数控折弯机液压系统工作原理解读
数控折弯机床结构原理介绍说明

数控折弯机床结构原理介绍说明注:目录中标红的内容为服务人员在机床安装调试时必须按照此手册给客户进行培训的内容;其余内容由客户自行学习了解,后期若有需要可来我公司培训或者由服务人员上门培训。
一、机床结构原理1.1机床主要机械结构、机械主要大部件介绍PBH机床主要由机架、滑块、油缸、后挡料、模具、防护部件、数控系统等部分组成。
防护数控系统滑块模具机架后挡料防护1.2机床各数控轴的定义、功能见电气中文说明书P101.3数控折弯机工作原理现场服务人员简单介绍1.4各数控轴参考点的定义及寻参动作过程,寻参时的特殊注意事项数控系统每次上电,各个数控轴的参考点必须重新寻找。
寻参动作过程:机床上电以后,将数控系统的工作方式切换到手动工作页面,启动油泵电机,油泵工作正常的指示灯点亮以后,启动数控系统。
此时数控系统将执行机床各个数控轴的回参考点操作。
滑块向上运动寻找Y1、Y2轴的参考点,当滑块分别经过左右光栅尺的REF 点后,滑块将停在上死点。
Y轴的参考点寻找完成。
后挡料机构往后运动寻找X轴的参考点,运动到后RSD开关处等待其它轴(X1轴、R轴、Z1轴、Z2轴)寻找到参考点并定位完成后,后挡料X轴反向向前寻找到参考点并定位到手动页面中所编程的X值。
假如后挡料只配置了X 轴时,后挡料将直接反向寻找到参考点并定位完成。
后挡料机构向上运动寻找R轴的参考点,到达RSD开关处,立即反向向下寻找到参考点并定位到编程值。
左侧后挡指向左运动寻找Z1轴的参考点,到达RSD开关处,立即反向向右寻找到参考点并定位到编程值。
右侧后挡指向右运动寻找Z2轴的参考点。
到达RSD开关处,立即反向向左寻找到参考点并定位到编程值。
特殊注意事项:机床寻参一般为刚开机的第一步动作,所以在启动机器之前一定要查看机床及周边的安全情况,例如机床后侧防护门是否被打开,机床两侧防护门是否关闭,机床安全范围内是否站人,排除一切安全隐患后方可启动机器。
再操作完机器关机之前一定要将滑块放下,以防止下次开机时Y轴寻参异常。
数控折弯机原理

数控折弯机原理
数控折弯机是一种利用数字控制技术实现金属板材折弯加工的机械设备。
它的工作原理如下:
1. 设计输入:首先,通过计算机辅助设计(CAD)软件绘制出要加工的零件的三维模型,并确定折弯的位置、角度和弯线等参数。
2. 程序生成:根据设计输入的模型,使用专门的数控编程软件生成相应的数控程序。
这个程序包含了机床的控制指令,如进给速度、折弯角度等等。
3. 数控系统设置:将生成好的数控程序加载到数控折弯机的数控系统中。
同时,根据具体的工件材料和参数进行系统的设置和校准。
4. 夹紧工件:将待加工的金属板材放置在折弯机的夹具上,并进行合理的夹紧固定。
这样可以保证加工过程中工件不会发生位移或变形。
5. 加工过程:一旦以上准备工作完成,就可以开始数控折弯机的加工过程。
数控系统根据事先生成的数控程序,控制液压系统对夹紧的工件施加压力,从而使其发生弯曲。
6. 自动控制:数控系统通过传感器实时监测工件的变形情况,并根据设定的参数进行调整。
一旦折弯角度和弯线达到预定的要求,数控系统会自动停止加工。
7. 产品检验:完成加工后,需要对成品进行质量检验。
检查折弯角度、弯线的准确性以及工件表面的质量等方面,确保产品符合设计要求。
以上就是数控折弯机的工作原理。
通过将数字控制技术应用于折弯加工过程中,大大提高了生产效率和加工精度,也降低了操作难度和人力成本。
折弯机液压系统工作原理

折弯机液压系统工作原理
折弯机液压系统工作原理如下:
液压系统是通过液体的压力传递力量和控制运动的系统。
在折弯机中,液压系统主要由液压泵、液压缸、液压阀等组成。
首先,液压泵将液体从油箱吸入,然后通过压力能将液体压力提高,再推送到液压缸中。
液压泵可以是手动操作的,也可以是电动或者液压马达驱动的。
液压泵将高压液体推送至液压缸中,液压缸分为两个活塞室,当液压油进入一个活塞室时,另一个活塞室的油液则会返回油箱。
液压缸内的活塞会随着液压油的进出而运动,从而驱动机械装置进行工作。
在液压系统中,液压阀起着控制液体流动的作用。
通过液压阀的开关控制,可以实现液压油的进出、压力的提高和释放。
液压阀可以根据要求进行不同的控制操作,以满足折弯机的工作需要。
整个液压系统中,液压油的流动迅速且稳定可靠,液压泵和液压阀的合理配合可以实现对液压系统的精确控制。
这样,折弯机的工作能够在液压系统的支持下实现高效、准确的操作。
折弯机液压系统的设计解读

折弯机液压系统的设计折弯机机属于一种锻造机械。
它是一个主要角色在金属加工行业。
产品广泛应用于 :轻工、航空、船舶、冶金、仪表、电器、不锈钢制品、钢结构建筑和装饰行业。
液压系统采用活塞泵的压力补偿提供油、回油节流控制 , 合理使用能源。
垂直液压缸使用平衡和锁定措施 , 所以 safly 和在国内工作。
同时液压缸组件的实现有伟大的夹紧力和剪切力。
当系统剪切板材料 , 它的性能很好新闻系统的设计 , 金属板剪切系统和液压泵站系统的电路设计和泵站的结构、布局和一些非标准组件的设计。
在设计过程中 , 实现了结构紧凑、布局合理、制造简单。
液压系统的概况安妮媒体 (液体或气体 , 自然流动或可以被迫流可以用来传递能量的流体动力系统。
使用最早的流体是水因此得名液压应用于系统使用液体。
在现代术语 , 液压意味着电路使用矿物油。
图 1 - 1显示了一个基本的液压系统的动力装置。
(注意 , 水是有了复苏迹象的末 90年代 ; 一些流体动力系统今天海水甚至操作。
其他常见的流体在流体动力电路是压缩空气。
如图 1 - 2所示 , 大气——压缩 7 - 10倍——是现成的和流动很容易通过管道 , 管道或软管传送能量来工作。
其他气体 , 如氮或氩 , 可以使用但昂贵的生产和过程。
权力是最难理解的行业。
在大多数植物很少有直接责任人员流体动力电路设计或维护。
通常 , 一般力学保持流体动力电路 fluid-power-distributor 最初设计的销售人员。
在大多数设施 , 负责流体动力系统是机械工程师的工作描述的一部分。
问题是 , 机械工程师通常在大学接受小如果任何流体动力的培训 , 所以他们会疲于执行这个任务。
适度的流体动力培训和足够多的处理工作 , 工程师往往取决于流体动力分配器的专业知识。
订单 , 经销商销售人员很高兴设计电路 , 经常协助安装和启动。
这种安排相当有效 , 但与其他技术的进步 , 许多机器上流体动力被拒绝的功能。
折弯机的工作原理
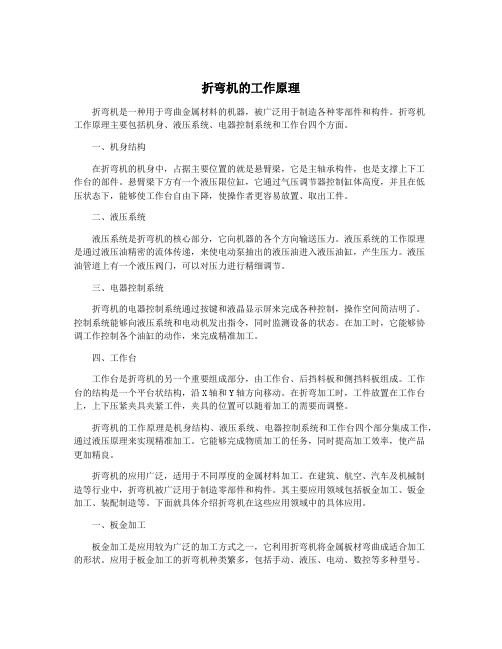
折弯机的工作原理折弯机是一种用于弯曲金属材料的机器,被广泛用于制造各种零部件和构件。
折弯机工作原理主要包括机身、液压系统、电器控制系统和工作台四个方面。
一、机身结构在折弯机的机身中,占据主要位置的就是悬臂梁,它是主轴承构件,也是支撑上下工作台的部件。
悬臂梁下方有一个液压限位缸,它通过气压调节器控制缸体高度,并且在低压状态下,能够使工作台自由下降,使操作者更容易放置、取出工件。
二、液压系统液压系统是折弯机的核心部分,它向机器的各个方向输送压力。
液压系统的工作原理是通过液压油精密的流体传递,来使电动泵抽出的液压油进入液压油缸,产生压力。
液压油管道上有一个液压阀门,可以对压力进行精细调节。
三、电器控制系统折弯机的电器控制系统通过按键和液晶显示屏来完成各种控制,操作空间简洁明了。
控制系统能够向液压系统和电动机发出指令,同时监测设备的状态。
在加工时,它能够协调工作控制各个油缸的动作,来完成精准加工。
四、工作台工作台是折弯机的另一个重要组成部分,由工作台、后挡料板和侧挡料板组成。
工作台的结构是一个平台状结构,沿X轴和Y轴方向移动。
在折弯加工时,工件放置在工作台上,上下压紧夹具夹紧工件,夹具的位置可以随着加工的需要而调整。
折弯机的工作原理是机身结构、液压系统、电器控制系统和工作台四个部分集成工作,通过液压原理来实现精准加工。
它能够完成物质加工的任务,同时提高加工效率,使产品更加精良。
折弯机的应用广泛,适用于不同厚度的金属材料加工。
在建筑、航空、汽车及机械制造等行业中,折弯机被广泛用于制造零部件和构件。
其主要应用领域包括板金加工、钣金加工、装配制造等。
下面就具体介绍折弯机在这些应用领域中的具体应用。
一、板金加工板金加工是应用较为广泛的加工方式之一,它利用折弯机将金属板材弯曲成适合加工的形状。
应用于板金加工的折弯机种类繁多,包括手动、液压、电动、数控等多种型号。
加工过程中,通过调整工作台长度、调整工件的位置以及调整夹具压力来实现工件的精确弯曲。
折弯机液压工作原理

折弯机液压工作原理
折弯机液压工作原理的解析:
折弯机是一种利用液压系统来实现金属板材折弯加工的机械设备。
它主要由液压系统、工作台、上模、下模和辅助装置等部分组成。
液压系统是折弯机的核心部分。
其工作原理是利用液体在封闭系统中的传递压力来实现机械运动。
液压系统包括一个液压泵、一个液压缸和一些液压阀。
液压泵负责将外界提供的原动力转化为液压能。
当液压泵工作时,液体被吸入液压泵的工作腔内,然后通过压力作用将液体送入液压缸。
液压缸是将液体的压力能转化为机械能的装置。
液体进入液压缸时,其压力会使活塞在液压缸内移动,从而驱动工作台进行上下运动。
液压缸的活塞杆则与上模相连,通过活塞的推拉运动,上模可以实现左右移动。
辅助装置主要包括限位器、刚度装置和主从同步装置等。
限位器可以控制上模和下模的行程,确保折弯工件的准确性和稳定性。
刚度装置可以增加机床的刚度,提高折弯机的精度和工作性能。
主从同步装置则可以实现上模和下模的相对运动,以保证折弯工件的一致性。
在折弯机的工作过程中,操作人员首先将待加工的金属板材放置在工作台上,并进行必要的调整和固定。
然后,通过液压系
统的控制,活塞开始驱动上模向下移动,将金属板材弯曲成所需的形状。
最后,上模向上移动,完成一次折弯过程。
总结起来,折弯机液压工作的基本原理是利用液压系统来传递压力,驱动上模和下模的运动,从而实现金属板材的折弯加工。
这种工作原理可以提高折弯机的工作效率和精度,广泛应用于金属加工领域。
数控折弯机液压说明书解读

电液同步折弯机液压系统原理说明该液压阀组是专为电液同步折弯机配套使用。
采用意大利ATOS闭环同步控制系统,抗偏载能力强,同步精度高。
该液压控制系统包含1、压力块:由比例压力阀(4)、安全阀(4.1)、电磁换向阀(6)、比例减压阀(10)、滤油器等组成。
2、同步控制块:直接安装在两只油缸上,它由比例伺服阀(2),下腔安全阀(3)、背压阀(4)、锥式电磁换向阀(5)等组成。
3、充液阀:40T-300T为常开型充液阀安装在油缸体内,400T-1200T为常闭型充液阀,安装在油缸体上。
原理说明(参照液压原理图和动作顺序图)一、压力控制:启动油泵电机,根据所需的折弯力不同,由比例压力阀(4)控制二通插装阀(2)来调节液压系统的压力。
以满足折弯力的要求。
压力阀(4.1)为安全阀,控制系统最高压力。
二、工作循环1、快下:给比例压力阀(4)1Y1电压(20%~30%),电磁换向阀(6)1Y2失电,电磁阀(5)4Y3得电时,给比例伺服阀正电压(80%左右),由于滑块自重快速下降,油液通过充液阀吸入油缸上腔,另外油泵排出的油液经比例伺服阀(2)同时进入油缸上腔。
油缸下腔的油液通过电磁阀5(A→P)、比例伺服阀(2)(A→T)回油箱。
滑块快下速度可通过调节比例伺服阀的控制电压控制比例伺服阀开口而得到不同速度。
2、工进:给比例压力阀(4)1Y1得电,电磁换向阀(6)1Y2得电,使充液阀关闭,电磁阀(5)4Y3失电,油泵排出的压力油,经比例伺服阀(2)进入油缸上腔(无杆腔)。
油缸下腔的油经过背压阀(4)、比例伺服阀(2)回油箱。
滑块下压。
通过调节比例伺服阀的控制电压控制比例伺服阀开口而得到不同工进速度。
安全阀(3)是防止油缸下腔压力过高,设定压力比系统压力高10%,背压阀(4)设定压力一般为平衡压力加(30~50)bar。
3、保压:当滑块到达下死点后,给比例伺服阀0V,切断油缸上、下腔的通路,滑块停止在下死点上。
4、卸荷:折弯机保压结束后,比例压力阀仍然保持压力,将比例伺服阀2给比例伺服阀一定负电压,使比例阀微量开启(返程方向),同时滑块也会微量上行,上行量由卸荷距离参数设定,卸荷过程所用时间由减压速度参数设定,油缸上腔的压力通过比例伺服阀(2)卸荷。
数控折弯机工作原理和利用方式档

数控折弯机工作原理和利用方式这种对薄板进行折弯的数控折弯机模具。
该数控折弯机模具包括支架、工作台和夹紧板,利历时由导线对线圈通电,通电后对压板产生引力,从而实现对压板和底座之间薄板的夹持。
由于采纳了电磁力夹持,使得压板能够做成多种工件要求,而且可对有侧壁的工件进行加工,操作上也十分简便。
按一般的液压数控折弯机模具加工Q235板料来做简单介绍:一、第一是接通电源,在操纵面板上打开开关,再启动油泵,如此你就听到油泵的转动声音了(现在机械不动作)。
二、行程调剂,利用必需要注意调剂行程,在折弯前必然要测试。
它的上模下行至最底部时必需保证有一个板厚的间隙。
不然会对模具机械造成损坏。
行程的调剂也是有电动快速调整。
3、折弯槽口选择,一样要选择板厚的8倍宽度的槽口。
如折弯4mm的板料,需选择32左右的槽口。
4、后挡料调整一样都有电动快速调整和手动微调,方式同剪板机。
五、踩下脚踏开关开始折弯,数控折弯机模具与剪板机不同,能够随时松开,松开脚便停下,在踩继续下行。
塑料数控折弯机模具,塑料折边机,塑料板数控折弯机模具,塑料板材折弯塑料板材直接折弯,不需拼接,不需开槽,不需用焊条,它的折角外表美观不漏水,它将手工焊接转变成全自动的机械操作,提高了质量,提高了劳动效率,降低了劳动本钱,大缩短了产品的生产周期。
全自动塑料折角机属电气一体化全自动机械设备。
依照塑料板加热变软熔化焊接的原理研制而成,它适合所有热塑性材料的折角。
速度快,折角处置表面美观,强度高。
液压剪板机又分为摆式与闸式.摆式活性炭由于是圆弧运动,而圆弧刀片制作又相当困难,一样是用刀片以后做垫铁补偿,因此所得出的间隙并非精准,剪出来的板料也不是很理想.因为是弧形运动,其刀片也不能做成矩形,而应做成锐角,因此刀片的受力情形也不睬想,刀片损伤也较厉害.做摆式剪板机国内代表为天水机床厂与冲剪机床厂.闸式液压剪板机就克服了以上所有毛病.但目前国内厂家能做闸式剪板机的并非多。
- 1、下载文档前请自行甄别文档内容的完整性,平台不提供额外的编辑、内容补充、找答案等附加服务。
- 2、"仅部分预览"的文档,不可在线预览部分如存在完整性等问题,可反馈申请退款(可完整预览的文档不适用该条件!)。
- 3、如文档侵犯您的权益,请联系客服反馈,我们会尽快为您处理(人工客服工作时间:9:00-18:30)。
液压系统工作原理
1 启动
电磁铁全部不得电,主泵输出油液通过阀6、21中位卸载。
2 主缸快速下行
电磁铁1Y、5Y 得电,阀6 处于右位,控制油经阀8 使液控单向阀9 开启。
进油路:泵1-阀6右位-阀13-主缸上腔。
回油路:主缸下腔-阀9-阀6右位-阀21中位-油箱。
主缸滑块在自重作用下迅速下降,泵1 虽处于最大流量状态,仍不能满足其需要,因此主缸上腔形成负压,上位油箱15 的油液经充液阀14 进入主缸上腔。
3 主缸慢速接近工件、加压
当主缸滑块降至一定位置触动行程开关2S 后,5Y 失电,阀9 关闭,主缸下腔油液经背压阀10、阀6 右位、阀21 中位回油箱。
这时,主缸上腔压力升高,阀14 关闭,主缸在泵1 供给的压力油作用下慢速接近
工件。
接触工件后阻力急剧增加,压力进一步提高,泵1 的输出流量自动减小。
4 保压
当主缸上腔压力达到预定值时,压力继电器7发信号,使1Y失电,阀6回中位,主缸上下腔封闭,单向阀13 和充液阀14 的锥面保证了良好的密封性,使主缸保压。
保压时间由时间继电器调整。
保压期间,泵经阀6、21的中位卸载。
5 泄压,主缸回程保压结束,时间继电器发出信号,2Y 得电,阀
6 处于左位。
由于主缸上腔压力很高,液动滑阀12 处于上位,压力油使外控顺序阀11 开启,泵1输出油液经阀11 回油箱。
泵1 在低压下工作,此压力不足以打开充液阀14 的主阀芯,而是先打开该阀的卸载阀芯,使主缸上腔油液经此卸载阀芯开口泄回上位油箱,压力逐渐降低。
当主缸上腔压力泄到一定值后,阀12 回到下位,阀11关闭,泵1 压力升高,阀14完全打开,此时进油路:泵1-阀6左位-阀9-主缸下腔。
回油路:主缸上腔-阀14-上位油箱15。
实现主缸快速回程。
6 主缸原位停止
当主缸滑块上升至触动行程开关1S,2Y失电,阀6 处于中位,液控单向阀9将主缸下腔封闭,主缸原位停止不动。
泵1 输出油液经阀6、21中位卸载。
7 下缸顶出及退回
3Y得电,阀21 处于左位。
进油路:泵1-阀6中位-阀21左位-下缸下腔。
回油路:下缸上腔-阀21 左位-油箱。
下缸活塞上升,顶出。
3Y失电,4Y得电,阀21 处于右位,下缸活塞下行,退回。
8 浮动压边
下缸活塞先上升到一定位置后,阀21 处于中位,主缸滑块下压时下缸活塞被迫随之下行,下缸下腔油液经节流器19 和背压阀20 回油箱,使下缸下腔保持所需的压边压力,调整阀20 即可改变浮动压边压力。
下缸上腔则经阀21中位从油箱补油。
溢流阀18 为下缸下腔安全阀。