冲压工艺与模具设计实例分解
冲压磨具结构设计的实例解析学习成功案例提升自己

冲压磨具结构设计的实例解析学习成功案例提升自己冲压磨具在工业制造领域中扮演着重要角色,其结构设计的合理与否直接影响产品的质量和生产效率。
本文将通过一个成功案例的实例解析,探讨冲压磨具结构设计的关键要点,以提升读者自己在这一领域的专业能力。
一、案例背景分析某汽车制造公司在冲压生产过程中遇到了困扰多时的问题——冲裁加工时模具频繁易损坏,导致生产效率低下、成本高昂。
经过对问题的深入调研和分析,决定对冲压磨具的结构设计进行优化,以提高磨具的使用寿命和生产效率。
二、案例分析与解决方案该汽车制造公司对原有的冲压磨具结构进行了全面评估,并根据实际需求进行改进。
以下是该案例中的几个关键问题及其解决方案。
1. 冲压磨具材料选择原有的冲压磨具使用的材料强度不足,容易出现损坏现象。
为了解决这个问题,公司选择了一种更坚固耐用的合金钢材料,以增强磨具的耐用性和抗压能力。
2. 磨具结构优化通过对现有冲压磨具结构的深入分析,公司发现存在磨具结构复杂、加工独特等问题。
为了降低制造成本和提高生产效率,公司对原有结构进行了简化并优化流程。
他们采用了模块化的设计思路,通过设置可更换的零部件,提高了磨具的可维护性和灵活性。
3. 表面涂层技术应用为了进一步提升冲压磨具的使用寿命,该公司引入了表面涂层技术。
他们选取了合适的材料和涂层工艺,使冲压磨具表面形成了一层坚硬的保护膜,提高了其抗磨损和防腐蚀能力。
4. 冲裁动力系统升级经过对冲裁动力系统的分析,公司发现原有的动力输入方式存在一定的缺陷。
为了解决这个问题,他们采用了一种先进的液压传动系统,提高了冲压磨具的工作效率和精度。
三、成功案例的启示与学习通过这个成功案例的解析,我们可以得到一些关于冲压磨具结构设计的启示,并从中学习以提升自己。
1. 深入分析问题根源在解决冲压磨具结构设计问题时,我们首先要深入分析问题的根源,找出造成问题的原因。
只有找准问题所在,才能采取针对性的解决方案。
2. 结构优化与标准化冲压磨具结构设计的优化与标准化是提高生产效率和产品质量的关键。
冲压工艺与模具设计实例

冲压工艺与模具设计实例冲压工艺是一种通过对金属材料施加力量,使其通过模具形成所需要的形状的加工工艺。
冲压工艺在制造业中广泛应用,它可以生产各种金属零件,包括汽车零件、家电零件、电子产品外壳等。
下面是一个冲压工艺与模具设计的实例。
以汽车车门锁模具的设计为例,首先需要确定车门锁的设计要求,包括形状、尺寸、材料等。
然后进行模具的设计。
模具的设计分为上模和下模。
上模是用于将金属材料推入下模,并通过压力将材料压制成所需形状的部分。
下模是用于接收金属材料的零件,并承受压力以及塑性变形的部分。
在设计上模时,首先需要绘制车门锁的三维模型。
然后,根据所需形状和尺寸,进行刀具路径规划和切削力分析,确定上模的几何形状和结构。
在设计下模时,首先需要根据上模的几何形状绘制下模的轮廓。
然后,根据下模的结构要求,确定下模的结构件、导向件和固定件,并进行设计。
在模具设计过程中,还需要考虑材料的选择和热处理工艺。
根据车门锁的材料特性和所需强度要求,选择合适的模具材料,并进行热处理以提高模具的硬度和耐磨性。
在具体生产过程中,首先将金属材料放置在冲床上,并将模具安装在冲床上。
然后,通过冲击力将金属材料推入上模中,经过压力和塑性变形,使材料形成车门锁的形状。
最后,将成品从模具中取出,进行后续加工和组装。
通过冲压工艺和模具设计,可以高效地生产出符合要求的汽车车门锁。
冲压工艺具有生产效率高、质量稳定、成本低等优点,因此在制造业中得到广泛应用。
模具设计是冲压工艺的重要环节,合理设计的模具可以提高生产效率和产品质量。
通过不断改进和优化模具设计,可以进一步提高冲压工艺的效率和质量。
冲压工艺与模具设计实例
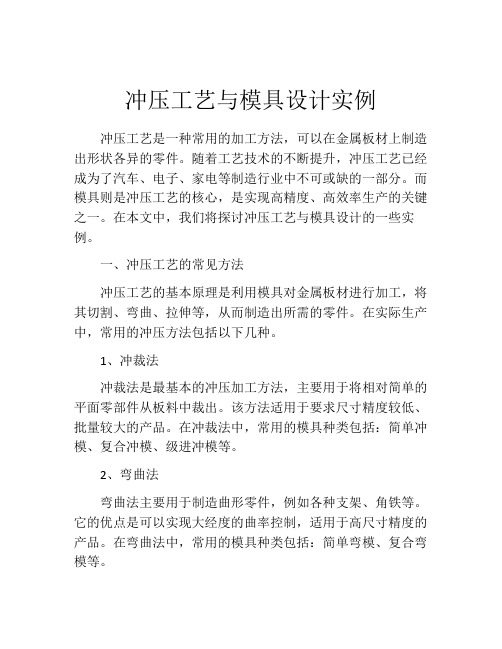
冲压工艺与模具设计实例冲压工艺是一种常用的加工方法,可以在金属板材上制造出形状各异的零件。
随着工艺技术的不断提升,冲压工艺已经成为了汽车、电子、家电等制造行业中不可或缺的一部分。
而模具则是冲压工艺的核心,是实现高精度、高效率生产的关键之一。
在本文中,我们将探讨冲压工艺与模具设计的一些实例。
一、冲压工艺的常见方法冲压工艺的基本原理是利用模具对金属板材进行加工,将其切割、弯曲、拉伸等,从而制造出所需的零件。
在实际生产中,常用的冲压方法包括以下几种。
1、冲裁法冲裁法是最基本的冲压加工方法,主要用于将相对简单的平面零部件从板料中裁出。
该方法适用于要求尺寸精度较低、批量较大的产品。
在冲裁法中,常用的模具种类包括:简单冲模、复合冲模、级进冲模等。
2、弯曲法弯曲法主要用于制造曲形零件,例如各种支架、角铁等。
它的优点是可以实现大经度的曲率控制,适用于高尺寸精度的产品。
在弯曲法中,常用的模具种类包括:简单弯模、复合弯模等。
3、拉伸法拉伸法是一种将板材拉伸成型的方法,适用于制造拉伸高度较大的零部件。
它的优点是可以制造出复杂的形状,缺点则是对板材的性能有较高的要求。
在拉伸法中,常用的模具种类包括:简单拉伸模、复合拉伸模等。
二、模具设计的注意事项模具的设计是冲压工艺中十分重要的步骤,它直接决定了产品的精度和品质。
在模具设计的过程中,需要注意以下几点。
1、材料选择模具的主要材料应该是坚固、耐磨的合金钢,以保证模具的使用寿命。
在选择材料时,还需要考虑到生产成本、耐腐蚀性和加工性能等因素。
2、结构设计模具的结构设计应该符合产品的形状尺寸,能够保证加工精度和产品品质。
模具的设计需要考虑到成型力度、冲孔位置、冲孔大小等因素。
3、表面处理为了防止磨损和腐蚀,在模具表面需要采用一定的表面处理方式。
常用的表面处理方式包括渗碳、氮化、电化学抛光等。
三、模具设计实例为了更好地阐述模具设计的重要性,我们介绍一个手机机壳模具设计的实例。
手机机壳是一款外壳非常薄的产品,具有较高的尺寸精度和表面要求。
冲压工艺与模具设计实例

冲压工艺与模具设计实例首先,汽车门板是汽车外部的重要组成部分,其工艺要求较为严格,所以在生产过程中需要采用冲压工艺来完成。
在进行冲压工艺设计时,首先需要根据门板的设计要求确定其尺寸、形状和材质。
然后根据这些参数来确定冲压工艺的具体流程和步骤,包括拉伸、冲裁、弯曲等。
接下来是模具设计。
模具设计是冲压工艺中非常重要的一环,其质量和精度直接影响到产出产品的质量和成本。
在进行模具设计时,首先需要根据门板的形状和工艺要求来确定模具的结构和尺寸。
然后根据这些参数来设计模具的具体形状和结构,包括上模、下模、剪切模、冲压模等。
在完成模具设计后,需要进行模具加工和调试。
模具加工是指根据设计图纸来制作模具的具体零部件,包括机加工、热处理、组装等。
而模具调试是指在完成模具加工后,需要对模具进行调试和试验,以确保其能够满足冲压工艺的要求。
最后,经过上述步骤,我们就可以将汽车门板的冲压工艺和模具设计完成。
这样一来,我们就可以通过冲压工艺来生产出符合设计要求的汽车门板,从而满足市场需求并获得经济效益。
这也充分体现了冲压工艺与模具设计在制造业中的重要性和应用价值。
冲压工艺与模具设计在汽车制造中的应用非常广泛,因为许多汽车零部件都需要使用冲压工艺来生产,其中汽车车门板就是一个非常典型的例子。
通过冲压工艺,可以使车门板具有良好的强度和表面质量,并且可以大大提高生产效率。
接下来我们将深入探讨汽车门板的冲压工艺与模具设计的相关内容。
首先我们要了解汽车门板的冲压工艺。
汽车门板常常采用多工序冲压工艺来完成,主要包括拉伸、冲裁、弯曲等工序。
在进行冲压工艺设计时,需要充分考虑材料的特性和板料的变形规律。
比如在进行拉伸工序时,需要注意材料的延展性和变形能力,确保拉伸后的板料能够满足设计要求。
在冲裁工序中,需要考虑板料的裁剪力和裁剪形状,以及切边拉伸等问题。
在弯曲工序中,需要考虑板料的抗弯性能和成形效果等因素。
只有理解和掌握了这些特性,才能够设计出合理的冲压工艺流程。
冲 压 工 艺 设 计 及 案 例 分 析

如 分 离 工 序 中 的 冲 孔 、 落 料 、 切边 , 成 形 工 序 中 的 弯 曲、翻边、拉深等。工序性质的确定主要取决于冲压 件 的 结 构 形 状 、 尺寸 精 度 , 同 时 需 要 考 虑 工 件 的 变 形 性 质和具体的生产条件。 • 工序性质的确定,应遵循以下原则。
上一页 下一页 返回
学习单元一 工艺方案的制定
• 2) 工 序 性 质 应 保 证 变 形 区 为 弱 区 • 弱 区 : 是 指 变 形 抗 力 小 的 区 域 , 根 据 阻 力 最 小 定 律 ,应
使 变 形 区 为 弱 区 , 以 达 到 变 形 容易 , 同 时 又 保 证 不 变 形 区的相对稳定。 • 如 图 8-2 所 示 的 起 伏 件 , 若 外 形 有 效 尺 寸 D 很 大 , 则 平 板 外 圈 部 分 与 所 要 胀 出 的 凸 起内 圈 相 比 强 弱 明 显 , 起 伏时外缘就不会发生收缩变形。若D很小,则不能保 证 不 变 形 区 的稳 定 , 只 好 改 变 工 序 性 质 。 • 有时变形区与非变形区强弱对比不明显,为了使变形 区 为 弱 区 , 就 需 要 增 加 工 序 。 如图 8-3 所 示 的 冲 压 件 , 外 径 尺 寸 是 100 mm, 翻 边 时 产 生 收 缩 变 形 。 当 改 为 115 mm 时 ,翻 边 时 外 径 不 再 收 缩 , 最 后 切 边 保 证 外 径 尺 寸 100 mm, 切 边 工 序 就 是 附 加 的 工 序。
• 3) 工 序 性 质 应 保 证 零 件 的 质 量 • 冲压件的几何形状或尺寸精度要求较高时,必须增加
校 形 工 序 或 其 他 工 序 。例 如 , 如 图 8-3 所 示 , 若 竖 边 的 厚 度 不 允 许 变 薄 , 就 不 能 采 用 翻 边 工 序 。 又 如 图 8- 5所 示 的 平 板 压 筋 件 , 由 于 筋 离 平 板 边 缘 很 近 , 将 使 压 筋 变 形 不 均 匀 , 制 件 产 生 较 大 的 翘 曲 或皱 折 , 因 而 必 须 增加拉深工序,提高制件周边的刚度后再压筋,压筋 后 则 需 修 边 。 这 里 拉 深和 修 边 工 序 便 是 保 证 零 件 质 量 而 增加的工序。
冲压工艺案例分析讲解
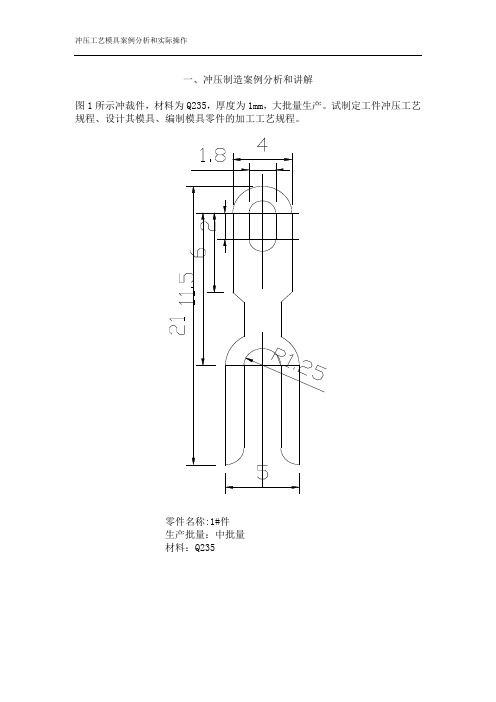
一、冲压制造案例分析和讲解图1所示冲裁件,材料为Q235,厚度为1mm,大批量生产。
试制定工件冲压工艺规程、设计其模具、编制模具零件的加工工艺规程。
零件名称:1#件生产批量:中批量材料:Q235一、冲压件工艺分析2. 工艺方案及模具结构类型3. 排样设计4.冲压力与压力中心计算工件如图找到坐标计算得24*12+60*0+24*12+14.5*24+38.6*27.97+14.5*24+31.4*12+31.4*12Y= ——————————————————————————————=2.5 24+60+24+14.5+38.5+14.5+34.1+31.4X=8.35.工作零件刃口尺寸计算落料部分以落料凹模为基准计算 ,落料凸模按间隙值配制;冲孔部分以冲孔凸模为基准计算,冲孔凹模按间隙值配制。
既以落料凹模、冲孔凸模为基准,凸凹模按间隙值配制。
刃口尺寸计算见表1。
表 1 刃口尺寸计算6.工作零件结构尺寸7.其它模具零件结构尺寸根据倒装复合模形式特点: 凹模板尺寸并查标准JB/T-6743.1-94,确定其它模具模板尺寸列于表2:根据模具零件结构尺寸 ,查标准GB/T2855.5-90选取后侧导柱125×25标准模架一副。
8.冲床选用根据总冲压力 F总=352KN,模具闭合高度,冲床工作台面尺寸等,并结合现有设备,选用J23-63开式双柱可倾冲床,并在工作台面上备制垫块。
其主要工艺参数如下:公称压力:1630KN滑块行程: 120mm行程次数: 60 次∕分最大闭合高度: 140mm连杆调节长度: 50mm工作台尺寸(前后×左右): 63*639.冲压工艺规程切料63*25的板料排样图设计10.模具总装配图图 4 模具装配图11.模具零件图上模座下模座凹模凸模垫板下模座板卸料板卸料螺钉挡料销螺钉导套凹模垫板1. 主要模具零件加工工艺过程落料凹模加工工艺过程材料 :Gr12 硬度 : 60 ~ 64 HRC冲孔凸模加工工艺过程材料: T10A 硬度: 56 ~ 60HRC凸凹模加工工艺过程材料 :Gr12 硬度 : 60 ~ 64 HRC凸模固定板加工工艺过程材料 :45# 硬度 : 24 ~ 28 HRC凸凹模固定板加工工艺过程材料 :45# 硬度 : 24 ~ 28 HRC卸料板加工工艺过程材料 :45# 硬度 : 24 ~ 28 HRC上垫板加工工艺过程材料 :T8A 硬度 : 54 ~ 58 HRC下垫板加工工艺过程材料 :T8A 硬度 : 54 ~ 58 HRC空心垫板加工工艺过程材料 :45# 硬度 : 24 ~ 28 HRC上模座加工工艺过程材料 :HT200下模座加工工艺过程材料: HT200推件块加工工艺过程材料 :45# 硬度 : 24 — 28 HRC2. 加工过程:详见素材资源库中的视频。
第九讲冲压模具设计实例分析
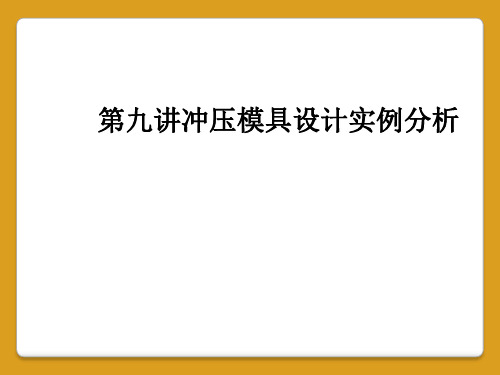
第八章 冲压模具结构及设计
9、模具的装配 根据级进模装配要点,选凹模作为装配基准件,先装下模,再装上模,并调整间隙、试冲、返修。
第八章 冲压模具结构及设计
二、拉深模设计与制造实例
零件名称:端盖 生产批量:大批量 材料:镀锌铁皮 材料厚度:1mm
第八章 冲压模具结构及设计
1、冲压件工艺性分析 冲压工序:落料、拉深; 材料:为镀锌铁皮,具有良好的拉深性能,适合拉深; 结构:简单对称; 精度:全部为自由公差,工件厚度变化也没有作要求,只是该工件作为另一零件的盖,口部尺寸 φ69可稍作小些。而工件总高度尺寸14mm可在拉深后采用修边达要求 。
第八章 冲压模具结构及设计
2、冲压工艺方案的确定 方案一:先落料,后拉深。采用单工序模生产。 方案二:落料-拉深复合冲压。采用复合模生产。 方案三:拉深级进冲压。采用级进模生产。 方案一:模具结构简单,但成本高而生产效率低; 方案二:生产效率较高,尽管模具结构较复杂,但因零件简单对称,模具制造并不困难; 方案三:生产效率高,但模具结构比较复杂,送进操作不方便,加之工件尺寸偏大。 结论:采用方案二为最佳工艺方案。
起粗定距的活动挡料销、弹簧和螺塞选用标准件,规格为8×16。
φ8mm导正销
第八章 冲压模具结构及设计
(3)导料板的设计 (4)卸料部件的设计
① 卸料板的设计 ②卸料螺钉的选用 (5)模架及其它零部件设计
第八章 冲压模具结构及设计
6、模具总装图(右图) 7、冲压设备的选定 8、模具零件加工工艺
模具关键零件因采用线切割,所以这些零件的加工 就变得相对简单。
第八章 冲压模具结构及设计
(4)冲压工序压力计算 拟采用正装复合模,固定卸料与刚性推件。 根据冲压工艺总力计算结果并结合工件高度,初选开式双柱可倾压力机J23-25。
冷冲压工艺制定及模具设计实例冲压与模具15640
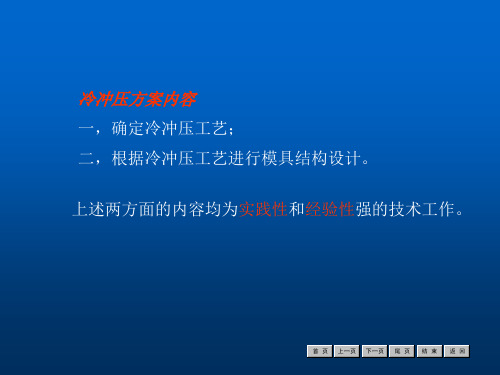
具体内容包括冲压工艺规程卡片(如表8-4所示)、冲 压工序卡片、工艺路线明细表等。在大批量生产中,需要 制定每个零件的工艺过程卡和工序卡;成批生产中,一般 需要制定工艺过程卡;小批量生产一般只需要填写工艺路 线明细表。
对于重要的冲压件工艺制定和模具设计,往往还需要 编制计算说明书。计算说明书的内容包括:1冲压件工艺性 分析;2毛坯尺寸计算;3排样及剪板;4工序次数及工序件 形状和尺寸;5工艺方案的技术、经济性分析比较;6模具 结构形式分析;7模具主要零件结构、材料、公差、技术要 求等;8凸、凹模工作部分尺寸与公差确定;9模具主要零 件强度计算、压力中心、弹性元件选用和核算;10设备类 型、吨位、主参数等。
主要根据确定的冲压工艺和冲压件形状特点、精度 要求、生产批量、模具加工条件、操作是否方便与安全 等要求,以及利用现有通用机械化、自动化装置的可能 性等,选定冲模类型及结构形式。
此外还需要进行必要的计算,包括模具零件强度计 算、压力中心计算、弹性元件选用和核算,再进行模具 总装配图设计、列出模具零件明细表,设计模具凸、凹 模等工作零件以及非标准零件的技术图纸。
8.1.2 分析冲压件的工艺性
汽车前大灯外壳
连接件
8.1.3 冲压工艺方案的确定
1.确定工序性质
翻边零件图
翻边件的工序安排
直接翻边成形
一次拉深成形:采用落料并冲Ф11孔、拉深、冲Ф23孔 的工艺方案,使凸缘保持为弱区,则可以一次拉深成形。
不能采用:落料、拉深、冲Ф23孔的工艺方案 。
变形减轻孔的应用
8.1.3 冲压工艺方案的确定
2.工序数的确定 3.工序顺序的确定
弯曲前冲孔
多孔拉深件拉深后冲孔
4.工序的合并
- 1、下载文档前请自行甄别文档内容的完整性,平台不提供额外的编辑、内容补充、找答案等附加服务。
- 2、"仅部分预览"的文档,不可在线预览部分如存在完整性等问题,可反馈申请退款(可完整预览的文档不适用该条件!)。
- 3、如文档侵犯您的权益,请联系客服反馈,我们会尽快为您处理(人工客服工作时间:9:00-18:30)。
第一节冲压工艺与模具设计的内容及步骤冲压工艺与模具设计是进行冲压生产的重要技术准备工作。
冲压工艺与模具设计应结合工厂的设备、人员等实际情况,从零件的质量、生产效率、生产成本、劳动强度、环境的保护以及生产的安全性各个方面综合考虑,选择和设计出技术先进、经济上合理、使用安全可靠的工艺方案和模具结构,以使冲压件的生产在保证达到设计图样上所提出的各项技术要求的基础上,尽可能降低冲压的工艺成本和保证安全生产。
一般来讲,设计的主要内容及步骤包括:⒈工艺设计(1) 零件及其冲压工艺性分析根据冲压件产品图,分析冲压件的形状特点、尺寸大小、精度要求、原材料尺寸规格和力学性能,并结合可供选用的冲压设备规格以及模具制造条件、生产批量等因素,分析零件的冲压工艺性。
良好的冲压工艺性应保证材料消耗少、工序数目少、占用设备数量少、模具结构简单而寿命高、产品质量稳定、操作简单。
(2) 确定工艺方案,主要工艺参数计算在冲压工艺性分析的基础上,找出工艺与模具设计的特点与难点,根据实际情况提出各种可能的冲压工艺方案,内容包括工序性质、工序数目、工序顺序及组合方式等。
有时同一种冲压零件也可能存在多个可行的冲压工艺方案,通常每种方案各有优缺点,应从产品质量、生产效率、设备占用情况、模具制造的难易程度和寿命高低、生产成本、操作方便与安全程度等方面进行综合分析、比较,确定出适合于现有生产条件的最佳方案。
此外,了解零件的作用及使用要求对零件冲压工艺与模具设计是有帮助的。
工艺参数指制定工艺方案所依据的数据,如各种成形系数(拉深系数、胀形系数等)、零件展开尺寸以及冲裁力、成形力等。
计算有两种情况,第一种是工艺参数可以计算得比较准确,如零件排样的材料利用率、冲裁压力中心、工件面积等;第二种是工艺参数只能作近似计算,如一般弯曲或拉深成形力、复杂零件坯料展开尺寸等,确定这类工艺参数一般是根据经验公式或图表进行粗略计算,有些需通过试验调整;有时甚至没有经验公式可以应用,或者因计算太繁杂以致于无法进行,如复杂模具零件的刚性或强度校核、复杂冲压零件成形力计算等,这种情况下一般只能凭经验进行估计。
(3) 选择冲压设备根据要完成的冲压工序性质和各种冲压设备的力能特点,考虑冲压加工所需的变形力、变形功及模具闭合高度和轮廓尺寸的大小等主要因素,结合工厂现有设备情况来合理选定设备类型和吨位。
常用冲压设备有曲柄压力机、液压机等,其中曲柄压力机应用最广。
冲裁类冲压工序多在曲柄压力机上进行,一般不用液压机;而成形类冲压工序可在曲柄压力机或液压机上进行。
⒉模具设计模具设计包括模具结构形式的选择与设计、模具结构参数计算、模具图绘制等内容。
(1) 模具结构形式的选择与设计根据拟定的工艺方案,考虑冲压件的形状特点、零件尺寸大小、精度要求、生产批量、模具加工条件、操作方便与安全的要求等选定与设计冲模结构形式。
(2) 模具结构参数计算确定模具结构形式后,需计算或校核模具结构上的有关参数,如模具工作部分(凸、凹模等)的几何尺寸、模具零件的强度与刚度、模具运动部件的运动参数、模具与设备之间的安装尺寸,选用和核算弹性元件等。
(3) 绘制模具图模具图是冲压工艺与模具设计结果的最终体现,一套完整的模具图应该包括模具和使用模具的完备信息。
模具图的绘制应该符合国家制定的制图标准,同时考虑模具行业的特殊要求与习惯。
模具图由总装图和非标准件的零件图组成。
总装配图主要反映整个模具各个零件之间的装配关系,应该对应绘制说明模具构造的投影图,主要是主视图和俯视图及必要的剖面、剖视图,并注明主要结构尺寸,如闭合高度、轮廓尺寸等。
习惯上俯视图由下模部分投影而得,同时在图纸的右上角绘出工件图、排样图,右下方列出模具零件的明细表,写明技术要求等。
零件图一般根据模具总装配图测绘,也应该有足够的投影各必要的剖面、剖视图以将零件结构表达清楚。
此外,要标注零件加工所需的所有结构尺寸、公差、表面粗糙度、热处理及其他技术要求。
对于一个完整的生产过程,冲压工艺与模具设计是密不可分的,二者相互联系,相互影响,因此前述督可能需要交叉、反复进行。
若方案有变化,则需重新进行设计计算。
⒊编写工艺文件及设计计算说明书为了规范生产,加强管理,每一种冲压产品的生产需写相应的工艺文件(如工序卡片)。
对零件冲压工艺和模具设计应编写设计计算说明书,以供日后查阅。
设计计算说明书应该包括冲压件的工艺分析以及模具设计的主要内容。
第二节冲压工艺与模具设计实例一、摩托车侧盖前支承冲压工艺设计图12-1所示为摩托车侧盖前支承零件示意图,材料Q215钢,厚度1.5mm,年生产量5万件,要求编制该冲压工艺方案。
⒈零件及其冲压工艺性分析mm的凸包定位且摩托车侧盖前支承零件是以2个9.5焊接组合在车架的电气元件支架上,腰圆孔用于侧盖的装配,故腰圆孔位置是该零件需要保证的重点。
另外,该零件属隐蔽件,被侧盖完全遮蔽,外观上要求不高,只需平整。
图12-1侧盖前支承零件示意图该零件端部四角为尖角,若采用落料工艺,则工艺性较差,根据该零件的装配使用情况,为了改善落料的工艺性,故将四角修改为圆角,取圆角半径为2mm。
此外零件的“腿”较长,若能有效地利用过弯曲和校正弯曲来控制回弹,则可以得到形状和尺寸比较准确的零件。
腰圆孔边至弯曲半径R中心的距离为2.5mm。
大于材料厚度(1.5mm),从而腰圆孔位于变形区之外,弯曲时不会引起孔变形,故该孔可在弯曲前冲出。
⒉确定工艺方案首先根据零件形状确定冲压工序类型和选择工序顺序。
冲压该零件需要的基本工序有剪切(或落料)、冲腰圆孔、一次弯曲、二次弯曲和冲凸包。
其中弯曲决定了零件的总体形状和尺寸,因此选择合理的弯曲方法十分重要。
(1) 弯曲变形的方法及比较该零件弯曲变形的方法可采用如图12-2所示中的任何一种。
第一种方法(图12-2a)为一次成形,其优点是用一副模具成形,可以提高生产率,减少所需设备和操作人员。
缺点是毛坯的整个面积几乎都参与激烈的变形,零件表面擦伤严重,且擦伤面积大,零件形状与尺寸都不精确,弯曲处变薄严重,这些缺陷将随零件“腿”长的增加和“腿”长的减小而愈加明显。
第二种方法(图12-2b)是先用一副模具弯曲端部两角,然后在另一副模具上弯曲中间两角。
这显然比第一种方法弯曲变形的激烈程度缓和的多,但回弹现象难以控制,且增加了模具、设备和操作人员。
第三种方法(图12-2c)是先在一副模具上弯曲端部两角并使中间两角预弯45°,然后在另一副模具上弯曲成形,这样由于能够实现过弯曲和校正弯曲来控制回弹,故零件的形状和尺寸精确度高。
此外,由于成形过程中材料受凸、凹模圆角的阻力较小,零件的表面质量较好。
这种弯曲变形方法对于精度要求高或长“脚”短“脚”弯曲件的成形特别有利。
图12-2弯曲成形a)一副模具成形b)、c)两副模具成形(2) 工序组合方案及比较根据冲压该零件需要的基本工序和弯曲成形的不同方法,可以作出下列各种组合方案。
方案一:落料与冲腰圆孔复合、弯曲四角、冲凸包。
其优点是工序比较集中,占用设备和人员少,但回弹难以控制,尺寸和形状不精确,表面擦伤严重。
方案二:落料与冲腰圆孔复合、弯曲端部两角、弯曲中间两角、冲凸包。
其优点是模具结构简单,投产快,但回弹难以控制,尺寸和形状不精确,而且工序分散,占用设备和人员多。
方案三:落料与冲腰圆孔复合、弯曲端部两角并使中间两角预弯45°、弯曲中间两角、冲凸包。
其优点是工件回弹容易控制,尺寸和形状精确,表面质量好,对于这种长“腿”短“脚”弯曲件的成形特别有利,缺点是工序分散,占用设备和人员多。
方案四:冲腰圆孔、切断及弯曲四角连续冲压、冲凸包。
其优点是工序比较集中,占用设备和人员少,但回弹难以控制,尺寸和形状不精确,表面擦伤严重。
方案五:冲腰圆孔、切断及弯曲端部冲腰圆孔、切断连续冲压、弯曲中间两角、冲凸包。
这种方案实质上与方案二差不多,只是采用了结构复杂的连续模,故工件回弹难以控制,尺寸和形状不精确。
方案六:将方案三全部工序组合,采用带料连续冲压。
其优点是工序集中,只用一副模具完成全部工序,其实质是把方案三的各工序分别布置在连续模的各工位上,所以还具有方案三的各项优点,缺点是模具结构复杂,安装、调试和维修困难。
制造周期长。
综合上述,该零件 虽然对表面外观要求不高,但由于“腿”特别长,需要有效地利用过弯曲和校正来控制回弹,其方案三和方案六都能满足这一要求,但考虑到该零件件生产批量不是太大,故选用方案三,其冲压工序如下:落料冲孔、一次弯形 (弯曲端部两角并使中间两角预弯45°)、二次弯形(弯曲中间两角)、冲凸包。
⒊ 主要工艺参数计算(1) 毛坯展开尺寸 展开尺寸按图12-3分段计算。
毛坯展开长度l l l l l L 222254321++++=式中 l 1=12.5mm;l 2=45.5m;l 3=30mm;l 4和l 5按()xt r +2π计算。
其中圆周半径r 分别为2mm 和4mm ,材料厚度t=1.5mm ,中性层位置系数x 按t r 由表3-2查取。
当r=2mm 时取x=0.43,r=4mm 时取x=0.46。
将以上数值代入上式得()()()mm L 1695.146.04225.143.0222305.4525.122=⨯++⨯+++⨯+⨯=ππ 考虑到弯曲时材料略有伸长,故取毛坯展开长度L=168mm 。
对于精度要求高的弯曲件,还需要通过试弯后进行修正,以获得准确的展开尺寸。
(2) 确定排样方案和计算材料利用率1) 确定排样方案,根据零件形状选用合理的排样方案,以提高材料利用率。
该零件采用落料与冲孔复合冲压,毛坯形状为矩形,长度方向尺寸较大,为便于送料,采用单排方案 (见图12-4)。
图12-3毛坯计算图图12-4排样方案搭边值a和a1由表2-12查得,得a=2mm,a1=1.8mm。
2) 确定板料规格和裁料方式。
根据条料的宽度尺寸,选择合适的板料规格,使剩余的边料越小越好。
该零件宽度用料为172mm,以选择1.5mm×710mm×1420mm的板料规格为宜。
裁料方式既要考虑所选板料规格、冲制零件的数量,又要考虑裁料操作的方便性,该零件以纵裁下料为宜。
对于较为大型的零件,则着重考虑冲制零件的数量,以降低零件的材料费用。
(3) 计算材料消耗工艺定额和材料利用率。
根据排样计算,一张钢板可冲制的零件数量为n=4×59=236(件)。
材料消耗工艺定额kg G 04998.023********.014207105.1=⨯⨯⨯==量一张钢板冲制零件的数一张钢板的质量材料利用率%100⨯⨯=一张钢板面积零件面积一张钢板冲制零件数量η ()%10014207105.61312221682362⨯⨯⨯-⨯-⨯⨯=πη =79.7%零件面积由图12-5计算得出。