镁碳砖
镁碳砖分类
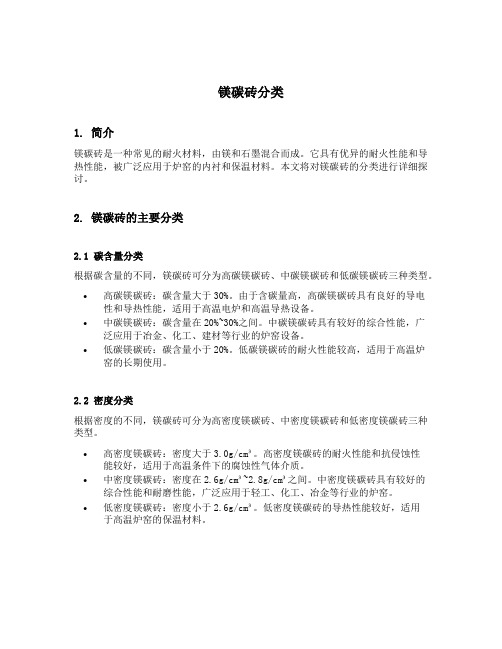
镁碳砖分类1. 简介镁碳砖是一种常见的耐火材料,由镁和石墨混合而成。
它具有优异的耐火性能和导热性能,被广泛应用于炉窑的内衬和保温材料。
本文将对镁碳砖的分类进行详细探讨。
2. 镁碳砖的主要分类2.1 碳含量分类根据碳含量的不同,镁碳砖可分为高碳镁碳砖、中碳镁碳砖和低碳镁碳砖三种类型。
•高碳镁碳砖:碳含量大于30%。
由于含碳量高,高碳镁碳砖具有良好的导电性和导热性能,适用于高温电炉和高温导热设备。
•中碳镁碳砖:碳含量在20%~30%之间。
中碳镁碳砖具有较好的综合性能,广泛应用于冶金、化工、建材等行业的炉窑设备。
•低碳镁碳砖:碳含量小于20%。
低碳镁碳砖的耐火性能较高,适用于高温炉窑的长期使用。
2.2 密度分类根据密度的不同,镁碳砖可分为高密度镁碳砖、中密度镁碳砖和低密度镁碳砖三种类型。
•高密度镁碳砖:密度大于3.0g/cm³。
高密度镁碳砖的耐火性能和抗侵蚀性能较好,适用于高温条件下的腐蚀性气体介质。
•中密度镁碳砖:密度在2.6g/cm³~2.8g/cm³之间。
中密度镁碳砖具有较好的综合性能和耐磨性能,广泛应用于轻工、化工、冶金等行业的炉窑。
•低密度镁碳砖:密度小于2.6g/cm³。
低密度镁碳砖的导热性能较好,适用于高温炉窑的保温材料。
3. 镁碳砖的应用领域3.1 高温炉窑镁碳砖由于其良好的耐火性能和导热性能,在高温炉窑中得到广泛应用。
例如钢铁冶炼中的转炉、电炉和蓄热炉,情况高且易受腐蚀的环境中,高碳镁碳砖是首选材料。
而在一些保温要求较高的炉窑中,可以选择低密度镁碳砖作为保温层材料。
3.2 腐蚀性气体介质某些特殊环境中含有腐蚀性气体介质,例如氯化钠、氯化铝等化学物质。
在这些环境中,高密度镁碳砖能够提供良好的抗侵蚀性能,减少材料的损耗。
3.3 轻工行业镁碳砖还广泛应用于轻工行业,如玻璃窑炉、水泥旋窑等。
在这些设备中,中密度镁碳砖能够提供良好的耐磨性能,在高温和磨损的环境下保持较长的使用寿命。
镁碳砖1

• 该砖的技术路线是,在高铝质料的基质中,参加 尖晶石材料并参加MgO细粉,以便在高温下形成 镁铝尖晶石,提高砖的使用性能。为提高砖的抗 渣性、抗热震性,参加适量的碳素材料,研制成 功了铝镁碳质不烧砖,简称铝镁碳砖。 • 铝镁碳砖用的原材料,根据钢包大小和使用条件 而定。一般中小型钢包采用低档原材料,用水玻 璃做结合剂制砖;大中型钢包,特别是连铸和炉 外精炼用的钢包,必须选择优质原材料并用树脂 结合剂制砖,方可满足使用要求。
• 在本钢、新余使用效果良好,受到了用户的好评,同时被 多家耐材企业所采购使用,良好的使用性能为公司创造效 益同时,又为公司带来了很高的声誉。以下为我公司刚玉 自流料的性能:
刚玉自流料的性能
编号 1#
化学成分/%
耐压强度/MPa 抗折强度/MPa 烧后线变化/% 水用量/%
Al2O3 110℃
1500℃ 110℃
显气孔率/%
体积密度/g.cm-3
17
2.94
刚玉自流料
• 自流耐火浇注料(S.F.C)是一种高触变性的拌合 料靠自身重力作用而能流动和脱气的材料。我公 司研制的刚玉自流料具有以下特点:
• (1)浇注料性能与同材质振动型低水泥系列耐火浇注料相似或略好 些。 • (2)无需振动设备,自流性好,因此能减少施工费用,无噪声污染, 降低劳动强度。 • (3)高温性能良好,抗侵蚀性强,抗热震性、耐剥落性强。
无碳预制块(座砖)
• 预制块是不定形耐火材料中的定型产品。该类制 品与现场施工的不定性耐火材料相比,具有外形 尺寸准确、性能稳定、施工周期短等优点。与烧 成耐火砖相比,制品成品率高,不用烧成窑炉, 可节约能源,生产成本低和性能优良。 • 我公司研制开发的无碳刚玉尖晶石预制块外形尺 寸准确、性能稳定、使用寿命高,在武钢三炼钢 使用效果良好,受到了用户好评。 • 无碳预制块的主要性能如下表所示:
镁碳砖生产工艺流程

镁碳砖生产工艺流程镁碳砖是一种高温材料,由镁和碳两种元素组成,具有优良的导热性能和耐高温性能,在航空、航天、电子等领域有着广泛的应用。
下面将介绍镁碳砖的生产工艺流程。
镁碳砖的生产工艺流程主要包括原料准备、原料混合、压制成型、烘干、煅烧、研磨抛光等步骤。
具体流程如下:1.原料准备:镁碳砖的主要原料为氧化镁(MgO)和石墨(C),所选用的原料应具备高纯度和细度。
一般按照一定配比将氧化镁和石墨粉末分别称量。
2.原料混合:将称量好的氧化镁和石墨粉末放入混合机中进行均匀混合,以保证材料的均一性。
3.压制成型:将混合好的材料放入压制机中,根据需要的砖块尺寸和形状,选择相应的模具进行压制成型。
压制过程中,通过控制压力和时间,使材料充分结合成型。
4.烘干:将成型的砖块放入烘干炉中进行烘干处理。
烘干的目的是去除材料中的水分和有机物,提高材料的强度和稳定性。
烘干温度和时间根据具体材料和砖块厚度来确定。
5.煅烧:将烘干后的砖块放入电炉或隧道窑中进行煅烧处理。
煅烧温度一般在2000℃以上,时间和温度的选择要根据具体材料和砖块的要求来确定。
煅烧过程中,镁粉和石墨将发生化学反应,生成镁碳化合物,并与氧化镁形成致密的结合。
6.研磨抛光:煅烧后的砖块需要进行表面的研磨和抛光处理,以提高其表面光洁度和尺寸精度。
一般采用机械研磨或化学抛光的方法进行处理。
以上就是镁碳砖的生产工艺流程,每个步骤均对最终产品的质量和性能有着重要影响。
生产过程中需要严格控制原料比例、混合均匀度、压制力度、烘干温度和时间、煅烧温度和时间等参数,以确保产品的质量和性能达到要求。
镁碳砖介绍
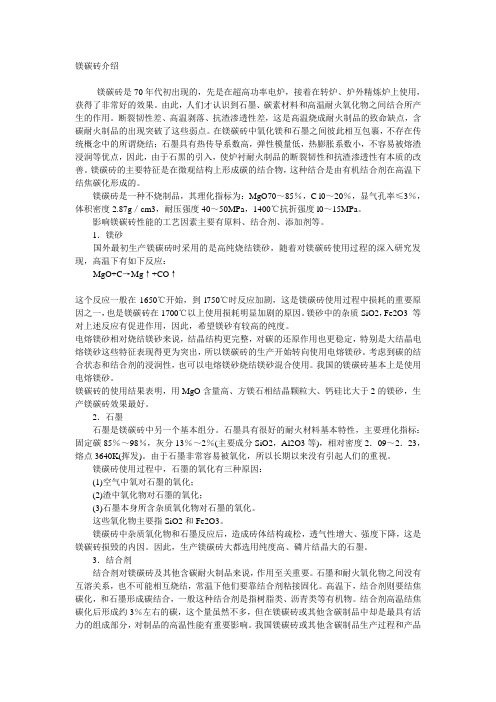
镁碳砖介绍镁碳砖是70年代初出现的,先是在超高功率电炉,接着在转炉、炉外精炼炉上使用,获得了非常好的效果。
由此,人们才认识到石墨、碳素材料和高温耐火氧化物之间结合所产生的作用。
断裂韧性差、高温剥落、抗渣渗透性差,这是高温烧成耐火制品的致命缺点,含碳耐火制品的出现突破了这些弱点。
在镁碳砖中氧化镁和石墨之间彼此相互包裹,不存在传统概念中的所谓烧结;石墨具有热传导系数高,弹性模量低,热膨胀系数小,不容易被熔渣浸润等优点,因此,由于石黑的引入,使炉衬耐火制品的断裂韧性和抗渣渗透性有本质的改善。
镁碳砖的主要特征是在微观结构上形成碳的结合物,这种结合是由有机结合剂在高温下结焦碳化形成的。
镁碳砖是一种不烧制品,其理化指标为:MgO70~85%,C l0~20%,显气孔率≤3%,体积密度2.87g/cm3,耐压强度40~50MPa,1400℃抗折强度l0~15MPa。
影响镁碳砖性能的工艺因素主要有原料、结合剂、添加剂等。
1.镁砂国外最初生产镁碳砖时采用的是高纯烧结镁砂,随着对镁碳砖使用过程的深入研究发现,高温下有如下反应:MgO+C→Mg↑+CO↑这个反应一般在1650℃开始,到l750℃时反应加剧,这是镁碳砖使用过程中损耗的重要原因之一,也是镁碳砖在1700℃以上使用损耗明显加剧的原因。
镁砂中的杂质SiO2,Fe2O3 等对上述反应有促进作用,因此,希望镁砂有较高的纯度。
电熔镁砂相对烧结镁砂来说,结晶结构更完整,对碳的还原作用也更稳定,特别是大结晶电熔镁砂这些特征表现得更为突出,所以镁碳砖的生产开始转向使用电熔镁砂。
考虑到碳的结合状态和结合剂的浸润性,也可以电熔镁砂烧结镁砂混合使用。
我国的镁碳砖基本上是使用电熔镁砂。
镁碳砖的使用结果表明,用MgO含量高、方镁石相结晶颗粒大、钙硅比大于2的镁砂,生产镁碳砖效果最好。
2.石墨石墨是镁碳砖中另一个基本组分。
石墨具有很好的耐火材料基本特性,主要理化指标:固定碳85%~98%,灰分13%~2%(主要成分SiO2,Al2O3等),相对密度2.09~2.23,熔点3640K(挥发)。
镁砖生产工艺流程
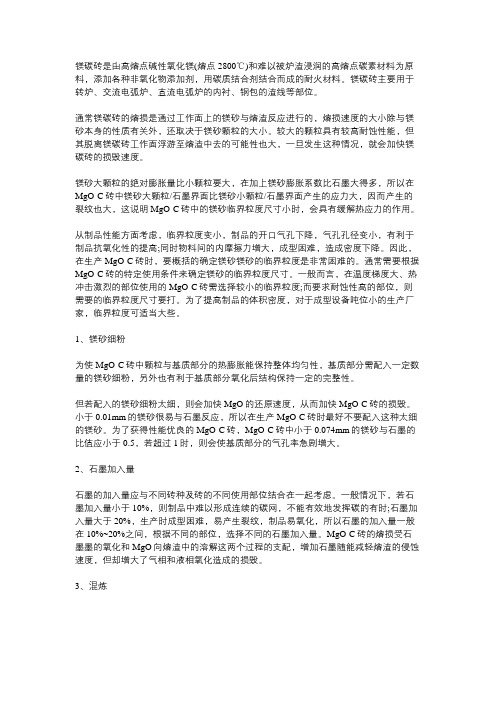
镁碳砖是由高熔点碱性氧化镁(熔点2800℃)和难以被炉渣浸润的高熔点碳素材料为原料,添加各种非氧化物添加剂,用碳质结合剂结合而成的耐火材料。
镁碳砖主要用于转炉、交流电弧炉、直流电弧炉的内衬、钢包的渣线等部位。
通常镁碳砖的熔损是通过工作面上的镁砂与熔渣反应进行的,熔损速度的大小除与镁砂本身的性质有关外,还取决于镁砂颗粒的大小。
较大的颗粒具有较高耐蚀性能,但其脱离镁碳砖工作面浮游至熔渣中去的可能性也大,一旦发生这种情况,就会加快镁碳砖的损毁速度。
镁砂大颗粒的绝对膨胀量比小颗粒要大,在加上镁砂膨胀系数比石墨大得多,所以在MgO-C砖中镁砂大颗粒/石墨界面比镁砂小颗粒/石墨界面产生的应力大,因而产生的裂纹也大,这说明MgO-C砖中的镁砂临界粒度尺寸小时,会具有缓解热应力的作用。
从制品性能方面考虑,临界粒度变小,制品的开口气孔下降,气孔孔径变小,有利于制品抗氧化性的提高;同时物料间的内摩擦力增大,成型困难,造成密度下降。
因此,在生产MgO-C砖时,要概括的确定镁砂镁砂的临界粒度是非常困难的。
通常需要根据MgO-C砖的特定使用条件来确定镁砂的临界粒度尺寸。
一般而言,在温度梯度大、热冲击激烈的部位使用的MgO-C砖需选择较小的临界粒度;而要求耐蚀性高的部位,则需要的临界粒度尺寸要打。
为了提高制品的体积密度,对于成型设备吨位小的生产厂家,临界粒度可适当大些。
1、镁砂细粉为使MgO-C砖中颗粒与基质部分的热膨胀能保持整体均匀性,基质部分需配入一定数量的镁砂细粉,另外也有利于基质部分氧化后结构保持一定的完整性。
但若配入的镁砂细粉太细,则会加快MgO的还原速度,从而加快MgO-C砖的损毁。
小于0.01mm的镁砂很易与石墨反应,所以在生产MgO-C砖时最好不要配入这种太细的镁砂。
为了获得性能优良的MgO-C砖,MgO-C砖中小于0.074mm的镁砂与石墨的比值应小于0.5,若超过1时,则会使基质部分的气孔率急剧增大。
2、石墨加入量石墨的加入量应与不同砖种及砖的不同使用部位结合在一起考虑。
镁碳砖生产工艺
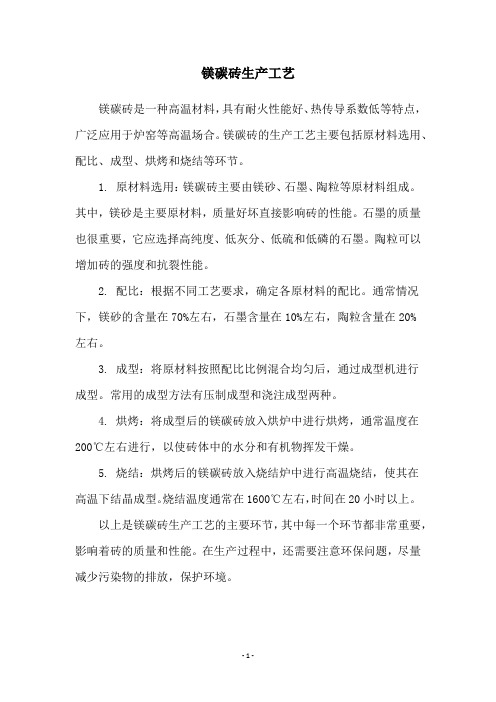
镁碳砖生产工艺
镁碳砖是一种高温材料,具有耐火性能好、热传导系数低等特点,广泛应用于炉窑等高温场合。
镁碳砖的生产工艺主要包括原材料选用、配比、成型、烘烤和烧结等环节。
1. 原材料选用:镁碳砖主要由镁砂、石墨、陶粒等原材料组成。
其中,镁砂是主要原材料,质量好坏直接影响砖的性能。
石墨的质量也很重要,它应选择高纯度、低灰分、低硫和低磷的石墨。
陶粒可以增加砖的强度和抗裂性能。
2. 配比:根据不同工艺要求,确定各原材料的配比。
通常情况下,镁砂的含量在70%左右,石墨含量在10%左右,陶粒含量在20%
左右。
3. 成型:将原材料按照配比比例混合均匀后,通过成型机进行
成型。
常用的成型方法有压制成型和浇注成型两种。
4. 烘烤:将成型后的镁碳砖放入烘炉中进行烘烤,通常温度在200℃左右进行,以使砖体中的水分和有机物挥发干燥。
5. 烧结:烘烤后的镁碳砖放入烧结炉中进行高温烧结,使其在
高温下结晶成型。
烧结温度通常在1600℃左右,时间在20小时以上。
以上是镁碳砖生产工艺的主要环节,其中每一个环节都非常重要,影响着砖的质量和性能。
在生产过程中,还需要注意环保问题,尽量减少污染物的排放,保护环境。
- 1 -。
制作镁碳砖的工艺要点
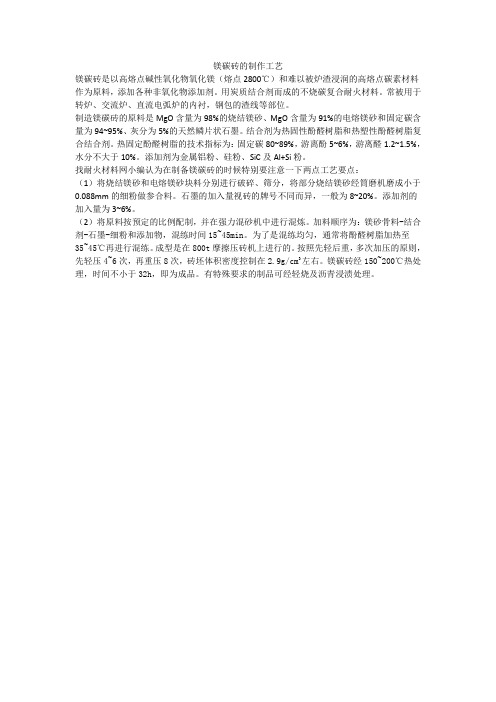
镁碳砖的制作工艺
镁碳砖是以高熔点碱性氧化物氧化镁(熔点2800℃)和难以被炉渣浸润的高熔点碳素材料作为原料,添加各种非氧化物添加剂。
用炭质结合剂而成的不烧碳复合耐火材料。
常被用于转炉、交流炉、直流电弧炉的内衬,钢包的渣线等部位。
制造镁碳砖的原料是MgO含量为98%的烧结镁砂、MgO含量为91%的电熔镁砂和固定碳含量为94~95%、灰分为5%的天然鳞片状石墨。
结合剂为热固性酚醛树脂和热塑性酚醛树脂复合结合剂。
热固定酚醛树脂的技术指标为:固定碳80~89%,游离酚5~6%,游离醛1.2~1.5%,水分不大于10%。
添加剂为金属铝粉、硅粉、SiC及Al+Si粉。
找耐火材料网小编认为在制备镁碳砖的时候特别要注意一下两点工艺要点:
(1)将烧结镁砂和电熔镁砂块料分别进行破碎、筛分,将部分烧结镁砂经筒磨机磨成小于0.088mm的细粉做参合料。
石墨的加入量视砖的牌号不同而异,一般为8~20%。
添加剂的加入量为3~6%。
(2)将原料按预定的比例配制,并在强力混砂机中进行混炼。
加料顺序为:镁砂骨料-结合剂-石墨-细粉和添加物,混练时间15~45min。
为了是混练均匀,通常将酚醛树脂加热至
35~45℃再进行混练。
成型是在800t摩擦压砖机上进行的。
按照先轻后重,多次加压的原则,先轻压4~6次,再重压8次,砖坯体积密度控制在2.9g/cm3左右。
镁碳砖经150~200℃热处理,时间不小于32h,即为成品。
有特殊要求的制品可经轻烧及沥青浸渍处理。
镁碳砖 研究

低碳镁碳砖的实验研究1镁碳砖发展概况MgO–C砖是20世纪70年代兴起的新型耐火材料,最早由日本九洲耐火材料公司渡边明首先开发,它是以镁砂(高温烧结,具有耐火度高、抗热震性优良和抗侵蚀能力强等优良特性而被广泛应用于钢铁企业,如转炉炼钢和电炉炼钢[1]。
我国在1980前后年开始研究含碳耐火材料[2],并被列入国家“七五”(1985~1989)科技攻关项目。
1987年鞍钢三炼钢厂在转炉上试用MgO–C砖后,仅用一年时间就超额完成了“七五”转炉炉龄达千次的攻关目标。
发展到目前,全国各大中小钢厂已普遍推广使用MgO–C 质耐火材料作为转炉和电炉的炉衬。
随着冶炼技术的进步对耐火材料的新要求,低碳镁碳耐火材料成为镁碳耐火材料新的发展热点。
低碳MgO–C砖一般是指总含碳量不超过8%、由镁砂与石墨通过有机结合剂结合而成的MgO–C砖,降低碳含量可明显降低材料的热导率[3]。
近年来,对精炼钢包用低碳量、性能优异的低碳镁碳砖的开发受到国内外业界的重视,这方面的研究开发工作已取得一定的成果,展现了良好的发展前景。
镁碳砖既保持了碱性耐火材料的优点,同时又彻底改变了以往碱性耐火材料中耐剥落性能差,容易吸收炉渣等的固有缺点,如图12 镁碳砖的生产过程影响镁碳砖性能的工艺因素主要有原料、结合剂、添加剂等。
2.1 原料MgO–C砖的主要原料包括电熔镁砂或烧结镁砂、鳞片状石墨、有机结合剂以及抗氧化剂。
2.1.1 镁砂镁砂是生产MgO–C砖的主要原料,有电熔镁砂和烧结镁砂之分。
电熔镁砂与烧结镁砂相比具有方镁石结晶粒粗大、颗粒体积密度大等优点,是生产镁碳砖中主要选用的原料。
生产普通镁质耐火材料,对镁砂原料要求主要具有高温强度和耐侵蚀性能,因此注重镁砂的纯度及化学成分中的C/S比和B2O3含量。
随着冶金工业的发展,冶炼条件日益苛刻,在冶金设备(转炉、电炉、钢包等)上应用的MgO–C砖所用的镁砂,除了化学成分外,在组织结构方面,还要求高密度和大结晶。
- 1、下载文档前请自行甄别文档内容的完整性,平台不提供额外的编辑、内容补充、找答案等附加服务。
- 2、"仅部分预览"的文档,不可在线预览部分如存在完整性等问题,可反馈申请退款(可完整预览的文档不适用该条件!)。
- 3、如文档侵犯您的权益,请联系客服反馈,我们会尽快为您处理(人工客服工作时间:9:00-18:30)。
镁碳砖开发及其在钢包渣线的应用河北瀛都复合材料有限公司王丕轩孙志红摘要:概述了镁碳砖的发展概况、生产过程及在钢包渣线的应用,并对其发展前景进行了展望。
关键词:镁碳砖;渣线;低碳化;精炼11镁碳砖发展概况MgO–C砖是20世纪70年代兴起的新型耐火材料,最早由日本九洲耐火材料公司渡边明首先开发,它是以镁砂(高温烧结镁砂或电熔镁砂)和碳素材料为原料,用各种碳质结合剂制成的耐火材料。
由于MgO–C砖具有耐火度高、抗热震性优良和抗侵蚀能力强等优良特性而被广泛应用于钢铁企业,如转炉炼钢和电炉炼钢[1]。
在日本研发出树脂结合MgO–C砖后,西欧开发了沥青结合的MgO–C砖,其残碳量约为10%,由于价格低于树脂结合MgO–C砖,故被成功地用于水冷电炉中的高温热点部位,同时也用于转炉。
我国在1980前后年开始研究含碳耐火材料[2],并被列入国家“七五”(1985~1989)科技攻关项目。
1987年鞍钢三炼钢厂在转炉上试用MgO–C砖后,仅用一年时间就超额完成了“七五”转炉炉龄达千次的攻关目标。
发展到目前,全国各大中小钢厂已普遍推广使用MgO–C 质耐火材料作为转炉和电炉的炉衬。
随着冶炼技术的进步对耐火材料的新要求,低碳镁碳耐火材料成为镁碳耐火材料新的发展热点。
低碳MgO–C砖一般是指总含碳量不超过8%、由镁砂与石墨通过有机结合剂结合而成的MgO–C砖,降低碳含量可明显降低材料的热导率[3]。
近年来,对精炼钢包用低碳量、性能优异的低碳镁碳砖的开发受到国内外业界的重视,这方面的研究开发工作已取得一定的成果,展现了良好的发展前景。
2 镁碳砖的生产过程2.1 原料MgO–C砖的主要原料包括电熔镁砂或烧结镁砂、鳞片状石墨、有机结合剂以及抗氧化剂。
2.1.1 镁砂镁砂是生产MgO–C砖的主要原料,有电熔镁砂和烧结镁砂之分。
电熔镁砂与烧结镁砂相比具有方镁石结晶粒粗大、颗粒体积密度大等优点,是生产镁碳砖中主要选用的原料。
生产普通镁质耐火材料,对镁砂原料要求主要具有高温强度和耐侵蚀性能,因此注重镁砂的纯度及化学成分中的C/S比和B2O3含量。
随着冶金工业的发展,冶炼条件日益苛刻,在冶金设备(转炉、电炉、钢包等)上应用的MgO–C砖所用的镁砂,除了化学成分外,在组织结构方面,还要求高密度和大结晶。
2.1.2 碳源不论是在传统的MgO-C砖还是在目前大量使用的低碳MgO-C砖,主要利用鳞片状石墨作为其碳源。
石墨作为生产MgO-C砖的主要原料,主要得益于其优良的物理性能:①对炉渣的不湿润性。
②高的导热性。
③低的热膨胀性。
此外,石墨与耐火材料在高温下不发生共熔,耐火度高。
石墨的纯度对MgO-C砖的使用性能影响较大,一般要使用碳含量大于95%,最好是大于98%的石墨。
除石墨外,炭黑也普遍用于镁碳砖的生产。
炭黑是由烃类碳氢化合物的热分解或不完全燃烧制得的具有高度分散的黑色粉末状碳质物料,炭黑颗粒细小(小于1μm),比表面积大,碳的质量分数为90~99%,纯度高,粉末电阻率大,热稳定性高,热导率较低,属难石墨化碳。
炭黑的加入可有效改善MgO-C砖的抗剥落性,增加残碳量,并提高砖的密度[4]。
2.1.3 结合剂生产MgO-C砖常用的结合剂有煤焦油,煤沥青和石油沥青,以及特殊碳质树脂,多元醇,沥青变性酚醛树脂,合成树脂等。
目前所用到的结合剂有以下几种类型:1)沥青类物质。
焦油沥青是一种热塑性材料,具有与石墨、氧化镁亲和力大,炭化后残碳率高,成本低的特点,过去曾大量使用;但是焦油沥青中含有致癌的芳香烃,尤其是苯并茁含量高;由于环境意识的加强,现在焦油沥青的使用量在减少。
2)树脂类物质。
合成树脂是由苯酚和甲醛反应制得,在常温下便能和耐火材料颗粒很好的混合,炭化后残碳率高,是当前生产MgO-C砖用主要结合剂;但它炭化后形成的玻璃态网络结构,对耐火材料的抗热震性和抗氧化性都不理想。
3)在沥青和树脂的基础上,经过改性得到的物质。
如果结合剂炭化后能形成镶嵌结构和原位形成碳纤维物质,那么这种结合剂将改善耐火材料的高温性能。
2.1.4 抗氧化剂为了提高MgO-C砖的抗氧化性,常加入少量的添加剂,常见的添加剂有Si、Al、Mg、Al-Si,Al-Mg,Al-Mg-Ca,Si-Mg-Ca、SiC、B4C、BN和最近报导的Al-B-C和Al-SiC-C系等添加剂[5–7]。
添加剂的作用原理大致可分为两个方面:一方面是从热力学观点出发,即在工作温度下,添加物或者添加物和碳反应生成其他物质,它们与氧的亲和力比碳与氧的亲和力大,优先于碳被氧化从而起到保护碳的作用;另一方面,即从动力学的角度来考虑添加剂与O2,CO或者碳反应生成的化合物改变碳复合耐火材料的显微结构,如增加致密度,堵塞气孔,阻碍氧及反应产物的扩散等[8]。
2.2 镁碳砖的生产工艺及分类MgO-C砖的制造工艺主要包括原料准备,配料,混练,成型和热处理,其流程图如下:镁碳砖一般按其所含碳含量进行分类,国标按此标准将目前生产的镁碳砖分为7类,而每类又分为A、B、C三种,因而总共有21种牌号(见表1)。
表1 不同牌号镁碳砖的理化性能3. 3.镁碳砖在钢包渣线的应用早期钢包渣线部位使用的耐火材料是直接结合镁铬砖,电熔再结合镁铬砖等优质碱性砖。
MgO-C砖成功在转炉上使用后,精炼钢包渣线部位也开始使用MgO-C砖,并取得了良好的使用效果。
目前,我国和日本一般都使用含碳量为12%~20%的以树脂结合的MgO-C 砖,而欧洲多采用沥青结合的MgO-C砖,含碳量一般在10%左右。
日本住友金属公司小仓钢铁厂在VAD渣线部位使用MgO含量为83%,C含量为14-17%的MgO-C砖代替直接结合镁铬砖,渣线部位的寿命从20次提高到30-32次[9]。
日本仙台钢铁厂LF精炼钢包,利用MgO-C砖代替镁铬砖,渣线部位寿命从20-25次提高到40次,取得了不错效果。
大阪窑业耐火材料公司研究了碳含量,抗氧化剂种类对MgO-C砖抗氧化性,抗渣性及高温抗折强度的影响。
研究认为:由电熔镁砂与烧结镁砂组成的混合物,外加15%磷片石墨及少量镁铝合金作抗氧化剂制得的MgO-C砖,具有很好的使用效果,在容量为100吨LF钢包渣线使用,与不含抗氧化剂的C含量为18%的MgO-C砖相比,损毁速率降低20-30%,平均侵蚀速度为1.2-1.3mm/炉。
我国精炼钢包渣线砖自从采用MgO-C砖代替镁铬砖后,综合使用效果明显。
宝钢股份总公司300t钢包渣线从1989年7月开始使用MT−14A镁碳砖,渣线寿命保持在100次以上[9];150T电炉钢包渣线采用低碳镁碳砖冶炼帘线钢,出钢温度1600℃~1670℃,取得了良好的试用效果,其使用寿命比原材质有大幅提高,由原来冶炼帘线钢的5炉左右提高到8炉以上,下线残厚也优于原材质。
上钢五厂40吨LF钢包渣线部位应用洛阳耐火材料厂生产的MgO-C砖,并与电熔再结合镁铬砖进行了比较,使用结果表明,其侵蚀速度为1.28mm/炉,远高于镁铬砖的1.67mm/炉,使用39炉后发现,渣线MgO-C砖侵蚀均匀,不像镁铬砖那样局部蚀损严重、不均匀[10]。
44低碳镁碳砖及其在精炼钢包上的应用近年来,世界各国都在大力发展炉外精炼工艺,低碳钢和超低碳钢的产量越来越高。
洁净钢工艺要求严格控制耐火材料中碳的含量;二次精炼工艺要求钢水的温度不能下降太多,即要求炉衬具有低的热导率。
因此,开发低碳镁炭砖是非常必要的。
4.1 镁碳砖低碳化后需解决的关键及主要对策镁碳砖中碳含量降低引起的主要问题是热震稳定性及抗渣渗透性下降。
众所周知,镁碳砖中碳含量降低以后,使砖的热导率下降,弹性模量增大,从而使砖的抗热震稳定性变差。
碳含量降低以后,使熔渣及钢水与材料的润湿性增强,材料的抗熔渣及钢水的渗透性变差。
目前对解决这些问题的认识主要包括以下三个方面[11, 12]:(1) 通过改善结合碳的碳结构提高镁碳砖的热震稳定性。
传统镁碳砖的结合剂多为酚醛树脂,这种结合剂炭化以后的炭结构呈各向同性的玻璃态,所以使镁碳砖呈脆性,弹性模量高,对制品的热稳定性不利,且制品的高温强度也低。
在酚醛树脂中引入能石墨化的碳素前躯体后,这种复合结合剂在镁碳砖使用环境下能碳化成为具有流动状或镶嵌状结构的次生碳,或原位形成纳米碳纤维,通过碳结构的改善及纳米碳纤维形成的增强作用来提高低碳镁碳砖的热震稳定性及高温强度。
(2) 优化镁碳砖的基质结构。
镁碳砖的热震稳定性及抗渣渗透性主要取决于基质的组成与结构,在碳含量大幅度降低的情况下,如何提高骨料颗粒与炭粒子的接触频率,即降低碳粒子的尺度并保证其高度分散,是改善低碳镁碳砖热震稳定性及抗渣渗透性的重要措施之一。
通过调整基质配料的粒度组成来控制气孔的尺寸、形状和分布,也会对材料的热导率产生明显影响。
(3) 采用高效抗氧化剂。
随着镁碳砖中碳含量的降低,对碳的氧化保护尤为重要,所以采用合适的高效抗氧化剂也是十分必要的。
4.2 低碳镁碳砖的应用及前景近几年,以日本为代表,应用纳米技术的低碳镁碳砖已有了较大的发展。
所采用的低碳镁碳砖大致可以分为两种类别:(1) 在使用条件下原位形成纳米炭纤维结合的低碳镁碳砖。
这种砖中的w C=1%,在VOD钢包上的使用寿命是传统镁铬砖的两倍。
(2) 纳米结构基质低碳镁碳砖,砖中的w C =3%~5。
在日本,这种砖作为镁铬砖的替代产品,已广泛地应用于RH 精炼炉,其使用寿命明显优于传统镁铬砖。
近年来,国内低碳镁碳砖的开发与应用也取得了较大的进展。
浙江东瑞高级陶瓷有限公司与武汉科技大学专家联合开发的通过采用纳米尺度的碳源和高效抗氧化剂,w c=4~6%的低碳镁碳砖已成功地应用于宝钢120 t VOD精炼钢包的渣线与包壁,冶炼钢种为304,304L,316,409,409L,410等不锈钢种,最高冶炼温度1750℃。
所开发的低碳镁碳砖的使用寿命与进口的镁钙砖相当。
并获得了2008年国家科技进步二等奖的殊荣。
表2为他们所开发的两种低碳镁碳砖典型的性能指标。
[11]低碳镁碳砖是耐火材料工业按照国家工业转型升级一个典型的产品,特别是2010年石墨价格剧烈的变化,对于镁碳砖生产带来了严重的影响,低碳镁碳砖采用少量的鳞片石墨,首先可以少用鳞片石墨资源。
另外,产品在使用时,可以降低热量损失,节能环保。
按照行业统计,镁碳砖消耗为4公斤/吨钢,按照2009年全国5.68亿吨,全国消耗227万吨镁碳砖,低碳镁碳砖目前在宝钢、武钢、太钢广泛使用,已经得到了用户的认可,根据冶炼钢种不同,如有一半高碳镁碳砖被低碳镁碳砖取代,全国需要100万吨以上的用量,所以,镁碳砖生产企业要引起重视,努力开发适合冶炼各钢种的低碳镁碳砖。
55镁碳砖的发展方向低碳镁炭砖是镁炭砖的发展方向之一。
对于低碳镁炭砖来说,最为关键的还是要提高其抗热剥落性能和抗渣渗透性能。