IE数据处理与常用公式资料教程
IE 常见图文符号及运算公式

四.常用基本公式: 常用基本公式:
例:一天上班時間為480分,早會20分,生產過程中機器故障20分,模治具故障20分,一天共生產產品420sets,生產一個產品須時20分 ,流水線瓶頸工時為0.5分(含有寬放),不良率為5%,試計算: 1)總標準工時 2)作業效率 3)生產效率 4)設備綜合效率 解:根據以上介紹可知如下信息: 停止時間=早會20分 停機時間=機器故障20分+模治具故障20分=40分 總投入工時=480分 不良率=5% 1)總標準工時=420*0.5=210(分) 2)作業效率=(總標準工時/總使用工時)*100% =(總標準工時/總投入工時-停止時間-停機時間)*100% =[210/(480-20-40)]*100% =50% 3)生產效率=(總標準工時/總投入工時) *100% =(210/480)*100% =43.75% 4)設備綜合效率=時間稼動率*性能稼動率*良品率 時間稼動率=(總投入工時-停機時間)/總投入工時) *100% =[(480-40)/480]*100% =91.67% 性能稼動率=(總標準工時/負荷工時) *100% =[總標準工時/(總投入工時-停止時間)]*100% =[210/(480-20)]*100% =45.65% 良品率=1-不良率=1-5%=95% 故: 設備綜合效率=時間稼動率*性能稼動率*良品率 =91.67%*45.65%*95% =39.75%
S
1
三. 常見圖文符號
18种動素的定義及符號
動素分析是由美國工程師Frank Bunker Gilbreth(1862-1924)創立的,動作分析基本要素共有18种動作,也 有文獻定義為17种,本書設定為18种.(詳見下圖)
A.工 作 有 效 推 進 的 動 作 動 素 定 義 分 類 符號 B.造 成 工 作 遲 延 的 動 作 C.動 作 本 身 不 能 推 進 作 業 NO 1 名稱 伸手 英文及縮寫 Transport Empty (TE) Grasp (G) Transport Loaded (TL) Assemble (A) Disassemble (D) Use (U) Release Load (RL) 符號說明 手中無物的形狀 分類 A 定義 空 手 移 動 ,伸 向 目 標 ,又 稱空運 手或身體的某些部位充 分控制物體 手或身體某些部位移動 物 品 的 動 作 ,又 稱 運 實 將零部件組合成一件物 體的動作 將零部物進得分離和拆 解的動作 利用器具或裝置所做的 動 作 ,稱 使 用 或 應 用 握 取 的 相 反 動 作 ,放 開 控 制物的動作
IE常用公式
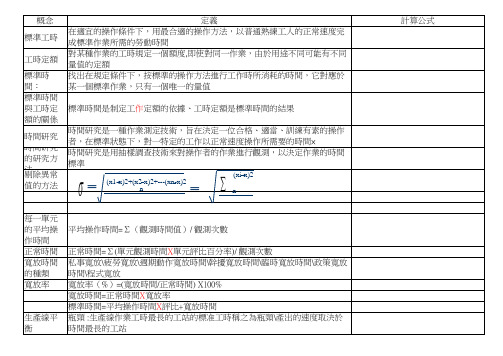
客戶緊急稽核﹐現場看板准備﹑5S抽查1.客戶緊急稽核﹐現場看板准備﹑5S抽查
2.C07棟廠房暖氣管道重新布置規划AYOUT繪制
棟廠房暖氣管道重新布置規划AYOUT繪制
跟工務檢討確認C07棟廠房1.5樓VIP辦公室施工方案及更新LAYOUT
應服務單位要求﹐准備客戶過來稽核的文件及相關事項
1.應服務單位要求﹐准備客戶過來稽核的文件及相關事項
廊坊SRM三樓清洗制程LAYOUT重新規划及現場數據調查
ALONA機種連線自動化改善效果驗証及收集和分析數據
1.應服務單位要求﹐准備客戶過來稽核的文件及相關事項
2。
IE计算公式
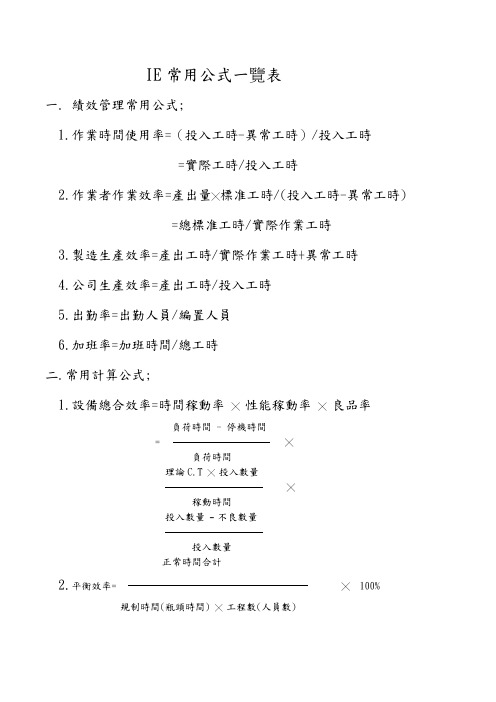
IE常用公式一覽表
一. 績效管理常用公式;
1.作業時間使用率=(投入工時-異常工時)/投入工時
=實際工時/投入工時
2.作業者作業效率=產出量╳標准工時/(投入工時-異常工時)
=總標准工時/實際作業工時
3.製造生產效率=產出工時/實際作業工時+異常工時
4.公司生產效率=產出工時/投入工時
5.出勤率=出勤人員/編置人員
6.加班率=加班時間/總工時
二.常用計算公式;
1.設備總合效率=時間稼動率╳性能稼動率╳良品率
負荷時間- 停機時間
= ╳
負荷時間
理論C.T ╳投入數量
╳
稼動時間
投入數量–不良數量
投入數量
正常時間合計
2.平衡效率= ╳100%
規制時間(瓶頭時間) ╳工程數(人員數)
1.時間利用率
實際作業時間
總投入時間
2.作業效率
總標準工時
總實際工時
單位時間實際產出標準人數
標準產出實際人數
實際作業時間內之效率指針
3.生產效率
生產效率= 作業效率x 時間利用率
單位時間實際產出標準人數
標準產出實際人力總標準時間總投入時間
總投入時間內之效率指針(含除外工時在內)
1.生產線平衡率
T1+T2+T3+…+T n
n.T m a x
T m a x﹕瓶頸工時
2.平衡率提升途徑
1.合併
2.重排
3.取消
4.簡化。
IE数据处理与常用公式
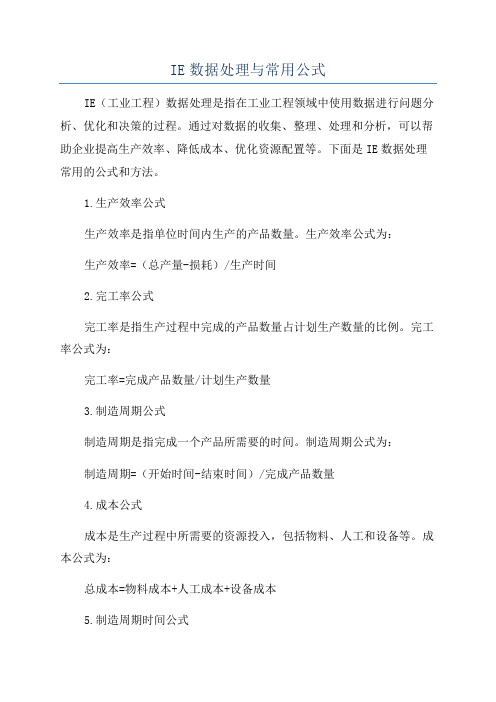
IE数据处理与常用公式IE(工业工程)数据处理是指在工业工程领域中使用数据进行问题分析、优化和决策的过程。
通过对数据的收集、整理、处理和分析,可以帮助企业提高生产效率、降低成本、优化资源配置等。
下面是IE数据处理常用的公式和方法。
1.生产效率公式生产效率是指单位时间内生产的产品数量。
生产效率公式为:生产效率=(总产量-损耗)/生产时间2.完工率公式完工率是指生产过程中完成的产品数量占计划生产数量的比例。
完工率公式为:完工率=完成产品数量/计划生产数量3.制造周期公式制造周期是指完成一个产品所需要的时间。
制造周期公式为:制造周期=(开始时间-结束时间)/完成产品数量4.成本公式成本是生产过程中所需要的资源投入,包括物料、人工和设备等。
成本公式为:总成本=物料成本+人工成本+设备成本5.制造周期时间公式制造周期时间是指完成一个产品所需要的总时间,包括加工时间、等待时间和运输时间等。
制造周期时间公式为:制造周期时间=加工时间+等待时间+运输时间6.资源利用率公式资源利用率是指生产过程中所使用的资源占总资源的比例。
资源利用率公式为:资源利用率=生产所使用的资源/总资源7.效率公式效率是指生产过程中实际产出与标准产出之间的比例。
效率公式为:效率=实际产出/标准产出8.容量公式容量是指生产过程中单位时间内能够完成的工作量。
容量公式为:容量=总资源/单位时间9.平均停留时间公式平均停留时间是指在生产过程中产品在其中一工序的平均停留时间。
平均停留时间公式为:平均停留时间=生产时间/生产数量10.时间效率公式时间效率是指单位时间内完成的工作量。
时间效率公式为:时间效率=完成工作量/单位时间以上是IE数据处理常用的公式和方法。
通过对数据进行准确的收集、整理、处理和分析,可以帮助企业发现问题、优化流程,并做出合理的决策,以提高生产效率和降低成本。
IE基础计算方法

2020/11/2
IE基础计算方法
如何计算设备的产能
4. 如果一个产品流程需要经过该设备多次,则WPH可以用以下方法计算 5. 例如:某产品经过设备3次,Batch=25;
6. Step 1 0.5 hour
WPH1=50
HPW1=0.02;
7. Step2 1 hour
WPH2=25
HPW2=0.04;
2020/11/2
IE基础计算方法
效率改善分析见解
先定义下生产线直接效率计算公式:
直接效率=(机型ST*良品数)/纯作业时间; 纯作业时间=生产线直接人员投入时间-无作业时间; 如果数据准确的话,直接效率应该满足以下公式: 直接效率+线体平衡损失+不良率=100%
这样你会说,如果线体平衡率只有60%,那效率最高岂不是不会超过60%? 理论上是这样,但还有其他的因素: 我们的标准工时是针对普通熟练工人而且还考虑了宽放率,生产线实际作业时间有时会比标准工时少, 所以上面的公式也只是起理论参考作用,实际的数据会有点点偏差。 不过有了上面这个工时,我们就知道了如果要提高生产线效率,只要降低:线体平衡损失和不良率即可。
设备产能是由设备能力,工艺流程和产品结构等多个因素决定的。
2020/11/2
IE基础计算方法
如何计算设备的产能
• Equipment metrics(SEMI E79) – Uptime (down, PM); – Available (QC, Engineer use); – Utilization (Idle);
8. Step3 2 hour
WPH3=12.5
HPW3=0.08;
9. HPWt =∑HPWi =0.14
10.WPHt = 1/HPWt = 1/0.14 = 7.1 11.则该设备对应该产品的设备产出速率 WPH = 7.1 wafers/hour
IE基础讲义

定義 1:
工業工程是對人員、物料、設備、能源和信息所組 成的集成系統,進行設計、改善和設置的一門學科. 它綜合運用數學、物理學和社會科學方面的專門知 識和技術,以及工程分析和設計的原理與方法,對該 系統所取得的成果進行確定、預測和評價.
----美國 工業工程師學會(AIIE) 1995年
IE基礎講義
定義 2:
工業工程是對一個組織中人、物料和設備的使用及 其費用作詳細分析研究,這种工作由工業工程師完成, 目的是使組織能夠提高生產率、利潤率和效率.
----美國 大百科全書 1982年版
IE基礎講義
定義 3:
工業工程的目標就是設計一個生產系統及該系統的 控制方法,使它以最低的成本生產具有特定質量水平 的某种或幾种產品,並且這种生產必須是在保證工人 和最終用戶的健康和安全的條件下進行.
省錢的IE
IE基礎講義
IE 常用技術
• 1.工作研究. • 2.生產計劃與控制. • 3.設施規劃與設計. • 4.質量控制與可靠性技術. • 5.工程經濟. • 6.工效學. • 7.組織行為學. • 8.集成信息系統.
IE基礎講義
IE 七大手法
• 抽查法:協助我們去認清問題的地點以及問
題的事實真象.
•3. 數人操作一共同工作.
IE基礎講義
人機法的運用
•1. 發掘空間與等待時間. •2. 使工作平衡. •3. 減少周程時間. •4. 獲得最大的機器利用率. •5. 合適的指派人員與機器.
IE基礎講義
6. 雙手法
• 意義:
•利用雙手操作分析圖,研究雙手在操作時閑置 的狀況,並尋求改善的方法,以充分發揮雙手 的能力.
2. 動 改 法
• 意義: •應用動作經濟原則,改善工作,以達到省力、
服装IE常用计算工式
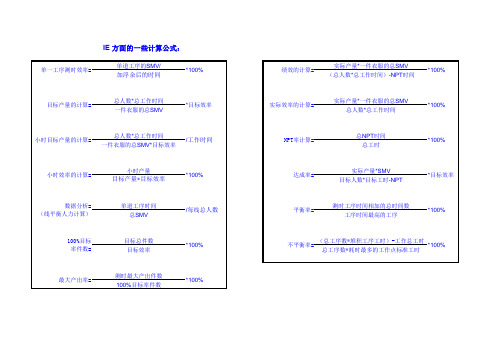
IE 方面的一些计算公式:
单一工序测时效率=单道工序的SMV/
*100%绩效的计算=实际产量
*一件衣服的总SMV
*100%加浮余后的时间(总人数*总工作时间)-NPT时间
目标产量的计算=总人数*总工作时间
*目标效率实际效率的计算=实际产量
*一件衣服的总SMV
*100%一件衣服的总SMV总人数*总工作时间
小时目标产量的计算=
总人数*总工作时间
/工作时间NPT率计算=总
NPT时间
*100%一件衣服的总SMV*目标效率总工时
小时效率的计算=
小时产量
*100%达成率=实际产量
*SMV
*目标效率目标产量*目标效率目标人数*目标工时-NPT
数据分析=单道工序时间
/每线总人数平衡率=测时工序时间相加的总时间数*100%(线平衡人力计算)总SMV工序时间最高的工序
100%目标目标总件数
*100%不平衡率=(总工序数*堆积工序工时)-工作总工时*100%率件数=目标效率总工序数*耗时最多的工作点标准工时
最大产出率=测时最大产出件数
*100% 100%目标率件数。
IE资料基础IE概论课件
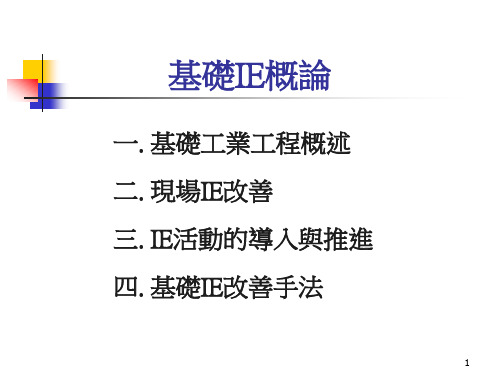
*方法研究
方法研究的主要內容:程序分析—程序是任何個人、機構完成任何工作所需經過的路線和行為;分析是對路線和行為的研究.操作分析—分析以人為主體的工序,使操作者、操作對象、工具三者間合理地布局和配合.動作分析—研究人在進行各種操作時的身體動作,以排除多餘動作、減輕疲勞和提高效率.
標準時間
*通常情況下的標準時間
掌握真實和業確的數據進行分析﹔不放過細少的浪費和改善點﹔遵守解決問題的程序﹔錯了只需要馬上改正﹔不求完美﹐提升到50分也可以馬上行動﹔改善與學習無止境﹔
4.IE的改善意識(1)
7) 兩人的知識大于一人的智慧﹐全員參與才可以共同進步﹔8) 改善不應大量投資﹔9) 積極尋找解決問題的方法而不是不可行的理由﹔10)不要為現狀辯解﹐實事求是﹔
個個方法行不通﹔沒有預算﹔那是件遙遠的事情﹔這事情超過我們的權限﹔不是我的工作﹔沒有時間﹔客戶不會接受﹔
4.現場IE活動的21種抵抗情緒(2)
這違反公司的策略﹔我們沒有准備好﹔我們會虧本的﹔現在也不錯﹔再研究研究﹔不可能﹔太理想化了﹔
4.現場IE活動的21種抵抗情緒(3)
5.一般活動程序(1)
2.IE的定義
我們的定義:“工業工程是通過規劃/改善/創新/診斷等手段﹐發展先進制造生產力﹐整合企業之工程技術/管理技術/制造系統,使工作流程標准化﹑高效化﹐提升企業經營績效” ---DT(II)IE 2003年
2.IE的定義
3.IE的基本意識
成本和效率﹔改善和變革﹔簡化和標准化﹔系統和人本意識﹔
準備動作的時間,例如:前述的確認動作,拿取動作
使產品按客戶意愿發生變化的操作時間
便於操作而發生的時間,例如:翻轉產品,移動身體
操作動作的時間,例如:安裝,鎖緊,剪除等時間
- 1、下载文档前请自行甄别文档内容的完整性,平台不提供额外的编辑、内容补充、找答案等附加服务。
- 2、"仅部分预览"的文档,不可在线预览部分如存在完整性等问题,可反馈申请退款(可完整预览的文档不适用该条件!)。
- 3、如文档侵犯您的权益,请联系客服反馈,我们会尽快为您处理(人工客服工作时间:9:00-18:30)。
1、按工步测 2、5次时间均匀 3、不能打扰员工作业 4、测工时角度能看清员工所有作业 5、异常时间要记录问题点 6、新旧员工识别
步骤二:实物数据分析
3、制作节拍图
瓶颈岗位在哪里?
步骤二:实物数据分析
4、平衡率分析
CT表示完成一次单位作业需要的时间 TT表示实际生产一件产品需要的时间
隐性时间
VA 增值时间 NVA 无价值时间
操作时间(CT)
作业效率的定义
作业效率 =
产出总工时 出勤时间-无效时间
X 100%
∑标准时间ST × 生产台数
=
人 员 × 有效时间 X 100%
弊端: 作业员很难立即了解作业效率的高低。
作业效率的定义
精益生产重视的是改善、提高,参照物最多 的是自己,目标不是精益生产追求的结果,目标 是对精益生产提高的评价,因此精益生产中相对 作业效率来说,人均时产量更为直接。
第一类
第九种浪费: 第九种浪费“人员的浪费”,
定义不是指人员配置多余的浪费, 而是 “仅仅利用了员工的体力, 而将员工的智力拒之门外的浪费”
五五识别法
识别问题
what
where
when
why
who
how
做这个? 在此处做? 要此时做? 由他做? 要这样做?
从必要性发问 从空间、面积发问 从时间柔性发问 从多能、防呆性发问 从方法性发问
步骤六:改善过程
1、装配线人员定岗作业
a) 固定岗(作业员)与移动岗区分 (移动岗位:修理员、物料员、拉长、多能工) b) 由员工自已离岗去拿物料,变为专人配送物料到岗(编
岗位物料配送清单,明确数量/次、频次/天); c) 员工的作业范围要规划合理,减少不必要的走动; d) 员工离岗,设定顶岗人员机制(多能工配置)。
序 号
项目
1 在册人数
2 借入工时
3 借出工时
4 直接工时
5 投入工时
6 能率实绩
7 生产性实绩
取数方法
取该生产线所有人数(助拉以下人员)(各组件/工程不取) 该线所有借入人员的时间 该线所有借出人员的时间 按该线各组件:在“机种”工作表中求和取得 按该线各组件:在“机种”工作表中求和取得 计算公式:量产完成工时/直接工时(各线、系列适用) 计算公式:完成工时/投入工时(系列、机种适用)
∑CT=576.77 TT=13.58
作业时间 线内损失时间
CTmax=11.68
综合损失:46.2% 线内平衡损失:30.45%
TT CT
产线平衡率:69.55%
线外损失时间
产线平衡率=
∑CT 瓶颈节拍时间X工位数量
X 100%
步骤二:实物数据分析
几种生产性向上计算
系统平衡率= 产线平衡率= 工艺平衡率=
活动程序
PD AC
PD AC
P-Plan D-Do C-Check A-Action
活动基本步骤
改善对象选定
现状调查
总结及标准化
效果确认
改善实施
问题点提出 设定改善目标 改善案确立
步骤一:现状调查
选定改善对象
XX工段XX生产线(班) 针对XX品号(系列)进行改善
计划产量
XX台/8H(或XX台/10H)
出勤时间
8H(28800S)或10H(36000S)(是否倒班)
出勤方式
单班/两班/三班
步骤一:现状数据调查
实际节拍时间
=实际出勤时间/实际产量
目前人均时产量
人员配置
出勤方式
步骤二:实物数据分析
1. 编制生产节拍测定表
能够看出每个岗位中的作业内容和作业顺序,所需物料、工作工具都列明
步骤二:实物数据分析
2、物流图制作
物流图是对搬运(布局合理性)、中间库(库存、异常)两项内
。 容平面展示找出改善内容,加快物流,缩短生产周期
步骤三:实物流分析
3、瓶颈工序节拍分析
节拍分析的目的是找出非增值时间的比例,确定非增值项的改善
内容。
步骤四:现状数据汇总
项目
现状
生产方式
手推滚筒线
产量
XX台/8H
目标节拍
29S
认识节拍及计算
• 什么是节拍(Cycle Time) 我们定义的节拍是指从作业开始到作业结
束的时间间隔,不包括作业前的等待时间。
• 实际生产节拍(TT)是指实际生产一个产品的 时间。
认识节拍及计算
工序时间分解
Байду номын сангаас
TT 实际生产节拍时间
Scrap 生产废品时间 Changeover 换型时间 Downtime 停机时间
步骤六:改善过程
1、装配线人员定岗、定置作业
a) 固定岗(作业员)与移动岗区分 (移动岗位:修理员、物料员、拉长、多能工) b) 由员工自已离岗去拿物料,变为专人配送物料到岗(编
岗位物料配送清单,明确数量/次、频次/天); c) 员工的作业范围要规划合理,减少不必要的走动; d) 员工离岗,设定顶岗人员机制(多能工配置)。
∑OCT ∑TT
X 100%
∑CT 瓶颈节拍时间X工位数量
∑VA VAMAX X 工位数量
X 100% X 100%
作业有效率=
∑VA ∑OCT
X 100%
工艺作业有效率 =
∑VA ∑TT
X 100%
步骤三:实物流分析
1、排拉图制作
排拉图是对生产过程做全面的了解,并掌握人员 配置情况。
步骤三:实物流分析
人均时产量=
同机型每小时的产量 实际作业人员
流水线效率改善步骤
IE常用公式一览表
一. 绩效管理常用公式; 1.作业时间使用率=(投入工时-异常工时)/投入工时 =实际工时/投入工时
2.作业者作业效率=产出量╳标准工时/(投入工时-异常工时) =总标准工时/实际作业工时
3.制造生产效率=产出工时/实际作业工时+异常工时 4.公司生产效率=产出工时/投入工时 5.出勤率=出勤人员/編置人员 6.加班率=加班时间/总工时
IE数据处理与计算 公式整理汇集
曾茂青
2011、10、11
课题目录
➢ 识别问题 ➢认识节拍及计算 ➢ 作业效率的定义 ➢ 流水线改善步骤
识别问题
什么是浪费?
◊ 不增值的活动
◊ 增值活动,但所有资源超过“绝对最少”界限的活 动
浪费类别:
第一类:不增值和超出资源的浪费(八大浪费) 第二类:没有开发利用的浪费(人员的浪费)
作业者人数
直接
9
辅助
2
实测时间合计
157
生产线平衡率
62%
在制品数
13
瓶颈工序
工序 岗位1 时间
28S
单位产品生产耗时
5.08M
生产线长度/面积
长度
XX
面积
XX
步骤五:设定目标
以产量提升为目标,人员不变
目标节拍 =实测时间合计/直接人员
以人员减少为目标,产量不变
直接人员 =实测时间合计/目标节拍