再订货点订货周期T订货数量
订货点技术
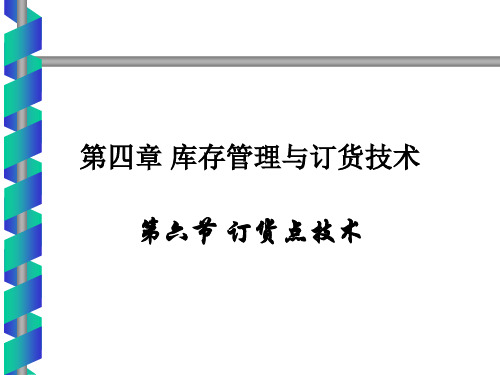
例:某商品在过去三个月中的实际需求 量分别为:一月份126箱,二月份110箱, 三月份127箱。最大订货提前期为2个月, 缺货概率根据经验统计为5%,求该商品 的订货点。
解:平均月需求量=(126+110+127)/3=121箱 缺货概率为5%,查表得:安全系数=1.65
2
需求变动值did
n1
安全系数值 0.54 0.60 0.68 0.84 1.00 1.04 1.10
缺货概率(%) 11.5 10.0 8.1 6.7 5.5 5.0 4.0
安全系数值 1.20 1.28 1.40 1.50 1.60 1.65 1.75
缺货概率(%) 3.6
2.9
2.3
2.0
1.4 1.0 0.5
安全系数值 1.80 1.90 2.00 2.05 2.20 2.33 2.58
订货提前期 值需 (求 样量 本变 标动 准差)
单位时间 需 平求 均量 订方 货 订 差 提 货前 提期 前 单 间 d i d 需求 订量 货方 提 L i 差 前 L期方差
n 1
n 1
安全系数表
缺货概率(%) 30.0 27.4 25.0 20.0 16.0 15.0 13.6
U为订货提前期需求量 ,R为订货点量
R U SS
U d L
SS zσ U
L (7 12 25 16 14 15)/6 14.83
D(L) { 7 -14.83
2
12
-14.83
2
....
15 -14.83
2
}/
6
- 1
34
.97
D (d ) 40 d 40
解:根据 S=R(T+Tk)+ss =120(18+3)+360 =2880(箱)
关于订货策略及各种批量数量问题
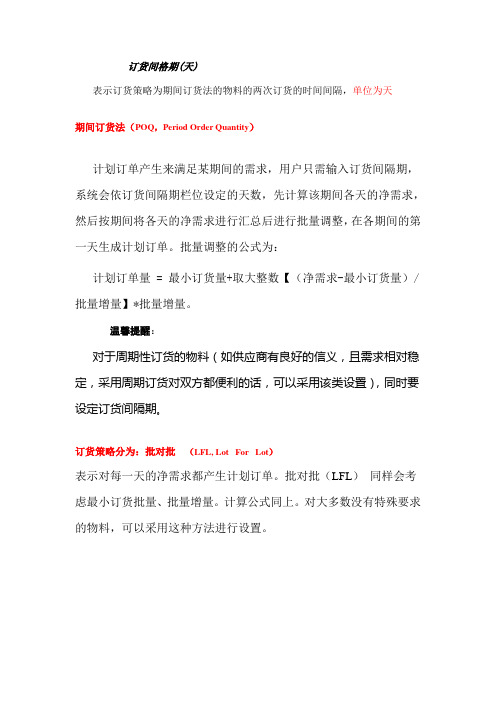
订货间格期(天)表示订货策略为期间订货法的物料的两次订货的时间间隔,单位为天期间订货法(POQ,Period Order Quantity)计划订单产生来满足某期间的需求,用户只需输入订货间隔期,系统会依订货间隔期栏位设定的天数,先计算该期间各天的净需求,然后按期间将各天的净需求进行汇总后进行批量调整,在各期间的第一天生成计划订单。
批量调整的公式为:计划订单量 = 最小订货量+取大整数【(净需求-最小订货量)/批量增量】*批量增量。
温馨提醒:对于周期性订货的物料(如供应商有良好的信义,且需求相对稳定,采用周期订货对双方都便利的话,可以采用该类设置),同时要设定订货间隔期。
订货策略分为:批对批(LFL, Lot For Lot)表示对每一天的净需求都产生计划订单。
批对批(LFL)同样会考虑最小订货批量、批量增量。
计算公式同上。
对大多数没有特殊要求的物料,可以采用这种方法进行设置。
固定批量(FOQ, Fixed Order Quantity)计划订单数量是以净需求为基础,订单数量必须为固定/经济批量所定数量的整数倍。
此时系统将设定:最小订货批量=批量增量=固定批量,调整公式同上。
温馨提醒:如果每次订货的数量都是固定的,可以采用该类设置。
同时要设置固定批量。
在订货点(ROP, ReOrder Point )当库存降低到再订货点以下时,系统将产生需求,计划订单量为固定/经济批量指定的数量。
如果库存大于再订货点,则用(库存—再订货点)/ 日消耗量的最小整数算出库存还可维持的天数,在该日期后再产生计划订单。
温馨提醒:对于不太重要的物料,因其金额低,可以设置成这种订货方式。
其前提是需求固定。
同时要设置再订货点。
最小、最大订货批量及批量增量、固定/经济批量最小订货批量是指每次订货量不能低于此值;最大订货批量是指每次订货量不能大于此值(最大订货量在计算过程中未做限制,只会在计算日志里进行提示);批量增量是指物料的最小包装单位或最少生产数量;固定/经济批量是指每次订货最佳的批量。
原材料的五种订货方法
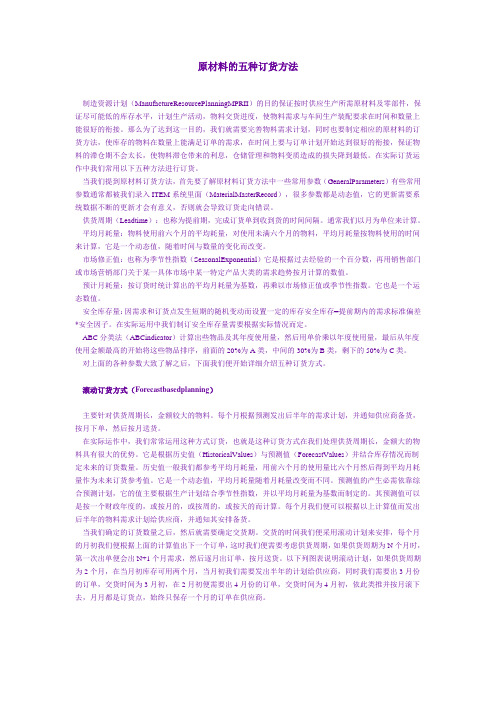
原材料的五种订货方法制造资源计划(ManufactureResourcePlanningMPRII)的目的保证按时供应生产所需原材料及零部件,保证尽可能低的库存水平,计划生产活动,物料交货进度,使物料需求与车间生产装配要求在时间和数量上能很好的衔接。
那么为了达到这一目的,我们就需要完善物料需求计划,同时也要制定相应的原材料的订货方法,使库存的物料在数量上能满足订单的需求,在时间上要与订单计划开始达到很好的衔接,保证物料的滞仓期不会太长,使物料滞仓带来的利息,仓储管理和物料变质造成的损失降到最低。
在实际订货运作中我们常用以下五种方法进行订货。
当我们提到原材料订货方法,首先要了解原材料订货方法中一些常用参数(GeneralParameters)有些常用参数通常都被我们录入ITEM系统里面(MaterialMasterRecord),很多参数都是动态值,它的更新需要系统数据不断的更新才会有意义,否则就会导致订货走向错误。
供货周期(Leadtime):也称为提前期,完成订货单到收到货的时间间隔。
通常我们以月为单位来计算。
平均月耗量:物料使用前六个月的平均耗量,对使用未满六个月的物料,平均月耗量按物料使用的时间来计算,它是一个动态值,随着时间与数量的变化而改变。
市场修正值:也称为季节性指数(SeasonalExponential)它是根据过去经验的一个百分数,再用销售部门或市场营销部门关于某一具体市场中某一特定产品大类的需求趋势按月计算的数值。
预计月耗量:按订货时统计算出的平均月耗量为基数,再乘以市场修正值或季节性指数。
它也是一个运态数值。
安全库存量:因需求和订货点发生短期的随机变动而设置一定的库存安全库存=提前期内的需求标准偏差*安全因子。
在实际运用中我们制订安全库存量需要根据实际情况而定。
ABC分类法(ABCindicator)计算出些物品及其年度使用量,然后用单价乘以年度使用量,最后从年度使用金额最高的开始将这些物品排序,前面的20%为A类,中间的30%为B类,剩下的50%为C类。
订货批量和订货策略
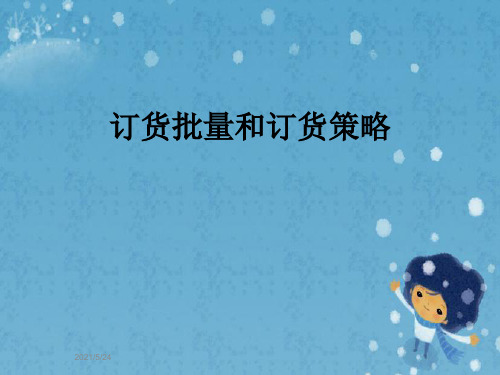
二)控制系统
• 一个库存控制系统有以下要素构成: 1. 需求特性:从可预知性分为确定性需求、随机性
需求、不确定性需求。 2. 供应特性:包括:备货周期或订货周期、订货点、
采购价格和价格折扣影响采购量、订货间隔期 3. 进货方式:定量订货、定期订货、按需求计划组
织订货
• 任何库存控制系统都必须回答:何时发出订货? 订多少?——订货策略
期内总费用(C)=采购成本+订货成本+持时到货保管费
持时到货保管费:
Q 2
( 1-
R p
)c1
C
K
R
R c0 Q
Q 2
(1
R P
)c1
订货周期: T*=Q0/R
(EQCO) Q R
cc021RQ(Pc2 0cR2P1 )(1
R P
)
T0 *
=
2c0
c1(1
-
R p
)R
说明:
持时和瞬时进货区别:持时导致保管费用减少、 导致Q0增大、订货周期增长
按EOQ计算出的不是一个整数单位,2.7车? 不方便分票,22.7kg钢钉,而标准包装整箱重50公斤 运输车辆载重固定,12吨装的车,但EOQ=13吨?
• 如果在EOQ附近出现一点小小的偏离的话,成本与订单 批量的变化敏感度到底多大?会不会引起成本的大幅上 升?还是可忽略不计?
EOQ对成本的影响
2
1000
显然,总费用最低的订货批量为1000件,此时的总费用为17440元
四)允许缺货的订货量
库存 S
-D
0
t
td
允许缺货的库存量变化状态
时间 2t
单位时间总库存费用(库存费+缺货费+订货费)
存货扩展模型:订货提前期与再订货点

订货提前期
即发出订货申请到存货到货的时间。也就 是说,如果到存货耗用完再发出订货申请, 存货就不能按时到货。
因此,当一项存货因耗用或消耗而减少到 某个数量时,存货相关部门就应向有关部 门提出采购申请,以便存货耗用完时有新 的存货使用。
存货申请订购时的这个数量称为再订货点。
(1)安全存量为0时,再订货点为1000 期望缺货量 =(1500-1000)×0.2+(2000-1000)
×0.05=150 缺货成本=2×150×(360/30)
=3600 储存成本=0×5×10%=0 总成本=3600+0=3600
(2)安全存量为500时,再订货点为 1500
例:若该企业订货提前期为10天,原材 料每日消耗量为10吨,预计每日存货最 大需求量为20吨。则再订货点 为:10×10+(20-10)×10=200吨
当有安全存量时,意味着允许缺货,因 此缺货成本为决策相关成本。因此,安 全存量的决策相关成本为
总成本=缺货成本+安全存量的储存成本
其中,
(年)缺货成本=单位缺货成本×一次订 货缺货量×年订货次数
2.经济订购量的扩展模型——(3)订货提前期
例:若企业订货提前期为10天,原 材料每日消耗量为10吨。 再订货点为: 10×10=100(吨)
存货管理-扩展经济进货批量模型
保险储备
2.经济订购量的扩展模型——(4)保险储备
保险储备:提前订货的情况下,为了防止缺货,
企业往往多储备一些存货以备不时之需,多储
总成本=500
若安全存量为1000个,其总成本 为500,最少,所以选择安全存量 1000的方案。
订货提前期
运筹学11-存储论
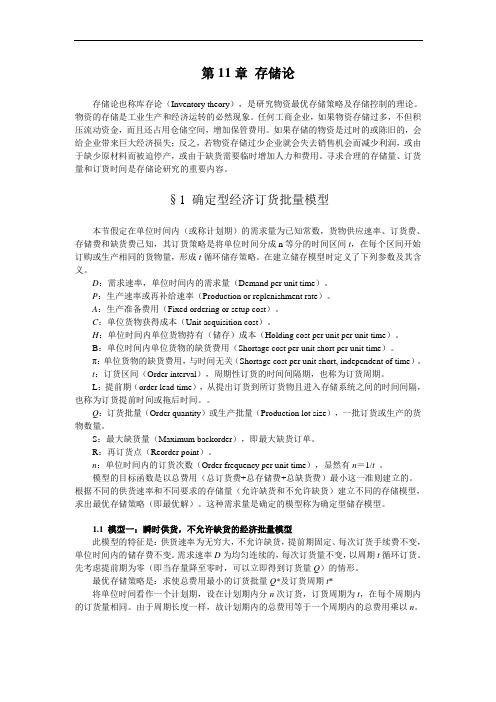
第11章存储论存储论也称库存论(Inventory theory),是研究物资最优存储策略及存储控制的理论。
物资的存储是工业生产和经济运转的必然现象。
任何工商企业,如果物资存储过多,不但积压流动资金,而且还占用仓储空间,增加保管费用。
如果存储的物资是过时的或陈旧的,会给企业带来巨大经济损失;反之,若物资存储过少企业就会失去销售机会而减少利润,或由于缺少原材料而被迫停产,或由于缺货需要临时增加人力和费用。
寻求合理的存储量、订货量和订货时间是存储论研究的重要内容。
§1 确定型经济订货批量模型本节假定在单位时间内(或称计划期)的需求量为已知常数,货物供应速率、订货费、存储费和缺货费已知,其订货策略是将单位时间分成n等分的时间区间t,在每个区间开始订购或生产相同的货物量,形成t循环储存策略。
在建立储存模型时定义了下列参数及其含义。
D:需求速率,单位时间内的需求量(Demand per unit time)。
P:生产速率或再补给速率(Production or replenishment rate)。
A:生产准备费用(Fixed ordering or setup cost)。
C:单位货物获得成本(Unit acquisition cost)。
H:单位时间内单位货物持有(储存)成本(Holding cost per unit per unit time)。
B:单位时间内单位货物的缺货费用(Shortage cost per unit short per unit time)。
π:单位货物的缺货费用,与时间无关(Shortage cost per unit short, independent of time)。
t:订货区间(Order interval),周期性订货的时间间隔期,也称为订货周期。
L:提前期(order lead time),从提出订货到所订货物且进入存储系统之间的时间间隔,也称为订货提前时间或拖后时间。
库存管理名词解释。
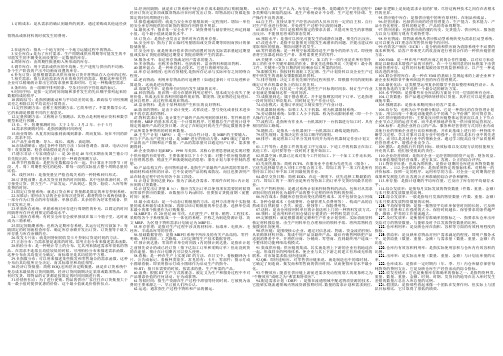
1.订购成本:是从需求的确认到最终的到货,通过采购或其他途径获得物品或原材料的时候发生的费用。
2.在途库存:指从一个地方到另一个地方运输过程中的物品。
3.安全库存;s是为了应付需求、生产周期或供应周期等可能发生的不可能发生的不测变化而设置的一定数量的库存。
4.周转库存:由周期性批量购入所形成的库存。
5.调节库存:用于需求或供应的不均衡、生产速度与供应的不均衡、各个生产阶段的产出不均衡而设置的库存。
6.补充订货:是指根据需求从供应商处订货并将物品存入仓库的过程。
7.相关需求:指与其他需求有内在的相关性的需求,根据这种相关性企业可以精确的计算出它的需求量和需求时间,它是一种精确型需求。
8.条形码:由一组顺序排列的条、空及对应的字符组成的标记。
9.时间序列:是按一定的时间间隔和事件发生的先后顺序排列起来的数据构成的排序。
10跟踪信号:是指预测滚动和与平均误差的比值,跟踪信号可用预测误差之和除以其平均误差计算得出。
11.定性预测方法:也称主观预测方法,它简单明了,不需要数学公式,它的来源是根据不同的主观意见。
12.定量预测方法:又称统计与预测法,其特点是利用统计资料和数学模型来进行预测。
13.长、中、短期预测时间:大于2年、3月-2年、小于3月14.需求预测的时间:是指预测的时间跨度15.商业周期:从复苏到高涨到衰竭到萧条,周而复始。
处在不同的阶段,需求不同。
15.产品生命周期:导入、成长、成熟、衰退期。
16.市场调研法:通过各种不同的方法(如问卷调查、面谈、电话访问等)收集数据,检查市场假设是否正确。
17.德尔非法(专家调查法):是20世纪40年代末期由美国兰德公司首先提出的,很快在世界上盛行的一种调查预测方法。
18.季节性指数法:是把历史数据综合在一起,并计算出不同季节(时段、月、周)周期性变化的趋势,即每一段的实际值占整个周期总量的比值。
19。
线性回归:是指变量呈严格直线关系的一种特殊回归形式。
20.订货提前期:是从发货至到货的时间间隔,其中包括准备时间、供方接受订货、供方生产、产品发运、产品到达、提货、验收、入库等所花费的时间。
再订货点与安全库存
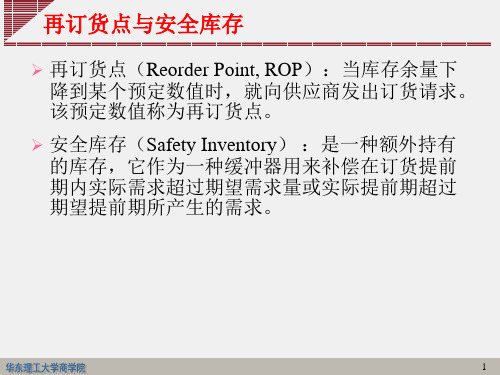
首先计算订货提前期内的标准差 σDLT=LT σ = 3 ×30=1.732×30=51.96
查正态分布表得 z(0.95)=1.64
因此安全库存SI=1.64×51.96≈ 85件
再订货点ROP=200×3+85=685件 订货批量可由一般经济订货批量模型确定。
10
降低安全库存的方法
缩短供应提前期 如果提前期缩短到原来的k倍,安全库存则降低为原 来的 k 倍。
=112 .7 SI=1.64×112.69≈185件 ROP=200×3+185=785件
13
多级库存管理
• 多级库存管理:管理整个渠道的库存而不只是 各自独立的存储点的库存。 • 基本逻辑:渠道中的每一级都按自己的库存水平 加上来自所有下游的库存来进行库存计划。也即, 每一级库存水平 的计划都不是仅仅考虑自己下 一级的需求信息,而是考虑最终客户的需求信息。
Q1 AIL1= + z× σ1 2
LTR
0.25= 61.38
= 311.8/2 +1.28×16.8 0.25= 166.65
17
零售商1
订货量,Q 再订货点,ROP 平均库存,AIL 订货周期(月) 312 61 167 1.54
零售商2
220 35 120 2.19
零售商3
381 87 202 1.26
1
需求与提前期都是常数时的再订货点
在库存持有量能够满足等待订货期间(即提 前期)的需求时下订单。
若需求与提前期都是常数,再订货点为:
ROP = d LT 其中: d —— 需求率; LT —— 提前期
Q*=93 ROP=?
2
需求与提前期变化时的再订货点
- 1、下载文档前请自行甄别文档内容的完整性,平台不提供额外的编辑、内容补充、找答案等附加服务。
- 2、"仅部分预览"的文档,不可在线预览部分如存在完整性等问题,可反馈申请退款(可完整预览的文档不适用该条件!)。
- 3、如文档侵犯您的权益,请联系客服反馈,我们会尽快为您处理(人工客服工作时间:9:00-18:30)。
1、出现背景
库存管理人员通过排查物料的库存情况,如发现
某一种物料没有了,就填写缺料表,以通知采购部
门采购。缺料表反映的是当时库存中没有的原材料。
思考:这会出现什么问题?
2、基本工作原理
库存控制订货点理论是一种库存补充方法,目
的是保证仓库中的某一物料始终都有一定的存量, 以便需要时随时使用。其基本工作原理是当满足订 货条件时,即再订货点时,就要立即进行订货来补 充。
安全库存
时间 T 订货间隔 订货提前期 T 订货间隔 T 订货间隔
定量订货方式示意图
4、两种具体方法
(1)定量订货法
订货控制特点:基于数量的订货控制法,订
货周期是变化的,每次订货数量保持不变。
订货控制参数:再订货点(库存数量水平)、
订货数量(经济订货批量)
适用物料:A类物料
4、两种具体方法
Q*
不可行
2 存货总需要量 每次订货成本 2 400018 Q* = 970个 单位存货存储成本 0.153
可行
第二步:计算最小经济订货批量的总费用,并与取得最低价格 折扣的最小数量的总费用比较。
TC 970 保管成本+订货费用+ 货款
970 4000 = 0.153 18 0.85 4000 3458 元 2 970
定期订货方式示意图
4、两种具体方法
(2)定期订货法
订货控制特点:基于时间的订货控制法,订
货周期不变,每次订货数量变化。
订货控制参数:再订货点(订货周期T)、
订货数量(不固定)
适用物料:C类物料
思考:什么是经济订货批量(EOQ)?
如何计算?
Q*: 经济订货批量 D: 年总需求量 S: 单位订货费用 H: 单位物料单位时间(通常为年)保管费
(2)定期订货法 基本原理:是一种基于时间的订货控制方法,即 按照预先设定的时间间隔,周期性地检查库存物 料数量,然后发出订货通知,将库存补充到目标
水平。
库存数量
再订货点:订货周期T
本次订货量 消耗减慢
最大库存
一般消耗
消耗加快
安全库存
时间 T 订货间隔 订货提前期 T 订货间隔 T 订货间隔
4、两种具体方法
(1)定量订货法 Βιβλιοθήκη 本原理:是一种基于物料数量的订货控制
方法,通过不断地监控库存物料数量,当库
存物料数量降低到预先设定的某一基准(再 订货点)时,发出订货通知并按固定订货批 量补充库存。
库存数量
再订货点:库存数量水平
最大库存 本次订货量 消耗减慢 消耗加快
一般消耗 再订货点
TC 1000 保管成本+订货费用+ 货款
1000 4000 = 0.1476 18 0.82 4000 3426 元 2 1000
思考:
如何确定定量订货法的再订货点(库存数
量水平)?
再订货点=平均订货提前期需求量+ 安全库存量
思考:
如何确定定期订货法中的再订货点(订货
5)条件之五:根据物料的库存消耗情况来确定订货 数量及订货时间。
周期T)?
T*: 经济订货周期 D: 年总需求量 S: 单位订货费用 H: 单位物料单位时间(通常为年)保管费
5、库存控制订货点理论使用假设条件(局限性)
1)条件之一:物料资源是无限的,即不管在什么时 间、什么地点企业都能买到生产需要的物料。 2)条件之二:物料需求是相对均匀、连续、稳定的。 3)条件之三:未来时间段内的物料需求是通过预测 得到的。 4)条件之四:各种物料的需求是相互独立的。
例:某电商公司每年需要4000个纸箱。纸箱的价格为: 购买数量为1~499个时,每个纸箱0.9元;购买数量为 500~999个时,每个纸箱0 .85元;购买1000个以上时, 每个纸箱0.82元。每次订货费用为18元,库存保管费率 为18%,求经济订购批量和年总费用。
订货数量(个) 单价(元) 单位产品库存保管费用
库存量
最大库存量
再订货点
·
订货提前期 时 间
安全库存量
什么时 候买? 买多少 ?
一个物料一张图进行计划
3、三个相关概念
(1)再订货点。再订货点是指发生下一次订货行 为时所出现的状态。 (2)订货提前期。订货提前期即为从订货开始直 至物料到达仓库的这一时间段。 (3)安全库存。安全库存是指除了保证在正常状 态下的库存计划量外,为了防止由不确定因素引起的 缺货而备用的缓冲库存。
1~499
500~999 1000个以上
0.9
0.85 0.82
0.18×0.9=0.612
0.18×0.85=0.153 0.18×0.82=0.1476
第一步:对每一个报价,从低到高分别用EOQ公式计算可行解。
2 存货总需要量 每次订货成本 2 400018 = 988个 单位存货存储成本 0.1476