冲压工艺及模具设计
冲压工艺及模具设计
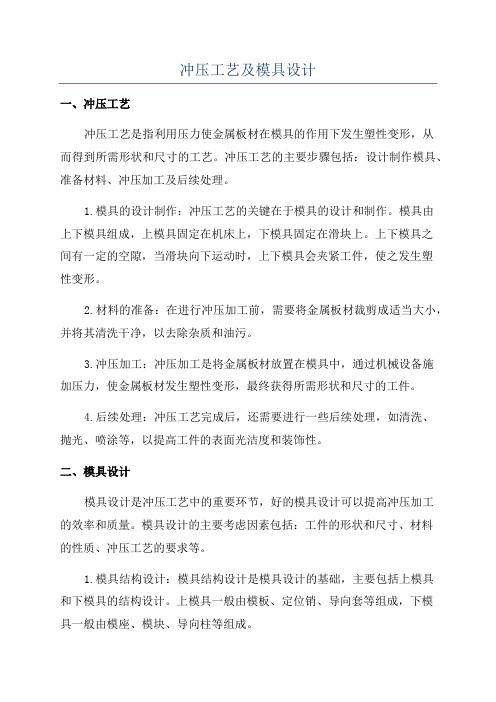
冲压工艺及模具设计一、冲压工艺冲压工艺是指利用压力使金属板材在模具的作用下发生塑性变形,从而得到所需形状和尺寸的工艺。
冲压工艺的主要步骤包括:设计制作模具、准备材料、冲压加工及后续处理。
1.模具的设计制作:冲压工艺的关键在于模具的设计和制作。
模具由上下模具组成,上模具固定在机床上,下模具固定在滑块上。
上下模具之间有一定的空隙,当滑块向下运动时,上下模具会夹紧工件,使之发生塑性变形。
2.材料的准备:在进行冲压加工前,需要将金属板材裁剪成适当大小,并将其清洗干净,以去除杂质和油污。
3.冲压加工:冲压加工是将金属板材放置在模具中,通过机械设备施加压力,使金属板材发生塑性变形,最终获得所需形状和尺寸的工件。
4.后续处理:冲压工艺完成后,还需要进行一些后续处理,如清洗、抛光、喷涂等,以提高工件的表面光洁度和装饰性。
二、模具设计模具设计是冲压工艺中的重要环节,好的模具设计可以提高冲压加工的效率和质量。
模具设计的主要考虑因素包括:工件的形状和尺寸、材料的性质、冲压工艺的要求等。
1.模具结构设计:模具结构设计是模具设计的基础,主要包括上模具和下模具的结构设计。
上模具一般由模板、定位销、导向套等组成,下模具一般由模座、模块、导向柱等组成。
2.模具材料选择:模具的材料选择直接影响到模具的使用寿命和加工质量。
一般情况下,模具材料应具有高硬度、高强度、良好的热导性和耐磨性等特性。
3.模具零件设计:模具零件的设计应考虑到工件的形状和尺寸,以及冲压工艺的要求。
模具零件的设计应尽量简化,减少加工难度,提高生产效率。
4.模具配合设计:模具零件之间的配合关系直接影响到模具的精度和稳定性。
模具配合设计应确保零件的定位准确、运动平稳,并充分考虑到热膨胀等因素。
综上所述,冲压工艺及模具设计是一项复杂的工程,它涉及到材料、结构、流程等多个方面。
通过合理的冲压工艺和精心的模具设计,可以实现高效、高质量的冲压加工,为生产制造提供有力支持。
冲压工艺及模具设计知识要点

冲压工艺及模具设计知识要点冲压工艺及模具设计知识要点冲压工艺是制造业中广泛应用的一种金属成形加工方式,它通过在金属材料表面施加压力,使其塑性变形,以达到所需的工艺和形状。
在冲压工艺中,模具的设计和制造是至关重要的一环。
因此,掌握冲压工艺及模具设计知识要点,对于提高冲压制造技术水平、提高产品质量和降低成本具有重要意义。
下面,将结合实际生产实践,总结一些关于冲压工艺及模具设计的知识要点。
一、冲压工艺的基本要素1.材料选择:冲压材料必须具备良好的塑性变形能力、疲劳寿命和均匀性,同时要满足在特定条件下的强度、硬度和耐磨性等要求。
2.模具设计:模具的设计必须充分考虑冲压材料的变形特性和受力条件,以及零件的加工要求和成本控制等因素。
模具的各个组成部分必须协调配合,且具备高精度、高刚度和耐用性等特点。
此外,模具的加工和装配需要注意细节化管理和工艺标准化。
3.加工工艺:冲压工艺过程需要严格控制各个工艺环节,特别是在模具定位、定量进料、开裂垫片等关键环节,需要特别加以关注。
此外,对于一些复杂形状或外观有要求的零件,可以考虑采用多道冲压或辅助模具等方式进行加工。
二、模具设计的基本原则1.要具备较好的适应性:模具应根据零件的形状、尺寸和材料特性等因素,合理选用模具结构类型和尺寸规格,以满足生产要求。
2.要具有高精度和稳定性:模具必须具备高精度、高刚性和高耐用性,以确保在大量生产过程中,始终保持稳定的加工质量。
3.要考虑冲压力分布均匀性:在模具设计时应充分考虑冲压时的力分布状况,特别是在切断底部的操作中,需要合理安排模具结构,使冲头的力能够均匀作用在零件的各个角落,避免切口不整齐等质量问题。
4.要注意保障安全性:模具设计时必须考虑操作安全和保护措施的设置,以避免操作工程师在工作中出现安全事故和模具损坏情况,同时还需要考虑环境保护和资源利用等问题。
三、模具加工工艺模具加工工艺是冲压工艺中的重要环节之一,是对模具设计的实际落地。
冲压工艺与模具设计课程设计
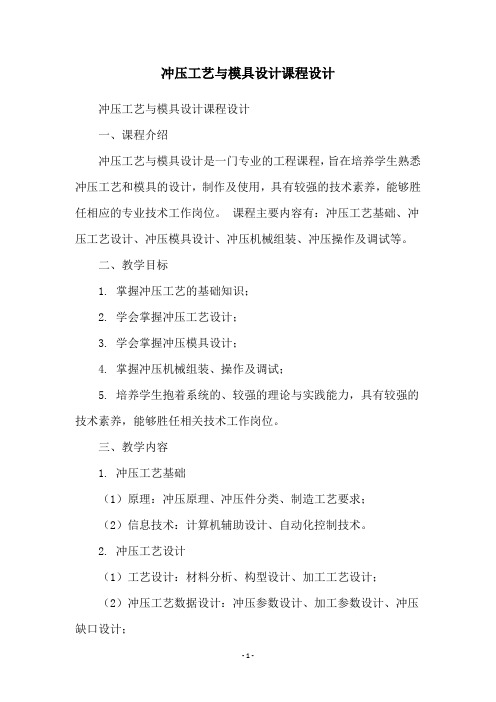
冲压工艺与模具设计课程设计冲压工艺与模具设计课程设计一、课程介绍冲压工艺与模具设计是一门专业的工程课程,旨在培养学生熟悉冲压工艺和模具的设计,制作及使用,具有较强的技术素养,能够胜任相应的专业技术工作岗位。
课程主要内容有:冲压工艺基础、冲压工艺设计、冲压模具设计、冲压机械组装、冲压操作及调试等。
二、教学目标1. 掌握冲压工艺的基础知识;2. 学会掌握冲压工艺设计;3. 学会掌握冲压模具设计;4. 掌握冲压机械组装、操作及调试;5. 培养学生抱着系统的、较强的理论与实践能力,具有较强的技术素养,能够胜任相关技术工作岗位。
三、教学内容1. 冲压工艺基础(1)原理:冲压原理、冲压件分类、制造工艺要求;(2)信息技术:计算机辅助设计、自动化控制技术。
2. 冲压工艺设计(1)工艺设计:材料分析、构型设计、加工工艺设计;(2)冲压工艺数据设计:冲压参数设计、加工参数设计、冲压缺口设计;(3)工艺过程设计:冲压过程设计、冲压加工组合设计。
3. 冲压模具设计(1)模具结构特性及原理:模具种类、模具结构特性、模具加工技术;(2)模具外形设计:模具尺寸设计、模具外形设计、模具开模方式设计;(3)模具细部设计:模具夹具设计、模具油道设计、模具放料口设计。
4. 冲压机械组装、操作及调试(1)机械组装:机床部件安装、工作台安装、冲程控制装置安装;(2)机械操作:调整冲程、挤压调节、调整冲头;(3)机械调试:机械功能调试、挤压参数调试、冲头快速调试。
四、教学安排本课程为2学期,每周3个小时,36学时。
主要采取实验操作和讨论报告的方式,在实验中锻炼学生的实践能力,在讨论中增强学生的专业综合能力。
五、教学考核及格考核和综合考核:成绩由实验操作50%、讨论报告50%组成。
冲压工艺及模具设计

冲压工艺及模具设计冲压工艺及模具设计是现代工业制造中常用的一种技术,它通过将金属板材或者其他形状的金属件置于模具中,然后通过冲压机的动作使得金属材料发生塑性变形以得到所需的形状和尺寸。
冲压工艺及模具设计是一门综合性强的工艺技术,以下将介绍其包括冲压工艺流程、模具设计原则、模具结构设计、模具构件选用等相关内容。
一、冲压工艺流程冲压工艺分为单道冲压和多道冲压两种。
单道冲压是指在一个冲压过程中完成产品的全体造型,多道冲压是指通过多次冲压工艺来完成产品的全体造型。
下面将以多道冲压为例介绍冲压工艺流程。
1.材料准备:选择合适的板材材料,进行剪切、铺料等准备工作。
2.模具设计:根据产品的形状和尺寸要求,设计合适的冲压模具。
3.上料:将材料板厚按照模具规格要求剪切成对应尺寸,然后放置在模具上。
4.开模:通过冲压机的动作,使得模具上的凸模与凹模对压,使材料发生塑性变形。
5.去杂及模具保养:在冲压过程中会产生一些杂质,需要及时清理,并对模具进行保养和维护。
二、模具设计原则模具设计是冲压工艺的核心环节,它直接影响着产品的质量和成本。
在进行模具设计时,需要遵循以下原则:1.合理性原则:模具结构要合理,能够满足产品的形状和尺寸要求,并且易于加工和调整。
2.稳定性原则:模具要具有足够的刚性和稳定性,能够承受冲压机的冲击力和振动。
3.高效原则:模具设计要考虑工作效率,设计出能够实现快速冲压的模具结构。
4.经济原则:模具的设计和制造成本要较低,以降低产品的制造成本。
三、模具结构设计模具的结构设计是模具设计的重要环节,它包括模具的整体结构、分段结构、导向结构等。
下面将介绍常用的模具结构设计方法:1.整体结构设计:将模具设计为一个整体结构,具有较好的刚性和稳定性。
2.分段结构设计:根据产品的形状和尺寸要求,将模具分为多个部分,通过连接件进行连接。
3.导向结构设计:模具需要具有良好的导向性,避免材料在冲压过程中发生歪斜和偏移。
4.其他辅助结构设计:模具还需要考虑各种辅助结构,如剪断边缘结构、定位结构、脱模结构等。
冲压工艺与模具设计ppt课件
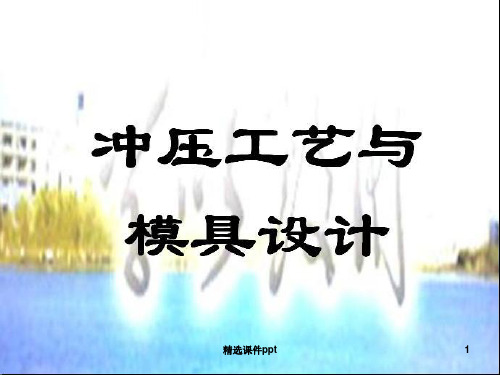
(7)大量生产时,产品成本低。
精选课件ppt
24
由此可见,冲压能集优质、高效、低能耗、 低成本于一身,这是其它加工方法无法与之相比拟的,
因此冲压的应用十分广泛,如汽车,拖拉机行业中,冲压 件占60%~70%,仪器仪表占到60~70%,还有日常生活中的 各种不锈钢餐具等等。从精细的电子元件,仪表指针到重 型汽车的覆盖件和大梁以及飞机蒙皮等均需冲压加工。
29
分离工序示意
D
D
D
落料
D
剪切
有分离现象发生,但不
改变空间形状
精选课件ppt
30
表1-1 分离工序
精选课件ppt
31
表1-1 分离工序(续)
精选课件ppt
32
(2)成形工序
冲压成形时,被加工材料在外力作用下,变形区材料所受 到的等效应力达到材料的屈服极限σs,但未达到强度极限σb, 使材料只产生塑性变形,从而得到一定形状和尺寸的零件。成 形工序主要有弯曲、拉深、翻孔、缩口、胀形等。
精选课件ppt
28
1.2 冲压工艺分类
1.按变形性质分类
➢分离工序 ➢成形工序
(1)分离工序
冲压成形时,被加工材料在外力作用下产生变形,当变 形区材料受到的剪切应力达到材料的抗剪强度,材料便产生 剪切而分离,从而形成一定形状和尺寸的零件。分离工序主 要有剪裁、冲孔、落料、切口、剖切等。
精选课件ppt
精选课件ppt
27
总之,模具工业是 一个国家的基础工业,模具设计与模 具制造水平的高低已成为衡量一个国家产品制造水平的高低。
发达国家非常重视模具的发展,日本认为:“模具就是进 入富裕社会的原动力”;德国:“金属加工业中的帝王”;罗 马尼亚:“模具就是黄金”;模具在国际上被认为是点石成金 的行业。不过这里的模具还包括塑模、锻模、压铸模、橡胶模、 食品模、建材模等等,但目前以冷冲模和塑料模的应用最广, 各占40%左右。
冲压工艺与模具设计
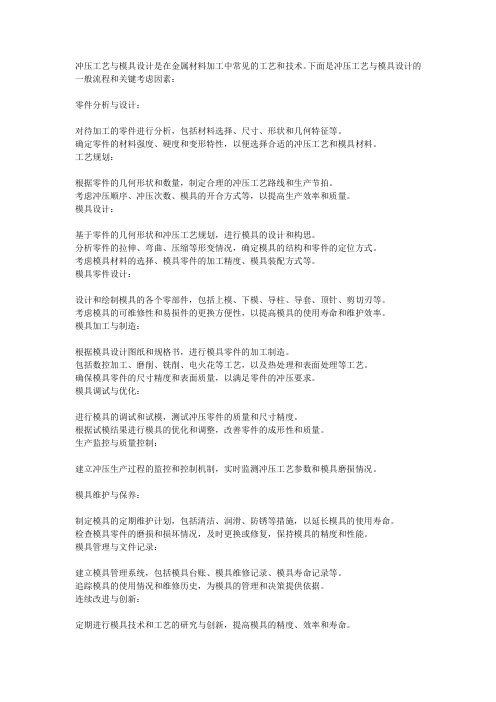
冲压工艺与模具设计是在金属材料加工中常见的工艺和技术。
下面是冲压工艺与模具设计的一般流程和关键考虑因素:零件分析与设计:对待加工的零件进行分析,包括材料选择、尺寸、形状和几何特征等。
确定零件的材料强度、硬度和变形特性,以便选择合适的冲压工艺和模具材料。
工艺规划:根据零件的几何形状和数量,制定合理的冲压工艺路线和生产节拍。
考虑冲压顺序、冲压次数、模具的开合方式等,以提高生产效率和质量。
模具设计:基于零件的几何形状和冲压工艺规划,进行模具的设计和构思。
分析零件的拉伸、弯曲、压缩等形变情况,确定模具的结构和零件的定位方式。
考虑模具材料的选择、模具零件的加工精度、模具装配方式等。
模具零件设计:设计和绘制模具的各个零部件,包括上模、下模、导柱、导套、顶针、剪切刃等。
考虑模具的可维修性和易损件的更换方便性,以提高模具的使用寿命和维护效率。
模具加工与制造:根据模具设计图纸和规格书,进行模具零件的加工制造。
包括数控加工、磨削、铣削、电火花等工艺,以及热处理和表面处理等工艺。
确保模具零件的尺寸精度和表面质量,以满足零件的冲压要求。
模具调试与优化:进行模具的调试和试模,测试冲压零件的质量和尺寸精度。
根据试模结果进行模具的优化和调整,改善零件的成形性和质量。
生产监控与质量控制:建立冲压生产过程的监控和控制机制,实时监测冲压工艺参数和模具磨损情况。
模具维护与保养:制定模具的定期维护计划,包括清洁、润滑、防锈等措施,以延长模具的使用寿命。
检查模具零件的磨损和损坏情况,及时更换或修复,保持模具的精度和性能。
模具管理与文件记录:建立模具管理系统,包括模具台账、模具维修记录、模具寿命记录等。
追踪模具的使用情况和维修历史,为模具的管理和决策提供依据。
连续改进与创新:定期进行模具技术和工艺的研究与创新,提高模具的精度、效率和寿命。
分析生产过程中的问题和不良品情况,提出改进措施,并进行试验验证。
在冲压工艺与模具设计过程中,需要综合考虑零件的形状复杂度、批量要求、成本效益等因素,确保模具的精度和稳定性,以实现高质量和高效率的生产。
冲压工艺与模具设计

冲压工艺与模具设计冲压工艺是一种通过对金属板材进行压制或冲剪,以改变其形状和尺寸的制造工艺。
在冲压过程中,需要使用模具来对金属板材施加确定的压力,使其发生塑性变形。
模具设计是冲压工艺的关键环节,合理的模具设计可以保证冲压过程的精度和效率。
一、金属材料的选择冲压工艺中常用的金属材料有钢板、铝板、铜板等。
不同金属材料的机械性能和加工性能不同,选择合适的金属材料对冲压工艺的成功至关重要。
二、冲压工艺的确定冲压工艺主要包括件的外形确定、孔位置的布置、切缘的设计等。
通过工艺确定,可以确定冲压工序的顺序、模具的需求以及操作要求。
三、模具设计要点1.模具结构的设计:模具结构设计要满足零件的加工要求,并在生产中方便拆卸、更换。
2.模具材料的选择:模具材料需要具有较高的硬度、强度和耐磨性,常用的模具材料有合金工具钢、硬质合金等。
3.模具配套设备的选择:根据冲压工艺的要求,选择合适的配套设备,如冲压机等。
4.压力分布的设计:模具在冲压过程中需要对板材施加一定的压力,合理的压力分布可以避免产生变形和裂纹。
5.模具的预紧力设计:预紧力是指模具在冲压过程中需承受的力量,需要合理设置预紧力以保证冲压过程的稳定性和精度。
6.附件的设计:模具附件是模具的辅助部件,如导向柱、定位销等,合理的设计可以提高模具的使用寿命和加工效率。
7.考虑模具的便于制造性和可维护性:在模具设计中,需要考虑到模具的制造难度和维护难度,合理的设计可以降低成本和提高效率。
总之,冲压工艺与模具设计是密不可分的,合理的模具设计可以保证冲压过程的精度和效率,最终提高产品的质量和生产效益。
在进行冲压工艺与模具设计时,需要考虑金属材料的选择、工艺的确定以及模具结构、材料等方面的要点。
只有全面考虑这些因素,才能设计出合理、高效的模具,实现优质的冲压加工。
冲压工艺及模具设计经典教材-冲压工艺及模具设计

数控压力机冲裁方式
(7) 模柄孔尺寸 模柄直径应略小于滑块内模柄安装孔的直径 。模柄的长度应小于模柄孔的深度。
(8) 压力机电动机功率 压力机电动机功率应大于冲压时所需 要的功率。
1.2.3 其他常用压力机简 介
(1) 偏心压力机 曲轴压力机的滑块行 程不能改变 ,而偏心 压力机的滑块行程是
可变的。 偏心压力机和曲
离合器
(3) 离合器 离合器是用来接通或断开大齿轮— 曲轴的运动 传递的机构 , 即控制滑块是否产生冲压动作, 由操作者操 纵 ,如图1.4所示。
制动 器
(4) 制动器 制动器是确保离合器脱开时 ,滑块比较准确地停止在曲 轴转动的上死点位置。 制动器的工作原理是 ,利用制动轮对旋转中心的偏心 ,使制动带对 制动轮的摩擦力随转动而变化来实现制动 。当曲轴转到上死点时 , 制动轮中心和固定销中心之间的中心距达到最大 。此时 ,制动带的 张紧力就最大 ,从而在此处产生制动作用 。转过此位置后 ,制动带 放松 ,制动器则不制动 。制动力的大小可通过调节拉紧弹簧来实现 。如图1.5所示。
(1)公称压力
压力机滑块 通过模具在 冲压过程中 产生的压力 就是压力机 工作压力。
2. (2) 滑块行 程 滑块行 程是指滑块 从上止点移 动到下止点 的距离。
3. (3) 滑块每 分钟冲压次 数。
1.2.2 曲柄压力机的主要技术参 数
压力机装模高度
(4) 压力机装模高度 压力机的装模高度是指滑块移动到下死点 时 ,滑块底平面到工作台垫板上平面的高度。
第1章 概 述
冷冲压加工概述
(1) 冲裁 使板料分离来获得制件的工序。 (2) 弯曲 使板料由平变弯来获得制件的工序 。 (3) 拉深 使平板料变成开口壳体制件的工序。 (4) 成形 使板料或其他形状的半成品的局部产 生凸凹变形的工序。
- 1、下载文档前请自行甄别文档内容的完整性,平台不提供额外的编辑、内容补充、找答案等附加服务。
- 2、"仅部分预览"的文档,不可在线预览部分如存在完整性等问题,可反馈申请退款(可完整预览的文档不适用该条件!)。
- 3、如文档侵犯您的权益,请联系客服反馈,我们会尽快为您处理(人工客服工作时间:9:00-18:30)。
冲压模具成型工艺及模具设计设计课题:工件如下图所示,材料Q235,板料厚度1mm,年产量8万件,表面不允许有明显的划痕。
设计成型零件的模具。
技术要求:未注圆角为R1;未注公差为IT14级;材料厚度t=1mm 一、冲压工艺分析1、该零件的材料是Q235,是普通的碳素工具钢,板厚为1mm,具有良好的可冲压性能。
2、该零件结构简单,并在转角处有R1的圆角,所冲的三个孔都是Φ5的尺寸,工艺性比较好,整个工件的结构工艺性好。
3、尺寸精度,零件上的三个孔的尺寸精度为IT12~13级,三个孔的位置精度是IT11~12级,其余尺寸的公差为IT12~14,精度比较低。
结论:适合冲压生产。
二、工艺方案确定该工件包括落料、冲孔两个基本工序,有以下3种工艺方案:方案一:先落料,后冲孔。
采用单工序模具生产。
方案二:落料—冲孔复合冲压,采用复合模生产。
方案三:冲孔—落料级进冲压,采用级进模生产。
方案一模具结构简单,但需要两道工序两幅模具,成本高而生产率低,难以满足中批量生产需求。
方案二只需一副模具,工件精度及生产效率都较高。
方案三也只需要一副模具,生产效率高,操作方便,但位置精度不如复合模具冲裁精度高。
通过对上述三种方案的分析比较,成型该零件应该采用方案二复合模具成型。
三、确定模具类型及结构形式1、该零件质量要求不高,板的厚度有1mm, 孔边距有6mm,所以可以选用倒装复合模。
2、定位方式的选择:控制条料的送进方向采用两个导料销,控制条料的送进步距采用挡料销。
3、卸料、出件方式的选择:采用弹性卸料。
下出件,上模刚性顶件。
4、导向方式的选择:为了方便操作,该模具采用后侧导柱的导向方式。
冲压件的形状简单、精度要求不高、生产批量为中批量,为了使得模具寿命较高,采用有导向、弹性卸料、下出件的模具结构形式。
四、工艺计算1、确定最佳排样方式,并计算材料利用率,选择板料规格。
该零件为近似矩形零件,设计排样1、排样2三种排样方式,如图:排样1:排样2::查《冲压手册》表2-18,最小搭边值是:工件间:1.5mm、侧边:2.0mm。
工件面积:s=60×26-8×10×2-3×3.14×2.5×2.5=1341mm2排样1:取搭边值2mm条料宽度B=30mm 步距L=62mm材料利用率:η=1341/(30×62)=72.1%排样2:取搭边值2mm条料宽度B=64mm 步距L=28mm材料利用率:η=1341/(64×28)=74.8%比较两种排样方式,第二种排样方式材料利用率较高,所以冲裁工件的排样方式可以采用排样2排列方式。
排样图如下选用1mm×900mm×1200mm的板料,可以裁14条,每一条可以冲42件。
总的材料利用率:14×42×1341/(900×1200)=73.1%2、计算冲床合力并预选冲床L=(212+47.1)=259.1mm t=1mm σb=450Mpa冲压力F=Ltσb=(212+47.1)×1×450=95.4+21.2=116.6KN查《冲压工艺及模具设计》表3-11 K卸=0.05 K推=0.055 K顶=0.06卸料力:F卸=K卸×F落料=95.4×0.05=4.77kN倒装复合模:顶件力等于零推件力:刃口高度为10 n=8/1 n取8F推=K推×F冲孔×8=0.055×21.2×8=9.33kN冲压合力F合=F+F卸+F推=9.33+4.77+116.6=130.6KN根据冲压合力预选J23—16的曲柄压力机3、确定冲裁压力中心(计算时忽略R1)如图所示因为关于Y轴对称所以X=0Y1=Y14=0 Y2=Y13 =13 Y3=Y7=Y8 = Y11 =26 Y4=Y6=Y9 =Y11=21Y5=Y10 =16Y0=(0x30+13x26+26x12x2+26x20x4+4x21x10+16x8x2+20x3.14x5+3..14x5)/.259.1=10..94 取X0=0 Y0=10.94作为模具压力中心的位置4、确定冲裁凸模和凹模的工作刃口尺寸落料以落料凹模为基准计算,落料凸模根据凹模和最小间隙计算,也可以根据凹模实际尺寸和间隙配制。
冲孔以冲孔凸模为基准计算、冲孔凹模根据凸模合最小间隙计算,也可以根据凸模实际尺寸和间隙值配制。
冲孔用分别加工法进行计算,落料、中心尺寸用配合加工法进行计算。
间隙值查《冲压工艺及模具设计》表3-4,Zmin=0.100mm Zmax=0.140mm落料凹模磨损后变大尺寸:6074.0-,2652.0-,1227.0-,8±0.1,63.0-磨损系数查《冲压工艺及模具设计》表3-5A1=(60-0.5x0.74)0185.0=59.63185.0(X1=0.5)A2=(26-0.5x0.52)13.0=25.7413.0A3=(12-0.75x0.27)0675.0=11.1980675.0(X3=0.75)A4=(6 -0.75x0.3)075.0=5.775075.0(X4=0.75)A5=(8 -0.75x0.2)05.0=7.8505.0(X5=0.75)A4,A5尺寸要标注在凸凹模上,所以要转化到凸凹模尺寸A4凸凹模==(公差:Zmax-Zmin-0.2/4=-0.065)=5.675065.0-A4凸凹模==(公差:Zmax-Zmin-0.2/4=-0.09)=7.7509.0-落料凹模磨损后变小尺寸:822.0-磨损系数查《冲压工艺及模具设计》表3-5 X=0.75B 1=(8+0.75x0.22)055.00-=8.165055.00-落料凹模磨损后不变尺寸:45±0.125、1022.00-C 1=45±0.125/4=45±0.03125 C 2=(10-0.5x0.22)±0.22/8=9.89±0.0275落料凸模(凸模固定板)按凹模实际尺寸配做,保证间隙0.100~0.140mm 冲孔凸模磨损后变小尺寸: 公差为IT12~IT13级凸、凹模公差按IT8级,Z max =0.140 Z min =0.100 δ凸模=0.018mm δ凹模=0.018mm校核间隙|δ凸模|+|δ凹模|=0.018+0.018=0.036<Zmax-Zmin=0.040可行磨损系数查《冲压工艺及模具设计》表3-5 X=0.75B 1凸模==(5+0.75x0.12)18.00-=5.0918.00-B 1凹模==(5.09+0.1)018.0=5.19018.05、确定弹性元件 聚氨酯橡皮允许承受的载荷较弹簧大,并且安装方便,所以选用橡皮。
卸料力为F 卸=4.77kN橡皮的高度:H 自由=H 工作/(0.25~0.3)=26.7~32 取30式中H 工作=t+1+H 修磨=1+1+6=8橡皮的面积:A=F 卸/p=9540~18346mm 2式中p 为橡皮预压(压10%~15% H 自由)时单位面积上的压力,取0.26~0.5取一块整开凸模孔的合四个卸料螺钉孔160×160×30的聚氨酯橡皮.面积校核:160×160-2768-452=22380mm2>8540mm2 可行五、编写工艺文件冲压工艺过程卡材料牌号及规格材料技术要求毛坯尺寸每件毛坯可制件数毛坯重量辅助材料Q235[1(±0.1)×900×1200]条料[1×64×1200]42工序号工序名称工序内容加工简图设备工艺装备0 下料剪板机上裁板64×12001 落料冲孔落料冲孔复合冲裁J23-16落料冲孔复合模六、选择和确定模具主要零部件的结构和尺寸1、工作零件的结构及尺寸设计(1)凸凹模:为了便于加工,凸凹模设计成直通式,1个M8沉头螺钉固定在垫板上,与凸凹模固定板的配合按H7/m6。
其总长L=H固定板+H卸料板+(H橡胶-H预压)=18+14+(30-2)=60mm(2)冲孔凸模:冲孔凸模采用台阶式的,与凸模固定板的配合按H7/m6.其总长H=H固定板+H凹模+H空心垫板=50mm,小端长32mm;(3)凹模采用薄凹模结构,薄凹模厚度尺寸(可以参考单工序模具凹模的厚度计算公式H=Ks=62×0.22=13.64mm)取14mm。
凹模壁厚尺寸C=(1.5~2)H=30~40mm式中K查《冲压工艺及模具设计》表3-15 取0.22 s=62mm凹模板边长:B≥28+2×(30~40)=88~108L≥62+2×(30~40)=122~142L取160,一般情况下,B≧L,所以B取160,故薄凹模板长、宽、厚度尺寸160mm×160mm×16mm(4)模具刚性校核凸凹模尺寸较大,模具强度较大,所以不需要校核,小凸模:单个凸模所受力:冲裁力:21.2/2=10.6kN;推件力(倒装复合模)9.33/2=4.66kN冲压合力:倒装:10.6+4.66=15.3kN无导向:L=19.2 mm 可行2、其他板的尺寸[参考典型组合结构(GB2858.2-81)]凸凹模垫板:160×160×8凸凹模固定板:160×160×18卸料板:160×160×14空心垫板:160×160×16小凸模固定板:160×160×20小凸模垫板:160×160×83、模架规格上模座的规格:160×160×40下模座的规格:160×160×45模柄的规格:A50×100导套:A28H7×90×38导柱:A28h6×1504、模具闭合高度40+8+60+45+16+16+20+8-1=212mm七、校核所选压力机J23-16压力机:标称压力160KN;滑块行程55(次/分);连杆调节长度45mm;最大装模高度220mm,工作台尺寸300mm×450mm,模柄孔尺寸φ30×50;电机功率1.5kw。
校核以上所有参数,可满足使用要求。
使用J23-16能满足该模具使用要求。
八、编制工作零件机械加工工艺卡凹模机械加工工艺规程卡凹模机械加工工艺规程材料Cr12 硬度60~64HRC 序号工序名称工序内容1 备料锻件(退火状态)165×165×182 粗铣铣六面到尺寸160.3×160.3×17。