高炉、烧结、球团工艺流程
高炉、烧结、球团工艺流程

炼铁工艺是将含铁原料(烧结矿、球团矿或铁矿)、燃料(焦炭、煤粉等)及其它辅助原料(石灰石、白云石、锰矿等)按一定比例装入高炉,并由热风炉向高炉内鼓入热风助焦炭燃烧,原料、燃料随着炉内熔炼等过程的进行而下降。
在炉料下降和煤气上升过程中,先后发生传热、还原、溶化、脱炭作用而生成生铁,铁矿石原料中的杂质与加入炉内的溶剂相结合而成渣,炉底铁水间断地放出装入铁水罐,送往炼钢厂。
同时产生高炉煤气、炉渣两种副产品,高炉渣水淬后全部作为水泥生产原料。
高炉是用焦炭、铁矿石和熔剂炼铁的一种竖式的反应炉(如图2-3)。
高炉是一个竖立的圆筒形炉子,其内部工作空间的形状称为高炉内型,即通过高炉中心线的剖面轮廓。
现代高炉内型一般由圆柱体和截头圆锥体组成,由下而上分为炉缸、炉腹、炉腰、炉身和炉喉五段。
由于高炉炼铁是在高温下进行的,所以它的工作空间是用耐火材料围砌而成,外面再用钢板作炉壳。
1-炉底耐火材料;2-炉壳;3-生产后炉内砖衬侵蚀线;4-炉喉钢砖;5-煤气导出管;6-炉体夸衬;7-带凸台镶砖冷却壁;8-镶砖冷却壁;9-炉底碳砖;10-炉底水冷管;11-光面冷却壁;12-耐热基墩;13-基座l图2-3 高炉的结构在高炉炉顶设有装料装置,通过它将冶炼用的炉料(由焦炭和矿石按一定比例组成)按批装入炉内。
在高炉下部炉缸的上沿,沿圆周均匀地布置了若干个风口(100m3小高炉有 8-10个,4000m3以上的大高炉则有36-42 个)。
加热到1000℃以上的热风,经铜质水冷风口送入炉内,供焦炭燃烧形成高温煤气。
在炉缸的底部设有铁口,可周期性或连续性地排放出液态生铁和炉渣。
在风口和铁口之间还设有渣口以排放部分炉渣,减轻铁口负担。
l现代高炉采用优质耐火材料,例如炉底、炉缸部位用微碳孔碳砖,炉身下部和炉腰部位用铝碳砖或碳化硅砖,其它部位用优质高铝砖和高致密度的粘土砖等作炉衬。
炉壳用含锰的高强度低合金钢制作,安装有性能好的含铬耐热铸铁、球墨铸铁或铜质立式冷却器,或铜质的卧式冷却器。
(完整版)高炉炼铁工艺流程及主要设备简介
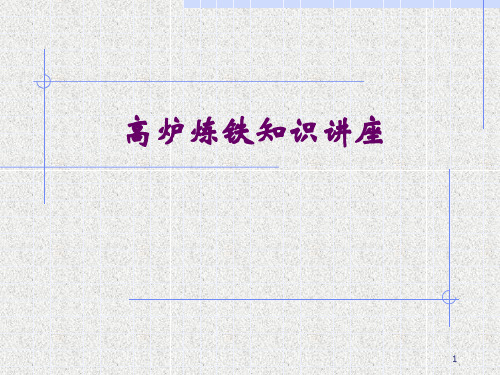
三、高炉冶炼主要设备简介
1、高炉 高炉炉本体较为复杂。 横断面为圆形的炼铁竖炉。用 钢板作炉壳,壳内砌耐火砖内衬。高炉本体自上而下 分为炉喉、炉身、炉腰、炉腹 、炉缸5部分。高炉生 产时从炉顶装入铁矿石、焦炭、造渣用熔剂(石灰 石),从位于炉子下部沿炉周的风口吹入经预热的空 气。在高温下焦炭中的碳同鼓入空气中的氧燃烧生成 的一氧化碳和氢气,在炉内上升过程中除去铁矿石中 的氧,从而还原得到铁。炼出的铁水从铁口放出。铁 矿石中未还原的杂质和石灰石等熔剂结合生成炉渣, 从渣口排出。产生的煤气从炉顶排出,经除尘后,作 为热风炉、加热炉、焦炉、锅炉等的燃料。高炉冶炼 的主要产品是生铁 ,还有副产高炉渣和高炉煤气。
1—高炉;2—重力除尘器;3 — 布袋除尘器; 4—调压阀组
23
三、高炉冶炼主要设备简介 重力除尘
24
三、高炉冶炼主要设备简介
箱体除尘: 由重力除尘后的荒煤气进入箱体进行布 袋过滤,最后成为净煤气。要求净煤气 粉尘量小于10毫克。
25
高炉冶炼主要设备简介
刮板机
26
高炉冶炼主要设备简介
27
高炉冶炼主要设备简介
炉渣和生铁定期通过铁口外排。通过炉前撇渣器进行渣 铁分离,铁水通过铁水罐运到炼钢或铸铁。炉渣经过 水淬后,输送到渣场。
高炉炼铁的主产品是生铁,副产品是高炉煤气、水渣、 炉尘。
5
二、高炉炼铁原理
6
三、高炉冶炼主要设备简介
高护炼铁设备组成有:①高炉本体;②供料设备;③ 送风设备;④喷吹设备;⑤煤气处理设备;⑥渣铁处 理设备。 通常,辅助系统的建设投资是高炉本体的4~5倍。生 产中,各个系统互相配合、互相制约,形成一个连续 的、大规模的高温生产过程。高炉开炉之后,整个系 统必须日以继夜地连续生产,除了计划检修和特殊事 故暂时休风外,一般要到一代寿命终了时才停炉。 高炉炼铁系统(炉体系统、渣处理系统、上料系统、 除尘系统、送风系统)主要设备简要介绍一下。
烧结和球团
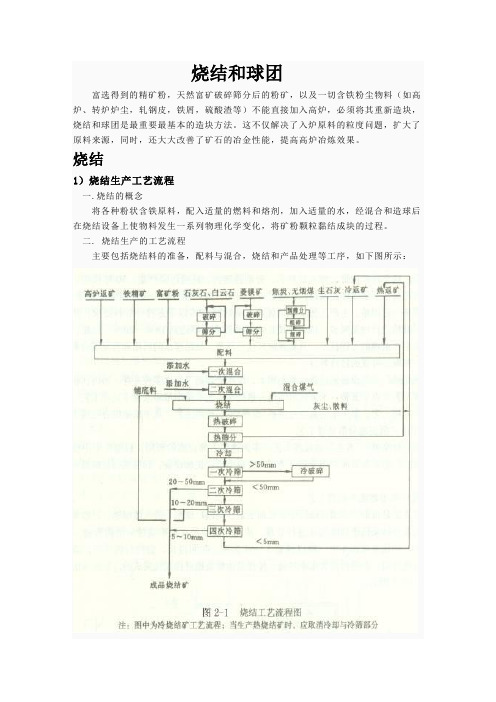
烧结和球团富选得到的精矿粉,天然富矿破碎筛分后的粉矿,以及一切含铁粉尘物料(如高炉、转炉炉尘,轧钢皮,铁屑,硫酸渣等)不能直接加入高炉,必须将其重新造块,烧结和球团是最重要最基本的造块方法。
这不仅解决了入炉原料的粒度问题,扩大了原料来源,同时,还大大改善了矿石的冶金性能,提高高炉冶炼效果。
烧结1)烧结生产工艺流程一.烧结的概念将各种粉状含铁原料,配入适量的燃料和熔剂,加入适量的水,经混合和造球后在烧结设备上使物料发生一系列物理化学变化,将矿粉颗粒黏结成块的过程。
二. 烧结生产的工艺流程主要包括烧结料的准备,配料与混合,烧结和产品处理等工序,如下图所示:1.烧结原料的准备①含铁原料含铁量较高、粒度<5mm的矿粉,铁精矿,高炉炉尘,轧钢皮,钢渣等。
一般要求含铁原料品位高,成分稳定,杂质少。
②熔剂要求熔剂中有效CaO含量高,杂质少,成分稳定,含水3%左右,粒度小于3mm 的占90%以上。
在烧结料中加入一定量的白云石,使烧结矿含有适当的MgO,对烧结过程有良好的作用,可以提高烧结矿的质量。
③燃料主要为焦粉和无烟煤。
对燃料的要求是固定碳含量高,灰分低,挥发分低,含硫低,成分稳定,含水小于10%,粒度小于3mm的占95%以上。
2.配料与混合配料目的:获得化学成分和物理性质稳定的烧结矿,满足高炉冶炼的要求。
混合目的:使烧结料的成分均匀,水分合适,易于造球,从而获得粒度组成良好的烧结混合料,以保证烧结矿的质量和提高产量。
混合作业:加水润湿、混匀和造球。
根据原料性质不同,可采用一次混合或二次混合两种流程。
一次混合的目的:润湿与混匀,当加热返矿时还可使物料预热。
二次混合的目的:继续混匀,造球,以改善烧结料层透气性。
3.烧结生产烧结作业是烧结生产的中心环节,它包括布料、点火、烧结等主要工序。
①布料将铺底料、混合料铺在烧结机台车上的作业。
当采用铺底料工艺时,在布混合料之前,先铺一层粒度为10~25mm,厚度为20~25mm 的小块烧结矿作为铺底料,其目的是保护炉箅,降低除尘负荷,延长风机转子寿命,减少或消除炉箅粘料。
高炉炼铁工艺流程(经典)

本文是我根据我的上传的上一个文库资料继续修改的,以前那个因自己也没有吃透,没有条理性,现在这个是我在基本掌握高炉冶炼的知识之后再次整理的,比上次更具有系统性。
同时也增加了一些图片,增加大家的感性认识。
希望本文对你有所帮助。
本次将高炉炼铁工艺流程分为以下几部分:一、高炉炼铁工艺流程详解二、高炉炼铁原理三、高炉冶炼主要工艺设备简介四、高炉炼铁用的原料附:高炉炉本体主要组成部分介绍以及高炉操作知识工艺设备相见文库文档:一、高炉炼铁工艺流程详解高炉炼铁工艺流程详图如下图所示:二、高炉炼铁原理炼铁过程实质上是将铁从其自然形态——矿石等含铁化合物中还原出来的过程。
炼铁方法主要有高炉法、直接还原法、熔融还原法等,其原理是矿石在特定的气氛中(还原物质CO、H2、C;适宜温度等)通过物化反应获取还原后的生铁。
生铁除了少部分用于铸造外,绝大部分是作为炼钢原料。
高炉炼铁是现代炼铁的主要方法,钢铁生产中的重要环节。
这种方法是由古代竖炉炼铁发展、改进而成的。
尽管世界各国研究发展了很多新的炼铁法,但由于高炉炼铁技术经济指标良好,工艺简单,生产量大,劳动生产率高,能耗低,这种方法生产的铁仍占世界铁总产量的95%以上。
炼铁工艺是是将含铁原料(烧结矿、球团矿或铁矿)、燃料(焦炭、煤粉等)及其它辅助原料(石灰石、白云石、锰矿等)按一定比例自高炉炉顶装入高炉,并由热风炉在高炉下部沿炉周的风口向高炉内鼓入热风助焦炭燃烧(有的高炉也喷吹煤粉、重油、天然气等辅助燃料),在高温下焦炭中的碳同鼓入空气中的氧燃烧生成的一氧化碳和氢气。
原料、燃料随着炉内熔炼等过程的进行而下降,在炉料下降和上升的煤气相遇,先后发生传热、还原、熔化、脱炭作用而生成生铁,铁矿石原料中的杂质与加入炉内的熔剂相结合而成渣,炉底铁水间断地放出装入铁水罐,送往炼钢厂。
同时产生高炉煤气,炉渣两种副产品,高炉渣铁主要矿石中不还原的杂质和石灰石等熔剂结合生成,自渣口排出后,经水淬处理后全部作为水泥生产原料;产生的煤气从炉顶导出,经除尘后,作为热风炉、加热炉、焦炉、锅炉等的燃料。
球团工艺流程简述

球团工艺流程简述生产球团所需铁精粉由铁路或汽车运输到综合料场存储,从地下配料仓上料,通过Φ2000 mm圆盘给料机、皮带称配料。
袋装膨润土由汽车运输到球团车间,储存在膨润土储库,膨润土通过拆袋机卸入膨润土仓,仓下装有星型给料机、螺旋绞刀电子秤。
每条线设4个精粉配料仓,1个膨润土仓。
单个精粉配料仓仓容约50 m3,膨润土仓仓容约35 m3。
配好的混合料通过皮带机输送至Φ3 m×20 m烘干机内进行烘干,烘干机热风来自热风炉,热风炉的燃料为高炉煤气(天然气点火)。
烘干后的物料通过皮带机输送至润磨机进行细磨。
润磨机规格为Φ 3.5 m×6.2 m。
当润磨机出故障或检修时,多余铁精粉通过旁通皮带直接运走,不经润磨。
经过润磨的物料通过皮带机输送至造球室混合料仓。
造球室内设置混合料仓3个,每个混合料仓对应1台Φ6000 mm造球盘。
混合料仓下设有拖式称量皮带,通过拖式称量皮带将物料均匀布在3个造球盘内,造球盘的倾角和转速可调。
造球盘出来的生球通过造球出料皮带送至摆动皮带,摆动皮带均匀地将物料布在上辊筛上,上辊筛间隙16 mm,将大于16 mm的大球通过溜槽和2400 mm宽皮带运至湿返料1#皮带;筛下球进入2800 mm宽皮带送至下辊筛,下辊筛间隙8 mm,将小于8 mm的筛下粉料,通过2400 mm宽皮带送入湿返料皮带,再通过返料皮带送回至造球配料仓,重新造球,合格球进入链篦机。
合格生球通过布料辊筛以160 mm~200 mm左右厚度均匀地布满篦床,随着篦床的运动,依次经过链篦机的干燥一段、干燥二段、预热段。
链篦机规格2.8 m×36 m,预热好的生球通过下料溜槽进入回转窑进行焙烧固结。
回转窑规格为Φ 4.0 m×30 m,在回转窑的窑头设有燃气烧嘴,同时来自环冷机一冷却段的高温废气作为二次风进入窑内。
预热球在窑内均匀焙烧,焙烧后成品球进入环冷机。
环冷机中径Φ12.5 m,台车宽度1.8 m,有效冷却面积50 m2,环冷机设三台冷却风机,对环冷机进行鼓风冷却,热风风箱分为三段,高温段气体引到回转窑做助燃风;中温段气体引至链篦机低温干燥段;低温段气体直接排空。
球团生产工艺流程

加热炉 (4座)
• 六、竖炉焙烧 • 竖炉主要分干燥、预热、焙烧、均热和冷却五个阶段。干燥带主要是 生球的干燥和初步加热,在干燥带生球的抗压强度提高,落下强度降
低,该带的温度一般控制在500℃以下,主要是避免因温度过高造成
生球爆裂;预热带:生球主要进行内部结晶水分解和排除,磁铁矿的 氧化和结晶,由于生球在预热带发生较多的物理化学变化,所以必须
• 三、烘干
• 为了使添加物能在矿粉颗粒间均匀分散,并使原料良好混合,同时也 为了使原料的水份适合造球,所以配好的混合料要进行烘干,烘干炉 温度控制在500℃±50℃。混匀料烘干后水份控制在7.5%±0.5%。 • 四、润磨
• 润磨系统采用球磨机,主要为了增强矿粉的表面活性以达到要求的矿
粉粒度、吸水能力和矿粉与矿粉间的吸附能力。在磨机内矿粉通过钢 球对其的砸、碾,磨,增强物料的表面活性,以满足造球对矿粉所需 的要求。控制润磨机工艺主要通过观察矿粉情况和润磨机的电流情况, 一般要求从润磨机内出来的矿粉粒度在200目以下达到80%,当润磨 机达不到此要求时应根据磨机电流情况及时给磨机内添加钢球。
膨润土
造 球 生球筛分
16毫米以上
煤气、空气
竖炉焙烧 成品矿仓
冷却风
污泥球新线工艺流程
• • 污泥球生产情况简介: 一、污泥球生产线的主要作用:是将炼钢收尘系统产生的的含铁尘泥 (简称 污泥)加入适量的膨润土和氧化铁皮,冷压成型,通过烘干和简单的焙烧成 成品污泥球。 二、生产设备及产能:目前公司本部污泥球生产系统由一套配料系统、一套 烘干系统、两台高压压球机、4座污泥球焙烧炉组成,生产系统的产能可达 400—450吨/日,目前日产300吨左右(6月30日后),现价段炼钢日产污泥 270吨(干基)左右。 三、污泥球生产配料:膨润土2%,炼钢污泥98%,正常情况下可配比一定量 的氧化铁皮。 四、成品球团指标情况: 质量指标:污泥球平均强度2400N, 950N合格率65%, 化学成份: TFe FeO SiO2 CaO MgO Al2O3 S P 成份
球团工艺简介及生产流程图
烧结厂球团工艺简介及生产流程图德晟金属制品有限公司烧结厂建设1座12m2竖炉,利用系数6。
3t/m2•h,年产酸性球团矿60万t。
车间组成及工艺流程1.1车间组成车间组成:配料室、烘干机室、润磨室、造球室、生筛室、转运站、焙烧室、带冷机通廊、成品缓冲仓、风机房、煤气加压站、软水站、高低压配电室等。
1.2工艺流程工艺流程图见付图1.2.1精矿接受与贮存竖炉生产主要原料为磁铁矿精粉,对铁精粉化学成分要求是进厂铁精粉化学成分精矿进料采用汽车输送,汽车将精矿粉卸到下沉式精矿堆场,经抓斗吊运至配料仓。
1.2.2膨润土接受与贮存竖炉对膨润土化学成分要求是:进厂膨润土化学指标袋装膨润土用汽车运入,储存在膨润土库,由库内设的电葫芦将袋装膨润土运至膨润土配料仓平台,由人工抖袋将膨润土卸到膨润土配料仓。
1.2.3配料系统配料矿槽采用单列配置,4个精矿配料仓,容积100m3,储量8.8h,三用一备;2个膨润土仓,膨润土仓为一用一备.配料室为地下结构。
采用自动重量配料,根据设定的给料量和铁精粉与膨润土的配比,自动调节给料量.铁精粉通过仓下2m圆盘给料机和配料皮带秤配料.膨润土通过螺旋给料机和螺旋秤配入皮带.圆盘给料机和螺旋给料机采用变频控制。
并且尽量做到铁精矿与膨润土两料流首尾重合。
在配料室膨润土落料点处和膨润土设抽风除尘,采用布袋除尘器,布袋除尘器采用反吹清灰方式。
设置铁精粉仓库和膨润土库。
铁精粉仓库能容纳约9天的用量,下沉式结构,铁精粉采用抓斗吊上料,设置2台10t抓斗吊。
膨润土库用来堆放袋装膨润土,膨润土设电葫芦环形轨道由电葫芦将袋装膨润土吊运至膨润土配料仓顶平台,人工抖袋卸料至膨润土配料仓。
1.2.4原料干燥系统精矿进厂水分为10。
5%左右,不能满足造球对精矿水分要求,因此设计中采用了干燥工艺,将精矿中水分部分脱除,以保证铁精矿水份满足造球工序的要求。
需干燥的湿精矿粉经配料胶带机运至干燥窑,物料干燥后经胶带机运至造球前料仓。
烧结、球团、白灰生产工艺流程
烧结、球团、白灰生产工艺流程2.6.1 烧结工艺烧结生产工艺流程为:(1)原料准备烧结所需的含铁原料在原料场经过混匀,由供料系统输送至烧结配料间,贮存在混匀料配料矿槽内;石灰粉和白云石粉由汽车运至烧结厂熔剂受矿槽,通过带式输送机卸入各自配料槽中;生产所用的熔剂生石灰粉由密封罐车运至配料室,用压缩空气输送至生石灰配料槽内;高炉返矿由汽车运输至配料室返矿仓内。
烧结用的固体燃料为<10mm的碎焦和无烟煤,燃料通过汽车送到受料槽,再由斗式提升机及带式输送机给至燃料破碎室的料槽中。
本项目燃料破碎系统由两个部分构成,每部分各由对辊破碎机和四辊破碎机组成。
本项目采用粗、细两段破碎流程,固体燃料首先进入第一段对辊破碎机进行粗破,破碎至0-20mm,然后进入第二段四辊破碎机进行细破,破至0-3mm粉料占90%以上,破碎后粒径合格的固体燃料送至燃料仓贮存。
(2)配料、混料混匀铁精粉、熔剂、燃料、返矿按设定的配料比例在配料室自动称量配料,配好的原料由胶带机送至混合室进行混料。
烧结采用二次混料,混合设备均为圆筒混合机。
一次混合主要是完成原料的混匀和加湿,二次混合主要是进行混匀制粒,使混合料中>3mm料球含量在80%以上,确保烧结料层具有良好的透气性,同时通入蒸汽预热混合料,以提高混合料料温。
(3)铺底料与布料为保护台车篦条,降低烟气含尘量,并使混合料烧结均匀,烧结机采用铺底料工艺。
铺底料烧结矿粒度为10-20mm,厚度为20-30mm,由摆动漏斗均匀地将底料布在烧结机台车上。
经二次混合的混合料由胶带机运至烧结室,经梭式布料器布至烧结机混合料矿槽内,再经圆辊给料机及六辊布料器将混合料布到烧结机台车上。
(4)点火抽风烧结烧结机点火以高炉煤气为燃料,点火温度约1100℃,布至台车上的混合料经点火后,料层中的燃料在烧结抽风机负压作用下自上而下逐渐燃烧,固结生成烧结矿。
(5)烧结矿卸料、冷却烧结机生产的烧结矿采用抽风环式冷却机进行冷却,烧成的烧结矿自烧结机机尾卸至单辊破碎机,破碎后的烧结矿,通过环冷机给料斗,落入环冷机进行冷却。
球团矿生产工艺流程
球团矿生产工艺流程
《球团矿生产工艺流程》
球团矿生产工艺流程是指将球团矿从原料到成品的生产过程。
球团矿是一种铁矿石的加工产品,经过适当的处理后可用于制造铁制品,如钢铁。
首先,在球团矿的生产过程中,原料的选择非常重要。
通常使用的原料包括铁矿石、焦炭和石灰石。
这些原料经过混合和研磨后,形成了适合球团矿的原料混合物。
接下来,原料混合物被送入球团机进行球团化处理。
球团机会将原料混合物压制成颗粒状的球形颗粒,这些颗粒即为球团矿。
在这个过程中,通常会添加一些粘结剂,以便球团矿颗粒能够保持形状和坚固度。
然后,球团矿颗粒被送入烧结炉进行烧结处理。
在烧结炉中,球团矿颗粒经过高温烧结,使得颗粒间的结合更加牢固,同时去除了一部分水分和杂质。
最后,经过烧结处理的球团矿成为了成品球团,可以被用于制造铁制品。
成品球团通常会被送往高炉进行冶炼,将其中的铁提取出来,再进行进一步的加工。
整个球团矿生产工艺流程中,各个环节的精细操作和控制都至关重要,以确保成品球团的质量和生产效率。
同时,对于球团
矿的生产还需要考虑环保和资源利用的问题,采取合理的措施来实现可持续发展。
烧结球团工艺流程图
烧结车间拥有90㎡*2台烧结机,主要依靠高炉煤气引燃,负压抽风烧结。
物料主要依靠胶带机运输,目前共有胶带机40条,拥有高压配电室一座,低压配电室5座,拥有高压变压器6台,大型高压风机2台,电除尘四座,6T余热锅炉2台(已停用),双气预热炉4台(已停用),桥式起重机3台,各类矿槽26座,湿法脱硫塔一座和硫铵制备系统等相关设备。
烧结车间下设有5个工段:生产系统含甲、乙、丙、丁四个工段,(205人);维修工段含电工班(21人)、钳工班(25人)、硫化班(18人);车间办公室(13人)2.2.2 烧结工艺系统简介
烧结工艺流程图
球团车间生产系统分为原料系统、配料系统、造球筛分系统、焙烧系统及成品系统五个系统,主要燃烧介质有焦炉煤气、高炉煤气及转炉煤气的混合气体,主要设备有4.3m*30m回转窑一台、3.1m*36m 链篦机一台、50㎡环冷机一台、3.2m*20m混合机一台、3500*6200mm 润磨机一台、直径6m的造球机5台、四条管带机、34条皮带机、两台高压风机、高压配电室一座、低压配电室9座等
球团车间下设2个工段:生产工段包含甲、乙、丙、丁四个作业班(132人),维修工段包含电工班和维修班(42人)。
2.2.2 球团工艺系统简介
球团工艺流程图。
- 1、下载文档前请自行甄别文档内容的完整性,平台不提供额外的编辑、内容补充、找答案等附加服务。
- 2、"仅部分预览"的文档,不可在线预览部分如存在完整性等问题,可反馈申请退款(可完整预览的文档不适用该条件!)。
- 3、如文档侵犯您的权益,请联系客服反馈,我们会尽快为您处理(人工客服工作时间:9:00-18:30)。
炼铁工艺是将含铁原料(烧结矿、球团矿或铁矿)、燃料(焦炭、煤粉等)及其它辅助原料(石灰石、白云石、锰矿等)按一定比例装入高炉,并由热风炉向高炉内鼓入热风助焦炭燃烧,原料、燃料随着炉内熔炼等过程的进行而下降。
在炉料下降和煤气上升过程中,先后发生传热、还原、溶化、脱炭作用而生成生铁,铁矿石原料中的杂质与加入炉内的溶剂相结合而成渣,炉底铁水间断地放出装入铁水罐,送往炼钢厂。
同时产生高炉煤气、炉渣两种副产品,高炉渣水淬后全部作为水泥生产原料。
高炉是用焦炭、铁矿石和熔剂炼铁的一种竖式的反应炉(如图2-3)。
高炉是一个竖立的圆筒形炉子,其内部工作空间的形状称为高炉内型,即通过高炉中心线的剖面轮廓。
现代高炉内型一般由圆柱体和截头圆锥体组成,由下而上分为炉缸、炉腹、炉腰、炉身和炉喉五段。
由于高炉炼铁是在高温下进行的,所以它的工作空间是用耐火材料围砌而成,外面再用钢板作炉壳。
1-炉底耐火材料;
2-炉壳;
3-生产后炉内砖衬侵蚀线;
4-炉喉钢砖;
5-煤气导出管;
6-炉体夸衬;
7-带凸台镶砖冷却壁;
8-镶砖冷却壁;
9-炉底碳砖;
10-炉底水冷管;
11-光面冷却壁;
12-耐热基墩;
13-基座
l图2-3 高炉的结构
在高炉炉顶设有装料装置,通过它将冶炼用的炉料(由焦炭和矿石按一定比例组成)按批装入炉内。
在高炉下部炉缸的上沿,沿圆周均匀地布置了若干个风口(100m3小高炉有 8-10个,4000m3以上的大高炉则有36-42 个)。
加热到1000℃
以上的热风,经铜质水冷风口送入炉内,供焦炭燃烧形成高温煤气。
在炉缸的底部设有铁口,可周期性或连续性地排放出液态生铁和炉渣。
在风口和铁口之间还设有渣口以排放部分炉渣,减轻铁口负担。
l现代高炉采用优质耐火材料,例如炉底、炉缸部位用微碳孔碳砖,炉身下部和炉腰部位用铝碳砖或碳化硅砖,其它部位用优质高铝砖和高致密度的粘土砖等作炉衬。
炉壳用含锰的高强度低合金钢制作,安装有性能好的含铬耐热铸铁、球墨铸铁或铜质立式冷却器,或铜质的卧式冷却器。
l4 工艺流程:
高炉冶炼过程是一个连续的生产过程,全过程是在炉料自上而下,煤气自下而上的相互接触过程中完成的。
如图2-4所示。
l炉料从受料斗进入炉腔。
在高炉底部的炉缸和炉腹中装满焦炭。
炉腰和炉身中则是铁矿石、焦炭和石灰石,层层相间,一直装到炉喉。
l从风口鼓入的热风温度高达1000-1300℃,炉料中焦炭在风口前燃烧,迅速产生大量的热,使风口附近炉腔中心温度高达1800℃以上。
l由于底部焦炭很厚,燃烧不完全,因此,炉气中存在大量CO气体,在炉内造成了良好的还原性气氛,产生的CO气体在炉体中上升。
同时,由于下部的焦炭燃烧产生空隙,上面的焦炭、矿石和熔剂在炉体内缓慢下降,速度大约为
0.5-1mm/s。
炽热的CO气体在炉内上升过程中加热缓慢下降的炉料,并把铁矿石中铁氧化物还原为金属铁,铁矿石在570-1200℃之间受到CO气体和红热焦炭的还原,形成了海绵铁。
海绵铁在1000-1100℃的高温下溶入大量的碳,因而铁的熔点下降,形成了生铁。
生铁的熔点约为1200℃,以液体状态滴入炉缸。
矿石中未被还原的物质形成熔渣,实现渣铁分离。
最后调整铁液的成分和温度达到终点,定期从炉内排入炉渣和生铁。
上升的高炉煤气流,由于将能量传给炉料而温度不断下降,最终形成高炉煤气从炉顶导出管排出。
1-料斗;2-大钟;
3-焦炭;4-燃料带;5-炉渣;6-铁水;
7-渣罐;8-铁罐;
9-铁口;10-风口;
11-矿石;12-上升煤气
l图2-3 高炉治炼过程示意图
烧结工艺流程介绍2010-04-29 08:42
烧结工艺流程介绍
为了保证供给高炉的铁矿石中铁含量均匀,并且保证高炉的透气性,需要把选矿工艺产出的铁精矿制成10-25mm的块状原料。
铁矿粉造块目前主要有两种方法:烧结法和球团法。
两种方法所获得的块矿分别为烧结矿和球团矿。
本专题将详细介绍烧结生产的工艺流程,主要工艺设备的工作原理以及控制要求等信息,其次,我们将简要介绍球团法生产的工艺流程,主要工艺设备的工作原理以及控制要求等信息。
由于时间的仓促和编辑水平有限,栏目中难免出现遗漏或错误的地方,欢迎大家补充指正。
铁矿粉造块的目的:
◆综合利用资源,扩大炼铁用的原料种类。
◆去除有害杂质,回收有益元素,保护环境。
◆改善矿石的冶金性能,适应高炉冶炼对铁矿石的质量要求。
铁矿粉造块的方法:烧结法和球团法。
铁矿粉造块后的产品:分别为烧结矿和球团矿。
(供高炉炼铁生产的主要原料)
一、烧结生产的工艺流程介绍:
查看冶金自动化频道 -> 烧结频道
烧结是钢铁生产工艺中的一个重要环节,它是将铁矿粉、粉(无烟煤)和石灰、高炉炉尘、轧钢皮、钢渣按一定配比混匀。
经烧结而成的有足够强度和粒度的烧结矿可作为炼铁的熟料。
利用烧结熟料炼铁对于提高高炉利用系数、降低焦比、提高高炉透气性保证高炉运行
均有一定意义。
烧结生产的流程
目前生产上广泛采用带式抽风烧结机生产烧结矿。
烧结生产的工艺流程如图下所示。
主要包括烧结料的准备,配料与混合,烧结和产品处理等工序。
烧结的原材料准备:
含铁原料:含铁量较高、粒度<5mm的矿粉,铁精矿,高炉炉尘,轧钢皮,钢渣等。
一般要求含铁原料品位高,成分稳定,杂质少。
熔剂:要求熔剂中有效CaO含量高,杂质少,成分稳定,含水3%左右,粒度小于3mm 的占90%以上。
在烧结料中加入一定量的白云石,使烧结矿含有适当的MgO,对烧结过程有良好的作用,可以提高烧结矿的质量。
燃料:主要为焦粉和无烟煤。
对燃料的要求是固定碳含量高,灰分低,挥发分低,含硫低,成分稳定,含水小于10%,粒度小于3mm的占95%以上。
烧结的配料与混合:
配料目的:获得化学成分和物理性质稳定的烧结矿,满足高炉冶炼的要求。
配料方法:质量配料法,即按原料的质量配料;通过电子计量设备,按一定比例配兑原材料。
混合目的:使烧结料的成分均匀,水分合适,易于造球,从而获得粒度组成良好的烧结混合料,以保证烧结矿的质量和提高产量。
混合的方法:加水润湿、混匀和造球。
根据原料性质不同,可采用一次混合或二次混合两种流程。
一次混合的目的:润湿与混匀,当加热返矿时还可使物料预热。
二次混合的目的:继续混匀,造球,以改善烧结料层透气性。
用粒度10~Omm的富矿粉烧结时,因其粒度已经达到造球需要,采用一次混合,混合时间约50s。
使用细磨精矿粉烧结时,因粒度过细,料层透气性差,为改善高炉透气性,必须在混合过程中造球,所以采用二次混合,混合
时间一般不少于2.5~3min。
我国烧结厂大多采用二次混合。
配料与混合的主要设备:
电子计量称:对放置在皮带上并随皮带连续通过的松散物料进行自动称量的衡器。
主要有机械式(常见的为滚轮皮带秤)和电子式两大类。
电子皮带秤是使用最广泛的皮带秤。
由承重装置、称重传感器、速度传感器和称重显示器组成。
主要用到的自动化产品:称重传感器、速度传感器、数显表、变频器、电动机
混合机:混合机械是利用机械力和重力等,将两种或两种以上物料均匀混合起来的机械。
混合机械广泛用于各类工业和日常生活中。
常用的混合机械分为气体和低粘度液体混合器、中高粘度液体和膏状物混合机械、热塑性物料混合机、粉状与粒状固体物料混合机械四大类。
主要用到的自动化产品:断路器、接触器、电动机
烧结生产:
烧结作业是烧结生产的中心环节,它包括布料、点火、烧结等主要工序。
布料:将铺底料、混合料铺在烧结机台车上的作业
点火:点火操作是对台车上的料层表面进行点燃,并使之燃烧。
烧结:准确控制烧结的风量、真空度、料层厚度、机速和烧结终点。
二、球团矿生产工艺流程
把细磨铁精矿粉或其他含铁粉料添加少量添加剂混合后,在加水润湿的条件下,通过造球机滚动成球,再经过干燥焙烧,固结成为具有一定强度和冶金性能的球型含铁原料。
球团矿生产的流程:
一般包括原料准备、配料、混合、造球、干燥和焙烧、冷却、成品和返矿处理等工序,如下图所示。
球团矿的生产流程中,配料、混合与烧结矿的方法一致;将混合好的原料经造球机制成10-25mm的球状。
球团矿生产中的主要设备:
圆盘造球机:将焦炭粉、石灰石粉或生石灰、铁精矿粉混合后,输入圆盘造球机上部的混合料仓内,均匀地向造球机布料,同时由水管供给雾状喷淋水,倾斜(倾角一般为40一50°)布置的圆盘造球机,由机械传动旋转,混合料加喷淋水在圆盘内滚动成球。
主要用到的自动化产品:断路器、接触器、电动机
带式焙烧机:带式焙烧机工艺使球团焙烧的整个工艺过程——干燥、预热、焙烧、冷却都在一个设备上完成,具有工艺过程简单、布置紧凑、所需设备吨位轻等特点,为工厂缩小占地面积、减少工程量、实现焙烧气体的循环利用以及降低热耗和电耗创造了条件。
主要用到的自动化产品:断路器、接触器、电动机。