18650流程与控制点
18650型三元锂离子电池的制备

18650型三元锂离子电池的制备18650型三元锂离子电池是一种常用的电池,具有高能量密度、长循环寿命和较低的自放电率等优点。
下面我们将介绍18650型三元锂离子电池的制备过程。
18650型三元锂离子电池的制备一般包括材料制备、电池制备和电池测试三个步骤。
首先是材料制备。
18650型三元锂离子电池的主要材料包括正极材料、负极材料和电解液。
正极材料通常采用锂镍钴锰酸(NCM)材料,其制备过程主要包括材料的混合、烧结和球磨等步骤。
首先将镍、钴和锰的化合物混合均匀,然后将混合物在高温下烧结,形成结晶体。
接下来,将烧结体球磨成粉末,得到细小的颗粒。
负极材料一般采用石墨材料,其制备方法相对简单。
首先将天然石墨破碎成小块,然后在高温和惰性气体的条件下烧结成固体块,最后将固体块球磨成粉末。
电解液一般采用碳酸二甲酯(DMC)、乙二醇二甲醚(EDM)和氟乙酸锂(LiPF6)等组成的溶液。
可以通过将这些物质按一定比例混合,加热搅拌溶解,得到需要的电解液。
电极涂布是将正极材料和负极材料分别涂布到铜箔和铝箔上,形成阳极和阴极。
首先将正极材料浆料涂布在铜箔上,然后通过刮刀或压花机进行压实和均匀涂布。
类似地,负极材料浆料也涂布在铝箔上。
成型是将涂布好的阳极和阴极通过滚压机进行成型,使其具有一定的形状和尺寸。
装配是将正极、负极和隔膜层叠放置在一起,形成电芯。
封装是将电芯放入金属壳体中,并封住端口,形成最终的电池。
最后是电池测试。
制备好的18650型三元锂离子电池需要进行严格的测试,包括静态性能测试和动态性能测试等。
静态性能测试主要包括容量测试、电压测试、内阻测试等;动态性能测试主要包括循环寿命测试、快充性能测试、高温性能测试等。
通过这些测试,可以评估电池的性能和品质,确保制备出的18650型三元锂离子电池具有稳定的性能和良好的使用寿命。
制备18650型三元锂离子电池需要经过材料制备、电池制备和电池测试三个步骤。
通过优化每个步骤的工艺和控制条件,可以制备出性能稳定、品质可靠的18650型三元锂离子电池。
18650型三元锂离子电池的制备
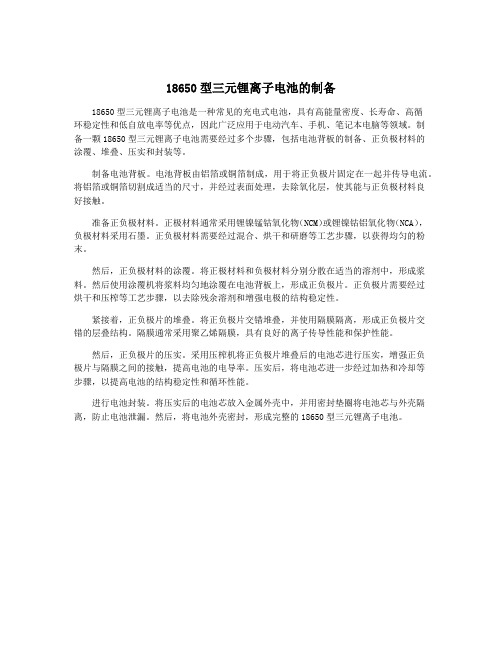
18650型三元锂离子电池的制备18650型三元锂离子电池是一种常见的充电式电池,具有高能量密度、长寿命、高循环稳定性和低自放电率等优点,因此广泛应用于电动汽车、手机、笔记本电脑等领域。
制备一颗18650型三元锂离子电池需要经过多个步骤,包括电池背板的制备、正负极材料的涂覆、堆叠、压实和封装等。
制备电池背板。
电池背板由铝箔或铜箔制成,用于将正负极片固定在一起并传导电流。
将铝箔或铜箔切割成适当的尺寸,并经过表面处理,去除氧化层,使其能与正负极材料良好接触。
准备正负极材料。
正极材料通常采用锂镍锰钴氧化物(NCM)或锂镍钴铝氧化物(NCA),负极材料采用石墨。
正负极材料需要经过混合、烘干和研磨等工艺步骤,以获得均匀的粉末。
然后,正负极材料的涂覆。
将正极材料和负极材料分别分散在适当的溶剂中,形成浆料。
然后使用涂覆机将浆料均匀地涂覆在电池背板上,形成正负极片。
正负极片需要经过烘干和压榨等工艺步骤,以去除残余溶剂和增强电极的结构稳定性。
紧接着,正负极片的堆叠。
将正负极片交错堆叠,并使用隔膜隔离,形成正负极片交错的层叠结构。
隔膜通常采用聚乙烯隔膜,具有良好的离子传导性能和保护性能。
然后,正负极片的压实。
采用压榨机将正负极片堆叠后的电池芯进行压实,增强正负极片与隔膜之间的接触,提高电池的电导率。
压实后,将电池芯进一步经过加热和冷却等步骤,以提高电池的结构稳定性和循环性能。
进行电池封装。
将压实后的电池芯放入金属外壳中,并用密封垫圈将电池芯与外壳隔离,防止电池泄漏。
然后,将电池外壳密封,形成完整的18650型三元锂离子电池。
圆柱电芯18650制造过程及流程培训课件
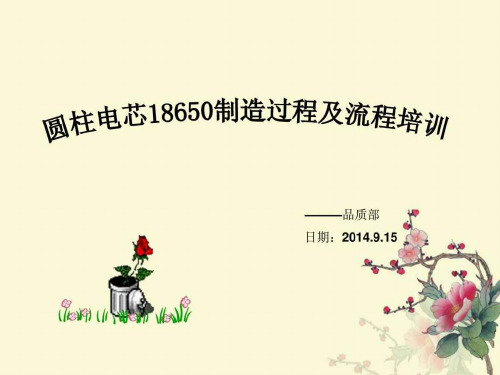
45
精选课件
46
精选课件
47
精选课件
48
精选课件
49
精选课件
50
精选课件
51
精选课件
52
精选课件
53
精选课件
54
精选课件
55
精选课件
56
精选课件
57
精选课件
58
精选课件Βιβλιοθήκη 59精选课件60精选课件
61
精选课件
62
精选课件
63
精选课件
64
精选课件
65
精选课件
66
精选课件
精选课件
1
精选课件
2
精选课件
3
精选课件
4
精选课件
5
精选课件
6
精选课件
7
精选课件
8
精选课件
9
精选课件
10
精选课件
11
精选课件
12
精选课件
13
精选课件
14
精选课件
15
精选课件
16
精选课件
17
精选课件
18
精选课件
19
精选课件
20
精选课件
21
精选课件
22
精选课件
23
67
精选课件
68
精选课件
69
精选课件
70
精选课件
71
精选课件
24
精选课件
25
精选课件
26
精选课件
27
精选课件
28
精选课件
29
精选课件
30
精选课件
18650锂电池工艺流程
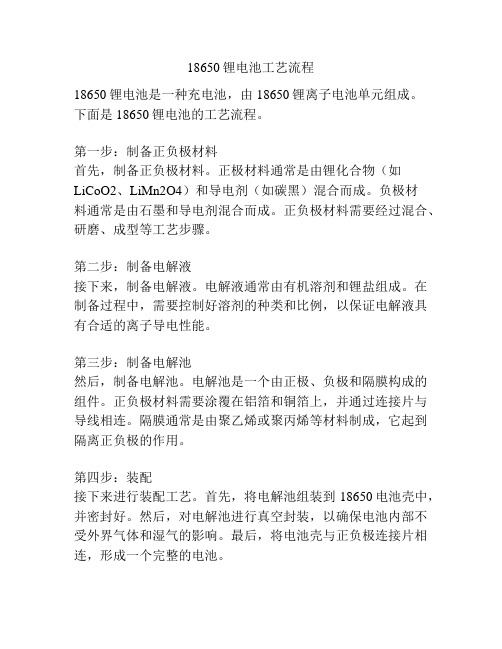
18650锂电池工艺流程18650锂电池是一种充电池,由18650锂离子电池单元组成。
下面是18650锂电池的工艺流程。
第一步:制备正负极材料首先,制备正负极材料。
正极材料通常是由锂化合物(如LiCoO2、LiMn2O4)和导电剂(如碳黑)混合而成。
负极材料通常是由石墨和导电剂混合而成。
正负极材料需要经过混合、研磨、成型等工艺步骤。
第二步:制备电解液接下来,制备电解液。
电解液通常由有机溶剂和锂盐组成。
在制备过程中,需要控制好溶剂的种类和比例,以保证电解液具有合适的离子导电性能。
第三步:制备电解池然后,制备电解池。
电解池是一个由正极、负极和隔膜构成的组件。
正负极材料需要涂覆在铝箔和铜箔上,并通过连接片与导线相连。
隔膜通常是由聚乙烯或聚丙烯等材料制成,它起到隔离正负极的作用。
第四步:装配接下来进行装配工艺。
首先,将电解池组装到18650电池壳中,并密封好。
然后,对电解池进行真空封装,以确保电池内部不受外界气体和湿气的影响。
最后,将电池壳与正负极连接片相连,形成一个完整的电池。
第五步:充电和放电测试装配完成后,对电池进行充电和放电测试。
这些测试可以检查电池的容量、电压和循环寿命等参数,以确保电池的品质符合规定标准。
同时也可以排除产品中存在的潜在缺陷。
第六步:封装和贴标签通过封装和贴标签的工艺,将电池打包成成品。
这个过程通常包括将电池包装在塑料封装体中,并贴上标签以标明电池的容量、型号和生产日期等信息。
以上就是18650锂电池的工艺流程。
通过以上步骤,18650锂电池可以顺利地生产出来,并用于各种电子设备中,如手机、笔记本电脑、电动车等。
制造过程中需要严格控制材料和工艺的质量,以确保最终产品的性能和安全性。
圆柱电芯18650制造过程及流程培训课件

关键要点:
电池外观 :清洗前电芯外观符合来料等级,清洗后电芯表面无水珠,无电芯表面发黄,清洗过程无卡 料;电芯在转化成后须在10分钟内清洗完毕。
壳体喷码
4VM9A01 ABA
关键要点: 壳体喷码与标识卡上信息吻合
4VM9A01 ABA
干燥存储
关键要点: 1、RH≤15%, 2、T≤30℃ 3、贮存时间H=40h~48h 4、标识卡与电芯喷码相符
、大颗粒、
2、胶液的外观要求:黑色均匀粘稠状胶体、无气泡、杂质
絮状凝胶、油污、沉淀等现象。
抽真空要求:真空度为-(0.085----0.1)MPa
干混罐残留物的清除: 罐内清洁、无污物、杂质。
涂布
涂布机烘区
准备好的浆料
涂布好的极片
涂布工序关键要点:
箔材外观:表面、切面平整,色泽均一,无明显亮线、明显凹凸点、暗痕条纹等,边缘 无明显翘边和褶皱,无掉粉,管芯无生锈。
石墨
导电剂
粘结剂 负 极 匀 桨
SBR
胶液
搅拌机
CMC
溶剂
制 胶 罐
浆料小车
负极制胶匀桨工序关键要点:
负极来料的确认:1、标识:清晰、明确,与BOM、发料单、工艺标准相一致。
2、外观:包装完整,符合《制程检验标准》。
3、保质:在有效期范围内。
加料比:严格按电池工艺标准执行
石墨粉:导电剂:SBR:CMC:制胶溶剂=100:2.1:4.2:1.7:92
3、真空输送管无堵塞、通气不顺,罐体清洁无污物、杂质。
除铁比率:来料和除铁后铁,铜,镍均要小于100PPM;除铁比率=除铁前铁含量(PPM) -出铁后铁含量(PPM)
电子秤的稳定性:用20Kg砝码每天校准一次。
18650型三元锂离子电池的制备
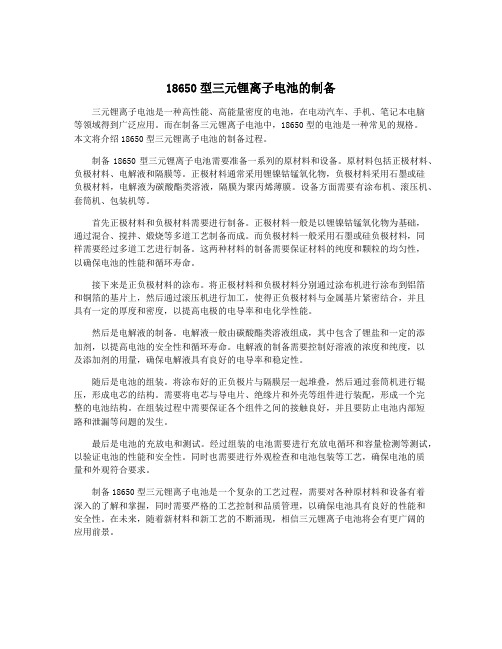
18650型三元锂离子电池的制备三元锂离子电池是一种高性能、高能量密度的电池,在电动汽车、手机、笔记本电脑等领域得到广泛应用。
而在制备三元锂离子电池中,18650型的电池是一种常见的规格。
本文将介绍18650型三元锂离子电池的制备过程。
制备18650型三元锂离子电池需要准备一系列的原材料和设备。
原材料包括正极材料、负极材料、电解液和隔膜等。
正极材料通常采用锂镍钴锰氧化物,负极材料采用石墨或硅负极材料,电解液为碳酸酯类溶液,隔膜为聚丙烯薄膜。
设备方面需要有涂布机、滚压机、套筒机、包装机等。
首先正极材料和负极材料需要进行制备。
正极材料一般是以锂镍钴锰氧化物为基础,通过混合、搅拌、煅烧等多道工艺制备而成。
而负极材料一般采用石墨或硅负极材料,同样需要经过多道工艺进行制备。
这两种材料的制备需要保证材料的纯度和颗粒的均匀性,以确保电池的性能和循环寿命。
接下来是正负极材料的涂布。
将正极材料和负极材料分别通过涂布机进行涂布到铝箔和铜箔的基片上,然后通过滚压机进行加工,使得正负极材料与金属基片紧密结合,并且具有一定的厚度和密度,以提高电极的电导率和电化学性能。
然后是电解液的制备。
电解液一般由碳酸酯类溶液组成,其中包含了锂盐和一定的添加剂,以提高电池的安全性和循环寿命。
电解液的制备需要控制好溶液的浓度和纯度,以及添加剂的用量,确保电解液具有良好的电导率和稳定性。
随后是电池的组装。
将涂布好的正负极片与隔膜层一起堆叠,然后通过套筒机进行辊压,形成电芯的结构。
需要将电芯与导电片、绝缘片和外壳等组件进行装配,形成一个完整的电池结构。
在组装过程中需要保证各个组件之间的接触良好,并且要防止电池内部短路和泄漏等问题的发生。
最后是电池的充放电和测试。
经过组装的电池需要进行充放电循环和容量检测等测试,以验证电池的性能和安全性。
同时也需要进行外观检查和电池包装等工艺,确保电池的质量和外观符合要求。
制备18650型三元锂离子电池是一个复杂的工艺过程,需要对各种原材料和设备有着深入的了解和掌握,同时需要严格的工艺控制和品质管理,以确保电池具有良好的性能和安全性。
18650制作控制点培训资料A0
制作过程中 控制要点:
1、温度
2、湿度 3、粉尘 4、粘度 5、颗粒度 6、转速 搅拌机
搅拌(配料)
将正极或者负极粉料以及其他配料混合均匀,并调制成浆。
混合头高速旋转产 生吸力,液体和固 体被吸入。 离心力使材料在混 合头中进行圆周运 动 材料在搅拌罐继续 运动,进入下一个 搅拌循环 材料从混合头甩出
45mm 40mm
点焊机 控制点:
1、极耳(导电柄)批锋(毛刺)、2、正负极极耳焊接的位置、尺寸 3、极耳熔接焊接强度及焊接外观、4、保护胶带的位置、尺寸、外观 5、电极裁切的涂工长、电极长,6、电极裁切的批锋(毛刺) 7、电极组立作业区域温湿度控制,8、粉尘控制
12mm
负极焊接
卷绕—正极片、负极片、隔离膜组合卷在一起
组装—吸尘(表面无明显粉尘/金属屑)
使用手动吸尘枪,对滚槽后的每只电芯进行 吸尘 为什么要吸尘? 粉尘/金属屑会导致电池短路、自放电大(内阻大)
组装-- 绝缘测试(检测出短路的电芯)
1、绝缘测试方法: 红/黑色表笔与电池的接法
2、绝缘测试的目的: 检测出短路的电芯 降低后工序的浪费 提前发现问题,及早解决
封口后槽上外径 封口后小高
封口后槽 下外径
控制要点: 高度 外径 外观 电镀层 封口后CID值及压破值
18650流程及控制点
18650流程及控制点1. 18650电池生产流程18650电池主要是锂离子电池,包括正极、负极、隔膜、电解液等元件。
在生产过程中,需要进行以下主要步骤:(1)材料处理材料处理包括对锂镍钴铝氧化物、电解液、隔膜等原料进行筛选、称量、混合等步骤,确保原材料符合生产标准,并且可以保证电池品质。
(2)制备电极电极是电池最重要的组成部分之一,电池的性能部分取决于电极的制备过程。
电极制备需要进行多次涂布、压制、干燥等步骤,制备出质量符合标准的电极。
(3)装配电池在电池制造中,需要将正极、负极、隔膜等组件按照一定比例、顺序进行装配,确保电池的可靠性和稳定性。
(4)充放电测试在电池生产过程中,需要进行多次充放电测试,对电池的电性能、循环寿命等因素进行评估,确保产品质量。
(5)包装在完成电池生产和测试后,需要进行包装,保证电池在物流过程中受到保护。
2. 18650电池生产常见控制点在18650电池的生产过程中,需要注意以下控制点,以确保产品质量:(1)原材料的选用和检测原材料的选用需要符合标准,原材料的检测也需要符合标准。
对原材料进行检测可以提前发现问题,确保产品质量。
(2)电极制备的工艺控制电极是影响电池性能的最主要因素之一,需要进行多次密度、厚度等参数的检测,以确保电极的质量符合标准。
(3)电池装配的制程控制在电池装配中,需要制定一系列工艺控制措施,以确保正负极的错位率低,隔膜的质量可靠。
(4)电池的充放电测试电池的充放电测试是电池性能的重要检测手段之一,需要进行多次测试,确保产品达到指标要求。
(5)主要参数的监控在电池的生产过程中,需要对参数进行监控,如电池容量、电压、温度、内阻等,以确保产品的质量。
3.18650电池的生产过程中需要严格把控每一个环节,以确保产品质量符合标准,同时也需要随着技术的进步,不断优化生产流程和提升生产效率。
锂电基础知识及各工序管控要点
(三)负极
负极材料主要由::负极活性物质 + 导电剂 + 增稠剂 (CMC) + 粘结剂 (SBR) + 集流体(铜箔) 1、负极活性物质:层状结构材料,容纳LI+居住的“家”。目前主要为:人造石墨、天然石墨
2、导电剂:a) 提高负极片的导电性b) 提高反应深度及利用率。c) 防止枝晶的产生。d) 利用导电材料的吸液能力, 提高反应界面,减少极化(可根据石墨粒度分布选择加或不加)。目前只要有导电碳黑(sp)、导电石墨(ks-6) 3、增稠剂/防沉淀剂(CMC):提高浆料粘度、浆料稳定性。高分子化合物,易溶于水和极性溶剂。 4、水性粘合剂(SBR):将石墨、导电剂、添加剂和铜箔或铜网粘合在一起。小分子线性链状乳液,极易溶于水 和极性溶剂。 5、去离子水(或蒸馏水):用来稀释浆料,改变浆料的流动性。 6、负极引线:用来传导电子,由铜箔或镍带制成。 7、添加剂:降低不可逆反应,提高粘附力,提高浆料黏度,防止浆料沉淀。
6C + XLi + + xe- (电子)→ LixC6
(二)正极
正极材料主要由:正极活性物质 + 导电剂 + 粘合剂 (PVDF) + 集流体(铝箔) 1、正极活性物质:为电池提高锂源。目前只要有钴酸锂、磷酸铁锂、三元材料(NCA/NCM) 目前主要正极材料:532与811
中信锰酸锂 DMLM 国联GN5L 广钢G50 贝特瑞 N8-C 长远LY 天力TLM 长远N8-L 鸿森 HSNCM 翔鹰XY 811
生产型号确认:A B段料区工艺长度+对辊后延展长度≈工艺A B尺寸 (初步确认极片型号版次)对极片厚度,重量再次检验。
小片重量=面密度*(敷料量长度*敷料量宽度)+ 箔材密度*(箔材长*宽)+极耳+胶纸 (重量=密度*面积) (容量=敷料量*克容量)
18650制作控制点培训资料A0
组装—底部焊接&插中心针(使负极极耳与钢壳
底部焊接在一起)
加center pin, Ni-Tab底部焊接拉 力:>30N
负极柄与钢壳底部焊接在一起
控制要点: 1、不能漏加中心针 2、加中心针不能插破隔离膜 3、底部不能漏加绝缘片 4、按工艺要求控制好设备参数 5、底部焊接强度:>30N 6、底部焊点不能出现黑点
组装—滚槽
自动滚 槽机
滚槽总高 槽位以上小高 槽位以下下高 槽位以上外径 槽位以下外径 内径
半自动滚槽机
滚槽的尺寸要 求
滚槽的 位置
+/-0.1 +/-0.1 +/-0.1 +/-0.05 +/-0.05 +/-0.1
规格 65.8 4.00 60.55 18.15 18.05 14.75
钢壳
控制要点:1、滚槽时掉镀层,2、裂纹,3、滚槽尺寸控制,4、设备参数设置
A、卷绕车间的湿度对电池质量有什么影响? 卷绕房内的湿度大时,极片吸水量大,增加了极片的水份含量,在电池中产生气体量增加,使 电池的内压增加,危害电池的安全性能。水份的增加多消耗电池中的活物质,使电池容量下降。 B、卷绕车间中空调机和除湿系统的作用? 保持室内的温度恒度,减小室内的湿度,以提高电池的性能。 C、卷绕车间是否可用水擦地板? ? D、卷绕电池芯的主要注意事项? 1、 极片与隔膜纸铺平对齐。用手按住极片与隔膜纸时,用力大小适中均匀。电池芯卷绕松紧 适当。 2、 注意极片上有无划痕、掉料、缺料、气孔、起泡等不良及隔膜纸有无不良,如有作废品处 理。 3、 卷绕时注意手脚的谐调性,不被卷针划伤手。 4、电池芯贴胶纸的目的和位置? 电池芯贴纸的位置在电芯卷绕成型后不变形。底部贴胶纸防止电芯内的正极片底部与电池外壳 接触电池造成短路。侧面贴纸使电芯卷绕成型后不变形。底部贴胶纸防止电芯内的正极片底部 与电池外壳接触造成电池短路。
- 1、下载文档前请自行甄别文档内容的完整性,平台不提供额外的编辑、内容补充、找答案等附加服务。
- 2、"仅部分预览"的文档,不可在线预览部分如存在完整性等问题,可反馈申请退款(可完整预览的文档不适用该条件!)。
- 3、如文档侵犯您的权益,请联系客服反馈,我们会尽快为您处理(人工客服工作时间:9:00-18:30)。
隔膜与负极覆盖差
三、装配车间工序简介-卷绕
5、卷绕方向极片覆盖差(外层负极超正极料长、内层负极超正极料长) 检测方式:每2H每台卷绕机抽检3PCS电芯解剖,分别用目镜和直尺测量两 种覆盖差尺寸。 不良影响:可能造成负极片未包住正极片,在电芯充电过程中,使正极脱 出的锂离子无法找到对应的石墨嵌入,造成电芯中有游离的锂离子在负极 上堆积产生枝晶,枝晶刺穿隔膜造成内部短路而产生安全隐患
18650流程及其控制点
三部品质王银城
一
18650锂电池生产流程
二
制片车间工序简介
三
装配车间工序简介
四
检测车间工序简介
五
电池生产过程中的关键控制点
一、18650锂电池生产流程
制片
投料 正极匀浆 正极涂布 正极碾压 正极分切
投料 负极匀浆 负极涂布 负极碾压 负极分切
装配
烘烤 卷绕 装载 入壳 点底焊 滚槽 注液
粉尘测试仪
1.注意检测粒径的选择; 2.测试的位置; 3.测试值为稳定后显示值; 4.测试的日常保养维护,及充电 的周期;
三、装配车间工序简介-卷绕
3、裁切毛刺异常 工艺要求:极片≤8μm;极耳毛刺≤12um; 检测方式:每班次每台机首检随机抽取1PCS电芯解剖,按《毛刺检测
作业指导书》检测正、负极片前后端及正、负极耳裁切毛刺。 不良影响:极片或极耳毛刺超出NG工艺要求可能导致毛刺OK 刺穿隔膜,使
①不良标贴的位置及外漏长度; ②分切的宽度; ③极片分切毛刺≤8μm; ④掉料露箔:依制程检验标准; ⑤边缘卷极片波浪严重; ⑥环境粉尘、环境温湿度:见 〈环境控制工艺标准〉。
三、装配车间工序简介
三部A线装配流程
极片烘烤
卷绕
装载
入壳
点底焊
涂油 涂油
清洗 套标
封口
激光焊
注液
喷码
X-RAY
微预充
三、装配车间工序简介-极片烘烤
负极片
正极耳 保护胶
正极耳 (铝带)
隔膜
隔膜
负大极耳 (镍带)
三、装配车间工序简介-卷绕
注意事项:
1、湿度控制≤1%RH 目的:防止正负极片卷绕过程中吸水,导致零电压、自放电、循环性 能差; 方法:计算露点值和温度值得出温湿度值;
露点仪
湿度参照表
温湿度记录表
三、装配车间工序简介
2、粉尘控制≤100,000 pc/ft3(检测粒径为0.5um) 目的:防止粉尘在卷绕时卷入极组导致电芯短路、过热、起火、自放 电等不良; 方法:使用粉尘测试仪;
1.极片烘烤
③
①
②
①烘箱温度显示表(红色为箱体内 温度,绿色为设定温度)
②真空表
③运行监控显示屏
5
极片烘烤参数设置
工 温度 步 /℃
1/
真空 /MPa
≤-0.085
氮气 /MPa
/
时间 /min
15
步骤解释 抽真空
2/
/
-0.03 5
充氮气
3 85 /
/
240
加热
循 4 85 环 5 85 次
6/
≤-0.085 /
电芯充电过程中,使正极脱出的锂离子无法找到对应的石墨嵌入,造成电芯 中有游离的锂离子在负极上堆积产生枝晶,枝晶刺穿隔膜造成内部短路而产 生安全隐患。
2.负极片与隔膜对齐度超出工艺 标准可能使负极片受到挤压变形, 极片上的负极料部分脱落,在充 电过程中电芯膨胀,粉料刺穿隔 膜导致正负极内部短路而产生安 全隐患;
外圈正面负 极超正极料 长
激光焊 封口 清洗 涂油 套标 喷码 X-ray 微预充
检测
静置 化成 装载 高温存储 OCV1 常温 OCV2
分容 分选 入库 包装 出货
二、制片车间工序简介-投料-匀浆
1.投料-匀浆
投原材料
储料罐
匀质机
分散釜
计量罐 成品罐
螺杆
除铁
二、制片车间工序简介-投料 匀浆
注意事项:
正极来料的确认: 1、标识:清晰、明确,与BOM、发料单、工艺标准相一致。 2、外观:包装完整,符合《制程检验标准》。 3、保质:在有效期范围内。 加料比:严格按电池工艺标准执行。 搅拌机的循环水温度、搅拌速度、搅拌时间、加料的顺序:严格按 工艺标准去设置和控制 搅拌速度、时间:严格按电池工艺标准执行。 浆料的粘度、固含量、外观: 1、浆料的粘度、固含量按工艺标准进行检验和控制 2、胶液的外观要求:黑色均匀粘稠状胶体、无气泡、杂质、大颗粒、 絮状凝胶、油污、沉淀等现象。
钴酸锂 导电剂
胶液
搅拌机
粘结剂
溶剂
制 胶 罐
成品罐
二、制片车间工序简介-涂布2.涂布Fra bibliotek成品罐
涂布机烘区 涂布好的极片
二、制片车间工序简介-涂布
1 箔材外观、箔材厚度、箔材宽度、箔材面密度;
2 涂布时的走速;
3 烘区温度;
注
意 事 项
4 正负极单双面面密度、涂宽、涂 长,间隙宽度;
5 片涂头涂尾削薄、两侧削薄;
4.注意极片外观:不掉粉、烤焦、边缘翘边;
三、装配车间工序简介-卷绕
动作示意图
隔膜1卷
正极耳 焊接台
卷芯运输带
负极耳 焊接台
正极片卷
终止胶带卷 隔膜2卷 负极片卷
三、装配车间工序简介-卷绕 卷 绕 单 个电芯
三、装配车间工序简介-卷绕
卷芯示意图
终止胶
正极片
铝箔 铜箔
负小极耳 (镍带)
正极耳覆盖胶 负极耳覆盖胶
115
/
-0.03 5
≤-0.085 /
15
加热/抽真空 加热/充氮气 抽真空
7/
/
-0.03 5
充氮气
8/
≤-0.085 /
待卷绕 保真空
极片烘烤的作用:真空状态下降低水的沸点,把极片中的水分汽化排出;
三、装配车间工序简介-极片烘烤
注意事项:
1.极片烘烤过程中注意巡检真空度、箱内温度;
2.烘烤后要求:正极水分≤300ppm,负极水分≤500ppm, 测试时注意取样的方式、水分测试仪的状态; 3.每次进出极片注意探头的位置,勿松动、碰壁;
6 单双面的对齐度≤1mm;
7 涂布外观无颗粒、划痕、拖尾、颗粒等不
良;
二、制片车间工序简介碾压
3.碾压
注意事项:
①碾压速度; ②碾压后极片厚度; ③极片外观:收卷整齐,极片 无结疤、断片、折皱、掉料不 良;
碾压机
二、制片车间工序简介-分切
4.分切
分切刀
分切机
二、制片车间制程简介-分切
注意事项:
正负极短路,电芯出现过热,严重时可能爆炸,存在严重安全隐患。
NG
NG
OK
OK
NG
NG
OK
OK
三、装配车间工序简介-卷绕
4、正负极片覆盖差 工艺要求:正、负极片对齐度0.75±0.55mm
负极片与隔膜对齐度1±0.5mm 检测方式:换卷后抽检连续3PCS电芯按《X-RAY作业指导书》检测对齐度 不良影响:1)正负极片对齐度超出工艺规格可能造成负极片未包住正极片,在