改善的四个基本原则
7、改善十大原则及行为规范
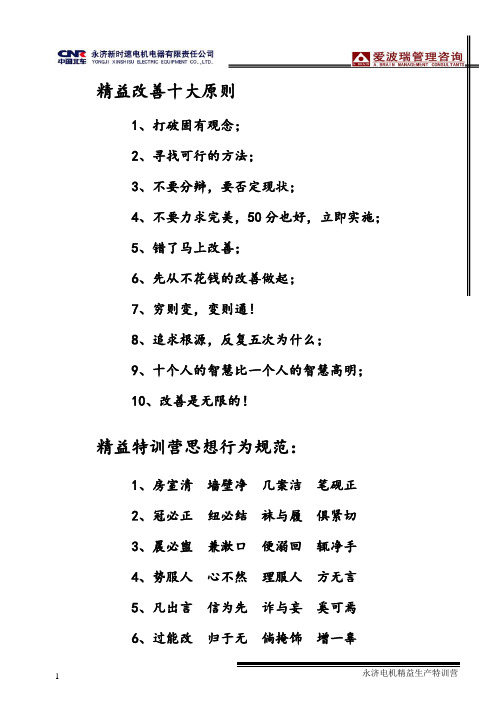
永济电机精益生产特训营
1
精益改善十大原则
1、打破固有观念;
2、寻找可行的方法;
3、不要分辩,要否定现状;
4、不要力求完美,50分也好,立即实施;
5、错了马上改善;
6、先从不花钱的改善做起;
7、穷则变,变则通!
8、追求根源,反复五次为什么;
9、十个人的智慧比一个人的智慧高明;
10、改善是无限的!
精益特训营思想行为规范:
1、房室清 墙壁净 几案洁 笔砚正
2、冠必正 纽必结 袜与履 俱紧切
3、晨必盥 兼漱口 便溺回 辄净手
4、势服人 心不然 理服人 方无言
5、凡出言 信为先 诈与妄 奚可焉
6、过能改 归于无 倘掩饰 增一辜。
现场改善四大原则概述

• (1)取消(Eliminate)——取消不必要的工序、动作、
操作,
•
这是不需要投资的一种改进,是改进的最高原则。
• (2)合并(Combine)——对于无法取消而又有必要的
,看是否能够合并,以达到省时简化的目的。
• (3)重排(Rearrange)——经过取消、合并后,可再
根据“何人、何地、何时”三个提问进行重排,使其能有
•提升效率﹐符合人因工程原理﹐提升員工士氣
“ECRS”改善原则 – 重排
• (3)重排(Rearrange)——经过取消、合并后, 可再根据“何人、何時、何地”三个提问进行重 排,使其能有最佳的組合.
“ECRS”改善原则 – 簡化
• (4)简化(Simple)——经过取消、合并、重排后的必要 工作,就可考虑能否采用最简单的方法及设备,以节省 人力、时间及费用。
• (2)根據2005/8/7~2005/8/9連續統 計1#﹐2#﹐3#﹐6#﹐10#不良品數 為0PCS﹐總投入數148,570PCS,不 良率0
• 對策﹕
• 全檢工站改為抽檢(定量追溯處理 )﹕
• (1)取消該工站﹐減少2人
• (2)增加品管抽檢(每箱抽5層(托盤 )﹐每層3PCS)
改善案例:電氣元件測試取消改善案.
连接更合理 使之更简单 去除多余动作
①把检查工程移到前面。 ②用台车搬运代替徒手搬运。 更换材料。
①改变布置,使动作边境更顺 。
②使机器操作更简单。 ③使零件标准化,减少材料种
类。
改善的优先顺序
•5.同工:設備和人員同步作業,不可有停滯、空閑.
生產線平衡實戰技法: 1.“ECRS”改善手法.
喇叭線 打結,並 套袋,需 專人拆 包裝.
精益生产改善的定义和改善13个基本点,不是每个公司都能做到!

精益生产改善的定义和改善13个基本点,不是每个公司都能做到!一、改善的定义精益生产思想的最后一个基本思想是“尽善尽美”。
“改善”活动是精益生产方式各目标顺利实现的基本的支撑,是精益生产方式的坚固基石,而且也是精益生产方式所追求的目标。
在1993年版(牛津英文词典)中“改善(Kaizen)”的定义:一种企业经营理念。
用以持续不断地改进工作方法与人员的效率等。
也可以同时理解:①改善是为达成工作的目的,追求更好的手段、方法。
②改善就是超越目前所有的水平。
改善有个说法就是,跟对方谈话5分钟,还没有出现过改善的字不会是精益的,因为改善的观念已经深入精益管理人的人心,习以为常,没有人觉得我或者别人发现我自己工作中的过失后或者可改进之处是可耻的事情。
这个状态在今天是合理的,是高效低成本的,所以主动去改善是保持高竞争力的最好方法。
要想做到尽善尽美,仅仅靠精益生产中的那些用法、工具是不够的。
还需要有持续不断人人参与的改善机制,密切协同无缝搭接的团队合作精神,异体同构离而不散的供应链系统,全员全方向全过程推动保障品质的TQM(全面质量管理)机制。
也就是下图中四个部分。
而唯有这四个方面的协同推动,整个企业的运作才有可能朝尽善尽美的方向发展。
二、“改善”的13个基本要点1、领导者要以身作则不要认为“改善的工作是部下的事,上司不必去做这些”。
事实上,不论是领导者还是员工,都必须要能致力于改善。
如果他自己没有办法首先身体力行,那么其部下也就无法跟着前进。
作为领导者,每天都要督促自己力行改善,同时也要常常要求下属人员“改善,再改善”,从而激发和提高下属人员改善工作的意愿和情绪。
当然,领导者所进行的改善与生产现场一线作业人员所进行的改善的主题是不相同的。
现场作业人员的改善是以作业程序和操作方法为主,而领导者则以组织、制度、管理体制等软件方面的改善为主。
尽管两者各自的具体改善对象和内容不相同,以身作则,并不断督促部下要“改善,再改善”,但是上级人员如能为人表率、那么下属人员就会增强改善意识,自觉贯彻上级的改善意图。
企业提案改善原则

企业提案改善原则一、明确目标和问题企业提案改善的第一个原则是明确目标和问题。
在提出任何改善方案之前,必须清楚地了解当前的问题和目标。
只有明确问题,才能找到解决方案。
因此,企业提案改善的第一步是对问题进行充分的分析和理解,确保所有的相关信息都已经准确收集,并明确目标是什么。
二、多方参与和反馈企业提案改善的第二个原则是多方参与和反馈。
改善方案应该不仅包括领导者的意见,还应该充分考虑员工的反馈和建议。
因为员工是最直接面对问题的人,他们的经验和观点对于解决问题非常宝贵。
因此,在制定改善方案时,应该积极邀请员工参与讨论,并鼓励他们提供自己的见解和建议。
三、优先权和效益分析企业提案改善的第三个原则是优先权和效益分析。
在提出改善方案时,应该根据不同的问题和目标,对各种可能的方案进行优先级排序。
优先级的确定应基于改善的效益和成本。
效益分析是评估方案的潜在好处和结果,成本分析是评估方案的实施成本和资源需求。
通过优先级和效益分析,可以确保有限的资源被正确分配并产生最大的效益。
四、阶段实施和测试企业提案改善的第四个原则是阶段实施和测试。
在实施改善方案之前,应该进行小规模的测试和试验,以验证该方案的可行性。
通过逐步实施和测试,可以识别和解决可能出现的问题,并确保改善方案能够在实际运行中有效地工作。
此外,阶段实施和测试也有助于员工适应和接受改变,减少潜在的阻力和负面影响。
五、监测和评估企业提案改善的第五个原则是监测和评估。
改善方案的实施并不是最终目标,企业应该对改善方案进行持续的监测和评估,以确保它们能够持续产生预期的效果。
监测和评估可以帮助企业及时发现问题并采取相应的纠正措施,同时也可以为进一步的改进提供有价值的反馈和经验教训。
六、沟通和培训企业提案改善的第六个原则是沟通和培训。
任何改变都需要员工的理解和支持,因此在实施改善方案之前,应该与员工进行充分的沟通,并提供必要的培训,以确保员工理解和掌握改进的内容和方法。
通过有效的沟通和培训,可以增加员工的参与度,减少误解和不确定性,并提高改善方案的成功实施率。
持续改善的四大要素
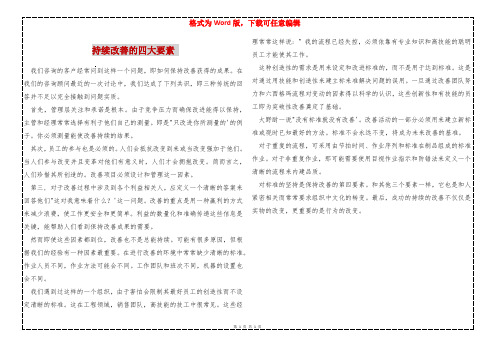
定清晰的标准。这在工程领域,销售团队,高技能的技工中很常见。这些经
第1页共1页
首先,管理层关注和承诺是根本。由于竞争压力而确保改进能得以保持, 主管和经理常常选择有利于他们自己的测量。即是"只改进你所测量的'的例 子。你必须测量能使改善持续的结果。
其次,员工的参与也是必须的。人们会抵抗改变到来或当改变强加于他们。 当人们参与改变并且变革对他们有意义时,人们才会拥抱改变。简而言之, 人们珍惜其所创造的。改善项目必须设计和管理这一因素。
格式为 WLeabharlann rd 版,下载可任意编辑持续改善的四大要素
理常常这样说: " 我的流程已经失控,必须依靠有专业知识和高技能的聪明 员工才能使其工作。
我们咨询的客户经常问到这样一个问题,即如何保持改善获得的成果。在 我们的咨询顾问最近的一次讨论中,我们达成了下列共识,即三种传统的回 答并不足以完全接触到问题实质。
大野耐一说"没有标准就没有改善'。改善活动的一部分必须用来建立新标 准或现时已知最好的方法。标准不会永远不变,将成为未来改善的基准。
对于重复的流程,可采用由节拍时间、作业序列和标准在制品组成的标准 作业。对于非重复作业,那可能需要使用目视作业指示和防错法来定义一个 清晰的流程来内建品质。
对标准的坚持是保持改善的第四要素。和其他三个要素一样,它也是和人 紧密相关而常常要求组织中文化的转变。最后,成功的持续的改善不仅仅是 实物的改变,更重要的是行为的改变。
关键,能帮助人们看到保持改善成果的需要。
然而即使这些因素都到位,改善也不是总能持续。可能有很多原因,但根
据我们的经验有一种因素最重要。在进行改善的环境中常常缺少清晰的标准。
作业人员不同,作业方法可能会不同。工作团队和班次不同,机器的设置也
JIT改善基本原则介绍
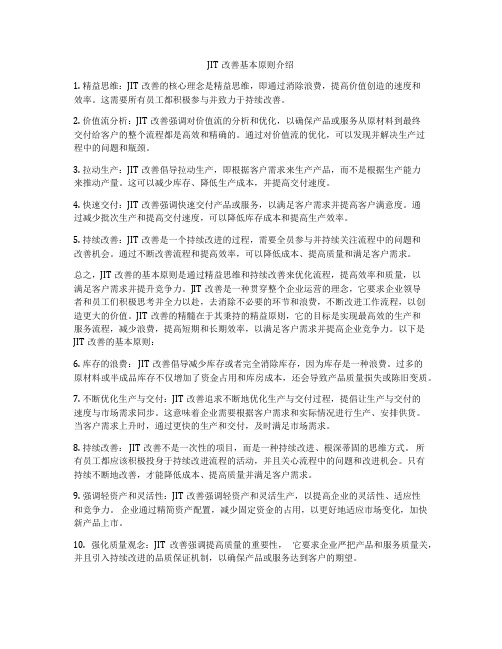
JIT改善基本原则介绍1. 精益思维:JIT改善的核心理念是精益思维,即通过消除浪费,提高价值创造的速度和效率。
这需要所有员工都积极参与并致力于持续改善。
2. 价值流分析:JIT改善强调对价值流的分析和优化,以确保产品或服务从原材料到最终交付给客户的整个流程都是高效和精确的。
通过对价值流的优化,可以发现并解决生产过程中的问题和瓶颈。
3. 拉动生产:JIT改善倡导拉动生产,即根据客户需求来生产产品,而不是根据生产能力来推动产量。
这可以减少库存、降低生产成本,并提高交付速度。
4. 快速交付:JIT改善强调快速交付产品或服务,以满足客户需求并提高客户满意度。
通过减少批次生产和提高交付速度,可以降低库存成本和提高生产效率。
5. 持续改善:JIT改善是一个持续改进的过程,需要全员参与并持续关注流程中的问题和改善机会。
通过不断改善流程和提高效率,可以降低成本、提高质量和满足客户需求。
总之,JIT改善的基本原则是通过精益思维和持续改善来优化流程,提高效率和质量,以满足客户需求并提升竞争力。
JIT改善是一种贯穿整个企业运营的理念,它要求企业领导者和员工们积极思考并全力以赴,去消除不必要的环节和浪费,不断改进工作流程,以创造更大的价值。
JIT改善的精髓在于其秉持的精益原则,它的目标是实现最高效的生产和服务流程,减少浪费,提高短期和长期效率,以满足客户需求并提高企业竞争力。
以下是JIT改善的基本原则:6. 库存的浪费: JIT改善倡导减少库存或者完全消除库存,因为库存是一种浪费。
过多的原材料或半成品库存不仅增加了资金占用和库房成本,还会导致产品质量损失或陈旧变质。
7. 不断优化生产与交付:JIT改善追求不断地优化生产与交付过程,提倡让生产与交付的速度与市场需求同步。
这意味着企业需要根据客户需求和实际情况进行生产、安排供货。
当客户需求上升时,通过更快的生产和交付,及时满足市场需求。
8. 持续改善: JIT改善不是一次性的项目,而是一种持续改进、根深蒂固的思维方式。
改善的五大原则
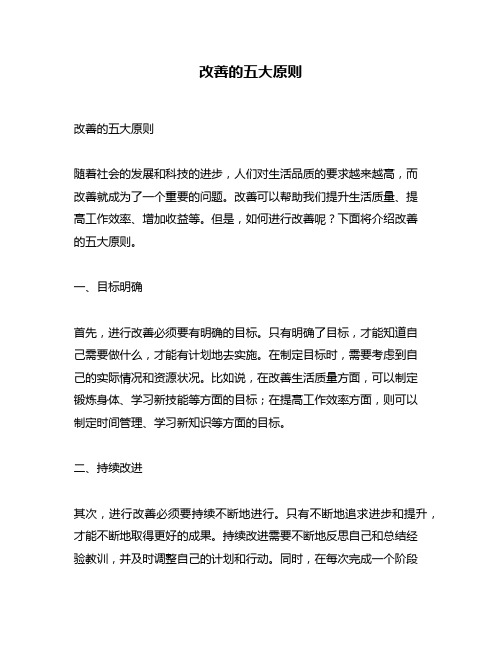
改善的五大原则改善的五大原则随着社会的发展和科技的进步,人们对生活品质的要求越来越高,而改善就成为了一个重要的问题。
改善可以帮助我们提升生活质量、提高工作效率、增加收益等。
但是,如何进行改善呢?下面将介绍改善的五大原则。
一、目标明确首先,进行改善必须要有明确的目标。
只有明确了目标,才能知道自己需要做什么,才能有计划地去实施。
在制定目标时,需要考虑到自己的实际情况和资源状况。
比如说,在改善生活质量方面,可以制定锻炼身体、学习新技能等方面的目标;在提高工作效率方面,则可以制定时间管理、学习新知识等方面的目标。
二、持续改进其次,进行改善必须要持续不断地进行。
只有不断地追求进步和提升,才能不断地取得更好的成果。
持续改进需要不断地反思自己和总结经验教训,并及时调整自己的计划和行动。
同时,在每次完成一个阶段后也需要对自己的成果进行评估和反馈,以便更好地指导下一步的行动。
三、重视细节第三,进行改善必须要注重细节。
细节决定成败,只有把每一个细节都做好,才能取得更好的效果。
在注重细节方面,需要注意以下几点:一是要认真分析问题,找到问题的根源;二是要仔细制定计划和行动方案,并严格按照计划执行;三是要注重执行过程中的每一个环节,并及时发现和解决问题。
四、合理利用资源第四,进行改善必须要合理利用资源。
资源包括时间、金钱、人力等方面。
在利用资源方面,需要注意以下几点:一是要认真分析自己拥有的资源状况,并制定适合自己的计划;二是要合理规划时间和金钱等资源的使用;三是要充分利用个人网络和人际关系等人力资源。
五、持之以恒最后,进行改善必须要持之以恒。
只有坚持不懈地追求目标,才能取得更好的成果。
在持之以恒方面,需要注意以下几点:一是要保持积极向上的心态,不断地激励自己;二是要克服困难和挫折,不轻易放弃;三是要保持耐心和毅力,坚持到底。
总之,改善是一个需要长期投入和不断努力的过程。
只有在目标明确、持续改进、重视细节、合理利用资源、持之以恒等五个方面做好了工作,才能取得更好的成果。
现场改善的基本原则
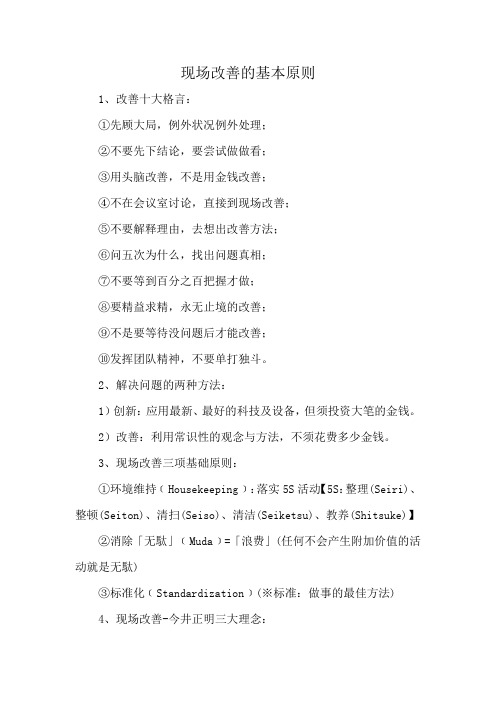
现场改善的基本原则1、改善十大格言:①先顾大局,例外状况例外处理;②不要先下结论,要尝试做做看;③用头脑改善,不是用金钱改善;④不在会议室讨论,直接到现场改善;⑤不要解释理由,去想出改善方法;⑥问五次为什么,找出问题真相;⑦不要等到百分之百把握才做;⑧要精益求精,永无止境的改善;⑨不是要等待没问题后才能改善;⑩发挥团队精神,不要单打独斗。
2、解决问题的两种方法:1)创新:应用最新、最好的科技及设备,但须投资大笔的金钱。
2)改善:利用常识性的观念与方法,不须花费多少金钱。
3、现场改善三项基础原则:①环境维持﹝Housekeeping﹞:落实5S活动【5S:整理(Seiri)、整顿(Seiton)、清扫(Seiso)、清洁(Seiketsu)、教养(Shitsuke)】②消除「无駄」﹝Muda﹞=「浪费」(任何不会产生附加价值的活动就是无駄)③标准化﹝Standardization﹞(※标准:做事的最佳方法)4、现场改善-今井正明三大理念:①重视现场:任何问题都要到现场去了解,当场用最简单、最不花钱的方式来寻求「改善」,而非以投入资金,从外界购买最新的科技设备来提升工厂的水平。
②最简单的「改善」方式:日本式的TQM、TPM、JIT、5S、QCC及提案建议...等。
③高阶层的承诺﹝Commitment﹞:所谓承诺不是指应允某一件事,而是说从事这些改善活动必需要长久、持续地做下去,这不是一年、二年之事,而是一辈子的事。
5、日本式改善活动-「五心」:①信心:相信这些改善活动会带给你好处;②决心:下定决心赶快去做,不要犹豫不决;③耐心:要永远持续做下去,成果自然呈现;④关心:对员工表示出你的关怀及重视之意;⑤爱心:多用鼓励的方式来鼓舞员工士气。
6、主要的改善观念:①改善与管理;②过程与结果;③遵循PDCA循环/SDCA循环;④品质第一;⑤用数据说话;⑥下一工序就是顾客。
- 1、下载文档前请自行甄别文档内容的完整性,平台不提供额外的编辑、内容补充、找答案等附加服务。
- 2、"仅部分预览"的文档,不可在线预览部分如存在完整性等问题,可反馈申请退款(可完整预览的文档不适用该条件!)。
- 3、如文档侵犯您的权益,请联系客服反馈,我们会尽快为您处理(人工客服工作时间:9:00-18:30)。
改善的四个基本原则一、同时使用双手
1.双手同时进行动作,同时结束动作。
2.双手运动路线为对称时,将两手对称的向相反的方向运用。
3.将材料和部品排成可以同时用量手抓取的布置形式。
4.使用不用手抬或使用最少的力量来进行处理的装置。
5.灵活运用使用脚的装置。
二、减少动作要素的个数
1.更换动作顺序。
2.将两个以上的动作结合起来。
3.拿起工具就可以即可进行作业的状态。
4.使用处理材料和部品较容易的容器或器具。
5.将两个以上的工具合并为一。
6.利用引导器具或夹具给对象物正确地位置。
三、缩短移动距离
1.缩短使用身体部位的活动范围。
2.尽可能将材料,部品,工具防御近处布置。
3.利用重力落下的装置。
四、较少疲劳
1.使用最不容易产生疲劳的身体部位。
2.更换动作时用较圆滑的动作完成。
3.确定适当的作业高度。
4.烟气灰尘污水等应能够排放到车间外。
5.对象物被长时间抓住固定时,应利用固定装置。
6.尽量使用动力装置。