基于DEFORM三维多晶体材料微结构的有限元分析
基于DEFORM_3D的钛合金切削过程有限元仿真

80
90
图5
fz = 0.7 mm/z 时切削速度对切削力的影响
说明了切屑的形成过程。通过 DEFORM- 3D 模拟的结果展示 了工件材料在刀具的作用下发生变形, 产生切屑, 切屑逐渐与 工件分离, 并发生卷曲变形的过程。
表 3 和表 4 为背吃刀量 ap、 每齿进给量 fz 和切削速度 Vc 对切削力 Fy 影响程度的数据分析。
觶
觶觶 觶 觶觶
m
(1 )
式 (1 ) 中, A、 B、 n、 C 和 m 是由材料自身决定的常数; Tm 为材料的熔点; Tr 为室温; ε 0 为参考应变速率;等号右边第一 部分表示应变 ε 对流动应力 σ 的影响,第二部分表示应变速 率 ε 对流动应力 σ 的影响,而最后一部分表示温度 T 对流动 应力 σ 的影响。 本文中 TC4 材料模型采用的 J- C 模型为: 軈 軍 =觶 軈)0.375 觶 σ · 1+0.0394 ε 968.88+567.17(ε 觶 ε0 代分析得来的。
700
500
300
20
40 60 切削速度 Vc(m/min)
80
图4
1600 切削力 Fy(N)
fz = 0.3mm/z 时切削速度对切削力的影响
ap=0.5mm ap=1mm
1100
2
仿真及结果分析
图 2 中的显示了刀具切削加工过程的仿真过程,同时也
600 20
30
40
50 60 70 切削速度 Vc(m/min)
钛合金 TC4 的物理力学性能参数[3]
泊松比 0.307 热膨胀系 热导率 λ 比热容 c 数 w(m/K) [w(m/K)] [J/(gK)] 7.89 7.89 9.01 9.3 9.24 9.39 9.4 5.44 6.7 8.79 10.47 12.56 14.24 15.49 0.678 0.691 0.703 0.741 0.754 0.879
Deform3D操作介绍

Deform3D操作介绍第⼆章DEFORM-3D操作介绍2.1DEFORM-3D软件介绍20世纪70年代后期,位于美国加州伯克利的加利福尼亚⼤学⼩林研究室在美国军⽅的⽀持下开发出有限元软件ALPID,20世纪90年代在这⼀基础上开发出DEFORM-2D软件,该软件的开发者后来独⽴出来成⽴了SFTC公司,并推出了DEFORM-3D软件。
DEFORM-3D 是⼀套基于有限元分析⽅法的专业⼯艺仿真系统,⽤于分析⾦属三维成形及其相关的各种成形⼯艺和热处理⼯艺。
⼆⼗多年来的⼯业实践证明其有着卓越的准确性和稳定性,模拟引擎在⼤流动、⾏程、载荷和产品缺陷预测等⽅⾯同实际⽣产相符,被国际成形模拟领域公认为处于同类模拟软件的领先地位。
DEFORM-3D不同于⼀般的有限元软件,它是专门为⾦属成形⽽设计。
DEFORM-3D可以⽤于模拟零件制造的全过程,从成形、机加⼯到热处理。
通过DEFORM-3D模拟整个加⼯过程,可以帮助设计⼈员:设计⼯具和产品的⼯艺流程,减少实验成本;提⾼模具设计效率,降低⽣产和材料成本;缩短新产品的研究开发周期;分析现有⼯艺存在的问题,辅助找出原因和解决⽅法。
2.1.1DEFORM-3D特点1)DEFORM-3D具有⾮常友好的图形⽤户界⾯,可⽅便⽤户进⾏数据准备和成形分析。
2)DEFORM-3D具有完善的IGES、STL、IDEAS、PATRAN、等CAD和CAE接⼝,⽅便⽤户导⼊模型。
3)DEFORM-3D具有功能强⼤的有限元⽹格⾃动⽣成器以及⽹格重划分⾃动触发系统,能够分析⾦属成形过程中多个材料特性不同的关联对象在耦合作⽤下的⼤变形和热特性,由此能够保证⾦属成形过程中的模拟精度,使得分析模型、模拟环境与实际⽣产环境⾼度⼀致。
DEFORM-3D采⽤独特的密度控制⽹格划分⽅法,⽅便地得到合理的⽹格分布。
计算过程中,在任何有必要的时候能够⾃⾏触发⾼级⾃动⽹格重划⽣成器,⽣成细化、优化的⽹格模型。
4)DEFORM-3D系统⾃带材料模型包含有弹性、弹塑性、刚塑性、热弹塑性、热刚粘塑性、粉末材料、刚性材料及⾃定义材料等类型,并提供丰富的开放式材料数据库,包括美国、⽇本、德国的各种钢、铝合⾦、钛合⾦、⾼温合⾦等250种材料的相关数据。
Deform有限元模拟技术介绍及应用
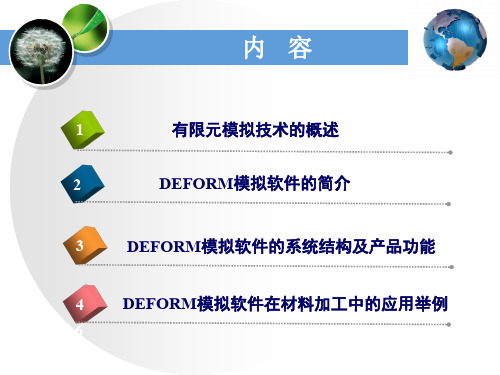
。把整个系统分解成性态容易了解的单个的元件 或“ 单元”,然后由这些元件重建原来的系统, 以研究其性态变化等。
静态 隐式
有限元模拟算法
动态 显式
数值模拟:求偏微分方程的数值解
数值模 拟方法
•1.有限元法、 • 2.边界元法、 • 3.离散单元法 •4.有限差分法
综上本模拟试验中所选取的基本参数:
• TiAl合金坯料的直径为14mm • TiAl合金坯料髙径比为2,2.5,3 • 包套材料为321不锈钢,厚度为3,5,8mm • 上下模尺寸为50×50×15mm,温度为20 ℃ • TiAl合金的温度为1150℃ • 上模向下运动的速度为1mm/sec • 各物体之间的接触摩擦系数为0.3 • 公差设为最佳值 • 模拟控制中步长设为0.7mm
5 DEFORM模拟软件在材料加工中的应用
以DEFORM软件在塑性成形中的应用为主,以 TiAl合金的包套镦粗以及方形件的锻压为例,详 细介绍deform的功能,应用的步骤,以及可以 解决的一些主要问题
A
前期造型
B
模拟的前处理
C
启动模拟计算器
D
后处理操作
前期造型
内容
1
Hale Waihona Puke 有限元模拟技术的概述2DEFORM模拟软件的简介
3
DEFORM模拟软件的系统结构及产品功能
4 DEFORM模拟软件在材料加工中的应用举例 6
有限元模拟软件的概述
有限元的基本思想在20世纪40年代初就已经提出, 到70年代才开始逐渐被应用,应用的范围,分析 的对象也越来越广,分析的作用也更加强大
• 专门适用于塑性加工领域的CAE分析软件
运用Deform有限元分析优化锻造模具设计

软件介绍D eform 是一套基于有限元的工艺仿真系统,用于分析金属成形及其相关工艺的各种成形和热处理工艺。
通过在计算机上模拟整个加工过程,帮助工程师和设计人员设计工具和产品工艺过程,减少昂贵的现场实验成本。
提高模具的设计效率,降低生产的材料成本,缩短产品的研究开发周期。
案例分析以下就通过一个案例阐述在实际设计中如何运用D eform 有限元分析来优化锻造工艺及其锻造模具的设计。
图1产品是水龙头的一个重要零件,材质为铅黄铜(C uZn40Pb2),产品重量419克。
锻造工艺有两种方案:①开式模锻,如图2,②闭式挤压,如图3。
运用Deform 有限元分析优化锻造模具设计刘名水图1水龙头重要零件图2开式模锻图3闭式挤压!!!!!!!!!!!对两种方案分别运用DEFROM 进行模拟分析。
DEFROM 软件操作过程:因DEFROM -3D 本身建立几何模型功能较差,难以建立复杂几何模型,且模具设计是用P roe设计,所以就用P roe 建立几何模型。
上模,下模,以及锻造原材料(铜棒)。
用P roe 建好几何模型后,把上模,下模,原材料分别导成.stl 文件。
打开DEFROM -3D 中的DEFROM -F3模块,建立模拟文件,首先进行前处理。
导入之前建立的几何模型(.stl 文件),为了简化计算,不考虑热量在原材料与模具之间的传递,原材料进行网格划分,设定锻造参数:锻造温度700℃,模具温度150℃,摩擦系数0.3,上模移动速度400mm/sec ,上模移动距离等,原材料选择DE -FROM-3D 软件自带材料库里的DI N -CuZn40Pb2。
其中最重要的是注意原材料的网格划分,网格划分越粗,即网格数量越少,模拟计算就越不准确。
相反,网格划分越细,即网格数量越多,模拟计算就越准确,但计算量就越大。
需根据计算机硬件条件及分析需求,合理划分网格数。
前处理设定好,检测数据OK 后,生成待模拟计算数据。
然后进行模拟计算。
基于DEFORM的三维多晶体材料微结构的有限元分析的开题报告

基于DEFORM的三维多晶体材料微结构的有限元分析的开题报告1. 研究背景和意义在当今工程领域中,越来越多的新材料被开发出来,其中包括了许多多晶体材料。
多晶体材料由于具有较好的力学性能,因此在许多工程领域得到广泛应用,例如航空航天、汽车、船舶等。
然而,多晶体材料具有复杂的三维微结构,其力学性能的分析和设计具有一定的难度。
有限元方法是一种用于计算结构和材料力学行为的数值方法。
在多晶体材料力学性能的分析和设计中,有限元方法也被广泛应用。
然而,在有限元分析中如何准确地描述三维微结构仍然是一个有待解决的问题。
近年来,基于DEFORM的有限元方法逐渐成为研究多晶体材料微结构的重要工具。
DEFORM是一种用于金属变形加工模拟的集成软件,其有限元分析能力具有较高的精度和可靠性。
通过DEFORM可以对多晶体材料的三维微结构进行建模,从而研究材料的力学性能。
因此,本研究旨在基于DEFORM进行多晶体材料三维微结构的有限元分析研究,以期在多晶体材料的力学性能分析和设计中提供新的解决方案。
2. 研究内容和方法本研究的研究内容主要包括以下两个方面:(1)建立多晶体材料的三维微结构模型本研究采用图片处理软件和有限元建模软件共同建立多晶体材料的三维微结构模型。
首先,利用图片处理软件将多晶体材料的2D显微镜照片转化为3D模型;其次,利用有限元建模软件对其进行处理并得到三维微结构模型。
(2)基于DEFORM进行多晶体材料的有限元分析本研究采用基于DEFORM的有限元方法,对多晶体材料进行有限元分析。
主要包括:建立三维微结构模型和确定边界条件、定义材料模型和材料参数、进行动态和静态力学分析以及讨论分析结果。
3. 预期研究结果通过本研究,预期可以得到以下几点研究结果:(1)建立多晶体材料的三维微结构模型,提供一种可供参考的多晶体材料建模方法;(2)利用基于DEFORM的有限元方法对多晶体材料的力学性能进行分析,探讨微结构对材料力学性能的影响;(3)通过对分析结果的讨论,提出新的解决方案和研究思路,为多晶体材料的力学性能分析和设计提供参考和借鉴。
多晶体材料三维微结构有限元分析的后处理
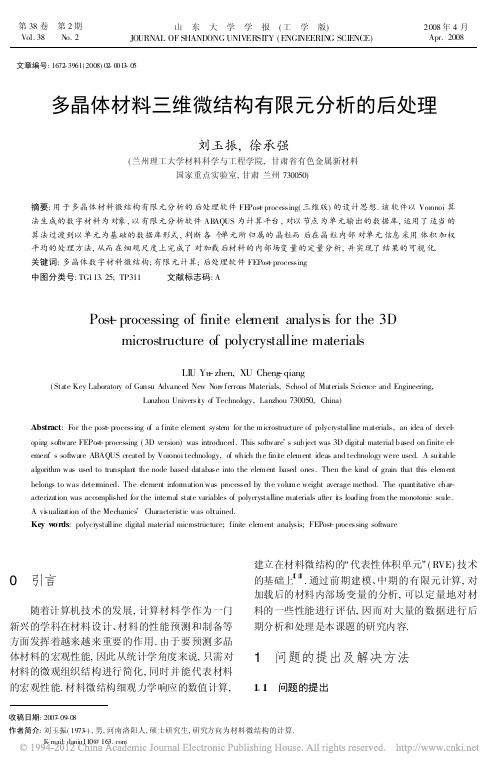
.
图 3 4 节点单元 Fig. 3 4 - node element 图 2 总的程序流程图 Fig. 2 The overall process flow chart
( 2) 8 节点( 6 面体 ) 单元 , 如图 4, 求 6 面体体积 时可以分为 3 部分, 即 V = VA - A 1 B 1 C1 D1 + VA VA C CDD
15
加以区分了, 算法如图 2.
( z 3- z 1) - ( y 3- y 1) ( z 2- z 1) , B = ( x 3 - x 1 ) ( z 2z 1 ) - ( x 2 - x 1 ) ( z 3 - z 1 ) , C = ( x 2 - x1 ) ( y3 - y 1 ) ( x 3 - x 1 ) ( y 3 - y 1 ) ; 设点 ( x 0 , y 0 , z 0 ) 为底面 ABC 上 A , B 和 C 3 点的算术平均坐标, 则 D = - ( Ax 0 + By 0+ Cz 0 ) , 平面外一点 S ( x , y , z ) 到该面的距离如下. d= | Ax + By + Cz + D | A + B + C
2
元法引入其中 , 并以 ABAQUS 为计算平台, 对短裂纹 / 微孔洞的扩展进行预测. Peter MATIC, Andrew. B 等 人在 细 观 2D 尺 度 上 利 用 元 胞 自 动 机 技 术 在 ABAQUS 中建模并对短裂纹的萌芽、 扩 展及其聚合 效应进行进行模拟 , 研究表明了大范围的破坏组织 可以从简单的模拟结构中获得 . . Marko KOVAC 等 人提出了跨尺度的模型 ( 多晶粒总数的最小尺寸 ) , 对一个压力容器进行了微观应力分布的计算, 从而 在一定程度上预测了整个材料的性能 . 从以上几 个例子来看, 引入有限元的方法, 分析计算微观组织 结构的应力场分布 , 已是复合材料 发展的热点 . 总 之, 本课题所提出的在 ABAQUS 中实现材料微结构 计算的后处理是为了解决针对多晶体材料微观组织 结构 , 细观尺度上应力的分布情况, 从而可以从细、 微观上预测材料的整体性能以及给出材料失效的科 学依据, 比较准确地预测材料的失效问题, 进而给材 料的设计提供理论依据 . 1 2 解决的方法 由软件 ProDesign 生 成的或 经由 软件 MsCopier 重构的材料微结构数据经过 TransMesh 软件的识别、 组装和转换并导入 ABAQUS 后 , 能够依据多晶体材 料微结构组成物的几 何轮廓进行数值计算网 格划 分, 从而得到了二、 三维多晶体基异质性复合材料微 结构的数值计算网格划分. 并对数字材料的边界进 行加载, 设定分析步导出所需要的数据 . 这些数据是 以节点( Node) 为基础输出的, 把大量的数据转化为 以晶粒为基础的形式, 并要实现结果的可视化. 假设所研究的材料的属性是线弹性的、 正交各 向异性的. 材料的模型由 44 个晶粒组成 , 边界和加 载情况如图 1, 模型左端固定, 右端施以均匀的拉力 6E+ 008Pa.
基于DEFORM 3D的转模挤压纯铜有限元分析
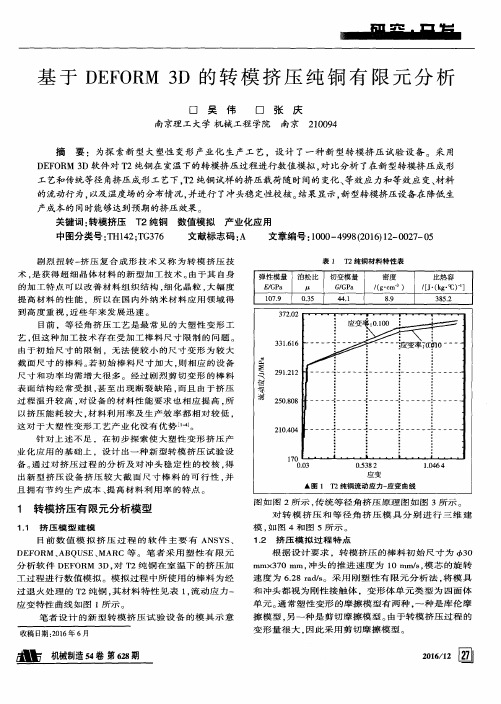
中图分类 号 : T H1 4 2 ; T G 3 7 6
文 献标 志码 : A
剧烈 扭转 一 挤 压 复 合 成 形 技 术 又 称 为 转 模 挤 压 技
术, 是获得 超 细晶体 材料 的新型 加工 技术 。 由于 其 自身
的加 工特 点可 以改善 材料 组织结 构 , 细化 晶粒 , 大 幅 度 提 高 材 料 的 性 能 ,所 以 在 国 内外 纳 米 材 料 应 用 领 域 得
到高 度重视 , 近些 年来 发展 迅速 。
密度 / ( g ・ c m 。)
8. 9
比热容 / [ J ・ ( k g ・ ℃) ]
3 8 5. 2
G / GP a
4 4. 1
目前 。等 径 角 挤 压 工 艺 是 最 常 见 的 大 塑 性 变 形 工
艺, 但 这种加 工技 术存 在受 加工棒 料尺 寸 限制 的 问题 。 由 于 初 始 尺 寸 的 限 制 ,无 法 使 较 小 的 尺 寸 变 形 为 较 大 截 面 尺寸 的棒料 。 若 初始棒 料尺 寸加 大 , 则 相 应 的 设 备
这 对 于大塑 性变形 工艺 产业 化没有 优势 B - a ] 。 针 对 上 述 不 足 ,在 初 步 探 索 使 大 塑 性 变 形 挤 压 产 业 化 应 用 的 基 础 上 ,设 计 出一 种 新 型 转 模 挤 压 试 验 设 备。 通 过对挤 压过 程 的分析及 对 冲头稳 定性 的校 核 . 得 出新 型挤压 设 备挤 压 较 大截 面 尺 寸棒 料 的可行 性 . 并
模 , 如 图 4和 图 5所 示 。
目前 数 值 模 拟 挤 压 过 程 的 软 件 主 要 有 ANS YS、
基于DEFORM-3D的Al2024锻造成形模拟

基于DEFORM-3D的Al2024锻造成形模拟冉乙川;崔超;周丽【摘要】利用DEFORM-3D有限元分析软件对Al2024材料进行锻造模拟,分析各变形工艺参数对Al2024材料锻造过程的应变场、损伤场和平均晶粒尺寸的变化规律.结果表明:随着压下量增大,锻件内部的变形不均匀程度加剧,且平均晶粒尺寸逐渐增大;随着温度的增加,最大应变、损伤和平均晶粒尺寸越来越大,从400℃增加到450℃时,最大损伤值有明显增大;当温度达到500℃时,平均晶粒尺寸减小.%The forging process of Al2024 are simulated by DEFORM-3D software.The influence of the deformation parameter on strain field,damage field and average grain size of Al2024 during forging process were analyzed.The results show that with the increase of rolling reduction,the degree of deformation in the forging increases and the average grain size increases gradually.With the increase of temperature,the maximum strain,damage and average grain size become larger and larger,and the maximum damage value increases obviously from 400℃ to450℃.When the temperature reaches 500℃,the average grain size decreases.【期刊名称】《沈阳理工大学学报》【年(卷),期】2017(036)004【总页数】5页(P78-82)【关键词】DEFORM-3D;Al2024;锻造【作者】冉乙川;崔超;周丽【作者单位】沈阳理工大学机械工程学院,沈阳 110159;沈阳理工大学机械工程学院,沈阳 110159;沈阳理工大学机械工程学院,沈阳 110159【正文语种】中文【中图分类】TP391铝合金由于密度低、比强度高、耐腐蚀强、易导热导电、塑性和加工性能良好、成本低等一系列优点,是航空航天等领域的主要结构材料。
- 1、下载文档前请自行甄别文档内容的完整性,平台不提供额外的编辑、内容补充、找答案等附加服务。
- 2、"仅部分预览"的文档,不可在线预览部分如存在完整性等问题,可反馈申请退款(可完整预览的文档不适用该条件!)。
- 3、如文档侵犯您的权益,请联系客服反馈,我们会尽快为您处理(人工客服工作时间:9:00-18:30)。
甘肃科 技
Ga s ce c n e h oo y n u S in e a d T c n l g
r. 5 0 2 Z
.4 1
J/ 2 0 u. 09
基 于 D F M 三 维 多晶体 E OR 材 料微 结构 的有 限元分 析
工件表面中心节点 P , l及工件边部节点 P 3在挤压 过程 中 , 与上模 具 产生接 触温度 曲线起伏 显著 , 温度 急剧 下 降 ; 件在 与 空气 的 热 交换 过 程 中温 度 变化 工 缓慢 ,4的温 降 变 化不 太 明显 。中 心 处节 点 P P 2温 度略 有提 升 ( 是 因为塑性 功转 化为 热 的结 果 ) 这 。
利 用本 课 题 组 自主开 发 的计 算 机 软件 A . u tV , o E 即可在 A A U 有限元软件 中, R BQ S 建立材料微
结构的“ 代表性体积单元” R E 的几何模型 , (V ) 并根
■ 1 ■ 2
3
据几 何模 型 画 出有 限元 计算 网格, 单元 体数 目: 193 , 978 结点 :60 , 30 o 总模拟步数 为 1o 模 拟时 间 o,
2 D F R 前 处理 程 序 的二 次 开发 EO M
2 1 材料 代表性 体积 单元 ( V . R E)
材料微结构细观力学响应的数值计算建立在材 料微 观组织 结 构 的 “ 表性 体 积 单 元 ” R E 技 术 代 (V ) 上 。微 观组 织 结 构 的 “ 表性 体 积 单 元 ” 义 在 材 代 定 料的细观尺度上 。“ 代表性体 积单元 ” 其体积尺寸 是最小 的, 但体积单元内却包含 了足够多微观组织 结构组成物的几何信息、 晶体学取向信息、 分布信息 与相 场信息 , 并能 在统计 学 意义 上 ( 统计 平 均 性 质 ) 代表材料微观组织结构 的基本特征 , 代表性体 由“ 积单元 ” 成 的材 料 称 为 统 计 均 匀 材 料 , 计 均 匀 组 统
点P 2的应力 最 大 , 件边部 节 点 P 工 3在挤 压过 程 中
通过对关键点等效应变变化进行跟踪, 5演 图 示了含有 10 0o个 晶粒的三维多晶体材料微结构模 型算例及其等效应变分析结果。如图 5 a 所示 , () 在 整个挤压过程 中, 在工件边部及挤压变形 内部 中心 区呈现出较大的等效应 变, 表面 中心处和侧 面处应 变相对较小。图 5 b 为等效应变随计算 时间的变 () 化 曲线 , 以看出 : 可 关键点等效应变首先增长缓慢几
所需的模 拟数据。D F R E O M允许 用户对其数据库 进行操作 , 对系统设置进行修改 , 以及定义 自己的材 料模 型 等¨ , 图 1 示 。 J如 所
是统计均匀场。值得指出的是 , 应该根据材料实际 ( 或模拟) 的微观组织结构组成物的几何构造、 取向 分布与结构 , 算材料微观组织结构 的“ 计 代表性体
何凤 兰, 李旭东 , 国梁 王
( 州理工大学 甘肃省有 色金属新材料省部共建 国家重点实验室 , 兰 甘肃 兰州 7 0 5 ) 30 0 摘 要: 利用本课题组 自主开发 的计算机软件 A tR E, uo V 实现 三维 多晶体材料微结构的几何建模 , 网格划 分 , 并将生
成 的 Ipt nu 的文件通过脚本语 言 Pt n y o 的编译 , h 实现在 D F R 中建立三维多 晶体微 结构的具体材料模 型 , EO M 并进行
限元系 统 ( E , 门设 计 用 于分 析 各种 金 属 成形 F M) 专 过程 中的三维 (D) 3 流动 , 提供极 有 价值 的工艺 分 析 数据 , 有关成 形 过 程 中的 材 料 和温 度 流 动 。主要 及
包 括前处 理器 、 拟器 、 模 后处 理器 仿真分析 , 演示出了三维多晶体材料微结构 的温度场及等效应力 、 等效应变分布结果。 关键 词 : 三维多晶体 ; 材料微结构 ; e K y文件 ; p t 件 I u文 n
中图分类号 :G1 T 4
1 D F R 简介 EO M
DFR 3 E O M一 D是一套基于工艺模拟系统 的有
与上模具产生接触应力 曲线起伏不大 , 如图4 b 为 () 等效应力随计算 时间的变化 曲线 。各节点的应力急 剧上升 , 而后在达到稳定状态呈缓慢增长趋势 , 在整 个 挤压 过程 中 , 节点 P 1应力 曲线起 伏相 当大 。
乎趋近于零 , 在工件挤压后塑性变形逐渐增大 , 等效
塑性应变也随之增大。在整个挤压过程 中, 工件边
积单元 ” 的细 观 力 学 响应 以及 材 料 性 能 。 “ 表 内 代 性体 积单元 ” 细观 应力 的体积 平均 响应程 度 必 须 的
与“ 代表性体积单元” 边界上所承受 的外加载荷程 度相一 致 一 引。
2 2 几何模 型 的建立 .
挤 压 件 原 始 尺 寸 为: 00 m X 10 m × 10m 00 m
材料受 到均 匀边 界条 件 的 作用 , 介 质 内 的场 变 量 则
器处理模具和坯料的材料信息及几何信息的输入 、 成形 条件 的输入 , 立边 界条 件 , 建 它还包 括有 限元 网
格 自动生 成器 ; 模拟 器是 集 弹 性 、 弹塑 性 、 ( ) 刚 粘 塑 性、 热传 导于一 体 的有 限元求 解器 ; 后处 理器是 将模 拟 结果 可视化 , 持 O eG 支 pn L图形 模 式 , 输 出用户 并
为0 7 . 。坐标 系的建立为 : 的负方 向为挤 压方 z轴
图 1 有 限元 分 析 流 程 图
向。
第1 4期
何 凤 兰等 : 于 D F R 三维 多 晶体材 料微 结构 的有 限元分 析 基 EO M
 ̄ae a ln {
1 1
2 3 多晶体 材 料微 结构 的数 据准 备 .
步长 为 :. 1。 由于 D F R 对 工 件 赋 予 不 同材 O 0S EO M
曝 4
s
料属性的限制 , 在编译 的过程 中, 设置 6 材料属 种
性 。实 现对所 有 的单 元 赋材 料 属 性 , 具体 是 将 同一 晶粒 对应 的多 个单 元 赋予 同一材 料属性 。而后 利 用
面 的中心 点 。结 果 表 明 , 件 各 部 位 关键 点 的温 度 工 随挤压 过程 时 间的增 加 均呈 现 下 降 的趋 势 , 别 是 特
3 三维多晶体材料微结构模拟结果及 分 析
3 1 温 度场 分布 .
为 更好地 反 映整 个挤 压过 程 中工件各部 位温 度
的变化规 律 , 工 件 的 中心 和表 面 , 在 沿工 件 长度方 向
( ) 5 步温度分布 a第 O
( )节点温度随时间变化分布 b
图 3 多晶体 材料挤压过程温度场分布
3 2 应 力分 析 .
3 3 应 变 分 析 .
通过对关键点等效应力变化进行跟踪 , 4演 图 示了含有 1o 0O个 晶粒 的三维多晶体材料微结构模 型算例及其等效应力分析结果。当工件开始与上下 模接触时, 图 4 a 所示 , 如 () 挤压变形 内部 中心区节
提取截面上的关键 点进行温度跟踪分析 , 将各点 的 温度 随 时 问变 化作 曲线 ,演 示 了含 有 】0 0o个 晶 粒 的多 晶体 材 料 挤 压 过 程 中 温 度 分 布 , 图 3所 示 。 如 P 为多晶体材料商标名 的中心点 ,2为多晶体材 1 P 料 的 内部 中心 点 ,3为上 表 面 的侧 面 中点 ,4为侧 P P
1 B
图 2 三 维 多 晶体 网 格 划分 材 料 微 结构 ( 压 工 件 模 型 ) 挤
c语言编译生成 6种新材料 , 为了使整个工件的材 料属性 差别 不 易过 大 , 在编 译 材 料 属性 时 仅 对材 料
的杨 氏模 量进 行 少 量 的增 加 , 别 命 名 为 N W —I 分 E ( =1— ) I 6 。这 样 即可将 每个 晶粒 可视化 显现 出来 。 图 2显 示 了含有 10 00个 晶粒 的三维 多 晶体 网格 划 分 材料微 结构 ( 压件 模 型 ) 挤 。
50 m( 0 r 长度 × a 宽度 X 厚度) 其开始温度为 90 , , 0℃
上下模具温 度都为 30 0 ℃。材料假定 是各相 同性 的, 挤压件和上下模之间采用剪切摩擦模型, 摩擦系
数是 0 3 . 。工件的 自由表面与周围环境之间的等效 换热系数取为 10 2 / s m c , 8 .N ( ・ ・ ) 工件与上下模 之间的接触传热系数取为 5 / s・ C , N ( m ・ ) 辐射率