加工中心两种对刀方式
加工中心对刀与刀具补偿操作教程

加工中心对刀与刀具补偿操作教程时间:2012-05-30 作者:模具联盟网点击: 1479 评论:0 字体:T|T一、对刀对刀方法与具体操作同数控铣床。
二、刀具长度补偿设置加工中心上使用的刀具很多,每把刀具的长度和到 Z 坐标零点的距离都不相同,这些距离的差值就是刀具的长度补偿值,在加工时要分别进行设置,并记录在刀具明细表中,以供机床操作人员使用。
一般有两种方法:1、机内设置这种方法不用事先测量每把刀具的长度,而是将所有刀具放入刀库中后,采用 Z 向设定器依次确定每把刀具在机床坐标系中的位置,具体设定方法又分两种。
( 1 )第一种方法将其中的一把刀具作为标准刀具,找出其它刀具与标准刀具的差值,作为长度补偿值。
具体操作步骤如下:①将所有刀具放入刀库,利用 Z 向设定器确定每把刀具到工件坐标系 Z 向零点的距离,如图 5-2 所示的 A 、 B 、 C ,并记录下来;②选择其中一把最长(或最短)、与工件距离最小(或最大)的刀具作为基准刀,如图 5-2 中的 T03 (或 T01 ),将其对刀值 C (或 A )作为工件坐标系的 Z 值,此时 H03=0 ;③确定其它刀具相对基准刀的长度补偿值,即 H01= ±│ C-A │, H02= ±│ C-B │,正负号由程序中的 G43 或 G44 来确定。
④将获得的刀具长度补偿值对应刀具和刀具号输入到机床中。
( 2 )第二种方法将工件坐标系的 Z 值输为 0 ,调出刀库中的每把刀具,通过 Z 向设定器确定每把刀具到工件坐标系 Z 向零点的距离,直接将每把刀具到工件零点的距离值输到对应的长度补偿值代码中。
正负号由程序中的 G43 或 G44 来确定。
2、机外刀具预调结合机上对刀这种方法是先在机床外利用刀具预调仪精确测量每把在刀柄上装夹好的刀具的轴向和径向尺寸,确定每把刀具的长度补偿值,然后在机床上用其中最长或最短的一把刀具进行 Z 向对刀,确定工件坐标系。
浅谈加工中心零件的对刀
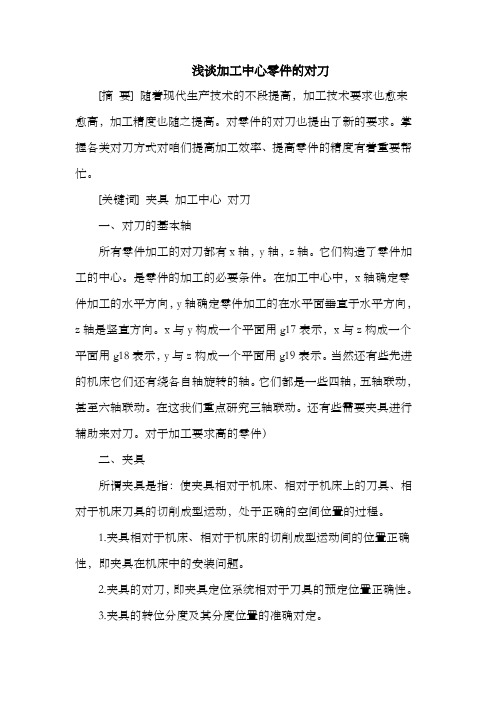
浅谈加工中心零件的对刀[摘要] 随着现代生产技术的不段提高,加工技术要求也愈来愈高,加工精度也随之提高。
对零件的对刀也提出了新的要求。
掌握各类对刀方式对咱们提高加工效率、提高零件的精度有着重要帮忙。
[关键词] 夹具加工中心对刀一、对刀的基本轴所有零件加工的对刀都有x轴,y轴,z轴。
它们构造了零件加工的中心。
是零件的加工的必要条件。
在加工中心中,x轴确定零件加工的水平方向,y轴确定零件加工的在水平面垂直于水平方向,z轴是竖直方向。
x与y构成一个平面用g17表示,x与z构成一个平面用g18表示,y与z构成一个平面用g19表示。
当然还有些先进的机床它们还有绕各自轴旋转的轴。
它们都是一些四轴,五轴联动,甚至六轴联动。
在这我们重点研究三轴联动。
还有些需要夹具进行辅助来对刀。
对于加工要求高的零件)二、夹具所谓夹具是指:使夹具相对于机床、相对于机床上的刀具、相对于机床刀具的切削成型运动,处于正确的空间位置的过程。
1.夹具相对于机床、相对于机床的切削成型运动间的位置正确性,即夹具在机床中的安装问题。
2.夹具的对刀,即夹具定位系统相对于刀具的预定位置正确性。
3.夹具的转位分度及其分度位置的准确对定。
三、机床夹具的作用机床夹具之所以能够在生产中得到广泛应用,与它在生产中所起的重要作用密不可分。
机床夹具的主要作用可以归纳为以下几方面:1.保证工件的加工精度夹具的设计和应用注重于保证工件的可靠定位和稳定装夹,可使同一批工件的装夹结果几近一致,各工件间的加工条件差异性大为减小。
所以,采用夹具可以在保证工件加工精度的基础上极大地稳定整批工件的加工质量。
2.提高劳动生产率依靠夹具所设置的专门定位元件和高效夹紧装置,可以快速而准确地完成工件在加工工位上的定位和夹紧,省去对工件逐个找正调整的装夹过程。
大大缩短了工件的装夹辅助工时,这对于大批量生产的工件,尤其是对外形轮廓较复杂、不易找正装夹的工件,效果就更家明显。
3.扩大机床工艺范围使用专用夹具可以改变机床的用途,扩大机床的使用范围,实现一机多能。
法兰克加工中心对刀步骤
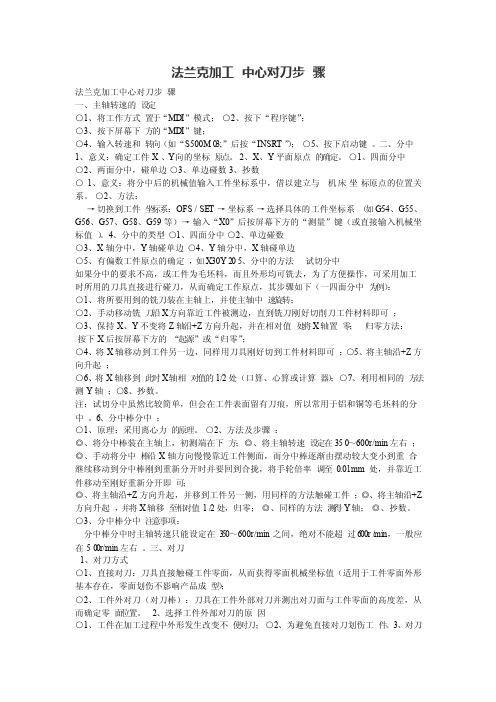
法兰克加工中心对刀步骤法兰克加工中心对刀步骤一、主轴转速的设定○1、将工作方式置于“MDI”模式;○2、按下“程序键”;○3、按下屏幕下方的“MDI”键;○4、输入转速和转向(如“S500M03;”后按“INSRT”);○5、按下启动键。
二、分中1、意义:确定工件X、Y向的坐标原点。
2、X、Y平面原点的确定。
○1、四面分中○2、两面分中,碰单边○3、单边碰数 3、抄数○1、意义:将分中后的机械值输入工件坐标系中,借以建立与机床坐标原点的位置关系。
○2、方法:→切换到工件坐标系:OFS / SET →坐标系→选择具体的工件坐标系(如G54、G55、G56、G57、G58、G59等)→输入“X0”后按屏幕下方的“测量”键(或直接输入机械坐标值)。
4、分中的类型○1、四面分中○2、单边碰数○3、X轴分中,Y轴碰单边○4、Y轴分中,X轴碰单边○5、有偏数工件原点的确定,如X30Y20 5、分中的方法试切分中如果分中的要求不高,或工件为毛坯料,而且外形均可铣去,为了方便操作,可采用加工时所用的刀具直接进行碰刀,从而确定工作原点,其步骤如下(一四面分中为例):○1、将所要用到的铣刀装在主轴上,并使主轴中速旋转;○2、手动移动铣刀沿X方向靠近工件被测边,直到铣刀刚好切削刀工件材料即可;○3、保持X、Y不变将Z轴沿+Z方向升起,并在相对值处将X轴置零;归零方法:按下X后按屏幕下方的“起源”或“归零”;○4、将X轴移动到工件另一边,同样用刀具刚好切到工件材料即可;○5、将主轴沿+Z方向升起;○6、将X轴移到此时X轴相对值的1/2处(口算、心算或计算器);○7、利用相同的方法测Y轴;○8、抄数。
注:试切分中虽然比较简单,但会在工件表面留有刀痕,所以常用于铝和铜等毛坯料的分中。
CNC加工中心是如何对刀
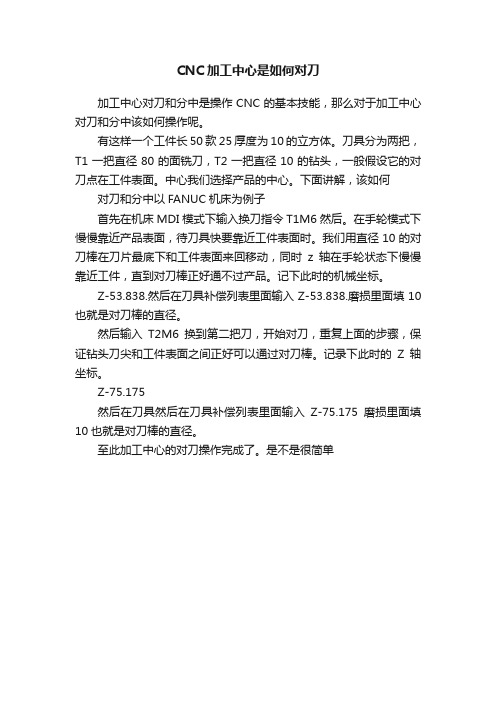
CNC加工中心是如何对刀
加工中心对刀和分中是操作CNC的基本技能,那么对于加工中心对刀和分中该如何操作呢。
有这样一个工件长50款25厚度为10的立方体。
刀具分为两把,T1一把直径80的面铣刀,T2一把直径10的钻头,一般假设它的对刀点在工件表面。
中心我们选择产品的中心。
下面讲解,该如何对刀和分中以FANUC机床为例子
首先在机床MDI模式下输入换刀指令T1M6然后。
在手轮模式下慢慢靠近产品表面,待刀具快要靠近工件表面时。
我们用直径10的对刀棒在刀片最底下和工件表面来回移动,同时z轴在手轮状态下慢慢靠近工件,直到对刀棒正好通不过产品。
记下此时的机械坐标。
Z-53.838.然后在刀具补偿列表里面输入Z-53.838.磨损里面填10也就是对刀棒的直径。
然后输入T2M6换到第二把刀,开始对刀,重复上面的步骤,保证钻头刀尖和工件表面之间正好可以通过对刀棒。
记录下此时的Z轴坐标。
Z-75.175
然后在刀具然后在刀具补偿列表里面输入Z-75.175磨损里面填10也就是对刀棒的直径。
至此加工中心的对刀操作完成了。
是不是很简单。
浅谈加工中心手动对刀技术的改进

有 可 能弄 错 。 我们 可 以按 以 下更 直接 、 更 简便 的方法 进 行对 刀操 作 : 方案 2 : 直 接 刀补 法 ( 不采 用 基 准刀 ) 直 接 刀 具 偏 补法 , 就 是将 所 有 刀 具 都是 对准 T 件 表 面 , 然 后 将 此 时 的机 床 坐标 值直 接 输入 到对 应 的 刀具 长度 补偿 值 中。 对 于 丁件 坐 标 系 的 z坐标 值 清 零 。 它避 免 了基 准 刀具 所 带 来 的 各 种 坐标 计 算, 因此 它更 直接 、 更 方便 。 ( 1 ) 对 刀 步骤 如下 : 第 1 把 z轴 设定 器 ( 5 0 . O 0 m m) 放 置 在 L 件 表面 上 。 第 2调 用 T 1 刀具 , 将 刀具 装在 主 轴上 。 第3 将 该 刀 具 移 动到 z轴 设 定 器上 方 , 并 轻 轻 接触 , 直 到 其 指 针指 示 到 零 位 , 记 下 此 时 的机 床 坐 标 z轴麴 值 , 用 此 数 值 减 去 设 定 器高 度 ( 5 0 . 0 0 a r m) , 将 所 得结 果 输入 到 1 #刀具 补偿 值 中 。 第 4调 用 T 2 刀具 , 将 刀具 装在 主 轴 上。 将 刀具 移动 到 z轴 设 定 器上 方 , 并轻 轻 接触 , 直 到 其 指针 指 示 到零 位 , 记 下 此时 的机床 坐 标
关 键词 : 手 动对 刀 ; 镗铣 类加 工 中心 ; z方向 ; 加 工效 率
引言
工 件 上 常用 的对 刀 表面 有 上表 面 和 下表 面 , 即对 顶为 零 和 对底 为 零 。对 刀方 法有 手 动 对刀 和 利用 对 刀 仪 自动 对 刀 , 而在 实 践 中应 用 较 多 的是 手动 对 刀 。 本文讲述 F A N U C数控系统的镗铣类加工中心 Z轴方 向手动对 刀方法( 对工件顶面为零 , 底面类似 ) 及操作步骤 , 同时分析各 种对 刀 方法 的优缺 点 。 比较 改进 后 的对 刀方 法 的优 点 。 假 设 现 在有 4把 刀具 : T 1( 0 8 0面铣 刀 ) 、 T 2( 1 2 立铣刀 ) 、 T 3 ( 03中心 钻 ) 、 T 4 ( ( I ) 6 . 8 钻头 ) , 当每 把 刀 的 X Y 坐标 值 不 变 时 , 改 变 的则 只是 z坐标 值 。 那 么 我们 在对 刀 时 只要 找准 所 有刀 具 的 z轴 方 向位 于 同一 工 件 表 面上 ,此 时 , z轴 方 向有 一 数 值 ,既是 机 床 坐 标 值, 把 这 一数 值 输 入 到 刀补 中 , 或者 利 用 基 准 刀具 及 与 各 刀 具 的 长 度 差 来 修 正 补偿 值 , 然后 利 用 刀 具 长度 补 偿 指 令 来调 用 该 值 , 即 可 将 所 有 刀具 对准 工 件 的 同一表 面作 为 z轴零 点 。 1 以下将 分 别 介绍 各种 对 刀方 法 、 步 骤及 优 缺点 : 方案 1 : 基准 刀 具法 ( 对 顶 面为 零l l l , 下同) 基 准刀 具 的对 刀思 路是 设 置 一把 基 准 刀 具 , 控 制 该 基 准 刀具 接 触 工 件 上表 面 , 把此 时 的机 床 坐标 值 输人 到 工 件坐 标 系 的 z值 参 数 中。 当调 用其 它 刀具 时 , 将 每把 刀具 都 接触 到该 工 件 同一 表 面上 , 把 此 时的机 床 坐标 值 与基 准 刀具 的机 床 坐标 值 相减 , 将 所 得 结果 输 入 到相 应 刀具 的 刀补 中 。在 编 程时 只要 建 立 该 工件 坐 标 系 , 再应 用 刀 具补 偿 指令 调用 相 应 的刀 具 补偿 值 即可 。 其原 理是 用 基 准刀 具建 立 工 件坐 标 系 , 刀 具 长 度 补偿 值 为 零 , 其 它 刀 具 的 长度 补 偿 值 为 相 应 刀具的机床坐标值减去基准刀具的机床坐标值的差值 。
加工中心对刀方法全解!再也不用担心对刀啦

加工中心对刀方法全解!再也不用担心对刀啦1. 加工中心的Z向对刀加工中心的Z向对刀一般有以下三种方法:1) 机上对刀方法一这种对刀方法是通过对刀依次确定每把刀具与工件在机床坐标系中的相互位置关系。
其具体操作步骤如下。
(1) 把刀具长度进行比较,找出最长的刀作为基准刀,进行Z向对刀,并把此时的对刀值(C)作为工件坐标系的Z值,此时H03=0。
(2) 把T01、T02号刀具依次装在主轴,通过对刀确定A、B的值作为长度补偿值。
(此方法没有直接去测量刀具补偿,而是通过依次对刀确定的与方法三不同.)(3)把确定的长度补偿值(最长刀长度减其余刀具长度)填入设定页面,正、负号由程序中的G43、G44来确定,此时一般用G44H—表示。
当采用G43时,长度补偿为负值。
这种对刀方法的对刀效率和精度较高,投资少,但工艺文件编写不便,对生产组织有一定影响。
2) 机上对刀方法二这种对刀方法的具体操作步骤如下:(1) XY方向找正设定如前,将G54中的XY项输入偏置值,Z项置零。
(2) 将用于加工的T1换上主轴,用块规找正Z向,松紧合适后读取机床坐标系Z项值Z1,扣除块规高度后,填入长度补偿值H1中。
(3) 将T2装上主轴,用块规找正,读取Z2,扣除块规高度后填入H2中。
(4) 依次类推,将所有刀具Ti用块规找正,将Zi扣除块规高度后填入Hi中3) 机外刀具预调+机上对刀这种对刀方法是先在机床外利用刀具预调仪精确测量每把刀具的轴向和径向尺寸,确定每把刀具的长度补偿值,然后在机床上用最长的一把刀具进行Z向对刀,确定工件坐标系。
这种对刀方法对刀精度和效率高,便于工艺文件的编写及生产组织,但投资较大。
2. 对刀数据的输入(1) 根据以上操作得到的对刀数据,即编程坐标系原点在机床坐标系中的X、Y、Z值,要用手动方式输入到G54~G59中存储起来。
操作步骤如下:①按【MENU OFFSET】键。
②按光标移动键到工件坐标系G54~G59。
数控铣床、加工中心常见对刀方法

数控铣床、加工中心常见对刀方法
数控铣床、加工中心在加工过程中,需要进行对刀才能保证加工精度和效率。
下面将
介绍常见的数控铣床、加工中心对刀方法。
一、机械对刀法
机械对刀法是最基本的对刀方法,它利用机床本身的机械结构进行对刀。
操作人员只
需将对刀仪放在加工刀具上,然后通过调整机床的移动量,使对刀仪与机床刀具位置对齐
即可完成对刀。
机械对刀法简单易操作,但精度有限,只适用于一般的加工任务。
二、光电对刀法
光电对刀法具有精度高、快速方便等优点,适用于精密加工任务。
三、感应对刀法
感应对刀法适用于各种类型的加工刀具,但需要注意的是,在进行对刀时,加工刀具
需要具有导电性。
四、摄像对刀法
以上就是常见的数控铣床、加工中心对刀方法,根据不同加工任务和机床的具体情况,可以选择最适合的方法进行对刀,以保证加工精度和效率。
加工中心对刀方法全解!再也不用担心对刀啦

加工中心对刀方法全解!再也不用担心对刀啦1. 加工中心的Z向对刀加工中心的Z向对刀一般有以下三种方法:1) 机上对刀方法一这种对刀方法是通过对刀依次确定每把刀具与工件在机床坐标系中的相互位置关系。
其具体操作步骤如下。
(1) 把刀具长度进行比较,找出最长的刀作为基准刀,进行Z向对刀,并把此时的对刀值(C)作为工件坐标系的Z值,此时H03=0。
(2) 把T01、T02号刀具依次装在主轴,通过对刀确定A、B的值作为长度补偿值。
(此方法没有直接去测量刀具补偿,而是通过依次对刀确定的与方法三不同.)(3)把确定的长度补偿值(最长刀长度减其余刀具长度)填入设定页面,正、负号由程序中的G43、G44来确定,此时一般用G44H—表示。
当采用G43时,长度补偿为负值。
这种对刀方法的对刀效率和精度较高,投资少,但工艺文件编写不便,对生产组织有一定影响。
2) 机上对刀方法二这种对刀方法的具体操作步骤如下:(1) XY方向找正设定如前,将G54中的XY项输入偏置值,Z项置零。
(2) 将用于加工的T1换上主轴,用块规找正Z向,松紧合适后读取机床坐标系Z项值Z1,扣除块规高度后,填入长度补偿值H1中。
(3) 将T2装上主轴,用块规找正,读取Z2,扣除块规高度后填入H2中。
(4) 依次类推,将所有刀具Ti用块规找正,将Zi扣除块规高度后填入Hi中3) 机外刀具预调+机上对刀这种对刀方法是先在机床外利用刀具预调仪精确测量每把刀具的轴向和径向尺寸,确定每把刀具的长度补偿值,然后在机床上用最长的一把刀具进行Z向对刀,确定工件坐标系。
这种对刀方法对刀精度和效率高,便于工艺文件的编写及生产组织,但投资较大。
2. 对刀数据的输入(1) 根据以上操作得到的对刀数据,即编程坐标系原点在机床坐标系中的X、Y、Z值,要用手动方式输入到G54~G59中存储起来。
操作步骤如下:①按【MENU OFFSET】键。
②按光标移动键到工件坐标系G54~G59。
- 1、下载文档前请自行甄别文档内容的完整性,平台不提供额外的编辑、内容补充、找答案等附加服务。
- 2、"仅部分预览"的文档,不可在线预览部分如存在完整性等问题,可反馈申请退款(可完整预览的文档不适用该条件!)。
- 3、如文档侵犯您的权益,请联系客服反馈,我们会尽快为您处理(人工客服工作时间:9:00-18:30)。
加工中心两种对刀方式
刀补计算:刀补值+ 绝对零点= 加工时刀尖的坐标
刀补:刀尖到工作面的距离,若为正,则加工时Z轴上抬,为负则向下。
第一种:测量实际刀长
刀具补正:用卡尺测量刀尖到主轴端面的尺寸作为刀长补正值,此值为正值。
工件坐标:用任意一把刀的刀尖碰工件表面,记下此时的Z轴机械坐标C,此值为负值。
用此值减去该刀具的刀长值L。
负值减去正值相当与绝对值相加,结果为负值。
用
此值作为工件Z轴坐标原点。
验证:G91 G28 Z0.0;Z轴回原点
G90 G59 X0 Y0;XY轴回到工作原点。
G43 H01 Z0.0;刀尖(Z轴)走到工件原点。
G43 执行时将工件坐标原点加上刀补,绝对值相减,结果为负,行程向下,将
此点作为工具(刀尖)坐标原点,即工件表面。
应用于森精机对刀方式:
森精机对刀方式(补正方式1),使用对刀器,刀长的算法
刀长= 主轴端面到工作台距离(回零点时)—对刀时Z轴位置(向下行程)—对刀器高度(1)刀长测量是自动进行的,直接用对刀程序对刀就行。
(2)工件坐标测量。
选中坐标系(如G54)光标指向Z轴值——定中心——参考面——出现“选择参考面”窗口——输入“5”指定Z轴正面——按箭头向下进入“长度补偿号”输入此次碰工件表面的刀具号,则计算Z轴坐标时将此刀长计算进去(正确),否则不计算(错)——测量——写就将工件坐标计算并写入。
然后取消、返回。
优:刀补值即刀长,直观,不易错。
劣:若忘记写刀补,G90Z0; 则刀具插入工件。
第二种:
刀具补正:用治具放在工作台上,刀尖碰治具,记下此时的Z轴机械坐标值(负值)作为此刀长补正。
同时将相对坐标清零,用作计数。
工件坐标:用该刀尖碰工件表面,记下此时相对坐标值,作为工件坐标原点。
此值可正可负。
若工件高,则为正值,若治具高则为负值。
验证:G91 G28 Z0.0;Z轴回原点
G90 G59 X0 Y0;XY轴回到工作原点。
G43 H01 Z0.0;刀尖(Z轴)走到工件原点。
G43 执行时将工件坐标原点加上刀补,结果为负,行程向下,将此点作为工具
(刀尖)坐标原点,即工件表面。
应用丽伟对刀方式。
(1)刀具测量,不用治具,直接在工件表面测量。
将对刀时Z的机床坐标当成刀补。
(2)工件坐标原点就是机床零点。
这是特殊情况,相当于治具与工件的高度差为零,因为工件与治具是同一个。
劣:刀补值是刀尖碰到对刀治具表面时Z轴的高度,是负值,不直观。
优:若忘记写刀补,G90Z0; Z轴向上抬,不扎刀。
此页1 共1 页。