3合成气衍生产品
费托合成产物分布

费托合成产物分布1. 费托合成简介费托合成(Fischer-Tropsch synthesis)是一种通过合成气(合成气主要由一氧化碳和氢气组成)制造液体燃料和化工产品的过程。
费托合成是一种重要的工业化学反应,具有广泛的应用领域。
在费托合成过程中,合成气通过催化剂的作用,发生一系列的化学反应,生成各种有机化合物。
2. 合成气的制备合成气是费托合成的重要原料,通常由煤炭、天然气或生物质通过气化反应制备而成。
气化反应将固体或液体碳源转化为气体燃料,主要产物是一氧化碳和氢气。
3. 费托合成反应机理费托合成反应机理复杂,涉及多个反应步骤。
主要反应包括: - 一氧化碳和氢气的加氢反应生成醇类化合物; - 醇类化合物的脱水反应生成烯烃; - 烯烃的聚合反应生成烷烃。
4. 费托合成产物费托合成反应产物种类繁多,包括液体燃料和化工产品。
主要的产物有: - 烷烃:包括甲烷、乙烷、丙烷等,是费托合成的主要产品之一。
烷烃具有较高的热值和稳定性,可用作燃料和化工原料。
- 醇类化合物:包括甲醇、乙醇、丙醇等,是费托合成的中间产物。
醇类化合物具有较高的溶解性和反应活性,可用于合成其他有机化合物。
- 烯烃:包括乙烯、丙烯、丁烯等,是费托合成的重要产物之一。
烯烃具有较高的反应活性和催化活性,可用于合成聚合物和化工产品。
- 氧化物:包括醛、酮、酸等,是费托合成的副产物。
氧化物具有较高的化学活性,可用于合成其他有机化合物。
5. 费托合成产物分布费托合成产物的分布受多种因素影响,包括反应条件、催化剂选择、反应器设计等。
不同的反应条件和催化剂选择会导致产物分布的差异。
一般来说,低温和高压条件下,费托合成反应产物以烷烃为主。
随着反应温度的升高,烯烃和醇类化合物的产量逐渐增加。
此外,催化剂的选择也会对产物分布产生影响。
铁基催化剂通常偏向于产生烯烃和醇类化合物,而钴基催化剂则更倾向于产生烷烃。
在实际工业生产中,费托合成产物的分布通常通过优化反应条件和催化剂选择来实现。
Chapter 3 合成氨及下游产品

平衡常数随温度的↗而↙,因而↙温度有利于变换反应的进行,
变换气中残余的一氧化碳含量低。
2011/12/24 School of Chemistry and Chemical Engineering, SWPU 18
3.4.1 一氧化碳变换
二、平衡变换率及影响因素 1、变换率与平衡转化率
变换率
衡量CO变换程度的参数称为变换率,以x表示;已变换的CO的 量与变换前CO的且之百分比。
2011/12/24
School of Chemistry and Chemical Engineering, SWPU
13
3.3 合成氨的原料
合成氨原料:N2、H2。
N2:来源于空气 可以在低温下将空气液化、分离而得;或在制氢时中加入空气。 H2:蒸汽转化而来 天然气、油田气、炼厂气、焦炉气、石油产品、煤或者电解水
17
3.4.1 一氧化碳变换
危害:CO对氨合成催化剂有毒害。 目的:利用水蒸气把CO变换为H2和易清除的CO2。 化学反应:CO与H2O反应,生成CO2和H2。 CO+H2O=CO2+H2 一、反应热效应和平衡常数 变换反应为放热反应,平衡常数为 △H=-41.19 kJ/mol
Kp
* * yCO y H2 2 * * yCO yH 2O
3.4.1 一氧化碳变换
2、影响平衡变换率的因素 (1)温度 温度↙,平衡变换率↗。 (2)H2O/CO 平衡变换率随H2O/CO的↗而↗。 (3)压力
在4MPa以下时,压力对变换率无影响。
(4)CO2 ↙变换气中的CO2,有利于↗CO平衡变换率。
2011/12/24
School of Chemistry and Chemical Engineering, SWPU
合成气制甲醇 合成气成分
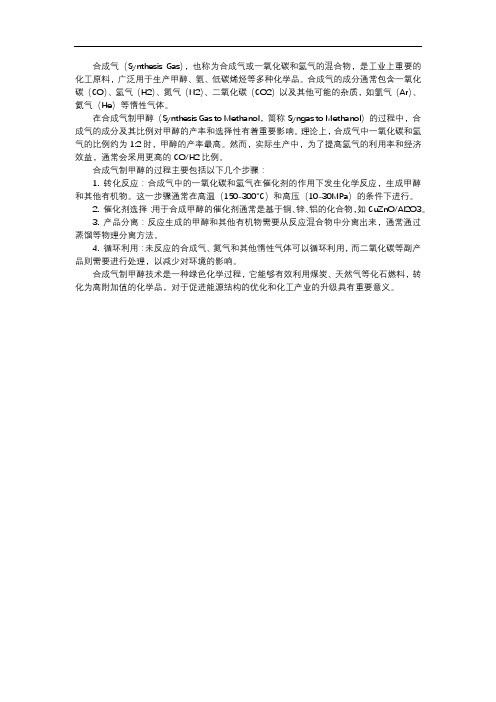
合成气(Synthesis Gas),也称为合成气或一氧化碳和氢气的混合物,是工业上重要的化工原料,广泛用于生产甲醇、氨、低碳烯烃等多种化学品。
合成气的成分通常包含一氧化碳(CO)、氢气(H2)、氮气(N2)、二氧化碳(CO2)以及其他可能的杂质,如氩气(Ar)、氦气(He)等惰性气体。
在合成气制甲醇(Synthesis Gas to Methanol,简称Syngas to Methanol)的过程中,合成气的成分及其比例对甲醇的产率和选择性有着重要影响。
理论上,合成气中一氧化碳和氢气的比例约为1:2时,甲醇的产率最高。
然而,实际生产中,为了提高氢气的利用率和经济效益,通常会采用更高的CO/H2比例。
合成气制甲醇的过程主要包括以下几个步骤:
1. 转化反应:合成气中的一氧化碳和氢气在催化剂的作用下发生化学反应,生成甲醇和其他有机物。
这一步骤通常在高温(150-300°C)和高压(10-30MPa)的条件下进行。
2. 催化剂选择:用于合成甲醇的催化剂通常是基于铜、锌、铝的化合物,如CuZnO/Al2O3。
3. 产品分离:反应生成的甲醇和其他有机物需要从反应混合物中分离出来,通常通过蒸馏等物理分离方法。
4. 循环利用:未反应的合成气、氮气和其他惰性气体可以循环利用,而二氧化碳等副产品则需要进行处理,以减少对环境的影响。
合成气制甲醇技术是一种绿色化学过程,它能够有效利用煤炭、天然气等化石燃料,转化为高附加值的化学品,对于促进能源结构的优化和化工产业的升级具有重要意义。
煤气化产物

煤气化产物1. 煤气化产物概述煤气化是一种将固体煤转化为可燃气体的过程,其产物主要包括: - 合成气 - 焦炉煤气 - 煤焦油 - 煤灰和煤渣2. 合成气合成气是煤气化的主要产物之一,它是由一氧化碳(CO)和氢气(H2)组成的混合气体。
合成气具有高的燃烧价值和广泛的应用价值,可以用作工业过程中的燃料或化工原料。
2.1 合成气的用途合成气可以用于以下方面: 1. 合成甲醇、甲醇汽车燃料和一些有机化学品的原料;2. 生产氨,用于制造化肥;3. 用作合成石化产品的催化剂;4. 作为工业锅炉和热电厂的燃料。
2.2 合成气的制备技术合成气的制备技术主要包括: 1. 煤气化技术:通过高温和压力将煤转化为合成气;2. 水煤气转化技术(WGS):将一氧化碳和水蒸气在催化剂的作用下转化为二氧化碳和氢气。
3. 焦炉煤气焦炉煤气是煤炭冶炼过程中的主要煤气产物。
它是在焦炉中煤炭加热过程中产生的,主要成分为一氧化碳、氮气和一些有害物质。
3.1 焦炉煤气的利用焦炉煤气可以用于以下方面: 1. 作为燃料用于热电厂的发电; 2. 用于生产合成氨和合成甲醇等化学产品; 3. 作为城市燃气供应; 4. 用于钢铁厂内的其他生产工艺。
3.2 焦炉煤气的净化处理焦炉煤气中含有一些有害物质,如硫化物、氰化物和苯系物等,需要进行净化处理。
净化处理主要包括: 1. 脱硫:使用吸收剂吸收焦炉煤气中的硫化物,使其达到符合环保标准; 2. 脱氰:通过氧化反应去除焦炉煤气中的氰化物; 3. 脱苯:使用吸附剂去除焦炉煤气中的苯系物。
4. 煤焦油煤焦油是煤气化过程中产生的一种液体副产物,它具有较高的能量价值和广泛的应用价值。
4.1 煤焦油的组成和性质煤焦油主要由多环芳烃和杂原子组成,具有高粘度和高热值。
其主要性质包括: 1. 粘度:煤焦油的粘度较高,影响其在输送和应用过程中的流动性; 2. 热值:煤焦油的热值较高,可以用作燃料或燃料油; 3. 成分:煤焦油中含有多种有机化合物,可以作为化工原料。
合成气的生产工艺与设备
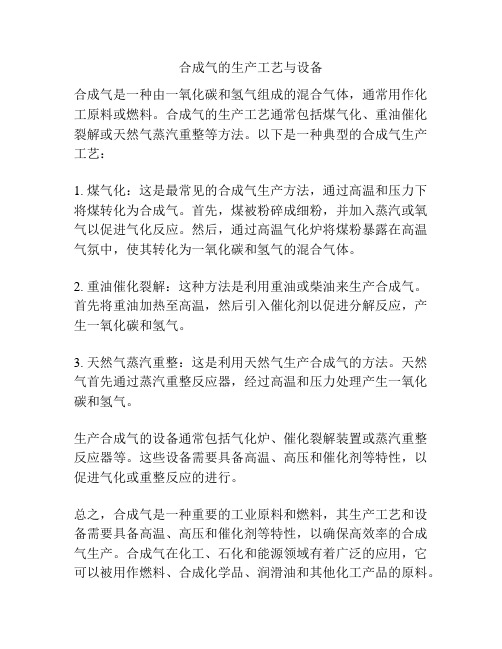
合成气的生产工艺与设备合成气是一种由一氧化碳和氢气组成的混合气体,通常用作化工原料或燃料。
合成气的生产工艺通常包括煤气化、重油催化裂解或天然气蒸汽重整等方法。
以下是一种典型的合成气生产工艺:1. 煤气化:这是最常见的合成气生产方法,通过高温和压力下将煤转化为合成气。
首先,煤被粉碎成细粉,并加入蒸汽或氧气以促进气化反应。
然后,通过高温气化炉将煤粉暴露在高温气氛中,使其转化为一氧化碳和氢气的混合气体。
2. 重油催化裂解:这种方法是利用重油或柴油来生产合成气。
首先将重油加热至高温,然后引入催化剂以促进分解反应,产生一氧化碳和氢气。
3. 天然气蒸汽重整:这是利用天然气生产合成气的方法。
天然气首先通过蒸汽重整反应器,经过高温和压力处理产生一氧化碳和氢气。
生产合成气的设备通常包括气化炉、催化裂解装置或蒸汽重整反应器等。
这些设备需要具备高温、高压和催化剂等特性,以促进气化或重整反应的进行。
总之,合成气是一种重要的工业原料和燃料,其生产工艺和设备需要具备高温、高压和催化剂等特性,以确保高效率的合成气生产。
合成气在化工、石化和能源领域有着广泛的应用,它可以被用作燃料、合成化学品、润滑油和其他化工产品的原料。
由于其多种用途和重要性,合成气的生产工艺和设备一直是广大化工企业和研究机构关注的焦点。
在合成气的生产过程中, 控制气化过程的温度、压力、气氛等参数对于合成气的产率和质量至关重要。
气化反应需要高温(通常在1000℃以上)和高压(通常在20-30个大气压),这就需要设备具备很强的耐高温、耐腐蚀和耐压能力。
气化炉一般采用高温合金钢制造,内衬耐火材料(如铬铝砖)以抵御高温、腐蚀和机械磨损。
此外,气化反应还需要通过控制氧气或蒸汽的进气速率和气氛成分来实现反应的均匀性和高产率。
为了做到这一点,相关的配气系统和电控系统也是必不可少的。
而在重油催化裂解法中,需要催化剂和催化裂解装置。
催化剂一般采用钼、镍、镁等金属氧化物和硅铝酸盐等复合物,以促进重油分解并提高合成气产率。
第四章_合成气的生产过程.pptx
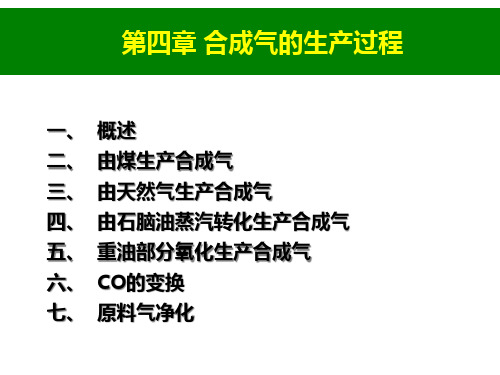
0.1MPa下碳 -蒸汽反应 的平衡组成
2MPa下碳蒸汽反应的 平衡组成
动力学特征 气固反应,反应速率不仅与化学反应速率,还与气化剂 向碳 表面的扩散速率有关。另外,反应速率还与煤的 种类有关:无烟煤<焦炭<褐煤(反应活性)
(1) 对于碳与氧气的反应,一般认为先生成CO2,然后0~ 1200℃高温反应 ;大量吸热
要求:大量供热 采取措施: 通过燃烧一部分C的反应热, 维持整个系 统的热平衡。
具体方法包括: 固定床 间歇式气化法 连续式气化法(鲁奇法) 流化床 气流床(德士古法)
.固定床间歇法(蓄热法)
优:制气时 不用氧气, 不需空分装 置
缺:生产 过程间歇, 发生炉的生 产强度低, 对煤的质量 要求高。
• 蒸汽转化法 Steam reforming
分H6部H氧2k29分J98化=8/氧m2法=部0化-o63l法k分5CCJ.HH7/氧mk44CCJo++H化H/强lm14H4/法o++22外OOl1H强2/热22供OO催外高平2化热温P供催剂衡高a化,r温热,技tCH剂iO,a2C技术/lCOC+o术OCO3+成xHO+易成2i2dH3熟+调熟Ha22t2H,节,iHHoH2Hn2.22需/29/CH98CH=8纯O222=9O098=-氧=863=2k35=0J.-73/63mkk5JJo.7//lmmkJoo/llm强热ol外平强热供衡外平热,供H衡 -35.7kJ/mol 热平衡,H2/CO易调节.需纯氧
.鲁奇炉结构示意图
1.煤箱 2.分布器 3.水夹套 4.灰箱 5.洗涤器
特点:
气化剂:水蒸汽和氧气的 混合物
燃料层分层:与间歇法 大致相同
合成气的生产过程
合成气的生产过程1. 简介合成气是由一氧化碳和氢气组成的气体混合物,通常用作能源源和化工原料。
它可以通过多种不同的方法来生产,本文将介绍合成气的主要生产过程。
2. 生产方法2.1 煤气化法煤气化法是最常见和传统的合成气生产方法之一。
该方法将煤炭与氧气和水蒸气在高温下反应,产生一氧化碳和氢气。
具体的步骤如下: 1. 原料准备:将煤炭破碎成适当的大小并干燥。
2. 煤气化反应:将干燥的煤炭与预热的氧气和水蒸气一起送入煤气化炉中,在高温下反应生成合成气。
3. 硫化物的处理:通过添加适当的催化剂或吸收剂,去除合成气产生过程中的硫化物。
4. 分离和净化:将产生的合成气进行分离和净化,去除杂质和不需要的组分。
2.2 水蒸气重整法水蒸气重整法是另一种常用的合成气生产方法。
该方法主要用于天然气和液化石油气等碳氢化合物的转化。
具体的步骤如下: 1. 原料准备:准备天然气或液化石油气作为原料。
2. 蒸汽重整反应:将天然气或液化石油气与水蒸气以适当的比例混合,通过蒸汽重整催化剂在高温下反应,生成一氧化碳和氢气。
3. 硫化物的处理:与煤气化法相同,通过添加适当的催化剂或吸收剂,去除合成气产生过程中的硫化物。
4. 分离和净化:将产生的合成气进行分离和净化,去除杂质和不需要的组分。
2.3 部分氧化法部分氧化法是一种将重油、煤焦油和煤等碳质燃料直接部分氧化而制取合成气的方法。
具体的步骤如下: 1. 原料准备:准备重油、煤焦油或煤作为碳质燃料。
2. 燃烧反应:将碳质燃料与氧气在合适的反应条件下进行部分燃烧,生成一氧化碳和氢气。
3. 硫化物的处理:与前两种方法一样,通过添加适当的催化剂或吸收剂,去除合成气产生过程中的硫化物。
4. 分离和净化:将产生的合成气进行分离和净化,去除杂质和不需要的组分。
3. 应用领域合成气作为一种重要的能源源和化工原料,被广泛应用于以下领域: - 化工工业:合成气可用于制造合成油、合成烯烃、合成醇、氨和甲醇等化学品。
鲁奇(MTP)三合一项目简介(甲醇制烯烃)
(3)项目采用工艺
本项目采用鲁奇专利的两级氧克劳斯(OXYCLAUS®)硫回
收工艺加LTGT®(Lurgi Tail Gas Treatment)尾气处理技 术,处理能力可达传统工艺的200%,总硫回收率可达99.8% 以上。 硫磺产品的指标如下:
典型克劳斯工艺流程
氧克劳斯硫回收
分 离 器
过 滤 器
CO18.5% CO237.5% H242.46%
Ø3200×5100 单重59.7T 材质: 14Cr1MoR+ 347 催化剂K811:25m3
第 一 变 换 炉
450℃
250℃
去低温甲醇洗 40℃, 3.4MPa,262000 Nm3/Hr 低压蒸汽
36.5T/h, 160℃
H2S0.43%
第 二 变 换 炉
370℃
48.4T/h, 108℃
Ø 3800×1 1000 单重68.4T 催化剂 QCS01:76m3
去气化
分 离 器
脱盐水
低温甲醇洗工艺(Rectisol)
以各种不同原料制取成气的工艺中,都有相
当数量的CO2以及对甲醇合成有害的毒物H2S、 COS等毒物需要除去,这类酸性气体经中合 成气中脱出后又可进一步回收利用。在本项 目里,脱出的CO2经压缩后作为Shell煤气化 工序的粉煤载气,富硫气体(以H2S为主) 经过进一步回收利用生产硫磺。
克劳斯工艺的基本原理
克劳斯硫回收工艺是1883年由CLAUS提出的,并在20世纪初
实现工业化,此法回收硫的基本反应如下:
以上反应均是放热反应,反应(1)、(2)在燃烧炉中进行,
H2S+1/2O2=S+H2O H2S+3/2O2=SO2+H2O 2H2S+SO2=3S+2H2O
合成气的生产过程
合成气的生产过程
概述 由煤制合成气
由天然气制合成气
由渣油制合成气
概述
合成气:CO和H2 (H2/ CO=1/2~1/3)
原料: ①煤 ②天然气 ③石油馏分 ④农林废料 ⑤城市垃圾等
合成气的生产方式
一、以煤为原料
间隙 方式 连续 气化剂: 水蒸气和氧气
二、以天然气为原料
方法: √ 转化法和部分氧化法
用途: 1、合成氨和氢气(H2/CO=3) 2、甲醇、醋酸、乙烯、乙二醇等
三、以重油或渣油为原料
方法:
部分氧化法 三种方法比较: 天然气成本最低 重油或渣油可以使石油资源充分利用
合成气的应用实例
一、工业化的主要产品 1、合成氨 2、合成甲醇 3、合成醋酸 4、烯烃的氢甲酰化 5、合成天然气、汽油和柴油
天然气蒸汽转化流程和主要设备 基本步骤: √
天然气蒸汽转化流程
由渣油制合成气
步骤:
渣油部分氧化过程的反应 C: 84%~87% H: 11%~12.5% S、N、O 、Ni 、V 渣油部分氧化操作条件 1.温度 2.压力 3.氧油比 4.蒸汽油比 5.原料的预热温度 (渣油不超过120~150℃)
天然气蒸汽转化过程工艺原理 甲烷水蒸气转化过程工艺原理 影响平衡转化率的主要因素: 1.温度 2.水碳比 3.压力 甲烷水蒸气转化催化剂 (催化剂的共性)
甲烷水蒸气转化反应动力学 1.温度的影响 2.压力的影响 3.水碳比 过高 过低
天然气蒸汽转化过程的工艺条件 依据: 热力学 动力学 化工原理 条件: 1.压力 2.温度 3.水碳比 4.气流速度
流化床连续式气化制水煤气
温克勒(Winkler) 示意图如图。
气流床连续式气化制水煤气
合成气的生产过程
合成气的生产过程合成气(Synthesis gas,简称syngas)是一种含有一氧化碳和氢气的混合气体,可用于许多重要的工业过程,如制氢、化学合成和能源生产。
合成气的主要生产过程有煤气化、蒸汽重整和部分氧化三种方法。
以下是对这三种方法的详细介绍。
1.煤气化:煤气化是通过将固体煤转化为可燃气体的过程,它是合成气生产中最常用的方法。
煤气化过程分为两个阶段:干煤气化和水煤气化。
首先,干煤气化是将煤在高温条件下与空气或氧气反应产生一氧化碳和氢气。
煤被加热至高温(约700-1400℃)并通过供气管注入少量的氧气或空气,从而引发煤的部分燃烧和热裂解。
在这个过程中,煤中的可燃物质将转化为一氧化碳和氢气,同时产生煤气化渣滓。
然后,水煤气化是在干煤气化的基础上继续进行的。
煤气化渣滓与水蒸气反应生成CO和H2、在水煤气化中,煤中的碳氢化合物与水蒸气反应生成更多的一氧化碳和氢气。
该反应通常在较低的温度(约200-350℃)和较高的压力(约20-50个大气压)下进行。
整个煤气化过程产生的合成气可以根据不同用途进一步处理,例如通过净化去除杂质,或进行酸碱平衡调整以满足特定的化学反应要求。
2.蒸汽重整:蒸汽重整是一种将天然气、石油或重质烃类转化为合成气的方法。
这种方法经常用于制备合成氨、合成甲醇和合成烃等化学品。
首先,通过部分燃烧天然气或石油产生的混合燃料与空气混合并通过催化剂床,使其部分氧化。
在这个过程中,产生一氧化碳和氢气。
然后,将得到的混合气体与过量的水蒸气反应,通过蒸汽重整反应产生更多的一氧化碳和氢气。
该反应在高温(700–1100℃)和中等压力(10-30个大气压)条件下进行。
最后,合成气经过净化、升压和其他处理,以满足特定的产品要求。
3.部分氧化:部分氧化是通过将碳氢化合物(如天然气、石油或液化石油气)与氧气反应产生合成气的一种方法。
这种方法通常用于合成气和液体燃料的生产。
首先,将碳氢化合物与过量的氧气在高温(约1300–1500℃)和高压(20-30个大气压)条件下反应。
- 1、下载文档前请自行甄别文档内容的完整性,平台不提供额外的编辑、内容补充、找答案等附加服务。
- 2、"仅部分预览"的文档,不可在线预览部分如存在完整性等问题,可反馈申请退款(可完整预览的文档不适用该条件!)。
- 3、如文档侵犯您的权益,请联系客服反馈,我们会尽快为您处理(人工客服工作时间:9:00-18:30)。
3.1 氨
3.1.1 概述
(1)合成氨工业的重要性
农业:尿素、硝酸铵、硫酸铵、碳酸氢氨等;还可以生产 多种氮混肥、复合肥。
工业:
炸药:
硝酸、硝酸铵、硝化甘油、三硝基甲苯和硝基纤维素
化纤、塑料工业:
己内酰胺、尼龙6单体、己二胺、人造丝、丙烯腈、酚醛 树脂
制冷剂:用于空调、制冰、冷藏系统
1 yNH3 yi
2 Kpp
r1.5 r 1 2
7
①压力和温度的影响
表3-1 氨合成的平衡常数Kp与温度和压力的关系
/MPa-1
压力,MPa
0.1
10
15
20
30
40
350 0.260 0.298 0.329 0.353 0.424 0.514
温
度
400 0.125 0.138 0.147 0.158 0.182 0.212
5
K f K K p
6
(2)影响平衡氨含量的因素
若总压为p的混合气体中N2、H2、NH3、惰性气体的摩尔 分数分别为yN2, yH2,yNH3,yi。
令原始氢氮比r= yH2/yN2,
pH2 p 1 yNH3 yi
1 yNH3 yi
1 r 1
yNH3
惰性组分的存 在,降低了氢、 氮气的有效分压, 会使平衡氨含量 降低。
11
图3-2 30.4MPa下平衡氨含量与温度的关系(H2:N2=3:1)
(3)合成氨反应动力学 ①动力学过程 反应过程的机理
N2 2 2N
氮气解离吸附
H2 2 2H
氢气解离吸附
N H NH
速
NH H NH2
表面反应
率 控
NH2 H NH3
制
NH3 NH3
产物脱附
步
骤
12
② 影响反应速率的因素 a 压力:当压力增高时,正反应速率加快,逆反应速率减 慢,净反应速率提高 b 温度:温度正逆反应速率常数都有影响,存在最适宜的 温度,具体由气体、压力和催化剂活性而定 c 氢氮比 :对于氢氮比的要求,热力学和动力学上有所不 同,要统筹考虑 d 惰性气体:惰性气体含量增加,反应速率下降
径、孔长和孔结构,反应组分的扩散系数,温度压力以及 气相主流体的浓度与平衡浓度的差距等等。 提高内表面的利用率最好的办法是减小催化剂的颗粒的粒 度,他可以有效的缩短微孔的长度。但是粒度还不能太小, 否则床层阻力增加,动力消耗增加。 综上所述:
低温可能是动力学控制,高温时可能是内扩散。 在相同的温度下大颗粒可能是内扩散,小颗粒可能是化 学动力学控制。
18
催化剂的还原和使用
Fe3O4
H2
3Fe
4
H
2O(
g
),
H
0 298
149.9kJ
/
mol
确定还原条件的原则:
A、使 FeO Fe充2O分3 还原为α-Fe B、使生成的α-Fe结晶不因重结晶而长大。
19
催化剂使用13个月以后各层的状态
试样
促进剂含量
表面 氨含 反应 总孔 平均
AL2O CaO SiO2
℃
450 0.0641 0.0713 0.0749 0.0790 0.0884 0.0996
500 0.0366 0.0399 0.0416 0.0430 0.0475 0.0523
550 0.0213 0.0239 0.0217 0.0256 0.0276 0.0299
8
表3-2 纯3H2-N2混合气体的平衡含量Y﹡NH3×102
13
1、30.4MPa,yi=12%;2、30.4MPa,yi=15%;3、20.3MPa,
yi=15%
1.P定,yNH3↑,则Te、Tm↓
2.P定,yNH3定, 则yi↑, Te 、Tm ↓
3. yNH3定, yi定,则P ↑, Te 、Tm ↑
4. Te、Tm的相对关系只与催化剂活性有关
14
③内扩散对氨合成的影响 影响内表面利用率的因素很多,主要有催化剂内微孔的孔
15
内扩散控制
rNH3 pK
K:扩散系数 P:总压 rNH3:反应速率
16
化学动力学控制
rNH3
k1 pN2
pH3 2 p2
NH 3
k2
p2 NH 3
pH3 2
1
k1、k2:正、逆反应速率常数 rNH3:净反应速率 α为常数,与催化剂性质和反应条件有关,由实验测定
17
3.1.3 合成氨催化剂
冶金工业:提炼矿石中的铜、镍等金属
医药和生物化学:磺胺类药物、维生素
1
(2)合成氨工业发展简介
1754年 普利斯特利
发现
1784年 伯托利 确定
1898年 富兰克和卡罗
氰化法
CaC2 N2 CaCN2 C
CaCN2 3H2O CaCO3 2NH3
1911年 米塔西 铁催化剂
1909年 哈伯
温度越低、压力越高,平衡常数越大,平衡氨含量越高
9
②氢氮比的影响 温度、压力、惰性气体含量一定时,
r1.5
R K p p r 12 0
r=3 时,平衡氨含量最大 (不考虑r对Kp的影响)
实际反应( Kp随r发生变化 )
具有最大氨的平衡含量时,r略小于3,大约在2.68-
2.90之间
10
③惰性气体的影响
低温、高压有利于氨的生成
平衡常数:
Kp
pNH3 P P 0.5 1.5
N2 H2
1 p
yNH3 y y 0.5 1.5
N2 H2
用逸度表示:
K f
f NH3 f f 0.5 1.5
N2 H2
y NH3 K K 0.5 1.5 y y N2 H2
NH3 0.5 1.5 N2 H2
p
4
普遍化逸度系数图
锇催化剂
1901年 吕.查得利 直接合成法
N2 3H2 2NH23
(3)合成氨的原料及流程 原料 氢气和氮气。 流程
原料
造
净
合
分
气
化
成
离
氨
循环气
氨合成是生产过程中的核心部分
3
3.1.2 合成氨理论基础
(1)化学平衡及平衡常数
0.5N2 1.5H2 NH3
H
298
46.22KJ
/
mol
氢气和氮气合成氨是放热的,体积缩小的可逆反应
K2O
SO3
积 m2/
量%
速度 常k
以铁为主的催化剂活性高、寿命长、活性温度范围广、廉价易得、抗毒性好
催化剂的组成
活性组分:四氧化三铁 AL2O3在催化剂中能起到保持原结构骨架的作用,从而 防止活性铁的微晶长大,增加催化剂的表面积提高活性。 CaO起助熔剂作用,可以使晶粒减小,比表面增大。 K2O的加入可以促使催化剂的金属电子逸出功降低。 MgO主要作用是抗硫化物中毒的能力,从而延长催化剂 的使用寿命。