中北大学毕业设计英文文献及中文翻译
中北大学毕业设计外文翻译
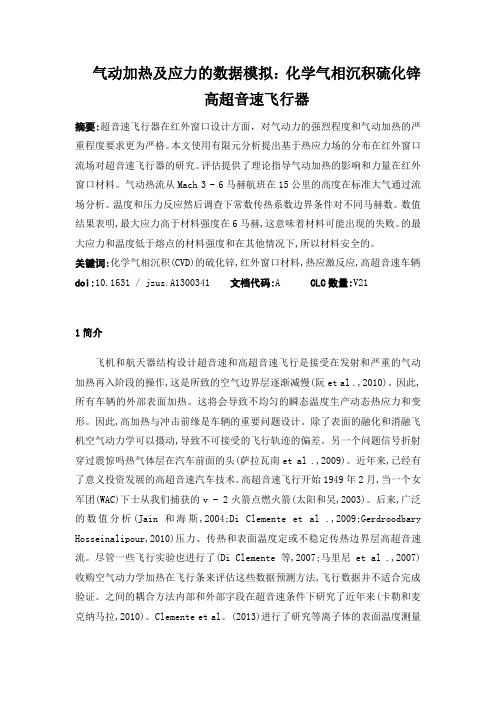
气动加热及应力的数据模拟:化学气相沉积硫化锌高超音速飞行器摘要:超音速飞行器在红外窗口设计方面,对气动力的强烈程度和气动加热的严重程度要求更为严格。
本文使用有限元分析提出基于热应力场的分布在红外窗口流场对超音速飞行器的研究。
评估提供了理论指导气动加热的影响和力量在红外窗口材料。
气动热流从Mach 3 - 6马赫航班在15公里的高度在标准大气通过流场分析。
温度和压力反应然后调查下常数传热系数边界条件对不同马赫数。
数值结果表明,最大应力高于材料强度在6马赫,这意味着材料可能出现的失败。
的最大应力和温度低于熔点的材料强度和在其他情况下,所以材料安全的。
关键词:化学气相沉积(CVD)的硫化锌,红外窗口材料,热应激反应,高超音速车辆doi:10.1631 / jzus.A1300341 文档代码:A CLC数量:V211简介飞机和航天器结构设计超音速和高超音速飞行是接受在发射和严重的气动加热再入阶段的操作,这是所致的空气边界层逐渐减慢(阮et al .,2010)。
因此,所有车辆的外部表面加热。
这将会导致不均匀的瞬态温度生产动态热应力和变形。
因此,高加热与冲击前缘是车辆的重要问题设计。
除了表面的融化和消融飞机空气动力学可以摄动,导致不可接受的飞行轨迹的偏差。
另一个问题信号折射穿过震惊吗热气体层在汽车前面的头(萨拉瓦南et al .,2009)。
近年来,已经有了意义投资发展的高超音速汽车技术。
高超音速飞行开始1949年2月,当一个女军团(WAC)下士从我们捕获的v - 2火箭点燃火箭(太阳和吴,2003)。
后来,广泛的数值分析(Jain和海斯,2004;Di Clemente et al .,2009;Gerdroodbary Hosseinalipour,2010)压力、传热和表面温度定或不稳定传热边界层高超音速流。
尽管一些飞行实验也进行了(Di Clemente等,2007;马里尼et al .,2007)收购空气动力学加热在飞行条来评估这些数据预测方法,飞行数据并不适合完成验证。
毕业设计外文翻译英文加中文
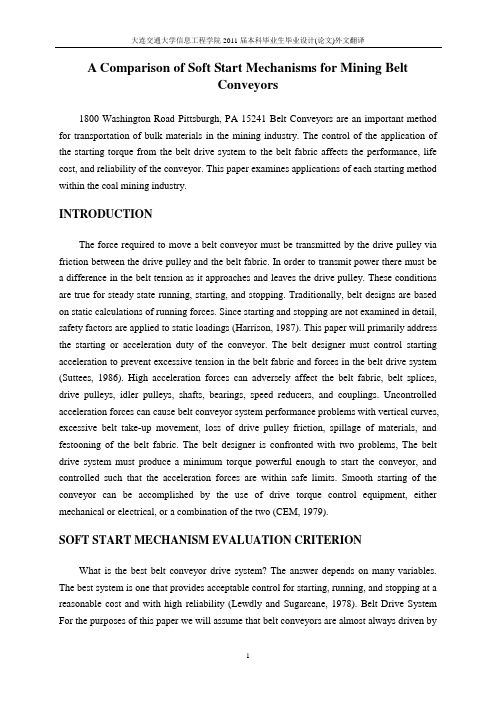
A Comparison of Soft Start Mechanisms for Mining BeltConveyors1800 Washington Road Pittsburgh, PA 15241 Belt Conveyors are an important method for transportation of bulk materials in the mining industry. The control of the application of the starting torque from the belt drive system to the belt fabric affects the performance, life cost, and reliability of the conveyor. This paper examines applications of each starting method within the coal mining industry.INTRODUCTIONThe force required to move a belt conveyor must be transmitted by the drive pulley via friction between the drive pulley and the belt fabric. In order to transmit power there must be a difference in the belt tension as it approaches and leaves the drive pulley. These conditions are true for steady state running, starting, and stopping. Traditionally, belt designs are based on static calculations of running forces. Since starting and stopping are not examined in detail, safety factors are applied to static loadings (Harrison, 1987). This paper will primarily address the starting or acceleration duty of the conveyor. The belt designer must control starting acceleration to prevent excessive tension in the belt fabric and forces in the belt drive system (Suttees, 1986). High acceleration forces can adversely affect the belt fabric, belt splices, drive pulleys, idler pulleys, shafts, bearings, speed reducers, and couplings. Uncontrolled acceleration forces can cause belt conveyor system performance problems with vertical curves, excessive belt take-up movement, loss of drive pulley friction, spillage of materials, and festooning of the belt fabric. The belt designer is confronted with two problems, The belt drive system must produce a minimum torque powerful enough to start the conveyor, and controlled such that the acceleration forces are within safe limits. Smooth starting of the conveyor can be accomplished by the use of drive torque control equipment, either mechanical or electrical, or a combination of the two (CEM, 1979).SOFT START MECHANISM EVALUATION CRITERIONWhat is the best belt conveyor drive system? The answer depends on many variables. The best system is one that provides acceptable control for starting, running, and stopping at a reasonable cost and with high reliability (Lewdly and Sugarcane, 1978). Belt Drive System For the purposes of this paper we will assume that belt conveyors are almost always driven byelectrical prime movers (Goodyear Tire and Rubber, 1982). The belt "drive system" shall consist of multiple components including the electrical prime mover, the electrical motor starter with control system, the motor coupling, the speed reducer, the low speed coupling, the belt drive pulley, and the pulley brake or hold back (Cur, 1986). It is important that the belt designer examine the applicability of each system component to the particular application. For the purpose of this paper, we will assume that all drive system components are located in the fresh air, non-permissible, areas of the mine, or in non-hazardous, National Electrical Code, Article 500 explosion-proof, areas of the surface of the mine.Belt Drive Component Attributes SizeCertain drive components are available and practical in different size ranges. For this discussion, we will assume that belt drive systems range from fractional horsepower to multiples of thousands of horsepower. Small drive systems are often below 50 horsepower. Medium systems range from 50 to 1000 horsepower. Large systems can be considered above 1000 horsepower. Division of sizes into these groups is entirely arbitrary. Care must be taken to resist the temptation to over motor or under motor a belt flight to enhance standardization. An over motored drive results in poor efficiency and the potential for high torques, while an under motored drive could result in destructive overspending on regeneration, or overheating with shortened motor life (Lords, et al., 1978).Torque ControlBelt designers try to limit the starting torque to no more than 150% of the running torque (CEMA, 1979; Goodyear, 1982). The limit on the applied starting torque is often the limit of rating of the belt carcass, belt splice, pulley lagging, or shaft deflections. On larger belts and belts with optimized sized components, torque limits of 110% through 125% are common (Elberton, 1986). In addition to a torque limit, the belt starter may be required to limit torque increments that would stretch belting and cause traveling waves. An ideal starting control system would apply a pretension torque to the belt at rest up to the point of breakaway, or movement of the entire belt, then a torque equal to the movement requirements of the belt with load plus a constant torque to accelerate the inertia of the system components from rest to final running speed. This would minimize system transient forces and belt stretch (Shultz, 1992). Different drive systems exhibit varying ability to control the application of torques to the belt at rest and at different speeds. Also, the conveyor itself exhibits two extremes of loading. An empty belt normally presents the smallest required torque for breakaway and acceleration, while a fully loaded belt presents the highest required torque. A mining drive system must be capable of scaling the applied torque from a 2/1 ratio for a horizontal simple belt arrangement, to a 10/1 ranges for an inclined or complex belt profile.Thermal RatingDuring starting and running, each drive system may dissipate waste heat. The waste heat may be liberated in the electrical motor, the electrical controls,, the couplings, the speed reducer, or the belt braking system. The thermal load of each start Is dependent on the amount of belt load and the duration of the start. The designer must fulfill the application requirements for repeated starts after running the conveyor at full load. Typical mining belt starting duties vary from 3 to 10 starts per hour equally spaced, or 2 to 4 starts in succession. Repeated starting may require the dreading or over sizing of system components. There is a direct relationship between thermal rating for repeated starts and costs. Variable Speed. Some belt drive systems are suitable for controlling the starting torque and speed, but only run at constant speed. Some belt applications would require a drive system capable of running for extended periods at less than full speed. This is useful when the drive load must be shared with other drives, the belt is used as a process feeder for rate control of the conveyed material, the belt speed is optimized for the haulage rate, the belt is used at slower speeds to transport men or materials, or the belt is run a slow inspection or inching speed for maintenance purposes (Hager, 1991). The variable speed belt drive will require a control system based on some algorithm to regulate operating speed. Regeneration or Overhauling Load. Some belt profiles present the potential for overhauling loads where the belt system supplies energy to the drive system. Not all drive systems have the ability to accept regenerated energy from the load. Some drives can accept energy from the load and return it to the power line for use by other loads. Other drives accept energy from the load and dissipate it into designated dynamic or mechanical braking elements. Some belt profiles switch from motoring to regeneration during operation. Can the drive system accept regenerated energy of a certain magnitude for the application? Does the drive system have to control or modulate the amount of retarding force during overhauling? Does the overhauling occur when running and starting? Maintenance and Supporting Systems. Each drive system will require periodic preventative maintenance. Replaceable items would include motor brushes, bearings, brake pads, dissipation resistors, oils, and cooling water. If the drive system is conservatively engineered and operated, the lower stress on consumables will result in lower maintenance costs. Some drives require supporting systems such as circulating oil for lubrication, cooling air or water, environmental dust filtering, or computer instrumentation. The maintenance of the supporting systems can affect the reliability of the drive system.CostThe drive designer will examine the cost of each drive system. The total cost is the sum of the first capital cost to acquire the drive, the cost to install and commission the drive, thecost to operate the drive, and the cost to maintain the drive. The cost for power to operate the drive may vary widely with different locations. The designer strives to meet all system performance requirements at lowest total cost. Often more than one drive system may satisfy all system performance criterions at competitive costs.ComplexityThe preferred drive arrangement is the simplest, such as a single motor driving through a single head pulley.However,mechanical, economic,and functional requirements often necessitate the use of complex drives.The belt designer must balance the need for sophistication against the problems that accompany complex systems. Complex systems require additional design engineering for successful deployment. An often-overlooked cost in a complex system is the cost of training onsite personnel, or the cost of downtime as a result of insufficient training.SOFT START DRIVE CONTROL LOGICEach drive system will require a control system to regulate the starting mechanism. The most common type of control used on smaller to medium sized drives with simple profiles is termed "Open Loop Acceleration Control". In open loop, the control system is previously configured to sequence the starting mechanism in a prescribed manner, usually based on time. In open loop control, drive-operating parameters such as current, torque, or speed do not influence sequence operation. This method presumes that the control designer has adequately modeled drive system performance on the conveyor. For larger or more complex belts, "Closed Loop" or "Feedback" control may he utilized. In closed loop control, during starting, the control system monitors via sensors drive operating parameters such as current level of the motor, speed of the belt, or force on the belt, and modifies the starting sequence to control, limit, or optimize one or wore parameters. Closed loop control systems modify the starting applied force between an empty and fully loaded conveyor. The constants in the mathematical model related to the measured variable versus the system drive response are termed the tuning constants. These constants must be properly adjusted for successful application to each conveyor. The most common schemes for closed loop control of conveyor starts are tachometer feedback for speed control and load cell force or drive force feedback for torque control. On some complex systems, It is desirable to have the closed loop control system adjust itself for various encountered conveyor conditions. This is termed "Adaptive Control". These extremes can involve vast variations in loadings, temperature of the belting, location of the loading on the profile, or multiple drive options on the conveyor. There are three commonadaptive methods. The first involves decisions made before the start, or 'Restart Conditioning'. If the control system could know that the belt is empty, it would reduce initial force and lengthen the application of acceleration force to full speed. If the belt is loaded, the control system would apply pretension forces under stall for less time and supply sufficient torque to adequately accelerate the belt in a timely manner. Since the belt only became loaded during previous running by loading the drive, the average drive current can be sampled when running and retained in a first-in-first-out buffer memory that reflects the belt conveyance time. Then at shutdown the FIFO average may be use4 to precondition some open loop and closed loop set points for the next start. The second method involves decisions that are based on drive observations that occur during initial starting or "Motion Proving'. This usually involves a comparison In time of the drive current or force versus the belt speed. if the drive current or force required early in the sequence is low and motion is initiated, the belt must be unloaded. If the drive current or force required is high and motion is slow in starting, the conveyor must be loaded. This decision can be divided in zones and used to modify the middle and finish of the start sequence control. The third method involves a comparison of the belt speed versus time for this start against historical limits of belt acceleration, or 'Acceleration Envelope Monitoring'. At start, the belt speed is measured versus time. This is compared with two limiting belt speed curves that are retained in control system memory. The first curve profiles the empty belt when accelerated, and the second one the fully loaded belt. Thus, if the current speed versus time is lower than the loaded profile, it may indicate that the belt is overloaded, impeded, or drive malfunction. If the current speed versus time is higher than the empty profile, it may indicate a broken belt, coupling, or drive malfunction. In either case, the current start is aborted and an alarm issued.CONCLUSIONThe best belt starting system is one that provides acceptable performance under all belt load Conditions at a reasonable cost with high reliability. No one starting system meets all needs. The belt designer must define the starting system attributes that are required for each belt. In general, the AC induction motor with full voltage starting is confined to small belts with simple profiles. The AC induction motor with reduced voltage SCR starting is the base case mining starter for underground belts from small to medium sizes. With recent improvements, the AC motor with fixed fill fluid couplings is the base case for medium to large conveyors with simple profiles. The Wound Rotor Induction Motor drive is the traditional choice for medium to large belts with repeated starting duty or complex profilesthat require precise torque control. The DC motor drive, Variable Fill Hydrokinetic drive, and the Variable Mechanical Transmission drive compete for application on belts with extreme profiles or variable speed at running requirements. The choice is dependent on location environment, competitive price, operating energy losses, speed response, and user familiarity. AC Variable Frequency drive and Brush less DC applications are limited to small to medium sized belts that require precise speed control due to higher present costs and complexity. However, with continuing competitive and technical improvements, the use of synthesized waveform electronic drives will expand.REFERENCES[1]Michael L. Nave, P.E.1989.CONSOL Inc.煤矿业带式输送机几种软起动方式的比较1800 年华盛顿路匹兹堡, PA 15241带式运送机是采矿工业运输大批原料的重要方法。
毕业设计外文参考资料及译文

Fundamental information, including the effects of porosity, water-to-cement ratio, cement paste characteristic, volume fraction of coarse aggregates, size of coarse aggregates on pervious concrete strength, had been studied [3, 9−12]. However, for the reason that the porosity played a key role in the functional and structural performances of pervious concretes [13 − 14], there was still a need to understand more about the mechanical responses of pervious concretes proportioned for desired levels of porosities. Although it was possible to have widely different pore structure features for a given porosity, or similar pore structure features for varied porosities in pervious concrete, it was imperative to focus on the mechanical responses of pervious concrete at different designed porosities. However, compared with the related research on conventional concrete, very limited study had been conducted on the fracture and fatigue behaviors of pervious concrete, which were especially important for pavement concrete subjected to heavy traffic and to severe seasonal temperature change. The presented work outlined the raw materials and mixing proportions to produce high-strength supplementary cementitious material (SCM) modified pervious concrete (SPC) and polymer-intensified pervious concrete (PPC) at different porosities within the range of 15%−25%. Then, the mechanical properties of pervious concrete, including the compressive and flexural strengths, fracture energy, as well as fatigue property, were investigated in details.
毕设外文文献+翻译1
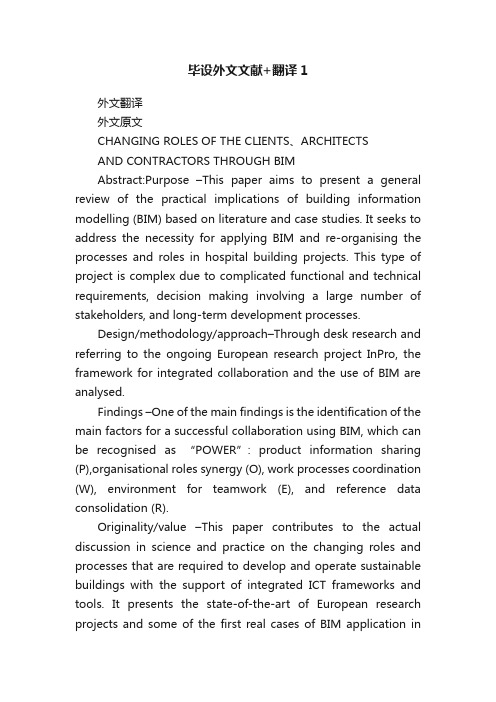
毕设外文文献+翻译1外文翻译外文原文CHANGING ROLES OF THE CLIENTS、ARCHITECTSAND CONTRACTORS THROUGH BIMAbstract:Purpose –This paper aims to present a general review of the practical implications of building information modelling (BIM) based on literature and case studies. It seeks to address the necessity for applying BIM and re-organising the processes and roles in hospital building projects. This type of project is complex due to complicated functional and technical requirements, decision making involving a large number of stakeholders, and long-term development processes.Design/methodology/approach–Through desk research and referring to the ongoing European research project InPro, the framework for integrated collaboration and the use of BIM are analysed.Findings –One of the main findings is the identification of the main factors for a successful collaboration using BIM, which can be recognised as “POWER”: product information sharing (P),organisational roles synergy (O), work processes coordination (W), environment for teamwork (E), and reference data consolidation (R).Originality/value –This paper contributes to the actual discussion in science and practice on the changing roles and processes that are required to develop and operate sustainable buildings with the support of integrated ICT frameworks and tools. It presents the state-of-the-art of European research projects and some of the first real cases of BIM application inhospital building projects.Keywords:Europe, Hospitals, The Netherlands, Construction works, Response flexibility, Project planningPaper type :General review1. IntroductionHospital building projects, are of key importance, and involve significant investment, and usually take a long-term development period. Hospital building projects are also very complex due to the complicated requirements regarding hygiene, safety, special equipments, and handling of a large amount of data. The building process is very dynamic and comprises iterative phases and intermediate changes. Many actors with shifting agendas, roles and responsibilities are actively involved, such as: the healthcare institutions, national and local governments, project developers, financial institutions, architects, contractors, advisors, facility managers, and equipment manufacturers and suppliers. Such building projects are very much influenced, by the healthcare policy, which changes rapidly in response to the medical, societal and technological developments, and varies greatly between countries (World Health Organization, 2000). In The Netherlands, for example, the way a building project in the healthcare sector is organised is undergoing a major reform due to a fundamental change in the Dutch health policy that was introduced in 2008.The rapidly changing context posts a need for a building with flexibility over its lifecycle. In order to incorporate life-cycle considerations in the building design, construction technique, and facility management strategy, a multidisciplinary collaboration is required. Despite the attempt for establishing integrated collaboration, healthcare building projects still facesserious problems in practice, such as: budget overrun, delay, and sub-optimal quality in terms of flexibility, end-user?s dissatisfaction, and energy inefficiency. It is evident that the lack of communication and coordination between the actors involved in the different phases of a building project is among the most important reasons behind these problems. The communication between different stakeholders becomes critical, as each stakeholder possesses different setof skills. As a result, the processes for extraction, interpretation, and communication of complex design information from drawings and documents are often time-consuming and difficult. Advanced visualisation technologies, like 4D planning have tremendous potential to increase the communication efficiency and interpretation ability of the project team members. However, their use as an effective communication tool is still limited and not fully explored. There are also other barriers in the information transfer and integration, for instance: many existing ICT systems do not support the openness of the data and structure that is prerequisite for an effective collaboration between different building actors or disciplines.Building information modelling (BIM) offers an integrated solution to the previously mentioned problems. Therefore, BIM is increasingly used as an ICT support in complex building projects. An effective multidisciplinary collaboration supported by an optimal use of BIM require changing roles of the clients, architects, and contractors; new contractual relationships; and re-organised collaborative processes. Unfortunately, there are still gaps in the practical knowledge on how to manage the building actors to collaborate effectively in their changing roles, and todevelop and utilise BIM as an optimal ICT support of the collaboration.This paper presents a general review of the practical implications of building information modelling (BIM) based on literature review and case studies. In the next sections, based on literature and recent findings from European research project InPro, the framework for integrated collaboration and the use of BIM are analysed. Subsequently, through the observation of two ongoing pilot projects in The Netherlands, the changing roles of clients, architects, and contractors through BIM application are investigated. In conclusion, the critical success factors as well as the main barriers of a successful integrated collaboration using BIM are identified.2. Changing roles through integrated collaboration and life-cycle design approachesA hospital building project involves various actors, roles, and knowledge domains. In The Netherlands, the changing roles of clients, architects, and contractors in hospital building projects are inevitable due the new healthcare policy. Previously under the Healthcare Institutions Act (WTZi), healthcare institutions were required to obtain both a license and a building permit for new construction projects and major renovations. The permit was issued by the Dutch Ministry of Health. The healthcare institutions were then eligible to receive financial support from the government. Since 2008, new legislation on the management of hospital building projects and real estate has come into force. In this new legislation, a permit for hospital building project under the WTZi is no longer obligatory, nor obtainable (Dutch Ministry of Health, Welfare and Sport, 2008). This change allows more freedom from the state-directed policy, and respectively,allocates more responsibilities to the healthcare organisations to deal with the financing and management of their real estate. The new policy implies that the healthcare institutions are fully responsible to man age and finance their building projects and real estate. The government?s support for the costs of healthcare facilities will no longer be given separately, but will be included in the fee for healthcare services. This means that healthcare institutions must earn back their investment on real estate through their services. This new policy intends to stimulate sustainable innovations in the design, procurement and management of healthcare buildings, which will contribute to effective and efficient primary healthcare services.The new strategy for building projects and real estate management endorses an integrated collaboration approach. In order to assure the sustainability during construction, use, and maintenance, the end-users, facility managers, contractors and specialist contractors need to be involved in the planning and design processes. The implications of the new strategy are reflected in the changing roles of the building actors and in the new procurement method.In the traditional procurement method, the design, and its details, are developed by the architect, and design engineers. Then, the client (the healthcare institution) sends an application to the Ministry of Healthto obtain an approval on the building permit and the financial support from the government. Following this, a contractor is selected through a tender process that emphasises the search for the lowest-price bidder. During the construction period, changes often take place due to constructability problems of the design and new requirements from the client.Because of the high level of technical complexity, and moreover, decision-making complexities, the whole process from initiation until delivery of a hospital building project can take up to ten years time. After the delivery, the healthcare institution is fully in charge of the operation of the facilities. Redesigns and changes also take place in the use phase to cope with new functions and developments in the medical world.The integrated procurement pictures a new contractual relationship between the parties involved in a building project. Instead of a relationship between the client and architect for design, and the client and contractor for construction, in an integrated procurement the client only holds a contractual relationship with the main party that is responsible for both design and construction. The traditional borders between tasks and occupational groups become blurred since architects, consulting firms, contractors, subcontractors, and suppliers all stand on the supply side in the building process while the client on the demand side. Such configuration puts the architect, engineer and contractor in a very different position that influences not only their roles, but also their responsibilities, tasks and communication with the client, the users, the team and other stakeholders.The transition from traditional to integrated procurement method requires a shift of mindset of the parties on both the demand and supply sides. It is essential for the client and contractor to have a fair and open collaboration in which both can optimally use their competencies. The effectiveness of integrated collaboration is also determined by the client?s capacity and strategy to organize innovative tendering procedures.A new challenge emerges in case of positioning an architect in a partnership with the contractor instead of with the client. In case of the architect enters a partnership with the contractor, an important issues is how to ensure the realisation of the architectural values as well as innovative engineering through an efficient construction process. In another case, the architect can stand at the client?s side in a strategic advisory role instead of being the designer. In this case, the architect?s responsibility is translating client?s requirements and wishes into the architectural values to be included in the design specification, and evaluating the contractor?s proposal against this. In any of this new role, the architect holds the responsibilities as stakeholder interest facilitator, custodian of customer value and custodian of design models.The transition from traditional to integrated procurement method also brings consequences in the payment schemes. In the traditional building process, the honorarium for the architect is usually based on a percentage of the project costs; this may simply mean that the more expensive the building is, the higher the honorarium will be. The engineer receives the honorarium based on the complexity of the design and the intensity of the assignment. A highly complex building, which takes a number of redesigns, is usually favourable for the engineers in terms of honorarium. A traditional contractor usually receives the commission based on the tender to construct the building at the lowest price by meeting the minimum specifications given by the client. Extra work due to modifications is charged separately to the client. After the delivery, the contractor is no longer responsible for the long-term use of the building. In the traditional procurement method, all risks are placed with theclient.In integrated procurement method, the payment is based on the achieved building performance; thus, the payment is non-adversarial. Since the architect, engineer and contractor have a wider responsibility on the quality of the design and the building, the payment is linked to a measurement system of the functional and technical performance of the building over a certain period of time. The honorarium becomes an incentive to achieve the optimal quality. If the building actors succeed to deliver a higher added-value thatexceed the minimum client?s requirements, they will receive a bonus in accordance to the client?s extra gain. The level of transparency is also improved. Open book accounting is an excellent instrument provided that the stakeholders agree on the information to be shared and to its level of detail (InPro, 2009).Next to the adoption of integrated procurement method, the new real estate strategy for hospital building projects addresses an innovative product development and life-cycle design approaches. A sustainable business case for the investment and exploitation of hospital buildings relies on dynamic life-cycle management that includes considerations and analysis of the market development over time next to the building life-cycle costs (investment/initial cost, operational cost, and logistic cost). Compared to the conventional life-cycle costing method, the dynamic life-cycle management encompasses a shift from focusing only on minimizing the costs to focusing on maximizing the total benefit that can be gained. One of the determining factors for a successful implementation of dynamic life-cycle management is the sustainable design of the building and building components, which means that the design carriessufficient flexibility to accommodate possible changes in the long term (Prins, 1992).Designing based on the principles of life-cycle management affects the role of the architect, as he needs to be well informed about the usage scenarios and related financial arrangements, the changing social and physical environments, and new technologies. Design needs to integrate people activities and business strategies over time. In this context, the architect is required to align the design strategies with the organisational, local and global policies on finance, business operations, health and safety, environment, etc.The combination of process and product innovation, and the changing roles of the building actors can be accommodated by integrated project delivery or IPD (AIA California Council, 2007). IPD is an approach that integrates people, systems, business structures and practices into a process that collaboratively harnesses the talents and insights of all participants to reduce waste and optimize efficiency through all phases of design, fabrication and construction. IPD principles can be applied to a variety of contractual arrangements. IPD teams will usually include members well beyond the basic triad of client, architect, and contractor. At a minimum, though, an Integrated Project should include a tight collaboration between the client, the architect, and the main contractor ultimately responsible for construction of the project, from the early design until the project handover. The key to a successful IPD is assembling a team that is committed to collaborative processes and is capable of working together effectively. IPD is built on collaboration. As a result, it can only be successful if the participants share and apply common values and goals.3. Changing roles through BIM applicationBuilding information model (BIM) comprises ICT frameworks and tools that can support the integrated collaboration based on life-cycle design approach. BIM is a digital representation of physical and functional characteristics of a facility. As such it serves as a shared knowledge resource for information about a facility forming a reliable basis for decisions during its lifecycle from inception onward (National Institute of Building Sciences NIBS, 2007). BIM facilitates time and place independent collaborative working. A basic premise of BIM is collaboration by different stakeholders at different phases of the life cycle of a facility to insert, extract, update or modify information in the BIM to support and reflect the roles of that stakeholder. BIM in its ultimate form, as a shared digital representation founded on open standards for interoperability, can become a virtual information model to be handed from the design team to the contractor and subcontractors and then to the client.BIM is not the same as the earlier known computer aided design (CAD). BIM goes further than an application to generate digital (2D or 3D) drawings. BIM is an integrated model in which all process and product information is combined, stored, elaborated, and interactively distributed to all relevant building actors. As a central model for all involved actors throughout the project lifecycle, BIM develops andevolves as the project progresses. Using BIM, the proposed design and engineering solutions can be measured against the client?s requirements and expected building performance. The functionalities of BIM to support the design process extend to multidimensional (nD), including: three-dimensional visualisation and detailing, clash detection, material schedule, planning, costestimate, production and logistic information, and as-built documents. During the construction process, BIM can support the communication between the building site, the factory and the design office– which is crucial for an effective and efficient prefabrication and assembly processes as well as to prevent or solve problems related to unforeseen errors or modifications. When the building is in use, BIM can be used in combination with the intelligent building systems to provide and maintain up-to-date information of the building performance, including the life-cycle cost.To unleash the full potential of more efficient information exchange in the AEC/FM industry in collaborative working using BIM, both high quality open international standards and high quality implementations of these standards must be in place. The IFC open standard is generally agreed to be of high quality and is widely implemented in software. Unfortunately, the certification process allows poor quality implementations to be certified and essentially renders the certified software useless for any practical usage with IFC. IFC compliant BIM is actually used less than manual drafting for architects and contractors, and show about the same usage for engineers. A recent survey shows that CAD (as a closed-system) is still the major form of technique used in design work (over 60 per cent) while BIM is used in around 20 percent of projects for architects and in around 10 per cent of projects for engineers and contractors.The application of BIM to support an optimal cross-disciplinary and cross-phase collaboration opens a new dimension in the roles and relationships between the building actors. Several most relevant issues are: the new role of a model manager; the agreement on the access right and IntellectualProperty Right (IPR); the liability and payment arrangement according to the type of contract and in relation to the integrated procurement; and the use of open international standards.Collaborative working using BIM demands a new expert role of a model manager who possesses ICT as well as construction process know-how (InPro, 2009). The model manager deals with the system as well as with the actors. He provides and maintains technological solutions required for BIM functionalities, manages the information flow, and improves the ICT skills of the stakeholders. The model manager does not take decisions on design and engineering solutions, nor the organisational processes, but his roles in the chain of decision making are focused on:the development of BIM, the definition of the structure and detail level of the model, and the deployment of relevant BIM tools, such as for models checking, merging, and clash detections;the contribution to collaboration methods, especially decision making and communication protocols, task planning, and risk management;and the management of information, in terms of data flow and storage, identification of communication errors, and decision or process (re-)tracking.Regarding the legal and organisational issues, one of the actual questions is: “In what way does the intellectual property right (IPR) in collaborative working using BIM differ from the IPR in a traditional teamwork?”. In terms of combine d work, the IPR of each element is at tached to its creator. Although it seems to be a fully integrated design, BIM actually resulted from a combination of works/elements; for instance: the outline of the building design, is created by the architect, the design for theelectrical system, is created by the electrical contractor, etc. Thus, in case of BIM as a combined work, the IPR is similar to traditional teamwork. Working with BIM with authorship registration functionalities may actually make it easier to keep track of the IPR.How does collaborative working, using BIM, effect the contractual relationship? On the one hand,collaborative working using BIM does not necessarily change the liability position in the contract nor does it obligate an alliance contract. The General Principles of BIM A ddendum confirms: …This does not effectuate or require a restructuring of contractual relationships or shifting of risks between or among the Project Participants other than as specifically required per the Protocol Addendum and its Attachments? (ConsensusDOCS, 2008). On the other hand, changes in terms of payment schemes can be anticipated. Collaborative processes using BIM will lead to the shifting of activities from to the early design phase. Much, if not all, activities in the detailed engineering and specification phase will be done in the earlier phases. It means that significant payment for the engineering phase, which may count up to 40 per cent of the design cost, can no longer be expected. As engineering work is done concurrently with the design, a new proportion of the payment in the early design phase is necessary.4. Review of ongoing hospital building projects using BIMIn The Netherlands, the changing roles in hospital building projects are part of the strategy, which aims at achieving a sustainable real estate in response to the changing healthcare policy. Referring to literature and previous research, the main factors that influence the success of the changing roles can be concluded as: the implementation of an integrated procurementmethod and a life-cycle design approach for a sustainable collaborative process; the agreement on the BIM structure and the intellectual rights; and the integration of the role of a model manager. The preceding sections have discussed the conceptual thinking on how to deal with these factors effectively. This current section observes two actual projects and compares the actual practice with the conceptual view respectively.The main issues, which are observed in the case studies, are: the selected procurement method and the roles of the involved parties within this method;the implementation of the life-cycle design approach;the type, structure, and functionalities of BIM used in the project;the openness in data sharing and transfer of the model, and the intended use of BIM in the future; and the roles and tasks of the model manager.The pilot experience of hospital building projects using BIM in the Netherlands can be observed at University Medical Centre St Radboud (further referred as UMC) and Maxima Medical Centre (further referred as MMC). At UMC, the new building project for the Faculty of Dentistry in the city of Nijmegen has been dedicated as a BIM pilot project. At MMC, BIM is used in designing new buildings for Medical Simulation and Mother-and-Child Centre in the city of Veldhoven.The first case is a project at the University Medical Centre (UMC) St Radboud. UMC is more than just a hospital. UMC combines medical services, education and research. More than 8500 staff and 3000 students work at UMC. As a part of the innovative real estate strategy, UMC has considered to use BIM for its building projects. The new development of the Faculty ofDentistry and the surrounding buildings on the Kapittelweg in Nijmegen has been chosen as a pilot project to gather practical knowledge and experience on collaborative processes with BIM support.The main ambition to be achieved through the use of BIM in the building projects at UMC can be summarised as follows: using 3D visualisation to enhance the coordination and communication among the building actors, and the user participation in design;integrating the architectural design with structural analysis, energy analysis, cost estimation, and planning;interactively evaluating the design solutions against the programme of requirements and specifications;reducing redesign/remake costs through clash detection during the design process; andoptimising the management of the facility through the registration of medical installations andequipments, fixed and flexible furniture, product and output specifications, and operational data.The second case is a project at the Maxima Medical Centre (MMC). MMC is a large hospital resulted from a merger between the Diaconessenhuis in Eindhoven and St Joseph Hospital in Veldhoven. Annually the 3,400 staff of MMC provides medical services to more than 450,000 visitors and patients. A large-scaled extension project of the hospital in Veldhoven is a part of its real estate strategy. A medical simulation centre and a women-and-children medical centre are among the most important new facilities within this extension project. The design has been developed using 3D modelling with several functionalities of BIM.The findings from both cases and the analysis are as follows.Both UMC and MMC opted for a traditional procurement method in which the client directly contracted an architect, a structural engineer, and a mechanical, electrical and plumbing (MEP) consultant in the design team. Once the design and detailed specifications are finished, a tender procedure will follow to select a contractor. Despite the choice for this traditional method, many attempts have been made for a closer and more effective multidisciplinary collaboration. UMC dedicated a relatively long preparation phase with the architect, structural engineer and MEP consultant before the design commenced. This preparation phase was aimed at creating a common vision on the optimal way for collaboration using BIM as an ICT support. Some results of this preparation phase are: a document that defines the common ambition for the project and the collaborative working process and a semi-formal agreement that states the commitment of the building actors for collaboration. Other than UMC, MMC selected an architecture firm with an in-house engineering department. Thus, the collaboration between the architect and structural engineer can take place within the same firm using the same software application.Regarding the life-cycle design approach, the main attention is given on life-cycle costs, maintenance needs, and facility management. Using BIM, both hospitals intend to get a much better insight in these aspects over the life-cycle period. The life-cycle sustainability criteria are included in the assignments for the design teams. Multidisciplinary designers and engineers are asked to collaborate more closely and to interact with the end-users to address life-cycle requirements. However, ensuring the building actors to engage in an integrated collaboration to generate sustainable design solutions that meet the life-cycle。
毕业设计外文文献翻译范文
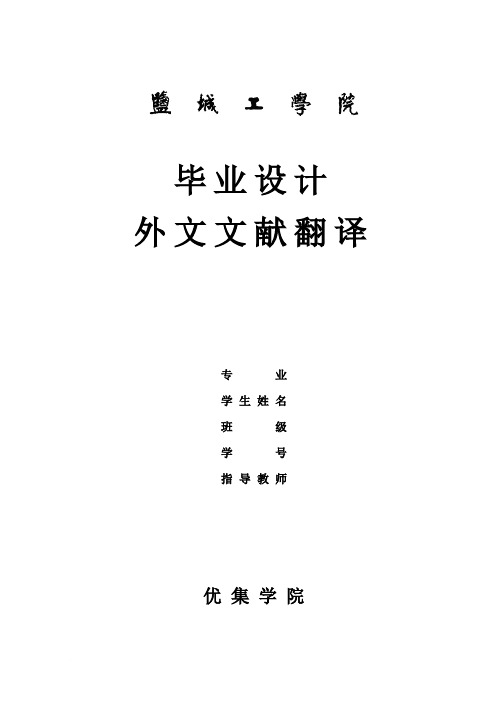
毕业设计外文文献翻译专业学生姓名班级学号指导教师优集学院外文资料名称:Knowledge-Based Engineeri--ng Design Methodology外文资料出处:Int.J.Engng Ed.Vol.16.No.1附件: 1.外文资料翻译译文2.外文原文基于知识工程(KBE)设计方法D. E. CALKINS1.背景复杂系统的发展需要很多工程和管理方面的知识、决策,它要满足很多竞争性的要求。
设计被认为是决定产品最终形态、成本、可靠性、市场接受程度的首要因素。
高级别的工程设计和分析过程(概念设计阶段)特别重要,因为大多数的生命周期成本和整体系统的质量都在这个阶段。
产品成本的压缩最可能发生在产品设计的最初阶段。
整个生命周期阶段大约百分之七十的成本花费在概念设计阶段结束时,缩短设计周期的关键是缩短概念设计阶段,这样同时也减少了工程的重新设计工作量。
工程权衡过程中采用良好的估计和非正式的启发进行概念设计。
传统CAD工具对概念设计阶段的支持非常有限。
有必要,进行涉及多个学科的交流合作来快速进行设计分析(包括性能,成本,可靠性等)。
最后,必须能够管理大量的特定领域的知识。
解决方案是在概念设计阶段包含进更过资源,通过消除重新设计来缩短整个产品的时间。
所有这些因素都主张采取综合设计工具和环境,以在早期的综合设计阶段提供帮助。
这种集成设计工具能够使由不同学科的工程师、设计者在面对复杂的需求和约束时能够对设计意图达成共识。
那个设计工具可以让设计团队研究在更高级别上的更多配置细节。
问题就是架构一个设计工具,以满足所有这些要求。
2.虚拟(数字)原型模型现在需要是一种代表产品设计为得到一将允许一产品的早发展和评价的真实事实上原型的过程的方式。
虚拟样机将取代传统的物理样机,并允许设计工程师,研究“假设”的情况,同时反复更新他们的设计。
真正的虚拟原型,不仅代表形状和形式,即几何形状,它也代表如重量,材料,性能和制造工艺的非几何属性。
毕业设计外文原文及翻译
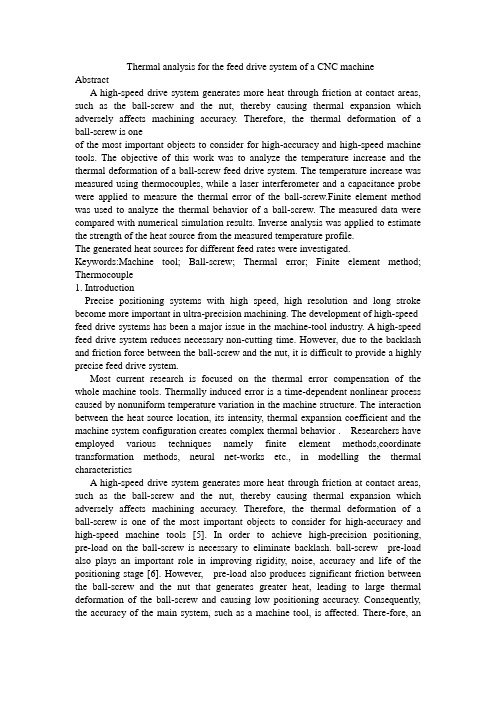
Thermal analysis for the feed drive system of a CNC machineAbstractA high-speed drive system generates more heat through friction at contact areas, such as the ball-screw and the nut, thereby causing thermal expansion which adversely affects machining accuracy. Therefore, the thermal deformation of a ball-screw is oneof the most important objects to consider for high-accuracy and high-speed machine tools. The objective of this work was to analyze the temperature increase and the thermal deformation of a ball-screw feed drive system. The temperature increase was measured using thermocouples, while a laser interferometer and a capacitance probe were applied to measure the thermal error of the ball-screw.Finite element method was used to analyze the thermal behavior of a ball-screw. The measured data were compared with numerical simulation results. Inverse analysis was applied to estimate the strength of the heat source from the measured temperature profile.The generated heat sources for different feed rates were investigated.Keywords:Machine tool; Ball-screw; Thermal error; Finite element method; Thermocouple1. IntroductionPrecise positioning systems with high speed, high resolution and long stroke become more important in ultra-precision machining. The development of high-speed feed drive systems has been a major issue in the machine-tool industry. A high-speed feed drive system reduces necessary non-cutting time. However, due to the backlash and friction force between the ball-screw and the nut, it is difficult to provide a highly precise feed drive system.Most current research is focused on the thermal error compensation of the whole machine tools. Thermally induced error is a time-dependent nonlinear process caused by nonuniform temperature variation in the machine structure. The interaction between the heat source location, its intensity, thermal expansion coefficient and the machine system configuration creates complex thermal behavior . Researchers have employed various techniques namely finite element methods,coordinate transformation methods, neural net-works etc., in modelling the thermal characteristicsA high-speed drive system generates more heat through friction at contact areas, such as the ball-screw and the nut, thereby causing thermal expansion which adversely affects machining accuracy. Therefore, the thermal deformation of a ball-screw is one of the most important objects to consider for high-accuracy and high-speed machine tools [5]. In order to achieve high-precision positioning, pre-load on the ball-screw is necessary to eliminate backlash. ball-screw pre-load also plays an important role in improving rigidity, noise, accuracy and life of the positioning stage [6]. However, pre-load also produces significant friction between the ball-screw and the nut that generates greater heat, leading to large thermal deformation of the ball-screw and causing low positioning accuracy. Consequently, the accuracy of the main system, such as a machine tool, is affected. There-fore, anoptimum pre-load of the ball-screw is one of the most important things to consider for machine tools with high accuracy and great rigidity.Only a few researchers have tackled this problem with some success. Huang used the multiple regression method to analyze the thermal deformation of a ball-screw feed drive system. Three temperature increases at front bearing, nut and back bearing were selected as independent variables of the analysis model. The multiple-regression model may be used to predict the thermal deformation of the ball-screw. Kim et al. Analyzed the temperature distribution along a ball-screw system using finite element methods with bilinear type of elements. Heat induced due to friction is the main source of deformation in a ball-screw system, the heat generated being dependent on the pre-load, the lubrication of the nut and the assembly conditions. The proposed FEM model was based on the assumption that the screw shaft and nut are a solid and hollow shaft respectively. Yun et al. used the modified lumped capacitance method and genius education algorithm to analyze the linear positioning error of the ball-screw.The objective of this work was to analyze the temperature increase and the thermal deformation of a ball-screw feed drive system. The temperature increase was measured using thermocouples while a laser interferometer and a capacitance probe were applied to meas-ure the thermal error of the ball-screw. Finite element method was also applied to simulate the thermal behavior of the ball-screw. Measured data were compared with numerical simulation results. Inverse analysis was applied to estimate the strength of the heat source from the measured temperature pro file. Generated heat sources for different feed rates were investigated.2 Experimental set-up and procedureIn this study, the object used to investigate the thermal characteristics of a ball-screw system is a machine center as shown in Fig. 1. The maximum rapid speed along thex-axis of the machine center is 40 m/min and the x-axis travel is 800 mm. The table repeatedly moved along the x-axis with a stroke of 600 mm. The main heat sourceFig. 1. Photograph of machine center.of the ball-screw system is the friction caused by a moving nut and rotating bearings. The produced temperature increase and thermal deformation were measured to study the thermal characteristics of the ball-screw system.In order to measure the temperature increase and the thermal deformation of a ball-screw system under long-term movement of the nut, experiments were performed with the arrangement shown in Fig. 2. Temperatures at nine points were measured as shown in Fig. 2a .Two thermocouples (numbered 1 and 8) were located on the rear and front bearing surfaces, respectively. They were used to measure the surface temperatures of these two support bearings. The last one (numbered 9) was used to measure the room temperature. The recorded room temperature was to eliminate the effect of environmental variation. These three thermocouples were used for continuous acquisition under moving conditions. The other six thermocouples (numbered 2 –7) were used to measure the surface temperatures of the ball-screw. Because the moving nut covered most of the ball-screw, thermocouples cannot be consistently fixed on the ball-screw. While temperature measurement was necessary, the ball-screw stopped running and these six thermocouples were quickly attached to specified locations of the ball-screw. Having collected the required data, the thermocouples were quickly removed.Thermal deformation errors were simultaneously measured with two methods. Because a thrust bearing is used on the driving side of the ball-screw, this end is considered to be fixed. A capacitance probe was installed next to the driven side of the ball-screw with a direction perpendicular to the side surface as shown in Fig. 2b. This probe was used to record the whole thermal deformation of the ball-screw. The values can be collected continuously during running conditions. The second method is used to measure the thermal error distribution at some specified time. Before the feed drive system started to operate, the original positional error distribution was measured with a laser interferometer (HP5528A). The table moved step-by-step (the increment ofFig. 2. Locations of measured points for (a) temperatures and (b) thermal errors.each step was 100 mm) and the positioning error was recorded at each step. Then the feed drive system started to operate and generate heat. After a certain time interval, the feed drive system stopped to measure thermal errors. In the same way, the positioning error distribution was again collected with the laser interferometer. Subtracting the actual error from the original error of the x-coordinates, the results are net thermal errors. Having collected the temperature increase (with thermocouples) and deformation distribution, the feed drive system starts running again.In this study, three feed rates (10, 15 and 20 m/min) along the x-axis and three different pre-loads (0, 150 and 300 kgf·cm) were used. The table moved along the x-axis in a reciprocating motion and the stroke was 600mm. The point temperatures and thermal errors were measured at sampling intervals of 10 min. Each stopping time was only about 10 s. These procedures were operated repeatedly until the temperature reached a steady state.3. Experimental results and discussionThe developed experimental setup was utilized for three constant feed rates (running at 10, 15 and 20m/min, respectively). The table reciprocated until point temperatures and thermal errors reached a steady state. Firstly, the ball-screw pre-load was zero and its thermal characteristics were studied. In Fig. 3, temperature variationsFig. 3. (a) Measured temperature increase and (b) thermal error over time for feed rate of 10 m/min and zero-pre-load.and thermal errors of the feed drive system are shown over time for a feed rate of 10 m/min. Measurements can also be made for feed rates of 15 and 20m/min. Themeasured data at a steady state are shown in Tables 1 and 2 . A brief discussion can be made as fol-lows.1. The higher feed rate produces larger frictional heat at the interface between the ball-screw and the nut. The frictional heat generated by the support bearings and the motor also increases with the feed rate. Therefore, the temperature of the ball-screw increases with the feed rate.2. The table travels over the middle part with a 600 mm stroke. The central part of the ball-screw reveals a higher temperature increase. Support bearings do not have high temperature increase because the bearing pre-load is zero.3. A higher rotational speed brings a larger thermal expansion for the ball-screw. The middle part of the screw has a slightly larger thermal expansion because of its higher temperature increase. However, this phenomenon is not obvious. The thermal error at some specified point of the ball-screw is approximately proportional to the distance between this point and the front end (the motor-driving side of the screw). Secondly, the ball-screw pre-load was set at 150kgf·cm and its thermal characteristics were studied. In Figs. 4 –5, temperature variations around the feed drive system and thermal errors are shown over time for feed rates of 10 and 15 m/min. Measured data are shown in Tables 1 and 2. Results reveal two interesting phenomena shown as follows.1. Temperature increases of measured points grow gradually until the ball-screw reaches a steady state except for the temperature increase of the bearing on the driven side. The temperature of this bearing quickly reaches a maximum value and then gradually drops.2. The thermal errors of P6, P7 and P8 are negative at the steady state. It means that these three points move to the driving side due to thermal expansion, while other points move to the driven side. Furthermore, the thermal errors of P4 to P8 show a gradual decrease after 60 min.These phenomena are different from previous results with no pre-load. Some experiments were carried out to study these phenomena. We found that the two bearing stands bent if the ball-screw was pre-loaded. After the pre-load was applied on the ball-screw, the original positional error distribution was measured using a laser interferometer. At this moment, the bending effects on error distribution were includ- Table 1Temperature distribution at steady state with different pre-loads and feed rates (unit: °C)Table 2Thermal error distribution at steady state with different pre-loads and feed rates (unit:µm)Fig. 4. (a) Measured temperature increase Fig. 5. (a) Measured temperature increase and (b) thermal error over time for feed and (b) thermal error over time for feed rate of 10 m/min and pre-load of rate of 15 m/min and pre-load of150kgf ·cm. 150kgf ·cm.-ed in the measured positioning error. The feed drive system starts to run and the ball-screw expands. The expansion relaxes the pre-load of the ball-screw and the bending deformation of two bearing stands. Therefore, the points on the driving side move closer to the motor, thereby thermal errors are negative, nevertheless, the points on the driven side move to the free end, thereby thermal errors are positive.The temperature change of the rear bearing was also investigated. A journal bearing was applied on the driven side and a thrust bearing was applied on the driving side. The pre-load of the ball-screw increases the pre-load of the bearing on the driven side. When the feed drive system runs, the bearing temperature on the driven side sharplyincreases due to the rising pre-load. However, the thermal expansion of the ball-screw relaxes the ball-screw and decreases pre-load of the bearing on the driven side. Therefore, the temperature gradually decreases to a steady state.Finally, the ball-screw pre-load was set to 300kgf·cm and its thermal characteristics were studied. In Figs. 6 and 7, temperature variations around the feed drive systemFig. 6. (a) Measured temperature increase and (b) thermal error over time for feed rate of 10 m/min and pre-load of 300kgf ·cm.Fig. 7. (a) Measured temperature increase and (b) thermal error over time for feed rate of 15 m/min and pre-load of 300kgf ·cm.and thermal errors are shown over time for feed rates of 10 and 15 m/min. The tendency with a 300kgf·cm is similar to that with a 150kgf·cm. Measured data are shown in Tables 1 and 2.4. Numerical simulationThe main heat source of a ball-screw system is the friction caused by a moving nut and the support bearings. In this study, temperature distribution was calculated using the FEM based on the following assumptions:1. The screw shaft is a solid cylinder.2. Friction heat generation between the moving nut and the screw shaft is uniform at contacting surface and is proportional to contacting time.3. Heat generation at support bearings is also constant per unit area and unit time.4. Convective heat coefficients are always constant during moving. The radiation term is neglected.The problem is de fined as transient heat conduction in non-deforming media without radiation. A classical form of the initial/boundary value problem is shown below:where is the internal heat generation rate, q the entering heat flux, a unit outward normal vector, the ambient temperature and h the convective heattrans-fer coefficient at a given boundary. A simplified heat transfer model of the ball-screw system is described in Fig. 8 along with the boundary conditions. The nut moves reciprocally with a stroke, s. The length of the nut is w. According to the previously mentioned assumption, No. 2, frictional heat fluxes on the balls-crew are shown as in Fig. 8b . Both ends of the balls-crew are subjected to frictional heat fluxq and q caused by the support bearings. Heat fluxes on rear and front ends are13 respectively. Other surfaces are subjected to convection heat transfer as shown in Fig.8c .To obtain an approximate solution, Eqs. (1)–(3) may be transformed through discretization into algebraic expressions that may be solved for unknowns. In orderto allow the replacement of the continuous system by an equivalent discrete system, the original domain is divided into elements. Four-node tetrahedral elements are chosen in this study. Elements and nodes of the balls-crew for FEM are shown in Fig.9.Once temperature distribution is obtained, the thermal expansion of the balls-crew may be predicted. In the case of linearly elastic isotropic three-dimensional solid, stress–strain relations are given by Hooke ’s law as [9]:of balls-crew.Fig. 9. Elements and nodes of ball-screw for FEM.where [C] is a matrix of elastic coefficients and 0ε→is the vector of initial strains. In the case of heating of an isotropic material, the initial strain vector is given by:where a is the coefficient of thermal expansion and T is the temperature change. Three unknowns 123,,q q and q are to be determined with inverse analysis. Firstly, initial guessing of these heat fluxes is applied in FEM simulation to obtain the temperature distribution of the balls-crew. If numerical results do not agree with the measured temperature distribution, the values of 123,,q q and q are adjusted iteratively until numerical and simulation results are in good agreement.Calculated values of 123,,q q and q for an un-pre-loaded ball-screw are listed in Table3. Measured and simulated temperature distributions for feed rates of 10, 15 and 20 m/min are indicated in Fig. 10. For each feed rate, it shows a good agreement between measured and simulated temperature distributions. The numerical program can also be used to simulate the thermal expansion of the ball-screw based on the calculated heatTable 3Values of heat flux at different locations (unit:2W m)/Fig. 10. Temperature increase from experimental measurement and numerical simulation for feed rate of (a) 10 m/min, (b) 15 m/min and (c) 20 m/min.fluxes. Measured and simulated thermal expansions of the ball-screw are compared as shown in Table 4. Thermal expansions also show good agreement with each other. From Table 3, the heat flux increases with the feed rate. Approximate linear relation can be found between the heat flux and the feed rate under the same operating condition.5. ConclusionsThis paper proposes a systematic method to investigate the thermal characteristics of a feed drive system. The approach measures the temperature increase and the thermal deformation under long-term movement of the working table. A simplified FEM model for the ball-screw was developed. The FEM model incorporated with themeasured temperature distribution was used to determine the strength of the frictional heat source by inverse analysis. The strength of the heat source was applied to the FEM model to calculate the thermal errors of the feed drive system. Calculated and measured thermal errors were found to agree with each other. From the results, the following conclusions can be drawn:1. The positional accuracy increases while closer to the driving side of the ball-screw. The thermal error increases with the distance to the driven side of the ball-screw. The maximum thermal error occurs at the driven side of the ball-screw (free end). This value can be taken as the total thermal error of the ball-screw and may be measured with a capacitance probe.2. The ball-screw pre-load raises the temperature increases of both support bearings, especially the bearing on the driven side. The surface temperature of the ball-screw decreases because the thermal effects relax the pre-load, thereby decreasing the friction between the nut and the ball-screw.3. The thermal expansion of the ball-screw increases with the feed rate, thereby increasing the positional error. However, the increasing pre-load reduces thermal errors and improves the positional accuracy of the feed drive system.4.Two bearing stands may bend if the ball-screw is pre-loaded. The thermal expansi Table 4Thermal errors at different feed rates-on relaxes the pre-load of the ball-screw and the bending deformation of two bearing stands. Therefore, the points on the motor side move closer to the motor and the thermal errors are negative; nevertheless, the points on the free side move to the free end and the thermal errors are positive.数控加工中心进给驱动系统的热分析摘要高速驱动系统在接触区域(如滚珠丝杠和螺母)通过摩擦产生大量的热,从而导致热膨胀,热膨胀严重地影响机械加工精度。
毕设外文文献翻译

毕设外文文献翻译移动机器人微型化:在控制算法方面的一个调查研究工具Francesco Mondada, Edoardo Franzi, and Paolo Ienne Francesco Mondada, Edoardo Franzi, and Paolo IenneFrancesco Mondada, Edoardo Franzi, and Paolo Ienne摘要:一个自主式移动机器人与现实世界互动的严重依赖于机器人形态和它的环境。
制造这些方面的模型是非常复杂的,因为模拟仿真不足以准确的验证控制算法。
如果仿真环境是高效的,那么用于实际机器人实验的工具往往是不够的。
传统的编程语言和工具对于真实的实验很少能提供足够多的支持,从而阻碍了对控制算法的理解,使得实验复杂而且费时。
有这样一个圆柱形状的微型机器人:直径55毫米,高度30毫米。
由于其体积小,实验可以在一个小工作区内迅速有效的进行。
可以设计小型的外围设备,并将其与基本模块相连,也可以利用一个通用的通信方案。
一个串行连接提供调试期间运行在工作站上的控制算法,从而使用户可以使用所有可用的图形工具。
一旦调试成功,该算法可以被下载到机器人,也可以在它自己的处理器中运行。
机器人组实验是很难用于现有的硬件。
所描述机器人的型号和价格提出了一种集体行为的成本效益调查的方式。
这方面的调查研究促进了本文中描述的机器人的设计。
在不久的将来计划进行大约二十个单位的实验。
关键字:移动机器人微型化Khepera机器人控制算法绘图器一、简介现在,移动机器人领域受到人们的高度重视。
一种全自主移动机器人有广泛的工业应用,包括自动清洗建筑物和工厂,用于移动监控系统,为工厂输送无固定装置需要配件,以及水果的采摘。
这些移动机器人应用已经超出了目前的技术范围,并显示了传统设计方法的不足。
人们试图用一些新的控制方法来改善机器人与现实世界的互动,以实现任务的自治。
布鲁克斯提出了一个包容结构的例子,该结构支持并行处理,以及强大的模块化。
毕业设计说明书外文文献及翻译
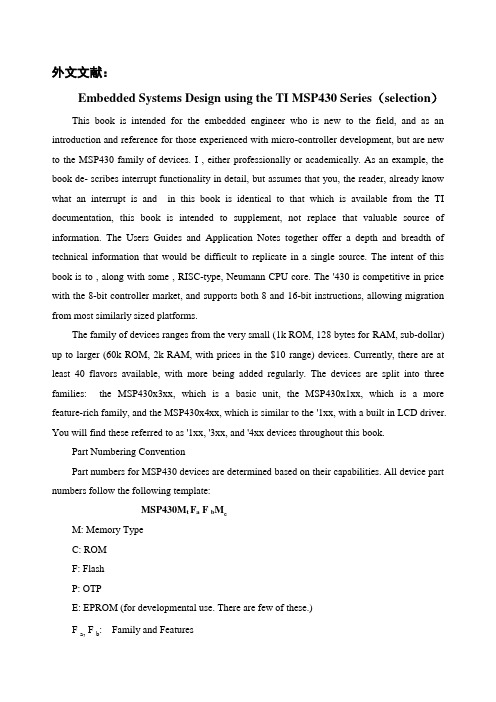
外文文献:Embedded Systems Design using the TI MSP430 Series(selection)This book is intended for the embedded engineer who is new to the field, and as an introduction and reference for those experienced with micro-controller development, but are new to the MSP430 family of devices. I , either professionally or academically. As an example, the book de- scribes interrupt functionality in detail, but assumes that you, the reader, already know what an interrupt is and in this book is identical to that which is available from the TI documentation, this book is intended to supplement, not replace that valuable source of information. The Users Guides and Application Notes together offer a depth and breadth of technical information that would be difficult to replicate in a single source. The intent of this book is to , along with some , RISC-type, Neumann CPU core. The '430 is competitive in price with the 8-bit controller market, and supports both 8 and 16-bit instructions, allowing migration from most similarly sized platforms.The family of devices ranges from the very small (1k ROM, 128 bytes for RAM, sub-dollar) up to larger (60k ROM, 2k RAM, with prices in the $10 range) devices. Currently, there are at least 40 flavors available, with more being added regularly. The devices are split into three families: the MSP430x3xx, which is a basic unit, the MSP430x1xx, which is a more feature-rich family, and the MSP430x4xx, which is similar to the '1xx, with a built in LCD driver. You will find these referred to as '1xx, '3xx, and '4xx devices throughout this book.Part Numbering ConventionPart numbers for MSP430 devices are determined based on their capabilities. All device part numbers follow the following template:MSP430M t F a F b McM: Memory TypeC: ROMF: FlashP: OTPE: EPROM (for developmental use. There are few of these.)F, F b: Family and Featuresa10, 11: Basic12, 13: Hardware UART14: Hardware UART, Hardware Multiplier31, 32: LCD Controller33: LCD Controller, Hardware UART, Hardware Multiplier41: LCD Controller43: LCD Controller, Hardware UART44: LCD Controller, Hardware UART, Hardware MultiplierM c: Memory Capacity0: 1kb ROM, 128b RAM1: 2kb ROM, 128b RAM2: 4kb ROM, 256b RAM3: 8kb ROM, 256b RAM4: 12kb ROM, 512b RAM5: 16kb ROM, 512b RAM6: 24kb ROM, 1kb RAM7: 32kb ROM, 1kb RAM8: 48kb ROM, 2kb RAM9: 60kb ROM, 2kb RAMExample: The MSP430F435 is a Flash memory device with an LCD controller, a features not consistently represented (type of ADC, number of timers, etc), and there are some other inconsistencies (for example, the 33 family their numbering scheme. Rather, once you chapter 1, the MSP430 utilizes a 16-bit RISC architecture, which is capable of processing instructions on either bytes or words. The CPU is identical for all members of the '430 family. It consists of a 3-stage instruction pipeline, instruction decoding, a 16-bit ALU, four dedicated-use registers, and twelve working (or scratchpad) registers. The CPU is connected to its memory through two 16-bit busses, one for addressing, and the other for data. All memory, including RAM, ROM, information memory, special function registers, and peripheral registers are mapped into a single, contiguous address space.This architecture is unique for several reasons. First, the designers at Texas Instrumentsawful lot of space for future development. Almost available special function registers are implemented.Second, there are plenty of working registers. After years of be much more efficient, especially in the most other small processors. But, beyond that, this architecture is simple, efficient and clean. There are two busses, a single linear memory space, a rather vanilla processor core, and all peripherals are memory-mapped.CPU FeaturesThe ALUThe '430 processor includes a pretty typical ALU (arithmetic logic unit). The ALU , subtraction, comparison and logical (AND, OR, XOR) operations. ALU operations can affect the overflow, zero, negative, and carry flags. The all devices, is implemented as a peripheral device, and is not part of the ALU (see Chapter 6).Working RegistersThe '430 gives the developer twelve 16-bit working registers, R4 through R15. (R0 through R3 are used for other functions, as described later.) They are used for register mode operations (see Addressing Modes, Chapter 8), which are much more efficient than operations which require memory access. Some guidelines for their use:Use these registers as much as possible. Any variable which is accessed often should reside in one of these locations, for the sake of efficiency.Generally speaking, you may select any of these registers for any purpose, either data or address. However, some development tools will reserve R4 and R5 for debug information. Different compilers will use these registers in different fashions, as well. Understand your tools.Be consistent about use of the working registers. Clearly document their use. I about 8 months ago, that performs extensive operations on R8, R9, and R15. Unfortunately, I don't know today what the values in R8, R9 and R15 represent. This was code I wrote to quickly validate an algorithm, rather than production code, so I didn't document it sufficiently. Now, it is relative gibberish. Don't let this to you. No matter as constant generators, so that register mode may be used instead of immediate mode for some common constants. (R2 is a dual use register. It serves as the Status Register, as well.) Generated constants include some common single-bit values (0001h, 0002h, 0004h, and 0008h), zero (0000h), and an all 1s field (0FFFFh). Generationis based on the W(S) value in the instruction word, and is described by the table below.W(S) value in R2 value in R300 ————0000h01 (0) (absolute mode) 0001h10 0004h 0002h11 0008h 0FFFFhProgram CounterThe Program Counter is located in R0. Since individual memory location addresses are 8-bit, but all instructions are 16 bit, the PC is constrained to even numbers (i.e. the LSB of the PC is always zero). Generally speaking, it is best to avoid direct manipulation of the PC. One exception to this rule of thumb is the implementation of a switch, where the code jumps to a spot, dependent on a given value. (I.e., if value=0, jump to location0, if value=1, jump to location1, etc.) This process is shown in Example 3.1.Example 3.1 Switch Statement via Manual PC ControlMov value,R15 ;put the switch value into R15Cmp R15,#8 ;range checkingJge outofrange ;if R15>7,do not use PC switchCmp #0,R15 ;more range checkingJn outofrange ;Rla R15 ;multiply R15 by two,since PC is always evenRla R15 ;double R15again,since symbolic jmp is 2 words longAdd R15,PC ;PC goes to proper jumpJmp value0Jmp value1Jmp value2Jmp value3Jmp value4Jmp value5Jmp value6Jmp value7OutofrangeJmp RangeErrorThis is a relatively common approach, and most C compilers will implement switch statements with something similar. When implementing this manually (i.e., in assembly language), the programmer needs to keep several things in mind:Always do proper range checking. In the example, we checked for conditions outside both ends of the valid range. If this is not performed correctly, the code can jump to an unintended location.Pay close attention to the addressing modes of the jump statements. The second doubling of R15, prior to the add statement, is added because the jump statement requires two words when symbolic mode addressing is used.Be careful that none of your interrupt the example). If the interrupt procedure is to push the register to the stack at the beginning of the ISR, and to pop the register at the end of the ISR. (See Example 3.2.)Example 3.2 PushPop Combination in ISRTimer_A_Hi_InterruptPush R12 ;We will use R12Mov P1IN,R12 ;use R12 as we pleaseRla R12Rla R12Mov R12&BAR ;Done with R12Pop R12 ;Restore previous value to R12Reti ;return from interruptORG 0FFF0hDW Timer_A_Hi_InterruptStatus RegisterThe Status Register is implemented in R2, and is comprised of various system flags. The flags are all directly accessible by code, and all but three of them are changed automatically by the processor itself. The 7 most significant bits are undefined. The bits of the SR are: • The Carry Flag (C)Location: SR(0) (the LSB)Function: Identifies when an operation results in a carry. Can be set or cleared by software, or automatically.1=Carry occurred0=No carry occurred•The Zero Flag (Z)Location: SR(1)Function: Identifies when an operation results in a zero. Can be set or cleared by software, or automatically.1=Zero result occurred0=Nonzero result occurred• The Negative Flag (N)Location: SR(2)Function: Identifies when an operation results in a negative. Can be set or cleared by software, or automatically. This flag reflects the value of the MSB of theoperation result (Bit 7 for byte operations, and bit 15 for word operations).1=Negative result occurred0=Positive result occurred• The Global Interrupt Enable (GIE)Location: SR(3)Function: Enables or disables all maskable interrupts. Can be set or cleared by software, or automatically. Interrupts automatically reset this bit, and the reti instructionautomatically sets it.1=Interrupts Enabled0=Interrupts Disabled• The CPU off bit (CPUOff)Location: SR(4)Function: Enables or disables the CPU core. Can be cleared by software, and is reset by enabled interrupts. None of the memory, peripherals, or clocks are affected bythis bit. This bit is used as a power saving feature.1=CPU is on0=CPU is off• The Oscillator off bit (OSCOff)Location: SR(5)Function: Enables or disables the crystal oscillator circuit (LFXT1). Can be cleared by software, and is reset by enabled external interrupts. OSCOff shuts downeverything, including peripherals. RAM and register contents are preserved.This bit is used as a power saving feature.1=LFXT1 is on0=LFXT1 is off• The System Clock Generator (SCG1,SCG0)Location: SR(7),SR(6)Function: These bits, along with OSCOff and CPUOff define the power mode of the device.• The Overflow Flag (V)Location: SR(8)Function: I dentifies when an operation results in an overflow. Can be set or cleared by software, or automatically. Overflow occurs when two positive numbers areadded together, and the result is negative, or when two negative numbers areadded together, and the result is positive.1=Overflow result occurred0=No overflow result occurredFour of these flags (Overflow, Negative, Carry, and Zero) drive program control, via instructions such as cmp (compare) and jz (jump if Zero flag is set). You will see these flags referred to often in this book, as their function represents a fundamental building block. The instruction set is detailed in Chapter 9, and each base instruction description there details the interaction between flags and instructions. As a programmer, you need to understand this interaction.Stack PointerThe Stack Pointer is implemented in R1. Like the Program Counter, the LSB is fixed as azero value, so the value is always even. The stack is implemented in RAM, and it is common practice to start the SP at the top ( one word in RAM (SP=SP-2), and puts the value to be pushed at the new SP. Pop does the reverse. Call statements and interrupts push the PC, and ret and reti statements pop the value from the TOS (top of stack) back into the PC. I , and don't fiddle with it manually after that. As long as you are wary of two stack conditions, the stack pointer manages itself. These two conditions are:Asymmetric pushpop combinations. Every push should empty stack, the SP moves out of RAM, and the program will fail.Stack encroachment. Remember, the stack is implemented in RAM. If your program RegistersSpecial function registers are, as you might of these registers, at memory locations 0000h through 000Fh. However, only the first six are used. Locations 0000h and 0001h contain interrupt enables, and locations 0002h and 0003h contain interrupt flags. These are described in Chapter 3.Locations 0004h and 0005h contain module enable flags. Currently, only two bits are implemented in each byte. These bits are used for the USARTs.Peripheral RegistersAll on-chip peripheral registers are mapped into memory, immediately after the special function registers. There are two types of peripheral registers: byte-addressable, which are mapped in the space from 010h to 0FFh, and word-addressable, which are mapped from 0100h to 01FFh.RAMRAM always begins at location 0200h, and is contiguous up to its final address. RAM is used for all scratchpad variables, global variables, and the stack. Some rules of thumb for RAM usage: The developer needs to be careful that scratchpad allocation and stack usage do not encroach on each other, or on global variables. Accidental sharing of RAM is a very common bug, and can be difficult to chase down. You need to clearly understand you need, and always deallocate as quickly as is reasonable. You can never flash devices only, located in memory locations 0C00h through 0FFFh. It is the only the flash devices. This memory contains the bootstrap loader, which is used for programming of flash blocks, via a USART module.Information Memory (flash devices only)Flash devices in the '430 family memory. This information memory acts as onboard EEPROM, allowing critical variables to be preserved through power down. It is divided into two 128-byte segments. The first of these segments is located at addresses 01000h through 0107Fh, and the second is at 01080h through 010FFh.Code MemoryCode memory is always contiguous at the end of the address space (i.e. always runs to location 0FFFFh). So, for 8k devices, code runs from 0E000h to 0FFFFh, and for the 60k devices, the code runs from 01100h to 0FFFFh. All code, tables, and this memory space.Interrupt VectorsInterrupt vectors are located at the very end of memory space, in locations 0FFE0h through 0FFFEh. Programming and use of these are described in detail in Chapter 3.Memory TypesThe MSP430 is available with any one of several different memory types. The memory type is identified by the letter immediately following "MSP430" in the part numbers. (Example: All MSP430Fxxx parts are flash decices).ROMROM devices, also known as masked devices, are identified by the letter "C" in the part numbers. They are strict ROM devices, shipped pre-programmed. They for -recurring engineering) costs, masked ROM is only cost-efficient when the process, the NRE costs acronym for "one time programmable", which pretty well describes the functionality of these devices. Identified by the letter "P" in the part number, OTP parts are a good compromise between ROM and flash parts. OTPs are shipped blank, and can be programmed at any time. They are typically more expensive than ROM. They also require programming, which can be a be a useful intermediate step when you are still uncertain about the stability of the design.EPROMTI offers windowed EPROM versions of several devices, intended for use in development. They are identified by the letter "E" in the part number. These devices are electrically programmable, and UV-erasable. EPROM devices are only available for a few devices, and typically cost on the order of $50 each. They are not intended for production use, but make ideal platforms for emulating ROM devices in development.FlashFlash devices, identified by the letter "F" in the part number, the past few years. They are more expensive, but code space can be erased and reprogrammed, thousands of times if necessary. This capability allows for features such as downloadable firmware, and lets the developer substitute code space for an external EEPROM.中文译文:利用TI的MSP430系列的嵌入式系统设计(节选)这本书是写给新进入此领域的嵌入式工程师,作为一个关于微控制器的开发经验的介绍和依据,但新的MSP430系列的设备。
- 1、下载文档前请自行甄别文档内容的完整性,平台不提供额外的编辑、内容补充、找答案等附加服务。
- 2、"仅部分预览"的文档,不可在线预览部分如存在完整性等问题,可反馈申请退款(可完整预览的文档不适用该条件!)。
- 3、如文档侵犯您的权益,请联系客服反馈,我们会尽快为您处理(人工客服工作时间:9:00-18:30)。
毕业设计说明书英文文献及中文翻译学生姓名:学号南社区0906064109学院:电子与计算机科学技术学院专业:网络工程指导教师:刘爽英2018年6月An Overview of Servlet and JSP TechnologyGildas Avoi ne and Philippe Oechsli nEPFL, Lausa nne, Switzerla nd1.1A Servlet's JobServlets are Java programs that run on Web or application servers, acting as a middle layer betwee n requests coming from Web browsers or other HTTP clie nts and databases or applicatio ns on the HTTP server. Their job is to perform the followi ngtasks, as illustrated in Figure 1-1b5E2RGbCAPWeb Server(Servlets JSP)Figure 1-1 1.Read the explicit data sent by the client. DatabaseLegacy Application Java Application Web ServiceClient (End User)The end user normally enters this data in an HTML form on a Web page. However, the data could also come from an applet or a custom HTTP clie nt program EanqFDPw2.Read the implicit HTTP request data sent by the browser X DiTa9E3dFigure 1-1 shows a single arrow going from the client to the Web server (the layer where servlets and JSP execute〉, but there are really two varieties of data: the explicit data that the end user en ters in a form and the behi nd-the-sce nes HTTP in formati on. Both varieties are critical. The HTTP information includes cookies, information about media types and compressi on schemes the browser un dersta nds, and sc RTCTpUDGiT3.Gen erate the results.This process may require talking to a database,executing an RMI or EJB call, invoking a Web service, or computing the response directly. Your real data may be in a relati onal database. Fine. But your database probably does n't speak HTTP or retur n results in HTML, so the Web browser can't talk directly to the database.Even if it could, for security reasons, you probably would not want it to. The same argument applies to most other applications. You need the Web middle layer to extract the incoming data from the HTTP stream, talk to the application, and embed the results in side a docume nt5PCzVD7HxA4.Send the explicit data (i.e., the document> to the client-BHrnAiLgThis document can be sent in a variety of formats, including text (HTML or XML>, bi nary (GIF images>, or eve n a compressed format like gzip that is layered on top of some other un derly ing format. But, HTML is by far the most com mon format, so an importa nt servlet/JSP task is to wrap the results in side of HTML H AQX74J0X5.Send the implicit HTTP response data.Figure 1-1 shows a single arrow going from the Web middle layer (the servlet or JSP page> to the clie nt. But, there are really two varieties of data sent: the docume nt itself and the behind-the-scenes HTTP information. Again, both varieties are critical to effective developme nt. Sending HTTP resp onse data invo Ives telli ng the browser or other clie nt what type of docume nt is being retur ned (e.g., HTML>, sett ing cookies and cach ing parameters, and other such task LD AYtR y KfE1.2Why Build Web Pages Dynamically?many client requests can be satisfied by prebuilt documents, and the server would handle these requests without invoking servlets. In many cases, however, a static result is not sufficie nt, and a page n eeds to be gen erated for each request. There are a nu mber of reas ons why Web pages n eed to be built on-the-f Z y z6ZB2Ltk1.The Web page is based on data sent by the clie dvZ f vkwMi1For instanee, the results page from search engines and order-confirmation pages at on li ne stores are specific to particular user requests. You don't know what to display un til you read the data that the user submits. Just remember that the user submits two kinds of data: explicit (i.e., HTML form data> and implicit (i.e., HTTP request headers>. Either kind of in put can be used to build the output page. In particular, it is quite com mon to builda user-specific page based on a cookie value.ni4ZNxi2.The Web page is derived from data that changes frequent f y.xvxotoc。
If the page changes for every request, then you certainly need to build the response at request time. If it changes only periodically, however, you could do it two ways: you could periodically build a new Web page on the server (in depe nden tly of clie nt requests>, or you could wait and only build the page whe n the user requests it. The right approach depends on the situation, but sometimes it is more convenient to do the latter: wait for the user request. For example, a weather report or news headli nes site might build the pages dyn amically, perhaps retur ning a previously built page if that page is still up todate sixE2yxpq53.The Web page uses information from corporate databasesor other server-sideSourceS6ewMyirQFLIf the information is in a database,you need server-side processing even if the clie nt is using dyn amic Web content such as an applet. Imagi ne using an applet by itself for a search engine site:avU42VRUs "Downloading 50 terabyte applet, please wait!" Obviously, that is silly。