基于BP神经网络的刀具寿命预测模型_丁怡
刀具的寿命识别与预测
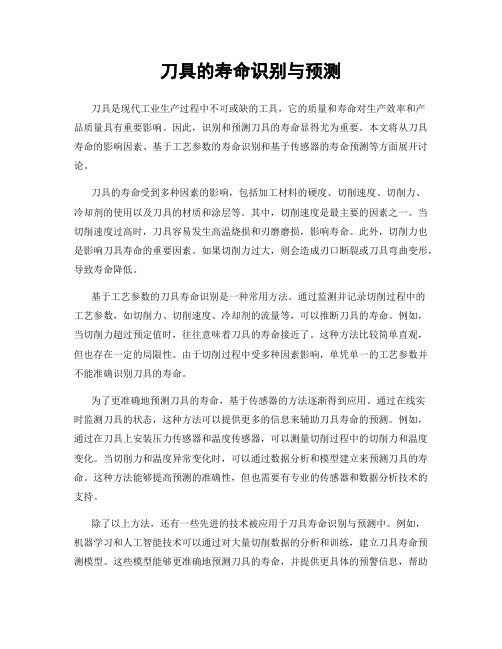
刀具的寿命识别与预测刀具是现代工业生产过程中不可或缺的工具,它的质量和寿命对生产效率和产品质量具有重要影响。
因此,识别和预测刀具的寿命显得尤为重要。
本文将从刀具寿命的影响因素、基于工艺参数的寿命识别和基于传感器的寿命预测等方面展开讨论。
刀具的寿命受到多种因素的影响,包括加工材料的硬度、切削速度、切削力、冷却剂的使用以及刀具的材质和涂层等。
其中,切削速度是最主要的因素之一。
当切削速度过高时,刀具容易发生高温烧损和刃磨磨损,影响寿命。
此外,切削力也是影响刀具寿命的重要因素。
如果切削力过大,则会造成刃口断裂或刀具弯曲变形,导致寿命降低。
基于工艺参数的刀具寿命识别是一种常用方法。
通过监测并记录切削过程中的工艺参数,如切削力、切削速度、冷却剂的流量等,可以推断刀具的寿命。
例如,当切削力超过预定值时,往往意味着刀具的寿命接近了。
这种方法比较简单直观,但也存在一定的局限性。
由于切削过程中受多种因素影响,单凭单一的工艺参数并不能准确识别刀具的寿命。
为了更准确地预测刀具的寿命,基于传感器的方法逐渐得到应用。
通过在线实时监测刀具的状态,这种方法可以提供更多的信息来辅助刀具寿命的预测。
例如,通过在刀具上安装压力传感器和温度传感器,可以测量切削过程中的切削力和温度变化。
当切削力和温度异常变化时,可以通过数据分析和模型建立来预测刀具的寿命。
这种方法能够提高预测的准确性,但也需要有专业的传感器和数据分析技术的支持。
除了以上方法,还有一些先进的技术被应用于刀具寿命识别与预测中。
例如,机器学习和人工智能技术可以通过对大量切削数据的分析和训练,建立刀具寿命预测模型。
这些模型能够更准确地预测刀具的寿命,并提供更具体的预警信息,帮助操作工人及时更换刀具,避免生产事故和损失。
此外,纳米技术也被应用于刀具的改性和涂层技术,提高刀具的耐磨性和寿命。
在刀具寿命识别与预测的研究和应用中,我们应该注重实践和理论的结合。
通过采用多种方法的综合应用,可以提高刀具寿命的识别和预测准确性。
基于BP神经网络的数控机床刀具磨损状态识别方法

基于BP神经网络的数控机床刀具磨损状态识别方法何一千,黄民,孙巍伟(北京信息科技大学机电工程学院,北京100192)摘要:为了提高三相电流信号监测刀具磨损状态的可靠性,提出了一种基于BP神经网络的数控机床刀具磨损状态识别方法。
首先对采集得到的三相电流信号进行时域、频域和小波分析,从中提取出与刀具磨损程度相关性较好的多个特征量,组合成敏感特征向量,然后搭建BP神经网络,建立三相电流信号特征向量与刀具磨损状态之间的联系。
最后,用经过训练后的BP神经网络识别多组未知样本的刀具磨损状态。
实验结果表明,该方法能够准确判定刀具的磨损状态。
关键词:三相电流信号;BP神经网络;刀具磨损;状态识别中图分类号:TG71文献标识码:B DOI:10.16621/ki.issn1001-0599.2019.09.150引言在数控机床切削加工的过程中,刀具的磨损是不可避免的。
刀具的磨损直接导致切削力的增大、切削温度的上升、工件表面粗糙度增大,严重时甚至会影响整个加工系统的正常运行,造成不可估量的损失[1]。
目前,刀具的磨损状态主要通过停机卸刀后,依靠工人的观察和经验来判断刀具的磨损程度,这严重影响了数控加工的整个自动化过程,且大大降低了生产效率。
因此对刀具的磨损状态进行在线监测,及时有效地识别刀具的磨损状态十分重要。
目前,在刀具状态监测这一领域经过各国学者的研究和探索总结出很多方法。
例如通过测量切削力、主机电流、光学图像、振动分析等多种方法都可以有效地监测刀具的磨损状态,总结起来可以分为直接监测和间接监测两大类[2]。
直接监测不能在线监测,如光学法、电阻法等直接检测方法需要停机获取刀具的磨损参数,所以在自动化系统中一般不予采用[3]。
间接监测虽然能够在线监测,但是如切削力信号检测法、振动检测法等大多数监测方法的传感器安装会影响到加工进程。
综合考虑多种原因,通过电流信号在线监测是一种比较好的监测方法,目前有很多研究均是监测机床主轴或者进给电机的电流信号。
基于ELM的刀具磨损量及剩余寿命预测

基于ELM的刀具磨损量及剩余寿命预测摘要:由于刀具磨损状态对加工质量影响较大,提出了一种基于单隐含层前馈神经网络——ELM的刀具磨损状态在线监测方法。
根据铣削刀具的实时工况数据,采用统计分析、快速傅里叶变换和小波变换多种特征提取方法,提取出34个对刀具磨损敏感的时域、频域、时频域混合特征。
将提取的特征与磨损量输入极限学习机网络框架中进行训练得到ELM模型,把测试集特征放入ELM模型进行预测评估,得到对应的预测刀具磨损量及剩余走刀次数。
通过与SVR和遗传算法优化BP神经网络的预测结果比较发现,ELM具有学习速度快、预测精度高、泛化能力强的显著优势,能实现刀具磨损状态的在线监测。
关键词:刀具磨损小波变换 ELM 遗传算法优化BP1、引言刀具是数控机床中关键的执行部件,它的状态直接影响着产品加工质量和设备运行效率。
以往,现场工人凭借丰富的经验判断刀具的使用情况,根据加工过程中的现象及声音来判别刀具的磨损状态以此来把握最佳的换刀时间。
随着数控机床自动化的到来,机床设备不仅仅要提高生产效率,还要能检测刀具状态,实现快速自动换刀功能。
刀具磨损监测评估技术能够实时监测刀具磨损状态,尽早发现刀具使用过程中的问题并采取相应措施。
这一技术具有延长刀具使用寿命,避免刀具磨损带来的损失,节省加工成本,减少机床故障停机时间,提高加工效率的重大意义。
本文提出了一种基于单隐含层前馈神经网络——ELM的刀具磨损状态在线监测方法,用于拟合预测刀具磨损量与剩余使用寿命评估。
极限学习机算法中输入层与隐含层间的连接权值和隐含层神经元的阈值是随机产生的,在训练过程中仅设置隐含层的神经元个数一个参数,不需要对随机产生的权值和阈值再加以迭代调整便可以获得全局唯一的最优解。
这一网络学习训练速度快、获得的解为全局最优解,另一大优点是泛化能力强。
本文通过与其他方法的对比实验分析,从拟合预测的准确度、模型的普适性等方面验证极限学习机在刀具磨损预测及剩余寿命评估的有效性。
基于BP神经网络技术的刀具状态监控系统
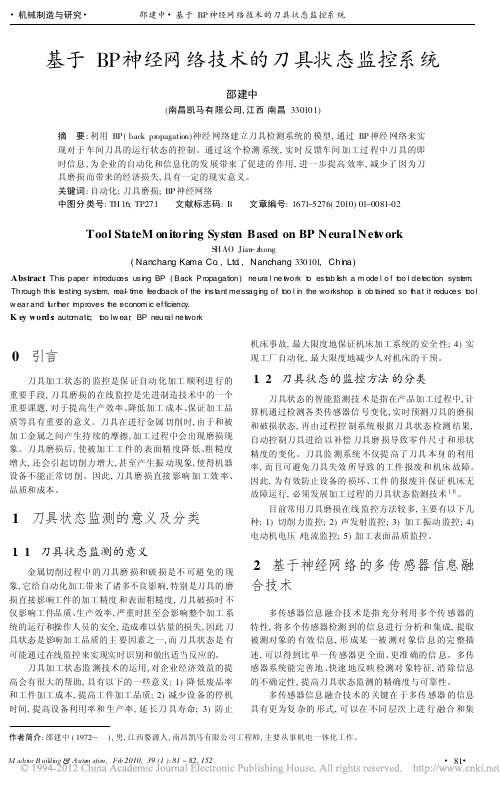
基于BP神经网络技术的刀具状态监控系统邵建中(南昌凯马有限公司,江西南昌330101)摘要:利用BP(back propagation)神经网络建立刀具检测系统的模型,通过BP神经网络来实现对于车间刀具的运行状态的控制。
通过这个检测系统,实时反馈车间加工过程中刀具的即时信息,为企业的自动化和信息化的发展带来了促进的作用,进一步提高效率,减少了因为刀具磨损而带来的经济损失,具有一定的现实意义。
关键词:自动化;刀具磨损;BP神经网络中图分类号:TH16;TP271文献标志码:B文章编号:1671-5276(2010)01-0081-02Tool StateM onitoring Syste m Based on BP Neural Net w orkS HAO Jian-z hong(Nanchang Kama Co.,Ltd.,Nanchang330101,Ch ina)Abstrac t:This paper introduces us ing BP(Back Propagation)neura l ne t w ork t o es t ab lish a m ode l o f t oo l det ec tion syst em. Through this t esting syst em,rea-l tm i e f eedback of the ins t ant messaging of t oo l in the workshop i s ob t ained so t hat it reduces t ool w ear and f urt her m i proves t he econom ic efficiency.K ey word s:auto mati c;t oo lw ear;BP neural net work0引言刀具加工状态的监控是保证自动化加工顺利进行的重要手段,刀具磨损的在线监控是先进制造技术中的一个重要课题,对于提高生产效率、降低加工成本、保证加工品质等具有重要的意义。
基于PSO-BP神经网络的刀具寿命预测
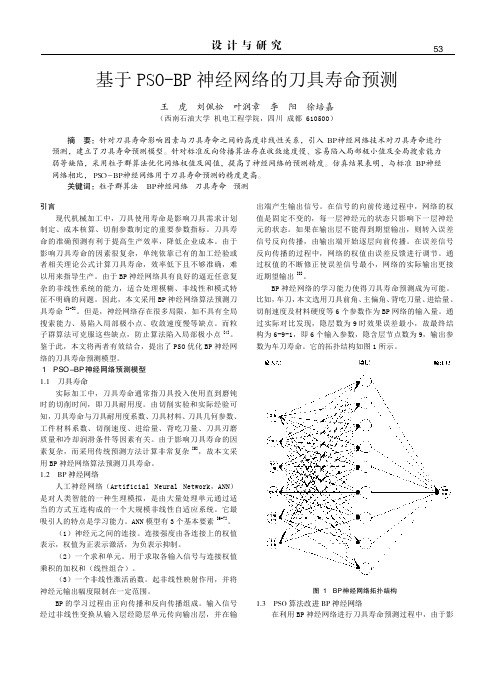
PSO 算法可以有效克服这些问题,所以本文利用 PSO 算法对 BP 神经网络进行初始权值训练 [9]。
BP 神经网络最佳初始权值和阈值的求解过程如下:
(1)PSO 算法变量设置
设当前种群中的粒子 i 的位置为 BP 神经网络权值和阈
值的集合 Xi:
Xi=(xi1xi2…xid)
(1)
设当前粒子的飞行速度为 Vi。迭代过程中,粒子 Xi 根
Vi ∈ [-Vmax,Vmax]。权重函数 W 采用线性递减方式确定:
W = W max− W max−W min × iter iter max
(3)
(2)迭代更新
①计算均方误差:
∑ = Err ( Xi) 1 N
( ) C
k =1
Sik − Qik
2
(4)
其中 C 为输出端个数,Sik 为第 i 个粒子第 k 端实际输 出值,Qik 为期望值。
最大迭代次数,算法结束。
用 PSO 算法优化 BP 网络的具体流程图如图 2 所示。
关键词:粒子群算法 BP 神经网络 刀具寿命 预测
引言 现代机械加工中,刀具使用寿命是影响刀具需求计划
制定、成本核算、切削参数制定的重要参数指标。刀具寿 命的准确预测有利于提高生产效率,降低企业成本。由于 影响刀具寿命的因素很复杂,单纯依靠已有的加工经验或 者相关理论公式计算刀具寿命,效率低下且不够准确,难 以用来指导生产。由于 BP 神经网络具有良好的逼近任意复 杂的非线性系统的能力,适合处理模糊、非线性和模式特 征不明确的问题。因此,本文采用 BP 神经网络算法预测刀 具寿命 [1-3]。但是,神经网络存在很多局限,如不具有全局 搜索能力、易陷入局部极小点、收敛速度慢等缺点。而粒 子群算法可克服这些缺点,防止算法陷入局部极小点 [4]。 鉴于此,本文将两者有效结合,提出了 PSO 优化 BP 神经网 络的刀具寿命预测模型。 1 PSO-BP 神经网络预测模型 1.1 刀具寿命
基于径向基神经网络的刀具寿命预测模型研究

———————————————收稿日期:2018-07-10基金项目:2017年智能制造综合标准化与新模式应用(2017ZZ001);四川省科技支撑计划(2017GZ0064、2017GZ0066)作者简介:徐营利(1993-),男,河南周口人,硕士研究生,主要研究斱向为数字化车间;王展(1980-),男,四川南江人,工程硕基于径向基神经网络的刀具寿命预测模型研究徐营利1,王展2,胡晓兵1,张波1,刘志明1(1.四川大学 制造科学与工程学院,四川 成都 610065; 2.成都中电锦江信息产业有限公司,四川 成都 610051)摘要:通过分析总结影响刀具寿命的主要影响因素,建立铣削刀具加工参数与刀具寿命的径向基神经网络模型。
训练模型使用了10组样本数据,以刀具直径、铣削速度、铣削宽度、铣削深度、进给量、刀具齿数作为网络输入参数,采用十折交叉验证方法对所构建模型进行验证,能够对刀具寿命进行较为准确的预测。
与传统BP 神经网络模型比较发现,径向基神经网络具有更好的预测精度和稳定性,是预测刀具寿命的一条有效途径。
关键词:刀具寿命;径向基神经网络;十折交叉法 中图分类号:TH164文献标志码:Adoi :10.3969/j.issn.1006-0316.2019.02.003文章编号:1006-0316 (2019) 02-0013-05Research on Tool Life Prediction Model Based on Radial Basis Function Neural NetworksXU Yingli 1,WANG Zhan 2,HU Xiaobing 1,ZHANG Bo 1,LIU Zhiming 1( 1.School of Manufacturing Science and Engineering, Sichuan University, Chengdu 610065, China; 2.CECJinJiang Info Industrial Co., Ltd., Chengdu 610051, China )Abstract :By analyzing and summarizing the main influencing factors of tool life, a radial basis neural network model for machining parameters and life of milling tools is established. The training model uses 10 sets of sample data. The tool diameter, milling speed, milling width, milling depth, feed and tool teeth number are used as network input parameters. The ten-fold cross validation method is used to validate the model and the tool life can be accurately predicted. Compared with the traditional BP neural network model, the RBF neural network has better prediction accuracy and stability , and is an effective approach to tool life prediction. Key words :tool life ;radial basis neural network ;10-foldcross-validation刀具寽命是指一把刀具从第一次投入切削开始直到报废为止所经历的切削时间总和[1]。
基于CPSO-BP的刀具寿命预测算法

No. 8Aug. 2020第8期 2020年8月组合机床与自动化加工技术Modular Machine Tool & Automatic Manufacturing Technique文章编号:1001 -2265(2020)08 - 0057 - 03DOI : 10.13462/j. cnki. mmtamt. 2020.0&014基于CPSO-BP 的刀具寿命预测算法**收稿日期:2019-10 - 09;修回日期:2019-11-15*基金项目:国家自然科学基金(51805212);江苏省自然科学基金(BK20160182);山东省重大科技创新工程项目(2019JZZY020111)作者简介:曾晓雪(1993-),女,甘肃武威人,江南大学硕士研究生,研究方向为先进制造系统,(E-mail) xi aO xue_zeng@ 163. com;吉卫喜(1961-),男,江苏姜堰人,江南大学教授,博士生导师,博士,研究方向为先进制造系统、产品数字化设计及制造,(E-mail)ji_webd@ 126. com o曾晓雪i,吉卫喜V,徐杰1(1江南大学机械工程学院,江苏无锡214122;2江苏省食品制造装备重点实验室,江苏无锡214122)摘要:为了改善刀具寿命预测的精准度,文章在已有的PSO-BP 神经网络算法中引入混沌理论,提出 了一种基于混沌粒子群算法优化BP 神经网络(CPSO-BP 神经网络)的刀具寿命预测方法。
该方法采用粒子群算法优化网络权值和阈值,通过混沌扰动更新粒子的位置。
CPSO-BP 神经网络算法既避免了 BP 神经网络存在的收敛速度慢、易陷入局部最优的缺点,又改善了全局搜索能力,同时,降 低了粒子群优化算法造成早熟收敛或停滞的可能性。
仿真结果表明:与已有的PSO-BP 神经网络算法相比,该文的CPSO-BP 神经网络算法用于刀具寿命预测时收敛速度和预测精度均更胜一筹。
基于小波分析和神经网络的刀具磨损预测
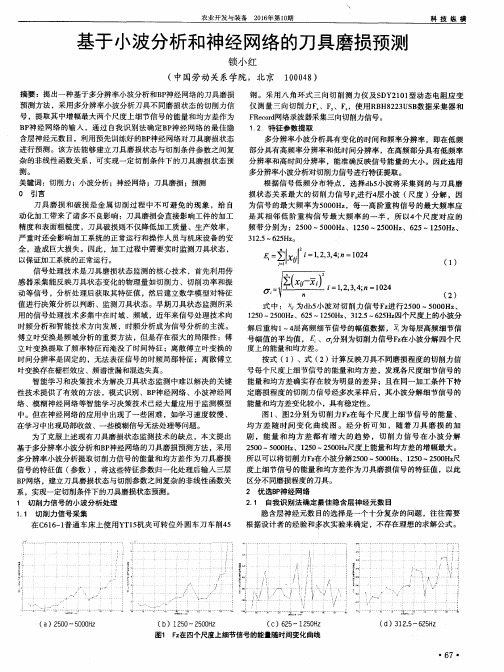
科 技 纵 横
基于 小波 分析 和神经 网络 的刀具磨损预测
锁 小 红
( 中国劳动关系学院,北京
摘 要 :提 出一种 基 于 多分 辨率 小 波 分析 和 B P 神 经 网络 的 刀具 磨损 预 测 方法 ,采用 多 分 辨 率小 波 分 析刀 具 不 同磨 损 状 态 的切 削 力信
1 . 2 特征 参数 提取 多分辨率小波分析具有变化的时间和频率分辨率 ,即在低频
号 ,提取其中增幅最大两个尺度上细节信号 的能量和均方差作为
B P 神 经 网络 的输 入 ,通 过 自我 识 别 法 确 定 B P 神 经 网 络 的最 佳 隐 含层 神 经元 数 目 ,利 用 预先 训 练好 的B P 神 经 网络 对 刀具 磨 损状 态 进 行 预 测 。该 方 法 能够 建 立 刀具 磨 损状 态 与 切 削条 件 参 数 之 间复 杂 的非 线性 函数 关 系 ,可 实现 一 定 切 削条 件 下 的刀 具 磨 损状 态 预
C r : i =1 , 2 , 3 , 4 ; n= 1 0 2 4
…
信号处理技术是刀具磨损状态监测的核心技术 ,首先利用传 感 器采 集 能 反 映刀 具 状态 变 化 的 物理 量 如 切削 力 、切 削功 率 和 振 动等信号 ,分析处理判断、监测刀具状态。早期刀具状态监测所采 用的信号处理技术多集 中在时域、频域 ,近年来信号处理技术 向
测。
部分具有高频率分辨率和低时间分辨率 ,在高频部分具有低频率 分辨率和高时间分辨率,能准确反映信号能量的大小。因此选用 多分辨率小波分析对切削力信号进行特征提取。 根 据 信 号 低 频 分 布 特 点 ,选 择 d b 5 A x 波 将 采 集 到 的 与 刀具 磨 损状态关系最大 的切削力信号F 进行4 层小波 ( 尺度 )分解 ,因 为信号 的最大频率为5 0 0 0 H z ,每一高 阶重构信号 的最大频率应 是其 相邻低 阶重构信 号最大频率 的一半 ,所 以4 个尺度 对应 的
- 1、下载文档前请自行甄别文档内容的完整性,平台不提供额外的编辑、内容补充、找答案等附加服务。
- 2、"仅部分预览"的文档,不可在线预览部分如存在完整性等问题,可反馈申请退款(可完整预览的文档不适用该条件!)。
- 3、如文档侵犯您的权益,请联系客服反馈,我们会尽快为您处理(人工客服工作时间:9:00-18:30)。
1.2 刀具寿命预估的 BP 神经网络模型的建立
BP 神经网络误差反馈的学习能力为建立刀具寿 命预估模型提供了理论保证。建立刀具寿命预估模型 时,我们规定切削方式是一定的,选取工件材料、切削 用量来描述刀具的切削状态。它们分别对应着工件材 料切削加工性、切削深度、进给量、切削速度这 4 个影
2.2 寿命预测模型的运算流程
在刀具材料、加工方式确定的前提下,准备好样本 数据,按照 BP 学习算法过程,对预测模型进行仿真。
寿命预测模型的学习过程流程图如图 2 所示。
3 预测模型应用实例
下文以文献 [5] 中的资料和学校某数控车间中的刀 具使用寿命为例来验证预测模型的准确性,采用 YT15 硬质合金圆盘铣刀来进行寿命预测验证。
关键词:刀具寿命影响因素 人工神经网络模型 刀具寿命预测
[ABSTRACT] The dominant factors affecting tool life are analyzed. According to the nonlinear relationship between factors and tool life, the tool life prediction model based on BP neural network is built up and the computing and demonstration are carried out by using this model. The results show that the model prediction value is very closed to the expected value of tool life, so the model is proved to be reliable and effective.
6
较难切削 材料
0.5 ~ 0.65
45Cr 调质, 65Mn 调质
7
难切削 材料
普通 难切削材料
0.15 ~ 0.5
50CrV 调质, 1Cr18Ni9Ti 未淬火,
α 相钛合金
8
很难切削 材料
<0.15
β 相钛合金, 镍基高温合金
层与输出层之间的权值用 Nj 表示。所有的神经元采用
的激活函数均为 sigmoid 函数:
否
e-ε < 0
是
误差逆向传播 重新修改权重
图 2 寿命预测模型运算流程 Fig.2 Computing flow of tool life prediction model
表 2 样本数据集
样本组 工件相对 切削深度 αp/ 进给量 f/
序号
加工性
mm
(mm·r-1)
1
2.5
1
0.20
2
2.5
4
0.30
(5)误差逆向传播,逐层按梯度下降法修改联结权 值,根据 Delta 学习法则,误差逆向传播时隐含层 J 任一 节点与输出层 R 之间的联结权值为
学术论文
RESEARCH
输入一组样本数据;输入输入层与隐 含层之间的权值;输入隐含层与 输出层之间的权值
开始训练下一组 样本数据
调用激励函数 得到隐含层的数据大小
2.1 模型训练方法
寿命预测模型的学习算法实现过程: (1)初始化,设置网络结构,选取训练样本对 [X′k , Dk] 。赋给联结权值 Wij、Nj;各一个较小的随机非零初 始值,迭代次数 n=0。X′k 为每对样本中影响因素的数据 数组,Dk 为每组影响因素对应的期望寿命值。其中 k 为 样本对数。 (2)对训练样本中的每一个指标值 X′k i进行数据归 一化处理。变换关系式为:
3
2.5
8
0.40
4
2.0
1
0.20
5
2.0
4
0.30
6
2.0
8
0.40
7
1.5
1
0.20
8
1.5
4
0.30
9
1.5
80.40ຫໍສະໝຸດ 101.01
0.20
11
1.0
4
0.30
12
1.0
8
0.40
13
0.25
1
0.20
14
0.25
4
0.30
15
0.25
8
0.40
切削速度 v/ (m·min-1)
300 210 160 250 190 150 235 160 120 130 140 160 185 120 95
Keywords: Factors affecting tool Life Model based on artificial neural network Tool life prediction
随着数控机床应用范围的迅速扩展,车间自动化、 柔性化程度不断提高,加工中心刀具的种类和数量与日 俱增;同时,高速切削技术的广泛应用对刀具的切削性 能及可靠性要求更加苛刻。刀具寿命是一个非常关键 的问题,因为一旦刀具发生磨损或者破损而不能及时地 诊断出,就会导致工件或加工设备的损坏,所以必须对 刀具寿命进行有效的管理 [1]。在自动化生产线上,可能 存在刀具的频繁调度,即刀具可能先后处于不同的加工 状态。加工状态不同,工件材料、切削速度、进给量、切 削深度也不尽相同,这些因素都决定着刀具的磨损,即 决定着刀具的寿命。目前,生产车间中普遍采用累计刀 具当量切削时间的方法来评估刀具的寿命,这种传统的 寿命预测方法会造成大量刀具的保守使用,已经逐渐地 不再适应现代化制造的发展。
输入层 I
权值 Wij
隐含层 J
权值 Nj
输出层 R
图 1 刀具寿命预估的 BP 神经网络模型 Fig.1 Tool life prediction model based on
BP neural network
表 1 材料切削加工性分级表 [4]
等级 代号
材料种类
1
很容易 切削材料
材料名称
一般有色 金属
1 刀具寿命预估的 BP 神经网络模型
1.1 BP 神经网络原理 人工神经网络(Artificial Neural Network,ANN)是对
人类智能的一种生理模拟,它是由大量的处理单元通过 适当的方式互连构成的一个大规模的非线性自适应系 统,最吸引人的特点是它的学习能力。ANN 模型有 3 个 基本要素 [2]:
94 航空制造技术· 2010 年第 8 期
(3)计算实际输出 yk,计算目标函数
。
式中,dk 为第 k 组样本对应的期望寿命值,yk(n)为第 k 组样本迭代第 n 次时对应的寿命输出值,ek(n)为迭代 第 n 次期望寿命与输出寿命之间的误差。
(4)根据生产车间车削刀具的车削精度要求,确定 合适的刀具寿命预估模型的误差,用 ε 表示。若目标函 数 E(n)≤ ε ,则学习过程结束;否则进行误差逆向传播, 进入(5)。
(1)神经元之间的连接。连接强度由各连接上的权 值表示,权值为正表示激活,为负表示抑制。
(2)一个求和单元。用于求取各输入信号与连接权 值乘积的加权和(线性组合)。
(3)一个非线性激活函数。起非线性映射作用,并 将神经元输出幅度限制在一定范围之内。
1986 年,鲁梅尔哈特等人提出了 BP( Back Propagation)神经网络,这是目前应用最广泛的网络 , 采用了 输入层、隐含层和输出层多层感知器(MLP)。BP 网络的 学习过程由正向传播和反向传播组成。它可以将输出 端表现出的误差沿着与输入信号传送相反的方向逐级 向网络的输入端传播。在反向传播的过程中,通过重复 沿着梯度下降搜索求解 [3],以期获得期望输出与实际输 出的误差来满足目标函数。
2010 年第 8 期· 航空制造技术 93
学术论文 RESEARCH
响寿命的指标,并将上述 4 个影响指标作为模型的输 入层。对于隐含层节点数的选择,目前还没有公认的 理论推导方法,只能采取试算的方法。经过反复试算, 选取隐含层节点数为 6 个。输出层选取 1 个神经元即 刀具预估寿命。
模型的输入层指标包括切削用量和工件材料。 (1)切削用量。 切削用量的选择会直接影响切削力、切削功率、刀 具磨损和表面质量以及加工成本。具体对应着切削深 度、进给量和切削速度这 3 个刀具寿命的衡量指标。切 削速度衡量的是在单位时间内刀具(或工件)沿主运动 方向的相对位移 [4]。进给量衡量的是主运动在每行程 (或每转)内工件与刀具之间沿进给运动方向的相对位 移。切削深度衡量的是在通过切削刃基点并垂直于工 作平面的方向上测量的吃刀量(工件已加工表面与待加 工表面的垂直距离)。 在切削用量三要素中,切削速度对刀具寿命的影 响最大,进给量次之,切削深度的影响最小。 (2) 工件材料。 工件材料的硬度、塑性、强度、韧性、弹性模量、导热 系数等均影响工件的切削加工性。根据以上几个因素 划分材料切削加工性等级,直观、全面地反映材料切削 加工性能的特点。以相对加工性的数值量化来加工工 件材料。各种材料的相对加工性见表 1。 模型输出层即为刀具寿命。 预测模型结构为 4-6-1 三层。由此建立的刀具寿 命预估的三层 BP 神经网络模型如图 1 所示。 其中,输入层与隐含层之间的权值用 Wij 表示,隐含
调用激励函数 得到预测输出值
重新运算
计算误差 e
。 其中 j=1,2,3,4。输入层 I 任一节点与隐含层 J 任一节 点之间的联结权值为:
。 式中,η 为学习步长,η 越大,产生的震荡越大。可以选 η 为(n)常数,但其大小应慎重选择。本文中选 η(n)为 常数,η(n)=0.6。