精品热轧工艺流程
热轧工艺流程范文
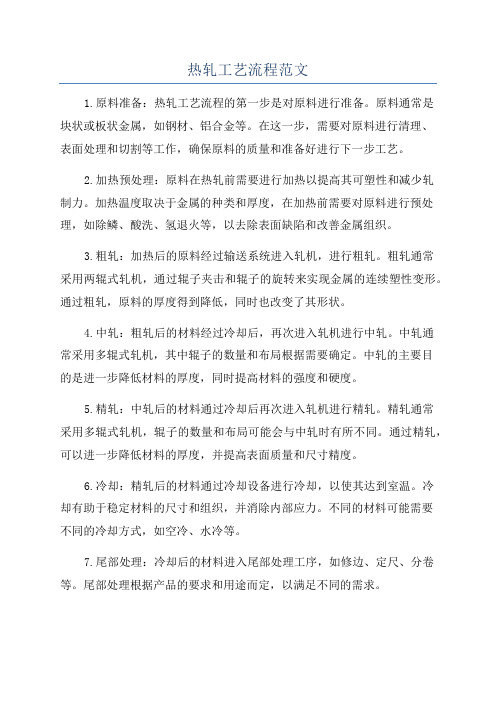
热轧工艺流程范文1.原料准备:热轧工艺流程的第一步是对原料进行准备。
原料通常是块状或板状金属,如钢材、铝合金等。
在这一步,需要对原料进行清理、表面处理和切割等工作,确保原料的质量和准备好进行下一步工艺。
2.加热预处理:原料在热轧前需要进行加热以提高其可塑性和减少轧制力。
加热温度取决于金属的种类和厚度,在加热前需要对原料进行预处理,如除鳞、酸洗、氢退火等,以去除表面缺陷和改善金属组织。
3.粗轧:加热后的原料经过输送系统进入轧机,进行粗轧。
粗轧通常采用两辊式轧机,通过辊子夹击和辊子的旋转来实现金属的连续塑性变形。
通过粗轧,原料的厚度得到降低,同时也改变了其形状。
4.中轧:粗轧后的材料经过冷却后,再次进入轧机进行中轧。
中轧通常采用多辊式轧机,其中辊子的数量和布局根据需要确定。
中轧的主要目的是进一步降低材料的厚度,同时提高材料的强度和硬度。
5.精轧:中轧后的材料通过冷却后再次进入轧机进行精轧。
精轧通常采用多辊式轧机,辊子的数量和布局可能会与中轧时有所不同。
通过精轧,可以进一步降低材料的厚度,并提高表面质量和尺寸精度。
6.冷却:精轧后的材料通过冷却设备进行冷却,以使其达到室温。
冷却有助于稳定材料的尺寸和组织,并消除内部应力。
不同的材料可能需要不同的冷却方式,如空冷、水冷等。
7.尾部处理:冷却后的材料进入尾部处理工序,如修边、定尺、分卷等。
尾部处理根据产品的要求和用途而定,以满足不同的需求。
8.质量检测和包装:完成尾部处理后,对材料进行质量检测,如尺寸测量、力学性能测试等。
通过检测,确认产品的质量是否符合要求。
最后,将产品进行包装,以便储运和使用。
总结:热轧工艺流程是一系列先进的金属加工工艺的组合,通过逐步减小金属坯料的尺寸并改变其形状,最终获得具有高强度和良好表面质量的金属制品。
同时,热轧工艺流程也需要对产品进行严格的质量控制和检测,以确保产品的质量和性能。
热轧钢板的工艺流程

热轧钢板的工艺流程热轧钢板是指钢坯经过预处理后,在高温状态下进行轧制加工而成的一种钢材产品。
它具有优良的机械性能和表面光洁度,广泛应用于建筑、机械制造、船舶、汽车等领域。
下面我们将详细介绍热轧钢板的工艺流程。
1.钢坯预处理:钢坯是从炼钢厂中得到的直接坯料,其表面通常包含锈蚀和杂质等不良物质。
因此,首先需要对钢坯进行预处理,包括酸洗、切割和加热等步骤。
酸洗可以去除钢坯表面的氧化层和锈蚀,并提高表面质量;切割将钢坯切割成适当大小的板坯;加热是为了提高钢坯的可塑性和降低轧制时的轧制力。
2.粗轧:预处理后的钢坯被送入热连轧机械设备中进行粗轧。
粗轧是热轧钢板生产过程中最关键的阶段之一。
在粗轧中,钢坯通过一对或多对辊轧制机进行减轧,使钢坯逐渐变薄,并同时增加长度和宽度。
这个阶段为后续的精轧和整平创造了条件。
3.精轧:在经过粗轧之后,还需要进行精轧来进一步降低钢板的厚度和获得更高的表面质量。
精轧的设备通常包括多高辊轧机或热连轧机。
通过多次的轧制过程,钢板的厚度逐渐减小,并且其内部组织也得到了更均匀的改善。
4.整平:精轧之后,钢板的表面质量已经得到了改善,但尚存在一定程度的不平整。
为了进一步提高钢板的平整度,需要进行整平操作。
整平的机械设备通常包括4辊整平机或6辊整平机。
在整平过程中,钢板通过辊轧制和加压处理,以消除钢板中的残余应力和形变,从而使钢板表面更加平整。
5.冷卷或切割:经过整平的钢板可直接用作一些特殊用途,如船板、容器板等,也可进一步进行冷轧或切割加工。
冷轧是指在室温下对钢板进行再轧制,以获得更高的精度和表面光洁度。
切割是将钢板按照所需尺寸进行切割,以满足客户的具体要求。
6.表面处理和成品检验:热轧钢板经过上述工艺流程后,需要进行最后的表面处理和成品检验。
常见的表面处理方式包括喷涂防锈漆、镀锌或涂漆等,以保护钢板表面不受腐蚀。
成品检验包括物理性能测试、尺寸检验和外观质量检查等,以确保热轧钢板的质量达到标准要求。
热轧工序的主要流程

热轧工序的主要流程热轧工序可是钢铁生产里超有趣的一个环节呢!一、坯料准备。
坯料就是热轧的起始材料啦。
这坯料的来源多种多样,有的是从炼钢车间直接送过来的钢坯,就像刚出炉的小宝贝一样。
这些钢坯的尺寸和形状那都是有一定标准的哦。
比如说,常见的有方坯、板坯啥的。
方坯可能就像个小正方体似的,板坯呢就扁扁的像个大板子。
在坯料准备阶段,工作人员还得仔细检查坯料的质量呢,就像挑水果一样,要是有啥缺陷,像表面有裂缝或者夹杂杂质,那可不行,得把它挑出来,不然会影响后面的工序。
二、加热。
坯料准备好了就得给它加热啦。
这个加热可是个很关键的步骤哦。
要把坯料送到加热炉里去,那加热炉就像一个超级大烤箱。
在这个大烤箱里,坯料会被加热到很高的温度,一般都能达到上千摄氏度呢。
为啥要加热到这么高的温度呀?这是为了让坯料变得软软的,就像橡皮泥一样,这样后面轧制的时候就容易塑形啦。
而且加热的过程也得小心控制呢,温度不能太高也不能太低。
要是温度太高了,坯料可能就会被烧坏,要是温度低了,又达不到理想的轧制效果。
就像烤蛋糕一样,火候得刚刚好才行。
三、轧制。
这轧制可是热轧工序的重头戏呢!加热好的坯料从加热炉里出来,就被送到轧机那里。
轧机就像一个超级大力士,把软软的坯料不断地压薄或者改变形状。
轧机的轧辊是一对大轮子,坯料就在这两个大轮子中间被来回地碾压。
刚开始的时候,坯料还比较厚,经过一道一道的轧辊,就变得越来越薄,或者从方的变成了长条形的,这过程就特别神奇。
而且在轧制的时候,工作人员还得时刻盯着,根据产品的要求调整轧机的压力、速度这些参数。
就好比我们做手工的时候,根据想要的成品不断调整手里的工具一样。
四、精整。
轧制完了可还不算完事儿呢,还得进行精整。
这个精整就像是给产品做最后的美容。
比如说,要把轧制好的钢材进行剪切,把多余的部分剪掉,让它的尺寸符合要求。
就像我们剪头发一样,把不齐的地方都修整齐。
还有的钢材可能需要进行平整处理,让表面更加光滑平整。
热轧工艺流程
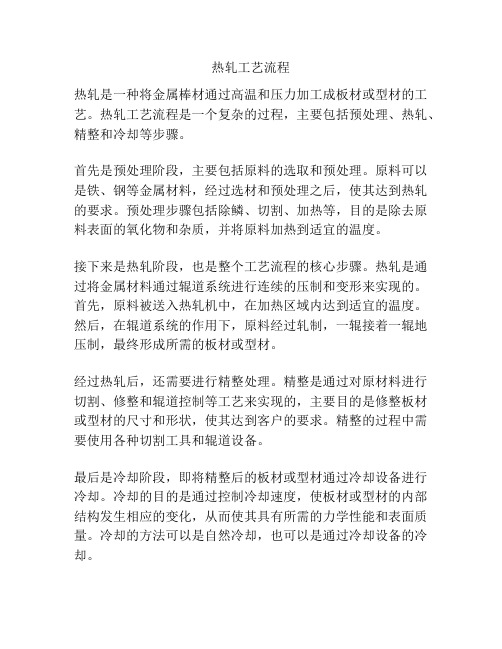
热轧工艺流程
热轧是一种将金属棒材通过高温和压力加工成板材或型材的工艺。
热轧工艺流程是一个复杂的过程,主要包括预处理、热轧、精整和冷却等步骤。
首先是预处理阶段,主要包括原料的选取和预处理。
原料可以是铁、钢等金属材料,经过选材和预处理之后,使其达到热轧的要求。
预处理步骤包括除鳞、切割、加热等,目的是除去原料表面的氧化物和杂质,并将原料加热到适宜的温度。
接下来是热轧阶段,也是整个工艺流程的核心步骤。
热轧是通过将金属材料通过辊道系统进行连续的压制和变形来实现的。
首先,原料被送入热轧机中,在加热区域内达到适宜的温度。
然后,在辊道系统的作用下,原料经过轧制,一辊接着一辊地压制,最终形成所需的板材或型材。
经过热轧后,还需要进行精整处理。
精整是通过对原材料进行切割、修整和辊道控制等工艺来实现的,主要目的是修整板材或型材的尺寸和形状,使其达到客户的要求。
精整的过程中需要使用各种切割工具和辊道设备。
最后是冷却阶段,即将精整后的板材或型材通过冷却设备进行冷却。
冷却的目的是通过控制冷却速度,使板材或型材的内部结构发生相应的变化,从而使其具有所需的力学性能和表面质量。
冷却的方法可以是自然冷却,也可以是通过冷却设备的冷却。
总的来说,热轧工艺流程是一个多步骤的过程,经过预处理、热轧、精整和冷却等阶段,最终得到所需的板材或型材。
这一过程需要高温和压力的作用,需要使用各种设备和工具,并且需要严格控制各个环节的参数,以确保最终产品的质量。
热轧、冷轧、退火、热镀锌等数十张工艺图详解
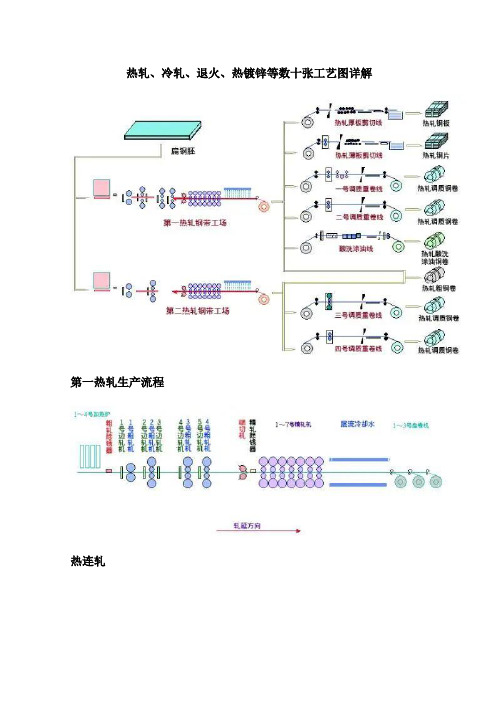
热轧、冷轧、退火、热镀锌等数十张工艺图详解第一热轧生产流程热连轧热轧生产流程>第一热轧钢带生产流程:热轧钢带工场主要制程是将扁钢胚加热后,经粗轧机及精轧机轧延成钢带,并以层流冷却系统喷水冷却至适当温度,再由盘卷机卷成粗钢卷。
开平剪切热轧生产流程>热轧板剪切线布置图:主要功能为将原料钢卷上线解卷、切边、切片、整平、堆叠、及包装为成品钢板叠(HR PLATE)。
调质卷、调质轧延、分切、重卷及包装为成品H.R COIL或H.R BAND〔HR BAND 未调质轧延〕。
调质热轧生产流程>二号调质重卷线布置图:主要功能为将原料钢卷上线解卷、调质轧延、分切、重卷及包装为成品H.R COIL或H.R BAND〔HR BAND 未调质轧延〕。
酸洗涂油卷、焊接、整平、酸洗、调质轧延、切边、涂油、分切及包装为成品酸洗钢卷。
第二热轧生产流程热连轧热轧生产流程>第二热轧钢带生产流程:热轧钢带工场主要制程是将扁钢胚加热后,经粗轧机及精轧机轧延成钢带,并以层流冷却系统喷水冷却至适当温度,再由盘卷机卷成粗钢卷。
调质卷、调质轧延、分切、重卷及包装为成品H.R COIL或H.R BAND〔HR BAND 未调质轧延〕。
调质热轧生产流程>四号调质重卷线布置图:主要功能为将原料钢卷上线解卷、调质轧延、分切、重卷及包装为成品H.R COIL或H.R BAND〔HR BAND 未调质轧延〕。
冷轧酸洗冷轧第一酸洗冷轧线:第一酸洗冷轧线接收热轧钢卷,经过解卷、焊接、整平、盐酸酸洗、裁边之后,再经由串列式冷轧机轧延成厚度较薄之冷轧钢卷。
酸洗冷轧第二酸洗冷轧线:第二酸洗冷轧线是利用张力整平机及酸洗去除热轧钢卷锈皮,清洗、烘干去除钢带表面残酸,由裁边机将钢带裁至下游产线所需宽度及经四站六重式轧延机将热轧钢卷轧至客户所需厚度,并藉自动板形控制器来改善钢带板形,是一连续式酸洗冷轧制程产线。
热浸镀锌连续热浸镀锌线:热浸镀锌线是一条连续性生产线,酸洗冷轧后钢卷送入本产线经过焊接、表面清洗及退火之后进入锌槽镀锌(GI材)或再加热产生锌铁合金(GA材),接着再经过调质轧延及张力整平,最后再依不同需求实施后处理或涂油作业。
热轧工艺流程及其设备
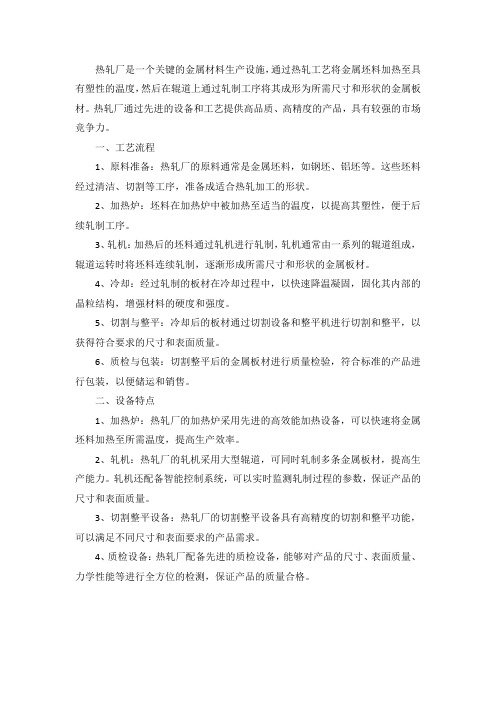
热轧厂是一个关键的金属材料生产设施,通过热轧工艺将金属坯料加热至具有塑性的温度,然后在辊道上通过轧制工序将其成形为所需尺寸和形状的金属板材。
热轧厂通过先进的设备和工艺提供高品质、高精度的产品,具有较强的市场竞争力。
一、工艺流程
1、原料准备:热轧厂的原料通常是金属坯料,如钢坯、铝坯等。
这些坯料经过清洁、切割等工序,准备成适合热轧加工的形状。
2、加热炉:坯料在加热炉中被加热至适当的温度,以提高其塑性,便于后续轧制工序。
3、轧机:加热后的坯料通过轧机进行轧制,轧机通常由一系列的辊道组成,辊道运转时将坯料连续轧制,逐渐形成所需尺寸和形状的金属板材。
4、冷却:经过轧制的板材在冷却过程中,以快速降温凝固,固化其内部的晶粒结构,增强材料的硬度和强度。
5、切割与整平:冷却后的板材通过切割设备和整平机进行切割和整平,以获得符合要求的尺寸和表面质量。
6、质检与包装:切割整平后的金属板材进行质量检验,符合标准的产品进行包装,以便储运和销售。
二、设备特点
1、加热炉:热轧厂的加热炉采用先进的高效能加热设备,可以快速将金属坯料加热至所需温度,提高生产效率。
2、轧机:热轧厂的轧机采用大型辊道,可同时轧制多条金属板材,提高生产能力。
轧机还配备智能控制系统,可以实时监测轧制过程的参数,保证产品的尺寸和表面质量。
3、切割整平设备:热轧厂的切割整平设备具有高精度的切割和整平功能,可以满足不同尺寸和表面要求的产品需求。
4、质检设备:热轧厂配备先进的质检设备,能够对产品的尺寸、表面质量、力学性能等进行全方位的检测,保证产品的质量合格。
简述热轧型钢工艺流程

简述热轧型钢工艺流程热轧型钢啊,这可挺有趣的呢。
一、原料准备。
这就像是做饭先得准备食材一样。
生产热轧型钢的原料呢,主要就是钢坯啦。
这钢坯可得符合一定的要求哦。
它的化学成分得合适,比如说碳含量啦、锰含量啦这些元素的比例都得在一个合理的范围内。
而且钢坯的尺寸也要精准,要是尺寸不对,后面加工就麻烦啦。
就像你要做一个特定形状的小饼干,面团的大小要是不合适,那做出来的饼干肯定不是你想要的样子。
钢坯在进入生产线之前呢,还得经过一些预处理,像表面清理之类的,得把表面的杂质啊、锈迹啊这些东西都除掉,这样才能保证后续加工的质量。
二、加热。
钢坯准备好了,就该加热啦。
这一步就像是给食材预热一样重要呢。
一般会把钢坯送到加热炉里,加热到一个很高的温度,通常都得有一千多摄氏度呢。
这么高的温度下,钢坯就变得软软的,就像软糖一样。
这样做是为啥呢?因为只有变软了,后面才能更好地进行变形加工呀。
要是钢坯是硬邦邦的,那想要把它变成我们想要的型钢形状,可就太难了,就像你想把一块硬石头雕刻成精美的雕像,那得多费劲呀。
在加热的过程中呢,还得控制好温度的均匀性。
要是有的地方热,有的地方冷,那钢坯在后续加工的时候就可能出现问题,比如说变形不均匀之类的。
三、轧制。
加热后的钢坯就来到了轧制这个环节啦。
轧制可是热轧型钢工艺流程里的重头戏哦。
轧机就像一个神奇的魔术师,它有不同形状的轧辊。
钢坯从这些轧辊中间穿过,就一点点地被压成我们想要的型钢形状啦。
比如说要生产工字钢,轧辊的形状就是按照工字钢的截面形状设计的。
这个过程就像是捏橡皮泥一样,不过难度可大多了。
轧机得不断地对钢坯施加压力,让它逐渐改变形状。
而且轧制可不是一次就能完成的,要经过好多个道次呢。
就像你想要把一个圆球捏成一个小房子的形状,得一点点地捏,一步一步来。
每一道次都会让钢坯的形状更接近最终的型钢。
在轧制的过程中,工人师傅们还得时刻盯着,看看有没有什么异常情况,比如说钢材表面有没有裂纹之类的,要是发现问题得赶紧调整。
热轧生产工艺流程

热轧生产工艺流程
《热轧生产工艺流程》
热轧生产工艺是指通过高温下对金属原料进行塑性加工,将其加工成带有一定厚度和宽度的钢板或钢板卷的工艺过程。
这一过程是钢铁生产中非常重要的环节,对于钢材的质量和性能都有着至关重要的影响。
热轧生产工艺流程包括原料准备、热轧加工、冷卷加工、热处理和表面处理等多个步骤。
首先,原料准备阶段需要选择适当的原材料,预处理并进行熔炼,得到符合要求的钢坯。
接下来是热轧加工阶段,将钢坯加热至适当的温度,通过轧制机械进行压制和成形,最终得到具有一定厚度和宽度的钢板或钢板卷。
冷卷加工是对热轧成品进行进一步精加工的阶段,通过冷轧机器对热轧成品进行压制和拉伸,使其获得更高的表面平整度和更好的机械性能。
而热处理则是对冷轧成品进行加热处理,以改善其组织结构和性能。
最后,表面处理阶段则是通过清洗、喷涂、防腐蚀处理等方式对成品表面进行处理,以确保产品的表面质量和使用寿命。
总的来说,热轧生产工艺流程是一个复杂的、多环节的过程,需要严格控制各个环节的参数和质量标准,以确保生产出符合用户需求和标准的优质钢材产品。
随着科技的发展和生产工艺的不断创新,热轧生产工艺流程也在不断演进和进步,为钢铁行业的发展和进步提供了坚实的基础。
- 1、下载文档前请自行甄别文档内容的完整性,平台不提供额外的编辑、内容补充、找答案等附加服务。
- 2、"仅部分预览"的文档,不可在线预览部分如存在完整性等问题,可反馈申请退款(可完整预览的文档不适用该条件!)。
- 3、如文档侵犯您的权益,请联系客服反馈,我们会尽快为您处理(人工客服工作时间:9:00-18:30)。
热轧工艺流程----初学必看1.主轧线工艺流程简述板坯由炼钢连铸车间的连铸机出坯辊道直接送到热轧车间板坯库,直接热装的钢坯送至加热炉的装炉辊道装炉加热,不能直接热装的钢坯由吊车吊入保温坑,保温后由吊车吊运至上料台架,然后经加热炉装炉辊道装炉加热,并留有直接轧制的可能。
连铸板坯由连铸车间通过板坯上料辊道或板坯卸料辊道运入板坯库,当板坯到达入口点前,有关该板坯的技术数据已由连铸车间的计算机系统送到了热轧厂的计算机系统,并在监视器上显示板坯有关数据,以便工作人员进行无缺陷合格板坯的核对和接收。
另外,通过过跨台车运来的人工检查清理后的板坯也需核对和验收,并输入计算机。
进入板坯库的板坯,由板坯库计算机管理系统根据轧制计划确定其流向。
常规板坯装炉轧制:板坯进入板坯库后,按照板坯库控制系统的统一指令,由板坯夹钳吊车将板坯堆放到板坯库中指定的垛位。
轧制时,根据轧制计划,由板坯夹钳吊车逐块将板坯从垛位上吊出,吊到板坯上料台架上上料,板坯经称量辊道称重、核对,然后送往加热炉装炉辊道,板坯经测长、定位后,由装钢机装入加热炉进行加热。
碳钢保温坑热装轧制:板坯进入板坯库后,按照板坯库控制系统的统一指令,由板坯夹钳吊车将板坯堆放到保温坑中指定的垛位。
轧制时,根据轧制计划,由板坯夹钳吊车逐块将板坯从保温坑取出,吊到板坯上料台架上上料,板坯经称量辊道称重、核对,然后送往加热炉装炉辊道,板坯经测长、定位后,由装钢机装入加热炉进行加热。
直接热装轧制:当连铸和热轧的生产计划相匹配时,合格的高温连铸板坯通过加热炉上料辊道运到称量辊道,经称重、核对,进入加热炉的装炉辊道,板坯在指定的加热炉前测长、定位后,由装钢机装入加热炉进行加热。
其中一部分通过卸料辊道运输的直接热装板坯需通过吊车吊运一次放到上料辊道后直接送至加热炉区。
如果炼钢厂可以实现直接热装板坯由上料辊道运送,则可减少部分吊车吊运作业。
板坯经加热炉的上料辊道送到加热炉后由托入机装到加热炉内,加热到设定温度后,按轧制节奏要求由出钢机托出,放在加热炉出炉辊道上。
加热好的板坯出炉后通过输送辊道输送,经过高压水除鳞装置除鳞后,将板坯送入定宽压力机根据需要进行侧压定宽。
定宽压力机一次最大减宽量为350 mm。
然后由辊道运送进入第一架二辊可逆粗轧机轧制及第二架四辊可逆粗轧机进轧制,根据工艺要求将板坯轧制成厚度约为30-60mm的中间坯。
在各粗轧机前的立辊轧机可对中间坯的宽度进行控制。
在R2与飞剪之间设有中间废坯推出装置,用于将中间废坯推到中间辊道的操作侧台架上。
中间坯由带保温罩的中间辊道输送到切头飞剪处切头、切尾,保温罩有利于减少中间坯的热量损失和带坯头尾温差。
飞剪前设有边部加热器,边部加热器可减少中间坯边部与中间部位的温度差,提高带钢性能的均匀性,提高轧件板型质量。
切头飞剪配有中间坯头尾形状检测仪及剪切优化控制系统,以实现优化剪切,减少切头切尾损失。
切头后的带坯经精轧前高压水除鳞装置清除二次氧化铁皮,由精轧前立辊导向进入精轧机组。
中间坯经过F1~F7四辊精轧机组,轧制成1.2~25.4 mm的成品带钢。
精轧机组的穿带速度、加速度、最大轧制速度、各机架压下量、工作辊窜辊行程、各机架弯辊力等均由计算机控制系统按轧制带钢的品种和规格进行计算和设定实现板形的闭环控制。
为了有效的控制带钢质量,在F7精轧机出口处设有凸度、平直度、厚度、宽度、温度等轧线检测仪表,在卷取机入口设有带钢表面质量、宽度、温度等轧线检测仪表。
精轧机轧出的带钢在输出辊道上由带钢层流冷却系统采用相应的冷却制度,将热轧带钢由终轧温度冷却到规定的卷取温度。
带钢的冷却方式,冷却水量都由计算机根据不同钢种、规格、终轧温度、卷取温度进行计算设定和控制。
当卷取机咬入带钢之前即穿带时,输出辊道、夹送辊、助卷辊和卷筒的速度均超前于末机架轧制速度;当带钢被卷取机咬入以后,输出辊道、夹送辊、卷取机随精轧机同步进行升速轧制;当带钢尾部离开末机架后,输出辊道、夹送辊要减速即滞后于卷取机卷取速度直到热轧钢卷尾部。
卷取完成后,由卸卷小车把钢卷托出至打捆机打捆。
再由钢卷运输系统将钢卷继续向后运送,经打捆、称重、标记后,分别运送到热轧钢卷成品库、冷轧原料库和精整原料库。
需要检查的钢卷则送到检查线,打开钢卷进行检查和取样后,再送回到钢卷运输系统,经打捆、称重、标记后分别送往热轧钢卷成品库、冷轧原料库和精整原料库。
在钢卷库内冷却后的钢卷按下一步加工工艺要求分别送至平整分卷机组、钢板横切机组、冷轧车间或按销售计划发货。
钢卷在运输和堆放的过程中均采用卧卷的方式,钢卷运往钢卷库或冷轧原料库的运输系统采用托盘运输系统,并与1780热轧厂的运输系统共同组成运输网络,由计算机统一控制。
从板坯进入板坯库开始至成品发货为止,全部工艺过程通过轧线物料跟踪系统及两库管理系统对板坯、轧件和钢卷进行全线跟踪,从而实现了计算机的自动化生产控制。
2.平整机工艺过程简述热轧卷放置在入口步进梁的入口鞍座上,步进梁将钢卷步运送到上卷小车上。
上卷小车将钢卷运送到钢卷准备站以便于拆除捆带,切掉带钢头部,同时进行宽度和径向定位,然后将钢卷运送到开卷机开卷。
带钢开卷后依次进入六辊矫直机、平整机、卷取机等从而完成设定的平整分卷工艺制度。
平整机采用衡压力控制技术,由计算机系统根据品种和规格设定平整压力,通过液压缸进行控制。
平整机设计平整厚度最大为6.5mm,厚度超过6.5mm的产品只分卷不平整。
分卷采用液压固定剪,设置在平整机出口。
平整分卷后的成品卷由卸卷小车卸卷,送到固定鞍座上,再由1#、2#步进梁将钢卷向后运输至成品库,在输送过程中完成称重和打捆作业。
最后钢卷由吊车运到指定位置堆放。
3. 钢板横切机组工艺流程简述车间的吊车将钢卷吊到机组的上料步进梁运输机上,然后运送到地辊站,钢卷在此进行水平、垂直对中和剪断捆带。
钢卷运载小车将钢卷装入开卷机卷筒后,带钢头部依次进入夹送辊、1#矫直机机组、活套、圆盘剪切边、飞剪成品定尺剪切、2#矫直机矫直、打印机或打号机进行描号、人工表面检查站,检查合格的钢板将送往垛板台进行堆垛。
次品板通过垛板台后的夹送辊送到次品区。
飞剪由计算机系统根据工艺制度设定速度和剪切长度,保证钢板剪切质量。
垛板台分为两组以便堆垛作业能按照钢板长度和数量进行连续操作。
堆垛由可横向移动的轮子来完成,根据不同板宽可进行调整。
堆垛完成后,升降台下降将钢板垛放到;链式板垛运输机上。
板垛通过运输机链条侧移,将其送到该运输机的称量机上。
称重后,用运输机将已称完重的板垛送到运输机后的卸料辊道上。
卸料辊道上有两个固定布置的打捆机,它负责对钢板垛进行打捆。
打捆完成后,板垛由吊车吊装入库。
mym 2008-05-09 14:24轧钢生产技术钢铁生产总是希望以成熟的新技术、新工艺,改进生产,降低运营成本,保证产品质量,提高竞争能力。
本文介绍近期轧钢生产所采用的新技术,其中有些是国外新技术,有些是投入新设备仪器的老工艺,其共同特点是可以达到生产顺利、成本降低,对钢铁企业会有所裨益。
轧钢生产的实用技术1 蓄热式加热炉高炉煤气发热值偏低,直接送到轧钢加热炉往往遇到加热能力不足的问题,所以一直需要配给一些焦炉煤气。
如果焦炉煤气不足,多余高炉煤气不得不放散或白白烧掉,造成浪费能源或污染空气。
蓄热式连续加热炉是20世纪90年代,美、日、英等国家开发的新技术,它利用高温烟气先预热蓄热箱中的蓄热体,之后更换阀门让待燃烧的空气或煤气进入蓄热箱吸收蓄热体的热量(图1)。
这样使空气或燃烧煤气提高500~800℃,燃烧温度可提高到1300℃,能够满足钢坯加热的需要。
由于高炉煤气价格低廉,国内某厂4座用焦炉煤气混烧或与重油混烧的加热炉改为蓄热式加热炉后,完全使用高炉煤气,加热成本基本降到原来的四分之一,不用两年即可收回改造费用。
其低氧燃烧和低NOx排放含量也达到较好水平。
该技术在加热炉、热处理炉都可应用。
目前,对于有高炉煤气的中国钢铁联合企业,已有不少完成蓄热炉的改造,获得显著效益。
2 悬浊液强力冷却由于终轧温度高,吐丝或上冷床的线材棒材温度过高,加上提速,原有冷却能力不足一直是困扰各棒线材厂的问题之一。
悬浊液强力冷却技术利用大比重悬浊物对汽膜的破坏,大大增强冷却能力,这是冷却理论上的重大突破。
由河北理工大学与宣钢二轧共同完成的棒材悬浊液穿水装置,经过生产实践检验证明,冷却效果十分显著。
该系统设计了新型喷嘴装置,其悬浊液循环系统经过近两年的运行,通畅可靠,水循环利用率高。
这一技术的成功为现场解决吐丝温度高、冷床能力不足、提高产品力学性能与合格率,提供了有效方法。
该棒材悬浊液穿水装置不必加长原有水冷段,仅仅增加一个小型蓄水池即可,冷却用水经过滤并循环利用,因而是现有车间实现中轧降温、进行低温精轧、或终轧后快速降温,大幅度提高产品的力学性能指标的切实可行的冷却新技术。
3 扁坯展宽轧窄带许多中窄带钢车间使用宽度尺寸不变的连铸坯,用常规轧法的轧件宽度就有限度。
有时轧辊宽度有所富余,因而出现用窄料轧制更宽带钢的需求。
为此,采用具有切深特点的强迫宽展开坯孔型,轧出较宽的带钢中间坯,精轧就可以轧出较宽带钢,更好适应市场的需求。
常用窄坯轧宽的方法是使用切展法和蝶式弯折法。
前者利用压下不均匀变形后,轧制变形区部分延伸少的金属阻碍其余金属的延伸,造成强迫宽展,目前已经可以生产比坯料宽出1 6倍的带钢。
4 圆钢定位测径仪在线测量终轧棒线尺寸,调节辊缝,扩大高精度产品比例,是众多棒线材厂的希望。
进口旋转式扫描式测径仪,可以在线测量高速运动的整个轧件凸起轮廓的外周边,但是这种仪器数百万元,而且整机长度大,放在现有长度十分有限的水冷段内很占空间。
其实,圆棒线生产主要掌握轧件高度和辊缝处的耳子,测量仪器如果能静止放置,就可以大大简化。
天津兆瑞测控公司生产的8点固定式测径,就能以非旋转的固定探头测量运动中的轧件尺寸,虽然不是连续反映轧件周边变化,但对高度、宽度等主要尺寸都能反映出来。
尤其该仪器宽度不到300mm,放在轨道车上,进入轧线或撤出轧线十分便利,适合精轧出口水冷段偏短的现场使用。
经过现场几年的使用证明,吹扫系统合理,光源寿命远比进口旋转测径仪持久,而价格仅为进口仪器的六分之一。
5 滚动轴承替换胶木轴瓦胶木轴瓦是长久以来使用的一种老式滑动轴瓦,虽然价格便宜,但刚度小,磨损快,在温度波动较大时,易出现轧件尺寸波动。
为此,某车间将三辊400中轧机改为密封的滚动轴承。
经过一段时间使用后,效果良好。
前面三辊轧机粗轧有尺寸波动的坯料,在这里也得到控制,使后面事故大大下降,对保证生产,提高产品尺寸精度起到显著作用,用水也显著减少。
6 弧齿接手替换梅花套筒梅花套筒传动是一种极为古老的传动轧辊方式,它在传递力矩时并不均匀,由于自重转动起来时常有悬空跌落过程,造成较大的噪音,同时对产品精度也有影响,严重时出现明暗交替的条纹。