模具设计的基本原则①满足压铸件质量要求;②确保模具结构合理、强度高、耐磨性好;③提高生产效率,降低生产成本;④便于模具制造、维修和更换;⑤保证模具的精度和寿命。
2. 压铸模具设计步骤(1)分析压铸件结构,确定模具结构根据压铸件的结构特点,分析其材料、尺寸、形状、精度等要求,确定模具结构。
(2)设计模具型腔根据压铸件结构,设计模具型腔的形状、尺寸、精度等。
(3)设计浇注系统根据压铸件结构、浇注方式、模具结构等因素,设计浇注系统的形状、尺寸、位置等。
(4)设计冷却系统根据压铸件材料、形状、尺寸、模具结构等因素,设计冷却系统的形状、尺寸、位置等。
(5)设计顶出系统根据压铸件结构、模具结构、生产要求等因素,设计顶出系统的形状、尺寸、位置等。
(6)设计导向系统根据模具结构、压铸件精度要求等因素,设计导向系统的形状、尺寸、位置等。
(7)设计侧向抽芯机构根据压铸件结构、模具结构、生产要求等因素,设计侧向抽芯机构的形状、尺寸、位置等。
(8)设计模具结构图根据以上设计内容,绘制模具结构图。
3. 压铸模具设计软件应用本次实训使用SolidWorks软件进行压铸模具设计。
SolidWorks是一款功能强大的三维设计软件,可以方便地进行模具设计、分析、模拟等。
三、实训过程1. 学习压铸模具设计的基本原理、方法和步骤通过查阅相关资料、学习教材、参加讲座等方式,掌握压铸模具设计的基本知识。
2. 分析压铸件结构,确定模具结构根据实训任务,分析压铸件结构,确定模具结构。
试模总结报告范文(3篇)
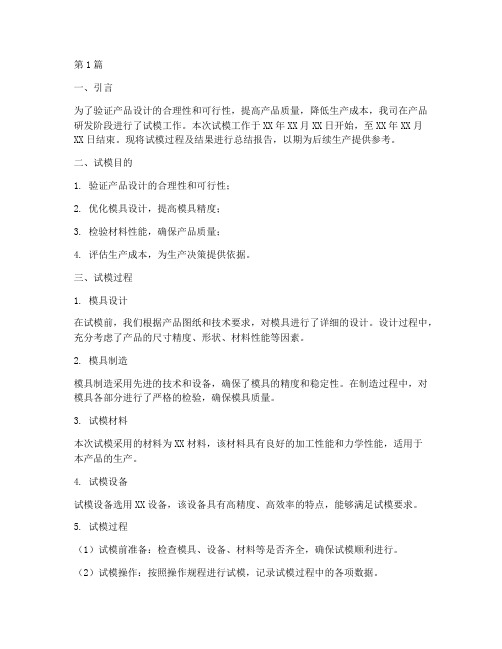
第1篇一、引言为了验证产品设计的合理性和可行性,提高产品质量,降低生产成本,我司在产品研发阶段进行了试模工作。
本次试模工作于XX年XX月XX日开始,至XX年XX月XX日结束。
现将试模过程及结果进行总结报告,以期为后续生产提供参考。
二、试模目的1. 验证产品设计的合理性和可行性;2. 优化模具设计,提高模具精度;3. 检验材料性能,确保产品质量;4. 评估生产成本,为生产决策提供依据。
三、试模过程1. 模具设计在试模前,我们根据产品图纸和技术要求,对模具进行了详细的设计。
设计过程中,充分考虑了产品的尺寸精度、形状、材料性能等因素。
2. 模具制造模具制造采用先进的技术和设备,确保了模具的精度和稳定性。
在制造过程中,对模具各部分进行了严格的检验,确保模具质量。
3. 试模材料本次试模采用的材料为XX材料,该材料具有良好的加工性能和力学性能,适用于本产品的生产。
4. 试模设备试模设备选用XX设备,该设备具有高精度、高效率的特点,能够满足试模要求。
5. 试模过程(1)试模前准备:检查模具、设备、材料等是否齐全,确保试模顺利进行。
(2)试模操作:按照操作规程进行试模,记录试模过程中的各项数据。
(3)试模结果分析:对试模结果进行分析,评估产品性能和模具质量。
四、试模结果及分析1. 产品性能(1)尺寸精度:产品尺寸精度达到设计要求,符合国家标准。
(2)形状:产品形状符合设计图纸,无明显变形。
(3)表面质量:产品表面光滑,无明显划痕、气泡等缺陷。
2. 模具质量(1)模具精度:模具精度达到设计要求,无明显磨损。
(2)模具稳定性:模具在试模过程中运行稳定,无异常现象。
3. 材料性能(1)力学性能:材料力学性能符合设计要求,具有较好的强度和韧性。
(2)加工性能:材料加工性能良好,易于加工。
4. 生产成本(1)模具成本:模具成本合理,符合预算。
(2)材料成本:材料成本合理,符合预算。
五、结论1. 产品设计合理,可行性高。
2. 模具设计精度高,稳定性好。
压铸试模报告

是□ 否□
I:产品顶杆孔和销子孔是否有毛刺 是□ 否□
J:产品上下分型面是否错位现象 是□ 否□
K:产品上销子碰穿孔是否过盈 是□ 否□
22.后期试模中要注意那些问题? 23.其它
L:产品是否有冲浇口现象 M:取样20pcs产品的平均重量
是□ 否□ 克
其他:
总结方
试模总结要求
总结人
日期
试模负责
项目负责
12.模腔内是否有氩焊痕? 13.模具腔内抛光要求是否满足生产要 求? 14.模具上滑块部位是否顺畅?
是□ 否□ 是□ 否□ 是□ 否□ 是□ 否□
A:产品表面是否有冷隔.花斑 B:产品表面是否有气泡 C:产品内部有超出标准的气孔 D:产品周边是否有缺料
占% 占% 占% 占%
5.模具压板位置是否符合机台要求? 是□ 否□ 15.模具上顶杆顶出是否顺畅?
8.喷雾吹气时间
(S)
12
本次试模问题点
设定值 实际值
13
14
15 每模总周期 (S)
1.模具上标识是否清晰明确? 2.上下模起吊孔环是否可以拧入到 位? 3.吊环孔位置是否与其它不会干涉?
4.模具结构规格是否与机台相匹配?
是□ 否□ 是□ 否□ 是□ 否□ 是□ 否□
11.模腔内是否有开裂痕和龟裂痕?
品质负责
模具工程 师
1.所有新产品试模全部按本单要求进行记录和反馈,必要时要附加图片。
表单流程
2.试模组根据(新品制作计划)内容要求落实试模工作,过程中产品不良缺陷统计的数据必须由工程项目和QE负责共同完成记录。其它信 息数据由试模组主导完成,模具工程师加以确认。
3.试模后两天内试模组把本单交付给工程项目,作为压铸工序新项目需要改善的依据。
- 1、下载文档前请自行甄别文档内容的完整性,平台不提供额外的编辑、内容补充、找答案等附加服务。
- 2、"仅部分预览"的文档,不可在线预览部分如存在完整性等问题,可反馈申请退款(可完整预览的文档不适用该条件!)。
- 3、如文档侵犯您的权益,请联系客服反馈,我们会尽快为您处理(人工客服工作时间:9:00-18:30)。
压铸试模加工报告范文
压铸试模加工报告
一、引言
压铸试模是用于进行压铸工艺试验的模具,其制作质量直接影响到压铸工艺的稳定性和产品质量。
本报告主要介绍了压铸试模的加工过程和相关实验结果。
二、材料准备
压铸试模的制作主要采用了铝合金材料,先进行了材料的购买和切割处理,确保材料具有一定的机械性能和加工性能。
三、加工工艺
1. 设计和制作模具结构:根据压铸试模的尺寸和要求,进行了模具结构的设计,并利用CAD软件进行了模具结构的三维设计和虚拟装配。
2. 加工模具零件:根据模具结构的设计图纸,进行了模具零件的加工。
首先进行了零件的数控铣削,保证零件的尺寸精度和装配精度。
然后进行了模具的钻孔加工和铣削加工,保证了模具的互换性和使用性能。
3. 装配和调试模具:根据模具设计图纸,进行了模具零件的装配,并进行了相关的调试工作,确保模具的孔位互换性和装配精度。
四、实验结果
1. 试模工艺性能测试:对已制作好的压铸试模进行了工艺性能测试,包括模具的开合力、模具的顶出力、模具的冷却性能等参数。
通过实验结果可以得出,该模具的开合力和顶出力达到设计要求,冷却性能良好。
2. 产品测试:使用已制作好的压铸试模进行了压铸工艺试验,得到了一批压铸产品。
通过对产品的外观质量、尺寸精度和机械性能等进行测试,结果表明,产品具有良好的外观质量和尺寸精度,机械性能满足设计要求。
五、问题和改进措施
在加工过程中,发现了一些问题,例如模具零件的加工精度不高、模具的冷却系统设计不合理等。
为了解决这些问题,可以采取以下改进措施:提高模具零件的加工精度,优化模具的冷却系统,以提高模具的使用性能和产品质量。
六、总结
通过对压铸试模的加工过程和实验结果的分析,可以得出结论:本次压铸试模加工质量良好,实验结果满足设计要求。
通过改进措施,可以进一步提高压铸试模的加工精度和产品质量,实现更好的工艺效果和经济效益。
七、参考文献
1. 张某某. 压铸试模加工技术与应用. 机械工业出版社,2009.
2. 李某某. 压铸试模结构设计原理. 机械工业杂志,2010,(1): 45-50.
以上即是本次压铸试模加工报告的全部内容,感谢各位的支持和参与。