轧钢生产工艺流程介绍
轧钢工艺流程
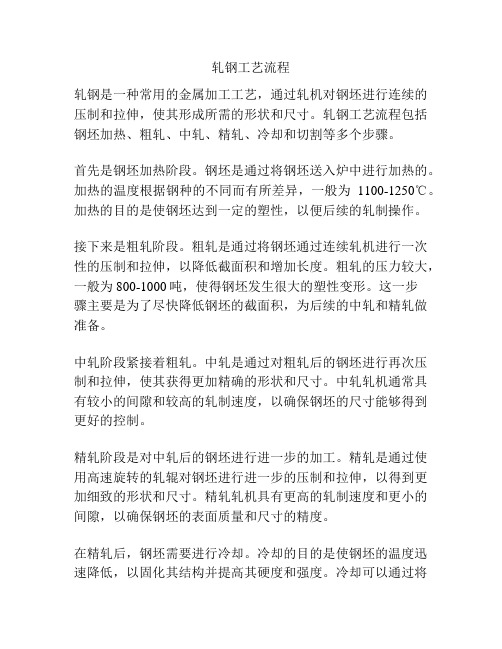
轧钢工艺流程轧钢是一种常用的金属加工工艺,通过轧机对钢坯进行连续的压制和拉伸,使其形成所需的形状和尺寸。
轧钢工艺流程包括钢坯加热、粗轧、中轧、精轧、冷却和切割等多个步骤。
首先是钢坯加热阶段。
钢坯是通过将钢坯送入炉中进行加热的。
加热的温度根据钢种的不同而有所差异,一般为1100-1250℃。
加热的目的是使钢坯达到一定的塑性,以便后续的轧制操作。
接下来是粗轧阶段。
粗轧是通过将钢坯通过连续轧机进行一次性的压制和拉伸,以降低截面积和增加长度。
粗轧的压力较大,一般为800-1000吨,使得钢坯发生很大的塑性变形。
这一步骤主要是为了尽快降低钢坯的截面积,为后续的中轧和精轧做准备。
中轧阶段紧接着粗轧。
中轧是通过对粗轧后的钢坯进行再次压制和拉伸,使其获得更加精确的形状和尺寸。
中轧轧机通常具有较小的间隙和较高的轧制速度,以确保钢坯的尺寸能够得到更好的控制。
精轧阶段是对中轧后的钢坯进行进一步的加工。
精轧是通过使用高速旋转的轧辊对钢坯进行进一步的压制和拉伸,以得到更加细致的形状和尺寸。
精轧轧机具有更高的轧制速度和更小的间隙,以确保钢坯的表面质量和尺寸的精度。
在精轧后,钢坯需要进行冷却。
冷却的目的是使钢坯的温度迅速降低,以固化其结构并提高其硬度和强度。
冷却可以通过将钢坯浸入冷水中或通过冷风吹扫来实现。
冷却的速度和方法根据钢种的不同而有所变化。
最后是切割阶段。
切割是将冷却后的钢坯切割成所需的长度和形状。
切割可以通过机械切割或火焰切割来实现,根据钢坯的尺寸和形状的不同而有所变化。
总结起来,轧钢工艺流程包括钢坯加热、粗轧、中轧、精轧、冷却和切割等多个步骤。
这些步骤的顺序和参数都会根据不同的钢种和需要的成品要求而有所变化。
轧钢工艺的发展使得钢材的生产更加高效和精确,满足了不同行业对钢材质量和性能的需求。
轧钢厂生产工艺流程图及简介
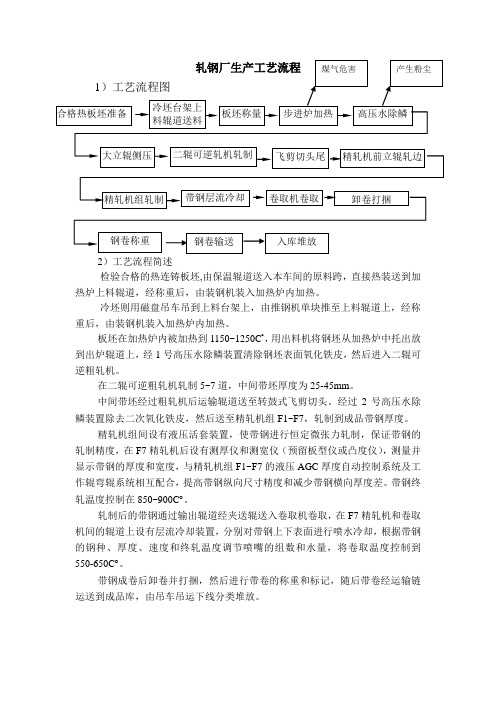
2)工艺流程简述
检验合格的热连铸板坯,由保温辊道送入本车间的原料跨,直接热装送到加热炉上料辊道,经称重后,由装钢机装入加热炉内加热。
冷坯则用磁盘吊车吊到上料台架上,由推钢机单块推至上料辊道上,经称重后,由装钢机装入加热炉内加热。
板坯在加热炉内被加热到1150~1250C︒,用出料机将钢坯从加热炉中托出放到出炉辊道上,经1号高压水除鳞装置清除钢坯表面氧化铁皮,然后进入二辊可逆粗轧机。
在二辊可逆粗轧机轧制5~7道,中间带坯厚度为25-45mm。
中间带坯经过粗轧机后运输辊道送至转鼓式飞剪切头。
经过2号高压水除鳞装置除去二次氧化铁皮,然后送至精轧机组F1~F7,轧制到成品带钢厚度。
精轧机组间设有液压活套装置,使带钢进行恒定微张力轧制,保证带钢的轧制精度,在F7精轧机后设有测厚仪和测宽仪(预留板型仪或凸度仪),测量并显示带钢的厚度和宽度,与精轧机组F1~F7的液压AGC厚度自动控制系统及工作辊弯辊系统相互配合,提高带钢纵向尺寸精度和减少带钢横向厚度差。
带钢终轧温度控制在850~900C︒。
轧制后的带钢通过输出辊道经夹送辊送入卷取机卷取,在F7精轧机和卷取机间的辊道上设有层流冷却装置,分别对带钢上下表面进行喷水冷却,根据带钢的钢种、厚度、速度和终轧温度调节喷嘴的组数和水量,将卷取温度控制到550-650C︒。
带钢成卷后卸卷并打捆,然后进行带卷的称重和标记,随后带卷经运输链运送到成品库,由吊车吊运下线分类堆放。
轧钢的工艺流程

轧钢的工艺流程
轧钢是一种将钢坯通过一系列工艺步骤加工成各种规格钢材的生产过程。
下面是轧钢的典型工艺流程。
1. 炼钢:首先,将原料如铁矿石、废钢等投入高炉或电弧炉中进行冶炼,产生熔融的钢液。
2. 连铸:从炼钢炉中得到的钢液经过脱氧、温度调节等处理后,通过连铸机连续浇铸成钢坯,得到粗钢。
3. 精炼:将粗钢进行精炼,其中包括脱硫、脱磷、脱氮等工艺,以提高钢的质量。
4. 预热:在开始轧制之前,将钢坯进行预热,以提高钢坯的塑性和可加工性。
5. 轧制:将预热后的钢坯送入轧机,经过多次高压轧制、冷却和拉伸等工序,使钢坯逐渐减小断面,得到所需的钢材形状。
6. 酸洗:为了去除钢表面的氧化物和锈蚀物质,对轧制后的钢材进行酸洗。
7. 表面处理:根据需要,对钢材进行镀锌、镀铬、涂层等表面处理,以提高钢的耐腐蚀性能。
8. 成品检验:对生产的钢材进行各项检测,包括化学成分、力学性能、外观质量等,确保钢材符合相关标准和要求。
9. 包装和出厂:经过检验合格的钢材进行包装,并按要求进行存放和运输,最终出厂供应给客户使用。
以上是轧钢的典型工艺流程,不同钢材的生产过程可能会有所差异,具体工艺参数也会根据不同钢材的特性进行调整。
建龙轧钢厂生产工艺流程
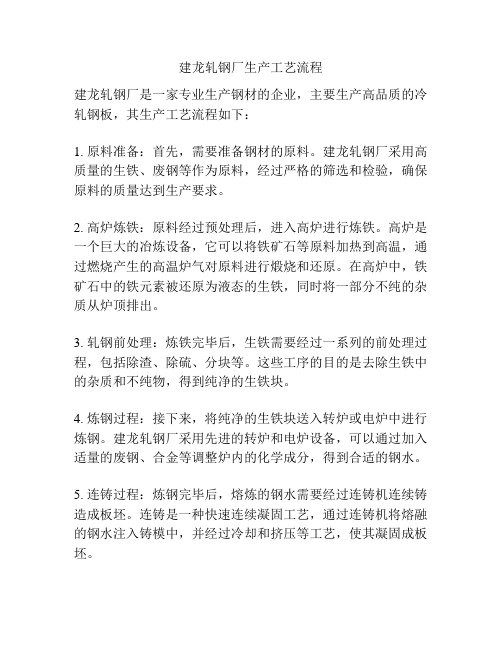
建龙轧钢厂生产工艺流程建龙轧钢厂是一家专业生产钢材的企业,主要生产高品质的冷轧钢板,其生产工艺流程如下:1. 原料准备:首先,需要准备钢材的原料。
建龙轧钢厂采用高质量的生铁、废钢等作为原料,经过严格的筛选和检验,确保原料的质量达到生产要求。
2. 高炉炼铁:原料经过预处理后,进入高炉进行炼铁。
高炉是一个巨大的冶炼设备,它可以将铁矿石等原料加热到高温,通过燃烧产生的高温炉气对原料进行煅烧和还原。
在高炉中,铁矿石中的铁元素被还原为液态的生铁,同时将一部分不纯的杂质从炉顶排出。
3. 轧钢前处理:炼铁完毕后,生铁需要经过一系列的前处理过程,包括除渣、除硫、分块等。
这些工序的目的是去除生铁中的杂质和不纯物,得到纯净的生铁块。
4. 炼钢过程:接下来,将纯净的生铁块送入转炉或电炉中进行炼钢。
建龙轧钢厂采用先进的转炉和电炉设备,可以通过加入适量的废钢、合金等调整炉内的化学成分,得到合适的钢水。
5. 连铸过程:炼钢完毕后,熔炼的钢水需要经过连铸机连续铸造成板坯。
连铸是一种快速连续凝固工艺,通过连铸机将熔融的钢水注入铸模中,并经过冷却和挤压等工艺,使其凝固成板坯。
6. 热连轧:板坯凝固后,进入热连轧机进行热轧加工。
热连轧是将板坯在高温下进行连续轧制的工艺,通过调整轧制的温度、压力和速度等参数,使板坯逐渐变形,并得到一定尺寸和形状的热轧钢板。
7. 酸洗处理:热连轧得到的钢板表面存在一定的氧化物和铁鳞等杂质,需要进行酸洗处理。
酸洗是将钢板浸入硫酸和盐酸组成的酸液中,去除表面的氧化物和铁鳞,使钢板表面更加洁净。
8. 冷连轧:酸洗处理后的钢板进一步经过冷连轧机进行冷轧加工。
冷连轧是将钢板在较低温度下进行连续轧制的工艺,能够进一步调整钢板的尺寸和形状,并提高钢板的表面光洁度和力学性能。
9. 表面处理:冷轧得到的钢板表面需要进行表面处理,包括锌涂层处理、镀锌处理等。
这些表面处理工艺能够提高钢板的防腐性能和装饰性能,延长钢板的使用寿命。
轧钢生产线工艺流程

轧钢生产线工艺流程
轧钢是将钢坯通过轧机进行连续轧制,使其形状、尺寸和表面质量得到一定的变化和改善的工艺。
轧钢生产线是钢铁行业中一个非常重要的生产设备,它的工艺流程对于钢材的质量和性能有着至关重要的影响。
下面将详细介绍轧钢生产线的工艺流程。
1. 钢坯加热
首先,将冷的钢坯放入加热炉中进行加热处理。
加热的温度和时间是根据不同的钢种和轧制要求而定的,一般来说,加热温度在1100℃-1250℃之间。
2. 粗轧
经过加热处理的钢坯被送入粗轧机中进行粗轧。
在粗轧机上,钢坯经过多道次的轧制,逐渐变形成为所需的形状和尺寸。
3. 精轧
粗轧后的钢坯被送入精轧机中进行精轧。
精轧是在辊道上进行
的,使钢坯的尺寸更加精确,表面质量更好。
4. 冷却
经过精轧后的钢坯需要进行冷却处理,以使其温度降到适合进
行后续加工的温度。
5. 切割
冷却后的钢坯被送入切割机中进行切割,切割成所需的长度。
6. 包装
经过切割后的钢坯被送入包装区进行包装,以便于运输和储存。
以上就是轧钢生产线的工艺流程,通过这一系列的工艺处理,
钢坯最终成为我们所需的各种形状和尺寸的钢材。
轧钢生产线的工
艺流程严格控制每一个环节,以确保钢材的质量和性能达到要求。
同时,随着科技的不断发展,轧钢生产线的工艺流程也在不断地进
行创新和改进,以满足市场对于钢材的不断提高的需求。
希望通过
不断的努力和创新,轧钢生产线的工艺流程能够更加完善,为钢铁
行业的发展做出更大的贡献。
轧钢厂生产工艺流程图及简介
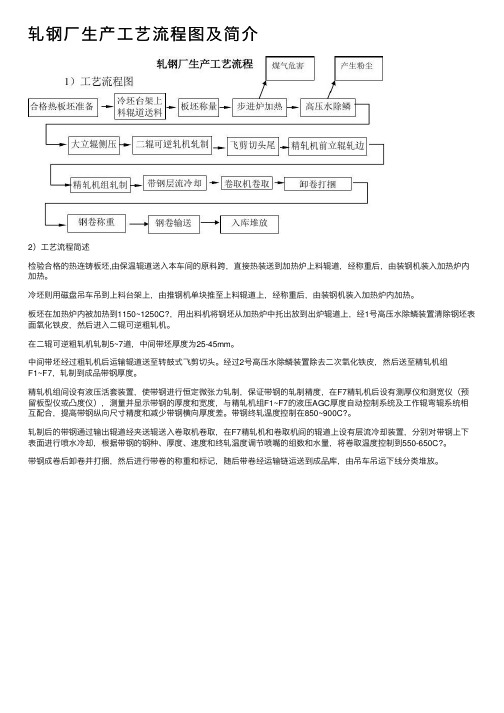
轧钢⼚⽣产⼯艺流程图及简介
2)⼯艺流程简述
检验合格的热连铸板坯,由保温辊道送⼊本车间的原料跨,直接热装送到加热炉上料辊道,经称重后,由装钢机装⼊加热炉内加热。
冷坯则⽤磁盘吊车吊到上料台架上,由推钢机单块推⾄上料辊道上,经称重后,由装钢机装⼊加热炉内加热。
板坯在加热炉内被加热到1150~1250C?,⽤出料机将钢坯从加热炉中托出放到出炉辊道上,经1号⾼压⽔除鳞装置清除钢坯表⾯氧化铁⽪,然后进⼊⼆辊可逆粗轧机。
在⼆辊可逆粗轧机轧制5~7道,中间带坯厚度为25-45mm。
中间带坯经过粗轧机后运输辊道送⾄转⿎式飞剪切头。
经过2号⾼压⽔除鳞装置除去⼆次氧化铁⽪,然后送⾄精轧机组
F1~F7,轧制到成品带钢厚度。
精轧机组间设有液压活套装置,使带钢进⾏恒定微张⼒轧制,保证带钢的轧制精度,在F7精轧机后设有测厚仪和测宽仪(预留板型仪或凸度仪),测量并显⽰带钢的厚度和宽度,与精轧机组F1~F7的液压AGC厚度⾃动控制系统及⼯作辊弯辊系统相互配合,提⾼带钢纵向尺⼨精度和减少带钢横向厚度差。
带钢终轧温度控制在850~900C?。
轧制后的带钢通过输出辊道经夹送辊送⼊卷取机卷取,在F7精轧机和卷取机间的辊道上设有层流冷却装置,分别对带钢上下表⾯进⾏喷⽔冷却,根据带钢的钢种、厚度、速度和终轧温度调节喷嘴的组数和⽔量,将卷取温度控制到550-650C?。
带钢成卷后卸卷并打捆,然后进⾏带卷的称重和标记,随后带卷经运输链运送到成品库,由吊车吊运下线分类堆放。
轧钢的生产流程
轧钢的生产流程
一、轧钢的生产流程
1、热轧:将钢坯加热至一定温度,并用机械力量压制成需要的规格或形状。
2、锻压:将钢材经过热处理、加工后,通过大压力将其转变成所需要的形状。
3、精炼:精炼是钢的加工步骤,它是把一定温度的原料经精炼处理,使金属组织的析出更加细腻,获得更高的性能。
4、热处理:主要是在一定的温度和时间内,利用淬火、正火、回火等技术,改变钢的组织结构,以改变钢的各项物理、机械性能、抗腐蚀性等性能的工艺。
5、热镀锌:将一定厚度的金属和氧化层放在一起,再经过高温加热,特别是与钢坯的表面接触成固溶体,从而形成锌层。
6、抛光和消光:将钢的表面抛光和消光,以改善表面的光泽度,使钢拥有漂亮的外观。
7、终检:在产品出厂前,还需要进行终检,确保所有产品符合要求标准。
- 1 -。
轧钢工艺流程简介
轧钢工艺流程简介轧钢工艺流程是将钢坯经过一系列的加工步骤,通过不断的压制和拉伸,最终得到所需形状和尺寸的金属板材的过程。
轧钢工艺流程在钢铁行业中具有重要的地位,对于钢材的品质和性能有着直接的影响。
1. 钢坯准备阶段在轧钢工艺流程中,首先需要对钢坯进行准备。
钢坯是通过炼钢过程中的连铸机连续浇铸而成的,其形状和尺寸不一。
在轧钢工艺中,首先需要对钢坯进行切割和去除表面的氧化层,以确保后续加工的顺利进行。
2. 加热阶段钢坯在进行轧制之前需要进行加热处理,以提高其可塑性和延展性。
加热的温度通常根据钢材的成分和要求的性能来确定。
加热的方式可以采用火焰加热或电加热,以使钢坯达到所需温度。
3. 粗轧阶段粗轧是轧钢工艺流程中的第一步,其目的是将加热后的钢坯进行初步的压制和拉伸,使其形成较薄的钢板。
这一阶段中,通常使用辊道机组进行轧制,通过辊道的旋转和压制,将钢坯逐渐变形成所需的形状和尺寸。
4. 中轧阶段中轧是对粗轧后的钢板进行进一步的压制和拉伸,以得到更加细薄的钢板。
在中轧阶段中,使用的轧机通常比粗轧阶段中的轧机更加先进和精密。
通过更高的压力和更精细的控制,中轧阶段可以使钢板的尺寸和形状达到更高的精度要求。
5. 精轧阶段精轧是轧钢工艺流程中的最后一道工序,其目的是对中轧后的钢板进行最后的压制和拉伸,使其达到最终的厚度和尺寸。
在精轧阶段中,使用的轧机通常更加精密和灵活,可以对钢板进行微调和修整,以确保其尺寸的一致性和平整度。
6. 冷却和整平阶段在精轧后,钢板需要进行冷却和整平,以恢复其原有的力学性能和平整度。
冷却可以采用水冷或空冷的方式,根据钢材的特性和要求来确定。
整平则是通过机械或液压的方式对钢板进行拉伸和修整,使其达到所需的平整度和表面质量。
7. 检验和包装阶段经过轧钢工艺流程的钢板需要进行严格的检验,以确保其质量和性能符合要求。
检验包括尺寸、表面质量、力学性能等方面的测试。
合格的钢板经过检验后,会进行包装和标识,以便于储运和使用。
轧钢的工艺流程
轧钢的工艺流程
《轧钢工艺流程》
轧钢是一种重要的金属加工方法,它可以将钢坯加工成各种不同形状和尺寸的钢材,广泛应用于建筑、汽车制造、船舶制造等领域。
下面介绍一下轧钢的工艺流程。
1. 熔炼和铸造:首先,将原料铁矿石经过熔炼和精炼的过程,得到精炼的铁水,再通过连铸连轧技术,将其浇铸成直条形的坯料。
2. 热轧坯料:接下来,将坯料进行预热处理,使其达到适宜的温度,然后通过热轧机器进行连续轧制,压制出所需形状的钢材。
3. 酸洗和精整:经过热轧后,钢材会产生一层氧化层,需要进行酸洗处理将其清除,并通过精整设备进行修整,以达到所需的尺寸和表面质量。
4. 冷轧和表面处理:对于一些要求更高的钢材,还需要经过冷轧处理,提高其尺寸精度和表面质量。
同时还可以经过镀锌、喷漆等表面处理工艺,增加钢材的耐腐蚀性和美观性。
5. 切割和包装:最后,将钢材按照客户需求进行切割和包装,以便于运输和使用。
以上就是轧钢的工艺流程,通过不同的轧制方式和表面处理工
艺,可以生产出各种不同形状和性能的钢材,满足各行业的需求。
轧钢生产工艺流程
轧钢生产工艺流程
轧钢生产工艺流程可以分为原料准备、预处理、轧制、控制与检验四个主要步骤。
以下是一个简要的轧钢生产工艺流程:
1. 原料准备:
首先需要准备合适的原材料,通常使用高质量的铁矿石和废旧钢材作为原料。
原料经过破碎、磨粉和筛分等步骤,使其达到符合要求的颗粒度和成分。
同时还需要添加适量的合金元素,以提高最终产品的性能。
2. 预处理:
对原料进行预处理,主要包括熔炼和炼钢两个过程。
在熔炼过程中,将铁矿石和废旧钢材与石灰石、焦炭等还原剂一起投入到高温高压的炉中,经过化学反应将金属铁分离出来,并排除掉杂质。
在炼钢过程中,将从熔炼过程得到的铁水进行净化、调质和炉炼等处理,以得到合格的钢水。
3. 轧制:
将炼钢得到的钢水倒入连续铸钢机中进行连铸,形成连续的铸坯。
然后将铸坯加热至适宜温度,通过轧钢机进行连续轧制。
轧制过程中可以按需控制轧制力和轧制速度,以获得所需的产品尺寸和形状。
通过不同的轧辊排列和轧制工艺,可以生产出各种不同规格、不同形态的钢材。
4. 控制与检验:
在整个生产过程中,需要根据产品的要求和相应的标准进行控制和检验。
使用各种仪器设备和自动化控制系统,对轧制过程
中的温度、力度、形状等参数进行实时监控和调整。
同时对轧制后的钢材进行检验,包括化学成分分析、物理性能测试和表面质量检查等。
只有合格的产品才能进行下一步的处理和出厂。
总之,轧钢生产工艺流程通过原料准备、预处理、轧制和控制与检验等环节,将原材料转化为符合要求的钢材产品。
同时,为了提高生产效率和产品质量,还需要不断推进技术改进和优化工艺流程。
- 1、下载文档前请自行甄别文档内容的完整性,平台不提供额外的编辑、内容补充、找答案等附加服务。
- 2、"仅部分预览"的文档,不可在线预览部分如存在完整性等问题,可反馈申请退款(可完整预览的文档不适用该条件!)。
- 3、如文档侵犯您的权益,请联系客服反馈,我们会尽快为您处理(人工客服工作时间:9:00-18:30)。
轧钢生产工艺流程介绍1、棒材生产线工艺流程钢坯验收f加热f轧制f倍尺剪切f冷却f剪切f检验f包装f计量f入库(1)钢坯验收=钢坯质量是关系到成品质量的关键,必须经过检查验收。
①、钢坯验收程序包括:物卡核对、外形尺寸测量、表而质量检查、记录等。
②、钢坯验收依据钢坯技术标准和内控技术条件进行,不合格钢坯不得入炉。
(2)、钢坯加热钢坯加热是热轧生产工艺过程中的重要工序。
①、钢坯加热的目的钢坯加热的目的是提高钢的塑性,降低变形抗力,以便于轧制;正确的加热工艺,还可以消除或减轻钢坯内部组织缺陷。
钢的加热工艺与钢材质量、轧机产量、能量消耗、轧机寿命等各项技术经济指标有直接关系。
②、三段连续式加热炉所谓的三段即:预热段、加热段和均热段。
预热段的作用:利用加热烟气余热对钢坯进行预加热,以节约燃料。
(一般预加热到 300〜450°C)加热段的作用:对预加热钢坯再加温至1150〜1250°C,它是加热炉的主要供热段,决定炉子的加热生产能力。
均热段的作用:减少钢坯内外温差及消除水冷滑道黑印,稳定均匀加热质量。
③、钢坯加热常见的几种缺陷a、过热钢坯在高温长时间加热时,极易产生过热现象。
钢坯产生过热现象主要表现在钢的组织晶粒过分长大变为粗晶组织,从而降低晶粒间的结合力,降低钢的可塑性。
过热钢在轧制时易产生拉裂,尤其边角部位。
轻微过热时钢材表面产生裂纹,影响钢材表而质M和力学性能。
为了避免产生过热缺陷,必须对加热温度和加热时间进行严格控制。
b、过烧钢坯在高温长时间加热会变成粗大的结晶组织,同时晶粒边界上的低熔点非金属化合物氧化而使结晶组织遭到破坏,使钢失去应有的强度和塑性,这种现象称为过烧。
过烧钢在轧制时会产生严重的破裂。
因此过烧是比过热更为严重的一种加热缺陷。
过烧钢除重新冶炼外无法挽救。
避免过烧的办法:合理控制加热温度和炉内氧化气氛,严格执行正确的加热制度和待轧制度,避免温度过高。
(C、温度不均钢坯加热速度过快或轧制机时产量大于加热能力时易产生这种现象。
温度不均的钢坯,轧制时轧件尺寸精度难以稳定控制,且易造成轧制事故或设备事故。
避免方法:合理控制炉温和加热速度;做好轧制与加热的联系衔接。
d、氧化烧损钢坯在室温状态就产生氧化,只是氧化速度较慢而己,随着加热温度的升高氧化速度加快,当钢坯加热到1100-1200°C时,在炉气的作用下进行强烈的氧化而生成氧化铁皮。
氧化铁皮的产生,增加了加热烧损,造成成材率指标下降。
减少氧化烧损的措施:合理加热制度并正确操作,控制好炉内气氛。
e、脱碳钢坯在加热时,表面含碳量减少的现象称脱碳,易脱碳的钢一般是含碳量较高的优质碳素结构钢和合金钢等。
这些钢都有其特殊用途,脱碳后,由于钢的表而与内部含碳量不一致,降低了钢的强度和影响了使用性能。
尤其对要求具有高耐磨性、高弹性和高韧性的钢来讲,由于脱碳而大大降低表而硬度和使用性能,甚至造成废品。
控制方法:严格加热制度,合理控制炉温和炉内氧化气氛。
(3)、轧制轧制工序是整个轧钢生产工艺过程的核心。
通过坯料轧制完成变形过程成为用户需要的产品。
轧制工序对产品质量起着决定性作用。
轧制产品质量包扌鼻产品的几何形状、尺寸精确度、内部组织、工艺力学性能及表面光洁度等几个方面。
因此,轧制工序必须根据产品技术标准或技术要求,生产产品特点和生产技术装备能力,以及生产成木和工人劳动条件等方面的要求,制定相应的轧制工艺技术规程和工艺管理制度。
以确保轧制产品质量和技术经济指标达到最优化。
轧制工序一般由一列(组)或二列(组)粗轧机、中轧机和精轧机组成。
分别承担钢坯断而压缩、半成品轧制变形和成品轧制功能。
成品轧机孔型或称精轧孔型为 K1孔,成品前轧机孔型为K2孔,成品前前轧机孔型为K3孔,以下如此类推。
连续式轧机和连轧常数连续式轧机是指几个轧机机座按轧制方向顺序排成一行, 轧件同时在几个轧机内轧制变形,各架轧制速度随着轧件长度的增加而增加,并保持金属在每架轧机中的秒流量相等或有轻微的堆拉钢关系的轧制方式称连续式轧机。
连续式轧机具有很高的机械化、自动化、轧制速度和轧制精度,因而劳动生产率高且产品品质优良,是棒、线材轧机改造和新建的方向。
保持在单位时间内轧件通过各轧机体积相等的轧制称连轧。
连轧常数二F1D1N1 二 F2D2N2= F3D3N3= ... = FnDnNn式中:F一轧件断而而积mm2D—轧车昆工作直径 mmN—轧车昆转数(1/min)(4)、精整①、钢材冷却冷床是轧制棒材产品的主要冷却设备。
散冷车昆道是线材产品的主要冷却设备。
冷床和散冷车昆道的作用是将800°C以上的高温轧件冷却到150-100°C以下,以恢复钢材固有的物理性能和便于保证剪切质量和后步工序操作。
冷却方式根据钢材的化学成分、组织状态、使用用途、以及冷却后可能产生的缺陷等方面,确定以下冷却方式:自然空气冷却自然空气冷却是碳素结构钢、低合金结构钢、优质碳素结构钢、以及奥氏体类不锈钢等钢种较为普遍采用的一种冷却方式,这种冷却方式一般不会影响钢材的物理性能。
]强迫快速冷却强迫快速冷却一般采用吹风、喷雾、喷水等方式,其工艺特点是使钢材在一定时间内速冷到某一温度后再进行自然冷却。
这种冷却方式一般能改变钢材的内部组织结构,会影响到钢材的物理性能。
如提高普通线材的机械性能;消除钢材网状碳化物等。
控制缓冷对冷却后产生应力敏感性较强的钢种一般均采用控制缓冷进行冷却,如高速工具钢、马氏体不锈钢、高合金工具钢以及高合金结构钢等。
这种冷却方式能够防止钢材组织发生变化和应力集中产生裂纹缺陷。
②、钢材剪切钢材剪切的目的:剪掉影响钢材使用(缺陷)的部位如钢材头和尾;切成用户需要的长度。
钢材剪切设备分冷剪和热剪。
热剪常用于半成品切头、切尾或倍尺剪切;冷剪常用于成品钢材切头、切尾或定(通)尺剪切。
③、钢材检验]钢材检验是确保产品质量符合产品技术标准和技术条件的关键工序。
产品检验通常包扌4钢材外形尺寸、表而质量、定尺长度、重量偏差、工艺性能、机械性能等。
不符合产品质量标准的钢材必须挑出并分类处置。
产品表而常见缺陷与预防措施棒、线材产品通常规定表面不得有裂纹、折叠、耳子、结疤、分层及夹朵等缺陷。
a.裂纹缺陷的产生与预防特征:在钢坯或钢材表面呈现深浅不一且分散的发状细纹,一般沿轧制方向不均匀排列。
产生原因:连铸坯的皮下气泡、表面气孔、非金属夹杂物、加热温度不均、钢温过低或轧后冷却不当(如优质碳素结构钢)等。
预防措施:炼钢应作好钢水的冶炼和脱气工作,降低出钢温度,采用保护浇铸,避免二次氧化;轧钢应合理控制炉温和冷却速度。
b、折叠特征:钢材表面沿轧制方向局部较长或连续的近似裂纹的缺陷。
一般呈直线状。
产生原因:轧件半成品出现耳子、严重划伤或孔型错车昆后的轧件再轧制时边角部位无法延展开而造成。
预防措施:合理控制半成品轧件尺寸,生产过程中应经常用木棒检查轧件车昆缝两边有无耳子和孔型错馄现象;注意观察轧件运行状况。
C、耳子特征:钢材辘缝两边或单边沿轧制方向过充满造成局部或连续的凸起状态。
产生原因:成品前孔轧件来料大;进口导卫偏、松,轧件扶不正;轧馄轴向窜动;加热不均或温度过低;成品孔型磨损产生带有台阶的凸起。
预防措施:合理控制加热炉温和半成品尺寸;严格导卫装置的调整;提高轧机预装精度;定时定量倒孔型。
d、结疤特征:钢材表而呈块状或鱼鳞状大小不等、厚度不均、外形不规则的“舌头形”或“指甲形”疤痕。
分闭合或不闭合;有根或无根。
结疤下面一般带有氧化铁皮。
翘起的结疤又称翘皮。
产生原因:钢坯有结疤、重皮、夹杂等缺陷;半成品轧件存在局部凸块;孔型掉块或沙眼;孔型刻痕或焊疤不良;轧件在孔型内打滑;外界金属轧入轧件表面;半成品轧件被外界物品刮伤等。
预防措施:不合格钢坯不得入炉;孔型采取刻痕或焊疤时,亥IJ、焊痕形状和高度应平缓圆滑;加强轧辘质量检查;合理孔型设计;严禁低温、黑头钢轧制;经常检查孔型磨损情况并及时倒孔型;轧件运送设备和运行场所应整洁圆滑。
e>划痕(刮伤、擦伤)特征:钢材表面有局部或断续的沟痕,一般呈直线或弧形。
产生原因:进口、出口导卫加工安装不当或轧件运送设备刮伤;轧件脱槽不利。
预防措施:正确加工、安装、使用进出口导卫设施;轧件运送设备和运行场所应整洁圆滑。
f、凹坑特征:钢材表面有局部周期性或无规律的凹下缺陷。
产生原因:轧制孔型有凸块或粘附有氧化铁皮;钢材表面无根结疤的脱落;外来金属物品代入孔型经轧制脱落后形成。
预防措施:孔型冷却水应干净,水量应充足;钢坯质量合格;生产环境无杂物。
2、线材生产工艺流程钢坯验收一加热一轧制一吐丝一散卷冷却一集卷一压卷一检验一包装一计量一入库线材生产钢坯验收、加热、轧制工艺部分与棒材生产工艺流程基本一致,但线材的冷却是通过散冷辘道进行的。
冷却后的散状线材需经过集卷机收集成盘,再经压卷机压实后进行小盘包装。
然后检验分类打包成大捆后计量入库。
3、棒、线材生产工艺故障判断分析与处理⑴、轧件不进产生原因:轧件毛烂头、劈头、黑头等;进口导卫安装不正或过小;进口导卫中有粘铁或异物;轧件翻转角度过大或过小;滚动导卫导轮不转或轴承烧坏;轧馄因断裂或连接原因不转;轧车昆车昆缝调整不当或来料尺寸不合要求;轧馄孔型摩擦系数太小(新孔型)等。
分析处理及预防措施①、分析轧件不进原因,加强轧件头部缺陷检查并及时处理;②、进口导卫安装后,应用内卡尺测量进口内腔宽度尺寸;用光线照明并从出口方向检查进口导卫是否对中孔型并紧固好导卫螺栓;③、用卡尺检查测量轧件实料尺寸,确保来料尺寸正确;④、轧鶴辘缝尺寸严格按轧制要求调整;⑤、勤对滚动导卫导轮、扭转出口进行检查并及时更换;勤对进口导板检查是否粘有铁宵和淤积氧化铁皮或杂物;⑥、新孔型应先用小料试车。
(2)、轧件堆钢故障轧件堆钢故障是指轧机间或轧机机组间轧件发生堆积后停滞不前的现象,称堆钢故障。
①、产生原因&、轧件来料尺寸、断而积过大;轧件本身存在表而或内部质量缺陷;b、轧车昆孔型摩擦系数不够,造成轧件打滑;c、来料轧机秒体积流量大于受料轧机秒体积流量;d、电器控制系统有误或失控。
e、自动活套系统机械运转部位或光电控制仪器安装有误、失控或失灵。
②、分析处理及预防措施38、调整来料尺寸而积,满足合理的连轧常数关系;b、动态严密监控轧件运行状况并及时调整;C、确保入炉钢坯质量;有质量缺陷的半成品轧件及时处理;d、定期检查各架轧机转数、活套系统和电器控制系统,确保运转设备和电控系统稳定正常。
(3)、轧件拉钢故障轧件拉钢故障是指轧机间或轧机机组间轧件过于拉紧或拉断的现象,称拉钢故障。
由于拉钢故障往往造成轧件尺寸发生变化,严重时甚至导致成品外形尺寸或不圆度超差造成废品。
①、产生原因8、轧件来料尺寸、断而积过小;b、来料轧机秒体积流量小于受料轧机秒体积流量;C、电器控制系统有误或失控。